垂直分型射压造型线型砂质量控制及生产应用
垂直无箱射压造型机介绍

垂直分型无箱射压自动造型机1.用途:本机为垂直分型无箱射压全自动造型机,适用于铸铁、铸钢及有色金属铸造行业有芯、无芯中小铸件高效、大批量生产的潮模砂造型。
具有生产效率高、占地小、投资少、见效快、省人工、节能环保等优点。
2.主要性能特点:2.1 采用机、电、气、液等一体化控制技术,国际化采购。
进口液压、气动、电气元器件,提高了造型主机运行的速度、准确性与可靠性。
2.2 人机对话界面:在界定的使用范围内,可在触摸屏上设定、存储和调整各种技术参数。
2.3 故障判断功能:通过一系列传感元件和计算机系统,可诊断主机的一般性故障并报警显示,同时在电气控制上可实现故障识别以及排除方法的提示。
2.4设备具有造型效率高、砂型紧实度高、合型精度高、造型无砂箱、浇注无压铁、配套辅机少、占地面积小、运行噪音低、劳动强度低、建设投资少见效快等特点。
2.5 机器正压板底部支撑采用气垫结构,确保精度、延长寿命。
2.6 机器的型腔底板采用磁吸附双板组合结构,且工作面采用进口高硬度面板,提高了精度,延长了寿命,便于更换且更换成本低。
2.7 型腔顶、侧板采用特殊工艺处理,提高使用寿命。
2.8 采用进口无接触磁致位移传感器,使用可靠、精度高、故障少、寿命长。
2.9 导柱采用集中润滑,延长导柱使用寿命并提高造型精度。
2.10 采用自动吹净及自动喷脱模液系统,减少劳动强度提高效率。
3. 主要规格和技术参数3.1 砂型尺寸:(宽×高×厚)ZZ416ALP:砂型尺寸600×480×(120~310);ZZ416BLP:砂型尺寸650×535×(120~310);ZZ417ALP:砂型尺寸720×530×(120~310);ZZ417BLP:砂型尺寸750×535×(120~310);ZZ417CLP:砂型尺寸750×600×(120~310);ZZ418ALP:砂型尺寸800×600×(120~310);3.2 生产率:(型/小时) 300 (型厚160 毫米)3.3 型腔最大深度:(不含模板厚度) 430 毫米3.4 射砂压力: 0.25-0.3兆帕3.5 压实比压: (无级可调) 0-1.5兆帕3.6 砂型平均硬度: >853.7 合型精度: 0.1-0.14毫米3.8 噪声:<90分贝3.9 液压系统最高工作压力: 10-12兆帕3.10 压缩空气压力: 0.55-- 0.65兆帕3.11 型砂消耗量: 28-60吨/小时3.12 压缩空气消耗量: 10立方米/分3.13 电机总功率: 47.5千瓦3.14 冷却水流量: 1.5-2.0吨/分4. 生产线工艺构成垂直无箱射压造型主机、同步夹持输送机(或同步托持输送机)、同步皮带冷却机、落砂机、磷板机、旧砂砂处理系统等设备构成。
垂直分型线在铸造厂应用分析
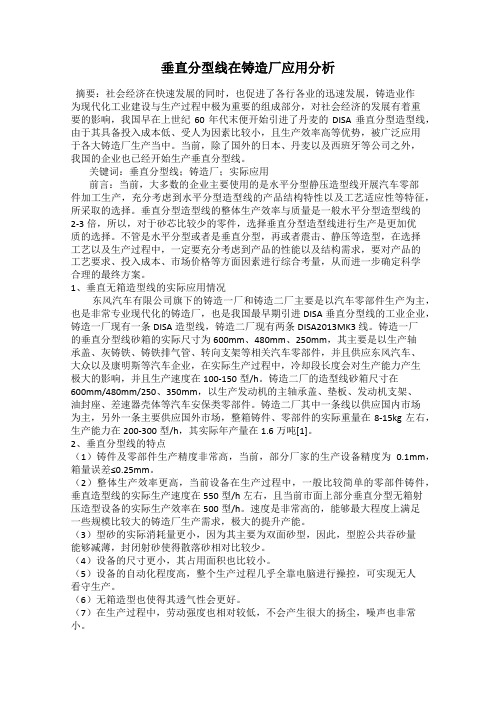
垂直分型线在铸造厂应用分析摘要:社会经济在快速发展的同时,也促进了各行各业的迅速发展,铸造业作为现代化工业建设与生产过程中极为重要的组成部分,对社会经济的发展有着重要的影响,我国早在上世纪60年代末便开始引进了丹麦的DISA垂直分型造型线,由于其具备投入成本低、受人为因素比较小,且生产效率高等优势,被广泛应用于各大铸造厂生产当中。
当前,除了国外的日本、丹麦以及西班牙等公司之外,我国的企业也已经开始生产垂直分型线。
关键词:垂直分型线;铸造厂;实际应用前言:当前,大多数的企业主要使用的是水平分型静压造型线开展汽车零部件加工生产,充分考虑到水平分型造型线的产品结构特性以及工艺适应性等特征,所采取的选择。
垂直分型造型线的整体生产效率与质量是一般水平分型造型线的2-3倍,所以,对于砂芯比较少的零件,选择垂直分型造型线进行生产是更加优质的选择。
不管是水平分型或者是垂直分型,再或者震击、静压等造型,在选择工艺以及生产过程中,一定要充分考虑到产品的性能以及结构需求,要对产品的工艺要求、投入成本、市场价格等方面因素进行综合考量,从而进一步确定科学合理的最终方案。
1、垂直无箱造型线的实际应用情况东风汽车有限公司旗下的铸造一厂和铸造二厂主要是以汽车零部件生产为主,也是非常专业现代化的铸造厂,也是我国最早期引进DISA垂直分型线的工业企业,铸造一厂现有一条DISA造型线,铸造二厂现有两条DISA2013MK3线。
铸造一厂的垂直分型线砂箱的实际尺寸为600mm、480mm、250mm,其主要是以生产轴承盖、灰铸铁、铸铁排气管、转向支架等相关汽车零部件,并且供应东风汽车、大众以及康明斯等汽车企业,在实际生产过程中,冷却段长度会对生产能力产生极大的影响,并且生产速度在100-150型/h。
铸造二厂的造型线砂箱尺寸在600mm/480mm/250、350mm,以生产发动机的主轴承盖、垫板、发动机支架、油封座、差速器壳体等汽车安保类零部件。
最新(1)湿型砂的性能要求
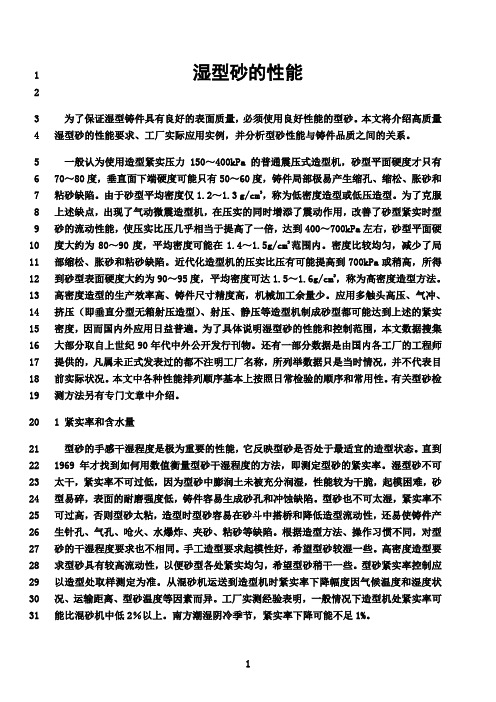
湿型砂的性能123为了保证湿型铸件具有良好的表面质量,必须使用良好性能的型砂。
本文将介绍高质量4湿型砂的性能要求、工厂实际应用实例,并分析型砂性能与铸件品质之间的关系。
5一般认为使用造型紧实压力150~400kPa的普通震压式造型机,砂型平面硬度才只有670~80度,垂直面下端硬度可能只有50~60度,铸件局部极易产生缩孔、缩松、胀砂和7粘砂缺陷。
由于砂型平均密度仅1.2~1.3 g/cm3,称为低密度造型或低压造型。
为了克服8上述缺点,出现了气动微震造型机,在压实的同时增添了震动作用,改善了砂型紧实时型9砂的流动性能,使压实比压几乎相当于提高了一倍,达到400~700kPa左右,砂型平面硬10度大约为80~90度,平均密度可能在1.4~1.5g/cm3范围内。
密度比较均匀,减少了局部缩松、胀砂和粘砂缺陷。
近代化造型机的压实比压有可能提高到700kPa或稍高,所得1112到砂型表面硬度大约为90~95度,平均密度可达1.5~1.6g/cm3,称为高密度造型方法。
高密度造型的生产效率高、铸件尺寸精度高,机械加工余量少。
应用多触头高压、气冲、1314挤压(即垂直分型无箱射压造型)、射压、静压等造型机制成砂型都可能达到上述的紧实15密度,因而国内外应用日益普遍。
为了具体说明湿型砂的性能和控制范围,本文数据搜集16大部分取自上世纪90年代中外公开发行刊物。
还有一部分数据是由国内各工厂的工程师17提供的,凡属未正式发表过的都不注明工厂名称,所列举数据只是当时情况,并不代表目18前实际状况。
本文中各种性能排列顺序基本上按照日常检验的顺序和常用性。
有关型砂检测方法另有专门文章中介绍。
19201 紧实率和含水量21型砂的手感干湿程度是极为重要的性能,它反映型砂是否处于最适宜的造型状态。
直到221969年才找到如何用数值衡量型砂干湿程度的方法,即测定型砂的紧实率。
湿型砂不可23太干,紧实率不可过低,因为型砂中膨润土未被充分润湿,性能较为干脆,起模困难,砂24型易碎,表面的耐磨强度低,铸件容易生成砂孔和冲蚀缺陷。
垂直分型射压造型线型砂质量控制及生产应用

压造 型 线 , 液 采用 中频 电炉 熔炼 , 件 以薄 壁 铸 铁 铁 铸 ( 灰铸 铁 和球 墨 铸 铁 ) 为 主 , 品包 括 汽车 零配 件 、 件 产 管道 件 阀门件 等 。我 公 司经 过 多年 生产 实 践 , 型 在 砂质 量控 制方 面做 了大量 工作 , 并取 得 了 良好效 果 。
用 的工 装 ( 箱 ) 钢 质 的 , 以 即使在 砂 箱 上 打 箱 砂 是 所
维普资讯
材 料工艺
T R, &TC N L G  ̄t. EH OO Y J J
垂直分型射压造型线型砂质量控制及生产应用
Modn a dQu l yCo to n eo ria ligS n ai nr l dUs f t l t a Ve c
Pa tn h o q e z o d n n r i g S o tS u e eM l i g Li e
赵占良( 河北 裕 龙铸 造有 限 公司 , 北 省石 家庄 市 河 003 5 0 5)
关键 词 : 型砂 性 能 , 量控 制 质
中图分 类号 : G 2 文 献标识 码 : ; T 2 l: A 文章编 号 : 0 — 6 8 2 0 ) 6 3 l 9 ( 0 7 0 — 06 5
样气 体 压力 骤 然上 升 ,且 裂解 产 物来 不 及 排 出时 出
现 反喷从 而 伤人 。浇 注过程 中 , 口杯始 终处 于充 满 浇
状 态 , 不 能 断 流 , 保 证 直 浇 道 处 于封 闭状 态 , 且 要 不
能充 入空 气 。 因为型 腔 内 的 E S模 样是 在 高 温高压 P
1 原 材 料 质 量 要 求 11 原 砂 .
12 煤粉 .
射压造型型砂性能要求

前言高密度造型方法(或称高紧实度造型,包括多触头高压、气冲、挤压、射压、静压、吸压造型方法)的生产效率高、铸件品质较好,因而国内外应用都很普遍。
高密度造型对型砂品质的要求比较严格。
本文用表格(见文后附表)列举部分典型的国内外铸造厂实际应用的和部分设备公司推荐的高密度砂型主要的和经常测定的型砂性能,并加以评论。
1 紧实率和含水量湿型砂不可太干,否则膨润土未被充分润湿,起模困难,砂型易碎,表面的耐磨强度低,铸件容易生成砂孔和冲蚀缺陷。
型砂也不可太湿,过湿型砂易使铸件产生针孔、气孔、呛火、水爆炸、夹砂、粘砂等缺陷,而且型砂太粘、型砂在砂斗中搭桥、造型流动性降低。
使砂型型腔表面松紧不均;还可能导致造型紧实距离过大和压头陷入砂箱边缘以内而损伤模具和砂型吃砂量过小。
表明型砂干湿状态的参数有两种:紧实率和含水量。
附表中国内各厂的紧实率和含水量除特别注明以外,取样地点都在混砂机处。
但是型砂紧实率和含水量的控制应以造型处取样测定为准。
从混砂机运送到造型机时紧实率和含水量下降幅度因气候温度和湿度状况、运输距离、型砂温度等因素而异。
如果只根据混砂机处取样检测结果控制型砂的湿度,就要略增少许,以补偿紧实率和水分的损失。
以前的观点认为手工造型和震压式机器造型最适宜于湿状态下的紧实率大约在45~50%;高压造型和气冲造型时为40~45%;挤压造型要求流动性好,紧实率为35~40%。
由表中可以看出,目前铸件品质较好的工厂,高密度造型的型砂紧实率(大多是从混砂机取样)通常都在25~45%范围内,比较集中于30~40%之间,比以前有明显降低。
这是由于高密度造型设备的起模精度提高,而且要求砂型各部位硬度均匀分布,使型砂的流动性成为重要因素。
工厂的控制原则大多是只要能够保证起模顺利就尽力降低紧实率。
从减少铸件气孔缺陷的角度出发,要求最适宜干湿状态下型砂的含水量尽可能低。
高强度型砂的膨润土加入量多,型砂中含有较多灰分,所购入煤粉和膨润土因品质低劣而需要增大加入量,混砂机的加料顺序不当、揉碾作用不强、刮砂板磨损、混砂时间太短,以致型砂中存在较多不起粘结作用的小粘土团块,都会提高型砂的含水量。
垂直分型无箱射压造型线应用中的几个工艺问题

现代粘土湿砂造型工艺和设备是多种多样的,并各有所长,但其共同的特点则是制造高紧实度的铸型、提高生产率和降低造型作业时产生的噪音。
垂直分型无箱挤压造型机是有代表性的现代造型设备中的一种,尤适用于生产小型和中等偏小的铸件,已为世界各国广泛采用。到目前为止,我国采用此类造型设备的铸造厂估计在100家以上。
使型砂通过3mm的筛网松散地填入Φ50mm,高100mm的试样筒,将试样筒上端的余砂用刮板刮去,然后用压头给型砂施以1MPa的压力或用标准重锤打击3次,测定试样筒内型砂经紧实后高度下降的毫米数。由于试样筒高100mm,这一读数也就是其高度下降的百分数,即可坚实性数值。
在不同的造型条件下,对型砂可紧实性的要求是不同的。
表1造型设备对型砂性能的要求
型砂性能
不同型号设备要求的指标
铸型尺寸较小的设备
铸型尺寸较大的设备
湿抗压强度(kPa)
167~206
216~245
湿抗拉强度(kPa)
>19.6
>24.0
湿抗劈强度(kPa)
>29.4
>37.3
透气性
>50
>50
可紧实性(%)
40±5
40±5
水分
不具体限定,以保证可紧实性符合要求为原则
用垂直分型造型机造型时虽然射砂后压实的行程并不固定而是以一定的压强压实铸型但是即使在此种情况下型砂的可紧实性太高除导致铸型厚度减小外也会使铸型的紧实度降低在砂台部位及射砂的盲区尤为显著
垂直分型无箱射压造型线应用中的几个工艺问题
一、前言
最近30年来,从通过机械化、自动化以求提高劳动生产率,到着重于降低生产成本和提高铸件的尺寸精度,粘土湿砂造型技术有了重大的发展。
大型垂直分型造型线生产铸铁件的质量控制(3)
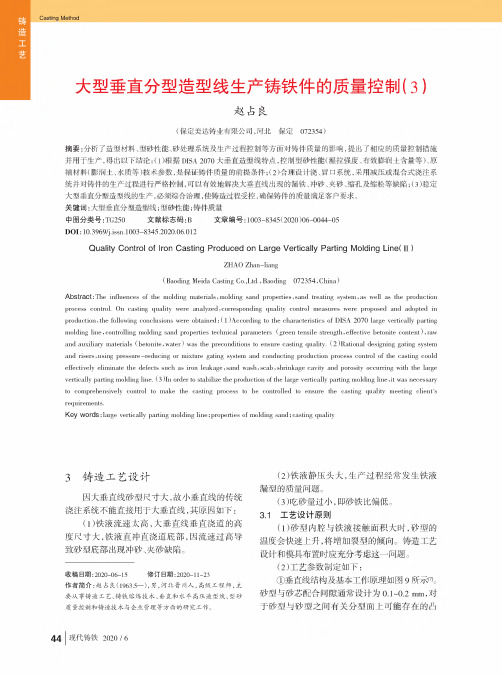
大型垂直分型造型线生产铸铁件的质量控制(3)赵占良(保定美达铸业有限公司,河北保定072354)摘要:分析了造型材料、型砂性能、砂处理系统及生产过程控制等方面对铸件质量的影响,提出了相应的质量控制措施用于生产,出下结:⑴;DISA2070大垂直型线,控制型砂能A度、量[、原A、质等);参数,铸件质量的;(2[浇、系统,采用压浇注系统并对铸件的生产过程制,大垂直线出现的漏铁、冲砂、夹砂、缺陷;(3)稳定大型垂直型造型线的生产,,铸过程受控,铸件的质足客户要求。
关键词:大型垂直分型型线;型砂能;铸质中图分类号:TG250文献标志码:B文章编号:1003-8345(2020)06-0044-05D01:10.3969/j.issn.l003-8345.2020.06.012Quality Control of Iron Casting Produced on Large Vertically Parting Molding Linet")ZHAO Zhan-liang(BaoEing MeiEa Casting Co.,LtE.,BaoEing072354,China)Abstract:The influences of the molEing materials,molEing sanE properties,sanE treating system,as well as the proEuction process control.On casting quality were analyzeE,corresponEing quality control measures were proposeE anE aEopteE in proEuction,the following conclusions were obtaineE:(1)AccorEing to the characteristics of DISA2070large vertically parting molEing line,controlling molEing sanE properties technical parameters(green tensile strength,effective betonite content),raw anE auxiliary materials(betonite,water)was the preconEitions to ensure casting quality.(2)Rational Eesigning gating system anE risers,using pressure-reEucing or mixture gating system anE conEucting proEuction process control of the casting coulE effectively eliminate the Eefects such as iron leakage,sanE wash,scab,shrinkage cavity anE porosity occurring with the large vertically parting molEing line.(3)In orEer to stabilize the proEuction of the large vertically parting molEing line,it was necessary to comprehensively control to make the casting process to be controlleE to ensure the casting quality meeting client's requirements.Key words:large vertically parting molEing line;properties of molEing sanE;casting quality3铸造工艺设计因大垂直线砂型尺寸大,故小垂直线的传统浇注系统不能直接用于大垂直线,其原因如下:(1)铁液流速太高,大垂直线垂直浇道的高度尺寸大,铁液直冲直浇道底部,因流速过高导致砂型底部出现冲砂、夹砂缺陷。
垂直分型射压造型线型砂质量控制及生产应用

垂直分型射压造型线型砂质量控制及生产应用在粘土砂铸造生产过程中,型砂是关键,其性能控制得好与坏,质量稳定与否,将对铸件质量产生巨大的影响。
我公司的造型线为ZZ416垂直分型射压造型线,铁液采用中频电炉熔炼,铸件以薄壁铸铁(灰铸铁和球墨铸铁)件为主,产品包括汽车零配件、管道件、阀门件等。
我公司经过多年生产实践,在型砂质量控制方面做了大量工作,并取得了良好效果。
1原材料质量要求1.1原砂选用河北围场擦洗砂,含泥量<1.0%,SiO2>85%,原砂粒度70/140目。
由于垂直分型射压造型属高密度造型,为减少砂型受热膨胀,避免因砂粒受挤压从砂型表面脱落而引起铸造缺陷,粒度要求不宜过于集中,原砂最好采用4筛集中率85%以上,主峰筛(100目)量控制在40%以内。
新砂补加量在5%以下。
1.2煤粉煤粉灰份应<10%,煤粉含灰量过高,使得型砂含泥量增加,影响型砂使用性能。
含硫量≤1.5%;煤粉粒度≥95%以上的颗粒通过140目筛,并且煤粉不允许有大颗粒存在,因其在浇注过程中遇金属液燃烧时间长,阻止铁液靠近型壁,待铁液凝固后,便会造成铸件表面凹坑,影响铸件表面粗糙度。
挥发分的高低是衡量煤粉质量好坏的主要指标之一,好的煤粉挥发分含量较高,浇注时,型腔内易形成还原性气体,析出大量的光亮碳,提高铸件的外观质量。
但挥发分超过40%,型砂发气量增大,铸件易产生气孔、浇不足等缺陷。
因此,挥发分一般在30%-38%。
1.3膨润土选用钠基膨润土。
湿压强度≥120kPa,吸蓝量(g/100g)≥38,粒度过200目≥90%。
2型砂性能质量控制2.1湿压强度如果型砂湿态强度不足,在起模、搬运砂型、下芯、合型等过程中,砂型有可能破损和塌落;浇注时砂型承受不住金属液的冲刷和冲击造成砂孔缺陷,甚至铁液泄漏。
一般用湿压强度来表示型砂湿态强度,一般控制在150-200kPa。
2.2透气性型砂的透气率不可太低以免浇注过程中发生呛火和铸件产生气孔缺陷,但绝不能理解为型砂透气率越高越好。
- 1、下载文档前请自行甄别文档内容的完整性,平台不提供额外的编辑、内容补充、找答案等附加服务。
- 2、"仅部分预览"的文档,不可在线预览部分如存在完整性等问题,可反馈申请退款(可完整预览的文档不适用该条件!)。
- 3、如文档侵犯您的权益,请联系客服反馈,我们会尽快为您处理(人工客服工作时间:9:00-18:30)。
垂直分型射压造型线型砂质量控制及生产应用在粘土砂铸造生产过程中,型砂是关键,其性能操纵得好与坏,质量稳固与否,将对铸件质量产生庞大的阻碍。
我公司的造型线为ZZ416垂直分型射压造型线,铁液采纳中频电炉熔炼,铸件以薄壁铸铁(灰铸铁和球墨铸铁)件为主,产品包括汽车零配件、管道件、阀门件等。
我公司通过多年生产实践,在型砂质量操纵方面做了大量工作,并取得了良好成效。
1原材料质量要求1.1原砂选用河北围场擦洗砂,含泥量<1.0%,SiO2>85%,原砂粒度70/140目。
由于垂直分型射压造型属高密度造型,为减少砂型受热膨胀,幸免因砂粒受挤压从砂型表面脱落而引起铸造缺陷,粒度要求不宜过于集中,原砂最好采纳4筛集中率85%以上,主峰筛(100目)量操纵在40%以内。
新砂补加量在5%以下。
1.2煤粉煤粉灰份应<10%,煤粉含灰量过高,使得型砂含泥量增加,阻碍型砂使用性能。
含硫量≤1.5%;煤粉粒度≥95%以上的颗粒通过140目筛,同时煤粉不承诺有大颗粒存在,因其在浇注过程中遇金属液燃烧时刻长,阻止铁液靠近型壁,待铁液凝固后,便会造成铸件表面凹坑,阻碍铸件表面粗糙度。
挥发分的高低是衡量煤粉质量好坏的要紧指标之一,好的煤粉挥发分含量较高,浇注时,型腔内易形成还原性气体,析出大量的光亮碳,提升铸件的外观质量。
但挥发分超过40%,型砂发气量增大,铸件易产动气孔、浇不足等缺陷。
因此,挥发分一样在30%-38%。
1.3膨润土选用钠基膨润土。
湿压强度≥120kPa,吸蓝量(g/100g)≥38,粒度过200目≥90%。
2型砂性能质量操纵2.1湿压强度如果型砂湿态强度不足,在起模、搬运砂型、下芯、合型等过程中,砂型有可能破旧和塌落;浇注时砂型承担不住金属液的冲刷和冲击造成砂孔缺陷,甚至铁液泄漏。
一样用湿压强度来表示型砂湿态强度,一样操纵在150-200kPa。
2.2透气性型砂的透气率不可太低以免浇注过程中发生呛火和铸件产动气孔缺陷,但绝不能明白得为型砂透气率越高越好。
因为透气率过高表明沙粒间孔隙较大,金属液易于渗透而造成表面粗糙,还可能产生气械粘砂。
湿粘砂的透气率按照浇注金属的种类和温度、铸件的大小和壁厚、造型方法、型砂的发气量大小等决定,一样操纵在90-160。
2.3紧实率和含水量紧实率和含水量是衡量型砂综合性能的重要参数。
湿型砂水分一定要适中,否则膨润土未被充分润湿阻碍混砂,进而导致造型起模困难且砂型发脆易碎、表面耐磨强度低,铸件易产生砂眼和冲蚀缺陷。
一样紧实率操纵在32%-40%,最佳34%-38%。
高密度造型用型砂含水量在2.8%-3.8%。
型砂的紧实率/含水量比值一样在10-12。
2.4含泥量高密度造型最理想的铸铁用型砂含泥量(含煤粉)为10%-13%,不应≥14%;理想的旧砂含泥量为8%-11%,不应≥12%。
2.5有效粘土型砂的有效膨润土是指全部仍旧具有粘结能力的膨润土。
一样高密度造型的有效膨润土操纵在6%-8%。
2.6有效煤粉量(燃损)煤粉高温下气相分解,在砂粒表面沉积形成“光亮碳”,防止铸件表面粘砂,提升铸件表面质量。
如果型砂中有效煤粉含量过高,同时型砂透气性又较差,因型腔内气体量增大,铸件易产动气孔、冷隔、浇不足等缺陷。
为此大多数铸造企业通过测定型砂及附加物的发气量,运算有效煤粉含量,一样操纵在3.0%-4.5%。
按照我们的体会并参照其他企业做法,我们将测定有效煤粉含量的方法改为测定型砂挥发分。
挥发分的测定时将样砂放入的坩埚并置于马弗炉内,在649℃下煅烧1h后称重测得。
现场通过型砂挥发重量的变化来操纵有效煤粉含量更切合实际,测发气性不是专门准确,缘故是型砂中有机物(砂芯)等也是发气的,不易辨论。
一样型砂挥发分含量操纵在2.0%-3.0%(质量分数)。
2.7粒度型砂粒度直截了当阻碍透气性和铸件表面粗糙度,但原砂粒度并不能代表实际型砂中砂子的粒度,因为在铸造过程中部分砂粒可能破裂成细粉,另一部分可能烧结成粗粒,而且不同粗细的砂芯溃碎后也会混入旧砂,因此应将测定含泥量的型砂用筛分法测定粒度,一样型砂粒度AFS值操纵在55—65。
2.8回用砂(旧砂)质量操纵回用砂的降温:因垂直分型造型线为造型、浇注连续作业,回用砂反复循环使用,其温度的高低将直截了当阻碍型砂的温度,从而阻碍型砂的整体性能:其一,热砂有粘贴在较冷料仓壁的倾向并形成料斗缩管,使系统砂中只有少部分被频繁使用,砂的周转率增加速度,使系统砂中只有少部分被频繁使用,砂的周转率增加速度,使砂温进一步升高;其次,热型砂与模具接触,由于水分凝聚而粘结在一起,脱模时造成型腔表面粗糙及砂粒松散;其三,砂温越高,砂型水蒸气压越大,砂型表面的水分蒸发速度越快,风干现象越严峻,风干后的型砂强度更低,浇注时铁液冲刷型腔内的风干砂导致铸件产生砂眼缺陷。
因此如何降低回用砂温度,将成为造型线能否生产出优质铸件的关键因素之一。
回用砂温度操纵的目的是最终向混砂机输送的旧砂温度应低于45℃。
最佳方法是在落砂机后安装冷却装置(冷却滚筒、沸腾冷却床、双盘冷却器等)。
其中沸腾冷却床冷却成效较好,因回用砂在沸腾冷却床中翻腾与喷水雾同时进行,从而增加了水与砂的接触面积和时刻,达到降低砂温之目的。
而传统的做法向传送带上的砂子喷水并不能有效地冷却回用砂,是不可取得。
其缘故是,传统方法中的水没有足够的时刻与所有砂粒充分接触,同时局部热砂和水的混合物有可能使周围空气的湿度达到饱和,在此情形下不可能将水由液体转变为气体,并把形成的水蒸汽有效排除。
回用砂中芯砂的阻碍:砂芯的加入对湿型砂性能有阻碍。
铸型浇注后仅有部分砂芯的砂粒表层数值被烧坏,而未被烧掉的仍滞留在型砂中,因砂芯打部分是覆膜砂芯(以树脂为粘结剂),芯砂表面树脂不亲水,补加的潮湿膨润土专门难与其粘结,导致产生脆性型砂。
脆性型砂不能保证砂型棱角处的质量,而且随着铁液的冲刷极易产生砂眼。
此外,脆性型砂还会给起模带来不良阻碍。
为了防止芯砂的加入对湿型砂的阻碍,加入新砂的量应保持在混制沙总量的2%--5%。
同时在安排铸件生产时应注意有芯和无芯产品的合理搭配,尽可能减少型砂中的芯砂量。
3生产应用3.1混砂工艺混砂过程第一应做到将砂、膨润土、水及附加物混和平均;在揉搓各种材料使粘土膜平均包覆在砂粒周围。
加料顺序一样是先将干料混合,再加水湿混。
但经观看,型砂通过松砂后总有些像小米粒大小坚硬的砂团包裹在型砂中,其成分实际上确实是膨润土和砂子的烧结物和粘土球,该砂团遇水就开。
因此混砂工艺建议改为,加砂后先加水湿混化解粘砂团,再加其它粉料。
旧砂+新砂+水(最好为雾化水);湿混15s后,加膨润土+煤粉+添加剂,混120~150s。
混砂时刻不易过长,否则砂子发热降低流淌性,强度反而受阻碍。
3.2造型造型前应先预热模板(专门是冬天冰冷季节),使其温度高于型砂5℃为宜,起模时不粘模,表面也不干燥,铸型表面光洁。
3.3型砂检测一是严格原材料的进货检验(包括原砂、膨润土、煤粉等);二是加大型砂的在线检测,对型砂性能进行定期检测,及时发觉咨询题并及时解决。
3.4型砂好坏的判定有些企业认为,能够“用湿压强度的值”代替“有效膨润土的值”来决定混砂机中膨润土的添加量,这种观点是不成立的。
简单讲,在型砂中的膨润土和死粘土都产生湿压强度,增加死粘土的量,而紧实率不变,湿压强度的值也会增加,因此湿压强度会有误导作用。
在考虑湿压强度的时候还要同时考虑其他性能和有效粘土、含泥量的结果。
“有效粘土含量测试”是唯独能够测定型砂中膨润土含量的方法。
在保证有效粘土含量的前提下,混砂现场应重点操纵型砂紧实率,使型砂中的膨润土和水分比例适中,充分发挥膨润土的粘结作用,幸免因水分过多使型砂显现自由水的现象。
3.5浇注应快速、高温、连续浇注,快速充型;否则易产生串气、冲砂,形成水分迁移(俗称放炮),造成砂型损坏,显现铸件废品。
4要紧缺陷分析与计策4.1砂眼砂眼是由于浇注系统或型内掉有砂粒或因铁液冲刷型壁,零散砂粒掉落引起。
如果型砂混制位置与造型线距离较远,湿砂型在皮带输送过程中,型砂表层脱水强度急剧下降,北方天气干燥季节中“风干”现象更加严峻,应引起注意和重视。
另外旧砂反复使用若型砂中的灰分、含泥量过高,将导致型砂韧性低发脆、起模性能差,使砂型的棱角和边缘破裂,引起砂眼缺陷。
防止砂眼措施:①采纳优质膨润土,按照季节(干燥、潮湿等)变化,合理操纵型砂水分,提升型砂强度;②调解旧砂除尘设备,将旧砂含泥量操纵在12%以下,造型处型砂紧实率提升为34%-38%,含水量为3.2% -3.8%,使紧实率与含水量的比例在10—12的范畴内;③型砂中加入少量淀粉,提升型砂韧性,降低起模摩擦阻力,增强表面风干强度;④及时调整旧砂中芯砂含量,适当延长混碾时刻。
4.2粘砂粘砂是由于铁液渗透铸型而产生的表面缺陷。
采取的计策为:①采纳粒度较细、分布适中的原砂,提升型砂的流淌性和紧实度(铸型硬度操纵在90左右),减少铸型表面的间隙;②使用高效优质煤粉,操纵型砂中的有效煤粉含量即挥发分,减少铁液表面氧化及对砂型表面的潮湿和渗透;③适当减低浇注温度,减少铁液压力。
4.3球铁件气孔气孔防止:①提升型砂透气性;②操纵型砂煤粉加入量及水分和芯砂含量,减少型砂发气量;③模板上合理布置排气槽,利于铸型内气体向外逸出;④适当提升浇注温度(>1380℃)和速度,在浇包液面上撒冰晶石粉。