浅析连铸结晶器保护渣渣圈
对连铸结晶器保护渣渣层的分析
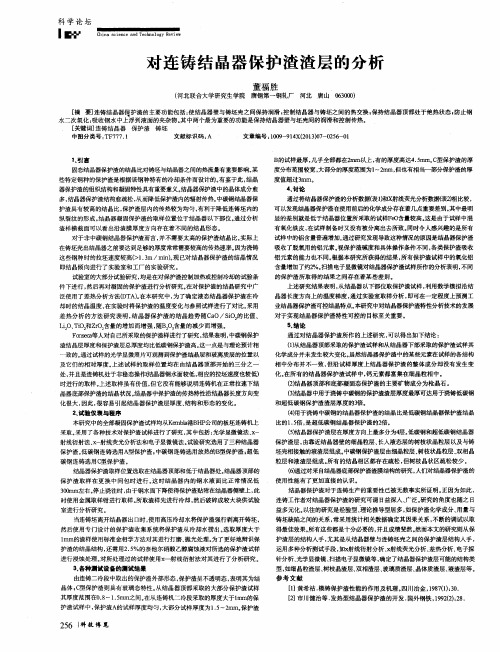
1 , 引言
B 的试样 最厚 , 几乎 全部都 :  ̄2 mm以上 , 有 的厚度 高达4 . 5 m m。 C 型保 护 渣的厚 度分布范 围较宽 , 大部分 的厚度范 围为1 -2 m m, 但也有相 当一部 分保护渣 的厚
度值超 过3 mm。 4 讨 论
固态 结晶器保 护渣 的结 晶 比对铸 坯与结 晶器 之间 的热 流量有 重要影响 。 某
渣结 晶层厚度 和保护渣 层总厚度 均 比低碳 钢保护渣 高。 这 一点是 与理论预计 相
一
致 的。 通过 试样 的光 学显微 照片可观 测到保 护渣结晶层 和玻离质 层的位置 以
及它 们 的相对 厚 度。 上述 试样 的取样 位置 均在 由结 晶器 顶部 开始 的三 分之 一
相 中分 布 并不一 致 , 但 沿试样 厚 度上结 晶器 保护 渣 的整体 成分 却没 有 发生变
科 学 论 坛
I ■
C h i n a s c i e n c e a n d T e c h n o l o g y R e v i e w
对连 铸 结 晶器 保护 渣渣 层 的分 析
董福 胜
( 河 北 联合 大学 研 究生学 院 唐 钢 第一 钢轧 厂 河北 唐山 0 6 3 0 0 0 )
些特 定钢 种的保 护渣是 根据 该钢种 特有 的冷却条 件而 设计 的。 有 鉴于 此 , 结 晶
器保 护渣 的组 织结构 和凝固特J 生具有重要 意义 。 } 结晶器保 护渣 中的晶体成分 愈
多, 结晶器 保护渣结 构愈疏 松 , 从 而降低保 护渣 内的辐射传 热。 中碳 钢结 晶器 保 护渣 具有 较高 的结 晶比 , 保护渣 层 内的传热 较为均 匀 , 有利于 降低 连铸坯 内的 纵 裂纹 的形成 。 结 晶器凝 固保护 渣 的取 样位 置位于 结 晶器以下 部位 。 通过 分析 渣 样横截 面 可 以看 出沿 渣膜 厚度方 向存 在着 不 同的结 晶形态 。
连铸结晶器保护渣渣圈的研究X

连铸结晶器保护渣渣圈的研究X吴杰,刘振清(武汉钢铁集团公司技术中心,湖北武汉430080)关键词:连铸;保护渣;渣圈中图分类号:TF111117+3 文献标识码:A摘要:对连铸过程中结晶器保护渣渣圈长大的机理进行了分析探讨,并提出了相应的防范措施1ResearchonfluxrimofmoldfluxesKeywords:continuouscasting(CC);moldflux;fluxrimAbstract:TheformationmechanismoffluxrimduringCCisdescribed,somecountermeasuresareintrodu cedtoo.由于具有高的生产效率!质量和低的成本!能耗,连铸在国际上已经获得了广泛的重视1近几年来,连铸在我国也得到了迅速的发展,新建投产了一大批连铸机,连铸比逐年提高,发展连铸已成为我国发展钢铁工业的一项重要技术政策1结晶器保护渣的采用是连铸得以迅速推广的重要保障,其性能直接关系到连铸坯的表面质量和内部质量1通常,结晶器钢水液面上的保护渣熔渣层与水冷结晶器壁接触,受冷凝固并粘附在器壁上,沿结晶器四周形成所谓的/渣圈0,俗称/渣条0!/渣皮0,见图11该渣圈在正常情况下一般较薄且脆,不会影响浇铸的顺利进行,然而一旦由于某些特殊原因造成渣圈长大,在结晶器振动的负滑脱期,渣圈有可能堵塞熔渣流入坯壳与结晶壁间的通道(见图2)[1],降低了保护渣渣膜的润滑和传热效果,而且铸坯容易发生纵裂,甚至会引起漏钢事故1长期以来,结晶器保护渣渣圈长大(即通常说的/结渣圈0)是连铸生产中较常见且令人头疼的问题,如果频繁出现结渣圈现象,操作工人需不断挑渣圈,增加了他们的劳动强度,并且这一行为严重影响铸坯的表面质量1由于钢水连铸过程中情况复杂,存在许多不确定因素,影响/结渣圈0的因素很多,有时可能是多个因素综合作用的结果,需要对具体情况具体分析1要求在保护渣的实际研究过程中,对比分析保护渣在实验条件下的性能和现场使用过程中的经验,全面掌握连铸工艺参数!保护渣各理化指标及原材料矿相结构与保护渣结渣圈的关系,结合具体的工艺条件,选择合适的化学成分和矿相组成1图1 结晶器保护渣渣圈示意图Fig.1 Schematicrepresentationoffluxriminthemold图2 渣圈影响熔渣流动状况示意图Fig.2 Effectoffluxrimonflowingoffluxlayer11结晶器;21渣圈;31熔渣层;41钢水;51坯壳1 保护渣结渣圈的原因1.1 结晶器钢水液面波动当结晶器内的钢水液面上下波动时,尤其在换中包!换水口,改变拉速等情形下,保护渣熔渣层随之波动,在结晶器铜板上/涂抹0并粘附着,如果钢液面波动频繁,结晶器壁上粘附的熔渣将越结越厚,最终形成渣圈11.2 保护渣熔化性能不好在保护渣的实际生产中,制渣原材料不一定完全是预熔料,而是在预熔料占绝大比例的前提下,配入少量助熔剂和含SiO2的原料调熔点和碱度1一旦原材料粒度和混匀程度不理想,就会造成保护渣熔化时出现局部分熔,低熔点物质先熔,高熔点物质后熔,有些高熔点物质的熔点甚至远高于钢水温度,如果它们粘附在结晶器壁上,就不容易二次熔化,只会越长越大11.3 保护渣低熔点物质过多保护渣开始烧结温度越低,收缩率越大,因烧结引起的渣圈生成!长大越明显[2]1氟化物!碱金属系碳酸盐原料在低温有收缩行为,而且,CaF2,Na2O等表面活性物质易在熔渣表面吸附,致使熔渣与器壁难于分离[3]11.4 保护渣中玻璃质原料过多由于玻璃质原料没有固定的熔点,熔化温度较低,具有低温烧结特性,增大保护渣分熔倾向,容易结渣圈11.5 保护渣结晶温度过高结晶温度过高,则保护渣的结晶倾向大,熔渣的G2T曲线变陡,属短渣,浇铸温度稍有波动,就会结渣圈11.6 保护渣绝热保温性能不好一旦粉渣层厚度不足,保护渣绝热效果不良,紧挨结晶器壁的熔渣层会更容易受冷凝结在器壁上11.7 保护渣中含有氧化剂保护渣中过高的氧化物如Fe2O3,MnO等,会增加熔渣的氧化性及其向钢水的传氧速度,当钢2渣界面发生较强的传质活动时,界面容易发生扰动[4],保护渣熔渣层随之波动,促进了渣圈长大1 1.8 连铸工艺的影响当浇铸高铝钢!不锈钢!稀土钢等合金钢种时,一些高熔点氧化物如Al2O3,TiO2,Cr2O3, RExOy等会进入熔渣,造成熔渣结晶温度和表面张力升高,使熔渣与器壁间粘附功增大,导致二者难于分离,熔渣则容易粘附在器壁上;当钢水浇铸温度!拉坯速度较低时,弯月面处的熔渣也易于凝固形成渣圈;而当拉速过高时,会造成保护渣绝热效果不良,同样结渣圈.2 防范保护渣结渣圈的措施2.1 抑制结晶器内钢水液面的波动提高连铸操作水平,采用钢水液面自动控制和电磁闸等措施抑制液面波动,可以降低结渣圈的程度.2.2 改善保护渣熔化性能改进制渣工艺,用适当的温度预加热处理保护渣基料,对控制低温烧结反应是有效的,这样可使低熔点物质形成热稳定性的新相[2].2.3 合理选择保护渣化学成分保护渣结渣圈受保护渣和铸坯表面之间的可润湿性及粘附性的影响,选择合适的保护渣成分可降低其与铸坯表面间的润湿性及粘附性1保护渣配方中,减少Na2O,CaF的用量,改加B2O3和MgO,BaO助熔,尽量减少保护渣中氧化剂的含量,不仅可避免保护渣粘器壁,还可降低结晶率[5,6]1由于高碱度保护渣表现为短渣,降低碱度可提高保护渣的玻璃特性.通过改变渣形(如空心颗粒渣),增加原始渣的碳含量及合理选择碳质材料种类,可以改善保护渣的绝热保温性能12.4 合理搭配保护渣原材料保护渣原料选择和组合模式,在一定意义上讲,比合理的成分组成更重要,这是因为即使在相同成分条件下,由于原料种类不同,其熔融特性差别很大.减少保护渣中玻璃质原料的用量,有利于控制保护渣的低温烧结特性.2.5 增强保护渣的适应性增加保护渣中MgO,BaO含量可降低渣的熔点,能使保护渣在较宽的温度范围内粘度和熔点变化平稳,也就是说,使保护渣对连铸工艺变化的适应性增强13 结束语(1)结晶器保护渣/结渣圈0是连铸生产中较常见的问题,它严重影响铸坯的表面质量和连铸工艺的顺行.(2)影响保护渣/结渣圈0的因素很多,主要有:结晶器钢水液面波动;保护渣熔化性能不好;保护渣开始烧结温度低,收缩率大;保护渣结晶温度过高;保护渣绝热保温性能不好;保护渣中含有氧化剂;连铸工艺变化等等1(3)通过抑制结晶器内钢水液面的波动;改善保护渣熔化性能;合理搭配保护渣原材料;增强保护渣的适应性等措施,可以防范保护渣结渣圈.。
连铸工艺、设备--07连铸保护渣及覆盖剂分析

三.保护渣的理化性能
1.熔化特性
A.熔化温度
保护渣是由多组元组成的混合物,没有固 定的熔点,熔化过程有一定的温度范围; 通常将熔渣具有一定流动性时的温度称为 熔点。保护渣的液渣形成渣膜其润滑作用, 因此保护渣的熔化温度应低于结晶器出口 处的铸坯表面温度,通常在1050~1100℃左 右。保护渣的熔化温度主要决定于渣子的 化学成分及渣料的粒度。
四.原料加工及成品
原料应按工艺要求各自经过研磨加工成细 粉状,要求彼此之间粒度应相近。
§7—3 保护渣的选用对策
一.保护渣对铸坯质量的重要性 1.粘结性漏钢
由于保护渣的熔化温度偏高或熔化速度偏低,致 使液渣层过薄或厚薄不均造成的。 2.表面纵向热裂纹 该缺陷发生在结晶器内,是由于结晶器内生成的坯 壳厚度不均匀,张应力集中在某一薄弱部位的情 况下发生的。在设备条件和操作因素不变的条件 下,保护渣熔化特性选用不当,液渣层厚薄不一, 造成渣膜厚度不均,使局部坯壳变薄产生纵裂。 纵裂产生与熔渣粘度(η)和拉坯速度(v)有关, 对连铸板坯, η·v值应控制在0.25~ 0.35Pa·s·m∕min,对小方坯连铸应控制在 η·v值为0.5 Pa·s·m∕min。
二.原料的选择及组合
原则:
原料的化学成分应尽可能稳定,尽可能接 近选择的保护渣的化学成分;基本原料的 种类不宜过多,以配制工序过于复杂,便 于调整渣子性能;原料来源广泛且价格便 宜。
常用的原料有天然矿物(如硅灰石、珍珠 岩、石灰石、石英等),工业原料(水泥、 水泥熟料等),工业废料(玻璃、烟道灰、 高炉渣、电炉白渣、石墨尾矿等)。
2.超低碳钢用保护渣
浇注超低碳钢种(C≤0.03%)时,确有铸坯 增碳的问题。首先应选配易氧化的活性碳质 材料,并控制其配碳量,使液渣层厚度接近 上限,并避免富碳层出现或富碳层含碳量显 著降低。其次,可以在保护渣中配入适量的 MnO2,用它作氧化剂,可有效地抑制富碳层并 降低其中含碳量,还可起助熔剂作用,使熔 渣层增厚。再次,也可在保护渣中配入BN粒 子,用以取代碳粒子。
结晶器保护渣

渣圈
7 . 保 护 渣 的 性 能 评 价
在结晶器壁四周钢液面上形成渣圈, 渣圈发达,说明保护渣的熔化性能不良, 烧结层过分发展。
Cr、Ti的影响
6
. 保 护 渣 的 选 择 和 使 用 不锈钢中含有Cr、Ti等元素,因此,保护渣必须具 备净化结晶器内钢渣界面上的Cr2O3、TiO2等夹杂物的 能力,并且吸收夹杂物后其性能稳定。 Cr2O3不仅使熔渣的粘度显著升高,还会使析晶温 度升高,破坏渣的玻璃态,析出硅灰石(CaO·SiO2) 和铬酸钙(CaCrO4)等高熔点结晶。为消除Cr2O3的不 利影响,可往保护渣中配入适量的B2O3从而使溶渣的 粘度降低,并使凝渣恢复玻璃态,不再析晶。 含Ti 不锈钢产生的(TiN)和(TiC·TiN)夹杂物, 现行保护渣对它们是无能为力的,当前只有降低钢中N 含量和采用有效的保护浇注办法来减轻TiN 的生成。
304、150mm×1600mm、0.6~0.8m/min
粘结性漏钢
5 . 保 护 渣 对 铸 坯 质 量 的 影 响 生产实践表明,由于保护渣不良引起的粘结是 板坯连铸漏钢的主要原因,由于保护渣的熔化温度 偏高或熔化速度偏低,致使液渣层过薄或厚薄不均 造成的。
表面纵向裂纹
5 . 保 护 渣 对 铸 坯 质 量 的 影 响 该缺陷发生在结晶器内,是由于在结晶器内 生成的坯壳厚度不均匀,张应力集中在某一薄弱部 位的情况下发生的。在设备条件和操作因素不变的 条件下,保护渣熔化特性选用不当,液渣层厚薄不 一,造成渣膜厚度不均,使局部坯壳变薄产生纵裂。 纵裂产生与熔渣粘度(η)和拉坯速度(v)有关, 对连铸板坯,ηv值应控制在0.20~0.35P·m/min。
含氟量的选择:
6
. 保 护 渣 的 选 择 和 使 用 连铸结晶器保护渣中一般是依赖氟化物来调 节熔点、黏度。 a、浇注过程中保护渣中的氟化物大约有20%~30%溶 入二冷水中,造成水污染,如果循环使用会腐 蚀铸机,降低铸机寿命。 b、污染环境,对人体有害; c、F-是侵蚀浸入式水口的主要成分。 一般来说F-含量要控制在10%以下,不得 大于15%,如果是采用低氟或者无氟保护渣, 二冷水的成本可节约90%,而且由于减轻了铸 机的腐蚀,使得设备维修成本降低,喷嘴寿命 延长。
渣圈形成的机理和预防措施

保护渣渣圈形成的机理:结晶器钢水液面波动。
当液面上升时,液渣层也上升并贴在裸露的结晶器铜壁上,过大的液渣层厚度会造成液面波动,增加渣圈的形成。
一般液渣层厚度为10MM左右。
保护渣熔化性能不好。
原材料粒度和混匀程度不理想,就会造成保护渣熔化时出现局部分熔,低熔点的物质先熔,高熔点的物质后熔,如果它们粘附在结晶器壁上,就不可能二次熔化,只会越长越大。
保护渣低熔点物质过多。
保护渣开始浇铸温度越低,收缩越大,因烧结形成的渣圈生长越明显。
氟化物、碱金属碳酸盐原料在低温有收缩行为。
而且氟化钙、氧化钠等表面活性物质多时,易在熔渣表面吸附致使熔渣与器壁难于分离。
保护渣中玻璃质原料过多。
玻璃质原料没有固定的熔点,开始熔化温度较低,具有低温烧结特性,增大保护渣的分熔倾向,容易结渣圈。
保护渣析晶温度过高。
析晶温度过高,则保护渣的结晶倾向大,保护渣的粘温曲线变陡,接近短渣类型,浇铸温度稍有波动,就会结渣圈。
保护渣绝热保温性能不好。
弯月面区域覆盖的保护渣中碳含量少于要求值,一旦粉渣层厚度不足,保护渣的保温效果不良,紧挨结晶器壁的液渣层会更容易受冷凝结在器壁上。
保护渣中含有氧化剂。
保护渣中不稳定的氧化物如三氧化二铁、氧化锰等过高,会增加熔渣的氧化性及其向钢水的传氧速度。
当钢—渣界面发生较强的传质活动时,界面发生扰动,保护渣液渣层随之波动,促进渣圈长大。
保护渣碱度高。
其原因是因为此类渣受冷后难出现玻璃体,渣的液相线和固相线温度区间窄,一受冷容易凝固结壳。
保护渣配碳量和配碳种类。
长期探索知:石墨渣容易形成渣圈,而碳黑有助于渣圈的消除。
连铸工艺的影响。
当浇铸高铝钢、不锈钢、稀土钢等合金钢时一些高熔点的氧化物会进入渣相,造成熔渣析晶温度升高以及表面张力升高,使熔渣于器壁间的粘附能力增大二者难于分离,当钢水温度、拉速低时,弯月面处的熔渣也易于凝固形成渣圈。
防范保护渣结渣圈的措施抑制结晶器内钢水面的波动。
提高操作水平,采用液面自动控制和电磁搅拌技术可降低结渣圈的程度。
板坯连铸结晶器保护渣卷渣及其影响因素的研究
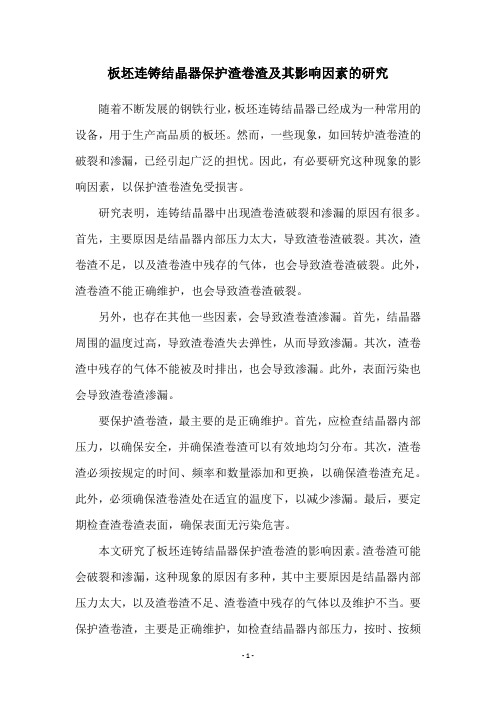
板坯连铸结晶器保护渣卷渣及其影响因素的研究随着不断发展的钢铁行业,板坯连铸结晶器已经成为一种常用的设备,用于生产高品质的板坯。
然而,一些现象,如回转炉渣卷渣的破裂和渗漏,已经引起广泛的担忧。
因此,有必要研究这种现象的影响因素,以保护渣卷渣免受损害。
研究表明,连铸结晶器中出现渣卷渣破裂和渗漏的原因有很多。
首先,主要原因是结晶器内部压力太大,导致渣卷渣破裂。
其次,渣卷渣不足,以及渣卷渣中残存的气体,也会导致渣卷渣破裂。
此外,渣卷渣不能正确维护,也会导致渣卷渣破裂。
另外,也存在其他一些因素,会导致渣卷渣渗漏。
首先,结晶器周围的温度过高,导致渣卷渣失去弹性,从而导致渗漏。
其次,渣卷渣中残存的气体不能被及时排出,也会导致渗漏。
此外,表面污染也会导致渣卷渣渗漏。
要保护渣卷渣,最主要的是正确维护。
首先,应检查结晶器内部压力,以确保安全,并确保渣卷渣可以有效地均匀分布。
其次,渣卷渣必须按规定的时间、频率和数量添加和更换,以确保渣卷渣充足。
此外,必须确保渣卷渣处在适宜的温度下,以减少渗漏。
最后,要定期检查渣卷渣表面,确保表面无污染危害。
本文研究了板坯连铸结晶器保护渣卷渣的影响因素。
渣卷渣可能会破裂和渗漏,这种现象的原因有多种,其中主要原因是结晶器内部压力太大,以及渣卷渣不足、渣卷渣中残存的气体以及维护不当。
要保护渣卷渣,主要是正确维护,如检查结晶器内部压力,按时、按频率、按数量添加和更换渣卷渣,保持温度适宜,以及定期检查渣卷渣表面,以防止渣卷渣受损害。
以上就是关于《板坯连铸结晶器保护渣卷渣及其影响因素的研究》的3000字文章。
连铸结晶器保护渣渣层结构研究报告
连铸结晶器保护渣渣层结构研究1 引言连铸结晶器保护渣的主要功能包括:使结晶器壁与铸坯壳之间保持润滑;控制结晶器与铸坯之间的热交换;保持结晶器顶部处于绝热状态;防止钢水二次氧化;吸收钢水中上浮到液面的夹杂物。
其中两个最为重要的功能是保持结晶器壁与坯壳间的润滑和控制传热。
固态结晶器保护渣的结晶比对铸坯与结晶器之间的热流量有重要影响。
某些特定钢种的保护渣是根据该钢种特有的冷却条件而设计的。
有鉴于此,结晶器保护渣的组织结构和凝固特性具有重要意义。
结晶器保护渣中的晶体成分愈多,结晶器保护渣结构愈疏松,从而降低保护渣内的辐射传热。
中碳钢结晶器保护渣具有较高的结晶比,保护渣层内的传热较为均匀,有利于降低连铸坯内的纵裂纹的形成。
结晶器凝固保护渣的取样位置位于结晶器以下部位。
为了便于比较,分别采取了用于浇铸中碳钢、低碳钢以及超低碳钢的结晶器保护渣样。
对所有渣样所作的成分分析表明:结晶器上部的渣样与粉状结晶器保护渣的成分相差无几。
x射线衍射分析和显微分析表明:位于结晶器底部的用于浇铸中碳钢的结晶器保护渣其结晶体组织占80%~90%,而低碳钢和超低碳钢用结晶器保护渣晶体分别约为65%和45%。
x射线衍射相分析表明各种保护渣的结晶相几乎全部是由矿物相枪晶石(3CaO.2SiO2.CaF2>组成。
对保护渣所作的扫描式电子显微镜分析证实中碳钢用结晶器保护渣可能还含有一定数量的霞石成分。
通过分析渣样横截面可以看出沿渣膜厚度方向存在着不同的结晶形态。
在低碳钢和超低碳钢结晶器保护渣中存在着细晶区、枝晶区和非晶区;中碳钢的非晶区相对较小,晶状区占有较大优势。
对于非中碳钢结晶器保护渣而言,并不需要太高的保护渣结晶比。
实际上在铸坯壳出结晶器之前要达到足够的厚度常常需要较高的传热速率。
因为浇铸这些钢种时的拉坯速度较高(>1.3m/min>。
现已对结晶器保护渣的结晶情况即结晶倾向进行了实验室和工厂的实验研究。
实验室的大部分实验研究,均是在对保护渣控制加热或控制冷却的实验条件下进行,然后再对凝固的保护渣进行分析研究。
连铸结晶器保护渣
连铸技术
炭质材料对熔化速度的影响规律是:炭量越多, 炭的粒度越小和比表面积越大,则降低熔化速 度的作用越强烈。常用的炭质材料降低熔化速 度的顺序是:碳黑>高炭石墨> 土状石墨。。
27
3.3 保护渣粘性特征
连铸技术
保护渣粘度是控制结晶器与铸坯之传热和润滑的 重要参数。粘度过大,熔化的保护渣不易渗入 结晶器和铸坯之间的缝隙内,铸坯的润滑条件 恶化,导致坯壳不易从结晶器内拉出,甚至造 成粘性漏钢事故。粘度过低,熔化的保护渣大 量流入结晶器和铸坯之间,铸坯润滑和传热不 均,导致表面裂纹产生,产生废品。
19
连铸技术
20
硅氧离子团结构图
连铸技术
21
氧化物对保护渣熔体网络的作用
连铸技术
22
3 连铸保护渣的物理和化学性质
连铸技术
连铸过程对保护渣的物理及化学性质有一定的要 求。保护渣的熔化温度、粘度及表面张力的大 小取决于渣的化学成分。保护渣的研制和使用 过程要对其密度、熔化温度、粘度、表面张力 和溶解吸收非金属夹杂物能力等基本性质进行 测定。除了上述几个基本性质之外,保护渣的 熔融速度、熔融模型以及导热性也是衡量保护 渣性能的主要指标。
用于连铸保护渣的原材料种类繁多,分为天然矿 物(如石灰石、萤石、硅灰石、石英砂等)和 人造矿物(工业废渣、水泥熟料、玻璃粉、人 造硅灰石等)。
6Leabharlann 连铸技术保护渣组成、性能与原料选择之间的关系
7
连铸技术
保护渣的物性指标主要包括成分、熔点、熔速、 粘度等,这些指标主要取决于 CaO、SiO2、 Al2O3的百分含量、组成助熔剂和熔速调节剂 的成分及加入量。不同的钢种、断面或拉速对 保护渣的特性要求差别比较大,相应地,保护 渣的化学成分变化也很大。
对连铸结晶器保护渣渣层分析
对连铸结晶器保护渣渣层的分析[摘要]连铸结晶器保护渣的主要功能包括:使结晶器壁与铸坯壳之间保持润滑;控制结晶器与铸坯之间的热交换;保持结晶器顶部处于绝热状态;防止钢水二次氧化;吸收钢水中上浮到液面的夹杂物。
其中两个最为重要的功能是保持结晶器壁与坯壳间的润滑和控制传热。
[关键词]连铸结晶器保护渣铸坯中图分类号:tf777.1 文献标识码:a 文章编号:1009-914x (2013)07-0256-011、引言固态结晶器保护渣的结晶比对铸坯与结晶器之间的热流量有重要影响。
某些特定钢种的保护渣是根据该钢种特有的冷却条件而设计的。
有鉴于此,结晶器保护渣的组织结构和凝固特性具有重要意义。
结晶器保护渣中的晶体成分愈多,结晶器保护渣结构愈疏松,从而降低保护渣内的辐射传热。
中碳钢结晶器保护渣具有较高的结晶比,保护渣层内的传热较为均匀,有利于降低连铸坯内的纵裂纹的形成。
结晶器凝固保护渣的取样位置位于结晶器以下部位。
通过分析渣样横截面可以看出沿渣膜厚度方向存在着不同的结晶形态。
对于非中碳钢结晶器保护渣而言,并不需要太高的保护渣结晶比。
实际上在铸坯壳出结晶器之前要达到足够的厚度常常需要较高的传热速率。
因为浇铸这些钢种时的拉坯速度较高(>1.3m/min)。
现已对结晶器保护渣的结晶情况即结晶倾向进行了实验室和工厂的实验研究。
试验室的大部分试验研究,均是在对保护渣控制加热或控制冷却的试验条件下进行,然后再对凝固的保护渣进行分析研究。
在对保护渣的结晶研究中广泛使用了差热分析方法(dta)。
在本研究中,为了确定液态结晶器保护渣在冷却时的结晶温度,在实验时将保护渣的温度变化与参照试样进行了对比。
采用差热分析的方法研究表明,结晶器保护渣的结晶趋势随cao/sio2的比值、li2o、tio2和zro2含量的增加而增强,随b2o3含量的减少而增强。
fonseca等人对自己所采取的保护渣样进行了研究,结果表明,中碳钢保护渣结晶层厚度和保护渣层总厚度均比低碳钢保护渣高。
连铸保护渣的基本功能及其在结晶器中的行为
个人收集整理勿做商业用途目录中文摘要........................................................................ 错误!未定义书签。
英文摘要........................................................................ 错误!未定义书签。
1 绪论 (1)1。
1连铸保护渣的基本功能及其在结晶器中的行为 (1)1.1。
1连铸保护渣的作用 (1)1。
1。
2连铸保护渣在结晶器内行为 (2)1.2裂纹敏感性钢种连铸面临的问题 (4)1。
3连铸保护渣结晶性能的研究现状 (6)1。
3.1影响连铸保护渣结晶特性的因素 (6)1.3。
2连铸保护渣结晶性能对传热的影响 (7)1。
3。
3结晶器中保护渣控制传热的途径 (8)1.4国内外关于保护渣凝固收缩性能的研究 (9)1。
5本课题的来源、研究的主要内容 (11)2 实验方案与设备 (12)2.1保护渣凝固收缩性能的测试方案 (12)2。
1.1保护渣体积变化率的评价方法 (12)2。
1。
2保护渣结晶体、玻璃体密度的测试方法 (12)2.1.3实验过程中渣样的对比研究方案 (14)2。
2实验渣成分的设计 (15)2. 3与保护渣结晶性能相关的参数的测定 (18)2.3。
1保护渣定点粘度、粘温曲线的测试 (18)2。
3.2保护渣熔化温度的测试 (20)3 实验结果及分析 (22)3.1相同渣系组分对结晶性能、凝固收缩性能影响的探讨 (22)3.2不同渣系的保护渣凝固收缩性能的探讨 (27)3。
3不同冷却速度对凝固收缩性能的影响的探讨 (28)4 结论 (30)5 致谢 (30)参考文献 (32)1 绪论连铸保护渣是连铸过程中关键性辅料,对连铸工艺的顺行和铸坯表面质量的控制具有重要影响。
保护渣从加入到离开结晶器这一过程中所发挥的作用可归结为:对结晶器钢液面绝热保温,避免钢液凝固;保护钢液面不受空气二次氧化;吸收钢液中上浮的夹杂物;润滑运动的铸坯;均匀和调节凝固坯壳向结晶器的传热.在上述诸多功能中,最重要的是润滑铸坯和控制传热两大特性。
- 1、下载文档前请自行甄别文档内容的完整性,平台不提供额外的编辑、内容补充、找答案等附加服务。
- 2、"仅部分预览"的文档,不可在线预览部分如存在完整性等问题,可反馈申请退款(可完整预览的文档不适用该条件!)。
- 3、如文档侵犯您的权益,请联系客服反馈,我们会尽快为您处理(人工客服工作时间:9:00-18:30)。
浅析连铸结晶器保护渣渣圈
王爱兰刘平陈建新
(包钢(集团)公司技术中心,包头 014010)
摘要:通过对连铸结晶器保护渣渣圈形成原因的剖析,结合生产实际分析并讨论了
影响渣圈形成的因素及对保护渣使用性能的影响。
关键词:连铸结晶器保护渣渣圈
Analyse of slag circule to mould powder
WANG Ailan Liu Ping Chen Jianxin
(Technology center of Baotou Iron and Steel(Group)Co)
Abstract: this paper analyse forming factors of slag circule to mould powder
and application performance of mould powder in according to production.
Keywords: mould powder slag circule of mould powder
1 前言
连铸保护渣是直接影响连铸稳定生产和改善铸坯质量的一种消耗性材料,在结晶器中必须保证合适的熔渣层结构才能充分发挥其五大冶金功能:覆盖保温、防止二次氧化、吸收夹杂、在结晶器与铸坯间起润滑作用和改善结晶器与铸坯间的传热。
其中最重要的两个冶金功能是“润滑”和“控制传热”,这两个功能的良好发挥是借助于熔融保护渣充填到结晶器壁和坯壳之间的缝隙内形成渣膜得以实现,而渣膜又受流入结晶器壁的熔渣量控制,熔渣流入量与渣圈之间存在着内在的联系。
深入研究渣圈结构特征及其与冶金功能之间的关系具有实际意义。
2 连铸结晶器保护渣渣圈的形成及对使用性能的影响
连铸结晶器保护渣渣圈是在熔渣与结晶器壁之间高梯度温度场内形成的[1]。
保护渣在浇注条件下,结晶器的上下运动和熔渣的粘滞流动使熔渣由弯月面流向结晶器和铸坯之间,粘附在结晶器的铜壁上,起润滑作用,使铸坯顺利拉出铸机。
在熔渣的流入过程中,高温状态
下的液渣与水冷的结晶壁相接触,在这个高梯度温度场内,如果保护渣的物理性能不适当,必然在弯月面上方的结晶器边缘形成渣圈,随着浇注的进行,渣圈越长越大。
如图1所示。
在浇注过程中一旦形成渣圈,必然会影响流入结晶器壁与坯壳之间的熔渣量的大小。
在负滑脱时期,由于渣圈会使凸出的弯月面压向钢液,这就可能在负滑脱时期内阻塞熔渣的流入通道。
只有当结晶器向上运动处于最高位置时,熔渣流入通道畅通,钢液弯月面上的熔渣才能进入与结晶器接触的部位,其后被带入弯月面以下,粘附在结晶器的铜壁上。
此涂层由于与高温坯壳接触部分被重熔,起到润滑铸坯的作用。
从熔渣这种流入机制可以看出,结晶器每振动一个周期所流入的熔渣量除了与钢液面上的熔渣层厚度和熔渣的物理性能有关外,还与保护渣在结晶器边缘形成的渣圈的性状有关。
当渣圈形成较薄而少时,其熔渣流入结晶器与坯壳间的量就大,反之流入量就少,而此时渣圈成长速度也异常的快,较厚的凝固渣圈势必影响钢液弯月面的性状,使弯月面的曲率半径变小[1],这种情况可使铸坯表面缺陷增多,尤其容易引起铸坯表面纵裂。
可见,渣圈对保护渣的消耗有很大的影响,从而影响其冶金功能的正常发挥。
3 导致渣圈形成的因素
3.1保护渣的粒度和熔化均匀性
在配制保护渣时,当各种原料粒度差别大,或原料混合不均匀易出现分熔现象,易熔成分首先熔化而流失,难熔的残留部分成为烧结物,这样就可能逐渐在结晶器铜壁四周结成很厚渣壳,从而形成渣圈。
在配制过程中基料选择必须适当且混合均匀,粒度适中,才能保证加入结晶器后熔化性能良好,从而减少渣圈的形成。
3.2保护渣的熔化温度与凝固温度
保护渣的熔化区间与凝固区间窄,其熔渣在高温状态下稳定性差,在结晶器弯月面处易形成渣圈。
3.3保护渣的化学组成
基料中尽量减少常规熔剂如Na2O、CaF2的加入,改加BaO 、Li2O、MgO等能降低保护渣熔化温度的物质,从而减少枪晶石和霞石的析出,提高了保护渣的润滑性,减少渣圈的生成。
使用的助熔剂和基料之间不能产生较大的偏析,否则它们之间的化学反应差,产生分熔现象,也易形成渣圈[2]。
另外在保护渣生产过程中,如果所用基料的矿物组成与所设计的保护渣化学成分有较大的差异,使保护渣的物理性能不稳,也易形成渣圈。
3.4工艺条件
在生产过程中,拉速变化、结晶器液面的波动、结晶器水量[2]、液渣层的厚度、浇钢温度的波动及保护渣的加入方式不合理等原因都可加剧渣圈的形成。
3.4.1拉速:适当提高拉速,将使热面温度升高,因而使在弯月面处的液渣的粘度降低,使渣圈变薄。
反之,易生成厚的渣圈。
3.4.2结晶器液面的波动:波动大,在弯月面处的熔渣温度过低,渣子极易凝固和析晶,易生成厚的渣圈。
3.4.3结晶器水量:减少结晶器水量,将使铜板热面温度升高,使渣圈变薄。
3.4.4液渣层的厚度:液渣层太高,易形成大的渣圈。
3.4.5钢水过热度:过热度太低,在浇注过程中,弯月面处的钢水温度偏低,影响保护渣的熔化,易形成渣圈。
3.4.6保护渣的加入方式:在浇注过程中保护渣加入的量、时间不当或不均匀,易形成渣圈,在操作中要遵循勤加少加的原则。
4 连铸结晶器保护渣实际使用过程中产生渣圈的分析
4.1浇注工艺
钢水由80吨转炉冶炼,经LF钢包炉精练后运至圆坯连铸机进行浇注,浇注条件见表1。
4.2浇注所用保护渣的测试方法和理化性能检测结果
熔化温度采用半球点法测定,试样熔化并降至3/4高度时为软化温度,降至1/2高度时为半球温度,降至1/4高度时为流动温度,半球温度为熔化温度。
熔化区间为保护渣流动温度与软化温度之差。
粘度计检测1300℃粘度,并测出保护渣粘度--温度曲线,粘度曲线出现拐点时的转折温度为保护渣的结晶温度,粘度达到10 Pa.s时的温度为保护渣的凝固温度[3]。
保护渣理化性能检测见表2,粘度温度曲线见图2
图2粘度温度曲线
4.3使用情况
1#渣在连铸过程中产生的渣圈较多且肥大,现场操作工需及时的挑出。
从渣圈的外观看,表面粗糙,断面有明显的分层现象,为了进一步了解其组成结构,进行了岩相分析,结果表明:渣圈主要由结晶体组成,在靠近铸坯一侧主要是由黄长石和少量的枪晶石组成结晶体,颜色呈深黄色,约占50%左右,见图3。
接下来部分主要是枪晶体和玻璃体,约占20%左右,见图4。
在靠近结晶器边缘是玻璃体,约占30%左右。
图3渣圈的黄褐色部分(主要是黄长石、亮点为小铁珠)图4渣圈的灰色部分(片柱状为枪晶石)
2#渣在使用过程中产生的渣圈较少,渣圈样是在连浇15炉过程中收集到的,表面平滑,断面呈两层结构,进行岩相分析,结果表明:在靠近铸坯一侧主要是枪晶石和少量黄长石的结晶体,约占60%左右,见图5。
靠近结晶器边缘是玻璃体,约占40%左右。
图5渣圈的边缘部分(片柱状为枪晶石、亮点为小铁珠)
4.4分析讨论
从熔化温度来看,1#渣的熔化温度偏低,熔化区间较窄55℃左右。
2#渣的熔化温度相对高一些,熔化区间较宽84℃左右。
保护渣的熔化温度直接影响结晶器弯月面处液渣的熔融状态。
较宽的熔化区间能使结晶器上部铸坯凝固壳表面渣膜处于粘滞的流动状态,保证熔渣有较好的性能稳定性。
1#渣熔化区间较窄,其熔渣在高温状态下稳定性较差,在弯月面处易形成厚的渣圈。
从粘度温度曲线和岩相结果可见,1#渣粘度温度曲线出现拐点后粘度上升较快,即凝固区间窄,仅为10℃左右。
2#渣粘度温度曲线出现拐点后粘度上升较缓慢,即凝固区间宽,为50℃左右。
液渣在冷却过程中,1#渣的结晶率明显比2#渣高。
由于1#渣凝固区间相对2#渣较窄,液渣在冷却过程中又具有较高的结晶率,当结晶器液面波动或温度不均时很易在弯月面处形成厚的渣圈。
通过以上分析可知,保护渣的理化性能直接影响其使用性能,2#渣的理化性能更适合中碳锰钢的生产,在现场生产中取得了良好的使用效果,铸坯表面质量得到了很大提高。
5 结论
在保护渣浇注过程中,保护渣的性能和拉坯速度直接影响着弯月面熔渣的性状,完全没有渣圈是不可能的,但是如果我们在其化学组成上进行合理的配制、连铸时根据不同钢种严格按其操作规程执行,就能大大减少渣圈的生成速度和数量。
通过以上分析表明,剖析渣圈结构,分析其对渣耗、润滑性能的影响,对优化结晶器保护渣使用性能具有实际意义。
参考文献
[1] 迟景灏,甘永年.连铸保护渣.东北大学出版社.1993.40-41
[2] 卢盛意.连铸坯质量.冶金出版社.2000.171-172
[3] 王玉霞,楚志宝.连铸结晶器保护渣的应用分析.连铸2004.1:41-4。