电镀(镀层)质量检测报告
热镀锌角钢质量证明书检测报告

热镀锌角钢质量证明书检测报告自查报告。
为了确保产品质量和安全性,我们对热镀锌角钢进行了自查。
以下是自查报告:
1. 规格和尺寸,我们检查了热镀锌角钢的规格和尺寸,确保符合客户要求和标准规定。
2. 表面质量,我们对热镀锌角钢的表面进行了检查,确保镀锌层均匀、无氧化、无损伤等质量问题。
3. 化学成分,我们对热镀锌角钢的化学成分进行了检测,确保符合相关标准要求。
4. 机械性能,我们进行了拉伸、弯曲等机械性能测试,确保热镀锌角钢的强度和韧性符合标准要求。
5. 包装和标识,我们对热镀锌角钢的包装和标识进行了检查,确保产品包装完好,标识清晰。
通过以上自查,我们确认热镀锌角钢的质量符合相关标准和客户要求,可以放心使用。
自查人,(签名)日期,(年/月/日)。
常用电镀产品质量检验标准

电镀产品质量检验规范电镀产品品质检验规范常用的检验项目为:1.膜厚;2.装配检查;3.镀层附着力;4.硬度测试;5.耐磨测试;6.耐酒精测试;7.高温高湿测试;8.冷热冲击测试;9.盐雾测试;10.排汗测试;11外观;12包装;一.膜厚:1.膜厚为电镀检测基本项目,使用基本工具为萤光膜厚仪(X-RAY),其原理是使用X射线照射镀2.3.1.2.3.1.将3M10a)b)d)2.3.1.真空镀:2H铅笔,500g力水镀测试:1H铅笔,200g力2.检查周期:每批;3.测试数量:n>2pcs ;五.耐磨测试:1.头施500g力,用于被测产品来回试擦50次,往返为一次,不能变色,脱镀及露底材;2.检查周期:一次/3个月3.数量:n>2pcs ;六.耐酒精测试:1.用500g砝码外包8层棉布,再将白棉布沾湿浓度为95%的乙醇,以不下滴为宜,将砝码与镀层面垂直,在同一位置往退,移动距离1英寸为一次,共100次,镀层不能有反应;2.检查周期:一次/3个月;3.测试数量:n>5pcs ;七.高温高湿测试:1.ABS底材温度设定为60度,PC底材温度设定为90度,湿度90%-95%,测试时间6小时,看镀层有无拱起,起泡或脱落;2.检查周期:一次/3个月;3.测试数量:n>5pcs ;1.2.3.其中:1.2.3.1.2.3.4.十一.12.??表面镀层符合规定要求,光滑、平整、均匀光亮,同批产品无色差(注:色差包括颜色和光泽度);3..镀层表面不得有如下缺陷:(1)起泡:镀层与基体因局部剥离致表面呈气泡现象;(2)脱皮:镀层与基体有剥离现象;镀层成片状脱离基体材料的现象(3)烧焦:在过高电流下形成的颜色黑暗、粗糙、松散等质量不佳的沉积物,其中常含有氧化物或其它杂质。
(4)麻点:在电镀或腐蚀中,与金属表面上形成的小坑或小孔(5)粗糙:在电镀过程中,由于种种原因造成的镀层粗糙不光滑的现象.(6)水印、色斑:通常用于表面被污染所引起的不均匀润湿性,使表面上的水膜变的不连续。
常用电镀产品质量检验标准
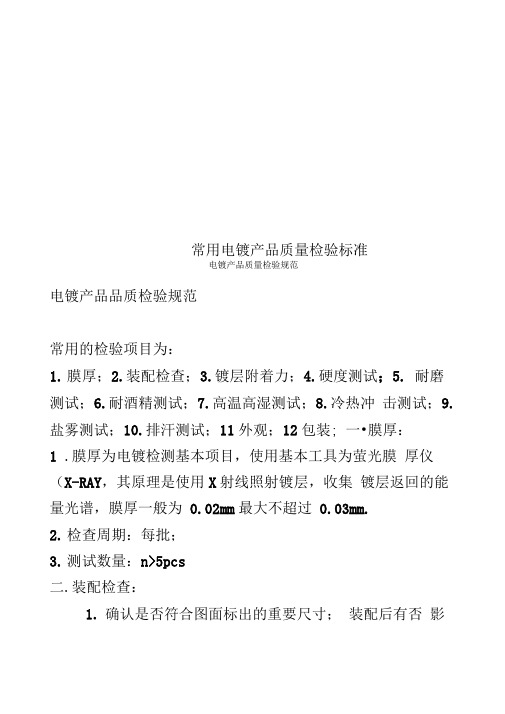
常用电镀产品质量检验标准电镀产品质量检验规范电镀产品品质检验规范常用的检验项目为:1.膜厚;2.装配检查;3.镀层附着力;4.硬度测试;5. 耐磨测试;6.耐酒精测试;7.高温高湿测试;8.冷热冲击测试;9.盐雾测试;10.排汗测试;11外观;12包装; 一•膜厚:1 .膜厚为电镀检测基本项目,使用基本工具为萤光膜厚仪(X-RAY,其原理是使用X射线照射镀层,收集镀层返回的能量光谱,膜厚一般为0.02mm最大不超过0.03mm.2.检查周期:每批;3.测试数量:n>5pcs二.装配检查:1.确认是否符合图面标出的重要尺寸;装配后有否影响外观及功能,手感;2.检查周期:每批;%3.测试数量:n>2pcs ;0「二.镀层附着力:1.将3M胶纸粘贴在刀切100格(每小格为1MM T 1MM 的电镀层表面,用橡皮擦在其上面来回磨擦,使其完全密贴后,以45度方向迅速撕开,镀层需无脱落现象。
如目视无法观察清楚,可使用10倍显微镜观察;•a)不可有掉落金属粉末及补胶带粘起之现象。
b)不可有金属镀层剥落之现象。
d)不可有起泡之现象2.检查周期:每批;3.测试数量:n>2pcs ;…四•硬度测试:1.用中华铅笔以45度角并且以1mm/s的速度向前推进,擦试后镀层不能有划痕;.其中:UV镀测试:3H铅笔,500g力真空镀:2H铅笔,500g力…水镀测试:1H铅笔,200g力2.检查周期:每批;-…3.测试数量:n>2pcs ;五.耐磨测试:1.头施500g力,用于被测产品来回试擦50次,往返为一次,不能变色,脱镀及露底材;e2.检查周期:一次/3个月3.数量:n>2pcs ;六•耐酒精测试:1.用500g砝码外包8层棉布,再将白棉布沾湿浓度为95%勺乙醇,以不下滴为宜,将砝码与镀层面垂直,在同一位置往退,移动距离1英寸为一次,共100次, 镀层不能有反应;2.检查周期:一次/3个月;…•3.测试数量:n>5pcs ;七.高温高湿测试:1.ABS底材温度设定为60度,PC底材温度设定为90度,湿度90沧95%测试时间6小时,看镀层有无拱起,起泡或脱落;62.检查周期:一次/3个月;3.测试数量:n>5pcs ;八.冷热冲击测试:1.零下1度30分钟常温2分钟,70度30分钟为一个回合,看镀层有无拱起,起泡或脱落;2.检查周期:一次/3个月;3.测试数量:n> 5pcs;其中:UV镀测试: 5回合; 真空镀:2回合;水镀测试:1回合;九.盐雾测试:u1.温度35度,浓度5%勺盐水,喷雾8小时,共3 回;看镀层有无起反应;2.检查周期:一次/3个月;3.测试数量:n>5pcs;十•排汗测试:1.常温下5%Nacl, 10%^酸,85嘯镏水,浸泡24 小时,看镀层有无反应;2.检查周期:一次/3个月;3.测试数量:n>5pcs;4.排汗测试只限定人体与镀层经常接触之电镀零件适用;g A ? -十-一.外观检查:1 •检验条件:在40W-60W日光灯相当照明度条件下,距离30—50cm2. 表面镀层符合规定要求,光滑、平整、均匀光亮,同批产品无色差(注:色差包括颜色和光泽度);3..镀层表面不得有如下缺陷:(1)起泡:镀层与基体因局部剥离致表面呈气泡现象;(2)脱皮:镀层与基体有剥离现象;镀层成片状脱离基体材料的现象$_ 一(3)烧焦:在过高电流下形成的颜色黑暗、粗糙、松散等质量不佳的沉积物,其中常含有氧化物或其它杂质/1 o " ““A(4)麻点:在电镀或腐蚀中,与金属表面上形成的小坑或小孔(5)粗糙:在电镀过程中,由于种种原因造成的镀层粗糙不光滑的现象• n(6)水印、色斑:通常用于表面被污染所引起的不均匀润湿性,使表面上的水膜变的不连续。
镀层湿热试验的质量评定

镀层湿热试验的质量评定良好:色泽变暗,镀层和底层金属无腐蚀;合格:镀层的腐蚀面积不走过镀层面积的1/3,但底层金属除边缘及棱角外无腐蚀;不合格:镀层腐蚀占面积的1/3或更多,或底层金属出现腐蚀。
金属镀层和化学处理层耐蚀性测定结果的评定(一)阴极性镀层经耐蚀性试验后电镀试样的评定一外观等级和保护等级的评定(GB6 461-86)本评级方法是以10*15标准电镀试样暴露在户外天然大气试验为基础的,也用于加速腐蚀试验后试验腐蚀状态的评定。
,如中性盐雾试验、醋酸盐雾试验、铜盐加速醋酸盐雾试验、腐蚀膏试验。
本方法仅适用于对基体为阴极的装饰性和保护性镀层,例如在钢和锌压铸件上镀-镍铬或铜-镍-铬。
本方法一般不用于如钢上镀锌和镀钱财镉的阳极性镀层。
1、评级原则(1) 由于本方法适用于对基体为阴极的装饰性和防护镀层,因此镀层对基体腐蚀的防护能力所评定的等级称为“保护”等级。
而对试样经试验后全面的外观缺陷(包括因暴露而引起的缺陷)所评定的等级称为“外观”等级。
对于单纯的防护性(不是装饰性)阴级镀层,其外观等级可以省略。
(2) 试样检查结果用斜线(/)把两种等级分别记录,保护等级记录在第一位。
(3) 除记录试样的级别外,还应注明影响评级的缺陷种类和严重程度。
2、保护等级的评定根据腐蚀缺陷所覆盖的面积按下计算得出保护等级R=3(2-1gA)式中R—保护等级A---缺陷占总面积的百分数(%)缺陷面积百分数与保护等级的关系见表54-5腐蚀缺陷面积的差别可借助于试样照片及图点图作为比较标准。
(详见ISO4540-86、GB6461-86)常见腐蚀缺陷的类型因大气暴露类型而异。
在海洋大气暴露中典型装饰性镀层往往腐蚀化基体金属严重。
(因此,同一标准的比较照片或比较图不适用于所有地区类型)照片评定对暴露在海洋大气中的试验更作乱,而圆点图则比较适用于工业大气试验。
表54-5缺陷面积(%)与保护等级关系评定过程既要对照标准体系逐一评定,又要对全组试样进行对比评定,以便对各个试样进行复查,确信所评定的等级能真正反映它们之间的优劣。
铁上镀铜实验报告(3篇)

第1篇一、实验目的1. 了解铁上镀铜的原理和方法。
2. 掌握电镀工艺的基本步骤和注意事项。
3. 掌握电镀设备的操作方法。
4. 通过实验,提高动手能力和实验技能。
二、实验原理铁上镀铜是一种电镀工艺,利用电解质溶液中的铜离子在铁表面还原沉积,形成一层铜膜。
电镀过程中,铁作为阴极,铜作为阳极,电解质溶液通常为硫酸铜溶液。
三、实验材料与仪器1. 实验材料:铁片、硫酸铜溶液、电流表、电源、烧杯、玻璃棒、砂纸、胶布等。
2. 实验仪器:电镀槽、直流电源、电镀电源、电镀夹具、量筒、pH试纸等。
四、实验步骤1. 准备工作:将铁片用砂纸打磨干净,去除表面油污和氧化层,并用胶布固定在电镀夹具上。
2. 配制硫酸铜溶液:按照实验要求,准确量取一定量的硫酸铜固体,加入适量的去离子水,搅拌均匀,配制成一定浓度的硫酸铜溶液。
3. 调节pH值:使用pH试纸检测硫酸铜溶液的pH值,根据需要加入适量的稀硫酸或稀氢氧化钠溶液,调节pH值至适当范围。
4. 电镀:将铁片放入电镀槽中,将铜片作为阳极,插入硫酸铜溶液中,连接好电源,调节电流至实验要求。
5. 镀层形成:保持电流稳定,电镀一段时间后,观察铁片表面是否形成均匀的铜膜。
6. 清洗与干燥:电镀完成后,关闭电源,取出铁片,用去离子水冲洗干净,晾干。
五、实验结果与分析1. 实验结果:通过电镀实验,铁片表面成功形成了均匀的铜膜,镀层厚度适中,表面光滑。
2. 结果分析:电镀过程中,硫酸铜溶液中的铜离子在铁表面还原沉积,形成铜膜。
电流密度、温度、时间等因素对镀层质量有较大影响。
在本实验中,通过合理控制电流密度、温度和时间等参数,成功实现了铁上镀铜。
六、实验结论1. 铁上镀铜实验成功,证明了电镀工艺在金属表面处理中的应用价值。
2. 通过实验,掌握了电镀工艺的基本步骤和注意事项,提高了动手能力和实验技能。
七、实验注意事项1. 实验过程中,注意安全,防止触电和烫伤。
2. 配制硫酸铜溶液时,要准确量取硫酸铜固体,避免溶液浓度过高或过低。
电镀车间质量检验标准

电镀车间质量检验标准一、外观质量:1、定义:(1)镀件的主要面为:目测所直观到的表面。
(2)镀件的非主要面为:目测所直观不到的表面,分侧面、背面等。
(3)微缺陷为:面积不大于0.05mm2,深度不大于0.05mm。
麻点、针孔直径不大于0.2mm,划伤深度不大于0.01mm。
2、电镀件的检验条件:应自然散射光下或无反射光的白色透明光线下进行(不得在太阳光直射下检查)。
光照度不应低于300Lx(相当于40W日光灯下距离500mm的光照度,不得借助任何放大工具)。
3、镀件的主要表面(圆柱件除外)不得有漏镀、起皮、针孔、镀花、剥落等任何缺陷。
4、镀件的非主要表在每cm2内允许有两处微缺陷。
对于旋转圆柱件面缺陷只允许对称出现。
5、允许存在的裂纹缺陷应是水封试验合格的,其宽度不应超过0.05mm,高度不大于5mm。
6、对于存在两侧面的产品缺陷只允许出现在一侧,不得左右两侧同时存在。
7、背面。
同时有两个背面的产品,缺陷只允许出现在其中一个背面,不得两个背面同时存在。
8、带有圆孔的镀件,孔周露黄的黄晕半径不得比孔径大2mm以上。
9、只许镀Ni的产品,镀Ni层均匀。
二、盐雾试验:1、铜材质涂、镀层按GB/T10125进行200h盐雾试验后,达到GB/T6461-1986中10级的要求。
锌合金手柄涂、镀层按GB/T10125进行96H盐雾试验后,达到GB/T6461-1986中10级的要求。
方法:使水嘴承受200H的中性盐雾试验,在喷雾进行100H左右,停止喷雾期间,试验箱继续加热,再继续喷雾52H后,应符合“一”的要求,锌合金在喷雾96H后,符合“一”的要求。
三、涂镀层经附着力试验后,不允许出现起皮或脱落现象。
1、工具:质量手册:MLEHIZZ-A-001《产品质量检验标准》中附件C所示工具。
2、方法:用上述工具,在水嘴表面划一个大约15mm×15mm的网格划痕时,手柄表面平行,痕迹相相隔大约8mm,深度应完全切开镀层。
金属电镀实验报告
金属电镀实验报告篇一:实验15 光亮镀锌及化学镀镍实验报告光亮镀锌及化学镀镍1 实验目的1.1 学习和实践氯化钾光亮镀锌的实验室基本操作流程,了解电镀的基本原理和工艺。
1.2 学习并掌握化学镀镍的原理及实验室的操作方法。
2 实验原理电镀是利用电化学方法在金属制品表面上沉积出一层其他金属或合金的过程。
电镀时,镀层金属做阳极,被氧化成阳离子进入电镀液;待镀的金属制品做阴极,镀层金属的阳离子在金属表面被还原形成镀层。
为排除其他阳离子的干扰,使镀层均匀,牢固,需用含镀层金属阳离子的溶液做电镀液,以保持镀层金属阳离子的浓度不变。
电镀层比热浸层均匀,一般都较薄,从几个微米到几十微米不等,电镀能增强金属制品的耐腐蚀性,增加硬度和耐磨性,提高导电性,润滑性,耐热性和表面美观等性能。
化学镀就是在不通电的情况下,利用氧化还原反应在具有催化表面的镀层上,获得金属合金的方法,用于提高抗蚀性和耐磨性,增加光泽和美观。
管状或外形复杂的小零件的光亮镀镍,不必再经抛光,一般将被镀制件浸入以硫酸镍,次亚磷酸钠,乙酸钠和硼酸所配成的混合溶液内,在一定酸度和温度下发生变化,溶液中的镍离子被次亚磷酸钠还原为原子而沉积于制件表面上,形成细致光亮的镍磷合金镀层。
钢铁制件可直接镀镍。
锡,铜和铜合金制件要先用铝片接触于其表面上1-3分钟,以加速化学镀镍。
化学镀镍的反应可简单地表示为:NiSO4+3NaH2PO2+3H2O=Ni+3NaH2PO3+H2SO4+2H2反应还生成磷,形成镍磷合金。
镀液由含有镀覆金属的化合物、导电盐、缓冲剂、pH调节剂和添加剂等的水溶液组成。
通电后,电镀液中的金属离子,在电场作用下移动到阴极上还原成镀层。
阳极的金属形成金属离子进入电镀液,以保持被镀覆的金属离子的浓度。
电镀的工艺过程:镀前处理(机械整平,抛光,除油,酸洗除锈,水洗)——电镀(挂镀或滚镀)——镀后处理(除氢,钝化,封闭,老化)——质量检验。
3 仪器及药品仪器:直流稳压电源,0.5级500mA电流表,水浴锅,电子分析天平,秒表。
电镀年度品质总结报告(3篇)
第1篇一、前言2021年,我司电镀部门在全体员工的共同努力下,严格遵循品质管理原则,不断提升电镀工艺水平,确保产品质量。
现将本年度电镀品质工作总结如下:二、年度品质达成情况1. 产品合格率:本年度电镀产品合格率达到98%,较去年同期提升了2个百分点,表明电镀工艺的稳定性和产品质量得到了有效提升。
2. 客户满意度:根据客户反馈,本年度客户满意度达到90%,较去年同期提高了5个百分点,说明客户对我司电镀产品的认可度有所提升。
3. 不良品率:本年度不良品率为1.5%,较去年同期降低了0.5个百分点,表明我们在不良品预防和控制方面取得了显著成效。
三、上年度及本年度品质对比情况1. 产品合格率:与去年同期相比,本年度产品合格率提升了2个百分点,主要得益于工艺改进和设备更新。
2. 不良品率:与去年同期相比,不良品率降低了0.5个百分点,说明我们在品质管理方面持续改进,效果显著。
3. 客户满意度:与去年同期相比,客户满意度提高了5个百分点,说明我们的产品和服务得到了客户的认可。
四、总结未达成的原因1. 原材料质量波动:本年度部分原材料质量波动较大,导致部分产品性能不稳定。
2. 工艺参数调整:部分产品工艺参数调整不当,影响了产品性能。
3. 人员培训不足:部分员工对电镀工艺的理解和操作技能有待提高。
五、新的一年的品质目标1. 产品合格率:力争将产品合格率提升至99%以上。
2. 客户满意度:将客户满意度提升至95%以上。
3. 不良品率:将不良品率控制在1%以下。
六、措施及计划1. 加强原材料采购管理:严格控制原材料质量,确保产品性能稳定。
2. 优化工艺参数:针对不同产品,优化工艺参数,提高产品性能。
3. 加强人员培训:定期对员工进行电镀工艺培训,提高员工操作技能。
4. 完善品质管理体系:建立健全品质管理体系,确保产品质量稳定。
5. 加强客户沟通:及时了解客户需求,提高客户满意度。
总之,我司电镀部门将继续努力,不断提升品质管理水平,为客户提供优质的产品和服务。
电镀产品通用检测标准
电镀产品通用检测标准电镀产品是一种常见的表面处理工艺,广泛应用于金属制品的防腐蚀、美观提升等方面。
然而,电镀产品的质量问题也时常受到关注,为了保证电镀产品的质量稳定性和可靠性,制定一套通用的检测标准显得尤为重要。
首先,电镀产品的通用检测标准应包括外观质量、镀层厚度、附着力、耐蚀性等方面的内容。
外观质量是电镀产品的首要特征,应当符合相关标准的表面光洁度、色泽和无损伤等要求。
镀层厚度是指电镀产品表面的金属镀层的厚度,其厚度应符合相关标准的要求,以保证产品的质量和使用寿命。
附着力是指金属镀层与基材的结合强度,良好的附着力是保证电镀产品质量的重要因素。
耐蚀性是指电镀产品在特定环境条件下的抗腐蚀能力,对于使用环境苛刻的产品尤为重要。
其次,电镀产品的通用检测标准应当包括检测方法和检测设备的规定。
检测方法是指对电镀产品进行检测时所采用的具体方法和步骤,包括外观检测、厚度测量、附着力测试、耐蚀性测试等内容,应当确保检测方法的科学性和准确性。
检测设备是指用于进行电镀产品检测的设备和仪器,应当符合相关标准的要求,并经过定期的校准和维护,以保证检测结果的准确性和可靠性。
最后,电镀产品的通用检测标准还应包括质量控制和质量管理的要求。
质量控制是指在电镀产品生产过程中对产品质量进行控制和监测的活动,应当建立完善的质量控制体系,并对关键工艺参数进行严格控制,以确保产品质量的稳定性。
质量管理是指对电镀产品质量进行全面管理和控制的活动,应当建立质量管理体系,并对产品质量进行全面监测和评估,以持续改进产品质量。
总之,制定一套通用的电镀产品检测标准对于保证产品质量和提升企业竞争力具有重要意义。
只有建立科学、合理的检测标准,才能有效地保障电镀产品的质量稳定性和可靠性,满足市场和客户的需求。
希望各相关企业和机构能够重视电镀产品的质量检测工作,加强标准制定和质量管理,共同推动电镀产品行业的健康发展。
电镀相关测试报告
2 PASS PASS PASS PASS PASS
3 PASS PASS PASS PASS PASS 不合格
4 PASS PASS PASS PASS PASS
5 PASS PASS PASS PASS PASS
结合力测试报告
测试日期: 供应商: 名称: 型号: 生产日期:
镀层厚度:
材质:
数量:
可焊性测试报告
测试日期: 供应商: 数量: 名称: 镀种: 化学镀镍 型号:
物料编码:
生产日期:
镀层厚度:
材质: 批次号:
订单号:
测பைடு நூலகம்要求
1.锡膏:alpha OL-107E(有铅)、alpha SAC305 OM-338(无铅) 2.用棉花蘸取酒精清洁待验证底板表面,确保其表面无脏污、灰尘、杂质 测试方法 3.将待验证底板表面均匀印刷锡膏 及要求 4.将印刷完成的底板放至平板炉进行加热,炉温220℃。从锡膏开始熔化起 算加热5秒钟后,将其停止加热放至散热片上至完全冷却,观察焊点 底板镀镍:印刷面积收缩率≤90%焊点浸润角≤90°
2 PASS PASS PASS PASS PASS
3 PASS PASS PASS PASS PASS 不合格
4 PASS PASS PASS PASS PASS
5 PASS PASS PASS PASS PASS
膜厚测试报告
测试日期: 供应商: 数量: 镀层种类 名称: 订单号: 膜厚要求 型号: 物料编码: 生产日期: 镀层厚度: 镀层/底材: 材质: 批次号:
镀种:
化学镀镍
物料编码:
订单号:
批次号:
测试要求
1.使用刀口宽度为10~12mm,每格间距为1~1.2mm的百格刀横竖划线形成 10*10的100格正方形,百格刀划下去应可见底材 2.使用毛刷对百格区域内对角线方向各刷五次,清理表面脏污及毛屑 测试方法 3.使用3M Transparent Tape 600胶带贴于百格位置,用手指压下将胶带紧 及要求 密贴附,垂直方向使用瞬间的力道将胶带拉起 4.将零件放入恒温箱中,使其在190±10℃下保持1h,然后立即放入室温冷 水中冷却。
- 1、下载文档前请自行甄别文档内容的完整性,平台不提供额外的编辑、内容补充、找答案等附加服务。
- 2、"仅部分预览"的文档,不可在线预览部分如存在完整性等问题,可反馈申请退款(可完整预览的文档不适用该条件!)。
- 3、如文档侵犯您的权益,请联系客服反馈,我们会尽快为您处理(人工客服工作时间:9:00-18:30)。
保温时间
试验结果
检验员:
日期:
主管:日期:
电镀(镀层)质量检测报告
客户名称:产品编号:产品名称:生产日期:
防腐(盐雾)性能试验
盐雾试样类型
________小时中性( NSS )
________小时酸性( ASS )
________小时铜加速( CASS )
试样数量
依据规范
试样材质
□ABS基体镀镍
□ABS基体镀酸铜
□ABS基体镀铜镍铬
□ABS+PC基体镀镍
□ABS+PC基体镀酸铜
□ABS+PC基体镀铜镍铬
盐雾箱温度
饱和器温度
配制溶液PH值
盐雾沉降量
收集溶液PH值
试验时间
自年月日时分
至年月日时分
合计小时连续试验
配制溶液比重
试验结果
镀层厚度试验
检测情况
检测情况
镀层种类
第一值
第二值
第三值
镀层种类
第一值
第பைடு நூலகம்值
第三值
备注
镀层结合力试验
试验方法
检验仪器
试验温度
试样材质