疲劳断裂失效分析与表面强化预防
65mn弹簧疲劳断裂失效分析

第45卷 第5期金 属 制 品2019年10月 Vol 45 No 5MetalProductsOctober2019 doi:10.3969/j.issn.1003-4226.2019.05.01065Mn弹簧疲劳断裂失效分析周斌斌, 廖 建, 彭 凯(新余新钢金属制品有限公司, 江西 新余 338004)摘要:65Mn弹簧钢丝生产的拉簧服役几个月后发生断裂。
采用SEM扫描电子显微镜对弹簧断口表面进行形貌、金相组织等检测,对弹簧断裂原因及断裂过程进行分析。
结果表明,弹簧断口为疲劳失效断口,疲劳源处表面微裂纹是引起疲劳裂纹萌生的直接原因,表面微裂纹则是由不良抛丸工艺造成的。
弹簧厂通过更换新钢丸并降低抛丸速度消除了疲劳性能不符合要求的情况。
关键词:弹簧钢丝;拉簧;疲劳断裂;金相组织;裂纹;失效分析中图分类号:TG142.71 文献标识码:AFatiguefracturefailureanalysisof65MnspringZhouBinbin,LiaoJian,PengKai(XinyuXinsteelMetalProductsCo.,Ltd.,Xinyu338004,China)Abstract:Thepullspringof65Mnspringsteelwirebrokeafterseveralmonths’service.TheSEMwasusedtodetectthesurfacemorphologyandmicrostructureofthespringfracture,andthespringfracturecausesandfractureprocesswereana lyzed.Resultsshowthatthespringfractureisfatiguefailurefracture,andsurfacemicrocrackatfatiguesourceisdirectcauseoffatiguecrackinitiation.Thesurfacemicrocrackiscausedbybadshotpeeningprocess.Thespringfactoryelimi natesthefatigueperformancebyreplacingnewsteelshotandreducingshotblastingspeed.Keywords:springwire;tensionspring;fatiguefracture;microstructure;crack;failureanalysis 弹簧作为蓄能部件以实现特定动作或缓冲过程,压簧能在压力变化时压缩和恢复,如汽车减振、自动伞打开动作和冲压设备上的模具簧,拉簧在受拉时积蓄返回原位置的能量,如汽车制动系统的回位簧等,还有扭簧、卡簧等,也是利用弹性能量实现一定的动作或定位。
2-防止金属疲劳失效的措施
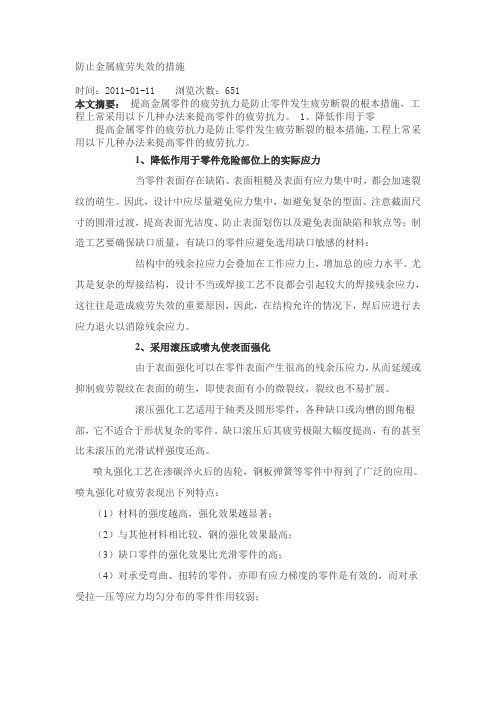
防止金属疲劳失效的措施时间:2011-01-11 浏览次数:651本文摘要:提高金属零件的疲劳抗力是防止零件发生疲劳断裂的根本措施,工程上常采用以下几种办法来提高零件的疲劳抗力。
1、降低作用于零提高金属零件的疲劳抗力是防止零件发生疲劳断裂的根本措施,工程上常采用以下几种办法来提高零件的疲劳抗力。
1、降低作用于零件危险部位上的实际应力当零件表面存在缺陷、表面粗糙及表面有应力集中时,都会加速裂纹的萌生。
因此,设计中应尽量避免应力集中,如避免复杂的型面、注意截面尺寸的圆滑过渡,提高表面光洁度、防止表面划伤以及避免表面缺陷和软点等;制造工艺要确保缺口质量,有缺口的零件应避免选用缺口敏感的材料:结构中的残余拉应力会叠加在工作应力上,增加总的应力水平。
尤其是复杂的焊接结构,设计不当或焊接工艺不良都会引起较大的焊接残余应力,这往往是造成疲劳失效的重要原因,因此,在结构允许的情况下,焊后应进行去应力退火以消除残余应力。
2、采用滚压或喷丸使表面强化由于表面强化可以在零件表面产生很高的残余压应力,从而延缓或抑制疲劳裂纹在表面的萌生,即使表面有小的微裂纹,裂纹也不易扩展。
滚压强化工艺适用于轴类及圆形零件,各种缺口或沟槽的圆角根部,它不适合于形状复杂的零件。
缺口滚压后其疲劳极限大幅度提高,有的甚至比未滚压的光滑试样强度还高。
喷丸强化工艺在渗碳淬火后的齿轮,钢板弹簧等零件中得到了广泛的应用。
喷丸强化对疲劳表现出下列特点:(1)材料的强度越高,强化效果越显著;(2)与其他材料相比较,钢的强化效果最高;(3)缺口零件的强化效果比光滑零件的高;(4)对承受弯曲、扭转的零件,亦即有应力梯度的零件是有效的,而对承受拉—压等应力均匀分布的零件作用较弱;(5)只对高周疲劳有效,而对低周疲劳作用不大,因为材料在高应变幅或高应力幅下要产生塑性变形,使应力松弛,这样残余压应力便不能保持;(6)对渗碳淬火的零件,要注意层深和心部强度的控制,较浅的层深有利于获得表层高的残余压应力,同时心部强度不能过高,否则,反会导致表面拉应力。
钻具断裂的失效分析及预防

2017年09月钻具断裂的失效分析及预防张孝兵海照新陈保民(川庆钻探工程公司长庆钻井总公司,陕西西安710018)摘要:油气田勘探开发过程中钻具受力状态十分复杂,所以其失效形式也多种多样。
如过量变形、断裂、表面磨损等。
发生井下钻具断裂事故,处理费用数额大,更甚者会发生打捞失败而弃井。
通过多年井下钻具断裂事故的处理经验、案例分析及试验研究总结出,大多数的钻杆断裂事故都是由于疲劳而引起的。
关键词:失效;疲劳;过量变形;钻具断裂1钻具断裂事故发生的一般规律在钻井实践中观察到的大量钻杆断裂现象可概括为:①钻杆大多数的断裂事故发生于旋转钻进过程中或在钻进后立即提离井底的时候;②大多数断裂发生在据钻杆接头1.2米的范围内;③管体的疲劳和腐蚀疲劳断裂均发生在内加厚过渡区消失处;④在有腐蚀性的洗井液中将引起管体或接头严重坑蚀,从断裂面上看到的这些裂纹是从内表面的腐蚀斑点开始的;⑤上提遇卡而拔断钻杆,断裂位置通常发生在已经产生疲劳裂纹,但尚未发展成为断裂的部位;⑥钻杆接头螺纹的疲劳断裂多发生于内螺纹接头大端第一和第二螺纹牙根部或外螺纹接头大端第一和第二螺纹牙根部。
2钻具断裂事故中钻具的失效形式2.1钻杆管体的疲劳和腐蚀疲劳断裂钻杆发生疲劳和腐蚀疲劳断裂破坏的主要原因是由于钻杆在弯曲井眼中旋转时发生周期性交变旋转弯曲应力以及井下腐蚀介质共同作用所致。
影响钻杆疲劳和腐蚀疲劳断裂的主要因素:①钻杆材料的抗拉强度和疲劳极限的影响;②钻杆材料冲击韧性的影响;③钻杆表面质量的影响;④腐蚀环境的影响;⑤拉伸和弯曲的组合影响;⑥累计疲劳。
2.2钻杆内加厚过渡区刺穿失效事故在钻杆管端镦粗加厚工艺控制过程中,由于内加厚过渡区太短,在钻杆使用中,在该区产生严重的应力集中,进而导致腐蚀集中并形成较深的腐蚀坑。
在旋转钻井过程中,钻杆受到旋转弯曲交变载荷的作用,在腐蚀坑底产生疲劳裂纹,最终导致钻杆刺穿或断裂,这属于钻杆的腐蚀疲劳断裂。
2.3内涂层钻杆加厚过渡区刺穿失效事故(内刺穿)由于钻杆(内涂层)内加厚过渡区的形状不良,在钻杆使用时导致局部涂层脱落并产生集中腐蚀(涂层脱落处的腐蚀速率要远远高于正常的腐蚀速率),很快会产生较深的腐蚀坑。
齿轮油泵传动轴断裂机理分析及预防措施

4 防止断裂措施和建议
结合上述疲 劳断裂机理 的分析 , 建议采取如下措施防止类似
断裂事故的再次发生 : ( 1 ) 严 密 监 控传 况 , 尽
在周 期性转矩作用 下, 应力集 中处的初始微裂纹不断发生扩 展。 当裂纹扩展 到一定尺 寸后, 传动 轴的剩余部 分不足 以承 受载 荷 的作用 , 因此发生瞬 时断裂 , 最后导致整个 传动轴发 生疲劳断 裂。 由于轴受扭转应力作用时 , 最大应 力方 向为环 向, 因此裂纹扩 展沿着 与轴线 垂直的方 向进 行, 最终形成 的断 口整体呈现正断特
系金属材料工程专业 , 大四在校 生。
( 上接 7 6页 )
[ 3 ] 张 厚美 ; 薛佑 刚 .岩 石可 钻性表 示 方法探 讨 [ J ] .钻 井工
艺 ,1 9 9 9 , 1 3 ( 1 ): 1 0 — 1 3 .
Z h an g H o u me i . X u e Y o ug a n g. Ro c k d ri l 1 a bi l i t y
l n m
应进行表面 处理。 具有相似 作用的常用表面处理方法 包括 : 激光
图 8疲 劳裂纹扩展三个阶段示意图
熔覆 、 热喷涂 、 电镀 、 化学镀等 , 这 些技 术在零件表 面处理方 面应
技术 也相对成熟 , 建议在 以后类似 的传 动轴发 生相似损 第 1阶段通常是起 始于金属 表面 的初始裂 纹处, 扩展方 向为 用很 广, 以提高备用件 的使用 寿命 。 最大切应 力方 向 ( 与主应 力成 4 5度角 ) , 沿晶面 向内扩展 。 由于 坏时有选择地采用相应技术 , 不 同的晶粒 的位 向不 同, 并且存在在 晶界的阻碍作 用, 因此随着 裂 纹的 向内扩展 , 其扩 展方 向逐渐转 向和主应 力垂直 。 第 一阶段 的裂 纹扩展深度 很小 , 通常约为几个 晶粒范 围。 若表面 受到力 的 作用 , 则会导致很难观察到第一阶段的裂纹扩展 。 疲劳 裂纹扩 展第 1 I阶 段的 主要特 征是裂 纹扩 展方 向与主 应力相垂直 , 当承 受扭转载荷 时, 该 主应 力方 向为传 动轴 的环 向 ( 或切 向 ) , 与该方向垂直的方 向为轴向或径 向, 在本例 中这一方 向为径 向, 即垂 直于轴 向的截 面。 在这一阶段 , 裂 纹尖 端的塑性区
金属材料疲劳断裂机理分析
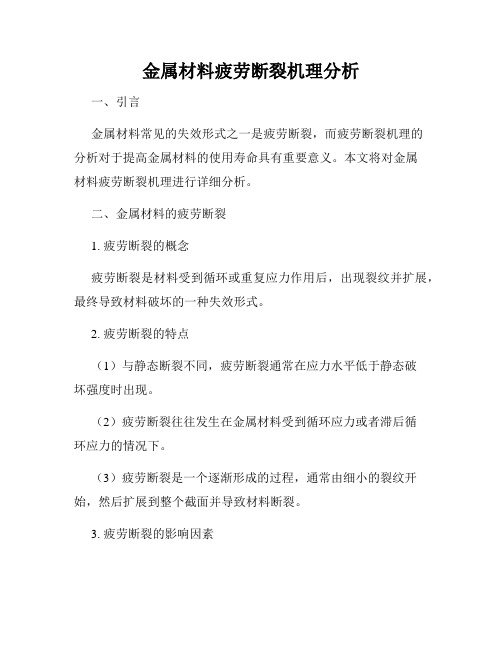
金属材料疲劳断裂机理分析一、引言金属材料常见的失效形式之一是疲劳断裂,而疲劳断裂机理的分析对于提高金属材料的使用寿命具有重要意义。
本文将对金属材料疲劳断裂机理进行详细分析。
二、金属材料的疲劳断裂1. 疲劳断裂的概念疲劳断裂是材料受到循环或重复应力作用后,出现裂纹并扩展,最终导致材料破坏的一种失效形式。
2. 疲劳断裂的特点(1)与静态断裂不同,疲劳断裂通常在应力水平低于静态破坏强度时出现。
(2)疲劳断裂往往发生在金属材料受到循环应力或者滞后循环应力的情况下。
(3)疲劳断裂是一个逐渐形成的过程,通常由细小的裂纹开始,然后扩展到整个截面并导致材料断裂。
3. 疲劳断裂的影响因素(1)应力幅值对于金属材料疲劳断裂的影响很大。
一般来说,应力幅值越大,疲劳断裂的损伤就越严重。
(2)材料的力学性质对于疲劳断裂也有很大的影响。
通常来说,强度越高的材料越难发生疲劳断裂,但是当强度相同时,材料的硬度越高,就越容易疲劳断裂。
(3)疲劳断裂还受到持续时间、温度、材料的化学成分和缺陷的影响。
4. 疲劳断裂的分类根据裂纹的扩展速率和应力比,疲劳断裂可以分为以下几类:(1)低周疲劳断裂:在循环应力下,材料的裂纹扩展速率很慢,往往需要上百万以上次循环才会导致疲劳断裂。
(2)中周疲劳断裂:循环应力下材料的裂纹扩展速率较快,在千-十万次循环后就能导致疲劳断裂。
(3)高周疲劳断裂:循环应力下材料的裂纹扩展速率极快,在数十万-数百万次循环内就会导致疲劳断裂。
5. 疲劳断裂的机理(1)金属材料的疲劳断裂过程一般分为始裂阶段和稳定扩展阶段。
(2)始裂阶段:在材料表面出现较小的裂纹,形成的原因是在应力作用下,材料中的微小缺陷和夹杂物开始聚集和扩散。
(3)稳定扩展阶段:当裂纹扩展到一定长度时,会出现塑性形变,当扩展到一定程度时,材料就会出现断裂。
(4)材料疲劳断裂机理可以采用形变、断裂学和金相学等多方面知识进行解释。
三、疲劳断裂机理分析1. 循环应力下的金属变形材料在循环应力下,会出现塑性变形和弹性变形两种不同的变形形式。
桥梁螺栓疲劳断裂失效分析
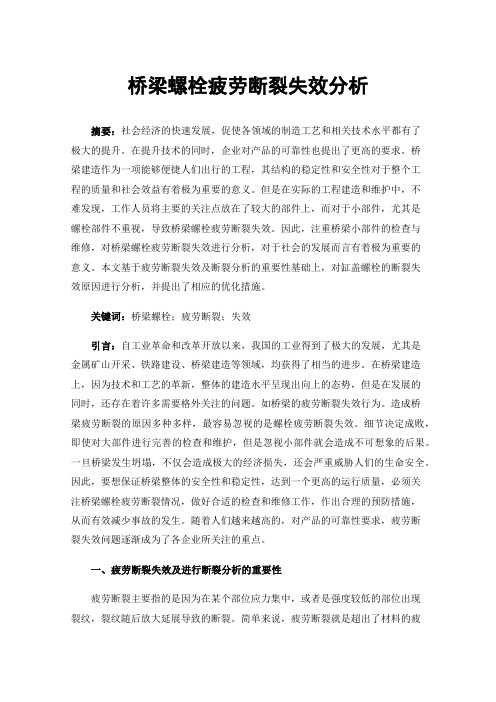
桥梁螺栓疲劳断裂失效分析摘要:社会经济的快速发展,促使各领域的制造工艺和相关技术水平都有了极大的提升。
在提升技术的同时,企业对产品的可靠性也提出了更高的要求。
桥梁建造作为一项能够便捷人们出行的工程,其结构的稳定性和安全性对于整个工程的质量和社会效益有着极为重要的意义。
但是在实际的工程建造和维护中,不难发现,工作人员将主要的关注点放在了较大的部件上,而对于小部件,尤其是螺栓部件不重视,导致桥梁螺栓疲劳断裂失效。
因此,注重桥梁小部件的检查与维修,对桥梁螺栓疲劳断裂失效进行分析,对于社会的发展而言有着极为重要的意义。
本文基于疲劳断裂失效及断裂分析的重要性基础上,对缸盖螺栓的断裂失效原因进行分析,并提出了相应的优化措施。
关键词:桥梁螺栓;疲劳断裂;失效引言:自工业革命和改革开放以来,我国的工业得到了极大的发展,尤其是金属矿山开采、铁路建设、桥梁建造等领域,均获得了相当的进步。
在桥梁建造上,因为技术和工艺的革新,整体的建造水平呈现出向上的态势,但是在发展的同时,还存在着许多需要格外关注的问题。
如桥梁的疲劳断裂失效行为。
造成桥梁疲劳断裂的原因多种多样,最容易忽视的是螺栓疲劳断裂失效。
细节决定成败,即使对大部件进行完善的检查和维护,但是忽视小部件就会造成不可想象的后果。
一旦桥梁发生坍塌,不仅会造成极大的经济损失,还会严重威胁人们的生命安全。
因此,要想保证桥梁整体的安全性和稳定性,达到一个更高的运行质量,必须关注桥梁螺栓疲劳断裂情况,做好合适的检查和维修工作,作出合理的预防措施,从而有效减少事故的发生。
随着人们越来越高的,对产品的可靠性要求,疲劳断裂失效问题逐渐成为了各企业所关注的重点。
一、疲劳断裂失效及进行断裂分析的重要性疲劳断裂主要指的是因为在某个部位应力集中,或者是强度较低的部位出现裂纹,裂纹随后放大延展导致的断裂。
简单来说,疲劳断裂就是超出了材料的疲劳极限。
断裂一般可以分为两种类型,即延性断裂和脆性断裂。
金属零件的疲劳断裂失效
(4) 装配与联接效应
装配与联接效应对构件的疲劳寿命有很大的影响。正确的拧紧力矩可使其疲劳寿命提高5倍以上。容 易出现的问题是,认为越大的拧紧力对提高联接的可靠性越有利,使用实践和疲劳试验表明,这种看 法具有很大的片面性。
(5) 使用环境
环境因素(低温、高温及腐蚀介质等)的变化,使材料的疲劳强度显著降低,往往引起零件过早的发 生断裂失效。例如镍铬钢(0.28%C,11.5% Ni,0.73%Cr),淬火并回火状态下在海水中的条件下疲 劳强度大约只是在大气中的疲劳极限的20%。
(5) 接触疲劳
02 疲劳断裂原因分析
(1) 零件的结构形状
零件的结构形状不合理,主要表现在该零件中的最薄弱的部位存在转角、孔、槽、螺纹等形状的突变 而造成过大的应力集中,疲劳微裂纹最易在此处萌生。 (2) 表面状态
不同的切削加工方式(车、铣、刨、磨、抛光)会形成不同的表面粗糙度,即形成不同大小尺寸和尖 锐程度的小缺口。这种小缺口与零件几何形状突变所造成的应力集中效果是相同的。由于表面状态不 良导致疲劳裂纹的形成是金属零件发生疲劳断裂的另一重要原因。
(3) 材料及其组织状态
材料选用不当或在生产过程中,由于管理不善而错用材料造成的疲劳断裂也时有发生,金属材料的组 织状态不良是造成疲劳断裂的常见原因。一般的说,回火马氏体较其它混合组织,如珠光体加马氏体 及贝氏体加马氏体具有更高的疲劳抗力;铁素体加珠光体组织钢材的疲劳抗力随珠光体组织相对含量 的增加而增加;任何增加材料抗拉强度的热处理通常均能提高材料的疲劳抗力。组织的不均匀性,如 非金属夹杂物、疏松、偏析、混晶等缺陷均使疲劳抗力降低而成为疲劳断裂的重要原因。
当外部的激振力的频率接近系统的固有频率时,系统将出现激烈的共振现象。共振疲劳断裂是机械设 备振动疲劳断裂的主要形式,除此之外,尚有颤振疲劳及喘振疲劳。
疲劳断裂失效分析与表面强化预防
1 .结构材料的疲劳失效特征
疲劳失效是材料在循环载荷作用 下发生 的损伤和破 坏过程 。一般而言疲劳断裂包 括裂纹 的萌 生 、裂纹 的扩
展和最终 的断裂三个过程 ,因此疲 劳断 口上有 三个相对
对疲劳断裂失效而 言,应该将疲 劳裂纹 的萌生 与疲 劳裂纹的扩展 ( 包括疲 劳小裂纹和长裂纹的扩展) 结合 起来 ,综合考 虑 疲 劳 裂 纹 的 “ ” 与 “ ” 的 过程 , 裂 断
参磊 工热 工 加
维普资讯
—
m
』 垫丝墨
特征 :
其 一, 劳裂纹源多位 于应 刀痕 、压 痕 、擦 伤 、锻 造 皱 皮 、折 l 叠 、疏松 、空洞 以及组织 中的晶界与孪 品界 、熔渣 、夹 杂物 、白点 、第二相粒子 、滑移集 中带 和形 变集 中带 等 部位都易于萌生疲劳裂纹 。 其二 ,疲劳裂纹扩展时 ,在延展性 好 的材料上易 产 生疲劳条带 ,在 脆性材料上多产生银纹或剪切带。 其三 ,对于疲 劳断裂 的瞬 断区 ,延展性好 的材料 多 以韧窝形态发生切 断 ,在脆性材料 上多产生结 晶特征 的
( )疲劳失效为低应力长时间无 明显 塑性 变形 的宏 1
观脆性断裂。
( )疲劳失效是 由材料局部的组 织不 断发生损伤变 2
化并且逐 渐 累积而 成 ,疲 劳总 是从 最 薄弱 的 区域 开始
( 图 1。 见 )
强调了裂纹的萌生 和扩展两个 阶段 。一 个零件要 “ 裂” 必须有裂纹 的产生并使裂纹长大 , 要想 “ 断” 必须是零
匀性 ,决定了疲 劳失效具有随机性 。
章, 对存在一定尺寸的裂纹或缺陷,通过分析剩余寿命
/ 剩余强度来计 算构 件 的安 全 ,一方 面可充 分发 挥材 料
汽车线束疲劳断裂分析及应对方案设计
汽车线束疲劳断裂分析及应对方案设计今天的TOPIC,是个头疼的问题--线束疲劳断裂,如果没有一定的失效经验积累或者有完备的实验验证方案,问题的突然发生,会让你感到惊讶不已。
什么是线束疲劳断裂?线束的金属导体(铜丝)在交变应力作用下(振动或者运动件产生),应力值虽然始终没有超过材料强度极限,经过长时间的应力反复循环作用以后,导体发生突然脆性断裂。
形象直观的生活案例:如图,手机充电线束尾部在长期使用,由于插拔时接口尾部线束受到扭曲弯转的应力,外护套首先开裂(外护套材质多为TPE),然后继续使用就会出现导体铜丝疲劳断裂。
那么研究充电线的耐折弯性能对改善充电线束的使用寿命变得尤为重要。
下方图片是疲劳断裂的导体断口位置的微观形貌,疲劳端口多发生在硬度差异的结合处,如上图充电线的圆圈位置,汽车线束线束固定卡扣的固定位置,导体会在长期挤压的位置形成凹痕,导体单丝之间会有相互运动产生的摩擦痕迹,一般导体断口位置会有一定的氧化。
线束疲劳断裂的危害手机充电线束的断裂只是影响我们手机充电,再借条充电线不影响我们看公众号、刷抖音,但作为汽车线束就大不相同,汽车线束作为高、低压电气/器部件的连接载体,承载整车的动力、信号传输,主导着整个汽车的安全与性能,汽车的载体是人,安全和客户感受尤为重要,。
线束疲劳断裂是线束的主要失效模式之一,汽车的车门线束、后背箱线束、发动机线束、车速传感器线束、新能源汽车的驱动电机线束(特别是轮边电机)、打气泵线束、空调压缩机线束等,在使用过程中承受弯曲载荷和振动载荷,恶劣环境下还要承受热载荷。
当这些汽车线束被运动或振动部件做周期性运动时,如果设计不合理,电缆耐弯曲性能不足,导体铜丝部分或全部会出现断裂、断股问题,就会影响车辆的正常功能及安全,目前整车对于导体断裂没有较好的检测手段,只有在线束导体完全短路、断路故障才能检测。
如果是新能源汽车高压线束突然发生短路,可能出线拉弧,对线束及电气部件甚至是整车造成不同程度的危害。
客车后钢板弹簧疲劳断裂原因的分析与改进措施
2)
簧片在断口处是否有附加应力产生除设计应力外,如果因某种原因有附加应力产生,使总应力加大也可能造成钢板弹簧片断裂,通过对断裂簧片断口处观察,发现此处在压延时造成了轻微急弯,使该片端部同上一片形成点接触,对这一点从试验后两片间的摩擦痕迹也证明了此点(如图)
摘 要:本文通过对BL客车后钢板弹簧断裂断口形状、设计应力、原材料及理化性能等方面的分析,找出造成钢板弹簧疲劳断裂的原因,提出了改进的措施,使该钢板弹簧的疲劳寿命达到日本五十铃公司标准的要求。
关键词:钢板弹簧;疲劳断裂;原因分析;改进措施
4 对钢板弹簧疲劳断裂原因分析
根据以上试验结果可以看出,疲劳断裂的簧片均在第7片且同在钢板弹簧的大卷耳端,且位置距钢板弹簧中心螺栓距离也差别不大(138、142、150),说明该钢板弹簧在此处存在规律性疲劳断裂源,而非偶然原因造成的,下面根据疲劳断裂试验结果及设计、生产过程对钢板弹簧疲劳断裂的原因进行分析。
......
I=7 σ1=37 σ2=41 σ3=44 σ4=47 σ5=17 σ6=2
......
注:I—片序 σ—应力 kg/mm2 各应力点为平均间隔(100mm)。
1 问题的提出
BL客车是对日本五十铃公司BE2ቤተ መጻሕፍቲ ባይዱ客车技术引进、吸收、消化后的一种轻型客车,该客车后悬挂弹性元件是一变刚度钢板弹簧,该种钢板弹簧的优点是在客车空载、满载状态下呈非线性状态,即悬挂在客车空载、满载状态下接近等频性,从而可以提高客车的平顺性,乘客乘坐舒适性,本文通过分析BL客车后钢板弹簧在设计、试制、试验过程中出现非正常疲劳断裂原因分析,提出了改进措施,使其达到了日本五十铃公司BE22客车后钢板弹簧疲劳寿命的标准要求。
- 1、下载文档前请自行甄别文档内容的完整性,平台不提供额外的编辑、内容补充、找答案等附加服务。
- 2、"仅部分预览"的文档,不可在线预览部分如存在完整性等问题,可反馈申请退款(可完整预览的文档不适用该条件!)。
- 3、如文档侵犯您的权益,请联系客服反馈,我们会尽快为您处理(人工客服工作时间:9:00-18:30)。
栏目主持李牟翔疲劳断裂失效分析与表面强化预防
北京航空材料研究院(100095)高玉魁
对于航空航天零部件而言,随着结构设计不断使用高强度结构材料来制造承力构件,越来越多的零件以疲劳断裂的方式发生失效事故。
因此,总结疲劳断裂的失效特征,分析其影响凶素,探讨疲劳失效的预防措施一直是材料和力学等学科的研究工作者和工程师们所关心的课题。
对疲劳断裂失效而言,应该将疲劳裂纹的萌生与疲劳裂纹的扩展(包括疲劳小裂纹和长裂纹的扩展)结合起来,综合考虑疲劳裂纹的“裂”与“断”的过程,定量计算疲劳寿命,以便为设计提供数据支持和依据。
目前的研究,材料工作者多从材料的组织结构特征方面来分析组织结构对疲劳寿命的影响,而断裂力学研究者则多从疲劳裂纹扩展寿命来计算安全的使用寿命。
这两种方法都有一定的道理,并分别侧重于裂纹的萌生与扩展阶段的研究。
对于疲劳断裂失效而言,疲劳断裂的过程都是先“裂”后“断”的。
“疲劳断裂”不如“疲劳裂断”科学,这不仅是因为“疲劳裂断”可反映疲劳裂纹的萌生、扩展与断开的先后次序,而且“裂”还同时强调了裂纹的萌生和扩展两个阶段。
一个零件要“裂”必须有裂纹的产生并使裂纹长大,要想“断”必须是零件上一定尺寸的裂纹在一定外力或环境的单独或共同作用下才能发生。
因此,从“疲劳裂断”的进程来看,如何“防裂”、“止裂”、“防断”和“止断”不仅在科学理论上,而且在工程应用中都具有十分重要意义的研究课题。
的强度潜力和使用性能;另一方面可提前预防失效事故并避免灾难的发生。
为便于理解和使用,除了在此强凋“裂”外,下文仍采用“疲劳断裂”来描述疲劳失效。
1.结构材料的疲劳失效特征
疲劳失效是材料在循环载荷作用下发生的损伤和破坏过程。
一般而言疲劳断裂包括裂纹的萌生、裂纹的扩展和最终的断裂三个过程,因此疲劳断口上有三个相对应的区域,即裂纹源区、裂纹扩展区和瞬断区。
根据所受载荷的水平、材料的力学特性、试样的形状尺寸与约束条件的不同,这三个区域的大小、形状和分布特征也不尽相同,但总体而言可归纳为下列的4个宏观规律特征:
(1)疲劳失效为低应力长时间无明显塑性变形的宏观脆性断裂。
(2)疲劳失效是由材料局部的组织不断发生损伤变化并且逐渐累积而成,疲劳总是从最薄弱的区域开始(见图1)。
图l疲劳裂纹萌生于内部的夹杂物缺陷
(3)疲劳断裂必须在循环应力和微观局部发生塑性
“防裂”和“止裂”是在“裂”上下功夫,通过分变形,以及拉伸应力作用下发生。
前者是裂纹形成的条析裂的规律,找出裂的原因,提出防裂的措施,采用合
理的结构设计、合适的材料、适宜的热处理制度及可靠
的零件加工与适当的表面强化来改进开裂的方式,提高
开裂的抗力。
“防断”和“止断”是在“断”字上做文
章,对存在一定尺寸的裂纹或缺陷,通过分析剩余寿命
/剩余强度来计算构件的安全,一方面可充分发挥材料
囵踅Q里堡箜!!塑整丝型堡旦箜蕉www.machinist.com.cn参磊卢工热lm-r
件,后者是裂纹扩展的需要。
(4)疲劳失效具有随机性,裂纹的形成与扩展都需
要一定的晶体学条件、力学条件和变形的协调条件,而
且材料本身的组织结构、成分偏析与夹杂缺陷等的不均
匀性,决定了疲劳失效具有随机性。
从疲劳失效的断口分析而言,微观上讲具有以下
万方数据
万方数据
的例子是对于飞机起落架,虽然形状相同,但采用强度不同的GC4、30CrMnSiNi2A和300M来加工制造,其飞行寿命相差很远。
对不同使用条件下的零件应选择性能相适应的材料,在室温下选择晶粒细小、强度高和韧性好的结构材料比较耐疲劳;而在高温下选择晶粒适当、组织稳定、强韧性配合较好的结构材料才可提高疲劳寿命。
合适的材料是制造长寿命抗疲劳零件的基础。
(3)适宜的热处理制度选择了一定的形状尺寸和合适的材料,对材料进行适宜的热处理显得非常关键。
相同的材料,热处理制度不同,疲劳性能也就完全不同。
40Cr材料在不同温度下进行回火或对其进行渗氮化学热处理,其疲劳强度绝对数值可差500MPa,相对数值差为40%。
热处理时不仅需要关注材料热处理后的组织与性能,更需要保证热处理制度的稳定性、可靠性,应避免在工件表面彤成脱碳、过热、硬脆相等变质层,以确保表面层的疲劳抗力。
(4)可靠的零件加工工艺零件的加工质量对其使用寿命的影响很大,相同的材料即使采用相同的热处理制度,但如果选用不同的加工方式进行制造,其疲劳性能也相差很大,尤其是对于高强度结构材料。
可靠稳定的零件加工制造工艺是零件表层质量的保证,没有好的零件加工工艺就得小到好的表面质量,也谈不上高的疲劳性能。
零件加工时要杜绝烧伤、吃刀等工艺所产生的缺陷,并尽量减小加工过程中产生的残余拉应力数值。
(5)适当的表面强化处理表面强化工艺技术虽然起源于结构的维护修理,但近年来已被设计单位和工厂作为一种设计技术和制造技术,用于零件的加工、制造与维护等过程。
零件的设计是基础和依据,零件的材料选择是关键的性能支撑,制造工艺是实现加1二的手段和可靠性的根本保证,表面强化则是零件表层性能的守护神。
采用合适的表面强化工艺技术处理零件,可使零件不在表面发生疲劳失效,而在表层下的基体处萌生疲劳裂纹,这将充分发挥材料的强度潜力,节省材料的消耗。
4.表面强化预防疲劳失效的机理、效果与应用
最初,国内外的表面强化技术主要应用于航空工业,以提高飞机关键部位的细节疲劳品质。
随着工业技术的发展,该技术被逐渐推广应用在机械、机车、交通、建筑和石油化工等行业,典型的零件如齿轮传动
囵2旦!璺堡箜!三塑麴丝型堡墅箜堕WWW.rrlachinis^com.cn参磊加工热加工
件、桥梁紧固件、石油钻具和化工容器等。
表面强化之
所以能够在工业上得以推广应用,主要与其普遍的适应
性、显著的强化效果、简便的操作技术等密切相关,但
要合适地采用表面强化工艺技术来预防疲劳失效,需要
知道表面强化的机理和强化效果的评价方法。
表面强化的机制很多,但表面形变强化的机理主要
包括以下几个方面:
(1)组织结构的细化与强化。
(2)表面形变所产生的加工硬化。
(3)残余压应力场的引入。
(4)表面缺陷的弥合消失与减少或减小。
(5)表面粗糙度与形貌的改善。
喷丸所产生的表面
完整性变化如图3所示。
图3喷丸产生的表面变化
表面强化效果常采用疲劳性能来进行评价,在相同
的应力水平下,对比不同表面处理状态下试样的疲劳寿
命,或进行疲劳强度/极限的对比,以考核表面强化的
效果,并对工艺参数进行优化。
图4喷丸试样的疲劳裂纹
大量的试验结果与理论研究分析表明,采用表面强
化可使疲劳强度/极限提高30%以上,且疲劳裂纹出现
在表面强化层下的残余拉应力区域(见图4)。
有关文
献指出,当疲劳裂纹萌生在距离表面10个晶粒尺寸以
下的区域时,可以认为表面强化效果最好,而且对于某
一材料而言,此时的疲劳强度/极限为材料的特征参数
是一个常数。
MW
(20080420)
万方数据
疲劳断裂失效分析与表面强化预防
作者:高玉魁, Gao Yukui
作者单位:北京航空材料研究院,100095
刊名:
金属加工(热加工)
英文刊名:MW METAL FORMING
年,卷(期):2008(17)
被引用次数:1次
1.雷声.黄曼平.薛正堂.吴跃波表面激光硬化轴承的疲劳失效分析[期刊论文]-热加工工艺 2013(2)
引用本文格式:高玉魁.Gao Yukui疲劳断裂失效分析与表面强化预防[期刊论文]-金属加工(热加工) 2008(17)。