精馏节能技术
自回热精馏节能技术使用计划方案
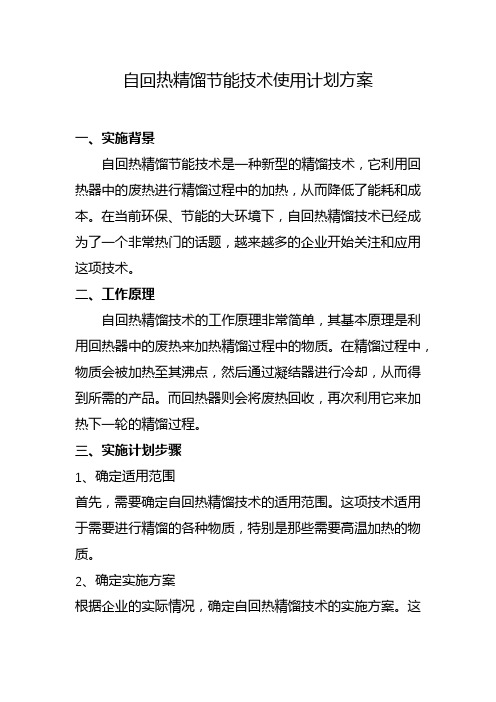
自回热精馏节能技术使用计划方案一、实施背景自回热精馏节能技术是一种新型的精馏技术,它利用回热器中的废热进行精馏过程中的加热,从而降低了能耗和成本。
在当前环保、节能的大环境下,自回热精馏技术已经成为了一个非常热门的话题,越来越多的企业开始关注和应用这项技术。
二、工作原理自回热精馏技术的工作原理非常简单,其基本原理是利用回热器中的废热来加热精馏过程中的物质。
在精馏过程中,物质会被加热至其沸点,然后通过凝结器进行冷却,从而得到所需的产品。
而回热器则会将废热回收,再次利用它来加热下一轮的精馏过程。
三、实施计划步骤1、确定适用范围首先,需要确定自回热精馏技术的适用范围。
这项技术适用于需要进行精馏的各种物质,特别是那些需要高温加热的物质。
2、确定实施方案根据企业的实际情况,确定自回热精馏技术的实施方案。
这包括确定使用的设备和工艺流程,以及需要进行的改造和调整。
3、进行设备改造根据实施方案,对设备进行改造。
这包括添加回热器、调整加热方式等。
4、进行试运行在设备改造完成后,进行试运行。
这可以帮助企业发现设备中存在的问题,并进行调整和改进。
5、正式应用在试运行结束后,正式应用自回热精馏技术。
在使用过程中,需要不断优化和改进,以达到更好的效果。
四、适用范围自回热精馏技术适用于各种需要进行精馏的物质,特别是那些需要高温加热的物质。
此外,该技术还适用于各种规模的企业,无论是大型企业还是中小型企业。
五、创新要点自回热精馏技术的创新点主要包括以下几个方面:1、利用回热器中的废热进行加热,降低了能耗和成本。
2、采用自动控制系统,可以对加热温度和流量进行精确控制,提高了生产效率和产品质量。
3、在设备改造过程中,可以采用先进的材料和工艺,提高了设备的稳定性和可靠性。
六、预期效果通过应用自回热精馏技术,企业可以获得以下效果:1、降低能耗和成本,提高生产效率。
2、减少废气和废水的排放,降低环境污染。
3、提高产品质量和市场竞争力。
七、达到收益应用自回热精馏技术可以带来以下收益:1、降低能耗和成本,提高经济效益。
精馏塔精馏影响因素分析及节能技术的应用
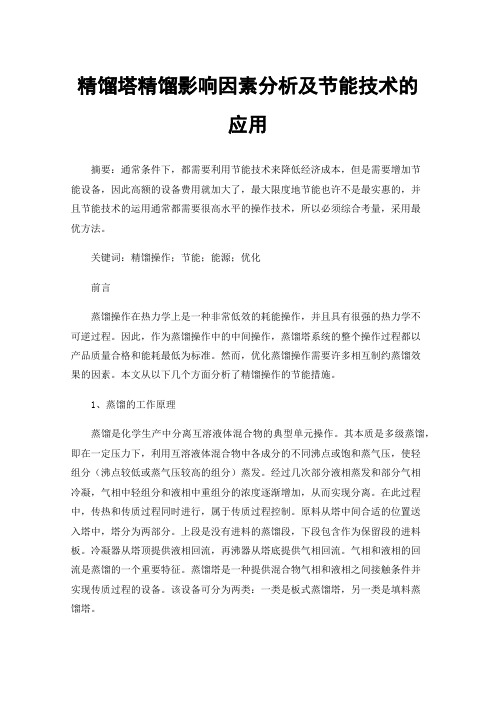
精馏塔精馏影响因素分析及节能技术的应用摘要:通常条件下,都需要利用节能技术来降低经济成本,但是需要增加节能设备,因此高额的设备费用就加大了,最大限度地节能也许不是最实惠的,并且节能技术的运用通常都需要很高水平的操作技术,所以必须综合考量,采用最优方法。
关键词:精馏操作;节能;能源;优化前言蒸馏操作在热力学上是一种非常低效的耗能操作,并且具有很强的热力学不可逆过程。
因此,作为蒸馏操作中的中间操作,蒸馏塔系统的整个操作过程都以产品质量合格和能耗最低为标准。
然而,优化蒸馏操作需要许多相互制约蒸馏效果的因素。
本文从以下几个方面分析了精馏操作的节能措施。
1、蒸馏的工作原理蒸馏是化学生产中分离互溶液体混合物的典型单元操作。
其本质是多级蒸馏,即在一定压力下,利用互溶液体混合物中各成分的不同沸点或饱和蒸气压,使轻组分(沸点较低或蒸气压较高的组分)蒸发。
经过几次部分液相蒸发和部分气相冷凝,气相中轻组分和液相中重组分的浓度逐渐增加,从而实现分离。
在此过程中,传热和传质过程同时进行,属于传质过程控制。
原料从塔中间合适的位置送入塔中,塔分为两部分。
上段是没有进料的蒸馏段,下段包含作为保留段的进料板。
冷凝器从塔顶提供液相回流,再沸器从塔底提供气相回流。
气相和液相的回流是蒸馏的一个重要特征。
蒸馏塔是一种提供混合物气相和液相之间接触条件并实现传质过程的设备。
该设备可分为两类:一类是板式蒸馏塔,另一类是填料蒸馏塔。
2、精馏塔影响的因素2.1、物料平衡精馏塔稳态操作的必须条件就是要保持精馏装置的物料平衡。
对于指定的原料液流量,只要分离度(馏出液中易挥发组分的摩尔分数)和釜残液中易挥发组分的摩尔分数是规定不变的,而馏出液流量和釜残液流量也能够确定了。
分离度和釜残液中易挥发组分的摩尔分数决定于气液平衡关系和理论板数,所以D和W或采出率 D F/ 与W F/ 只能根据分离度和釜残液中易挥发组分的摩尔分数确定,然而不能随意变化,否则进、出塔的两个组分的量会导致失衡,最终把塔内组成发生改变,波动不平的操作,这样一来整个工作工程的效率和效果不是特别理想。
浅析化工精馏高效节能技术开发及应用
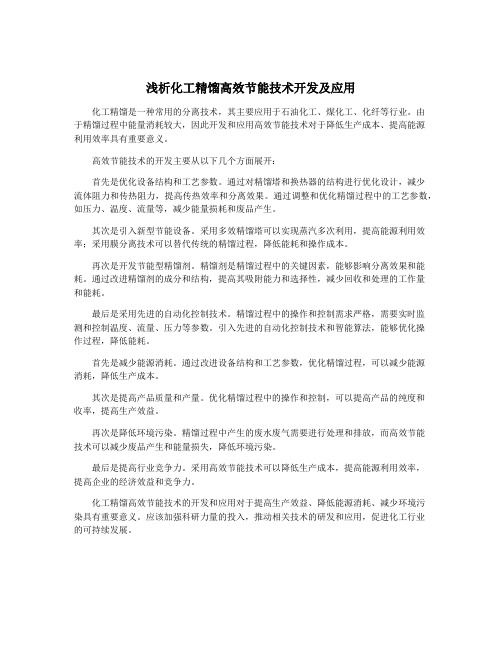
浅析化工精馏高效节能技术开发及应用化工精馏是一种常用的分离技术,其主要应用于石油化工、煤化工、化纤等行业。
由于精馏过程中能量消耗较大,因此开发和应用高效节能技术对于降低生产成本、提高能源利用效率具有重要意义。
高效节能技术的开发主要从以下几个方面展开:首先是优化设备结构和工艺参数。
通过对精馏塔和换热器的结构进行优化设计,减少流体阻力和传热阻力,提高传热效率和分离效果。
通过调整和优化精馏过程中的工艺参数,如压力、温度、流量等,减少能量损耗和废品产生。
其次是引入新型节能设备。
采用多效精馏塔可以实现蒸汽多次利用,提高能源利用效率;采用膜分离技术可以替代传统的精馏过程,降低能耗和操作成本。
再次是开发节能型精馏剂。
精馏剂是精馏过程中的关键因素,能够影响分离效果和能耗。
通过改进精馏剂的成分和结构,提高其吸附能力和选择性,减少回收和处理的工作量和能耗。
最后是采用先进的自动化控制技术。
精馏过程中的操作和控制需求严格,需要实时监测和控制温度、流量、压力等参数。
引入先进的自动化控制技术和智能算法,能够优化操作过程,降低能耗。
首先是减少能源消耗。
通过改进设备结构和工艺参数,优化精馏过程,可以减少能源消耗,降低生产成本。
其次是提高产品质量和产量。
优化精馏过程中的操作和控制,可以提高产品的纯度和收率,提高生产效益。
再次是降低环境污染。
精馏过程中产生的废水废气需要进行处理和排放,而高效节能技术可以减少废品产生和能量损失,降低环境污染。
最后是提高行业竞争力。
采用高效节能技术可以降低生产成本,提高能源利用效率,提高企业的经济效益和竞争力。
化工精馏高效节能技术的开发和应用对于提高生产效益、降低能源消耗、减少环境污染具有重要意义。
应该加强科研力量的投入,推动相关技术的研发和应用,促进化工行业的可持续发展。
精馏过程的节能降耗

精馏过程的节能降耗精馏过程在化工产业中是一项重要的分离技术,但是它也是能耗较高的过程。
为了降低能耗,节能降耗已经成为精馏技术的一个重要研究方向。
本文将介绍几种精馏过程的节能降耗技术。
首先,提高精馏塔的热效率是提高精馏过程的一个关键。
一种常见的做法是引入换热器网络来最大程度地利用出塔冷凝液和进塔蒸汽之间的热量传递。
这种方法可以降低所需的蒸汽量,从而降低了能耗。
此外,还可以使用多效精馏、热泵或采用废热回收技术进一步提高热效率。
其次,提高精馏过程的物质效率也是节能降耗的一个重要途径。
物质效率是指在精馏过程中使用的干燥剂或者吸附剂能够更有效地去除杂质,从而减少能耗。
通过改进精馏塔的操作条件,如温度、压力和液体流速等参数,可以提高物质效率。
同时,使用高效的精馏填料或者塔板也能够提高分离效果,减少杂质的含量。
此外,使用先进的辅助技术可以进一步降低精馏过程的能耗。
例如,在精馏过程中引入膜分离技术可以减少能源消耗。
膜分离技术是一种基于材料表面或孔隙的选择性渗透性原理分离混合物的方法。
与传统的溶剂萃取或者蒸馏技术相比,膜分离技术具有能耗低、操作简单、体积小等优点。
通过将膜分离技术与精馏过程相结合,可以实现更高效的分离效果。
最后,优化精馏过程的操作策略也是节能降耗的一个重要途径。
通过优化参数设定和控制策略,可以使精馏过程更加稳定和高效。
例如,采用先进的控制算法,如模型预测控制或者模糊控制算法,可以实现对精馏过程的快速响应和精确控制,从而降低了能耗和运行成本。
总的来说,精馏过程的节能降耗是一个涉及多个方面的工程问题。
通过提高热效率、物质效率,使用先进的辅助技术和优化操作策略,可以有效地降低精馏过程的能耗。
这些节能降耗技术不仅可以减少环境污染,还可以提高精馏过程的经济效益。
因此,精馏过程的节能降耗在工业应用中具有重要的意义。
精馏节能技术

热泵精馏工艺分析化工行业就是能耗大户,其中精馏又就是能耗极高的单元操作,而传统的精馏方式热力学效率很低,能量浪费很大。
如何降低精馏塔的能耗,充分利用低温热源,已成为人们普遍关注的问题。
对此人们提出了许多节能措施,通过大量的理论分析、实验研究以及工业应用表明其中节能效果比较显著的就是热泵精馏技术。
热泵精馏就是把精馏塔塔顶蒸汽加压升温,使其用作塔底再沸器的热源,回收塔顶蒸汽的冷凝潜热。
热泵精馏在下述场合应用,有望取得良好效果:(1)塔顶与塔底温差较小,因为压缩机的功耗主要取决于温差,温差越大,压缩机的功耗越大。
据国外文献报导,只要塔顶与塔底温差小于36℃,就可以获得较好的经济效果。
(2)沸点相近组分的分离,按常规方法,蒸馏塔需要较多的塔盘及较大的回流比,才能得到合格的产品,而且加热用的蒸汽或冷却用的循环水都比较多。
若采用热泵技术一般可取得较明显的经济效益。
(3)工厂蒸汽供应不足或价格偏高,有必要减少蒸汽用量或取消再沸器时。
(4)冷却水不足或者冷却水温偏高、价格偏贵,需要采用制冷技术或其她方法解决冷却问题时。
(5)一般蒸馏塔塔顶温度在38~138℃之间,如果用热泵流程对缩短投资回收期有利就可以采用,但就是如果有较便宜的低压蒸汽与冷却介质来源,用热泵流程就不一定有利。
(6)蒸馏塔底再沸器温度在300℃以上,采用热泵流程往往就是不合适的。
以上只就是对一般情况而言,对于某个具体工艺过程,还要进行全面的经济技术评定之后才能确定。
根据热泵所消耗的外界能量不同,热泵精馏可分为蒸汽加压方式与吸收式两种类型1、蒸汽加压方式蒸汽加压方式热泵精馏有两种:蒸汽压缩机方式与蒸汽喷射式。
1、1蒸汽压缩机方式蒸汽压缩机方式又可分为间接式、塔顶气体直接压缩式、分割式与塔釜液体闪蒸再沸式流程。
1、1、1间接式当塔顶气体具有腐蚀性或塔顶气体为热敏性产品或塔顶产品不宜压缩时,可以采用间接式热泵精馏,见图1。
图1 间接式热泵精馏流程图它主要由精馏塔、压缩机、蒸发器、冷凝器及节流阀等组成。
精馏过程节能技术综述
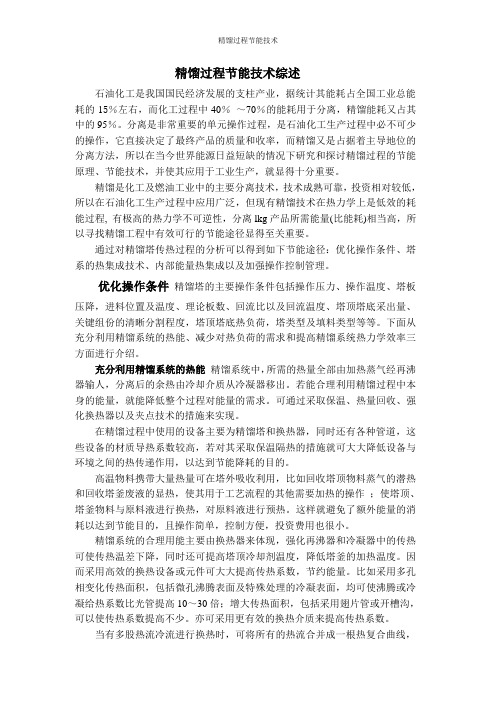
精馏过程节能技术综述石油化工是我国国民经济发展的支柱产业,据统计其能耗占全国工业总能耗的15%左右,而化工过程中40%~70%的能耗用于分离,精馏能耗又占其中的95%。
分离是非常重要的单元操作过程,是石油化工生产过程中必不可少的操作,它直接决定了最终产品的质量和收率,而精馏又是占据着主导地位的分离方法,所以在当今世界能源日益短缺的情况下研究和探讨精馏过程的节能原理、节能技术,并使其应用于工业生产,就显得十分重要。
精馏是化工及燃油工业中的主要分离技术,技术成熟可靠,投资相对较低,所以在石油化工生产过程中应用广泛,但现有精馏技术在热力学上是低效的耗能过程, 有极高的热力学不可逆性,分离lkg产品所需能量(比能耗)相当高,所以寻找精馏工程中有效可行的节能途径显得至关重要。
通过对精馏塔传热过程的分析可以得到如下节能途径:优化操作条件、塔系的热集成技术、内部能量热集成以及加强操作控制管理。
优化操作条件精馏塔的主要操作条件包括操作压力、操作温度、塔板压降,进料位置及温度、理论板数、回流比以及回流温度、塔顶塔底采出量、关键组份的清晰分割程度,塔顶塔底热负荷,塔类型及填料类型等等。
下面从充分利用精馏系统的热能、减少对热负荷的需求和提高精馏系统热力学效率三方面进行介绍。
充分利用精馏系统的热能精馏系统中,所需的热量全部由加热蒸气经再沸器输人,分离后的余热由冷却介质从冷凝器移出。
若能合理利用精馏过程中本身的能量,就能降低整个过程对能量的需求。
可通过采取保温、热量回收、强化换热器以及夹点技术的措施来实现。
在精馏过程中使用的设备主要为精馏塔和换热器,同时还有各种管道,这些设备的材质导热系数较高,若对其采取保温隔热的措施就可大大降低设备与环境之间的热传递作用,以达到节能降耗的目的。
高温物料携带大量热量可在塔外吸收利用,比如回收塔顶物料蒸气的潜热和回收塔釜废液的显热,使其用于工艺流程的其他需要加热的操作;使塔顶、塔釜物料与原料液进行换热,对原料液进行预热。
精馏节能技术
(3) 中间冷凝器和中间再沸器
如能在塔中部设置中间冷凝器,就可以采用较高温度 如能在塔中部设置中间冷凝器, 的冷却剂。 的冷却剂。 如在塔中部设置中间再沸器,对于高温塔, 如在塔中部设置中间再沸器,对于高温塔,可应用较 低温位的加热剂。 低温位的加热剂。 对于精馏,使操作线向平衡线靠拢,提高塔内分离过 对于精馏,使操作线向平衡线靠拢, 程的可逆程度。 程的可逆程度。 在生产过程中必须要由适当温位的加热剂或( 在生产过程中必须要由适当温位的加热剂或(和)冷 却剂与其相配,并需有足够大的热负荷值得利用, 却剂与其相配,并需有足够大的热负荷值得利用,再 加上塔顶和塔底的温度差要相当大, 加上塔顶和塔底的温度差要相当大,如此才会取得经 济效益。 济效益。
(5) 热泵精馏
将温度较低的塔顶蒸汽经压缩后作为塔底再沸器的热源, 将温度较低的塔顶蒸汽经压缩后作为塔底再沸器的热源, 称为热泵精馏。 称为热泵精馏。 三种典型的热泵精馏流程:使用另外的工作流体, 三种典型的热泵精馏流程:使用另外的工作流体,塔顶 蒸汽再压缩,再沸器液体闪蒸。 蒸汽再压缩,再沸器液体闪蒸。 热泵精馏是消耗一定量的机械功来提高低温蒸汽的能位 而加以利用的。因此消耗单位机械能能回收的热量是一 而加以利用的。因此消耗单位机械能能回收的热量是一 消耗单位机械能能回收的热量 项重要经济指标,称为性能系数,常记为 项重要经济指标,称为性能系数,常记为C.O.P.。 。 显然, 显然,对于沸点差小的混合物分离的精馏塔应用热泵精 馏效果会更好。 馏效果会更好。5Fra bibliotek2 精馏节能技术
精馏节能技术
热泵精馏工艺分析化工行业是能耗大户,其中精馏又是能耗极高的单元操作,而传统的精馏方式热力学效率很低,能量浪费很大。
如何降低精馏塔的能耗,充分利用低温热源,已成为人们普遍关注的问题。
对此人们提出了许多节能措施,通过大量的理论分析、实验研究以及工业应用表明其中节能效果比较显著的是热泵精馏技术。
热泵精馏是把精馏塔塔顶蒸汽加压升温,使其用作塔底再沸器的热源,回收塔顶蒸汽的冷凝潜热。
热泵精馏在下述场合应用,有望取得良好效果:(1)塔顶和塔底温差较小,因为压缩机的功耗主要取决于温差,温差越大,压缩机的功耗越大。
据国外文献报导,只要塔顶和塔底温差小于36°C,就可以获得较好的经济效果。
(2)沸点相近组分的分离,按常规方法,蒸馏塔需要较多的塔盘及较大的回流比,才能得到合格的产品,而且加热用的蒸汽或冷却用的循环水都比较多。
若采用热泵技术一般可取得较明显的经济效益。
(3)工厂蒸汽供应不足或价格偏高,有必要减少蒸汽用量或取消再沸器时。
(4)冷却水不足或者冷却水温偏高、价格偏贵,需要采用制冷技术或其他方法解决冷却问题时。
(5)—般蒸馏塔塔顶温度在38〜138C之间,如果用热泵流程对缩短投资回收期有利就可以采用,但是如果有较便宜的低压蒸汽和冷却介质来源,用热泵流程就不一定有利。
(6)蒸馏塔底再沸器温度在300C以上,采用热泵流程往往是不合适的。
以上只是对一般情况而言,对于某个具体工艺过程,还要进行全面的经济技术评定之后才能确定。
根据热泵所消耗的外界能量不同,热泵精馏可分为蒸汽加压方式和吸收式两种类型1.蒸汽加压方式蒸汽加压方式热泵精馏有两种:蒸汽压缩机方式和蒸汽喷射式。
1.1蒸汽压缩机方式蒸汽压缩机方式又可分为间接式、塔顶气体直接压缩式、分割式和塔釜液体闪蒸再沸式流程。
1.1.1间接式当塔顶气体具有腐蚀性或塔顶气体为热敏性产品或塔顶产品不宜压缩时,可以采用间接式热泵精馏,见图1。
图1间接式热泵精馏流程图它主要由精馏塔、压缩机、蒸发器、冷凝器及节流阀等组成。
化工精馏技术的应用及节能研究
化工精馏技术的应用及节能研究摘要:化工行业应积极开展节能减排工作,优化改革化工生产过程,达到降耗节能的目的,同时减少对生态环境的污染与破坏。
化工行业的发展,为人们生产生活带来了便利,但也带来了环境污染和能源浪费问题。
因此,实现化工行业可持续发展,必须采取节能减排措施,优化化工生产过程,降低能耗和污染。
化工生产过程分离与反应两个过程,其中分离过程所造成的能源消耗量占据整体能源消耗量的75%。
这是化工生产中能源浪费的主要原因,因此,降低分离过程的能耗是化工行业节能减排的一个重要方向。
关键词:化工;精馏;节能技术;应用1化工精馏分析化工蒸馏技术是将不同性质的物料放入蒸馏塔装置中,通过塔板装置实现传质传热,在塔板中进行汽化分离。
传统的蒸馏技术虽然可以实现物料的分离,但是会造成大量的蒸汽损耗,导致能源浪费。
为了实现节能降耗,化工精馏技术应运而生。
化工精馏技术能够合理利用多余热量,实现能源的有效利用。
但是,化工精馏技术受到许多因素的影响,如回流比例、环境温度、塔内压力、物料量等,需要注重控制。
如果这些因素不能得到有效的控制,将会导致化工精馏技术的效率降低,甚至出现质量问题。
传统的化工精馏需要大量能源物质加热蒸馏塔底部结构,且存在热量损耗与能源浪费现象。
因此,需要创新研发高效应用化工精馏节能降耗技术。
这样不仅可以降低能源消耗,减少对环境的影响,还可以提高生产效率,降低生产成本,推动化工行业的可持续发展。
化工精馏技术是化工行业中的重要技术之一,它的应用能够实现物料的分离和能源的节约。
在未来的发展中,化工精馏技术需要不断创新,应用高效节能降耗技术,实现更加可持续的发展。
2化工精馏高效节能技术开发及应用的现实意义2.1有助于提高化工精馏过程的效率与质量化工精馏在许多工业领域中都扮演着重要的角色,它能够将混合物质分离出不同的组分,达到纯净度的要求。
然而,精馏蒸馏塔的多流程串联运行特点使得化工精馏过程中的能量损耗现象比较严重。
精馏节能减耗总结
精馏节能减耗总结引言在许多化学工艺中,精馏作为一种常见的分离技术,广泛应用于石油化工、化学制药、能源等行业。
然而,传统的精馏过程存在能源消耗大的问题。
为了减少精馏过程中的能源消耗,提高能源利用率,许多节能减耗技术被引入并逐渐得到应用。
本文将对精馏节能减耗的相关技术进行总结,包括辅助加热装置、改进的精馏塔结构以及新型精馏塔填料等。
通过这些节能减耗技术的应用,精馏过程的能耗问题可以得到一定程度的改善,从而实现能源的可持续利用。
辅助加热装置传统的精馏过程中,常常需要大量的蒸汽或热能来提供塔底部的加热需求。
为了减少能源的消耗,引入一些辅助加热装置可以起到节能降耗的效果。
多效加热器多效加热器是一种高效的辅助加热装置,能够通过热传递的方式将高温废热回收利用。
其原理是在精馏塔的塔顶和塔底之间设置多级的加热器,利用顶部产生的低温蒸汽将底部的高温液体加热,从而实现能量的再利用。
热泵热泵是另一种常用的辅助加热装置,通过将低温的热能转移到高温区域,从而实现能量的传递和利用。
在精馏过程中,可以利用热泵将废热转化为可用的热能,供给精馏塔的加热需求。
这样不仅可以减少能源的消耗,还可以达到能源利用的最大化。
改进的精馏塔结构传统的精馏塔结构存在一些不利于能源节约的问题,如传质效率低、压力损失大等。
通过改进精馏塔的结构,可以减少能源的消耗,提高精馏效率。
塔板结构优化传统的精馏塔中,常见的结构是塔板结构,它的主要问题是传质效率低。
为了提高传质效率,可以引入一些新的塔板结构,如泡沫塔板、视窗塔板等。
这些新型塔板结构具有更大的表面积和更好的传质性能,能够有效地提高精馏效率,降低能源消耗。
塔内增加填料层除了改进塔板结构,也可以在精馏塔内部增加填料层,以增加界面面积,提高传质效果。
常见的填料包括金属填料、陶瓷填料、塑料填料等。
这些填料具有较大的表面积和较好的传质性能,能够增加相接触的机会,从而提高传质效率,减少能源消耗。
新型精馏塔填料塔填料作为精馏过程中的重要组成部分,对其传质效率和能源消耗有着直接的影响。
- 1、下载文档前请自行甄别文档内容的完整性,平台不提供额外的编辑、内容补充、找答案等附加服务。
- 2、"仅部分预览"的文档,不可在线预览部分如存在完整性等问题,可反馈申请退款(可完整预览的文档不适用该条件!)。
- 3、如文档侵犯您的权益,请联系客服反馈,我们会尽快为您处理(人工客服工作时间:9:00-18:30)。
热泵精徭工艺分析化工行业就是能耗大户,其中精镭又就是能耗扱鬲得单元揀作,而传统得精餾方式热力学效率很低,能量浪费很大。
如何降低精憎塔得能耗,充分利用低温热源,已成为人们普遍关注得问题。
对此人们提出了许多节能措施,通过大董得理论分析、实验研究以及工业应用表明其中节能效果比较显著得就是热泵精憎技术。
热泵精馅就是把精馅塔塔顶蒸汽加压升温,使其用作塔底再沸器得热源,回收塔顶蒸汽得冷凝潜热。
热泵精餾在下述场合应用,有望取得良好效果:(1)塔顶与塔底温差较小,因为压缩机得功耗主要取决于温差,温差越大,压缩机得功耗越大。
損国外文献报导,只要塔顶与塔底温差小于36°C,就可以获得较好得经济效果。
(2)沸点相近纽分得分离,按常规方法,蒸惚塔需要较多得塔盘及较大得回流比,才能得到合格得产品,而且加热用得蒸汽或冷却用得循环水都比较多。
若釆用热泵技术一般可取得较明显得经济效益。
(3)工厂蒸汽供应不足或价格偏商,有必要减少蒸汽用量或取消再沸器时。
(4)冷却水不足或者冷却水温偏高、价格偏喷■,需要釆用制冷技术或其她方法解决冷却问題吋。
(5)—般蒸憎塔塔顶温度在38〜138°C之间,如果用热泵流程对缩短投资回收期有利就可以釆用,但就是如果有较便宜得低压蒸汽与冷却介质来源,用热泵流程就不一定有利。
(6)蒸餾塔底再沸器温度在300°C以上,釆用热泵流程往往就是不合适得。
以上只就是对一般请况而言,对于某个具体工艺过程,还要进行全面得经济技术评定之后才能确定。
根据热泵所消耗得外界能量不同,热泵赭憎可分为蒸汽加压方式与吸收式两种类型J蒸汽加压方式蒸汽加压方式热泵箱憎有两种:蒸汽压缩机方式与蒸汽喷射式。
1> 1蒸汽压缩机方式蒸汽压缩机方式又可分为间接式、塔顶气体直接压缩式.分割式与塔釜液体闪蒸再沸式流程。
1> 1. 1间接式当塔顶气体具有腐蚀性或塔顶气体为热敏性产品或塔顶产品不宜压缩时,可以釆用间接式热泵精徭,见图1o图1间接式热泵精馅流程图它主要由祷惚塔、压缩机、蒸发器、冷凝器及节流阀等组成。
这种流程利用单独封闭循环得工质(冷剂)工作:冷剂与塔顶物料换热后吸收热董蒸发为气体,气体经压缩提高压力与温度后,送至塔釜加热釜液,而本身,親结成液体。
液体经节流减压后再去塔顶换热,完成一个循环。
于就是塔顶低温处得热董,通过冷剂得媒介传递到塔釜高温处。
在此流程中,制冷循环中得冷剂冷凝器与塔釜再沸器合为一个设备。
在此设备中冷剂冷凝放热而釜液吸热蒸发。
间接式热泵精鶴得特点就是:(1)塔中要分离得产品与冷剂完全隔离;(2)可使用标准精餾系统,易于设计与控制;(3)与塔顶气体直接压缩式相比较,多一个热交换器(即蒸发器),压缩机需要克服较离得温差与压力差,因此其效率较低。
考虑到工质得化学稳定性,间接式热泵箱镭应用得温度范围限制在130°C左右,而许多有机产品得精馅塔却在较商得温度下操作。
与普通制冷剂相比,水得化学与热稳定性好,泄漏时对人与臭氧层无负效应,价格便宜,而且具有极好得传热特性,在热交换中所需得换热面积较小,特别适合精憎塔底温度较高得赭馅系统。
表1就是以水为工质,用间接式热泵精馅分离乙苯-对二甲苯得节能结果。
虽然单独工质循环式热泵精馅比常规箱憎得总投资费用大,但回收期短,一般在一年之内。
耗能忌黄用常规精偶塔顶直接间接式热热泵精谓泵精谄熬汽十h 26 4) 0电Z 0 1350 1550冷却水E・h 1400 120 140蒸汽•示h ,07 0 20电元・h 0 X7.75 100.75冷却水元• h 45. 5 4.9 4 55总操作费用元小552 5 91.65 1()5.3节能敷益元,h 0 4仇防447. 2投资回收期年U 0.3 4 23麦1不同热泵精餾流程处理乙苯-对二甲苯溶液得节能及经济效果J 1. 2塔顶气体直接压缩式塔顶气体直接压缩式热泵精憎就是以塔顶气体作为工质得热泵,其流程见图2,精憎塔顶气体经压缩机压缩升温后进入塔底再沸器,冷凝放热使釜液再沸,冷凝液经节流阀城压降温后,一部分作为产品出料,另一部分作为精馅塔顶得回流。
图2塔顶气体直接压缩式热泵精憎流程图塔顶气体直接压缩式热泵精馅得特点就是:(1) 所需得载热介质就是现成得;(2) 因为只需要一个热交换器(即再沸器),压缩机得压缩比通常低于单独工质循环式得压缩 比; (3) 系统简单,稳定可靠。
塔顶气体直接压缩式热泵精餾适合应用在塔顶与塔底温度接近,或被分离物质因沸点接近难 以分离,必须釆用较大回流比得情况下,因此需要消耗大量加热蒸汽(即离负荷得再沸器),或 在低压运行必须釆用冷冻剂进行冷凝。
为了使用冷却水或空乞作冷凝介质,必须在较高塔压 下分离菜些易挥发物质得场合。
塔顶气体直接压缩式热泵精餾应用十分广泛,如丙烯-丙烷得分离釆用该流程,其热力学效率 可以从3、6%提离到8、1%,节能与经济效益非常显著。
菜厂釆用热泵精餾得结果见麦2,由此可见,当选用热泵精馅时,能源费用急剧下降。
此时,冷 却水温度已不再就是决定因素,赭镭塔可在更低得压力下操作,既简化了分离过程,又降低了 设备成本。
表2不同精镭形式下丙烯-丙烷分离得节能与经济效果比较1、1、3分割式热泵 分割式热泵精憎组成及其流程如图3所示。
图3分割式热泵精馅流程图分割式热泵焙憎流程分为上、下两塔,上塔类似于直接式热泵赭馅,只不过多了一个进料口;压 缩 机下塔则类似于常规箱镭得提馅段即蒸出塔,进料来自上塔得釜液,蒸汽則进入上塔塔底。
分割式热泵精馅得节能效果明显,投资费用适中,控制简单。
分割式热泵箱憎得特点就是可通过控制分割点浓皮(即下塔进料浓度)来调节上塔得温差,从而选择合适得压缩机。
在实际设计时,分割点浓度得优化就是很必要得。
分割式热泵箱徭适用于分离体系物得相图存在恒浓区与恒柿区得大温差精馅,如乙醇水溶液、异丙醇水溶液等。
表3就是菜工厂釆用常规精馅、塔顶直接式热泵精镭与分割式热泵焙镭工艺处理异丙醇水溶液得结果。
耗能及费用常规精憾塔顶直接热泵精馆分割式热泵精谓藝汽"h」36 () 2电{)2400 1200冷却水5宀IV 1 (X)() HX) HM)萎汽/元• h- 1350 0 20电/元・厂() 16X K4冷却水•'元・h" 20总操作裁用/元小」:57(> 170 106节能效益/元小」() 2(X> 264表3不同精镭形式下异丙醇溶液分离得节能与经济效果比较从表3可以瞧出,分割式可选择单级压缩机,其耗电量大大降低;而塔顶直接式就必须选择昂贵得多级压缩机。
其耗电量几乎就是分割式得2倍。
1、1、4闪蒸再沸闪蒸再沸就是热泵得一种变型,它以釜液为工质,其流程如图4所示。
与塔顶气体直接压缩式相似,它也比间接式少一个换热器,适用场合也基本相同。
不过,闪蒸再沸在塔压高时有利,而塔顶气体直接压缩式在塔压低时更有利。
图4闪蒸再沸式热泵精憎流程图1、2蒸汽喷射式图5就是釆用蒸汽喷射泵方式得蒸汽汽提减压精憎工艺流程。
在该流程中,塔顶蒸汽就是稍含低沸点组成得水蒸乞,其一部分用蒸汽喷射泵加压升温,随駆动蒸汽一起进入塔底作为加热蒸汽。
蒸汽(40) 詆汽在传统方式中,如果进料预热需蒸汽量10,再沸器需蒸汽# 30,则共需蒸汽量40。
而在釆用蒸汽喷射式热泵得精憎中,用于进料预热得蒸汽童不变,但由于向蒸汽喷射泵供给驱动蒸汽15就可得到用于再沸器加热得蒸汽30,故蒸汽消耗量就是25,可节省37、5%得蒸汽量,所以节能效果十分显箸。
釆用蒸汽喷射泵方式得热泵赭馅具有如下优点:(1)新增设备只有蒸汽喷射泵,设备费用低;⑵蒸汽喷射泵没有转动部件,容易维修,而且维修费用低。
蒸汽喷射式热泵精餾如果在大压缩比或离真空度条件下操作,蒸汽喷射泵得驱动蒸汽量增大, 再循环效果显著下降。
因此,这种方式得热泵精憎适合应用在:(1)精餾塔塔底与塔顶得压差不大;(2)减压精镭得真空度比较低得情况下°2吸收式吸收式热泵由吸收器、再生器、冷却器与再沸器等设备纽成,常用涣化蚀水溶液或氣化钙水溶液为工质。
由再生器送来得浓涣化锂溶液在吸收器中遇到从再沸器送来得蒸汽,发生了强烈得吸收作用,不但升温而且放出热董<Q吸〉,该热量即可用于赭镭塔蒸发器,实际上热泵得吸收器即为精憎塔得蒸发器。
浓涣化锂溶液吸收了蒸汽之后,浓度变稀,即送再生器蒸浓。
再生器所耗用得热能<Q生〉就是热泵得原动力。
从再生器中蒸发出来得水蒸气,在冷却器中冷却、冷凝,而后送入精餾塔冷凝器,在此冷凝器中,塔顶憎出物被冷凝,而水又电新蒸发进入吸收器。
由此可见,精餾塔得冷凝器也就是热泵得再沸器,详见图6。
图6吸收式热泵精馅流程图吸收式热泵按照机内循环方向得不同可分为:冷凝器压力大于蒸发器压力得第一类吸收式热泵(I型)与蒸发器压力鬲于冷凝器压力得第二类吸收式热泵(II型)。
第一类吸收式热泵需要高温热源驱动,但不需要外界冷却水,热量能得到充分利用,主要应用于产生热水;第二类吸收式热泵可利用低品位热能直接驱动,以低温热源与冷却水之间得温差为推动力,可产生低压蒸汽。
表4吸收式热泵得特点回收余执类型、小余热形式供热温度"c 腿动能量(:(•屮值題厂CI型[卜何)低温黒冰、低压废蒸汽阿瞅)高温水、幡斗"I[型的• 100低温熱水低压废蒸汽irn- 150 砒ctlh的余热0.4X由表4可瞧出:1型吸收式热泵与II型吸收式热泵虽就是吸收式热泵得两大分支,二者原理相似,但由于驱动能量及供热量温度得差异,使二者应用条件有所不同。
一般在余热源温度较低(30〜60?C),用热温度也较低(60〜1000 吋,可用I型热泵,其COP 值可达1、7左右,即消耗1kW驱动能,可以获得1、7kW得可用热。
而在余热源温度较高(60〜100°C)需要得供热温度也较高(100〜150°C)时,可用II型热泵,其COP值约为0、5,即每供给热泵1kW得低温余热,可以获得1>5kW温度较高得可用热,相当于不需要其它代价,就可以舟低温余热得一半左右回收利用。
吸收式热泵与压缩式热泵相比,虽然供热系数COP较小,但避免了使用动力,在动力紧张得情况下,有压缩式热泵所不可替代得优点。
吸收式热泵得优点就是:可以利用温度不离得热源作为动力,如工厂废汽、废热。
除功率不大得溶液泵外没有转动部件,设备维修方便,耗电量小,无噪音。
缺点就是热效率低,需要较高得投资,使用寿命不长。
因此只有在产热量很大、而温皮提升要求不商,并且可用废热直接驱动得情况下,吸收式热泵得工业应用才具有较大得吸引力。
以下就是吸收式热泵得应用举例。
日本某化工厂用II型热泵回收精憎塔有机蒸汽得余热8. 5t/ho 80C得有机余热蒸汽进入热泵得发生器与蒸发器,由吸收器将100C得热水加热到125〉C,经闪蒸获得1kg/cm2(表压)120°C得蒸汽4、25t/h,热泵一年运行以8000h计算,则可节约蒸汽34000to上海通用机械研究所为上海酒薪厂研制II型热泵回收蒸餾塔顶76°C酒精蒸汽23222kW功能量,产生0、5kg/cm2 (表压)得蒸汽1、8t/ho据估算热泵每年收利15万元,装置费用得回收期约为1、5年。