夹杂物的生成及控制
焊缝中的夹杂物名词解释

焊缝中的夹杂物名词解释焊接作为一种常见的连接技术,广泛应用于工业生产和制造领域中。
在焊接过程中,焊接接头中往往会存在一些不理想的因素,其中之一就是夹杂物。
夹杂物是焊缝中的一种非金属或金属异物,它们可能对焊接接头的强度和性能产生不良影响。
因此,了解夹杂物的类型和特点,对于优化焊接接头的质量和性能具有重要意义。
一、夹杂物的定义夹杂物是指在焊缝中存在的各种杂质,包括金属夹杂物和非金属夹杂物。
金属夹杂物主要指金属颗粒、气泡和夹杂等形状的物质,而非金属夹杂物主要指矿渣、油污、灰尘等。
夹杂物可能是由于焊接材料、焊接工艺、操作不当或环境污染等因素引起的。
二、夹杂物的分类1. 金属夹杂物金属夹杂物包括金属颗粒、气泡和夹杂等。
金属颗粒是金属夹杂物中最常见的形式,它们可能来自焊材、母材或其他焊接材料。
气泡是由于焊接过程中存在气体溶解度和气泡脱出问题而形成的。
夹杂是指不溶于金属基体的残余物质。
2. 非金属夹杂物非金属夹杂物主要包括矿渣、油污、灰尘等。
矿渣是在焊接过程中产生的,由于焊芯和焊渣等材料的残留而形成。
油污则是指焊件表面或环境中存在的油脂或润滑剂等污染物。
灰尘是由于焊接作业环境不洁净所致。
三、夹杂物的形成原因夹杂物的形成原因多种多样,主要包括以下几个方面:1. 焊材质量问题:焊材中含有金属碎屑、气泡,或含有过多的夹杂物。
2. 焊接工艺问题:焊接工艺参数设置不当,如焊接温度、焊接速度等。
3. 操作不当:焊接操作过程中存在疏忽或操作不规范等问题。
4. 环境污染:焊接作业环境中存在油脂、灰尘等污染物。
四、夹杂物对焊接接头的影响夹杂物的存在对于焊接接头的质量和性能可能产生以下不良影响:1. 强度降低:夹杂物会破坏焊接接头的结晶结构,导致焊缝强度降低。
2. 腐蚀敏感性增加:夹杂物会使焊接接头的耐腐蚀性下降,易受到腐蚀介质的侵蚀。
3. 疲劳性能下降:夹杂物可能成为应力集中点,导致焊接接头在循环载荷下易于发生疲劳破坏。
4. 导电性能下降:夹杂物会影响焊接接头的导电性能,降低其电流传导能力。
铸造合金中的夹杂物与杂质控制
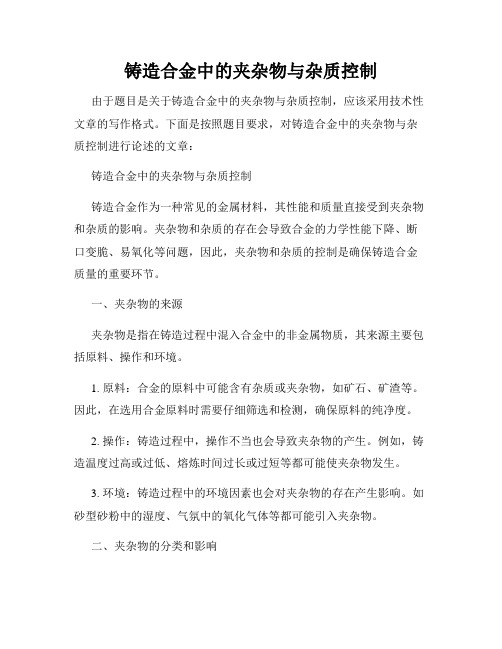
铸造合金中的夹杂物与杂质控制由于题目是关于铸造合金中的夹杂物与杂质控制,应该采用技术性文章的写作格式。
下面是按照题目要求,对铸造合金中的夹杂物与杂质控制进行论述的文章:铸造合金中的夹杂物与杂质控制铸造合金作为一种常见的金属材料,其性能和质量直接受到夹杂物和杂质的影响。
夹杂物和杂质的存在会导致合金的力学性能下降、断口变脆、易氧化等问题,因此,夹杂物和杂质的控制是确保铸造合金质量的重要环节。
一、夹杂物的来源夹杂物是指在铸造过程中混入合金中的非金属物质,其来源主要包括原料、操作和环境。
1. 原料:合金的原料中可能含有杂质或夹杂物,如矿石、矿渣等。
因此,在选用合金原料时需要仔细筛选和检测,确保原料的纯净度。
2. 操作:铸造过程中,操作不当也会导致夹杂物的产生。
例如,铸造温度过高或过低、熔炼时间过长或过短等都可能使夹杂物发生。
3. 环境:铸造过程中的环境因素也会对夹杂物的存在产生影响。
如砂型砂粉中的湿度、气氛中的氧化气体等都可能引入夹杂物。
二、夹杂物的分类和影响夹杂物按照形态和来源的不同,可以分为气体夹杂物、固体夹杂物和液体夹杂物。
它们分别来源于原材料、砂型、脱模剂等。
夹杂物的存在对合金的性能有着显著的影响。
首先,夹杂物会降低合金的强度和韧性,使其易于断裂。
其次,夹杂物还会影响合金的表面质量,引起合金表面的腐蚀和缺陷。
此外,夹杂物还可能影响合金的导热性能和热膨胀系数,导致合金的热失真。
三、夹杂物的控制方法为了控制铸造合金中的夹杂物,需要采取一系列措施。
1. 原料控制:对合金原料进行精选和检测,确保原材料的质量纯净。
2. 操作控制:在铸造过程中,严格控制熔炼温度、时间和工艺参数,避免产生夹杂物。
3. 环境控制:在铸造环境中要保持干燥和清洁,避免湿度和杂质的污染。
4. 精确检测:利用先进的检测技术和设备,对产成品进行全面检测,确保夹杂物的控制达到标准。
四、杂质的控制除了夹杂物,杂质也是影响铸造合金质量的重要因素。
连铸坯夹杂物产生原因分析及改进

连铸坯夹杂物产生原因分析及改进连铸坯夹杂物是指在连铸过程中,坯料表面或内部存在的一些异物或杂质。
夹杂物的产生原因可以从原料、工艺和设备等方面来分析。
下面将就连铸坯夹杂物的产生原因进行分析,并提出改进措施。
一、原料方面的原因:1.1 原料中的杂质:连铸坯夹杂物可能是由于原料中掺杂了一些杂质。
这些杂质可能来自原料的边角料、废料或回收材料等。
这些杂质在冶炼过程中不容易完全溶解,从而在连铸过程中形成夹杂物。
改进措施:对原料进行严格的筛分、清洗和破碎处理,以减少原料中的杂质含量。
1.2 未完全熔化的原料:原料在冶炼过程中未能完全熔化,残余的固体颗粒在连铸过程中会形成夹杂物。
改进措施:加强炉内熔化过程的控制,提高熔化温度和熔化时间,保证原料能够完全熔化。
二、工艺方面的原因:2.1 不合理的浇注工艺:浇注工艺参数的不合理会影响连铸坯的质量。
浇注速度过快、注入速度不均匀、浇注过程中的气体无法及时排出等都会造成夹杂物的产生。
改进措施:合理调整浇注工艺参数,控制好浇注速度和注入速度,确保浇注过程中的气体能够顺利排出。
2.2 结晶过程中的扩散现象:连铸过程中,坯料在结晶过程中会产生一定的扩散现象,由于扩散速度不同,会导致夹杂物在坯料内部的分布不均匀。
改进措施:优化连铸过程中的结晶条件,控制好结晶速度和结晶温度,减小夹杂物的分布不均匀性。
三、设备方面的原因:3.1 保护气体的不足:连铸过程中使用的保护气体对坯料表面的氧化物有较好的隔离作用。
如果保护气体流量不足,氧化物无法及时有效地被逼出,就会形成夹杂物。
改进措施:增加保护气体的流量,确保保护气体能够充分覆盖整个铸造过程。
3.2 坯料包浇注系统的设计不合理:连铸坯夹杂物的产生还与坯料包浇注系统的设计有关。
如果坯料包浇注系统的设计不合理,容易导致夹杂物的形成。
改进措施:优化坯料包浇注系统的结构,确保坯料包内的流动状态稳定,防止夹杂物的产生。
连铸坯夹杂物的产生原因与原料、工艺和设备等方面都有关。
底吹转炉钢中液相夹杂物的形成机理与控制方案

底吹转炉钢中液相夹杂物的形成机理与控制方案概述:底吹转炉是一种常用的钢铁冶炼设备,用于生产高品质的钢材。
然而,在底吹转炉生产过程中,钢中的液相夹杂物(如硫化物、氧化物等)的形成是一个常见的问题。
这些夹杂物会对钢的性能产生负面影响,因此了解液相夹杂物的形成机理以及控制方案对于提高钢的质量至关重要。
一、液相夹杂物的形成机理1. 成分:液相夹杂物的成分多种多样,其中包括硫化物、氧化物、碳化物、氮化物等。
这些夹杂物的形成主要与原料、炉料中的杂质以及底吹转炉操作参数有关。
2. 吸附和浮力:液相夹杂物的形成机理主要包括吸附和浮力两个方面。
原料和炉料中的杂质元素(如硫、氧、碳等)在钢液中会被吸附到夹杂物表面,形成液相夹杂物。
另一方面,炉底的浸没情况和钢液的流动状态会影响夹杂物的浮力,进而影响夹杂物的分布和浓度。
3. 变质作用:液相夹杂物的形成还与一些变质作用有关。
例如,底吹转炉中的氧化作用会导致氧化物的生成,而硫的存在会促进硫化物的形成。
此外,一些合金元素的加入也会影响液相夹杂物的形成机制。
二、控制液相夹杂物的方案1. 原料净化:为了控制液相夹杂物的形成,可以从原料净化入手。
采用高质量的生铁、废钢和合金元素,控制其中的杂质含量,可以有效减少液相夹杂物的形成。
2. 炉料配制:合理的炉料配制有助于控制液相夹杂物。
通过选择合适的炉料化学成分,控制硫、氧等元素的含量,可以减少夹杂物的生成。
3. 操作参数控制:底吹转炉的操作参数对于液相夹杂物的形成也起着重要的作用。
通过调整炉压、炉料粒度、渣化特性等操作参数,可以控制钢液的流动状态,降低夹杂物的生成。
4. 渣化控制:合理的渣化控制能够减少液相夹杂物的形成。
通过选择适当的渣剂和合理的渣化方式,提高渣中的还原性和脱硫能力,可以减少夹杂物与渣中元素的反应,从而减少夹杂物的形成。
5. 合金元素的加入:合适的合金元素的加入可以改善钢液的质量,并减少液相夹杂物的形成。
例如,加入硅、钙等元素可以提高夹杂物与钢液之间的界面能,减少夹杂物的生成。
连铸坯夹杂物产生原因分析及改进
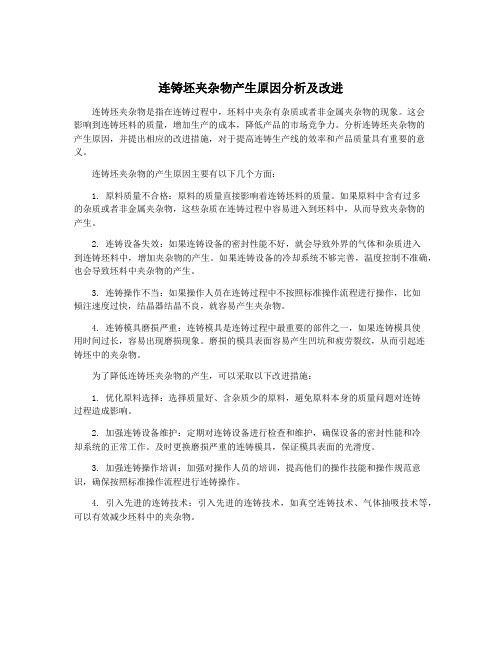
连铸坯夹杂物产生原因分析及改进连铸坯夹杂物是指在连铸过程中,坯料中夹杂有杂质或者非金属夹杂物的现象。
这会影响到连铸坯料的质量,增加生产的成本,降低产品的市场竞争力。
分析连铸坯夹杂物的产生原因,并提出相应的改进措施,对于提高连铸生产线的效率和产品质量具有重要的意义。
连铸坯夹杂物的产生原因主要有以下几个方面:1. 原料质量不合格:原料的质量直接影响着连铸坯料的质量。
如果原料中含有过多的杂质或者非金属夹杂物,这些杂质在连铸过程中容易进入到坯料中,从而导致夹杂物的产生。
2. 连铸设备失效:如果连铸设备的密封性能不好,就会导致外界的气体和杂质进入到连铸坯料中,增加夹杂物的产生。
如果连铸设备的冷却系统不够完善,温度控制不准确,也会导致坯料中夹杂物的产生。
3. 连铸操作不当:如果操作人员在连铸过程中不按照标准操作流程进行操作,比如倾注速度过快,结晶器结晶不良,就容易产生夹杂物。
4. 连铸模具磨损严重:连铸模具是连铸过程中最重要的部件之一,如果连铸模具使用时间过长,容易出现磨损现象。
磨损的模具表面容易产生凹坑和疲劳裂纹,从而引起连铸坯中的夹杂物。
为了降低连铸坯夹杂物的产生,可以采取以下改进措施:1. 优化原料选择:选择质量好、含杂质少的原料,避免原料本身的质量问题对连铸过程造成影响。
2. 加强连铸设备维护:定期对连铸设备进行检查和维护,确保设备的密封性能和冷却系统的正常工作。
及时更换磨损严重的连铸模具,保证模具表面的光滑度。
3. 加强连铸操作培训:加强对操作人员的培训,提高他们的操作技能和操作规范意识,确保按照标准操作流程进行连铸操作。
4. 引入先进的连铸技术:引入先进的连铸技术,如真空连铸技术、气体抽吸技术等,可以有效减少坯料中的夹杂物。
夹杂物的生成及控制

夹杂物的生成及控制作者:shicm 发表日期:2007-5-28 阅读次数:7631 非金属夹杂物情况及分类按其化学成分组成和结构可以分以下几类(1)氧化物夹杂:单一金属氧化物、硅酸盐、尖晶石和各种钙铝酸盐;(2)硫化物夹杂:MnS、CaS等,在轧制过程中具有良好的变形能力;(3)磷化物夹杂:CaP、BaP等还原脱磷产物,在一般钢种中较少出现;(4)氮化物夹杂:TiN、ZrN等夹杂物,是钢液从大气中吸氮的产物;(5)含不同类型夹杂物的复合夹杂。
按其来源主要分为两类:(1)外来夹杂物,主要来源为炉渣卷入钢液形成的卷渣、钢液或炉渣与炉衬耐火材料接触时的侵蚀产物、铁合金及其它炉料带入的夹杂等等,在浇铸过程未及时上浮而残留在钢中,它偶然出现,外形不规则,尺寸大,危害极大;(2)内生夹杂物,在液态或固态钢中,由于脱氧和凝固时进行的各类物理化学反应而形成的,主要是和钢中氧、硫、氮的反应产物,它的形成有四个阶段,钢液脱氧反应时形成的成为原生(一次)夹杂;出钢和浇铸过程中温度下降平衡移动时形成的成为二次夹杂;钢水凝固过程中生成为再生(三次)夹杂;固态相变时因溶解度变化而生成的成为四次夹杂;由于一次、三次夹杂生成和析出的热力学和动力学条件最有利,因此可以认为内生夹杂大部分是在脱氧和凝固时生成的,因此控制夹杂最主要的就是要加强脱氧和严格防止二次氧化。
(3)一些尺寸较大的多相复合结构的夹杂物,有时是不同类型的内生夹杂复合而成,有时则是内生夹杂物与外来夹杂物互相包裹而形成的。
为了方便生产评级和比较,按照标准评级图显微检验法根据夹杂物形态和大小分布将夹杂物分为A、B、C、D、DS五类,这五大类夹杂物代表最常观察到的夹杂物的类型和形态:—A类(硫化物类):具有高的延展性,有较宽范围形态比(长度/宽度)的单个灰色夹杂物,一般端部呈圆角;—B类(氧化铝类):大多数没有变形,带角的,形态比小(一般<3),黑色或带蓝色的颗粒,沿轧制方向排成一行(至少有3个颗粒);—C类(硅酸盐类):具有高的延展性,有较宽范围形态比(一般>3)的单个呈黑色或深灰色夹杂物,一般端部呈锐角;—D类(球状氧化物类,如钙铝酸盐):不变形,带角或圆形的,形态比小(一般<3),黑色或带蓝色的,无规则分布的颗粒;—DS类(单颗粒球状类):圆形或近似圆形,直径>13μm的单颗粒夹杂物。
夹杂物成分及形态控制
钢帘线夹杂物控制实验室研究
• 当炉渣碱度为0.71~1.36,Al2O3含量低于8 %时,可以将夹杂物的成分控制在塑性区 或其周边的区域。
夹杂物中的Al2O3含量随着钢液中酸溶铝含量的 增加而增加,当夹杂物中Al2O3含量为8%~25 %,钢液[Al]s含量应控制在0.0006%以下。
夹杂物成分及形态控制
刘建华
1. 概述
• 夹杂物成分和形态控制技术是现代洁 净钢冶炼的主要内容之一,不同用途的 钢材对非金属夹杂物的形态、数量、 组成有不同的要求.
• 根据钢种的要求及夹杂物的性质提出 夹杂物成分和形态控制要求。
• 根据钢-夹杂物反应热力学,利用MnO-Al2O3SiO2和CaO-Al2O3-SiO2等三元系图内钢液成分 等值线来预测夹杂物组成及钢液中氧、硅、锰、 铝、钙等成分的控制,并制定顶渣成分控制.
• 部分钢种还需结合S-Me反应热力学提出 钢中硫含量控制策略
• 问题:1)夹杂物是多元的;2)夹杂物有 时熔点较高,是固态的,反应未达到平衡; 3)炼钢、精炼工艺对夹杂物组成影响较大; 4)热力学相图局部区域组元活度测量有较 大误差
2. 脱氧剂对夹杂物成分的影响
• 脱氧剂对内生夹杂物的成分存在巨大影响。 • 根据钢种和产品质量,脱氧分为三种模式:
USS/KOBE钢厂精炼过程中夹杂物成分变化在相图中的体现
2)Kakogawa Works钢厂采用BOF-LF- CC工艺生产钢帘线
Kakogawa Works钢厂夹杂物成分变化在精炼过程中的变化
• Mn/Si低时形成SiO2夹杂会导致水口堵塞;Mn/Si 高时生成典型的液态MnO•SiO2,夹杂物容易上 浮。因此因调整钢成分,保持Mn/Si>2.5,
连铸坯夹杂物产生原因分析及改进
连铸坯夹杂物产生原因分析及改进
连铸坯夹杂物是指连铸坯表面或内部夹杂杂质的存在,这些夹杂物会对钢材质量产生
不良影响,影响铸坯表面和内部的均匀性和机械性能。
连铸坯夹杂物的产生原因主要有以
下几个方面:
1. 原材料夹杂物: 钢中的夹杂物主要来自于原材料、废钢和添加合金等物料,在钢
炉中未能完全脱除或控制。
2. 氧化物被再还原: 在钢液在连铸模内流动过程中,由于气体(氧、氮、氢)和钢液接触产生氧化反应,并形成氧化物,如果连铸坯表面温度过低且气体不能有效排除,那么
铸坯表面就容易形成氧化物。
这些氧化物随着液流一起进入连铸模中,如果温度下降过快,就会再次还原成气体和新的氧化物。
3. 连铸成分不一致: 连铸过程中,如果出现连铸成分梯度过大,过渡区过长,密度
差异大等问题,就会造成钢液的不同成分相互混合,产生夹杂物。
针对以上问题,可以采取以下改进措施:
1. 完善原材料检测制度: 通过加强原材料的检测工作,确保原材料中夹杂物的产生
率低,并采取有效措施控制沉积在钢炉底部的杂质。
2. 加强连铸过程监控: 通过加强连铸过程的电子监控,对铸坯进行实时监测,及时
发现和排除夹杂物。
3. 控制氧化物次氧化反应: 在连铸过程中,通过控制氧化反应、加大气体流量、降
低钢液表面温度等措施,有效减少夹杂物的产生率。
4. 优化连铸工艺: 采取合理连铸成分、减少过渡区,保证钢液的均匀性,减少夹杂
物的产生。
综上所述,连铸坯夹杂物的产生有多种原因,但可以通过加强原材料检测、加强连铸
过程监控、减少氧化反应、优化连铸工艺等措施来降低夹杂物产生率,提高连铸坯质量。
连铸坯夹杂物产生原因分析及改进
连铸坯夹杂物产生原因分析及改进连铸坯夹杂物的产生原因可以从多个方面进行分析和改进。
下面是一个大致的分析和改进措施,供您参考。
1. 原料质量问题:连铸坯夹杂物主要来自于熔化的金属和废钢原料,在回炉炉中的熔化过程中,可能会夹杂一些金属碎屑、渣滓和氧化物等杂质。
2. 冶炼工艺问题:连铸坯夹杂物的产生也与冶炼过程中的工艺参数有关。
冶炼温度不稳定、浇注速度过快或过慢、浇注过程中的氧气和杂质溶解等都可能导致夹杂物的产生。
3. 连铸机设备问题:连铸机的状态和性能也可能对夹杂物产生产生影响。
结晶器内部的损坏、结晶器震动不稳定、传动系统不正常等问题都可能导致夹杂物产生。
二、改进措施1. 提高原料质量:采用优质原料,并加强原料筛查和预处理,规范原料质量的控制。
可以采用一些物理和化学方法对废钢进行预处理,如磁选、浮选、热处理等,以减少夹杂物的含量。
2. 优化冶炼工艺:通过调整冶炼工艺参数,控制冶炼温度稳定性,避免过高或过低的温度对金属液中的杂质产生不良影响。
3. 改进连铸机设备:加强设备的维护保养,及时发现和修复连铸机设备的问题,确保连铸过程的稳定性和可靠性。
可以对结晶器进行优化设计,改进震动稳定性和结晶器内部布置,以减少夹杂物的产生。
4. 强化质量控制:加强连铸工艺过程的监测和控制,通过合理的浇注速度、浇注方式和辅助工具,减少夹杂物的产生。
建立完善的质量控制体系,追踪和分析夹杂物的来源和产生规律,以便更好地进行改进和控制。
5. 加强人员培训:提高工人的操作技能,加强工艺和设备知识的培训,使其能够熟练应对连铸过程中可能出现的问题,并及时采取正确的措施进行解决。
液态金属加工中的夹杂物控制
液态金属加工中的夹杂物控制在液态金属加工中,夹杂物的控制是一项至关重要的任务。
夹杂物是液态金属中的非金属颗粒或微小气泡,它们可能在金属凝固过程中形成,对最终产品的性能产生严重影响。
因此,了解夹杂物的来源、影响以及如何有效地控制它们,对于提高产品质量和生产效率具有重要意义。
一、夹杂物的来源夹杂物的来源主要有两个途径:原材料和加工过程。
在液态金属的制备过程中,如果原材料含有杂质,这些杂质可能在熔炼或净化过程中进入液态金属。
此外,在浇铸和凝固过程中,外部的颗粒或气体也可能会进入液态金属中形成夹杂物。
二、夹杂物的影响夹杂物对液态金属加工产品的性能有严重影响。
首先,它们会降低金属的强度和硬度,因为夹杂物往往是脆性的,容易在应力作用下断裂。
其次,夹杂物可能会引起应力集中,导致产品在铸造缺陷处的开裂。
此外,夹杂物还可能影响产品的导电性和导热性,从而影响产品的使用性能。
三、夹杂物的控制方法为了控制液态金属加工中的夹杂物,我们可以采取以下措施:1. 选用纯度高的原材料:在选择原材料时,应尽量选用纯度高的金属材料,以减少夹杂物的来源。
2. 优化熔炼和净化工艺:熔炼和净化工艺对夹杂物的含量有重要影响。
通过优化这些工艺参数,可以减少新夹杂物的形成并去除一部分已形成的夹杂物。
3. 浇铸和凝固过程的控制:在浇铸和凝固过程中,应采取措施减少颗粒或气体的进入。
例如,可以使用净化剂来吸附可能进入液态金属中的气体,并采用合适的浇铸速度和温度来减少颗粒的进入。
4. 定期检查和清理设备:在生产过程中,定期检查设备和清理残留的杂质是必要的。
这有助于减少新的夹杂物的形成并去除已形成的夹杂物。
综上所述,通过采取以上措施,我们可以有效地控制液态金属加工中的夹杂物,从而提高产品质量和生产效率。
这些措施不仅有助于提高产品的性能和使用寿命,还有助于降低生产成本和提高企业的竞争力。
- 1、下载文档前请自行甄别文档内容的完整性,平台不提供额外的编辑、内容补充、找答案等附加服务。
- 2、"仅部分预览"的文档,不可在线预览部分如存在完整性等问题,可反馈申请退款(可完整预览的文档不适用该条件!)。
- 3、如文档侵犯您的权益,请联系客服反馈,我们会尽快为您处理(人工客服工作时间:9:00-18:30)。
夹杂物的生成及控制
作者:shicm 发表日期:2007-5-28 阅读次数:763
1 非金属夹杂物情况及分类
按其化学成分组成和结构可以分以下几类
(1)氧化物夹杂:单一金属氧化物、硅酸盐、尖晶石和各种钙铝酸盐;
(2)硫化物夹杂:MnS、CaS等,在轧制过程中具有良好的变形能力;
(3)磷化物夹杂:CaP、BaP等还原脱磷产物,在一般钢种中较少出现;
(4)氮化物夹杂:TiN、ZrN等夹杂物,是钢液从大气中吸氮的产物;
(5)含不同类型夹杂物的复合夹杂。
按其来源主要分为两类:
(1)外来夹杂物,主要来源为炉渣卷入钢液形成的卷渣、钢液或炉渣与炉衬耐火材料接触时的侵蚀产物、铁合金及其它炉料带入的夹杂等等,在浇铸过程未及时上浮而残留在钢中,它偶然出现,外形不规则,尺寸大,危害极大;(2)内生夹杂物,在液态或固态钢中,由于脱氧和凝固时进行的各类物理化学反应而形成的,主要是和钢中氧、硫、氮的反应产物,它的形成有四个阶段,钢液脱氧反应时形成的成为原生(一次)夹杂;出钢和浇铸过程中温度下降平衡移动时形成的成为二次夹杂;钢水凝固过程中生成为再生(三次)夹杂;固态相变时因溶解度变化而生成的成为四次夹杂;由于一次、三次夹杂生成和析出的热力学和动力学条件最有利,因此可以认为内生夹杂大部分是在脱氧和凝固时生成的,因此控制夹杂最主要的就是要加强脱氧和严格防止二次氧化。
(3)一些尺寸较大的多相复合结构的夹杂物,有时是不同类型的内生夹杂复合而成,有时则是内生夹杂物与外来夹杂物互相包裹而形成的。
为了方便生产评级和比较,按照标准评级图显微检验法根据夹杂物形态和大小分布将夹杂物分为A、B、C、D、DS五类,
这五大类夹杂物代表最常观察到的夹杂物的类型和形态:
—A类(硫化物类):具有高的延展性,有较宽范围形态比(长度/宽度)的单个灰色夹杂物,一般端部呈圆角;
—B类(氧化铝类):大多数没有变形,带角的,形态比小(一般<3),黑色或带蓝色的颗粒,沿轧制方向排成一行(至少有3个颗粒);
—C类(硅酸盐类):具有高的延展性,有较宽范围形态比(一般>3)的单个呈黑色或深灰色夹杂物,一般端部呈锐角;
—D类(球状氧化物类,如钙铝酸盐):不变形,带角或圆形的,形态比小(一般<3),黑色或带蓝色的,无规则分布的颗粒;
—DS类(单颗粒球状类):圆形或近似圆形,直径>13μm的单颗粒夹杂物。
每类夹杂物又根据非金属夹杂物颗粒宽度的不同分成粗系和细系两个系列,每个系列由表示夹杂物含量递增从0.5至3级的六个等级图片组成,根据100倍显微视场下与标准图谱对比,来确定夹杂物级别。
2 国内外先进厂家夹杂物控制情况及我厂现状
近年来,加拿大的Mitchell 和新日铁的福本提出“零夹杂钢”的概念。
所谓“零夹杂钢”,不是钢中无夹杂物,而是夹杂物尺寸小于1μm。
在凝固之前非金属夹杂物不析出,在固相状态下析出的非金属夹杂物高度弥散分布,无法用光学显微镜观察到,这时夹杂物可发挥有益的作用,使钢的抗疲劳性能大幅度提高。
目前,日本先进厂家可以将钢中总氧含量控制在2~5ppm,钢中夹杂大小基本上控制在5~8μm以下。
我厂评价夹杂物主要根据标准图谱评级,目前夹杂物控制极不稳定,从评级来看,A细和D细系基本上都是1级,A粗、D粗、C系基本上都是0级,比较稳定,但B细系波动比较大,不时出现超长情况,另外还有出现由于夹杂物产生质量异议,钢中总氧含量在8~35ppm之间,波动也比较大。
3夹杂物控制原理
其中A类夹杂物与硫含量相关,通过脱硫来控制,C类为硅酸盐夹杂物,在现代精炼设备和条件下一般很少存在。
目前炼钢厂夹杂物波动最大、危害最大的是B类夹杂物,经常出现B细夹杂物评级超标。
B类夹杂与钢中全氧含量有很大相关性,B类夹杂与全氧量成一种线性递增关系,要降低钢中的B类夹杂总量,最主要的是降低总氧量。
因此一般把减少夹杂和加强脱氧要结合起来考虑。
解决夹杂物问题主要应该从热力学和动力学两方面考虑,热力学解决夹杂物的形成和变性,动力学解决夹杂物的脱除。
热力学的核心问题是围绕钢中溶解氧和全氧的含量决定合理的脱氧制度、合适的温度和还原气氛控制、以及对夹杂物的变性处理。
动力学的核心问题主要是通过优化精炼渣的物理化学性能(比如碱度、黏度,熔化温度等因素)、合适的吹氩制度和镇定时间、稳定的耐火材料、良好的中间包流场和合适的保护渣性能等来促进夹杂物的上浮和吸附去除。
4 夹杂物控制操作
对于夹杂物控制实际操作来说,首先要强调工艺的稳定性、标准化操作,必须抓好关键工序的操作。
电炉出钢要尽量减少下渣,稳定出钢的钢水量、温度和成分,尽量控制好稳定的过氧化程度,为精炼的顺利脱氧、脱硫作好前提准备;
精炼要注意优化脱氧工艺,目前炼钢厂生产基本上都是采用加铝进行强脱氧,将钢中溶解氧降低至2-4ppm,然后通过VD真空处理、保护浇铸、中间包冶。