蚀刻废液回用
印制板蚀刻废液循环利用及铜回收新技术及设备
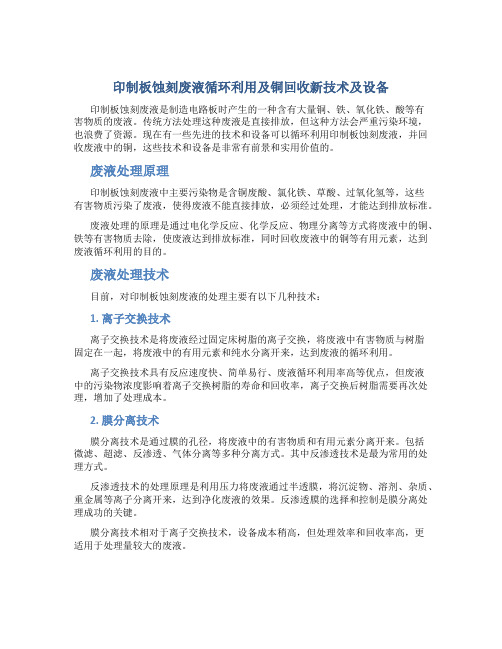
印制板蚀刻废液循环利用及铜回收新技术及设备印制板蚀刻废液是制造电路板时产生的一种含有大量铜、铁、氧化铁、酸等有害物质的废液。
传统方法处理这种废液是直接排放,但这种方法会严重污染环境,也浪费了资源。
现在有一些先进的技术和设备可以循环利用印制板蚀刻废液,并回收废液中的铜,这些技术和设备是非常有前景和实用价值的。
废液处理原理印制板蚀刻废液中主要污染物是含铜废酸、氯化铁、草酸、过氧化氢等,这些有害物质污染了废液,使得废液不能直接排放,必须经过处理,才能达到排放标准。
废液处理的原理是通过电化学反应、化学反应、物理分离等方式将废液中的铜、铁等有害物质去除,使废液达到排放标准,同时回收废液中的铜等有用元素,达到废液循环利用的目的。
废液处理技术目前,对印制板蚀刻废液的处理主要有以下几种技术:1. 离子交换技术离子交换技术是将废液经过固定床树脂的离子交换,将废液中有害物质与树脂固定在一起,将废液中的有用元素和纯水分离开来,达到废液的循环利用。
离子交换技术具有反应速度快、简单易行、废液循环利用率高等优点,但废液中的污染物浓度影响着离子交换树脂的寿命和回收率,离子交换后树脂需要再次处理,增加了处理成本。
2. 膜分离技术膜分离技术是通过膜的孔径,将废液中的有害物质和有用元素分离开来。
包括微滤、超滤、反渗透、气体分离等多种分离方式。
其中反渗透技术是最为常用的处理方式。
反渗透技术的处理原理是利用压力将废液通过半透膜,将沉淀物、溶剂、杂质、重金属等离子分离开来,达到净化废液的效果。
反渗透膜的选择和控制是膜分离处理成功的关键。
膜分离技术相对于离子交换技术,设备成本稍高,但处理效率和回收率高,更适用于处理量较大的废液。
3. 微生物处理技术微生物处理技术是利用微生物的去除能力,将有害物质降解为无害物质,是一种较为有潜力的处理技术。
这种技术存在工艺简单、处理成本低等优点。
目前,微生物处理技术主要包括好氧微生物法、厌氧微生物法和真菌生物法等,其中好氧微生物法的效果较好。
蚀刻废液回用
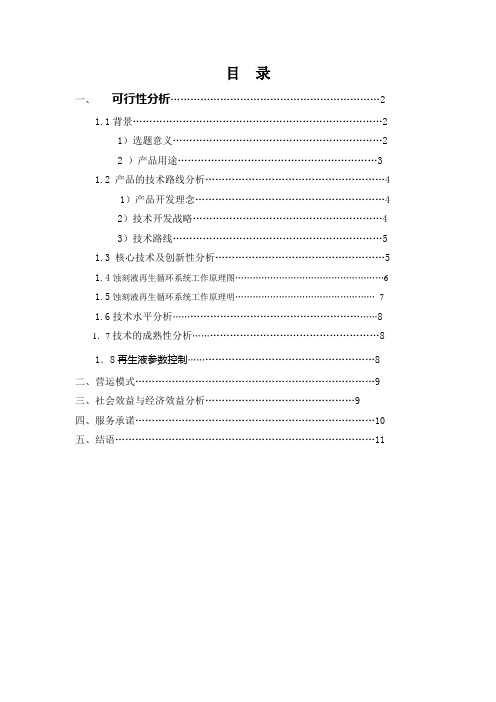
目录一、可行性分析 (2)1.1背景 (2)1)选题意义 (2)2 )产品用途 (3)1.2 产品的技术路线分析 (4)1)产品开发理念 (4)2)技术开发战略 (4)3)技术路线 (5)1.3 核心技术及创新性分析 (5)1.4蚀刻液再生循环系统工作原理图 (6)1.5蚀刻液再生循环系统工作原理明 (7)1.6技术水平分析 (8)1.7技术的成熟性分析 (8)1.8再生液参数控制 (8)二、营运模式 (9)三、社会效益与经济效益分析 (9)四、服务承诺 (10)五、结语 (11)《铜蚀刻液再生循环系统》项目建议书一、可行性分析1.1 背景1)选题意义印制电路板(PCB)行业是电子工业、信息产业和家电行业的基础,近20年来,作为重污染行业之一的PCB行业纷纷向中国转移,使得中国的PCB行业近几年一直保持高于10%的年增长速度。
目前全国约有各种规模的PCB企业近3000家,年产量达到2亿平方米以上,每年消耗精铜在10万吨以上,产出的蚀刻废液中总铜量在5万吨以上,对我国环境尤其是PCB厂周边地区的水资源环境构成了严重威胁和危害。
蚀刻生产线是PCB生产中消耗药水量较大的工序,也是产生废液(即危险废物——废蚀刻液,按国家环保总局的废物分类命名)和废水(即一次洗涤废水和二次洗涤废水)最大的工序。
一般而言,每生产一平方米正常厚度(18μm)的双面板消耗蚀刻液约为2—3升,并出废蚀刻液2—3升、一次洗涤废水5—10升、二次洗涤废水8——12升。
目前的做法是定时或不定时地从蚀刻槽排出部分铜含量很高的母液——废蚀刻液,同时向其中添加新的蚀刻液。
由于蚀刻液的最佳蚀刻铜离子浓度在100—140克/升,而废液外排时则希望铜离子浓度越高越好(常在150——160克/升),以尽可能提高蚀刻液利用率,降低溶液总的使用量。
因此,不论是采用人工间歇排放工艺还是比重控制的连续排放工艺,实际生产中蚀刻液并未处于其最佳技术状态。
从经济成本上说,目前的做法对PCB企业不利,一方面需要花费大量的钱购买蚀刻子液,而外排的废蚀刻液交给有废水处理能力的企业无偿或有偿处理后达标排放,增加了PCB企业的运菅成本和环保压力。
含铜蚀刻废液利用处置方案

含铜蚀刻废液利用处置方案背景在现代制造业中,蚀刻技术被广泛应用于电子、半导体、光电等领域。
在这些领域中,含铜蚀刻废液是其中一种常见的工业废液。
含铜蚀刻废液中的铜离子含量高,且具有一定毒性。
因此,如何对含铜蚀刻废液进行有效的处置和利用,成为了制造业中的重要问题。
含铜蚀刻废液的特性1.铜离子含量高2.具有一定毒性3.含有大量氢氟酸4.酸性较强处置方案1. 中和法中和法是含铜蚀刻废液处理的一种有效方式。
其主要原理是将含铜蚀刻废液和碱性物质混合,使其酸度降低到较为安全的范围内。
在中和法中,常用的碱性物质有氢氧化钠、氢氧化钙等。
中和法处理后的含铜废水,可通过过滤等方式进行净化后,得到清洁的水,再将其排放到环境中。
2. 电沉积法电沉积法是另一种常用的含铜蚀刻废液处理方式。
即利用电化学沉积原理,将废液中的铜离子沉积在电极上。
在电沉积的过程中,铜离子可以被还原成金属铜,从而达到废液净化的目的。
其优点是不需添加任何化学药剂,对环境污染小。
3. 分离法分离法是利用特定分离膜将含铜蚀刻废液中的铜离子与其他离子分离开来,达到净化的目的。
该方法操作简单,对环境的污染较小。
但是,由于分离膜的成本较高,分离法的应用范围受到一定的限制。
废液利用方案1. 铜的回收利用含铜蚀刻废液中的铜离子经过净化后可以进行回收利用。
一种常见的方法是通过化学物质将其还原成金属铜。
这种方法是一种经济实惠的方式,可将废液中的铜利用起来,同时也能减少对环境的污染。
2. 用于金属表面处理含铜蚀刻废液可以用于金属表面的处理。
特别是对铜及其合金的表面,其含有大量的铜离子,可在表面上形成保护膜,具有防腐、耐光、抗氧化等功能。
3. 用于其它行业含铜蚀刻废液经过净化后,可以用于其它行业。
如农业中的肥料、制造生产中的金属表面处理、矿山等。
结论含铜蚀刻废液处理和利用对环境保护具有重要意义,同时也与企业的可持续发展密切相关。
中和法、电沉积法、分离法是常用的处理方法,选用一种方法要考虑经济、环保、技术等多个方面的因素。
碱性蚀刻液中铜回收与废液铜氨废水的循环使用

碱性蚀刻液中铜回收与废液铜氨废水的循环使用碱性蚀刻液是一种用于蚀刻金属的溶液,其中包含有机酸、无机碱和助剂等成分。
在电子工业和光学工业中,铜是一种常见的材料,因此碱性蚀刻液中铜的回收和废液、铜氨废水的循环使用对于节约资源和保护环境具有重要意义。
铜的回收主要通过两个步骤完成:溶解铜和沉淀回收。
在碱性蚀刻液中,铜往往以离子的形式存在,因此可以通过加入还原剂将铜离子还原为金属铜。
还原剂常用的有二氧化硫、亚硫酸氢钠等。
还原反应可以用如下方程式表示:Cu2++2e-->Cu还原反应后,金属铜会从溶液中沉淀下来。
回收的金属铜可以用于再生和再利用。
在回收铜的过程中,也会产生一定量的废液和铜氨废水。
这些废液和铜氨废水富含有机酸、无机碱以及其他含有金属离子的溶质。
为了循环利用这些废液和铜氨废水,可以采用以下步骤:1.废液的中和:废液中的有机酸和无机碱可以互相中和,生成一定量的水和盐。
中和反应需要适当的酸碱指示剂来监测中和的程度,以确保中和反应完全。
2.沉淀回收:通过加入适当的还原剂,将溶液中的金属离子还原为金属沉淀,再通过过滤或离心等方法将沉淀分离出来。
沉淀可以通过烘干和熔融等方法得到金属的纯度较高的形态。
3.废液的再处理:在回收过程中生成的中和盐可以进一步处理,以从中提取有价值的化学物质或进行其他处理方式。
例如,可以通过晶体生长技术,将盐析出为晶体,再进行相应的晶体提纯工艺。
4.循环水系统:对于铜氨废水,可以采用循环水系统来回收和再利用。
该系统包括废水处理装置和循环水泵等设备,通过处理废水中的氨、铜离子和其他污染物,将废水进行处理后,再循环使用于蚀刻工艺中。
通过铜的回收和废液、铜氨废水的循环使用,可以减少资源的消耗和废液的排放,实现对环境的保护和可持续发展的要求。
同时,回收金属铜也可以带来经济效益,提高蚀刻液的利用率和生产效率。
因此,在碱性蚀刻液中铜回收和废液、铜氨废水的循环使用方面的研究和应用有着广阔的发展前景。
铝蚀刻废液再生的原理

铝蚀刻废液再生的原理
铝蚀刻废液再生的原理是利用电化学方法将废液中的有害物质转化成无害物质,从而达到废液的再生目的。
具体原理如下:
1. 废液中的有害物质主要包括铝离子、氧化剂和碱性物质。
铝离子是刻蚀过程中产生的,而氧化剂和碱性物质是用来促进刻蚀反应的。
2. 废液再生过程中,首先需要将废液分离出有害物质。
一种常用的方法是利用离心机将固体颗粒和液体相分离。
3. 接下来,在电解槽中进行电化学处理。
电解槽中设置阳极和阴极,废液作为电解液。
阴极上会析出铝金属,同时将铝离子还原成铝金属,从而减少废液中铝离子的浓度。
4. 在阳极上,氧化剂和碱性物质被氧化还原反应转化成无害物质。
一般来说,氧化剂会被还原成氧气或者水,碱性物质会被氧化成氨气等。
5. 经过电化学处理后,废液中的有害物质转化成无害物质。
最后,再将废液中的铝金属收集起来,进行下一轮蚀刻过程,实现了废液的再生利用。
蚀刻液再生

蚀刻液再生
蚀刻液再生是指将蚀刻过程中使用的废弃蚀刻液进行处理和回收,使其重新可以使用的过程。
蚀刻液再生的目的是减少废弃物的产生,并节约资源和降低环境污染。
蚀刻液再生一般包括以下步骤:
1. 液体分离:将废弃蚀刻液中的固体颗粒和其他杂质进行过滤分离。
2. 中和处理:将废弃蚀刻液中的酸碱性进行中和,通常是通过加入中和剂或者调节pH值进行处理。
3. 金属回收:将废弃蚀刻液中的金属离子进行回收,通常是通过电解沉积或其他金属回收技术进行处理。
4. 残余物处理:处理完成后的废弃物需要进行妥善处理,通常是进行固化处理或者交由专业机构进行处理。
1
蚀刻液再生可以降低生产过程中废弃液体的产生,减少资
源的消耗,并且可以降低环境污染的风险。
然而,蚀刻液
再生也需要考虑到处理过程中对环境的影响,以及回收处
理后的蚀刻液的质量是否能够满足再次使用的要求。
因此,在进行蚀刻液再生时需要进行详细的分析和评估,确保再
生过程的安全性和可行性。
2。
- 1、下载文档前请自行甄别文档内容的完整性,平台不提供额外的编辑、内容补充、找答案等附加服务。
- 2、"仅部分预览"的文档,不可在线预览部分如存在完整性等问题,可反馈申请退款(可完整预览的文档不适用该条件!)。
- 3、如文档侵犯您的权益,请联系客服反馈,我们会尽快为您处理(人工客服工作时间:9:00-18:30)。
目录一、可行性分析 (2)1.1背景 (2)1)选题意义 (2)2 )产品用途 (3)1.2 产品的技术路线分析 (4)1)产品开发理念 (4)2)技术开发战略 (4)3)技术路线 (5)1.3 核心技术及创新性分析 (5)1.4蚀刻液再生循环系统工作原理图 (6)1.5蚀刻液再生循环系统工作原理明 (7)1.6技术水平分析 (8)1.7技术的成熟性分析 (8)1.8再生液参数控制 (8)二、营运模式 (9)三、社会效益与经济效益分析 (9)四、服务承诺 (10)五、结语 (11)《铜蚀刻液再生循环系统》项目建议书一、可行性分析1.1 背景1)选题意义印制电路板(PCB)行业是电子工业、信息产业和家电行业的基础,近20年来,作为重污染行业之一的PCB行业纷纷向中国转移,使得中国的PCB行业近几年一直保持高于10%的年增长速度。
目前全国约有各种规模的PCB企业近3000家,年产量达到2亿平方米以上,每年消耗精铜在10万吨以上,产出的蚀刻废液中总铜量在5万吨以上,对我国环境尤其是PCB厂周边地区的水资源环境构成了严重威胁和危害。
蚀刻生产线是PCB生产中消耗药水量较大的工序,也是产生废液(即危险废物——废蚀刻液,按国家环保总局的废物分类命名)和废水(即一次洗涤废水和二次洗涤废水)最大的工序。
一般而言,每生产一平方米正常厚度(18μm)的双面板消耗蚀刻液约为2—3升,并出废蚀刻液2—3升、一次洗涤废水5—10升、二次洗涤废水8——12升。
目前的做法是定时或不定时地从蚀刻槽排出部分铜含量很高的母液——废蚀刻液,同时向其中添加新的蚀刻液。
由于蚀刻液的最佳蚀刻铜离子浓度在100—140克/升,而废液外排时则希望铜离子浓度越高越好(常在150——160克/升),以尽可能提高蚀刻液利用率,降低溶液总的使用量。
因此,不论是采用人工间歇排放工艺还是比重控制的连续排放工艺,实际生产中蚀刻液并未处于其最佳技术状态。
从经济成本上说,目前的做法对PCB企业不利,一方面需要花费大量的钱购买蚀刻子液,而外排的废蚀刻液交给有废水处理能力的企业无偿或有偿处理后达标排放,增加了PCB企业的运菅成本和环保压力。
本项目立项的目的是开发一种使蚀刻生产工序废液零排放的清洁生产技术。
即铜蚀刻液再生循环设备,它由三块集成:1)蚀刻液配方及循环再生技术,其中包括性能优良的蚀刻液组份调节剂成分的选择;2)从废蚀刻液中无损分离铜的技术,它由萃取分离技术和专用设备制造技术组成;3)电解铜技术,通过使用不溶性阳极板等特殊设备将废蚀刻液中的铜离子转化成高纯电解铜的技术。
蚀刻液再生循环设备实际上是一个完整的系统,该系统植入蚀刻工序后,不但可使其成为清洁生产工艺,同时可使该工序处于蚀刻的最佳状态,即在添加新液时使溶液混合时间最短、铜离子浓度梯度最少、蚀刻速度最快,侧蚀最小;在物料使用总量上大大减少,再生循环过程仅消耗少量蚀刻盐、组份调节添加剂和调节PH的酸碱,物耗总量减少96%以上;整个再生循环过程上变有危害的大量液体废物为工业应用广泛的宝贝——金属铜,它可以为冶金、材料加工及化工业行业直接使用,大幅提高PCB企业的经济收益;使PCB蚀刻工序的总成本(包括添加剂消耗、电力、设备维护等)比原来的(蚀刻液消耗、电力、水和废水处理费等)降低75%以上,使蚀刻工序这个倍受关注的产生危险废液的工序变成为一个清洁生产工序。
2)产品用途蚀刻液再生循环系统是与PCB企业蚀刻工序配套的清洁生产设备,它全天候为PCB企业的蚀刻工序提供蚀刻液及氨洗液,它与常规的环保治污设备不同的是,它是在线随机封闭式循环运行,蚀刻液循环再生设备还产出价值十分可观的副产品——金属铜,其价值远大于设备运行过程的水电、人工和物耗成本,使PCB蚀刻工序成为含铜废液零排放清洁生产工序变为现实。
1.2产品的技术路线分析1)产品开发理念蚀刻液循环再生系统是将精细化工、萃取工艺、有色冶金、电解工艺、环境工程、自动化控制、进行隐含和复合的高附加值技术组合。
我公司开发者从工艺的成熟性、可操作性、稳定性、品质控制技术、安全性等全方位研发,针对我国线路板蚀刻工序的特点,总结了目前囯内外同类型产品性能,研发了专用铜萃取分离技术,该技术完全符合我国蚀刻工艺要求及环境要求,优于目前囯内其它废蚀刻液处理技术。
我们以改善生态环境和公民健康状态为己任,积极响应国家和各级政府的号召,针对循环经济的时代要求,不断开发新技术以协助PCB企业进行节能降耗等技术改造。
我公司在支持PCB行业走可持续发展道路的同时,与PCB企业分享本公司高科技产品给该行业带来的经济效益、环境效益等社会综合效益。
2)技术开发战略我们的技术开发战略是从污染源头来预防而不是被动地从事后治理污染的角度出发。
对PCB企业各工序的污染源特征进行本质分析,以确定其采用循环使用、清洁生产的技术可能性;针对各工序(即污染源)产出的不同类型液体废物(废蚀刻液、一次洗涤氨废水、)之具体特点,分别实行资源化、和无害化战略,对其有价值部分进行回收,有用部分进行完全回用,以确保PCB企业蚀刻工序在生产品质上更稳定、含铜废液零排放、使生产成本大幅降低(≥75%)。
3)技术路线(如图2所示):图 2 铜蚀刻液循环再生技术路线1.3核心技术及创新性分析该系统由三部分组成:1、自控铜无损分离系统。
2、铜电积系统。
3、蚀刻液存储及组份调节系统。
自控铜无损分离系统:是将废蚀刻液中的铜离子通过富铜剂从废液中无损分离铜离子,并将铜离子移送到铜电积系统,释放铜离子后的贫铜剂再回到此系统继续工件。
铜电积系统:富铜剂中的铜离子释放到此系统中,通过电积提取高纯度电解铜。
蚀刻液存储及组份调节系统:系统将已降低铜含量的蚀刻液通过组份调节,使Cu²+、Clˉ、PH值达到生产要求,待生产所用。
系统工作时,整个系统物料实现无排放封闭式循环运行。
1.4蚀刻液再生循环系统工作原理图1.5蚀刻液再生循环系统工作原理说明(即四个循环)在线路板的蚀刻工序中,蚀刻液中铜离子含量会逐渐上升而使蚀刻性能下降。
要使蚀刻液达到最佳工作状态,须将蚀刻液中的Clˉ、Cu 、PH值调整到最佳范围内,通常采取不断添加子液,溢流排放母液(废蚀刻液)来调整上述各种成份达最佳浓度,从而恢复蚀刻液性能。
蚀刻液再生循环系统将生产中已失去功效的药液(废蚀刻液)采取无损分离降低铜离子浓度至生产需求的合理范围,添加少量的补充液使Cu 、Clˉ、PH值恢复到最佳蚀刻状态,同时对蚀刻工序中氨水洗液经再生系统处理后也可循环使用,使蚀刻工序含铜废水零排放,同时,过程物料也再生循环使用以达到清洁生产的目地(即蚀刻液-氨水洗液-硫酸-富铜剂(国产铜萃取剂)四个物料闭路循环)。
如图5。
1.5.1蓝色线条是系统的第一个循环系统,废蚀刻液经该系统MX1处理后铜离子被吸附分离出来,处理后的蚀刻液经调配后返回蚀刻机被循环使用;粉红色线条是第二个循环系统,是含铜的富铜剂被送入MX2系统,MX2系统也是氨水洗废液回收系统,当MX1系统富铜剂完成工作后则进入XW -Ⅱ系统中继续工作吸附氨水洗废液中的铜离子,使铜离子降达氨水洗正常工作要求并返回蚀刻机再使用;黑色线条是第三个循环系统,是含铜的富铜剂进入到MX3系统内,当富铜剂进入后会将其中的铜离子分离释放进硫酸中生成硫酸铜溶液, 富铜剂释放铜离子后经油缸进入MX1系统中重新开始工作;红色线条是第四个循环系统,即硫酸铜溶液形成电解液进入电解槽将铜离子还原成有价值的高纯度铜,被提取铜后的电解贫液则返回MX3系统;至此.该设备完成了一个完整循环工作程序。
1.6技术水平分析传统的生产硫酸铜工艺乃是对废蚀刻液进行“杀鸡取卵”的处理方案即破坏原蚀刻液的组份,且运输和处理中存在二次污染问题,使得对蚀刻有用的成份(氨、氯化物、氯酸盐、硫脲等)成为二次污染物,加上铜提取过程无法避免的含铜废水一起被排放,对区域性的水体系造成了严重的二次污染。
国外纯萃取工艺由于囯外萃取剂的性能与囯内蚀刻液不匹配造成组份调节不稳定,由于萃取剂不能稳定供货无法稳定生产和全面推广。
国内个别的离子膜工艺在操作工序、环保达标方面、组份调节、产铜纯度等方面工艺尚不够成熟无法突破、无使用及推广价值,各处理方案已有样板及案列。
1.7技术的成熟性本公司开发的蚀刻液循环再生设备已形成批量生产,并成功地在广东地区的怡富、胜华、瑞兴、普林、本立等线路板厂进行了连续工业化应用,证明该设备整个闭路工作循环时无废液、废气产生,产出的再生蚀刻液在生产中的应用性及稳定性能优于子液,蚀刻速度与原子液相比有微量变化在±5℅之间变化、但速度稳定性好。
反映了该系统的技术成熟性和可靠性;产出的副产品铜含量达99.9%以上。
1.8再生液参数控制我司处理后的再生液Cu2+控制在60~90g/L,这对因系统Delay 而导致加药过度的问题大大改善,尤其对比重控制器不先进(未有渐进式加药控制)的蚀刻机效果更明显。
因再生液含60~90g/L铜离子,生产添加时添加量比一般子液多,所以再生液PH控制在9.2~9.5便可保证生产线PH稳定在8.0~8.6。
我公司再生蚀刻液一般参考客户原生产线参数调配,如若贵司原生产参数为Cu2+=140g/L、Clˉ=170~190g/L、PH=8.0~8.6,则我司再生液控制在Cu2+=60~90g/L、Clˉ=170~190g/L、PH=9.2~9.5,经前期短磨合期稍作调整后,可稳定贵公司生产线生产参数,保证生产线路板质量。
二、运营模式PCB厂零成本运行:我司与PCB厂签订合作合同,是指只需厂方提供设备安装场所。
设备制造、设备安装,运营水、电费、组份调节、物料成本、人工、药水品质保证及设备维护等成本费用均由我公司承担,付产品铜作为我方投资回报。
厂方免费获取符合质量要求的生产用再生蚀刻液,同时还可在我司收回设备投资后按一定的比例分享附产铜的利润。
使贵公司蚀刻工序在零资金投入情况下就可达到无废蚀刻液产生、真正实现清洁生产。
此合作方式不同与传统的设备售卖方式,我公司的工程技术人员可以长期有效地保障设备在最佳的运行状态,以确保生产用再生蚀刻液质量,还可获得不断进行技术更新和免费的技术升级服务。
三.社会效益与经济效益分析本项目提供的蚀刻液循环再生设备,技术标准已经技术监督部门备案,并己通过政府环保部门的相关检测,可实现PCB行业在蚀刻工序的废蚀刻液零排放,达到清洁生产的要求,彻底解决如今国内PCB 行业中产出的大量危险液体——废蚀刻液的污染源及其扩散问题。
将有危害的大量危险废物转变为循环再生资源——金属铜,在收益上对PCB企业更加有利,采用蚀刻液循环再生设备后PCB企业的生产成本大幅下降,有利于我国PCB行业的可持续发展和提高该行业的国际竞争力。