薄壁圆筒零件车削加工
薄壁零件的数控车削加工探讨
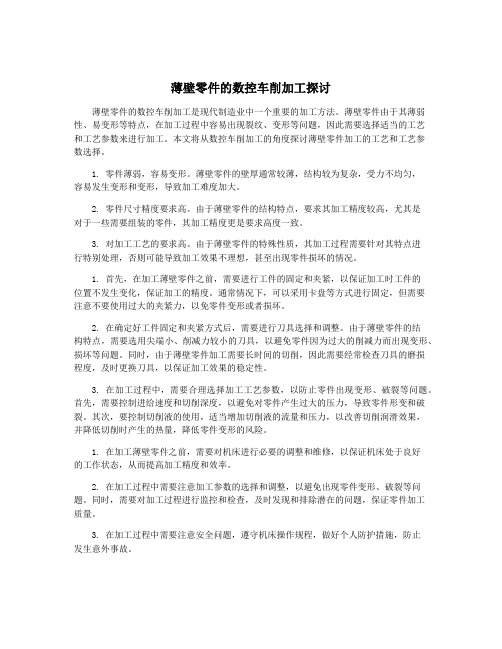
薄壁零件的数控车削加工探讨薄壁零件的数控车削加工是现代制造业中一个重要的加工方法。
薄壁零件由于其薄弱性、易变形等特点,在加工过程中容易出现裂纹、变形等问题,因此需要选择适当的工艺和工艺参数来进行加工。
本文将从数控车削加工的角度探讨薄壁零件加工的工艺和工艺参数选择。
1. 零件薄弱,容易变形。
薄壁零件的壁厚通常较薄,结构较为复杂,受力不均匀,容易发生变形和变形,导致加工难度加大。
2. 零件尺寸精度要求高。
由于薄壁零件的结构特点,要求其加工精度较高,尤其是对于一些需要组装的零件,其加工精度更是要求高度一致。
3. 对加工工艺的要求高。
由于薄壁零件的特殊性质,其加工过程需要针对其特点进行特别处理,否则可能导致加工效果不理想,甚至出现零件损坏的情况。
1. 首先,在加工薄壁零件之前,需要进行工件的固定和夹紧,以保证加工时工件的位置不发生变化,保证加工的精度。
通常情况下,可以采用卡盘等方式进行固定,但需要注意不要使用过大的夹紧力,以免零件变形或者损坏。
2. 在确定好工件固定和夹紧方式后,需要进行刀具选择和调整。
由于薄壁零件的结构特点,需要选用尖端小、削减力较小的刀具,以避免零件因为过大的削减力而出现变形、损坏等问题。
同时,由于薄壁零件加工需要长时间的切削,因此需要经常检查刀具的磨损程度,及时更换刀具,以保证加工效果的稳定性。
3. 在加工过程中,需要合理选择加工工艺参数,以防止零件出现变形、破裂等问题。
首先,需要控制进给速度和切削深度,以避免对零件产生过大的压力,导致零件形变和破裂。
其次,要控制切削液的使用,适当增加切削液的流量和压力,以改善切削润滑效果,并降低切削时产生的热量,降低零件变形的风险。
1. 在加工薄壁零件之前,需要对机床进行必要的调整和维修,以保证机床处于良好的工作状态,从而提高加工精度和效率。
2. 在加工过程中需要注意加工参数的选择和调整,以避免出现零件变形、破裂等问题。
同时,需要对加工过程进行监控和检查,及时发现和排除潜在的问题,保证零件加工质量。
15-5PH不锈钢薄壁筒形零件车削工艺
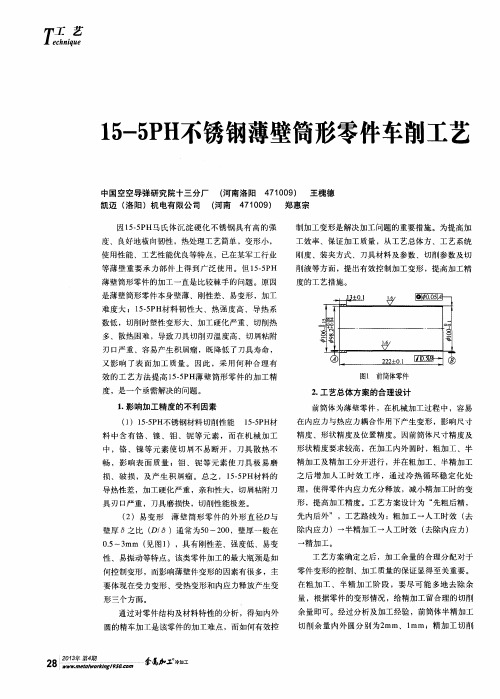
精加工。 工艺方案确定之后 ,加 工余量的合理分配对于
零 件 变形 的 控制 、加 工 质量 的 保证 显 得 至 关重 要 。
在粗 加工 、半精 加工阶 段 ,要尽可 能 多地 去除余 量 ,根据零件的变形情况 ,给精加工留合理的切 削 余量即可。经过分析及加工经验 ,前筒体半精加 工 切 削余量内外 圆分别为2 am、l r mm;精加工切 削
难 度大 ;1 5 — 5 P H材 料 韧 性 大 、热 强度 高 、导 热 系
oI 0 . 0 5 I A 卜 _ 一
数低 ,切削时塑性变形大、加工硬化严重、切削热
一
多、散热困难 ,导致刀具切削刃温度高 、切屑粘附
刃I : 1 严重、容易产生积屑瘤 ,既降低 了刀具寿命 , 又影响 了表 面加工 质量 。因此 ,采用何种 合理有 效的工艺方法提高 1 5 — 5 P H薄壁筒形零件的加工精 度 ,是一个亟需解决的问题 。
3 . 提高 工艺系统 刚度
为提高前简体加工工艺系统刚度 ,在进 行内圆
9 , T - 时 ,采 取 了合理 设 置 工 艺 台阶 法 ,以具 有 一 定
够满 足尺 寸精度 、表面 质量及相 关技术 条件的要
求。
刚性 ( 厚度 )的工艺台阶作为零件的装夹、定位基 准 ,并设计加长软爪 ( 有两处定位夹持面)装夹加 工 ,完成零 件尺寸加工后 ,最终将工艺台阶去除 ; 在进行外圆加工时 ,采取了填充防振物机械加工方 法 ,即零 件一端 ( 设置有工艺台阶端 )以内软爪反 撑夹持 ,将泡沫塑料、软性橡胶或发 泡材料等轻软 之物填充至零件内孔中,与零件内壁贴合一体不脱 落 ,并配专用堵头于尾部顶紧零件,完成装夹之后 加工 ( 可采用两端堵头顶紧方式)。内圆加工装夹 示意如 图2 所示 ,外圆粗 、半精加工装夹示意如 图3
薄壁筒类零件车削加工方法
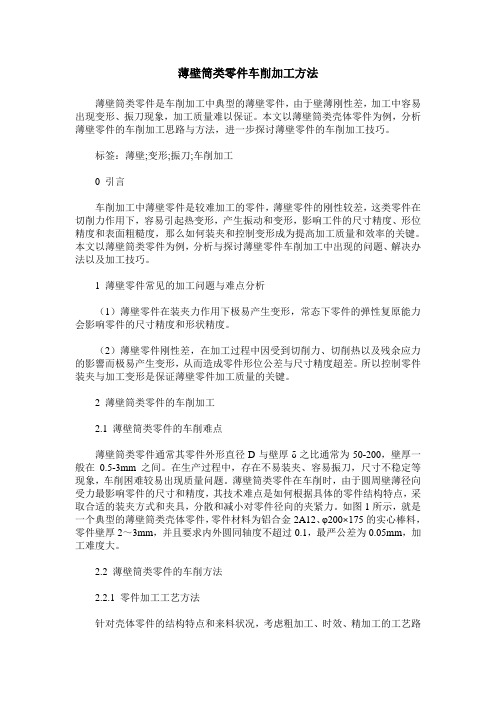
薄壁筒类零件车削加工方法薄壁筒类零件是车削加工中典型的薄壁零件,由于壁薄刚性差,加工中容易出现变形、振刀现象,加工质量难以保证。
本文以薄壁筒类壳体零件为例,分析薄壁零件的车削加工思路与方法,进一步探讨薄壁零件的车削加工技巧。
标签:薄壁;变形;振刀;车削加工0 引言车削加工中薄壁零件是较难加工的零件,薄壁零件的刚性较差,这类零件在切削力作用下,容易引起热变形,产生振动和变形,影响工件的尺寸精度、形位精度和表面粗糙度,那么如何装夹和控制变形成为提高加工质量和效率的关键。
本文以薄壁筒类零件为例,分析与探讨薄壁零件车削加工中出现的问题、解决办法以及加工技巧。
1 薄壁零件常见的加工问题与难点分析(1)薄壁零件在装夹力作用下极易产生变形,常态下零件的弹性复原能力会影响零件的尺寸精度和形状精度。
(2)薄壁零件刚性差,在加工过程中因受到切削力、切削热以及残余应力的影響而极易产生变形,从而造成零件形位公差与尺寸精度超差。
所以控制零件装夹与加工变形是保证薄壁零件加工质量的关键。
2 薄壁筒类零件的车削加工2.1 薄壁筒类零件的车削难点薄壁筒类零件通常其零件外形直径D与壁厚δ之比通常为50-200,壁厚一般在0.5-3mm之间。
在生产过程中,存在不易装夹、容易振刀,尺寸不稳定等现象,车削困难较易出现质量问题。
薄壁筒类零件在车削时,由于圆周壁薄径向受力最影响零件的尺寸和精度,其技术难点是如何根据具体的零件结构特点,采取合适的装夹方式和夹具,分散和减小对零件径向的夹紧力。
如图1所示,就是一个典型的薄壁筒类壳体零件,零件材料为铝合金2A12、φ200×175的实心棒料,零件壁厚2~3mm,并且要求内外圆同轴度不超过0.1,最严公差为0.05mm,加工难度大。
2.2 薄壁筒类零件的车削方法2.2.1 零件加工工艺方法针对壳体零件的结构特点和来料状况,考虑粗加工、时效、精加工的工艺路线,先粗车,时效后再精车外圆及右侧内孔尺寸。
薄壁圆筒零件车削加工
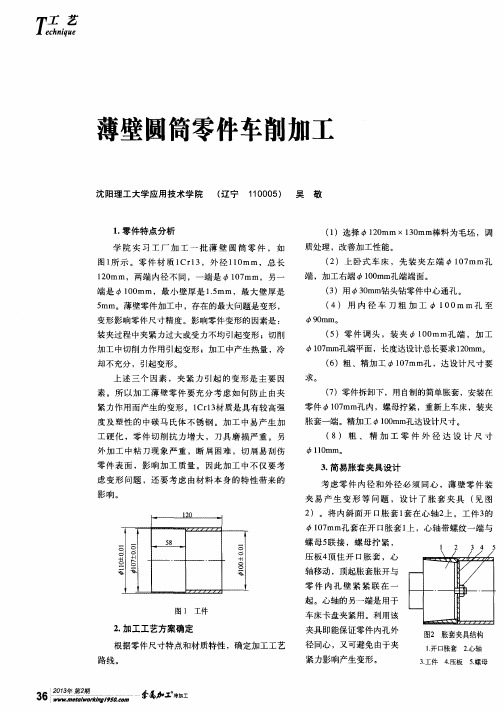
( 3 )铣 工 :铣 两端 保 证4 0 mm。
( 4 )钳 工 :钻、攻两处M3 深1 0 mm,并校形
图 1
保证 1 2 0 m m。
1 . 原先 的工艺
根据展开总长在两端加入适 当的余量 ,在 不锈 钢棒的一端套入加 力杆 ,利用图2 中的销柱5 和销柱
2 . 原 工艺不足之处分析
加工 中切 削力作用引起变形 ;加工中产生热量 ,冷
却 不 充分 , 引起 变 形 。
( 6 )粗 、精加工 1 0 7 mm ̄ L ,达设计尺寸要
求。
上述 三个 因素 ,夹 紧力 引起 的变形是 主要 因
素 。所以加 工薄壁零 件要充分 考虑如 何防止 由夹
紧力作用而产生的变形。1 Cr 1 3 材质是具 有较高 强 度 及塑性 的中碳马 氏体不锈钢 。加工 中易产生加 工硬化 ,零 件切 削抗 力增大 ,刀具磨 损严重 。另 外加 工 中粘 刀现象严 重 ,断 屑困难 ,切屑易刮 伤 零件 表面 ,影 响加工 质量 。因此加工 中不仅要 考
考 虑零件 内径和 外径 必须 同心 ,薄 壁零 件装
夹 易 产生 变 形 等 问题 ,设 计 了胀 套 夹具 ( 见图
2 ) 。 将 内 斜 面 开 口胀 套 1 套在心轴2 上 。工 件 3 的
虑 变形 问题 ,还要考 虑 由材料 本身的特 性带来 的
影 响。
1 0 7 mm ̄ L 套在开 口胀套1 上 ,心轴带螺纹一端与
( 1 )选择 1 2 0 mm×1 3 0 mm棒料为毛坯 ,调 质处理 ,改善加 工性能。 ( 2 )上卧式 车床 ,先 装夹 左端 1 0 7 mm ̄ t 端 ,加工右端 l O O mm  ̄ L 端端面。
碳纤维薄壁圆筒;车削加工;最优切削参数
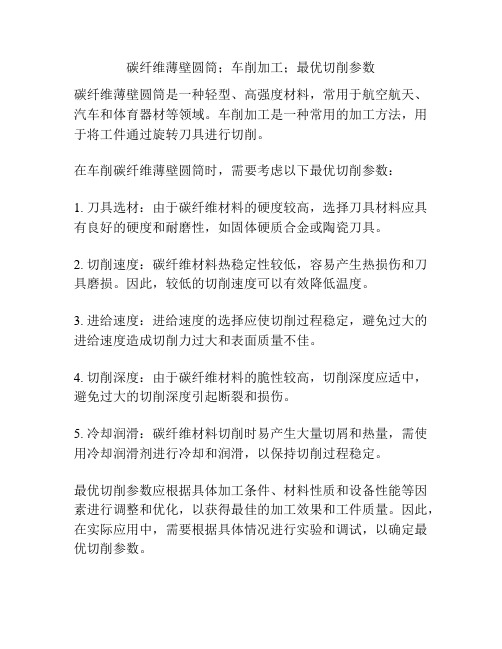
碳纤维薄壁圆筒;车削加工;最优切削参数
碳纤维薄壁圆筒是一种轻型、高强度材料,常用于航空航天、汽车和体育器材等领域。
车削加工是一种常用的加工方法,用于将工件通过旋转刀具进行切削。
在车削碳纤维薄壁圆筒时,需要考虑以下最优切削参数:
1. 刀具选材:由于碳纤维材料的硬度较高,选择刀具材料应具有良好的硬度和耐磨性,如固体硬质合金或陶瓷刀具。
2. 切削速度:碳纤维材料热稳定性较低,容易产生热损伤和刀具磨损。
因此,较低的切削速度可以有效降低温度。
3. 进给速度:进给速度的选择应使切削过程稳定,避免过大的进给速度造成切削力过大和表面质量不佳。
4. 切削深度:由于碳纤维材料的脆性较高,切削深度应适中,避免过大的切削深度引起断裂和损伤。
5. 冷却润滑:碳纤维材料切削时易产生大量切屑和热量,需使用冷却润滑剂进行冷却和润滑,以保持切削过程稳定。
最优切削参数应根据具体加工条件、材料性质和设备性能等因素进行调整和优化,以获得最佳的加工效果和工件质量。
因此,在实际应用中,需要根据具体情况进行实验和调试,以确定最优切削参数。
薄壁类零件的车削工艺分析
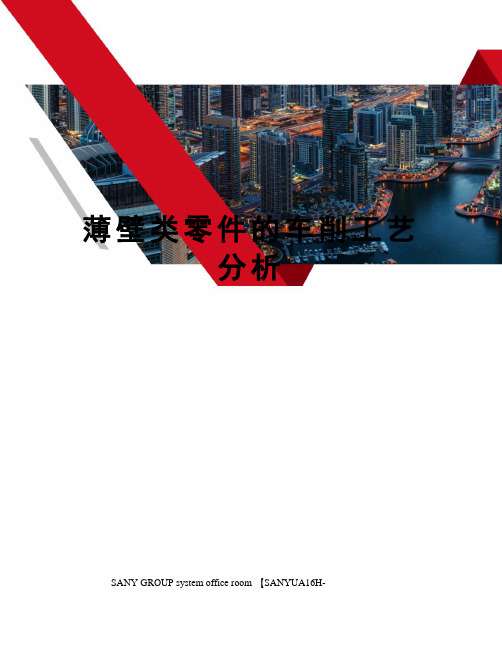
薄壁类零件的车削工艺分析SANY GROUP system office room 【SANYUA16H-薄壁类零件的车削工艺分析段立波一.引言薄壁类零件指的是零件壁厚与它的径向、轴向尺寸相比较,相差悬殊,一般为几十倍甚至上百倍的金属材料的零件,具有节省材料、结构简单等特点。
薄壁类零件已广泛地应用于各类石油机械部件。
但是薄壁类零件的车削加工是比较棘手的,具体的原因是因为薄壁类零件自身刚性差、强度弱,在车削加工中极容易变形,很难保证零件的加工质量。
如何提高薄壁类零件的加工精度是机械加工行业关心的话题。
二.薄壁类零件车削过程中常出现的问题、原因及解决办法我们在车削加工过程中,经常会碰到一些薄壁零件的加工。
如轴套薄壁件(图1),环类薄壁件(图2),盘类薄壁件(图3)。
本文详细分析了薄壁类零件的加工特点、防止变形的装夹方法、车刀材料、切削参数的选择及车刀几何角度。
进行了大量的实验,为以后更好地加工薄壁类零件,保证加工质量,提供了理论依据。
图1轴套薄壁件图2环类薄壁件图3盘类薄壁件1.薄壁类零件的加工特点1.1因零件壁薄,在使用通用夹具装夹时,在夹压力的作用下极易产生变形,而夹紧力不够零件又容易松动,从而影响零件的尺寸精度和形状精度。
如图4所示,当采用三爪卡盘夹紧零件时,在夹紧力的作用下,零件会微微变成三角形,车削后得到的是一个圆柱体。
但松开卡爪,取下零件后,由于零件弹性,又恢复成弧形三角形。
这时若用千分尺测量时,各个方向直径相同,但零件已变形不是圆柱体了,这种变形现象我们称之为等直径变形。
图4三爪卡盘装夹1.2因零件较薄,加工时的切削发热会引起零件变形,从而使零件尺寸难以控制。
对于膨胀系数较大的金属薄壁零件,如在一次安装中连续完成半精车和精车,由切削热引起零件的热变形,会对其尺寸精度产生极大影响,有时甚至会使零件卡死在芯轴类的夹具上。
1.3薄壁类零件加工内孔中,一般采用单刃镗刀加工,此时,当零件较长时,如果刀具参数及切削用量处理不当,将造成排屑困难,影响加工质量,损伤刀具。
薄壁零件的车削技巧

薄壁零件的车削技巧薄壁零件是指壁厚相对较薄的零件,在车削加工中,由于其壁厚薄,容易产生变形和振动,所以需要特殊的车削技巧来保证加工质量。
本文将介绍薄壁零件的车削技巧。
首先,保持机床的稳定性。
薄壁零件在车削时容易产生振动,而振动会影响加工精度和表面质量。
为了保持机床的稳定性,首先要确保机床具备足够的刚性和抗震性,同时要确保机床的紧固件处于良好的状态,以免因紧固件松动而导致振动。
此外,还可以通过合理的刀具和夹具选择来减少振动,例如选择合适的刀具长度和刚度,使用刀柄的支撑力等。
其次,选择合适的切削参数。
在车削薄壁零件时,要选择合适的切削参数,以保证刀具的切削力不会过大。
一般来说,应尽可能采用小的进给量和切削深度,降低切削力。
另外,应注意保持刀具的尖角和刃磨状况良好,以减小刀具的切削力。
第三,选择合适的刀具和夹具。
在车削薄壁零件时,要选择合适的刀具和夹具,以提高加工的稳定性和精度。
刀具要选择具有较高刚度和切削性能的硬质合金刀具,以减小切削力和振动。
夹具要选择刚性好的夹具,以确保零件的稳定夹持,同时要避免夹持过紧而导致变形。
第四,采用适当的刀具路径。
在车削薄壁零件时,为了避免产生振动和变形,应采用适当的刀具路径。
一般来说,应优先选择切削路径中的外切削和镗削,避免内切削和过切削,这样可以减小刀具对零件的负荷,减少振动和变形。
第五,采用适当的刀具进给方式。
在车削薄壁零件时,应采用适当的刀具进给方式,以减小切削力和振动。
一般来说,可以采用铣削进给,即刀具的进给方向与工件的旋转方向相同,这样可以减小刀具对零件的冲击力和振动。
最后,进行切削加工时要进行监控和调整。
在车削薄壁零件时,要进行监控和调整,以确保加工质量。
可以通过加工中的监测手段,例如振动传感器、力传感器等,对加工过程中的切削力、振动等进行监测,及时调整切削参数和刀具路径,以减小振动和变形,保证加工质量。
总之,薄壁零件的车削技巧包括保持机床稳定性、选择合适的切削参数、刀具和夹具、采用适当的刀具路径和进给方式,以及进行监控和调整等。
薄壁圆筒塑件车削加工专用夹具设计

N 00 C 1X 0.0 Y 7 .8F 0 . ( 近 ① ) 0 8 O 2 0 1 3 8 3 0 0 一 N 00 G 0 ( 消 刀 补 ) 0 9 4 撤
再更换  ̄0 m圆柱铣刀进行 z向的对刀操 作。 4m
x , 、】 、Z向 对刀, 如图5 示。 所
N 10 MO ( 0 0 O 暂停 换精 铣刀 ) N 10 M0 6 0( 定精铣主轴转 速并起 动主轴 ) 0 3¥ 0 设 1 N 10C 1X 0.0Y1 37 8 . 一 ①到精 铣切 人点) 0 2 2 0 6 .7 F 0 0( O
柱铣刀 刀心 A点 在工 件 坐标 系 的坐标 为 :A ( 0 0 ; 2 .0
2 3 7 /
图 5  ̄0 m圆柱铣刀对刀示意图 4m
在数控铣 削加 工 中 ,是 以铣 刀 中心 进 行编 程 计算 的,因此在对刀时 , 对刀尺寸应该 加上对刀 时使用 的铣
品。
()二次加工前 a
2 夹具设计及工作原理 .
()夹具结构组 成及 工作 原理 ( 图 3 1 见 、图 4 ) 该夹具包括 左 、右 心 轴 ,其 中左 边 心 轴装 在 车床 卡 盘 上 ,右边 部分装在尾座顶尖 的圆柱上 ,加 工时将顶尖 顶
住圆筒。
车削时,将圆筒装在左边心轴上,并通过定位螺栓
N 1 0 C 1X 0 0 6 . 7 F 0. ( ② ) 0 3 . 0 Y1 3 7 8 0 一 O
- 1、下载文档前请自行甄别文档内容的完整性,平台不提供额外的编辑、内容补充、找答案等附加服务。
- 2、"仅部分预览"的文档,不可在线预览部分如存在完整性等问题,可反馈申请退款(可完整预览的文档不适用该条件!)。
- 3、如文档侵犯您的权益,请联系客服反馈,我们会尽快为您处理(人工客服工作时间:9:00-18:30)。
冷加工
echnique
T
工 艺
沈阳理工大学应用技术学院 (辽宁 110005) 吴 敬
薄壁圆筒零件车削加工
1. 零件特点分析
学院实习工厂加工一批薄壁圆筒零件,如图1所示。
零件材质1C r13,外径110m m ,总长120mm ,两端内径不同,一端是φ107mm ,另一端是φ100m m ,最小壁厚是1.5m m ,最大壁厚是5mm 。
薄壁零件加工中,存在的最大问题是变形,变形影响零件尺寸精度。
影响零件变形的因素是:装夹过程中夹紧力过大或受力不均引起变形;切削加工中切削力作用引起变形;加工中产生热量,冷却不充分,引起变形。
上述三个因素,夹紧力引起的变形是主要因素。
所以加工薄壁零件要充分考虑如何防止由夹紧力作用而产生的变形。
1Cr13材质是具有较高强度及塑性的中碳马氏体不锈钢。
加工中易产生加工硬化,零件切削抗力增大,刀具磨损严重。
另外加工中粘刀现象严重,断屑困难,切屑易刮伤零件表面,影响加工质量。
因此加工中不仅要考虑变形问题,还要考虑由材料本身的特性带来的影响。
图 1 工件
2. 加工工艺方案确定
根据零件尺寸特点和材质特性,确定加工工艺路线。
(1)选择φ120mm ×130mm 棒料为毛坯,调质处理,改善加工性能。
(2)上卧式车床,先装夹左端φ107m m 孔端,加工右端φ100mm 孔端端面。
(3)用φ30mm 钻头钻零件中心通孔。
(4)用内径车刀粗加工φ100m m 孔至
φ90mm 。
(5)零件调头,装夹φ100m m 孔端,加工
φ107mm 孔端平面,长度达设计总长要求120mm 。
(6)粗、精加工φ107mm 孔,达设计尺寸要求。
(7)零件拆卸下,用自制的简单胀套,安装在零件φ107mm 孔内,螺母拧紧,重新上车床,装夹胀套一端。
精加工φ100mm 孔达设计尺寸。
(8)粗、精加工零件外径达设计尺寸
φ110mm 。
3. 简易胀套夹具设计
考虑零件内径和外径必须同心,薄壁零件装夹易产生变形等问题,设计了胀套夹具(见图2)。
将内斜面开口胀套1套在心轴2上。
工件3的
φ107mm 孔套在开口胀套1上,心轴带螺纹一端与螺母5联接,螺母拧紧,压板4顶住开口胀套,心轴移动,顶起胀套胀开与零件内孔壁紧紧联在一起。
心轴的另一端是用于
车床卡盘夹紧用。
利用该夹具即能保证零件内孔外径同心,又可避免由于夹紧力影响产生变形。
图2 胀套夹具结构
1.开口胀套
2.心轴
3.工件
4.压板
5.螺母
37
echnique
T
工 艺
生产中遇到如图1所示的零件,毛坯材料为:φ8mm 的1Cr18Ni9Ti 不锈钢棒,现要弯两处
R 12mm 的圆弧,两端钻、攻深10mm 的M3螺纹。
根据图1计算展开(中心线)长度:第 1 段(直线)长度24m m ,第 2 段(圆弧)长度 18.85mm ,第 3 段(直线)长度96mm ,第 4 段(圆弧)长度18.85m m ,第 5 段(直线)长度24mm ,展开总长24mm+18.85mm+96mm+18.85m m+2mm4=181.7mm 。
图 1
1. 原先的工艺
根据展开总长在两端加入适当的余量,在不锈钢棒的一端套入加力杆,利用图2中的销柱5和销柱3的作用,并在R 12mm 处用气割枪加热(加热弯形
减小阻力)分别对两处R 12mm 进行热弯形,再铣去两端多余长度,保证尺寸40mm ,最后钻、攻M3螺纹,校形保证尺寸120mm 。
工艺方法如下:
(1)车工:车2端面保证总长200mm 。
(2)钳工:(领图2所示工装)弯两处R 12mm 。
图 2
1、3、5.销柱 2.加力杆 4.基板
(3)铣工:铣两端保证40mm 。
(4)钳工:钻、攻两处M3深10mm ,并校形保证120mm 。
2. 原工艺不足之处分析
采用此弯形方法,虽然基本能够完成零件的加工,但主要存在几处不足:
(1)长度方向加入余量增加了原材料的消
中国人民解放军第5311工厂 (南京 211100) 张明光中国北方工业公司 (北京 100053) 郭 彦
棒料弯形的工艺改进
4.刀具及切削用量选择
考虑零件材质的特性,选用刀具不仅要具有较高的硬度和耐磨性,还要具有较高的强度和良好的韧性。
刀具选用Ti-TiCN-TiN 多复合材料的车刀。
车刀几何角度为前角15°,后角8°,刃倾角15°,主偏角93°。
考虑切削热对零件变形的影响,加工中要进行充分冷却,加工中选用水溶液作为切削液。
切削用量见附表。
5. 结语
采用合理的加工工艺,选择恰当的刀具材料和
刀具几何角度,设计简易的夹紧夹具,解决了加工中的变形问题,克服了材料本身特性带来的不利因素,零件加工定位夹紧可靠,零件变形小,加工效率提高,零件的加工质量得到保证。
(收稿日期:20120924)
加工零件切削用量
主轴转速
/r·min -1进给速度/mm·min -1
余量 /mm 粗车内孔4501000.2精车内孔 1 00030-粗车外径5001500.3精车外径
1 000
40
-。