车削粗糙度计算公式
车削切削参数计算

车削切削参数计算包括计算切削线速度、主轴转速、金属去除率、净功率、加工时间以及特定切削力。
这些参数的计算公式如下:
1. 切削线速度:Vc = πDn/1000(m/min),其中D为工件或刀具直径(mm),n为主轴转速(rpm)。
2. 主轴转速:n = 1000Vc/πD(rpm),其中D为工件或刀具直径(mm),Vc为切削线速度(m/min)。
3. 金属去除率:Q = F×Vc×S×η,其中F为切削截面积(mm^2),Vc为切削线速度(m/min),S为切削行程(mm),η为刀具寿命(min)。
4. 净功率:Pc = Q×Z/60,其中Q为金属去除率(cm^3/min),Z 为机械效率。
5. 加工时间:Tc = T×n,其中T为切削时间(min),n为主轴转速(rpm)。
6. 特定切削力:Kc = F×η/S,其中F为切削截面积(mm^2),η为刀具寿命(min),S为切削行程(mm)。
这些公式可以用来计算车削过程中的切削参数,有助于优化加工过程和提高生产效率。
车削表面粗糙度的计算

车削表面粗糙度的计算说说表面粗糙度的计算,以及"镜面效果"-表面粗糙度现在越来越受到各行业的重视,论坛里也经常问及如何提高表面粗糙度的帖子.今天讲一下关于车削的表面粗糙度.图片上面有车削表面粗糙度的计算方式,只需要将切削参数代入即可计算出可能最高的"表面粗糙度"(以下发言全部以粗糙度低为细,粗糙度高为粗)车削表面粗糙度=每转进给的平方*1000/刀尖R乘8以上计算方式是理论上的可能达到最坏的的效果,实际上因刀具品质、机床刚性精度、切削液、切削温度、切削速度、材料硬度等等原因,会将粗糙度提高或者降低的,如果你用上面的计算方式计算出来的粗糙度都不能满足想达到的效果,请先更改切削参数。
但进给一般和切深有着密切的关系,一般进给是切深的10%~20%之间,排削的效果是最好的切削深度,因为屑的宽度和厚度最合比例以上公式的各个参数我下面详细一项项解释一下对粗糙度的影响,如有不正请指点:1:进给——进给越大粗糙度越大,进给越大加工效率越高,刀具磨损越小,所以进给一般最后定,按照需要的粗糙度最后定出进给2:刀尖R——刀尖R越大,粗糙度越降低,但切削力会不断增大,对机床的刚性要求更高,对材料自身的刚性也要求越高。
建议一般切削钢件6150以下的车床不要使用R0.8以上的刀尖,而硬铝合金不要用R0.4以上的刀尖,否则车出的的真圆度、直线度等等形位公差都没办法保证了,就算能降低粗糙度也是枉然!3:切削时要计算设备功率,至于如何计算切削时所需要的功率(以电机KW的80%作为极限),下一帖再说。
要注意的时,现在大部分的数控车床都是使用变频电机的,变频电机的特点是转速越高扭力越大,转速越低扭力越小,所以计算功率是请把变频电机的KW除2比较保险。
而转速的高低又与切削时的线速度有密切关系,而传统的普车是用恒定转速/扭力的电机依靠机械变速来达到改变转速的效果,所以任何时候都是“100%最大扭力输出”,这点比变频电机好。
车削加工的计算式

车削加工的计算式切削速度(vc)vc (m/min) : 切削速度Dm (mm) : 工件材料直径π (3.14): 圆周率n (min-1) : 主轴转速(例题)主轴转速700min-1、工件直径Ø50,求此时的切削速度。
( 答)π=3.14、Dm=50、n=700代入公式vc=(π×Dm×n)÷1000=(3.14×50×700)÷1000=110(m/min)切削速度为110m/min进给量(f)f (mm/rev): 每转进给量I(mm/min): 每分钟切削长度n (min-1): 主轴转速(例题)主轴转速500min-1、每分钟切削长度120mm/min,求此时的每转进给量。
( 答)n=500、l=120代入公式f=l÷n=120÷500=0.24(mm/rev)每转进给量为0.24mm/rev切削时间(Tc)Tc (min): 切削时间Im (mm): 工件长度I(mm/min): 每分钟的切削长度(例题)长度100mm的工件,主轴转速1000min-1、进给量0.2mm/rev,求此时的切削时间。
( 答)首先根据进给量与主轴转速,求出每分钟切削长度。
l=f×n=0.2×1000=200(mm/min)将l代入公式Tc=lm÷l=100÷200=0.5(min)0.5×60=30秒理论表面粗糙度(h)h (µm): 表面粗糙度f (mm/rev): 每转进给量Re (mm): 刀尖圆弧半径(例题)刀尖圆弧半径0.8mm、进给量为0.2mm/rev, 求理论表面粗糙度。
( 答)将f=0.2mm/rev、Re=0.8代入公式h=f2÷(8×Re)×1000=0.22÷(8×0.8)×1000=6.25µm 理论表面粗糙度6μm。
粗糙度的三种表示方法
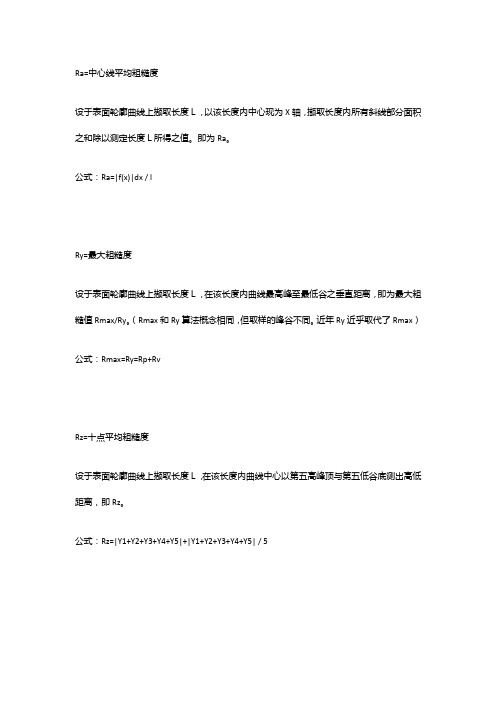
Ra=中心线平均粗糙度
设于表面轮廓曲线上撷取长度L,以该长度内中心现为X轴,撷取长度内所有斜线部分面积之和除以测定长度L所得之值。
即为Ra。
公式:Ra=|f(x)|dx / l
Ry=最大粗糙度
设于表面轮廓曲线上撷取长度L,在该长度内曲线最高峰至最低谷之垂直距离,即为最大粗糙值Rmax/Ry。
(Rmax和Ry算法概念相同,但取样的峰谷不同。
近年Ry近乎取代了Rmax)公式:Rmax=Ry=Rp+Rv
Rz=十点平均粗糙度
设于表面轮廓曲线上撷取长度L,在该长度内曲线中心以第五高峰顶与第五低谷底测出高低距离,即Rz。
公式:Rz=|Y1+Y2+Y3+Y4+Y5|+|Y1+Y2+Y3+Y4+Y5| / 5。
粗糙度计算公式

粗糙度计算公式粗糙度是指表面不平整程度的度量,它是表面形貌的一个参数。
在工业制造和科学研究中,粗糙度的计算是非常重要的,因为它可以用来描述表面的质量和功能性能,如摩擦、接触、润滑、密封等。
本文将介绍粗糙度计算的基本公式,包括平均粗糙度、均方根粗糙度、最大峰高度和最大谷深度等。
一、平均粗糙度平均粗糙度是表面粗糙度的一个基本参数,它是指表面高度的平均值。
平均粗糙度的计算公式如下:Ra = 1/n ∑|Zi|其中,Ra为平均粗糙度,n为采样点数,Zi为第i个采样点的高度。
在实际测量中,一般采用激光干涉仪、扫描电子显微镜、原子力显微镜等仪器来测量表面高度,然后通过计算平均值得到平均粗糙度。
二、均方根粗糙度均方根粗糙度是表面粗糙度的另一个重要参数,它是指表面高度的均方根值。
均方根粗糙度的计算公式如下:Rq = √(1/n ∑(Zi- Z)^2)其中,Rq为均方根粗糙度,n为采样点数,Zi为第i个采样点的高度,Z为所有采样点的平均高度。
与平均粗糙度不同,均方根粗糙度更能反映表面高度的分布情况,因此在某些应用中更为重要。
三、最大峰高度和最大谷深度最大峰高度和最大谷深度是表面粗糙度的两个极值参数,它们分别表示表面上最高的凸起和最低的凹陷。
最大峰高度和最大谷深度的计算公式如下:Rp = max(Zi) - ZRv = Z - min(Zi)其中,Rp为最大峰高度,Rv为最大谷深度,Zi为所有采样点的高度,Z为所有采样点的平均高度。
在实际应用中,最大峰高度和最大谷深度常用于描述表面的极端情况,如表面缺陷、损伤等。
总之,粗糙度计算是表面质量评价的重要手段之一,它可以用来描述表面的几何形貌和功能性能。
不同的粗糙度参数对应不同的表面特征,因此在实际应用中需要根据具体情况选择合适的参数。
同时,粗糙度计算也需要结合实际测量技术和仪器,以获得准确的表面高度数据。
车削粗糙度计算公式(Calculationformulaofturningroughness)
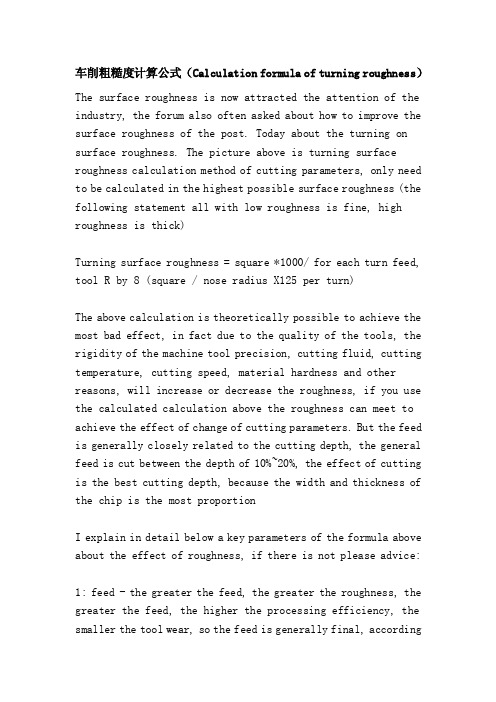
车削粗糙度计算公式(Calculation formula of turning roughness)The surface roughness is now attracted the attention of the industry, the forum also often asked about how to improve the surface roughness of the post. Today about the turning on surface roughness. The picture above is turning surface roughness calculation method of cutting parameters, only need to be calculated in the highest possible surface roughness (the following statement all with low roughness is fine, high roughness is thick)Turning surface roughness = square *1000/ for each turn feed, tool R by 8 (square / nose radius X125 per turn)The above calculation is theoretically possible to achieve the most bad effect, in fact due to the quality of the tools, the rigidity of the machine tool precision, cutting fluid, cutting temperature, cutting speed, material hardness and other reasons, will increase or decrease the roughness, if you use the calculated calculation above the roughness can meet to achieve the effect of change of cutting parameters. But the feed is generally closely related to the cutting depth, the general feed is cut between the depth of 10%~20%, the effect of cutting is the best cutting depth, because the width and thickness of the chip is the most proportionI explain in detail below a key parameters of the formula above about the effect of roughness, if there is not please advice:1: feed - the greater the feed, the greater the roughness, the greater the feed, the higher the processing efficiency, the smaller the tool wear, so the feed is generally final, accordingto the required roughness of the final set of feed2: tool point R - the greater the tool R, the lower the roughness, but the cutting force will continue to increase, rigid requirements of the machine tool higher, the higher the rigidity of the material itself. The following 6150 suggestions do not use more than R0.8 lathe tool cutting steel and aluminum alloy, do not use R0.4 above the tip, otherwise the car out of roundness, straightness tolerances and so on can't guarantee, even can reduce the roughness in vain!3: when cutting, to calculate the equipment power, as to how to calculate the power needed for cutting (motor KW 80% as the limit), the next said. Note, now most of the CNC lathe is the use of variable frequency motor, the characteristics of variable frequency motor speed higher torque is greater, the lower the speed of torque is small, so the calculation power is please variable-frequency motor KW except for 2 more insurance. While the speed level and cutting line speed are closely related, but the traditional car is in constant speed / torque motor on mechanical transmission to change the speed of the effect, so any time is "100% maximum torque output, this motor than good. But of course, if your spindle is driven by expensive constant torque servo motors, that's the perfect choiceThat was a bit of a mess, now for example to calculate the surface roughness: Turning 45 steel, the cutting speed of 150 meters, 3mm depth of cut, feed 0.15, R tip R0.4, this is my very commonly used in light cutting parameters, basically not finish requirements very high workpiece knife divided into coarse andfine cutting directly car surface, calculation of surface roughness is equal to 0.15*0.15/0.4/8*1000= (7 micron roughness units).If there is a requirement to finish to 0.8, as follows: the tool cutting parameters unchanged still above 0.4 blade, cutting parameters feed 0.05, depending on the depth of cut off and slot cutting tool, usually if given the depth of cut, only in a very narrow range (which is not said that the depth of cut and feed very well), when the cutting depth within a certain range will have the best effect of the chip discharge! Of course you don't mind taking a side of the car side ditch cuttings subgroove words is another matter! Lol: I'm about 10 times as deep as the feed, which is 0.5mm, which is 0.05*0.05/0.4/8*1000=0.78 microns, or 0.8 roughness.As for the representation of the roughness of RY is the largest roughness measurement, RA arithmetic is meter method surface roughness of the workpiece on average, while RZ is the 10 point average, generally the same workpiece with RA calculation of roughness is the lowest, while the RY is definitely the biggest,If you use RY formula, you can achieve a lower number than RA requirements, basically out of the car, you can achieve the tagging requirements of the RA. In addition, theoretically, a tool with a trim edge may reduce roughness by half, and if the top 0.8 of the workpiece is polished, the blade with a light trimmed blade has a minimum roughness of 0.4These are the book extracts of theoretical knowledge, integrated personal experience, the book, the following to talkabout some of my personal feelings of the theory, these books I have not seen:1: the lathe can reach the minimum roughness, the primary reason is that the precision of the spindle, in accordance with the method of calculating the maximum roughness, if you beat the precision lathe spindle is 0.002mm, which is 2 microns beating, that is theoretically impossible to process the roughness will be less than 0.002 mm roughness (RY2.0) of the workpiece, but this is the maximum possible value, the average is 50%, the surface roughness of 1 can be processed! Combined with the RA algorithm, generally do not reach more than 50% of the RY value, become RA0.5, and then calculate the role of light trimming reduced by 50%, then the final spindle jump 0.002 of the limit of the lathe can be processed about RA0.2 of the workpiece!。
流体力学 粗糙度计算公式
流体力学粗糙度计算公式流体力学是研究流体在静止和运动状态下的力学性质和运动规律的学科。
在工程实践中,流体力学的应用非常广泛,比如在水利工程、航空航天工程、能源工程等领域都有重要的应用。
而在流体力学中,粗糙度是一个非常重要的参数,它对流体的流动性能有着重要的影响。
粗糙度是指流体流动的管道或表面的不平整程度。
在实际工程中,粗糙度常常是一个需要进行准确计算的参数,因为它直接影响着流体的摩擦阻力和流速分布。
粗糙度的计算公式是流体力学中的一个重要内容,下面我们将介绍粗糙度的计算公式及其应用。
粗糙度的计算公式通常是根据实际工程情况和流体性质来确定的。
在工程实践中,常用的粗糙度计算公式有Colebrook公式、Nikuradse公式等。
其中,Colebrook公式是用来计算管道内流体的摩擦阻力系数的公式,它的表达式为:1/√f = -2log(ε/D/3.7 + 2.51/(Re√f))。
其中,f为摩擦阻力系数,ε为管道壁面的绝对粗糙度,D为管道的直径,Re 为雷诺数。
在工程实践中,可以根据实际情况和流体性质来确定Colebrook公式中的参数值,从而计算出管道内流体的摩擦阻力系数。
另外,Nikuradse公式是用来计算管道内流体的摩擦系数的公式,它的表达式为:1/√f = -1.8log(ε/3.7D + 6.9/Re√f)。
其中,f为摩擦系数,ε为管道壁面的绝对粗糙度,D为管道的直径,Re为雷诺数。
通过Nikuradse公式,可以计算出管道内流体的摩擦系数,从而进一步分析流体的流动性能。
在实际工程中,粗糙度的计算公式是非常重要的,它可以帮助工程师准确地分析流体的流动性能,从而为工程设计和优化提供重要的参考依据。
通过粗糙度的计算公式,工程师可以合理地选择管道材料、优化管道设计,从而降低流体的摩擦阻力,提高流体的流动效率。
除此之外,粗糙度的计算公式还可以帮助工程师分析流体的流速分布和流动状态,从而进一步优化流体的流动性能。
车床工时计算
3.2
>50
0.18~0.25
0.25~0.30
0.3~0.4
0.25~0.30
0.30~0.35
0.35~0.5
1.6
<50
50~100
>100
0.1
0.11~0.15
0.15~0.22
0.11~0.16
0.16~0.25
0.25~0.35
0.16~0.20
0.20~0.25
0.25~0.35
≦3
﹥3~5
﹥5~8
﹥8~12
f―进给量(r/mm)
碳钢、
合金钢、
耐热钢
20
0.3~0.4
---------
-----------
----------
40
0.4~0.5
0.3~0.4
-----------
----------
60
0.6~0.7
0.5~0.7
0.4~0.6
----------
100
0.8~1.0
0.112
60
66.9
355
0.280
84.8
450
0.158
84.8
450
0.120
75
65.9
280
0.296
83.6
355
0.172
83.6
355
0.124
95
66.8
224
0.136
83.5
280
0.192
83.6
280
0.136
125
70.6
180
0.316
87.9
224
常用车削加工计算公式
常用车削加工计算公式车削加工是金属加工中最常见的一种加工方式,适用于各种金属材料的加工。
在车削加工过程中,计算公式是帮助确定切削速度、进给速度和主轴转速等参数的关键因素。
下面将介绍一些常用的车削加工计算公式。
1.切削速度公式:切削速度是指工件表面的切削线速度,通常用Vc表示,单位是m/min。
切削速度公式如下:Vc=π×D×n其中,D为工件直径,单位是mm;n为主轴转速,单位是转/分钟。
2.进给速度公式:进给速度是指刀具在工件上移动的速度,通常用Vf表示,单位是mm/min。
进给速度公式如下:Vf=n×f×z其中,n为主轴转速,单位是转/分钟;f为每转进给量,单位是mm/转;z为刀具刃数。
3.主轴转速公式:主轴转速是指主轴每分钟旋转的圈数,通常用n表示,单位是转/分钟。
主轴转速公式如下:n=1000×Vc/(π×D)其中,Vc为切削速度,单位是m/min;D为工件直径,单位是mm。
4.主轴转动时间公式:主轴转动时间是指主轴从零转速加速到设定转速所需的时间,通常用t表示,单位是秒。
主轴转动时间公式如下:t=(n2-n1)/a其中,n1为初始主轴转速,单位是转/分钟;n2为最终主轴转速,单位是转/分钟;a为主轴加速度,单位是转/分钟²。
5.简化车削时间公式:简化车削时间是指刀具从初始位置移动到终点位置所需的时间,通常用t表示,单位是分钟。
简化车削时间公式如下:t=(L/1000)/Vf其中,L为刀具的移动路径长度,单位是mm;Vf为进给速度,单位是mm/min。
6.车削力公式:车削力是指刀具对工件施加的力,通常用F表示,单位是N。
车削力公式如下:F = K × f × ap × cos(ψ) × c其中,K为切削力系数;f为进给量,单位是mm/转;ap为切削深度,单位是mm;ψ为刀具前角;c为刀具刃数。
以车代磨在淬硬齿轮内孔加工中的应用
以车代磨在淬硬齿轮内孔加工中的应用新乡航空工业(集团)有限公司 453000摘要针对淬硬齿轮内孔磨削效率的不足,结合硬车削的特点,分析淬硬齿轮内孔采用以车代磨工艺的可行性。
通过制订切合实际的以车代磨加工方案,并给出了相应数据,在生产中获得成功,极大地提高了生产效率。
关键词以车代磨内孔加工粗糙度刀片一、引言二十一世纪初期,随着高硬度刀具材料、涂层技术机床结构刚性不断改进,如采用CBN 刀具、陶瓷刀具新型精密车床及车削加工中心上对淬硬钢进行车削等,结果都取得了非常好加工效果,其加工质量和精度可以达到精磨水平,车削硬度极限也已达到HRC68。
越来越多的工业强国已将硬车削作为替代磨削一种经济实用方法普及。
二、车削粗糙度的理论计算车床加工回转体工件时,刀刃在工件上运动轨迹是螺旋线,所以,让工件通过放大观测可以看到工件表面不是光滑的圆柱表面,而是等于螺距很小(等于进给量)的螺纹表面。
这是形成表面粗糙度的原因之一。
在加工过程中由于加工表面的塑性变形、刀具在工作表面的摩擦以及在切削过程中产生的其它现象,往往使已加工表面的实际粗糙度H实大于理论高度H。
表面粗糙度的理论高度H的计算可以按刀尖圆弧半径re=0与re≠0情形分别加以讨论。
2.1当re≠0时,根据几何学知识,有AB2=O1A2- O1B2即((re-H) 2=re2–(f 2)2∴ H= re(1- )一般来说,在加工粗糙度较高的工件表面时,刀尖圆弧半径re取得较大,而进给量f远比re小,这时≈1- 1 2( f 2re)2注:根据微分学中的近似计算公式f(x)= f(x0)+ f'(x0)(x-x0),对于f(x)= ,取x0=0,有≈ 1- 1 2x,(|X|充分小)故H= re{1-(1- 1 2( f 2re)2}得到H≈ f2 8re …………………………… 公式 12.2当re=0时∵ cotΨ1= f1H , cotΨ= f2H因(其中f1 + f2=f)∴cotΨ1+ cotΨ= f1H+ f2H= fH故H=f/( cotΨ1+ cotΨ)……………………… 公式 22.3提高表面粗糙度的研究由公式1、2可以看出:主偏角Ψ及副偏角Ψ1越小,刀尖圆弧re越大,f 越小时,表面粗糙度的理论高度H就越小。
- 1、下载文档前请自行甄别文档内容的完整性,平台不提供额外的编辑、内容补充、找答案等附加服务。
- 2、"仅部分预览"的文档,不可在线预览部分如存在完整性等问题,可反馈申请退款(可完整预览的文档不适用该条件!)。
- 3、如文档侵犯您的权益,请联系客服反馈,我们会尽快为您处理(人工客服工作时间:9:00-18:30)。
车削粗糙度计算公式
表面粗糙度现在越来越受到各行业的重视,论坛里也经常问及如何提高表面粗糙度的帖子.今天讲一下关于车削的表面粗糙度.图片上面有车削表面粗糙度的计算方式,只需要将切削参数代入即可计算出可能最高的"表面粗糙度"(以下发言全部以粗糙度低为细,粗糙度高为粗)
车削表面粗糙度=每转进给的平方*1000/刀尖R乘8(每转进给的平方/刀尖半径X125)
以上计算方式是理论上的可能达到最坏的的效果,实际上因刀具品质、机床刚性精度、切削液、切削温度、切削速度、材料硬度等等原因,会将粗糙度提高或者降低的,如果你用上面的计算方式计算出来的粗糙度都不能满足想达到的效果,请先更改切削参数。
但进给一般和切深有着密切的关系,一般进给是切深的10%~20%之间,排削的效果是最好的切削深度,因为屑的宽度和厚度最合比例
以上公式的各个参数我下面详细一项项解释一下对粗糙度的影响,如有不正请指点:
1:进给——进给越大粗糙度越大,进给越大加工效率越高,刀具磨损越小,所以进给一般最后定,按照需要的粗糙度最后定出进给
2:刀尖R——刀尖R越大,粗糙度越降低,但切削力会不断增大,对机床的刚性要求更高,对材料自身的刚性也要求越高。
建议一般切削钢件6150以下的车床不要使用R0.8以上的刀尖,而硬铝合金不要用R0.4以上的刀尖,否则车出的的真圆度、直线度等等形位公差都没办法保证了,就算能降低粗糙度也是枉然!
3:切削时要计算设备功率,至于如何计算切削时所需要的功率(以电机KW的80%作为极限),下一帖再说。
要注意的时,现在大部分的数控车床都是使用变频电机的,变频电机的特点是转速越高扭力越大,转速越低扭力越小,所以计算功率是请把变频电机的KW除2比较保险。
而转速的高低又与切削时的线速度有密切关系,而传统的普车是用恒定转速/扭力的电机依靠机械变速来达到改变转速的效果,所以任何时候都是“100%最大扭力输出”,这点比变频电机好。
但当然如果你的主轴是由昂贵的恒定扭力伺服电机驱动,那是最完美的选择
上面说得有点乱了,现在先举个例计算一下表面粗糙度:车削45号钢,切削速度150米,切深3mm,进给0.15,R尖R0.4,这是我很常用的中轻切削参数,基本上不是光洁度要求非常之高的工件一刀不分粗精切削直接车出表面,计算表面粗糙度等于0.15*0.15/0.4/8*1000=粗糙度7.0(单位微米)。
如果有要求光洁度要到0.8的话,切削参数变化如下:刀具不变依旧上面0.4的刀片,切削参数进给0.05,切深要视乎刀具的断削槽而定,通常如果进给
定了,那切深只会在一个
很窄的范围(上面不是说过切深和进给很大关系嘛)——当切深在一定范围之内才会有最良好的排屑效果!当然你不介意拿个沟子一边车一边沟屑的话又另当别论!:lol我大约会按照进给的10倍起定切深,也就是0.5mm,此时0.05*0.05/0.4/8*1000=0.78微米,也就是粗糙度达到0.8了。
至于粗糙度的表示方法:RY是测量出最大粗糙度,RA是算术计法将整个工件的表面粗糙度平均算,而RZ则是取10点再平均算,一般同一工件用RA计算粗糙度应该是最低的,而RY肯定是最大的,如果用RY的计算公式可以达到比RA要求更低的数字,基本上车出来就可以达到标注的RA要求了。
另外理论上带修光刃的刀具最大可能将粗糙度降低一半,如果上面车出0.8光洁度的工件用带修光刃的刀片粗糙度就最小可能是0.4
以上是书本摘录的理论知识综合个人经验所书,以下再说说一些我个人感觉的理论,这些书本上我没见过的:
1:车床可以达到的最小粗糙度,首要原因是主轴精度,按照最大粗糙度计算的方法,如果你的车床主轴跳动精度是0.002mm,也就是2微米跳动,那理论上是不可能加工出粗糙度会低于0.002毫米粗糙度(RY2.0)的工件,但这是最大可能值,一般平均下来算50%好了,粗糙度1.0的工件可以加工出!再结合RA的算法一般不会得出超过RY值的50%,变成RA0.5,再计算修光刃的作用降低50%,那最终主轴跳动0.002的车床极限是可以加工出RA0.2左右的工件!。