酸性蚀刻废液再生循环回收系统 _120吨_ (1)
碱性蚀刻循环再生直接电解工艺(80吨)

按操作规范以此为原材料调配成合格 蚀刻子液回用到蚀刻机进行蚀刻工 80 作,从而能实现资源的循环利用,达 到保护环境的目的
碱性蚀刻废液直接电解工艺是与蚀刻生产线联动的闭合循环系统,是消除 PCB 铜蚀刻废液二次污染的有效措施和重大革新。该系统再生液回收利用率达 100%,金属铜的回收率达 100%。整个系统主要由两部分组成: 1.铜提取系统, 通过阴阳极复合板直接电解提取高纯度铜,电沉积法降低蚀刻废液中的铜离子 浓度;2.蚀刻液储存和成分调节系统,将已降低铜含量的蚀刻液即行业中称为 的电解再生液通过成分调节,使其各项指标达到生产所需的要求,此时行业中 称之为蚀刻再生子液,通过比重控制进行自动添加返回至蚀刻生产线进行蚀刻 工作使,从而实现资源的循环利用及废液的零排放,达到清洁生产的目的。
如下:
蚀刻工艺 产品附价值 碱性蚀刻工
蚀刻废液 艺
价值所在
废液含大量 的金属铜
数量(吨)
能否实现资源循环利用
低价委外处理,既不能实现资源的循
80
环利用,还可能在转移的过程中会造
成二次污染
碱性直接电 解铜回收工
艺
电解铜 电解再生液
纯度高的单 质铜
含有大量蚀 刻液成分
直接高价售给冶炼厂进行进一步提纯 8
碱性蚀刻循环再生直接电解工艺
一、背景 为了响应国家环保政策,进一步节能减排,减少蚀刻废液在转移过程中带来
的环境污染及重金属的二次污染,结合本司的现有实际情况,引进碱性蚀刻循 环再生直接电解工艺。 二、工艺流程图
三、工艺原理 通过设计标准化的碱性直接电解槽,石墨板作为阳极,单面上铜的不锈钢
板(特殊处理)作为阴极,再在电解过程中加入少量的添加剂,使得碱性蚀刻 废液中的铜离子通过电沉积后以块状铜单质出现在阴极板上,不间断的工作使 得电解槽中碱性蚀刻废液中的铜离子浓度下降,并控制在一定的铜离子浓度(通 过流量控制器进行恒量补充相应量蚀刻废液),从而得到一个稳态运行的系统, 电解提铜后的高氨氮水再通过补加相应物料达到蚀刻子液的参数标准后完全回 用至蚀刻生产线进行蚀刻工作,实现零排放。
PCB 蚀刻废液资源再生产品标准

T/ZJGFTR XX-20XX PCB蚀刻废液资源再生产品标准1适用范围本标准规定了由印制电路板(PCB)蚀刻废液综合利用、深度加工生产的碱性蚀刻液、单液型酸性蚀刻液、双液型酸性蚀刻液、二水氯化铜与无水氯化铜的生产工艺、产品质量、采样、试验方法、检验规则、标志、包装、运输和贮存等要求。
本标准适用于PCB蚀刻废液的综合利用、深度加工的再生产品。
2规范性引用文件下列文件对于本文件的应用是必不可少的。
凡是标注时间的引用文件,仅所注时间的版本适用于本文件;凡是不标注时间的引用文件,其最新版本(包括所有的修改版)适用于本文件。
GB/T191-2008包装储运图示标志GB/T601-2016化学试剂标准滴定溶液的制备GB/T602-2002化学试剂杂质测定用标准溶液的制备GB/T603-2002化学试剂试验方法中所用制剂及制品的制备GB/T22592-2008水处理剂pH值测定方法通则GB/T22594-2008水处理剂密度测定方法通则GB/T14591-2016水处理剂聚合硫酸铁GBT31528-2015含铜蚀刻废液处理处置技术规范GB/T8170-2008数值修约规则与极限数值的表示和判定GB/T6678-2003化工产品采样总则GB/T6680-2003液体化工产品采样通则GB/T6682-2008分析实验室用水规格和试验方法GB∕T1618-2018工业氯酸钠GB_T1616-2014工业过氧化氢2GB-T23940-2009工业过硫酸盐产品的分析方法JJG694-2009原子吸收分光光度计检定规程CJ/T51-2018城镇污水水质标准检验方法3术语和定义碱性蚀刻液碱性蚀刻液属于铜-氨络离子体系的蚀铜液,适用于印刷电路板的蚀铜流程。
单液型酸性蚀刻液单液型酸性蚀刻液是以盐酸为主要成分的蚀铜液。
双液型酸性蚀刻液双液型酸性蚀刻液是以氯酸钠与氯化钠为主要成分的蚀铜液。
二水氯化铜与无水氯化铜从蚀刻废液中提取的铜加工成二水氯化铜(CuCl2·2H2O),再经干燥生产无水氯化铜(CuCl2)。
单液型酸性铜蚀刻液的循环再生与铜回收新工艺开发

用作者简介:王峰(1997-),男,河南邓州人,硕士,高级工程师,专业方向:工商管理。
基金项目:2017年广东省广州市南沙区技术开发项目(2017KF004)王峰,王辉,韩宝森,颜克海,李忠(广州弘高科技股份有限公司,广东广州511458)摘要:PCB 生产过程中的蚀刻液在使用后会产生大量的铜废水,若直接排放不仅会造成严重的资源浪费,还会带来严重的环境污染。
因此,对蚀刻液进行循环再生及铜回收是一项节约成本、降低污染的措施。
传统的蚀刻液循环再生及铜回收工艺一般采用双液型酸性蚀刻液,且工艺回收利用效果不足,资源浪费严重。
本工艺设计采用单液型酸性蚀刻液作为生产线蚀刻液,利用隔膜电解技术对废蚀刻液进行循环再生及铜回收,通过对生产线中ORP 值(氧化还原电位)和铜含量比重进行监控,对不同ORP 值废蚀刻液进行电解处理和调配,可直接循环再生回到生产线形成再生液。
该项工艺设计中设定蚀刻液的工作ORP 值为480~600mv ,铜含量比重为1.25~1.35。
通过实验检测提铜处理前的蚀刻液铜含量为55050mg/kg ,提铜处理后的蚀刻液铜含量为7551mg/kg ,铜回收率达到86.28%。
该工艺不仅有效提高了工作效率和废液循环再生利用,降低环境污染,而且具有重要的理论与应用价值。
关键词:蚀刻液;单液型;隔膜电解;铜回收;循环再生中图分类号:X703文献标志码:A文章编号:1674-0912(2019)08-0029-03印刷电路板(PCB )是电子信息产业的基础,已经成为电子信息的支柱产业。
然而PCB 产业在生产过程中进行的蚀刻、微蚀刻,会使得基材覆铜板中50%~60%以上的铜被蚀刻变成废的蚀刻液,产生的铜废水具有浓度高、污染严重的问题[1,2]。
因此,在发展PCB 生产的同时,如何进行废水处理、高效利用刻蚀废液中残留的有用成分、去除废液中影响微蚀效果的成分,形成分离铜、微蚀液循环再生利用,变得尤为重要。
传统工艺及现有的铜回收及蚀刻液循环再生工艺技术有以下缺点:(1)采用的双液型酸性蚀刻液使用时有安全性低、成本高的问题[3];(2)电路板生产过程中产生的微蚀液含有大量铜离子,未能有效回收利用,造成资源浪费[4];(3)传统工艺的微蚀液中铜离子浓度达到一定值,微蚀刻能力就明显减弱甚至失效,需要换槽,废液需排放,造成资源浪费。
PCB酸性蚀刻废液再生膜电积回收铜及副产三氯化铁术开发可行性研究报告

PCB酸性蚀刻废液再生膜电积回收铜及副产三氯化铁术开发可行性研究报告目录一、项目实施的背景和意义 (1)1.1项目的实施背景 (1)1.2项目的实施意义 (2)1.2.1项目的先进性、重要性、必要性和可行性 (2)1.2.2在行业发展中的地位和作用 (7)1.3项目的预期效益 (8)1.3.1社会效益 (8)1.3.2经济效益 (9)二、技术发展趋势及国内外发展现状 (9)2.1国内外处理技术发展趋势与现状 (9)2.1.1国外处理技术发展趋势与现状 (10)2.1.2国内处理技术发展趋势与现状 (10)2.2我市相关行业发展情况 (11)2.3市场需求情况 (12)三、项目主要研究 (14)3.1项目涉及的技术领域、工艺范畴 (14)3.2拟采用的技术原理、技术方法 (16)3.3拟解决的关键技术问题 (16)3.4拟采用的技术路线、工艺流程 (20)3.5项目的主要技术创新点 (22)3.6项目涉及的知识产权情况 (23)四、项目预期目标 (18)4.1预期成果 (18)4.2产业前景 (18)4.3培养的技术人才 (19)4.4预期贡献 (24)4.5二年期内的可考核技术指标和社会经济效益指标 (25)4.5.1技术指标 (25)4.5.2社会指标 (20)4.53经济指标 (20)五、项目实施方案 (21)5.1项目的组织管理方式 (21)5.2技术实施步骤 (22)5.3科技资源综合利用 (22)5.4成果产业化策略 (22)5.5研发资金的筹集与投入 (23)5.5.1资金筹集 (23)5.5.2资金投入情况 (24)5.6知识产权和技术标准的对策措施以及特殊行业的许可报批 (25)六、项目计划进度 (26)七、现有工作基础和条件 (27)7.1企业已有的研发基础、主要研究成果 (27)7.2项目实施具备的支撑条件 (28)7.3申请单位近三年承担的国家、省、市相关科技计划项目的完成情况 (28)7.4与其它企业、科研院所、大专院校的合作情况 (28)八、研发团队 (29)8.1研发团队的规模和结构 (29)8.2 项目核心研发人员 (30)一、项目实施的背景和意义1.1项目的实施背景印制电路板(PCB)是组装电子零件用的基板材料,是指在通用基材上按照预定设计所形成的点间连接以及印制元件印制板。
酸性蚀刻废液中铜的回收及废液再生新技术

T h e r e s u l t s s h o we d t h a t wh e n t h e i n i t i a l c o n c e n t r a t i o n o f Cu 2 i s ( 1 5 - 5 ) g / L a n d t h e c u r r e n t d e n s i t y i s 4 . 1 6 A/ d m2 。 a
酸碱性蚀刻液再生及铜回收系统
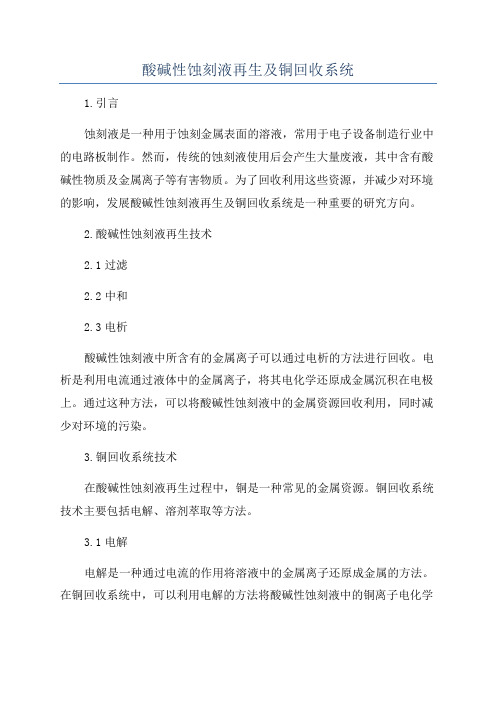
酸碱性蚀刻液再生及铜回收系统1.引言蚀刻液是一种用于蚀刻金属表面的溶液,常用于电子设备制造行业中的电路板制作。
然而,传统的蚀刻液使用后会产生大量废液,其中含有酸碱性物质及金属离子等有害物质。
为了回收利用这些资源,并减少对环境的影响,发展酸碱性蚀刻液再生及铜回收系统是一种重要的研究方向。
2.酸碱性蚀刻液再生技术2.1过滤2.2中和2.3电析酸碱性蚀刻液中所含有的金属离子可以通过电析的方法进行回收。
电析是利用电流通过液体中的金属离子,将其电化学还原成金属沉积在电极上。
通过这种方法,可以将酸碱性蚀刻液中的金属资源回收利用,同时减少对环境的污染。
3.铜回收系统技术在酸碱性蚀刻液再生过程中,铜是一种常见的金属资源。
铜回收系统技术主要包括电解、溶剂萃取等方法。
3.1电解电解是一种通过电流的作用将溶液中的金属离子还原成金属的方法。
在铜回收系统中,可以利用电解的方法将酸碱性蚀刻液中的铜离子电化学还原成铜金属。
这种方法具有高效、环保的特点,能够有效地回收利用酸碱性蚀刻液中的铜资源。
3.2溶剂萃取溶剂萃取是通过溶剂选择性地吸附和分离溶液中的特定成分的方法。
适当选择合适的溶剂,可以实现对酸碱性蚀刻液中的铜离子的吸附和回收。
这种方法具有操作简单、回收率高的特点,是一种常用的铜回收系统技术。
4.酸碱性蚀刻液再生及铜回收系统的优势4.1资源回收利用通过再生技术可以将酸碱性蚀刻液中的酸碱物质和金属离子回收利用,减少对自然资源的消耗。
4.2环境友好再生系统能够有效地处理和减少酸碱性蚀刻液中的废液,减少对环境的污染。
4.3经济效益通过再生和回收技术,可以降低酸碱性蚀刻液的成本,提高资源利用效率,从而带来经济效益。
5.结论酸碱性蚀刻液再生及铜回收系统是一种重要的研究方向,通过过滤、中和和电析等方法可以实现酸碱性蚀刻液的再生和回收利用。
通过电解和溶剂萃取等方法可以实现酸碱性蚀刻液中的铜离子的回收。
这些技术具有资源回收利用、环境友好和经济效益等优势,对于推动电子设备制造行业的可持续发展具有重要意义。
目前PCB行业酸性蚀刻制程废酸性蚀刻液处理方法浅谈

目前PCB行业酸性蚀刻制程废酸性蚀刻液处理方法浅谈关于目前PCB行业酸性蚀刻制程废酸性蚀刻液处理方法浅谈目前PCB铜回收行业正在蓬勃发展,自2002年以来国际铜价飙升,企业越来越重视开流节源,铜回收设备制造企业如雨后春笋般遍地开花。
但由于含铜废液回收铜行业入行门槛低,各企业素质参差不齐。
真正成规模,有实力的铜回收设备企业很少,大多数企业员工不超过20人,业务能力开展差,能安装一套设备也美其名曰环保科技公司。
此种现象造就PCB 企业无法真正了解到技术的发展程度,技术的可行性以及盲目安装设备后对自身造成的损失等;本文通过针对目前许多铜回收企业自称“已突破技术瓶颈,技术成熟稳定”的《PCB 酸性蚀刻废液再生与铜回收装置》的分析来让广大PCB企业更加直观更加清楚的了解目前的技术发展。
首先,要了解一个技术的稳定性我们需要了解其工艺流程及产物、企业工艺介绍是否符合生产工艺等。
众所周知PCB酸性蚀刻制程在蚀刻过程中,氯化铜中的Cu2+具有氧化性,能将板面上的铜氧化爲Cu+,形成的Cu2Cl2是不易溶于水的,在有过量的Cl-存在下,可形成可溶性的络离子,随着蚀刻的进行,溶液中的Cu+越来越多,蚀刻能力很快下降,以至最后失去蚀刻能力。
爲保持蚀刻能力,一般通过加入氧化剂对蚀刻液进行再生,使Cu+氧化重新转变爲Cu2+,使蚀刻得以连续的进行。
酸性废蚀刻液中酸性子液只是很少一部分,而大部分为生产中所添加的盐酸。
一般低酸生产子液与盐酸的比例大概为:1:1.5-2,高酸生产子液与盐酸比例大概为1:2-3。
通过酸性蚀刻的生产工艺我们可以得出,目前许多蚀刻铜回收企业所描述的酸性铜回收系统处理后废液可完全回用是不可能达到的。
以月废酸性蚀刻液100T为例,经提铜后回用再生液100T,酸性蚀刻生产中盐酸添加与再生液中的氯离子、铜离子含量均无关,固在处理完100T废液后将会超过150T的废液产生,如此循环废液量将是无限增长。
有人说可以回用一部分,另一部分排入PCB厂废水处理站。
酸性蚀刻液再生回收系统[实用新型专利]
![酸性蚀刻液再生回收系统[实用新型专利]](https://img.taocdn.com/s3/m/d00c0d6b71fe910ef02df84b.png)
专利名称:酸性蚀刻液再生回收系统专利类型:实用新型专利
发明人:明果英,周军,赵建成,张勇申请号:CN201120465136.1
申请日:20111121
公开号:CN202610332U
公开日:
20121219
专利内容由知识产权出版社提供
摘要:本实用新型提供了一种酸性蚀刻液再生回收系统,包括:蚀刻槽(6)、蚀刻废液回收槽(1)、离子膜电解槽(2)、氧化再生槽(3)和自动出铜装置(4),蚀刻废液回收槽(1)、离子膜电解槽(2)的阳极室(21)、氧化再生槽(3)和蚀刻槽(6)构成阳极回路;自动出铜装置(4)与离子膜电解槽(2)的阴极室(22)连通,自动出铜装置(4)和阴极室(22)构成阴极回路。
本实用新型的酸性蚀刻液再生回收系统中,形成了相互独立的阳极回路和阴极回路,以酸性蚀刻废液为阳极液,阳极液经电解后直接再生利用,进入蚀刻生产线,这样无需重新配置蚀刻液,使得电解生产效率大大提高,同时降低了生产成本。
申请人:湖南万容科技股份有限公司
地址:410100 湖南省长沙市长沙经济技术开发区盼盼路11号
国籍:CN
代理机构:北京康信知识产权代理有限责任公司
代理人:吴贵明
更多信息请下载全文后查看。
- 1、下载文档前请自行甄别文档内容的完整性,平台不提供额外的编辑、内容补充、找答案等附加服务。
- 2、"仅部分预览"的文档,不可在线预览部分如存在完整性等问题,可反馈申请退款(可完整预览的文档不适用该条件!)。
- 3、如文档侵犯您的权益,请联系客服反馈,我们会尽快为您处理(人工客服工作时间:9:00-18:30)。
0.42
0.3
0.08
99.2
总量(T)
0.0562
0.0401
0.0107
13.273
7.1.2 水平衡 根据设备供应商介绍,本项目使用的设备常年连续处于封闭状态运行,车间地坪
进行一般清扫,无需冲洗,且各设备进料单一,设备不需要进行清洗,新鲜水大概 需要 30 m3/月。
项目
洗气塔用水
组分调节
洗铜水
3.原辅材料情况
3.1 项目使用的化学原辅材料
工艺流程
酸性蚀刻 废液再生循 环回收利用
处理系统
原料 1 原料 2 辅料 1 辅料 2
物料类别
酸性蚀刻液
氯酸钠 盐酸
氯化钠 工业废铁 氢氧化钠 电解稳定剂 蚀刻添加剂 过滤棉芯
成分含量 H+:1.5~2.5 N Cu2+:100~160g/L Cl-:220~280 g/L
1
三氯化铁储存罐
PT-10000L
2
酸性蚀刻液子液储存罐 PT-10000L
2
新增 新增 新增 新增 新增 新增
酸性蚀刻废液储存罐
PT-10000L
2
依托现有
5.项目工艺流程及主要产污环节
5.1 酸性蚀刻液及铜回收工艺流程图
图 5-1 酸性蚀刻液及铜回收工艺流程图 5.2 工艺说明
酸性蚀刻液进入阳离子膜电沉积系统处理采用的是批量进液处理,每批次进液量 约 5 吨,每批次处理时间约 7 天。
8.1.4 本项目水污染物产生及排放情况:
废水类 型
产污环节
污染物产生量
治理措 污染物排放量 标准浓度
产生量 浓度(mg/L) (m3/a)
施
浓度 排放量 (限值)
(mg/L) (m3/a) (mg/L)
废水量
/
798
洗气塔 洗气塔 废水 段
COD
150
0.234
SS
70
0.109
/
798
/
50 0.078 50
洗铜水 2
0.264
8.项目废水产生情况
8.1 废水 8.1.1 生产废水:
本项目生产废水主要为酸性蚀刻废液的废水以及洗气废水。酸性蚀刻废液处理工 程产生的废水量项目年处理酸性蚀刻废液 1440 吨(比重约 1.3,即约 1100m3), 由于盐酸、氯化钠的投加,低铜酸液会过量,因此会排放一定的废液,根据工艺设 计,废水排放系数约 6.5%,即年排放废水约 71.5m3,主要污染物有 Cu、SS、 COD 等。该部分废液与铁块溶解生成氯化亚铁,作为工艺后续的铁水吸收槽原液使 用,饱和后打至三氯化铁储液槽,委外处理或作为污水处理站絮凝剂使用和制作聚 合氯化铁副产品外售。
废滤芯 三氯化铁溶液
连续产生
7. 工程污染源分析
7.1 主要物料的月平衡 7.1.1 铜平衡 项目铜离子去向主要有四部分,产生每月酸性蚀刻废液 120 吨(比重约 1.3,即
约 92.3m3),原始废液中铜离子浓度在 145g/L 左右,含铜量约为 13.38t。
项目
蚀刻水洗
电解液
洗铜水
电解铜
含铜量(%)
30 0.047 30
废水
酸性蚀 刻废液 处理工 艺段
废水量 COD SS
铜离子
/ 400 150 1200
152 0.009 0.003 0.021
/
152
/
50 0.001 50
30 0.007 50
0.3
0
0.3
9. 大气污染物产排情况
9.1 有组织废气
根据本项目的工艺流程分析,项目在生产过程中产生的有组织废气主要为氯气 雾、盐酸雾。各废气产生量根据《环境统计手册》酸雾计算公式估算: Gz=M(0.000352+0.000786U)·P·F 式中:Gz——酸雾量,kg/h;
电解过程产生的 Cl2 具有强氧化性,是蚀刻液很好的氧化再生剂,经过负压抽吸至溶 解吸收槽进行蚀刻液的再生,反应式:
2CuCl+Cl2=2CuCl2 在上述反应过程通过仪器控制氧化还原电位,CuCl 保持在高位,使得反应中 Cl2 得到充 分的吸收。同时在过量后自动切换排至铁水洗气塔,通过氯化亚铁来吸收过量的氯 气,并在后端设置一个碱洗喷淋缸,以进一步吸收氯气后再通过管道进入现有的碱 洗塔,而且氯气可溶于水,经吸收后排放的氯气极少。 反应式如下: 2FeCl2+Cl2=2FeCl3 Cl2+2NaOH=NaCl+NaClO+H2O
120
1440
持续溢流
2.5.技改项目设备处理规模与生产废液的匹配度 技改项目购置的酸性蚀刻废液处理设备单套处理能力 140 吨/月,共设置 1 套设
备,设计处理能力 1680 吨/年。企业根据以往三年废液危废转移联单,并按照实际 产能推算酸性蚀刻废液产生量约 1440 吨/年。由此可见,项目设计的处理规模与公 司废液产生量相匹配,设计的处理规模是合理的。
酸性蚀刻液循环再生系统是采用阴、阳离子膜电解—电沉积氧化法对低 ORP、 高含铜量的酸性蚀铜液进行处理。通过电解氧化法提高溶液的 ORP,同时通过电沉 积法得到阴极电解铜,降低蚀铜液的铜离子含量使其得以循环利用。废蚀刻液中的 铜离子与蚀刻液进行无损分离,保持蚀刻液原有的化学成分,然后通过有效处理等 使其成为具有稳定蚀刻性的再生子液重新返回工厂蚀刻线。酸性蚀刻液循环再生系 统主要包括三个组成部分:阳离子膜电沉积提铜循环系统、氧化性气体吸收系统、 再生液调配监控系统。酸性蚀刻废液经管道收集输送至项目废液中间槽罐内,再通 过管道进入电解系统电解,电解反应式: 阳极反应:2Cl-=Cl2+2e 阴极反应:Cu2++2e=Cu
参数控制如下: 酸性蚀刻废液处理工艺操作条件
同极距(mm) 电流密度(A/m2) 电解液停含铜(g/L) 电解液温度 进液方式 阳极
阴极
90
200
20~50
≤40℃ 管道输送 钛涂层
钛板
由于在电路板生产蚀刻工艺中板面会带走一定量的蚀刻液,因此在此过 程中蚀刻液可看作是一个自动更新再生的物质,药水通过电积后只需补加损 耗的物料,不会带入其他物质,所以蚀刻液在体系内可不断循环使用,不需 要更换。
无色或微黄色有刺激性臭味液体,熔点- 沸本品不燃,具强腐
115.8℃点为-84.9℃,比重约 1.2,易挥 蚀性、强刺激性,可
发,与水混溶,可溶于碱液。
致人体灼伤。
本品不会燃烧,遇水 白色不透明固体,易潮解,密度 2.12,熔点
和水蒸气大量放热, 318.4℃,沸点:1390℃,溶于水、乙醇,不
形成腐蚀性溶液。与 溶于丙酮。强碱,本品有强烈刺激和腐蚀
M——液体分子量; U——蒸发液体表面上的空气流速,m/s; P——相应于液体温度下空气的饱和蒸汽分压力,mmHg; F——蒸发面的面积,m2。 9.2 酸性蚀刻废液回收系统 酸性蚀刻废液回收系统中组分调节在尺寸为 1000*500*1000mm 再生液添加缸 中进行,在搅拌混合过程中将有 HCl 产生,再生液添加缸上部有盖板,风速取为 0.2m/s,再生液添加缸盐酸浓度控制在 20%,饱和蒸汽压 P=27.3pa(2mmHg),则 HCl 挥发量为 0.018kg/h,收集效率在 95%以上,有组织收集量约为 0.017kg/h。挥 发的 HCl 经相应的抽风管连接到废气洗涤塔内,送入碱液喷淋洗涤塔处理(和碱性蚀 刻液处理系统硫酸雾处理共同设置 1 套),尾气通过 1 个 15m 高排气筒排放。
≥99%
≥31%
≥99% /
≥96% 100% 100% 10um
年消耗量
1440t
40t 500t 20t 60t 35t 450kg 720kg 144 支
最大储存量
3
50 m
0.5t 30t 2t 2t 3t 20kg 30Kg 48 支
包装规格 储运方式
3
10m /罐
液态、储罐
25kg/袋
3
酸性蚀刻废液再生循环回收利用系统
1.项目背景
在线路板制造流程中的蚀刻工序,是线路板制造的一道重要工序,此工序过程中产 生的废液是一种高含铜量的废液[含铜 100-180 克/升]。对此蚀刻废液,目前通行的做 法是作为危险固废由资质单位进行回收处理。从清洁生产的角度来看,蚀刻废液具有较 高的回收价值。作为废物处理,一方面是废物处理公司对蚀刻液中的铜进行回收后,对 废液中酸及少量的金属铜离子的处理存在较大的难度,造成“二次污染”,从而对当地 水体生态系统造成较大破坏;另一方面,蚀刻液作为废物处理极大的增加了企业的运行 成本。
目前,蚀刻液再生及铜回收技术已经成熟,该回收技术能将废蚀刻液完全循环再 生,并获得高经济价值的电解铜产品且整个生产过程为闭路循环,对 PCB 行业实现清洁 生产和资源循环利用具有里程碑的意义。2009 年 2 月 1 日国家正式颁布的《清洁生产 标准印制电路板制造业》(HJ 450-2008)中就明确规定,一、二类清洁生产企业必须配 置此类资源回收设备。
6. 产污环节
6.1 本项目污染物产生环节汇总:
类别
废气
有组织
废液 固废 噪声
有组织
有组织 酸碱泵 1 酸碱泵 2
污染源 酸性蚀刻废液电解、组 份调节 酸性蚀刻废液电解、组 份调节 洗气塔 酸性蚀刻液定期排放 四芯过滤 铁水吸收槽
等效 A 声级
污染组成 HCL、Cl2
HCL pH、COD、SS COD、SS、总铜
酸发生中和反应并放 性。
热。
分子量 106.44,通常为白色或微黄色等轴晶
体。味咸而凉,易溶于水、微溶于乙醇。在 酸性溶液中有强氧化作用,300℃ 以上分解
不燃爆
出氧气
毒性毒理 LD50400mg/kg,(兔经口); LC504600mg/m3,1 小时(大鼠吸入)