结晶器用锆青铜中夹杂物的分析与控制
连铸坯夹杂物产生原因分析及改进

连铸坯夹杂物产生原因分析及改进连铸是指通过连续铸造设备将熔液连续浇铸成坯料的一种方法。
在连铸过程中,夹杂物是最常见的缺陷之一,它们对铸坯的质量和性能有着重要的影响。
分析连铸坯夹杂物产生原因,并采取相应的改进措施,可以有效地提高铸坯质量和生产效率。
连铸坯夹杂物产生的主要原因有以下几个方面:1.原料质量:连铸坯的夹杂物往往与原料的质量有关。
原料中存在的金属夹杂物、非金属夹杂物和气泡等会成为连铸夹杂物的来源。
提高原料的质量和纯净度,减少夹杂物的含量是解决连铸坯夹杂物问题的一项重要措施。
2.炉次操作:炉次操作对连铸坯夹杂物的产生也有较大的影响。
炉渣的不合理处理、熔炼温度和时间的控制不当等都可能导致夹杂物产生。
合理的炉次操作和炉渣处理是减少夹杂物产生的关键。
3.结晶器和冷却系统:结晶器和冷却系统的设计和使用状态对连铸坯夹杂物的产生起着重要的作用。
结晶器的凝固状态、结晶器涂层的质量和结晶器冷却水流量的控制都会影响到连铸坯的质量和夹杂物含量。
合理设计结晶器和冷却系统,并保持其良好的使用状态,对减少夹杂物具有重要意义。
4.连铸工艺参数:连铸工艺参数的选择和控制也是减少夹杂物产生的关键。
保证浇注速度、拉伸速度、结晶器超熔度、超温和过度冷却等参数的合理选择和控制,对提高铸坯质量和减少夹杂物具有重要的影响。
改进方法:1.加强原料质量控制:加强对原料的质量控制,选择优质的原料供应商,进行严格的质检,确保原料的纯净度和无夹杂物。
2.优化炉次操作:加强炉次操作的管理和控制,合理控制熔炼温度和时间,严格进行炉渣处理,确保炉渣中夹杂物的除去。
3.改善结晶器和冷却系统:优化结晶器和冷却系统的设计,确保结晶器的良好工作状态,减少结晶器涂层的破损和脱落,调整冷却水流量,避免过度冷却和不足冷却的情况。
连铸坯夹杂物的产生是多方面因素共同作用的结果。
通过加强原料质量控制、优化炉次操作、改善结晶器和冷却系统以及优化连铸工艺参数等措施,可以有效地减少夹杂物产生,提高铸坯质量和生产效率。
摘要:分析了连铸坯中夹杂物的来源和浇注过程中的二次氧化问题。

摘要:分析了连铸坯中夹杂物的来源和浇注过程中的二次氧化问题。
介绍了国内外先进炼钢厂(新日铁、JFE、克鲁斯、迪林根、浦项和宝钢等)中间包夹杂物的去除与控制措施。
通过增大中间包容量、采用H型中间包或离心流动中间包、设置中提供间包气幕挡墙和中间包控流装置,优化中间包结构。
通过采用中间包密封吹氩技术控制中间包开浇的二次污染;采用汇流旋涡抑制器防止中间包浇注过程中卷渣;采用碱性包衬和碱性覆盖剂、中间包无氧化烘烤与电磁感应加热、中间包连续真空浇注处理和电磁过滤,可以降低钢水二次污染,防止二次氧化,促进夹杂物上浮,提高铸坯的质量。
前言随着用户对钢材质量要求的进一步提高,中间包的精炼功能也越来越受到人们的关注。
作为设置在钢包和结晶器之间的冶金反应器,中间包除了实施钢水分配、稳定注流和保证连浇的基本功能外,还可以作为钢水的精炼容器。
通过中间包冶金,可以防止钢水二次氧化和吸气、改善钢水流动状态、防止卷渣和促进夹杂物上浮、微调钢水成分、控制夹杂物形态和精确控制钢水过热度。
中间包冶金对提高连铸机作业率和优化作业、顺利多炉连浇、扩大连铸品种改善铸坯质量等均起到重要作用。
1连铸坯中夹杂物的来源从炼钢生产流程来看,铸坯的洁净度主要取决于钢水进入结晶器之前的炼钢、精炼和中间包冶金工序,钢水中夹杂物的主要来源是内生夹杂物和外来夹杂物。
1 . 1内生夹杂物内生夹杂物主要是脱氧产物,是钢中的合金化元素与溶解在钢水中的氧以及硫、氮的反应产物。
如铝镇静钢,脱氧产物以Al 2O3为主;硅镇静钢,脱氧产物以MnO•Si O2 为主;钙处理钢,脱氧产物以mCaO•nAl 2O3、mCaO•nAl 2O3 •X为主;钛处理钢,脱氧产物以Ti O2、Al 2O3、Ti N、Al 2O3 与Ti N复合夹杂物为主。
内生夹杂物数量多,颗粒较小(一般小于10μm) ,分布较均匀,成分简单,对钢的质量危害较小。
1 . 2外来夹杂物外来夹杂物是指从炼钢到浇注的过程中,二次氧化产物和机械卷入钢中的各种氧化物。
连铸坯夹杂物产生原因分析及改进

连铸坯夹杂物产生原因分析及改进【摘要】连铸坯夹杂物是指在连铸生产过程中出现的一种缺陷,严重影响铸坯的质量和性能。
本文通过对连铸坯夹杂物的定义和影响进行分析,探讨了产生原因和改进方法。
夹杂物产生的主要原因包括连铸过程中的气体和杂质混入、结晶器和水口设计不合理等。
针对这些原因,可以通过改进连铸设备、优化操作流程和提高工人技术水平来减少夹杂物产生。
本文强调了连铸坯夹杂物产生原因分析及改进的重要性,并展望了未来研究方向。
通过技术改进的实施,可以有效提高铸坯质量,提升生产效率。
深入研究连铸坯夹杂物的产生原因和改进方法对于提高连铸生产质量具有重要意义。
【关键词】连铸坯夹杂物、产生原因、改进方法、技术改进、研究背景、目的、影响、意义、展望、未来研究方向、总结1. 引言1.1 研究背景连铸坯夹杂物产生是影响连铸坯质量的重要因素之一,夹杂物的存在直接影响着钢材的力学性能和表面质量,甚至可能导致产品质量不合格。
对连铸坯夹杂物产生原因进行深入分析,并寻找相应的改进方法是当前研究的热点与难点之一。
近年来,随着我国钢铁产业的快速发展,对连铸坯质量要求也越来越高。
夹杂物的产生会影响到产品的品质和市场竞争力,因此解决夹杂物产生问题对于提高产品质量,增强企业竞争力具有重要意义。
当前,国内外学者对连铸坯夹杂物的产生原因进行了一定的研究,但仍存在一些问题有待解决。
针对这些问题,本文将对连铸坯夹杂物的产生原因进行全面的分析,探讨改进方法,并提出技术改进的实施方案,以期为相关领域的研究提供新的思路和方法。
1.2 目的研究连铸坯夹杂物产生原因及改进方法的目的在于提高连铸坯质量,降低成本,改善生产环境,保障生产安全,提高企业竞争力。
通过深入分析连铸坯夹杂物的形成机理,找出产生夹杂物的根本原因,并提出有效的改进措施,从根本上解决夹杂物问题。
通过技术改进的实施,推动企业技术创新,提高生产效率,降低能耗,使企业更加环保和可持续发展。
这项研究旨在深化对连铸坯夹杂物问题的理解,为相关领域的研究提供新思路和方法,并对工业生产具有一定的推动作用。
连铸坯夹杂物产生原因分析及改进

连铸坯夹杂物产生原因分析及改进连铸坯夹杂物是指在连铸过程中,坯料表面或内部存在的一些异物或杂质。
夹杂物的产生原因可以从原料、工艺和设备等方面来分析。
下面将就连铸坯夹杂物的产生原因进行分析,并提出改进措施。
一、原料方面的原因:1.1 原料中的杂质:连铸坯夹杂物可能是由于原料中掺杂了一些杂质。
这些杂质可能来自原料的边角料、废料或回收材料等。
这些杂质在冶炼过程中不容易完全溶解,从而在连铸过程中形成夹杂物。
改进措施:对原料进行严格的筛分、清洗和破碎处理,以减少原料中的杂质含量。
1.2 未完全熔化的原料:原料在冶炼过程中未能完全熔化,残余的固体颗粒在连铸过程中会形成夹杂物。
改进措施:加强炉内熔化过程的控制,提高熔化温度和熔化时间,保证原料能够完全熔化。
二、工艺方面的原因:2.1 不合理的浇注工艺:浇注工艺参数的不合理会影响连铸坯的质量。
浇注速度过快、注入速度不均匀、浇注过程中的气体无法及时排出等都会造成夹杂物的产生。
改进措施:合理调整浇注工艺参数,控制好浇注速度和注入速度,确保浇注过程中的气体能够顺利排出。
2.2 结晶过程中的扩散现象:连铸过程中,坯料在结晶过程中会产生一定的扩散现象,由于扩散速度不同,会导致夹杂物在坯料内部的分布不均匀。
改进措施:优化连铸过程中的结晶条件,控制好结晶速度和结晶温度,减小夹杂物的分布不均匀性。
三、设备方面的原因:3.1 保护气体的不足:连铸过程中使用的保护气体对坯料表面的氧化物有较好的隔离作用。
如果保护气体流量不足,氧化物无法及时有效地被逼出,就会形成夹杂物。
改进措施:增加保护气体的流量,确保保护气体能够充分覆盖整个铸造过程。
3.2 坯料包浇注系统的设计不合理:连铸坯夹杂物的产生还与坯料包浇注系统的设计有关。
如果坯料包浇注系统的设计不合理,容易导致夹杂物的形成。
改进措施:优化坯料包浇注系统的结构,确保坯料包内的流动状态稳定,防止夹杂物的产生。
连铸坯夹杂物的产生原因与原料、工艺和设备等方面都有关。
连铸坯夹杂物产生原因分析及改进
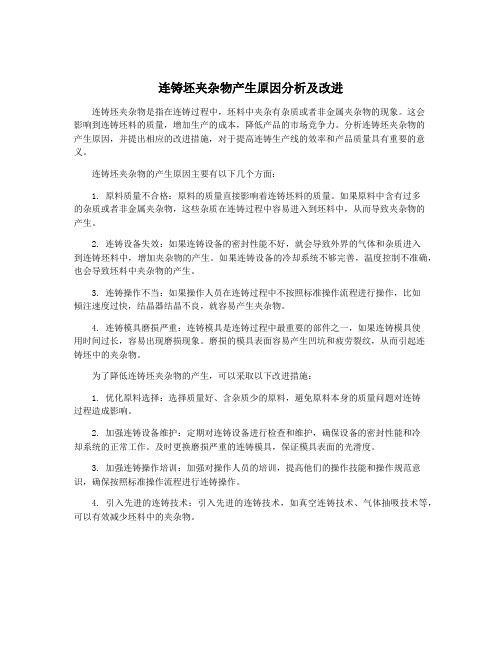
连铸坯夹杂物产生原因分析及改进连铸坯夹杂物是指在连铸过程中,坯料中夹杂有杂质或者非金属夹杂物的现象。
这会影响到连铸坯料的质量,增加生产的成本,降低产品的市场竞争力。
分析连铸坯夹杂物的产生原因,并提出相应的改进措施,对于提高连铸生产线的效率和产品质量具有重要的意义。
连铸坯夹杂物的产生原因主要有以下几个方面:1. 原料质量不合格:原料的质量直接影响着连铸坯料的质量。
如果原料中含有过多的杂质或者非金属夹杂物,这些杂质在连铸过程中容易进入到坯料中,从而导致夹杂物的产生。
2. 连铸设备失效:如果连铸设备的密封性能不好,就会导致外界的气体和杂质进入到连铸坯料中,增加夹杂物的产生。
如果连铸设备的冷却系统不够完善,温度控制不准确,也会导致坯料中夹杂物的产生。
3. 连铸操作不当:如果操作人员在连铸过程中不按照标准操作流程进行操作,比如倾注速度过快,结晶器结晶不良,就容易产生夹杂物。
4. 连铸模具磨损严重:连铸模具是连铸过程中最重要的部件之一,如果连铸模具使用时间过长,容易出现磨损现象。
磨损的模具表面容易产生凹坑和疲劳裂纹,从而引起连铸坯中的夹杂物。
为了降低连铸坯夹杂物的产生,可以采取以下改进措施:1. 优化原料选择:选择质量好、含杂质少的原料,避免原料本身的质量问题对连铸过程造成影响。
2. 加强连铸设备维护:定期对连铸设备进行检查和维护,确保设备的密封性能和冷却系统的正常工作。
及时更换磨损严重的连铸模具,保证模具表面的光滑度。
3. 加强连铸操作培训:加强对操作人员的培训,提高他们的操作技能和操作规范意识,确保按照标准操作流程进行连铸操作。
4. 引入先进的连铸技术:引入先进的连铸技术,如真空连铸技术、气体抽吸技术等,可以有效减少坯料中的夹杂物。
连铸坯夹杂物产生原因分析及改进

连铸坯夹杂物产生原因分析及改进【摘要】连铸坯夹杂物是影响连铸坯质量的重要因素之一。
本文从连铸坯夹杂物产生原因、改进措施和关键技术等方面进行了分析和探讨。
连铸坯夹杂物的形成可能与原料质量、工艺参数等因素有关,在连铸过程中容易产生。
为了提高连铸坯质量,可以采取一些控制措施和优化工艺流程,包括提高原料质量、调整工艺参数等。
连铸坯质量的改进不仅可以优化生产过程,提高产品质量,还可以降低生产成本,提高经济效益。
未来的研究方向应当深入研究连铸坯夹杂物的形成机理,进一步改进连铸工艺,提高连铸坯质量,为我国钢铁行业的发展做出贡献。
【关键词】连铸坯夹杂物, 产生原因, 改进措施, 关键技术, 工艺流程优化, 坯质量提高, 连铸坯质量, 形成机理, 连铸工艺改进.1. 引言1.1 研究背景连铸是一种连续铸造工艺,是在一个连续流动的铸模中进行的铸造方式,由于其高效节能的优势,被广泛应用于钢铁、有色金属等行业。
连铸坯夹杂物的产生却一直是制约连铸产品质量的一个重要问题。
夹杂物是指在连铸过程中夹杂在坯料中的杂质或气泡,严重影响了连铸坯的质量和性能。
夹杂物的产生有多种原因,主要包括原料质量不过关、连铸设备及工艺不完善、操作不当等方面。
一些固体夹杂物如氧化铁、硫化物等常常源自原料中的杂质,而气泡夹杂物则来源于钢水中气体的溶解度过高或者气体在过程中的渗透等。
连铸过程中的冷却速度、结晶过程等也会影响夹杂物形成的方式。
研究连铸坯夹杂物的产生原因,对于进一步提高连铸产品的质量、降低生产成本具有重要意义。
有必要深入探讨夹杂物的产生机理,找出关键的影响因素,并制定相应的改进措施。
本文将通过分析连铸坯夹杂物的产生原因,探讨改进措施和关键技术,以期为优化连铸工艺流程提供参考。
1.2 研究意义连铸坯夹杂物是连铸过程中常见的缺陷,对坯料质量和产品性能造成不利影响。
对于现代钢铁生产而言,提高产品质量和降低生产成本是至关重要的课题。
对连铸坯夹杂物产生原因进行深入分析和改进措施的研究具有重要的理论和应用价值。
浅析连铸坯中非金属夹杂物的产生及控制
浅析连铸坯中非金属夹杂物的产生及控制连铸坯中存在的非金属夹杂物对钢产品的质量将会带来极大的危害。
因此减少连铸坯中非金属夹杂物,使其具有高清洁度以保证钢的质量对连铸生产至关重要。
连铸坯中非金属夹杂物的来源比较复杂,有脱氧生成物、空气氧化、炉渣、覆盖剂、保护渣及耐火材料的熔损等。
因为从出钢后到中间包开浇,钢水二次氧化机会多、出钢过程的脱氧产物、挡渣失败、与耐火材料接触时间长等都易使钢水被污染。
另外结晶器保护渣的卷入及结晶器内钢水的强制对流,夹杂物被带到液相穴深处无法上浮,也将导致铸坯夹杂缺陷。
所以连铸生产过程中采用合理的操作工艺及技术,采取一切措施尽可能最大限度地去除钢中的非金属夹杂物,已成为连铸生产的关键。
随着技术的发展,钢中的夹杂物的浓度可控制得越来越低、即使存在一定的夹杂物也可使其变性。
1 连铸及铸坯非金属夹杂物的来源及性状1.1 钢中非金属夹杂物的分类钢中的非金属夹杂物主要是指钢中不具有金属性质的氧化物、硫化物、硅酸盐和氮化物等。
夹杂物的产生按其来源可以分为外来夹杂物和内生夹杂物。
外来夹杂物主要是在冶炼或凝固过程中混入而未及时浮出的炉渣或耐火材料等;而内生夹杂物主要是脱氧、脱硫等过程的产物,也叫一次脱氧(硫)产物,以及在冷却和凝固过程中由于某些元素(氧、硫、氮等)溶解度下降而形成的化合物(二、三次脱氧产物),当来不及排除而留在钢中时产生的。
非金属夹杂物从尺寸、大小来分可分为:显微夹杂物和宏观夹杂物。
显微夹杂物尺寸比较小,不大于50μm,一般在20μm以下,此类夹杂物均匀地分布在钢中,主要来自钢中的脱氧产物、浇注过程中的二次氧化产物。
宏观夹杂物为大型夹杂物,尺寸大于50μm,这类夹杂物颗粒大,数量少,主要是外来夹杂。
此类夹杂物在钢中呈偶然性分布,对产品质量危害最大。
根据夹杂物化学成份的不同可分为:氧化物系夹杂、硫化物系夹杂和氮化物系夹杂。
氧化物夹杂有:简单的单质氧化物,FeO、Fe2O3、Al2O3、SiO2、MnO等,在镇静钢中,用硅铁或铝脱氧时,则SiO2和Al2O3比较常见;复杂氧化物,包括尖晶石类夹杂物和各种钙的铝酸盐,FeO.Al2O3、MnO.Al2O3、MgO.Al2O3等;硅酸盐和硅酸盐玻璃,此类夹杂物组成复杂,常常是多相的。
第6讲:中高碳钢夹杂物控制
其形貌如下图所示。
(2)夹杂物的能谱特征
对外来夹杂物进行能谱分析发现,不同来源的夹杂 物具有不同的能谱特征,主要差别是保护渣卷入时,有 明显的Na峰,而炉渣和耐火材料无此峰;耐火材料带入 的夹杂物Al峰较高,这是区别与其它夹杂物的特征元素; 炉渣卷入时,保留了原始炉渣Ca峰较高的特征,但也有 明显的Al峰。外来夹杂物的能谱特征对区分钢中大型夹杂 物的来源有帮助,可以有针对性地来采取措施,进一步 降低外来夹杂物。
1 钢中夹杂物的分类及特点
夹杂物来源及分类
1.1 夹杂物的分类
钢中的夹杂物按照来源可以分为内生夹杂物和 外来夹杂物。
内生夹杂物包括在脱氧、二次氧化或钢液冷却 和凝固过程中生产的氧化物,外来夹杂物包括炉渣 卷入或耐火材料侵蚀卷入钢液。
夹杂物的来源和分类如上图所示:
1.2 内生夹杂物
内生夹杂物是脱氧产物或者是钢水冷却凝固过程中的 析出物,包括脱氧产物以及在钢水冷却和凝固过程中产生 的沉淀析出夹杂物。
连铸板坯中大型夹杂物的尺寸分布
4 夹杂物对中、高碳钢性能的影响
钢中非金属夹杂物的存在是影响钢制品性能的重要因素,有 时甚至是决定性因素。非金属夹杂物对钢性能的影响程度与夹杂 物本身的性质,更确切地说与其相对于周围金属基体性质的差异 有密切关系。这里所说的性质差异主要包括:
1)各种温度下弹性模量的差值, 2)各种温度下形变能力的差值。 其原因在于当钢基体热加工时,由于夹杂物与基体的热物性 和界面特性不同,必然影响到夹杂物与基体间的连接情况,从而 导致夹杂物周围应力集中。
连铸坯夹杂物产生原因分析及改进
连铸坯夹杂物产生原因分析及改进连铸坯夹杂物的产生原因可以从多个方面进行分析和改进。
下面是一个大致的分析和改进措施,供您参考。
1. 原料质量问题:连铸坯夹杂物主要来自于熔化的金属和废钢原料,在回炉炉中的熔化过程中,可能会夹杂一些金属碎屑、渣滓和氧化物等杂质。
2. 冶炼工艺问题:连铸坯夹杂物的产生也与冶炼过程中的工艺参数有关。
冶炼温度不稳定、浇注速度过快或过慢、浇注过程中的氧气和杂质溶解等都可能导致夹杂物的产生。
3. 连铸机设备问题:连铸机的状态和性能也可能对夹杂物产生产生影响。
结晶器内部的损坏、结晶器震动不稳定、传动系统不正常等问题都可能导致夹杂物产生。
二、改进措施1. 提高原料质量:采用优质原料,并加强原料筛查和预处理,规范原料质量的控制。
可以采用一些物理和化学方法对废钢进行预处理,如磁选、浮选、热处理等,以减少夹杂物的含量。
2. 优化冶炼工艺:通过调整冶炼工艺参数,控制冶炼温度稳定性,避免过高或过低的温度对金属液中的杂质产生不良影响。
3. 改进连铸机设备:加强设备的维护保养,及时发现和修复连铸机设备的问题,确保连铸过程的稳定性和可靠性。
可以对结晶器进行优化设计,改进震动稳定性和结晶器内部布置,以减少夹杂物的产生。
4. 强化质量控制:加强连铸工艺过程的监测和控制,通过合理的浇注速度、浇注方式和辅助工具,减少夹杂物的产生。
建立完善的质量控制体系,追踪和分析夹杂物的来源和产生规律,以便更好地进行改进和控制。
5. 加强人员培训:提高工人的操作技能,加强工艺和设备知识的培训,使其能够熟练应对连铸过程中可能出现的问题,并及时采取正确的措施进行解决。
液态金属加工中的夹杂物控制
液态金属加工中的夹杂物控制在液态金属加工中,夹杂物的控制是一项至关重要的任务。
夹杂物是液态金属中的非金属颗粒或微小气泡,它们可能在金属凝固过程中形成,对最终产品的性能产生严重影响。
因此,了解夹杂物的来源、影响以及如何有效地控制它们,对于提高产品质量和生产效率具有重要意义。
一、夹杂物的来源夹杂物的来源主要有两个途径:原材料和加工过程。
在液态金属的制备过程中,如果原材料含有杂质,这些杂质可能在熔炼或净化过程中进入液态金属。
此外,在浇铸和凝固过程中,外部的颗粒或气体也可能会进入液态金属中形成夹杂物。
二、夹杂物的影响夹杂物对液态金属加工产品的性能有严重影响。
首先,它们会降低金属的强度和硬度,因为夹杂物往往是脆性的,容易在应力作用下断裂。
其次,夹杂物可能会引起应力集中,导致产品在铸造缺陷处的开裂。
此外,夹杂物还可能影响产品的导电性和导热性,从而影响产品的使用性能。
三、夹杂物的控制方法为了控制液态金属加工中的夹杂物,我们可以采取以下措施:1. 选用纯度高的原材料:在选择原材料时,应尽量选用纯度高的金属材料,以减少夹杂物的来源。
2. 优化熔炼和净化工艺:熔炼和净化工艺对夹杂物的含量有重要影响。
通过优化这些工艺参数,可以减少新夹杂物的形成并去除一部分已形成的夹杂物。
3. 浇铸和凝固过程的控制:在浇铸和凝固过程中,应采取措施减少颗粒或气体的进入。
例如,可以使用净化剂来吸附可能进入液态金属中的气体,并采用合适的浇铸速度和温度来减少颗粒的进入。
4. 定期检查和清理设备:在生产过程中,定期检查设备和清理残留的杂质是必要的。
这有助于减少新的夹杂物的形成并去除已形成的夹杂物。
综上所述,通过采取以上措施,我们可以有效地控制液态金属加工中的夹杂物,从而提高产品质量和生产效率。
这些措施不仅有助于提高产品的性能和使用寿命,还有助于降低生产成本和提高企业的竞争力。