Fisher定位器使用说明书
FISHER_DVC2000_智能定位器参数设置方法
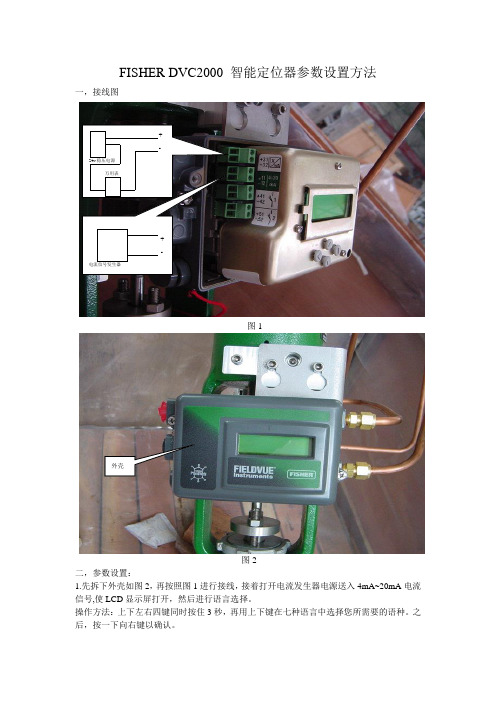
FISHER DVC2000 智能定位器参数设置方法一,接线图+-24v稳压电源万用表+-电流信号发生器图1外壳图2二,参数设置:1.先拆下外壳如图2,再按照图1进行接线,接着打开电流发生器电源送入4mA~20mA电流信号,使LCD显示屏打开,然后进行语言选择。
操作方法:上下左右四键同时按住3秒,再用上下键在七种语言中选择您所需要的语种。
之后,按一下向右键以确认。
2.然后根据阀体的执行机构是气开式还是气闭式进行对参数设置。
如图3就是气闭式。
操作方法:按向下键找到“详细设置”选项,再按右键确认进入如果阀体的执行机构是:气开式(FC):按右键查找“零控制信号”项,再按上下键选择“阀关”按右键确认再按右键查找“行程变送器输出4mA”项,按上下键选择“阀关”按右键确认气闭式(FO):按右键查找“零控制信号”项,再按上下键选择“阀开”按右键确认再按右键查找“行程变送器输出4mA”项,按上下键选择“阀关”按右键确认气开(FC)给定信号阀位指示LCD指示回讯/反馈信号4mA 0%0%4mA20mA 100%100%20mA气闭(FO)给定信号阀位指示LCD指示回讯/反馈信号4mA 100%100%20mA20mA 0%0%4mA3.行程自动标定设置操作方法:按向下键找到“行程标定”项,按右键确认进入,再按上下键选择“自动”按右键确认,LCD显示“按右键3秒钟阀门将动作”然后按照它的提示操作,它便可以自动搜索走完整个行程0%、100%、50%。
完成后按右键确认。
注:搜索途中不可退出,按任何键都不起作用,必须等走完整个行程才可以。
4.整定设置增益代码(C~M),C时阀门动作最慢,M时阀门动作最快。
选择合适的,一般设置为“L”,以阀门不振荡为准。
操作方法:按向下键找到“整定”项,按右键确认进入,再按上下键选择“自动”按右键确认,LCD显示“按右键3秒钟阀门将动作”然后按照它的提示操作,进入自动整定,接着等待,完成后按右键确认。
(费希尔)定位器操作说明
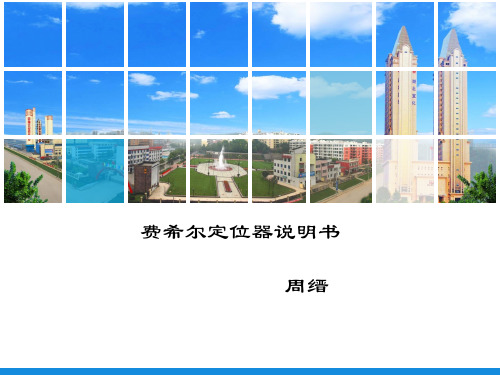
周缙
费希尔定位器说明书
周缙
型号:3620J
基本介绍:Fisher 3620J 电动气动单作 用定位器可与旋转式执行机构配合使 用,并精确定位节流应用中使用的控 制阀。
*
一、说明书 安装及内部结构
挡 板
*
一、调校步骤
1.将定位器按上图所示安装完毕,接通气源。
2.用校验仪给定位器输入4mA电流信号,调节调零螺钉,使定位器 输出气压为0。并输入5mA电流信号,查看定位器是否有气压输 出,阀门是否有动作。通过检查5mA信号阀门动作情况,检查 零位调节是否准确。 3.用校验仪分别输入8mA、 12mA、 16mA、 20mA检查定位器气压 输出情况和阀门动作情况。假若电流输出与阀门动作情况不一 致(输入信号还未达到20mA,定位器输出气压已最大,阀门动 作已达到量程最大值,说明定位器量程太短。输入信号已超过 20mA,例如21mA,定位器输出气压还未最大,阀门动作还未达 到量程做大值,说明定位器量程太大。)此时,应该旋转量程 微调螺钉,调整量程。 4.调完量程螺钉后,反过来重复第2步再次检查零位。 5.确定零位正常后,重复第3步,检查量程调整是否到位。若不到 位继续重复第2、3步骤。
*
二、应急处理方法
1. 若定位器输入电流信号无反应,手动按下挡板使定位器输出气压。
2.若手动按下挡板定位器扔无反应则用塑料气源管从调节阀的减压 阀出口接气源直接给阀门膜头通气,利用减压阀调节气源压力可对 调节阀进行适当的开度调节。
*
FISHER费希尔定位器调试说明书
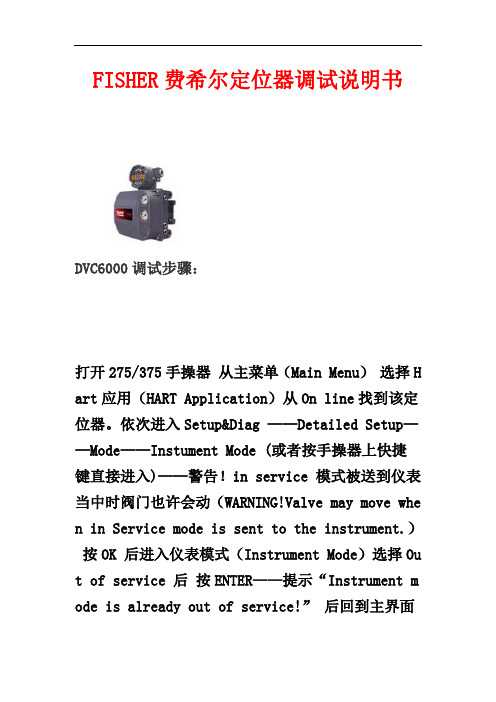
FISHER费希尔定位器调试说明书DVC6000调试步骤:打开275/375手操器从主菜单(Main Menu)选择H art应用(HART Application)从On line找到该定位器。
依次进入Setup&Diag ——Detailed Setup——Mode——Instument Mode (或者按手操器上快捷键直接进入)——警告!in service 模式被送到仪表当中时阀门也许会动(WARNING!Valve may move whe n in Service mode is sent to the instrument.)按OK 后进入仪表模式(Instrument Mode)选择Ou t of service 后按ENTER——提示“Instrument m ode is already out of service!”后回到主界面依次进入 Setup&Diag——Basic Setup——Auto se tup——Setup Wizard:1、选择你所使用的压力单位(Pressure units (psi))后ENTER ;2、输入供气压力(Max Supply Press (psi))后EN TER;3、选择执行机构的生产厂家(Actuator Manufcture)后ENTER 以上品牌没的话选OTHER ;4、如果执行机构单作用带弹簧选3 、双作用带弹簧选4 、双作用不带弹簧选2;5、选ROTARY 下一步根据阀门零信号时是开选2 关的话选1 下一步再选1 下一步选YES自动选择阀门转向及其增益大小;6、选择是否有加速器或者快速释放阀(Is a Volume Booster or Quick Release Present ? );7、提示执行机构的信息正被发送到仪表当中,请稍等“Actuator information is being sent to the instrument. Please wait…”;8、选择使用出厂默认设置Use Factory defaults f or setup?(Yes is recommended for Initial Setu p) Yes 后ENTER ;9、提示出厂默认设置正被发送到仪表当中,请稍等“Factory default are being sent to the inst rument. Please wait…”;10、继续自动设置选择放大器调整“To continue A uto Setup.selec Relay Adjust ”;11、你是否希望现在进行放大器调整?(Do you wish to run Relay Adjustment Calibration now ?) 假如是双作用选择Yes 单作用选择No后ENTER ;12、选择行程标定(To continue.selec Auto Calib Travel.)按OK;13、你希望现在进行自动行程标定吗?(Do you wi sh to run Auto Travel Calib now ?selec YES if initial setup)选择Yes 后按 ENTER;14、警告!标定将导致仪表的输出突然变化按 OK;15、选择交点的调整(selec Crossover Adjust)Ma nual/Last Value/Default 正常情况下选择 defaul t 后 ENTER 假如默认的调整后精度比较差才会选择Manual手动;16、下面进入自动行程标定的过程,完成后仪表模式恢复到In service!。
FISHER智能定位器自动调教方法
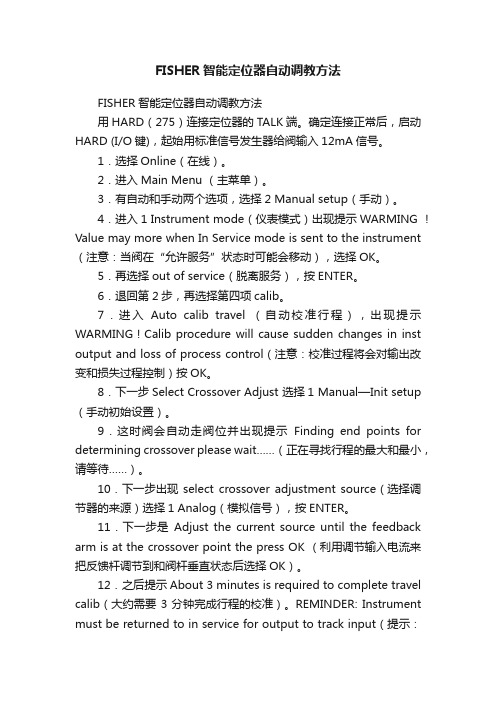
FISHER智能定位器自动调教方法FISHER智能定位器自动调教方法用HARD(275)连接定位器的TALK端。
确定连接正常后,启动HARD (I/O键),起始用标准信号发生器给阀输入12mA信号。
1.选择Online(在线)。
2.进入Main Menu (主菜单)。
3.有自动和手动两个选项,选择2 Manual setup(手动)。
4.进入1 Instrument mode(仪表模式)出现提示WARMING !Value may more when In Service mode is sent to the instrument (注意:当阀在“允许服务”状态时可能会移动),选择OK。
5.再选择out of service(脱离服务),按ENTER。
6.退回第2步,再选择第四项calib。
7.进入Auto calib travel (自动校准行程),出现提示WARMING!Calib procedure will cause sudden changes in inst output and loss of process control(注意:校准过程将会对输出改变和损失过程控制)按OK。
8.下一步Select Crossover Adjust 选择1 Manual—Init setup (手动初始设置)。
9.这时阀会自动走阀位并出现提示Finding end points for determining crossover please wait……(正在寻找行程的最大和最小,请等待……)。
10.下一步出现select crossover adjustment source(选择调节器的来源)选择1 Analog(模拟信号),按ENTER。
11.下一步是Adjust the current source until the feedback arm is at the crossover point the press OK (利用调节输入电流来把反馈杆调节到和阀杆垂直状态后选择OK)。
费希尔定位器操作说明
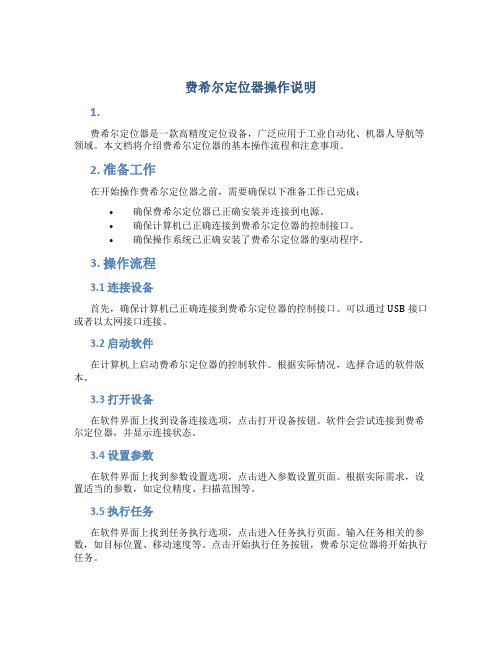
费希尔定位器操作说明1.费希尔定位器是一款高精度定位设备,广泛应用于工业自动化、机器人导航等领域。
本文档将介绍费希尔定位器的基本操作流程和注意事项。
2. 准备工作在开始操作费希尔定位器之前,需要确保以下准备工作已完成:•确保费希尔定位器已正确安装并连接到电源。
•确保计算机已正确连接到费希尔定位器的控制接口。
•确保操作系统已正确安装了费希尔定位器的驱动程序。
3. 操作流程3.1 连接设备首先,确保计算机已正确连接到费希尔定位器的控制接口。
可以通过USB接口或者以太网接口连接。
3.2 启动软件在计算机上启动费希尔定位器的控制软件。
根据实际情况,选择合适的软件版本。
3.3 打开设备在软件界面上找到设备连接选项,点击打开设备按钮。
软件会尝试连接到费希尔定位器,并显示连接状态。
3.4 设置参数在软件界面上找到参数设置选项,点击进入参数设置页面。
根据实际需求,设置适当的参数,如定位精度、扫描范围等。
3.5 执行任务在软件界面上找到任务执行选项,点击进入任务执行页面。
输入任务相关的参数,如目标位置、移动速度等。
点击开始执行任务按钮,费希尔定位器将开始执行任务。
3.6 监控定位结果在执行任务过程中,可以通过软件界面上的监控选项,实时监控费希尔定位器的定位结果。
根据实际需求,可以选择显示位置、速度、加速度等参数。
3.7 结束任务任务执行完成后,点击结束任务按钮,费希尔定位器将停止任务并返回到初始位置。
4. 注意事项•在操作费希尔定位器之前,请确保已经完全理解并掌握相关安全操作规程,以避免潜在的危险。
•在操作费希尔定位器过程中,应注意避免突然停止或者快速启动,避免对设备造成损坏。
•在操作费希尔定位器过程中,应注意避免碰撞或者强烈震动,避免影响设备的定位精度。
•在操作费希尔定位器过程中,应随时注意监控设备的状态,如温度、电源、通信等,确保设备正常运行。
5.本文档介绍了费希尔定位器的基本操作流程和注意事项。
通过正确的操作和合理的使用,可以充分发挥费希尔定位器的定位能力,提高工作效率和精度。
FISHER_DVC6000定位器调试说明
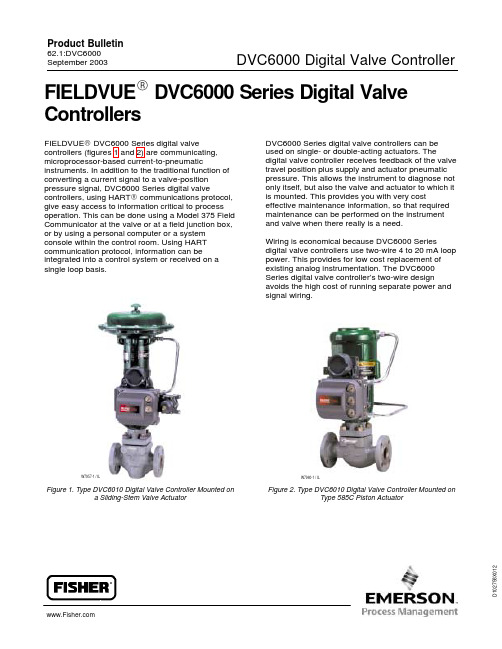
D 102758X 012FIELDVUE R DVC6000 Series Digital ValveControllersFIELDVUE RDVC6000 Series digital valvecontrollers (figures 1 and 2) are communicating,microprocessor-based current-to-pneumaticinstruments. In addition to the traditional function of converting a current signal to a valve-position pressure signal, DVC6000 Series digital valvecontrollers, using HART R communications protocol,give easy access to information critical to process operation. This can be done using a Model 375 Field Communicator at the valve or at a field junction box,or by using a personal computer or a system console within the control room. Using HART communication protocol, information can be integrated into a control system or received on a single loop basis.W7957-1 / ILFigure 1. Type DVC6010 Digital Valve Controller Mounted ona Sliding-Stem Valve Actuator DVC6000 Series digital valve controllers can be used on single- or double-acting actuators. Thedigital valve controller receives feedback of the valve travel position plus supply and actuator pneumatic pressure. This allows the instrument to diagnose not only itself, but also the valve and actuator to which it is mounted. This provides you with very costeffective maintenance information, so that required maintenance can be performed on the instrument and valve when there really is a need.Wiring is economical because DVC6000 Seriesdigital valve controllers use two-wire 4 to 20 mA loop power. This provides for low cost replacement of existing analog instrumentation. The DVC6000Series digital valve controller’s two-wire designavoids the high cost of running separate power and signal wiring.W7960-1 / ILFigure 2. Type DVC6010 Digital Valve Controller Mounted onType 585C Piston Actuator(continued) 2actuator has been tested to 15 meters (50 feet) maximum without performance degradation.2. These terms are defined in ISA Standard S51.1.3. Normal m3/hr--Normal cubic meters per hour at 0_C and 1.01325 bar, absolute; Scfh--Standard cubic feet per hour at 60_F and 14.7 psia.4. Values at 1.4 bar (20 psig) based on a single-acting direct relay; values at5.5 bar (80 psig) based on double-acting relay.5. Not applicable for Type DVC6020 digital valve controllers in long-stroke applications or remote-mounted Type DVC6005 digital valve controllers with long pneumatic tubing lengths.6. Approvals for remote-mounted units are pending.7. The Low Bleed Relay is offered as standard relay for DVC6000 ESD tier, used for On/Off applications.FeaturesD Improved Control—Two-way digital communications give you current valve conditions. You can rely on this real-time information to make sound process management decisions. By analyzing valve dynamics through AMS ValveLink Software , you can identify control areas needing improvement and maintain a high level of system performance. D Environmental Protection—You can avoid additional field wiring by connecting a leak detector or limit switch to the auxiliary terminals in theDVC6000 Series digital valve controller. In this way, the instrument will issue an alert if limits are exceeded.34D Enhanced Safety—You can check instrumentand valve operation and keep the process running smoothly and safely from a remote location. Access is possible at a field junction box, marshalling panel, or within the safety of the control room using either a 375 Field Communicator, a notebook PC, or a system workstation. Your exposure to hazardous environments is minimized and you can avoid having to access hard-to-reach valve locations.D Hardware Savings—DVC6000 Series digital valve controllers, when used in an integrated system, allow you to realize significant hardware and installation cost savings by replacing other devices in the process loop, such as positioners and limit switches, with a FIELDVUE digital valve controller.D Built to Survive—Field-tough DVC6000 Series digital valve controllers have fully encapsulated printed wiring boards that resist the effects of vibration, temperature, and corrosive atmospheres.A separate weather-tight field wiring terminal box isolates field-wiring connections from other areas of the instrument.D Increased Uptime—With the self-diagnostic capability of DVC6000 Series digital valve controllers, you can answer questions about a valve’s performance, without pulling the valve from the line. You can run diagnostics (I/P and relay integrity, travel deviation, and on-line friction and deadband analysis and trending) while the valve is in service and operating. You can also compare the present valve/actuator signature (bench set, seat load, friction, etc.) against previously stored signatures to discover performance changes, before they cause process control problems.D Faster Commissioning—The two-way communication capability allows you to quickly commission loops by remotely identifying each instrument, verifying its calibration, reviewing stored maintenance notes, and more.D Easy Maintenance—DVC6000 Series digital valve controllers are modular in design. The single master module can be removed from the instrument housing without disconnecting the field wiring, pneumatic connections or stem linkages. This module contains the critical sub-modules so component removal is quick and simple.DiagnosticsDVC6000 Series digital valve controllers are packed with user-configurable alerts and alarms. When integrated with a HART communication-based system, these flags provide real-time notification of current and potential valve and instrument problems. With AMS ValveLink R Software, tests can be performed to identify problems with the entire control valve assembly. Diagnostic capabilities available are Performance Diagnostics (PD) and Advanced Diagnostics (AD).Performance DiagnosticsPerformance Diagnostics enables the use of diagnostics while the valve is in service and operating.D Red/Yellow/Green Condition Indicator(see figure 3)D I/P and Relay Integrity DiagnosticD Travel Deviation DiagnosticD1-Button DiagnosticD On-Line Friction and Deadband Analysis(see figure 4)D Friction and Deadband TrendingWhile all diagnostics can be run while the valve is inline, only the Performance Diagnostics can be performed while the valve is in service and operating.5ERROR(RED)NO CONDITIONS HAVE BEEN DETECTED(GREEN)Figure 3. Red/Yellow/Green Condition Indicators, Shown in AMS ValveLink SoftwareFigure 4. Valve Friction and Deadband AnalysisAdvanced DiagnosticsAdvanced Diagnostics include the following dynamic scan tests:D Valve Signature (see figure 6)D Dynamic Error Band D Instrument Drive SignalThese diagnostic scans vary the positioner set point at a controlled rate and plot valve operation to determine valve dynamic performance. The valve signature test allows you to determine thevalve/actuator friction, bench set, spring rate, and seat load. The Dynamic Error Band test is a combination of hysteresis and deadband plus “slewing.” Hysteresis and deadband are static measurements. However, because the valve is moving, a dynamic error, or “slewing” error is introduced.Dynamic scan tests give a better indication of how the valve will operate under process conditions which are dynamic, not static.The Step Response Test checks the valveassemblies response to a changing input signal. and plots travel versus time. The end results of this test allow you to evaluate the dynamic performance of the valve. The Performance Step Test (25pre-configured points) provides a standardized step test with which to evaluate your valve performance.It utilizes small, medium and large changes.Advanced Diagnostics are performed with AMS ValveLink Software . The valve must be out ofservice for Advanced Diagnostics to be performed.6W8082 / ILHART MULTIPLEXERControl System I/O4-20 mA+HARTFigure 5. Integrate Information from the Digital Valve Controller into a Non-HART Compatible Control System With AMS ValveLinkSoftware’s Modbus InterfaceW7468/ILFigure 6. The Valve Signature DisplayIntegrationD Non-HART Systems—Because DVC6000Series digital valve controllers operate with atraditional 4 to 20 mA control signal, they directlyreplace older analog instruments.Microprocessor-based electronics provide improvedperformance along with repeatable and reliableconfiguration and calibration.D Modbus with AMS ValveLink Software andHART Multiplexers—HART communication allowsyou to extract more value from DVC6000 Seriesdigital valve controllers beyond their inherentimproved performance. When integrated into amultiplexer network and using AMS ValveLinkSoftware, the device and valve information isreal-time. From the safety of a control room, multipleinstruments can be monitored for alerts and alarms.Additionally, tasks such as configuration, calibrationand diagnostic testing do not require special trips tothe field. AMS ValveLink Software can communicatevia Modbus to the distributed control system (DCS)to provide critical information such as valve travelalerts and alarms (figure 5).D Integrated Control System—A control systemwith HART communication capabilities has the abilityto directly gather information from DVC6000 Seriesdigital valve controllers. Information such as valvetravel, alerts and alarms can be seamlesslyaccessed to provide a view into the field device fromthe safety of the control room.71200 Hz “1”2200 Hz “0”AVERAGE CURRENT CHANGE DURING COMMUNICATION = 0A6174/ILFigure 7. HART rFrequency Shift Keying TechniqueFigure 8. Perform Configuration and Calibration at the Valve or Anywhere on the 4 to 20 mA Loop with the Model 375Field CommunicatorCommunicationHART Protocol OverviewThe HART (Highway Addressable Remote Transducer) protocol gives field devices thecapability of communicating instrument and process data digitally. This digital communication occurs over the same two-wire loop that provides the 4 to 20 mA process control signal, without disrupting the process signal (figure 7). In this way, the analog process signal, with its faster response, can be used for control. At the same time, the HART digital communication gives access to calibration,configuration, diagnostic, maintenance, andadditional process data. The protocol provides total system integration via a host device.Model 375 Field CommunicatorYou can perform configuration and calibration at the valve or anywhere on the two-wire loop via a Model 375 Field Communicator (figure 8). Powerful tools such as the Setup Wizard and Auto TravelCalibration automate the tasks of commissioning DVC6000 Series digital valve controllers. Theseautomation tools not only save time, but also provide accurate and repeatable results.AMS ValveLink SoftwareAMS ValveLink Software is a Windows-based software package that allows easy access to the information available from DVC6000 Series digital valve controllers.Using AMS ValveLink Software, you can monitor the performance characteristics of the valve and obtain vital information without having to pull the valve from the line. I/P and Relay Integrity and Travel Deviation Diagnostics, as well as On-Line Friction andDeadband Analysis and Trending can be run while the valve is in service and operating. ValveSignature, Dynamic Error Band, and Step Response are displayed in an intuitive user-friendlyenvironment that allows easy interpretation of data.Diagnostic graphs can be superimposed over those previously stored to view areas of valve degradation.This allows plant personnel to concentrate efforts on equipment that needs repair, avoiding unnecessary maintenance. This diagnostic capability is readily accessible and available to you either in the control room or on the plant floor. In addition to the diagnostic features, AMS ValveLink Softwarecontains an Audit Trail, Batch Runner for automating repetitive tasks, and Trending to view valve performance.AMS ValveLink Software provides integration into AMS and DeltaV, with HART and Fieldbus communications.TRAVEL SENSORTERMINAL BOXTERMINAL BOX COVERPRINTED WIRING BOARD ASSEMBLYI/P CONVERTERPNEUMATIC RELAYGAUGESCOVERW8083-1 / ILFigure 9. DVC6000 Series Digital Valve Controller Assembly (valve-mounted instrument)Principle of OperationDVC6000 Series instruments (figures 9 and 10) receive a set point and position the valve where it needs to be.D The input signal provides electrical power and the set point simultaneously. It is routed into the terminal box through a twisted pair of wires.D The input signal is then directed to the printed wiring board assembly where the microprocessor runs a digital control algorithm resulting in a drive signal to the I/P converter.D The I/P converter assembly is connected to supply pressure and converts the drive signal into a pressure output signal.D The I/P output is sent to the pneumatic relay assembly. The relay is also connected to supply pressure and amplifies the small pneumatic signal from the I/P converter into a single larger pneumatic output signal used by a single-acting actuator. For double-acting actuators, the relay accepts the pneumatic signal from the I/P converter and provides two pneumatic output signals.D The change in relay output pressure to the actuator causes the valve to move.D Valve position is sensed through the feedback linkage by the instrument’s travel sensor. The travel sensor is electrically connected to the printed wiring board to provide a travel feedback signal used in the control algorithm.The valve continues to move until the correct position is attained.8E0408 / ILFigure 10. DVC6000 Series Digital Valve Controller Block DiagramInstallationThe Type DVC6010 digital valve controller is designed for yoke mounting to sliding stem actuators. Type DVC6020 digital valve controllers are designed for mounting to rotary actuators or long stroke sliding stem actuators (over 4-inches travel). Type DVC6030 digital valve controllers are designed for mounting on virtually any quarter-turn actuator. Dimensions for valve-mounted instruments are shown in figures 11, 12, and 13. Dimensions for remote-mounted instruments are shown in figures 14 and 15.The Type DVC6005 digital valve controller base unit may be remote mounted on 2-inch pipestand or wall. The remote-mounted Type DVC6005 base unit connects to the Type DVC6015, DVC6025, orDVC6035 feedback unit mounted on the actuator. Feedback wiring and pneumatic tubing to the control valve assembly must be connected in the field.9102 MOUNTING HOLES 8.6 (0.34)1/4-18 NPTOUTPUT CONN B28.6(1.13)122.8(4.84)144.5(5.69)210.7(8.29)148.7(5.85)ACTUATOR CENTERLINE1/4-18 NPTOUTPUT CONN PLUGGED1/2-14 NPTCONDUIT CONN BOTH SIDES 1/4-18 NPTOUTPUT CONN A 1/4-18 NPT VENT CONNTYPE 67CFR 1/4-18 NPTSUPPLY CONNFigure 11. Dimensions for Type DVC6010 Digital Valve Controller with Integrally Mounted Filter Regulator4 MOUNTING HOLES j 95.3(3.75)158.1(6.23)156.3(6.16)1/2-14 NPTCONDUIT CONN BOTH SIDES 1/4-18 NPTOUTPUT CONN A TYPE 67CFR 1/4-18 NPTSUPPLY CONN19B3557-A E0406 / ILmm(INCH)Figure 12. Dimensions for Type DVC6020 Digital Valve Controller with Integrally Mounted Filter Regulator19B3558-A E0407 / ILmm (INCH)Figure 13. Dimensions for Type DVC6030 Digital Valve Controller with Integrally Mounted Filter Regulator11PIPESTAND MOUNTED10C1795-A / DOC10C1796-A / DOC234184mm (INCH)WALL MOUNTED64(2.50)57(2.25)72(2.82)HOLES 0.86 (0.34)Figure 14. Dimensions for Remote-Mounted Instruments--Type DVC6005 Base UnitThe digital valve controllers are 4 to 20 mA loop powered and do not require additional power.Electrical connections are made in the terminal box.All pressure connections on the digital valvecontrollers are 1/4-inch NPT female connections.The digital valve controller outputs are typically connected to the actuator inputs using 3/8-inch diameter tubing. Remote venting is available.Ordering InformationNote: Fisher does not assume responsibility for the selection, use, or maintenance of anyproduct. Responsibility for proper selection, use,and maintenance of any Fisher product remains solely with the purchaser and end user.When ordering, specify:1. Actuator type and size2. Maximum actuator travel or rotation3. Optionsa. Supply pressure regulatorb. Supply and output gaugesc. HART filterd. Stainless steel housing (valve-mounted instruments only)e. Remote mountingTYPE DVC6015 SLIDING STEM ACTUATOR MOUNTINGUP TO 102 mm (4−INCH) TRAVEL TYPE DVC6025 ROTARY AND LONG−STROKE SLIDING STEMACTUATOR MOUNTINGE0867 / IL10C1799-AE0869 / ILTYPE DVC6035 ROTARY ACTUATOR SHAFT MOUNTING10C1798-A E0868 / ILmm (INCH)(4.50)(3.00)38(1.50)HOLES1/4 - 20 UNC46(1.83)46(1.81)67103135120CONDUIT CONNFigure 15. Dimensions for Remote-Mounted Instruments--Feedback UnitsFisherMarshalltown, Iowa 50158 USA Cernay 68700 France Sao Paulo 05424 Brazil Singapore 128461The contents of this publication are presented for informational purposes only, and while every effort has been made to ensure their accuracy,they are not to be construed as warranties or guarantees, express or implied, regarding the products or services described herein or their use or applicability. We reserve the right to modify or improve the designs or specifications of such products at any time without notice.Fisher does not assume responsibility for the selection, use or maintenance of any product. Responsibility for proper selection, use and maintenance of any Fisher product remains solely with the purchaser and end-user.FIELDVUE, ValveLink and Fisher are marks owned by Fisher Controls International LLC, a business of Emerson Process Management. The Emerson logo is a trademark and service mark of Emerson Electric Co. HART is a mark owned by the HART Communications Foundation.All other marks are the property of their respective owners. This product may be covered under one or more of the following patents (5,451,923; 5,434,774; 5,439,021; 5,265,637) or under pending patent applications.Emerson Process Management 。
美国Fisher公司G-3000磁场定位器产品说明书
G-3000 Transmitter features1 On/Off buttonPress and hold to reduce speaker volume.2 Direct Connection socket3 Loudspeaker4 Battery compartment To replace batteries, open the access cover using a screwdriver or coin. Use four LR20 or D alkaline batteries.5 Storage compartment Holding Connection Cable and Ground Stake.Locating with the R-3000 and G-3000The G-3000 is used to apply a tone to a buried conductor. This signal can be traced using the R-3000 locator switched to the G-3000 mode.Direct connectionDirect connection is the most effective form of signal application and is suitable for connection to a valve,meter, junction box or other access point.WARNINGConnection to a power cable sheath should only be undertaken by qualified personnel.MethodPlug the Connection lead into the G-3000 connection socket and attach the red lead to the target line. Ifnecessary clean the connection point to ensure a good electrical contact.Clip the ground lead to the earth stake which should be placed in the ground 3 to 4 paces away from, and at right angles to the target line.Alternatively the ground lead may be clipped to the rim of a valve box or manhole cover. Use the spool lead to extend the earth connection if necessary.Switch the G-3000 on. A good connection is indicated by a drop in loudspeaker tone. if there is no tone or it is a very slow bleep, replace the batteries.Switch the R-3000 to G-3000 mode and begin to trace the line from the point of application. Pinpoint using the same method as described for Power and Radio modes.When directly over the conductor and with the sensitivity level set for a narrow response, rotate the R-3000 on its axis until the signal minimum isfound. The blade is now in line with the conductor.Trace the conductor out of the area, marking the position as required with chalk or paint Radio modeFor detection of radio signals originating from distant radio transmitters. These penetrate the ground and are re-radiated by buried conductors. However, they are not always present.After completion of Power mode sweep, repeat the procedure with Radio mode selected.WARNINGThe R-3000 will detect almost all buried conductors but there are some which do not radiate any signal which the R-3000 will not detect.There are also some live power cables which the R-3000 is not able to detect in he Power mode.The R-3000 does not indicate whether a signal is from a single cable or from several in close proximity.NoteThe R-3000 will not provide depth information in either the Power or Radio modes.Liquid crystal displayR-3000 Locator features1 On/OffPress and hold to use R-30002 LoudspeakerTo use in noisy environments unscrew and hold to ear.3 Sensitivity control 4 Function switch Selects locate mode:Power, Radio, G-30005 Battery compartmentTo replace batteries, open theaccess cover using a screwdriver orcoin. Use eight LR6 or AA alkaline batteries.AT-3000 User guideThe R-3000 and G-3000 combine to make the perfect general purpose tools for cable avoidance. Their rugged construction ensures long life and reliability whilst the simple controls promote effective use with minimal training.For those who require pinpoint accuracy and depth information, the AT-3000 add visual indiction of signal strength together with a buried utility depth measurement capability.5341252134mDepthMode/clockface Signal strength Depth buttonOperation of Power and Radio modesRegularly check your R-3000 and G-3000 in all modes,over a cable which gives a response you are familiar with.Power modeFor detection of ‘Power’signals radiated by loaded cables. These are often found ‘re-radiated’by other,nearby conductors. Select Power using the Function switch. Press and hold the On/Off switch. Replace batteries if no initial ‘bleep’is heard to confirm good battery condition.Rotate the Sensitivity Control fully clockwise formaximum sensitivity but reduce if there is a blanket signal across the site.Define the area to be excavated and carry out a grid pattern sweep.Sweep holding the R-3000 upright and at your side.Continue the sweep beyond the perimeter of the area to be excavated.AMPROBE1-305-423-7500®The presence of a buried conducting pipe or cable will be indicated by a tone emitted from the loudspeaker.Keep the blade of the R-3000 vertical and move slowly backwards and forwards over the conductor, reducing the sensitivity for a narrower response. With the R-3000use the meter deflection to aid pinpointing. Maximum meter deflection will indicate the position of the conductor.Optional AccessoriesUsing the optional* Signal Clamp SC-3000The Signal Clamp applies a G-3000 signal safely to a pipe or live cable of up to 76mm (3 inches) diameter,without interrupting the supply.MethodPlug the Clamp into the G-3000 Connection socket.Place the Clamp around the pipe or cable ensuring the jaws are closed. Switch the G-3000 on. Open and close the Clamp. If the jaws are closing correctly a drop in speaker tone will be heard.An earth connection is not necessary but efficientsignal transfer is only achieved if the target conductor is grounded at both ends. This is usually the case with power cables.InductionInduction is a convenient and quick way of applying the G-3000 signal to a pipe or cable where limited access does not permit direct connection or use of the Signal Clamp.Place the G-3000 over the assumed position of the conductor in the orientation shown.Start tracing the cable or pipe at least five paces from the G-3000 with the R-3000 in G-3000 mode. Working too close to the G-3000 may give false readings as the R-3000 will detect more signal directly from the G-3000than from the conductor.Do not attempt to take depth readings unless the distance between the R-3000 and G-3000 is greater than 30 paces (see “Taking depth readings using the R-3000”).Active search using Induction Placing the G-3000 on its side swamps an area with G-3000 signal.Alternatively, use a two man technique to search an area for buried utilities.Taking line depth measurement using the R-3000Depth measurement is only possible when using the R-3000 in the G-3000 mode.MethodLocate the utility as described previously.Ensure that thedepth measurement position is at least 30 paces from the G-3000, especially if signal application is by Induction method.Hold the R-3000 still,vertical and at right angles to the buried line.Momentarily depress the depth button. The display will show a moving clock face followed by the depth measurement.Taking Mouse depth measurements using the R-3000Depth measurement is only possible when using the R-3000 in the G-3000 mode with a Mouse transmitter.MethodLocate the main Mouse signal as previously described.Hold the R-3000 vertically and in line with the Mouse.Press and hold the depth button until ‘M’appears on the display. A clock face will appear in the top right hand corner of the display while the depth calculation is made. The approximate depth to the Mouse will then be displayed on the meter.R-3000 error codesIndicates very shallow conductor Indicates conductor out of range Indicates depth measurement attempted in R or P mode which is not available.WARNINGDo not use the R-3000 depth measurement to decide if mechanical digging over buried conductor is appropriate.ddm in 30 p a c e sr e c o mm e n d e dUsing the optional* Mouse Signal Transmitter M-3000The mouse is a small self-contained watertighttransmitter which can be detected by the R-3000 when switched to the G-3000 mode.MethodReplace the battery in the Mouse. Attach the Mouse to a drain rod using an appropriate connector.Place the Mouse on the ground, set the R-3000 to G-3000 mode and, whilst holding the R-3000 in line with the Mouse, check that a signal is being received.Insert the Mouse approximately 1m/yd into theduct/drain and adjust the R-3000 sensitivity to receive the signal.A ghost signal appears before and behind the main signal position. Reduce the R-3000 sensitivity to receive only the main signal.PeakGhostGhostReplacementsConnection Kit CK-3000(Includes connection cable and ground stake)AmprobeTel: 305 423 7500Fax:305 423 7554Technical Support:800 327 506090/NUG01AMP/0 11.00。
fisher智能定位器的安装及调试
选择 manual
接着出现选择调整信号原的选择,有 analog 和 digital,选择 analog。
出现调整反馈臂与阀杆成 90°(也就是调节反馈臂水平)的提 示,此时调节输入信号使反馈臂与阀杆成 90°(见图 3-1),调
回车后接下来阀会自动调节知道完成,之后会出现一个是否把阀 投到“in service” 状态的提示。此时就把表投到“in service” 状态,设置和调试完成。
4
图 2-4 SS-roller
图 2-5 SStem-Standard
完成以上设置后可按“send”发送,之后可进行下面的调校工作。
5
三、调校
1-2-4-3 Auto Calib Travel
Ok?
abort
enter
Ok? enter
abort
出现调整反馈臂和阀杆 交叉点的方式选择菜单, manual, last value, 或 default.
3、Test
TV-2603 ☆
☆
注释 在改变仪表设置 和调校之前必须 把 模 式 设 为 in service 状态 仪表的控制模 式,我们的一般 为模拟信号-
Analog
1-1-2-3
Press & Actuator
见表 2-2
1-1-2-4
Tuning & Calib
1、Tuning Set
2、Relay Adjust 3 、 Auto Calib Travel
2
图 2-3 定位器与手操器通讯画面
4、下面以位号 TV-2603 为例,说明设置和调校过程。
快捷键 1-1-2-1
菜单名 Instrument Mode
1-1-2-2
(费希尔)定位器操作说明PPT课件
位继续重复第2、3步骤。
.
4
*
二、应急处理方法
1. 若定位器输入电流信号无反应,手动按下挡板使定位器输出气压。
2.若手动按下挡板定位器扔无反应则用塑料气源管从调节阀的减压 阀出口接气源直接给阀门膜头通气,利用减压阀调节气源压力可对 调节阀进行适当的开度调节。
.
5
*
费希尔定位器说明书 周缙
.
1பைடு நூலகம்
费希尔定位器说明书
周缙
型号:3620J
基本介绍:Fisher 3620J 电动气动单作 用定位器可与旋转式执行机构配合使 用,并精确定位节流应用中使用的控 制阀。
.
2
*
一、说明书 安装及内部结构
挡 板
.
3
*
一、调校步骤
1.将定位器按上图所示安装完毕,接通气源。
2.用校验仪给定位器输入4mA电流信号,调节调零螺钉,使定位器 输出气压为0。并输入5mA电流信号,查看定位器是否有气压输 出,阀门是否有动作。通过检查5mA信号阀门动作情况,检查 零位调节是否准确。
3.用校验仪分别输入8mA、 12mA、 16mA、 20mA检查定位器气压 输出情况和阀门动作情况。假若电流输出与阀门动作情况不一 致(输入信号还未达到20mA,定位器输出气压已最大,阀门动 作已达到量程最大值,说明定位器量程太短。输入信号已超过 20mA,例如21mA,定位器输出气压还未最大,阀门动作还未达 到量程做大值,说明定位器量程太大。)此时,应该旋转量程 微调螺钉,调整量程。
Fisher定位器中文版
定位器磁条安装Hall EffectSensorin DVCMagneticArrayOn ValveStem白色线条区间是有效感应区,白色区间距离要大于阀门实际行程,但不能大于实际行程的200%。
定位器内置霍尔线圈,位于定位器中间,用于感应磁条位置气开阀时,磁条上面白线对准定位器霍尔线圈气关阀时,磁条下面白线对准定位器霍尔线圈阀门在50%位置时磁条位置转行程磁条安装,确保阀门在50%开度时转行程的两个平面(贴白色标签的一面,是平面)与定位器背面的槽平行,如中间图示位置。
DVC6200 HART 调试步骤点现场通讯器点HART点组态,选择guild setup如果是以前没有调试过得定位器,点device setup,如果是已经标定过得定位器,还需重新校验的话点auto calibration。
如是新定位器,点device setup 之后跳出界面,把仪表模式设置为out of service选择压力单位,可选任一单位然后选择定位器放大器类型(拆开定位器盖子,relay上会写是哪种relay)一般选择A or C选择定位器控制方式travel control 行程控制Pressure control 压力控制Fallback-sensor failure 行程传感器失效,定位器切换到压力控制模式,当行程传感器恢复后,定位器自动切换到行程控制模式Fallback-sensor failure/Tvl deviation 行程传感器失效或行程偏差超过设定时,定位器切换到压力控制模式,当行程传感器恢复后,定位器自动切换到行程控制模式一般选择travel control输入最大压力,输入数值和仪表气减压阀后的压力值相同就行,假如减压阀设定到2.5bar,你就输入2.5bar。
选执行机构型号,如果是Fisher,选择Fisher这一选项,按照执行机构铭牌填写型号尺寸。
如果是其他品牌执行机构则点other,然后根据现场实际的情况选择执行机构类型分4种:Spring and diaphragm 弹簧膜片式Piston single with spring 活塞单作用带弹簧Piston double with spring活塞双作用带弹簧Piston double without spring 活塞双作用不带弹簧然后选择zero power condition:valve closed 气开阀Valve open 气关阀气路上有无放大器所有设置完后,发送到定位器里,点击send选Yes,点确定设置完成后,点确定进行自动校验,点确定点auto calibration点continue进入自动标定过程,找高点找低点找中间点行程标定完成后,进入压力标定过程压力标定完成后,标定过程结束,点确定。
- 1、下载文档前请自行甄别文档内容的完整性,平台不提供额外的编辑、内容补充、找答案等附加服务。
- 2、"仅部分预览"的文档,不可在线预览部分如存在完整性等问题,可反馈申请退款(可完整预览的文档不适用该条件!)。
- 3、如文档侵犯您的权益,请联系客服反馈,我们会尽快为您处理(人工客服工作时间:9:00-18:30)。
Fisher定位器使用说明书
一、Fisher定位器调校基本步骤
1.将375手操器连接到接线端子上,进入菜单
选择 Setup(设置)→Basic setup(基本设置)→Auto setup(自动设
置)→Setup wizard(设置向导)
2.根据Setup wizard的提示选择相应的参数
⑴instrument mode is in service ,continue for prompts to please
out of service.
仪表模式是在线状态,继续须要准时设置为离线状态
选择 Yes.
⑵output will not track input when instrument mode is out of
service.
当仪表在离线状态时,仪表的输出将不随输入的变化而变化
选择Yes.
⑶change to out of service to continue.
继续需改变为离线模式
选择out of service
选择enter
说明:仪表正常工作时其模式为in service状态,当对仪表进行调
校时需改为out of service状态。
⑷Tru/Press select 行程/压力选择
选择Travel control
⑸Pressure units 压力单位
选择psi
⑹Max supply press 最大供气压力
此时输入的最大供气压力值应与空气过滤减压阀的输出压力一致,此
值不宜过大,过大,阀门易损坏,超行程。
应调整空气过滤减压阀使
阀门刚好全行程,这时输入此时的压力值。
⑺Actuator manufacturer 执行机构制造商
选择Fisher controls
⑻Actuator model 执行机构型号
查看阀体上的铭牌,有此执行机构型号,选择相应型号,如667,1035,
1051等。
⑼Actuator size 执行机构尺寸
查看阀体上的铭牌,有此执行机构尺寸,选择相应尺寸,如30,34,
40,45,50,46,60,70,100等。
⑽setup wizard is ready to send config to the Drc6000
选择send
⑾use factory default 使用工厂默认,选择Yes.
⑿To finish setting up the value run Auto Travel Calib 完成阀门设置运行自动行程调校,选择OK.
⒀Warning! Calibration will cause sudden changes in instrument output , continue?
警告!调校将造成仪表输出突然改变,是否继续?选择Yes.
⒁select crossover adjust 选择交叉点调整
Ⅰ.Manual 手动
Ⅱ.Last vale 上一次值
Ⅲ.Default 默认值(缺省值)
如果是初次校验行程,推荐选择Manual调整,选择Enter.
⒂仪表开始自动行程校验
校验结束后,将提示把仪表设置到in service状态。
说明:
在调试仪表前应先调整交叉点。
即DCS给定位器50%的信号,调整定位器的调整臂,直到反馈臂
与阀杆成90°直角。
完成这项调整后,再开始375手操器调校。
二、在调校过程中出现的错误及处理方法
⑴Auto Calibration Failed:Driver signal exceed high limit check
supply pressure.
自动调校失败:设备信号超过了最高限,核对供气压力。
处理方法:
Ⅰ.检查供气压力是否太大,如果太大,适当降低供气过滤阀的输出压力。
Ⅱ.检查Actuator size,选择的尺寸是否和铭牌上一致。
⑵input current must exceed 3.8 mA for calibration.
校验时输入电流必须超过3.8 mA。
习惯上校验时,给12 mA信号。
⑶Calibration Aborted,An end point was not reached.
校验放弃,未达到行程终点。
处理方法:
Ⅰ.此时应检查,位置反馈及行程传感器连接是否完好。
Ⅱ.调校行程传感器是否在规定的范围内。