连铸结晶器液面自动加渣控制系统简介
连铸自动化系统介绍
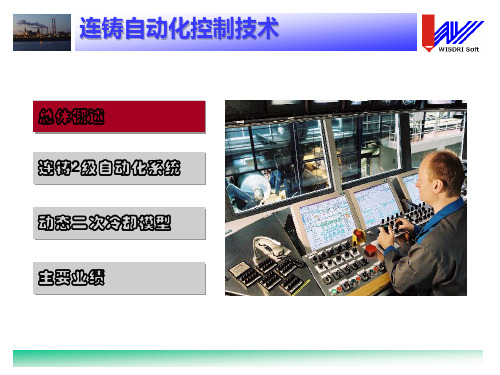
Level 3 生产控制级
Level 2 过程控制级
连铸控制模型 铸坯质量判定模型 生产状况监视 快速分析室检化验管理 数据通信
Level 1 基础自动化
Level 0 设备控制级 炼钢工艺过程
冶金自动化控制与管理技术 威仕软件助您成功
连铸自动化控制技术
总体概述 连铸2级自动化系统 动态二次冷却模型 主要业绩
冶金自动化控制与管理技术 威仕软件助您成功
连铸二次冷却技术
1 二次冷却控制的目的 为避免铸坯表面冷却不当,可采用气水雾化冷却技术, 使铸坯表面得到大面积喷射,保证整个铸坯表面冷却均匀. 而冷却强度的控制要复杂些.二次冷却水如果局部过 强,可能引起铸坯表面裂纹;过弱则会导致铸坯鼓肚而产生 内部缺陷.因此,要达到适当的冷却强度,合理控制二冷段内 的冷却水流量,是整个连铸二次冷却控制的关键.
连铸主操作室
切割操作室
威仕软件助您成功
2级连铸过程控制系统的目的
通过二次冷却控制模型,提高铸坯质量 通过切割优化和质量判定模型,提高金属收得率 延长设备寿命,降低能源消耗 简化操作,提高劳动效率 对过程数据存储、记录和处理,进一步提高生产水平
冶金自动化控制与管理技术
威仕软件助您成功
2级连铸过程控制系统的功能
Level 3 生产控制系统功能 Level 2 过程控制系统功能 冶炼过程优化
为模型计算准备和 收集相关数据: – 大/中包钢水数据 – 结晶器数据 – 二冷段数据 – 生产计划数据 – 冶炼标准数据 – 等等
数学模型,包括: – 动态冷却模型 – 切割长度优化 – 铸坯质量判定 – 浇铸速度计算
威仕软件助您成功
冶金自动化控制与管理技术
连铸二次冷却技术
连铸结晶器液面自动加渣控制系统简介

连铸结晶器液面自动加渣掌握系统简介一、概述连铸机浇筑时结晶器加保护渣是连铸生产中最重要的工作,保护渣在连铸生产中起着极为重要的作用,如防止二次氧化、润滑与吸附杂质等。
连铸工艺要求保护渣在浇铸过程中形成熔融层、烧结层与粉渣层等三层构造,以便更好的发挥作用。
少加勤加是添加保护渣的一条重要原则。
二、现场现状目前连铸机上承受的加渣方式大都还是人工方式,每个工人治理着一流或两流,需时刻观看着结晶口的状态,需要加时就用任凭的推上一堆,心情好或领导在时加的还均匀些,领导不在那就看自己的心情了,心情好负责些,心情不好那就任凭了。
况且连铸机旁的环境比较恶劣,工人的劳动强度很大,要求工人长时间的高质量的完成加渣工作也有难度。
因此人工添加保护渣受操作者因素的影响较大,很难保证添加的稳定性,简洁产生卷渣和液面波动,从而产生夹杂、振痕加深等缺陷。
针对这种状况,我公司最研发了一套连铸结晶器液面自动加渣掌握系统,可以代替工人进展自动加渣而根本无需工人干预。
三、系统简介我公司研发的连铸结晶器液面自动加渣掌握系统,包括工控机、掌握执行单元、现场掌握报警单元、加料仓、气动单元、结晶器渣液面温度检测装置、渣料喷头、料位计、专用软件组成。
料位计报警器干燥氮气元渣层温度显示控制界面连铸结晶器液面自动加渣掌握系统是一套闭环自动掌握系统,它以工控机为核心,通过专用软件来自动掌握各个组成局部自开工作,在根本参数设置完成后,由工控机来依据连铸机结晶器内渣液面的实际状况进展参数调整,无需再人工干预调整而能保证结晶器内渣液面的均匀和稳定。
系统的工作过程由工控机实时不停的读取结晶器内渣液面的外表温度,假设渣液面的外表温度超过设定的加料温度,则工控机掌握执行单元让加料仓下料,同时翻开气动单元,保护渣在下料管内被送料气体经渣料喷头均匀吹送到结晶器内,然后再测结晶器内渣液面的外表温度,假设渣液面的外表温度仍旧超过设定的加料温度,则工控机重复上面的加料过程,假设测量到结晶器内渣液面的外表温度低于设定的加料温度则停顿加料和关闭气动单元。
连铸机结晶器液位控制系统数学模型及其仿真

连铸机结晶器液位控制系统数学模型及其仿真连铸机结晶器液位控制系统是一个复杂的系统,它的性能直接影响到连铸机的生产效率,因此,对连铸机结晶器液位控制系统的研究是非常重要的。
本文首先简要介绍了连铸机结晶器液位控制系统的结构及工作原理,然后探讨了基于结构参数分析的数学模型,最后对模型进行仿真,得出了连铸机结晶器液位控制系统的数学模型及其仿真的结论。
1.连铸机结晶器液位控制系统简介连铸机结晶器液位控制系统是一种多参数控制系统,它是由连铸机结晶器、液位传感器、控制器、调节阀和电动蝶阀组成的(图1)。
图1铸机结晶器液位控制系统连铸机结晶器是一种机械设备,它将液体转化为固体,由于结晶过程的特点,液位变化会影响结晶质量,因此,需要对结晶器的液位进行控制。
液位传感器检测结晶器液位信号,控制器根据液位检测信号进行控制,调节阀和电动蝶阀调节结晶器的液位,从而实现对液位的控制。
2.数学模型为了研究连铸机结晶器液位控制系统,首先分析控制系统结构,建立系统数学模型,根据结构参数推导出如下数学模型:ttttt Vm = Kp*(|S|-S0)tttt(1)其中Kp为控制器参数,S0为液位参考值,|S|为液位测量值,Vm为控制器输出值。
3.仿真针对连铸机结晶器液位控制系统,结合数学模型,使用Matlab/Simulink环境建立了仿真模型,根据实际情况,设置参数如下:Kp=0.5,S0=2,液位变化范围为0~4。
图2铸机结晶器液位控制系统仿真模型根据仿真模型,控制器输出值Vm与液位|S|的变化曲线如图3所示:图3位及控制器输出值的变化曲线从上图可以看到,随着液位|S|的变化,控制器输出值Vm也随之变化,并且同步变化,Vm和|S|的变化幅度接近,这表明,控制器对液位的控制是有效的。
4.结论本文针对连铸机结晶器液位控制系统,根据结构参数推导出了数学模型,并且基于 Matlab/Simulink环境建立了仿真模型,仿真结果显示,控制器输出值Vm能有效地控制液位|S|,表明数学模型具有较强的可靠性和实际应用价值。
包钢炼钢厂连铸自动加渣控制系统应用

包钢炼钢厂连铸自动加渣控制系统应用摘要:本文讲述了包钢炼钢厂连铸自动加渣控制系统的开发与应用,该控制系统能实时计算出结晶器内各渣层厚度,依据目标渣厚来实时控制保护渣的加入速度。
应用效果表明,包钢炼钢厂应用该自动加渣控制系统后,结晶器内钢液面更加稳定,液渣层准确控制在8-12mm之间,浸入式水口在结晶器流场中受冲刷与侵蚀程度减轻,重轨钢坯洁净度得到提升,同时职工劳动强度也明显降低。
关键词:连铸;保护渣;自动加渣1引言在连铸过程中,保护渣被加入结晶器后,会很快的吸收高温钢水的热量,并且迅速的在钢水液面上形成液渣层,靠近液渣层的保护渣还没有达到熔化温度时,已被烧结成烧结层,在烧结层上方是粉渣层,这就是所谓的保护渣三层结构——液渣层,烧结层,粉渣层。
现代研究公认保护渣在连铸结晶器中有五大作用:绝热保温,防止氧化,润滑,改善传热和吸收夹杂物[1]。
保护渣加入过程中,如果保护渣加入过少,液渣层减少,结晶器润滑效果下降,引起粘结漏钢。
而如果保护渣加入过多,结晶器内液渣层过厚,结晶器液面渣圈严重并结团,保护渣结团会造成铸坯表面夹杂增加形成表面翻皮,夹渣及坯内夹渣等缺陷。
甚至会影响操作造成结晶过程中表面夹渣,当凝固外壳出结晶器下口时易重熔或被二冷水冲走造成夹渣漏钢。
结晶器内保护结团也会造成结晶坯壳与结晶器表面润滑不良,形成粘结漏钢[2]。
因此正确的加渣方法:保护渣要做到勤加少加,均匀铺盖。
目前国内绝大多数钢厂的结晶器保护渣加渣操作还是采用人工加渣。
人工加渣在操作上需要操作者不定时的向结晶器内推入保护渣,这样的操作容易造成结晶内钢液面的瞬间搅动,容易造成卷渣等缺陷。
由于人工加渣的效果很大程度上依靠操作者的经验,所以一般不可能产生稳定的液渣层。
人工加渣操作无法解决保护渣在储存过程中的返潮现象。
基于人工加渣的多种弊端,开发一种可以实现自动化,精确控制加渣量的结晶器自动加渣机成为必不可少的需求。
2包钢炼钢厂自动加渣原理与开发在20世纪70年代以前,各国连铸领域均采用人工方式加入保护渣。
结晶器液面自动控制系统功能的优化与创新

结晶器液面自动控制系统功能的优化与创新发布时间:2021-08-24T15:08:46.500Z 来源:《工程管理前沿》2021年4月10期作者:全嵩[导读] 连铸机结晶器钢水液面进行自动控制,是连铸生产中的关键技术之一,它对于提高铸还的质量与产量,减少溢钢和漏钢事故,提高炼钢连铸的管理水平都非常重要的。
全嵩武钢有限炼钢厂湖北武汉 430081摘要:连铸机结晶器钢水液面进行自动控制,是连铸生产中的关键技术之一,它对于提高铸还的质量与产量,减少溢钢和漏钢事故,提高炼钢连铸的管理水平都非常重要的。
在结晶器钢水液面进行自动控制中,通过一系列创新与实践过程,为了实现钢水液面波动在±5mm 以内,消除皮下夹渣。
针对液位检测失败,建立自动校准功能;针对开浇失败故障,建立并完善自动开浇功能。
合理修改程序,保证运行可靠性提升控制自动化水平。
文章就结晶器液位控制系统优化创新,提升设备性能来满足工艺生产需求,带来更好的质量、更低的成本、更高的效率。
关键词:自动控制;自动校准;自动开浇企业面临前所未有的压力,只有不断加快技术进步,优化产品结构,生产出技术含量高、高附加值的产品,才能处于不败之地。
若要增产创效,必须提高连铸浇钢的自动化控制程度。
钢水浇入结晶器内,为了防止钢水溢出,钢水液面必须保持稳定,否则在浇铸过程中,钢水液面波动太大,会卷入渣子,在铸坯表面形成皮下夹渣,影响铸坯质量。
经验表明:钢水液面波动在±5mm以内,可消除皮下夹渣。
同时,结晶器液面波动﹥±5mm,铸坯表面纵裂发生率30﹪,这就是说,钢水液面的波动,直接影响到铸坯的表面质量。
所以结晶器钢水液位的稳定性是连续铸钢生产中至关重要的问题。
我厂液位控制系统运行稳定性时有波动,多次因为液位自动控制无法投入造成生产非计划中断,或因液面波动大造成产品质量异议,必须优化创新提高稳定性。
1 结晶器液位自动控制系统故障分析为减少连铸机中断次数,保证生产的顺利进行,必须采用科学、合理的措施,提高结晶器液位自动控制系统运行稳定性。
结晶器液面自动控制
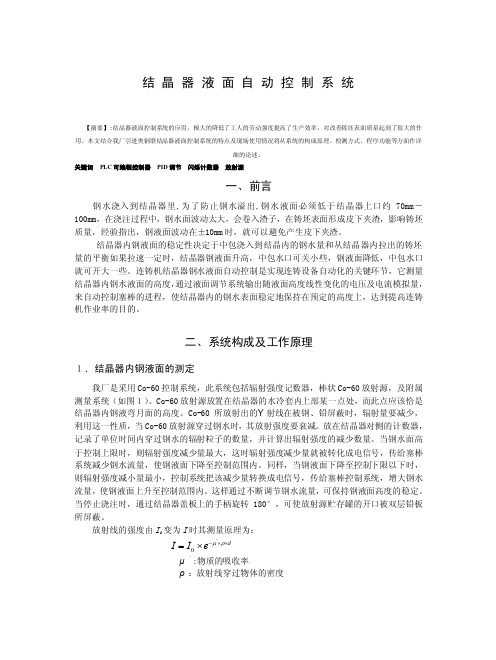
结 晶 器 液 面 自 动 控 制 系 统【摘要】:结晶器液面控制系统的应用,极大的降低了工人的劳动强度提高了生产效率,对改善铸坯表面质量起到了很大的作用。
本文结合我厂引进奥钢联结晶器液面控制系统的特点及现场使用情况将从系统的构成原理、检测方式、程序功能等方面作详细的论述。
关键词 PLC 可编程控制器 PID 调节 闪烁计数器 放射源一、前言钢水浇入到结晶器里,为了防止钢水溢出,钢水液面必须低于结晶器上口约70mm -100mm ,在浇注过程中,钢水面波动太大,会卷入渣子,在铸坯表面形成皮下夹渣,影响铸坯质量,经验指出,钢液面波动在±10mm 时,就可以避免产生皮下夹渣。
结晶器内钢液面的稳定性决定于中包浇入到结晶内的钢水量和从结晶器内拉出的铸坯量的平衡如果拉速一定时,结晶器钢液面升高,中包水口可关小些,钢液面降低,中包水口就可开大一些。
连铸机结晶器钢水液面自动控制是实现连铸设备自动化的关键环节,它测量结晶器内钢水液面的高度,通过液面调节系统输出随液面高度线性变化的电压及电流模拟量,来自动控制塞棒的进程,使结晶器内的钢水表面稳定地保持在预定的高度上,达到提高连铸机作业率的目的。
二、系统构成及工作原理1.结晶器内钢液面的测定我厂是采用Co-60控制系统,此系统包括辐射强度记数器,棒状Co-60放射源,及附属测量系统(如图1)。
Co-60放射源放置在结晶器的水冷套内上部某一点处,而此点应该恰是结晶器内钢液弯月面的高度。
Co-60所放射出的Υ射线在被钢、铅屏蔽时,辐射量要减少,利用这一性质,当Co-60放射源穿过钢水时,其放射强度要衰减。
放在结晶器对侧的计数器,记录了单位时间内穿过钢水的辐射粒子的数量,并计算出辐射强度的减少数量。
当钢水面高于控制上限时,则辐射强度减少量最大,这时辐射强度减少量就被转化成电信号,传给塞棒系统减少钢水流量,使钢液面下降至控制范围内。
同样,当钢液面下降至控制下限以下时,则辐射强度减小量最小,控制系统把该减少量转换成电信号,传给塞棒控制系统,增大钢水流量,使钢液面上升至控制范围内。
连铸机结晶器钢水液面塞棒自动控制系统介绍

1 . 2 系统基 本功 能 具有 塞 棒 控 制 和 拉 速 控 制 两 种 自动 控 制 模 式, 能通过 人 工 干 预方 式 由塞棒 控 制转 为 拉 速控 制, 或通过 人 工 干 预 方 式 由拉 速 控 制转 为 塞 棒 控 制 。转 为拉速 控 制 后 , 由钢 水 液 位 检测 仪 输 出的 模 拟量 ( 0~I O V或 4~2 0 mA可选 ) 自动控 制 拉 矫
中 车 的执 行 机 构 上 , 仪 表 电气 部 分 放 在 主控 室
内。
实现 自动 浇铸 、 系统故 障 自动关 闭 塞棒 、 防止 溢钢
或漏 钢等 功 能 , 有 力 保 证 用 户 的钢 坯 质量 。在 此 对 连铸机 结 晶器 钢水 液 面塞 棒 自动控 制 系统 进 行 详 细介绍 。
Sy s t e m I n t r o du c t i o n o f Li q ui d Le v e l Au t o ma t i c S t o pp e r Co n t r o l i n Co n t i n uo us Ca s t i ng Mo u l d
动 控制 来满 足生产 工 艺要 求 。在 保证 定 径 水 口拉
速 控制 功能 的前提 下 , 针对 不 同钢种 , 采 用 中间包 塞 棒 自动浇 注控 制功 能 。系 统利 用 放射 源 检测 系
统、 采 用高灵 敏度 的电动 缸 、 精 密 的塞棒 机 械 执行
机构 、 先进 的 控制 软 件 对 连铸 机 结 晶器 液 位 控 制 系统 实现 良好 的控制 , 控制 精度 达到 ± 2 m m 以 内。
Abs t r a c t : T he p a pe r b ie r l f y d e s c ibe r s c o mp o s i t i o n;f un c t i o n o f Au t o ma t i c c o n t r o l s y s t e m o f s t o p pe r , a n d r o d c o n t r o l pr in c i p l e i s d i s c u s s e d i n d e t a i l . Ke y W o r ds: s t o pp e r ; a u t o ma t i c c o n t r o l ; c r y s t a l l i z e r; l i q u i d l e v e l
连铸结晶器保护渣自动添加系统设计
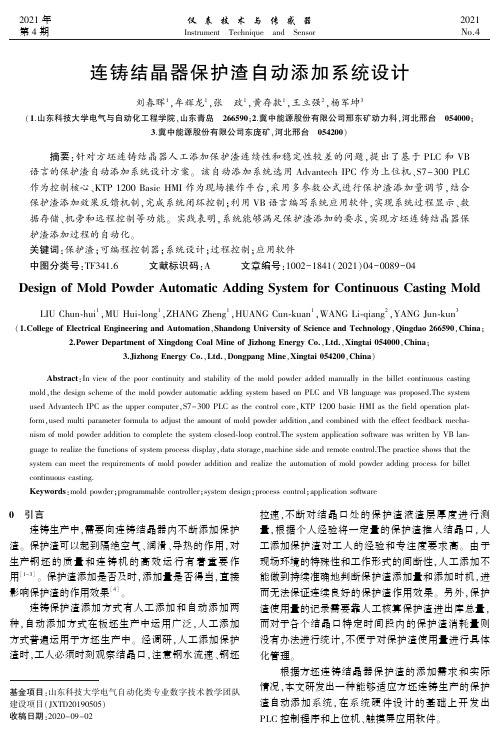
㊀2021年㊀第4期仪表技术与传感器Instrument㊀Technique㊀and㊀Sensor2021㊀No.4㊀基金项目:山东科技大学电气自动化类专业数字技术教学团队建设项目(JXTD20190505)收稿日期:2020-09-02连铸结晶器保护渣自动添加系统设计刘春晖1,牟辉龙1,张㊀政1,黄存款1,王立强2,杨军坤3(1.山东科技大学电气与自动化工程学院,山东青岛㊀266590;2.冀中能源股份有限公司邢东矿动力科,河北邢台㊀054000;3.冀中能源股份有限公司东庞矿,河北邢台㊀054200)㊀㊀摘要:针对方坯连铸结晶器人工添加保护渣连续性和稳定性较差的问题,提出了基于PLC和VB语言的保护渣自动添加系统设计方案㊂该自动添加系统选用AdvantechIPC作为上位机㊁S7-300PLC作为控制核心㊁KTP1200BasicHMI作为现场操作平台,采用多参数公式进行保护渣添加量调节,结合保护渣添加效果反馈机制,完成系统闭环控制;利用VB语言编写系统应用软件,实现系统过程显示㊁数据存储㊁机旁和远程控制等功能㊂实践表明,系统能够满足保护渣添加的要求,实现方坯连铸结晶器保护渣添加过程的自动化㊂关键词:保护渣;可编程控制器;系统设计;过程控制;应用软件中图分类号:TF341.6㊀㊀㊀文献标识码:A㊀㊀㊀文章编号:1002-1841(2021)04-0089-04DesignofMoldPowderAutomaticAddingSystemforContinuousCastingMoldLIUChun⁃hui1,MUHui⁃long1,ZHANGZheng1,HUANGCun⁃kuan1,WANGLi⁃qiang2,YANGJun⁃kun3(1.CollegeofElectricalEngineeringandAutomation,ShandongUniversityofScienceandTechnology,Qingdao266590,China;2.PowerDepartmentofXingdongCoalMineofJizhongEnergyCo.,Ltd.,Xingtai054000,China;3.JizhongEnergyCo.,Ltd.,DongpangMine,Xingtai054200,China)Abstract:Inviewofthepoorcontinuityandstabilityofthemoldpowderaddedmanuallyinthebilletcontinuouscastingmold,thedesignschemeofthemoldpowderautomaticaddingsystembasedonPLCandVBlanguagewasproposed.ThesystemusedAdvantechIPCastheuppercomputer,S7-300PLCasthecontrolcore,KTP1200basicHMIasthefieldoperationplat⁃form,usedmultiparameterformulatoadjusttheamountofmoldpowderaddition,andcombinedwiththeeffectfeedbackmecha⁃nismofmoldpowderadditiontocompletethesystemclosed⁃loopcontrol.ThesystemapplicationsoftwarewaswrittenbyVBlan⁃guagetorealizethefunctionsofsystemprocessdisplay,datastorage,machinesideandremotecontrol.Thepracticeshowsthatthesystemcanmeettherequirementsofmoldpowderadditionandrealizetheautomationofmoldpowderaddingprocessforbilletcontinuouscasting.Keywords:moldpowder;programmablecontroller;systemdesign;processcontrol;applicationsoftware0㊀引言连铸生产中,需要向连铸结晶器内不断添加保护渣㊂保护渣可以起到隔绝空气㊁润滑㊁导热的作用,对生产钢坯的质量和连铸机的高效运行有着重要作用[1-3]㊂保护渣添加是否及时,添加量是否得当,直接影响保护渣的作用效果[4]㊂连铸保护渣添加方式有人工添加和自动添加两种,自动添加方式在板坯生产中运用广泛,人工添加方式普遍运用于方坯生产中㊂经调研,人工添加保护渣时,工人必须时刻观察结晶口,注意钢水流速㊁钢坯拉速,不断对结晶口处的保护渣液渣层厚度进行测量,根据个人经验将一定量的保护渣推入结晶口,人工添加保护渣对工人的经验和专注度要求高㊂由于现场环境的特殊性和工作形式的间断性,人工添加不能做到持续准确地判断保护渣添加量和添加时机,进而无法保证连续良好的保护渣作用效果㊂另外,保护渣使用量的记录需要靠人工核算保护渣进出库总量,而对于各个结晶口特定时间段内的保护渣消耗量则没有办法进行统计,不便于对保护渣使用量进行具体化管理㊂根据方坯连铸结晶器保护渣的添加需求和实际情况,本文研发出一种能够适应方坯连铸生产的保护渣自动添加系统,在系统硬件设计的基础上开发出PLC控制程序和上位机㊁触摸屏应用软件㊂㊀㊀㊀㊀㊀90㊀InstrumentTechniqueandSensorApr.2021㊀1㊀自动添加系统总体设计1.1㊀系统功能要求方坯保护渣添加不同于板坯,方坯连铸结晶口较多,且每一结晶口对应的保护渣添加量和添加时机不同,因此对自动添加系统执行机构的独立性要求较高㊂根据方坯连铸保护渣添加作业流程,结合实践经验得出方坯连铸保护渣自动添加系统的基本要求,如下:(1)能对保护渣状态进行监测和控制;(2)能按照生产需求及时㊁准确地向各个结晶口添加保护渣;(3)能准确检测保护渣添加效果,实现保护渣添加的闭环控制;(4)能显示运行过程㊁记录历史数据㊁进行故障报警,并能实现机旁和远程控制㊂1.2㊀系统控制策略自动添加系统采用多参数加渣量公式控制保护渣添加量以适应连铸生产中对保护渣需求量的变化㊂通过采集方坯连铸生产中所有影响保护渣使用量的参数,结合专业经验和生产要求得出保护渣添加量计算公式[5],即为多参数加渣量公式,如下所示:Q=(0.74A0.3)ˑ(60f)ˑ[1/(α㊃vc)]0.5+0.17式中:Q为保护渣消耗量,kg/m3;A为结晶器振幅,mm;vc为拉速,m/min;f为结晶器振频,次/min;α为保护渣黏度,Pa㊃s㊂采用保护渣添加效果反馈机制对保护渣添加时机进行调节,可以实现保护渣自动添加系统的闭环控制㊂系统根据计算得到的结晶口保护渣液渣层厚度,根据此厚度调节下个检测周期内保护渣添加动作的时间间隔,厚度超过一定数值增大保护渣添加动作时间间隔,低于一定数值减小时间间隔,厚度在一定范围内则保持当前添加周期,一般厚度设置为2 3cm最为合适㊂1.3㊀系统组成及工作原理1.3.1㊀系统组成以6流方坯连铸生产车间使用的保护渣自动添加系统为样本,保护渣自动添加系统结构如图1所示,主要包含6个保护渣存储箱㊁6路下料管路㊁检测传感器及其驱动机构㊁现场操作箱㊁上位机和配电控制柜等部分㊂1.3.2㊀工作原理根据保护渣自动添加系统的组成结构和功能要图1㊀系统结构示意图求,本系统采用S7-300PLC实现保护渣自动添加系统的设计[6]㊂系统控制结构如图2所示㊂图2㊀系统控制结构图保护渣自动添加系统的执行机构将保护渣状态信息㊁步进电机运转情况㊁氮气压力信息发送给计算机,为系统执行保护渣添加动作做好准备㊂系统工作期间,计算机根据采集到的方坯连铸生产实时数据结合控制策略得出保护渣添加量和添加时间间隔,经PLC将保护渣添加量转化为电机转动角度,将添加时间间隔转化为电磁阀开通时间㊂存储箱内的保护渣在下料轴的带动下旋入下料管道,然后电磁阀开通压缩氮气将保护渣吹入结晶口,完成1次保护渣添加动作,每10个上述保护渣添加动作为1个检测周期,1个检测周期结束后,系统检测机构工作1次,对保护渣液渣层厚度进行测量,调节下一个检测周期内保护渣添加时间间隔㊂保护渣添加量根据方坯连铸实时生产情况及时调节,添加时间间隔根据检测机构反馈信息每1个检测周期调节1次㊂2㊀自动添加系统硬件设计硬件系统主要包括控制机构㊁检测机构和执行机构3部分㊂控制机构主要包括PLC㊁步进电机控制器㊁上位机和现场操作箱等㊂检测机构主要包括检测传感器和传感器驱动机构㊂执行机构主要包括保护渣㊀㊀㊀㊀㊀第4期刘春晖等:连铸结晶器保护渣自动添加系统设计91㊀㊀存储箱㊁下料管路㊁喷嘴和氮气管路等,其中保护渣存储箱包含保护渣料仓㊁加热板㊁步进电机和氮气电磁阀㊂2.1㊀检测传感器选型检测机构负责对每一结晶口的液位信息进行测量,方坯连铸结晶口处液位变化幅度不大,但因钢水的持续流入液位波动较为频繁,在保证精度的前提下选择能够持续测量的液位传感器;结晶口处温度极高,应选用非接触式测量传感器;结晶器平台空间有限,还要注意传感器尺寸[7]㊂综合考虑,检测传感器选用HZH-DDJ-S型激光液位仪,该传感器采用一体化设计,体积小,工作环境温度可达70ħ,能够适应结晶器平台的工作环境,通过RS485串口通信,测量范围0.05 40m,满足系统通讯和精度要求㊂2.2㊀控制系统设计系统硬件采用模块化设计,每个结晶口对应的执行机构相互独立,根据系统结构和控制策略进行S7-300PLC的I/O口地址分配[8-10]㊂具体分配情况如表1所示㊂分配好I/O口地址后对系统控制配电柜进行装配,控制配电柜实物如图3所示㊂表1㊀PLCI/O口分配输入地址注释输出地址注释I0.0操作箱开关Q0.01号氮气阀I0.11号保护渣位置Q0.12号氮气阀I0.22号保护渣位置Q0.23号氮气阀I0.33号保护渣位置Q0.34号氮气阀I0.44号保护渣位置Q0.45号氮气阀I0.55号保护渣位置Q0.56号氮气阀I0.66号保护渣位置Q1.01号加热板AI0.0氮气压力Q1.12号加热板AI0.11号保护渣温度Q1.23号加热板AI0.22号保护渣温度Q1.34号加热板AI0.33号保护渣温度Q1.45号加热板AI0.44号保护渣温度Q1.56号加热板AI0.55号保护渣温度Q2.01号电机AI0.66号保护渣温度Q2.12号电机Q2.23号电机Q2.34号电机Q2.45号电机Q2.56号电机Q3.0现场报警指示Q3.1检测器驱动机构Q3.2检测传感器图3㊀控制配电柜3㊀自动添加系统控制程序和软件设计3.1㊀控制程序设计鉴于连铸生产车间生产情况的不确定性,系统控制程序分为人工控制和自动控制两种,系统启动后默认为自动控制方式㊂自动控制状态下,系统根据生产情况进行保护渣添加动作调节,点击现场操作箱上的控制模式切换按键转换到手动控制,手动控制时工人视生产情况调节保护渣添加参数,系统根据设置的参数进行保护渣添加动作㊂系统主控制流程图如图4所示㊂图4㊀系统主控制流程图3.2㊀应用软件设计系统应用软件分为上位机应用软件和现场操作箱应用软件,采用VB语言编写㊂上位机选用㊀㊀㊀㊀㊀92㊀InstrumentTechniqueandSensorApr.2021㊀AdvantechIPC,现场操作箱选用KTP1200BasicHMI作为显示操作平台,结合专用软件,提供可视化的管理平台和操作平台㊂上位机应用软件包含主界面㊁记录界面㊁设置界面㊁修改密码㊁退出系统等主要操作选项,上位机应用软件结构如图5所示,实现动作过程显示㊁历史数据记录㊁报表生成㊁系统远程控制功能,软件主界面如图6所示㊂图5㊀上位机软件结构图图6㊀上位机软件主界面现场操作箱应用软件界面主要包含过程显示界面㊁控制模式切换㊁手动设置界面等,实现添加过程显示㊁系统控制模式选择㊁简单故障报警等功能,软件主界面如图7所示㊂4㊀结束语本文分析了方坯连铸生产中人工添加保护渣存在的不足,在大量实地调研的基础上设计出一种保护渣自动添加系统㊂分别对系统的硬件结构㊁控制策略㊁上位机和操作箱应用软件进行了介绍㊂系统硬件和软件设计都充分考虑现场实际应用情况,独立模块化的硬件设计和便捷可视化的软件设计提高了系统的适用性㊁操作性㊂该系统已在方坯连铸车间实际应用,实践结果表明,系统能够较为准确地实现保护渣添加动作控制,提高了连铸生产效率,减少了保护渣使用量,减轻了工人劳动负担,改善工人工作图7㊀HMI主界面环境㊂参考文献:[1]㊀汪国才,李浩,陶承岗,等.连铸圆坯表面纵裂原因及控制措施[J].炼钢,2020,36(2):53-58.[2]㊀朱苗勇.新一代高效连铸技术发展思考[J].钢铁,2019,54(8):21-36.[3]㊀王亚军.连铸主要机械设备功能精度控制[D].乌鲁木齐:新疆农业大学,2016.[4]㊀赵晓萍,王兵,张士宪.电磁场作用下连铸保护渣物化性能研究进展[J].炼钢,2019,35(4):53-58.[5]㊀谢长川,李富帅,钱亮,等.高拉速小方坯铸机关键技术的研发及应用[J].炼钢,2020,36(2):59-62.[6]㊀孙伟城,李磊.基于PLC与触摸屏的纸浆设备除尘系统设计[J].控制工程,2015,22(S1):106-109.[7]㊀魏鹏,李醒飞,杨少波,等.嵌入式数据采集压缩系统的设计[J].仪表技术与传感器,2020(7):122-126.[8]㊀田志勇,裘信国.基于PLC与RFID的物流自动分拣系统设计[J].现代制造工程,2020(3):157-160.[9]㊀赵建平,党博,胡军,等.基于FPGA的出砂信号同步采集与存储系统设计[J].仪表技术与传感器,2020(7):86-89.[10]㊀秦岩,代伟,杨杰,等.基于软PLC技术的磨矿过程运行控制系统及实验[J].东北大学学报(自然科学版),2015,36(3):309-313.作者简介:刘春晖(1979 ),硕士研究生,副教授,主要从事测试计量技术㊁智能仪器仪表及安全生产监测监控等方面的教学㊁科研和实践工作㊂E⁃mail:Liuch@sdust.edu.cn牟辉龙(1995 ),硕士研究生,主要从事仪器仪表的研究工作㊂E⁃mail:mhl15092693998@163.com。
- 1、下载文档前请自行甄别文档内容的完整性,平台不提供额外的编辑、内容补充、找答案等附加服务。
- 2、"仅部分预览"的文档,不可在线预览部分如存在完整性等问题,可反馈申请退款(可完整预览的文档不适用该条件!)。
- 3、如文档侵犯您的权益,请联系客服反馈,我们会尽快为您处理(人工客服工作时间:9:00-18:30)。
连铸结晶器液面自动加渣控制系统简介
一、概述
连铸机浇筑时结晶器加保护渣是连铸生产中最重要的工作,保护渣在连铸生产中起着极为重要的作用,如防止二次氧化、润滑及吸附杂质等。
连铸工艺要求保护渣在浇铸过程中形成熔融层、烧结层及粉渣层等三层结构,以便更好的发挥作用。
少加勤加是添加保护渣的一条重要原则。
二、现场现状
目前连铸机上采用的加渣方式大都还是人工方式,每个工人管理着一流或两流,需时刻观察着结晶口的状态,需要加时就用随便的推上一堆,心情好或领导在时加的还均匀些,领导不在那就看自己的心情了,心情好负责些,心情不好那就随便了。
况且连铸机旁的环境比较恶劣,工人的劳动强度很大,要求工人长时间的高质量的完成加渣工作也有难度。
因此人工添加保护渣受操作者因素的影响较大,很难保证添加的稳定性,容易产生卷渣和液面波动,从而产生夹杂、振痕加深等缺陷。
针对这种情况,我公司最新研发了一套连铸结晶器液面自动加渣控制系统,可以代替工人进行自动加渣而基本无需工人干预。
三、系统简介
我公司新研发的连铸结晶器液面自动加渣控制系统,包括工控机、控制执行单元、现场控制报警单元、加料仓、气动单元、结晶器渣液面温度检测装置、渣料喷头、料位计、专用软件组成。
连铸结晶器液面自动加渣控制系统是一套闭环自动控制系统,它以工控机为核心,通过专用软件来自动控制各个组成部分自动工作,在基本参数设置完成后,由工控机来根据连铸机结晶器内渣液面的实际情况进行参数调整,无需再人工干预调整而能保证结晶器内渣液面的均匀和稳定。
系统的工作过程由工控机实时不停的读取结晶器内渣液面的表面温度,如果渣液面的表面温度超过设定的加料温度,则工控机控制执行单元让加料仓下料,同时打开气动单元,保护渣在下料管内被送料气体经渣料喷头均匀吹送到结晶器内,然后再测结晶器内渣液面的表面温度,如果渣液面的表面温度仍然超过设定的加料温度,则工控机重复上面的加料过程,如果测量到结晶器内渣液面的表面温度低于设定的加料温度则停止加料和关闭气动单元。
在现场设有工人控制箱,可以控制任意一流加料系统的启动和停止。
当出现故障时控制箱会发出声光报警,并指示灯提示哪一流出现问题。
系统实现框图如下:
图1系统框图
图2现场控制箱图
图3现场储料机构箱
四、系统界面
五、系统功能
1)自动均匀可靠地添加保护渣,设定完成后,工作过程无需人工
干预调整;
2)可以通过设定控制保护渣表面温度上下限来调整添加保护渣
的厚度;
3)工人可以在现场通过报警控制单元来停止和启动加料系统;
4)保护渣加入既可以采用温度反馈方式也可以采用时间周期方
式;
5)具有加料仓料位不足时声光报警功能和杂物过滤功能;
6)具有加渣故障声光报警功能并记录保存;
7)具有下料数据统计和存储功能;
8)具有微机画面全程监控功能和加渣曲线和时间记录保存功能。
济南市电子技术研究所。