RoHS金属材料检验项目列表
ROHS指令检验判定标准

上海起风电器有限公司ROHS指令检验判定标准一、Array二、可豁免款项1.合金类:①钢合金:Pb≤0.35%;铝合金:Pb≤0.4%;铜合金:Pb≤4%②在铅—青铜合金轴承外壳和衬套中的Pb可豁免2.十聚溴联苯醚(Deca-BDE)可以豁免3.对于电子接触部件和电镀镉中的镉及其化合物三、备注1.XLt重金属分析仪测得的数据为样品中铬(Cr)的总含量和溴(Br)的总含量,六价铬(Cr +6)和聚溴联苯+聚溴联苯醚(PBB’S+PBDB’S)只是其中一部分。
2.XLt重金属分析仪测得的数据可精确到小数点后两位且带误差值,测量值具有95%的置信区间。
3.对于多种材料的包装,其所有包装材料(如印刷墨水、硬纸盒、水泡纸、扣带等)均要进行分别测试及分别符合含量要求。
四、关于NITON XLt797Z检测数据的说明(引自上海思创科技有限公司的传真资料)前提:依据ROHS标准,Cd﹤100ppm、Pb﹤1000ppm、Hg﹤1000ppm、Cr +6﹤1000ppm、PBB’S/PBDB’S﹤1000ppm1.Cd在塑料中(非金属)小于70ppm判定合格;70ppm﹤Cd﹤130ppm怀疑,作为企业进料,根据经验为避免麻烦一般判定不合格;大于130ppm判定不合格。
在金属中稳定的0.00%判定合格,小于0.03%用PLASTIC MODE再检测判断,判断标准同上;大于0.03%判断不合格。
2.Pb在塑料中(非金属)小于700ppm判定合格;700ppm﹤Cd﹤1300ppm怀疑,作为企业进料,根据经验为避免麻烦一般判定不合格;大于130ppm判定不合格。
在金属中根据豁免条例处理。
3.Br在塑料中(非金属)小于300ppm判定合格;大于300ppm:数值为几百/几千,经验认为是回炉料,因为以前的回炉料都不环保,故判定不合格;数值为几万(几十K),如果公司有阻燃要求,需通过供货方提供文件或第三方检测再做决定,如公司无阻燃要求,根据经验一般判定不合格。
rohs10项检测怎么做

ROHS10项检测的项目有铅Pb、汞Hg、镉Cd、六价铬Cr VI、多溴联苯PBB、多溴联苯醚PBDE、六溴环十二烷HBCDD、双-2-乙基己基邻苯二甲酸酯DEHP、邻苯二甲酸丁苄酯BBP、邻苯二甲酸二丁酯DBP 这些内容,新RoHS2.0指令2011/65/EU从2013年1月3日起强制实施,而且纳入CE认证范围。
产品如需出口欧盟国家就需要经过ROHS检测。
既然检测是一种硬性要求,那么怎么做就成为了一个大家比较关心的问题。
我们可以从以下几个方面来了解一下ROHS10项检测的重点和步骤。
一、ROHS2.0检测核心要求1、RoHS2.0指令规定,所管控产品按照“均质”材料计算(Homogenous material),所含铅(Pb)、汞(Hg)、六价铬(Cr(VI))、多溴联苯(PBBs)、多溴联苯醚(PBDEs)、邻苯二甲酸二(2-乙基己基)酯(DEHP),邻苯二甲酸丁苄酯(BBP),邻苯二甲酸二丁基酯(DBP),邻苯二甲酸二异丁酯(DIBP)的含量分别不得超过1000ppm,镉(Cd)的含量不得超过100ppm。
2、RoHS2.0生效后完全取代RoHS1.0,其中新加入的管控产品实施分阶段管理:医疗设备和视频监控设备从2014年7月22日起纳入管控,体外诊断医疗器械和工业监控设备将分别从2016年7月22日和2017年7月22日起纳入管控,最后一大类产品则从2019年7月22日起纳入管控。
3、依据2011/65/EU第16条的规定,今后贴有CE标志的产品将表明该产品不仅符合相关协调指令的要求(如EMC、LVD等),同时也符合RoHS2.0指令的要求。
同时根据欧盟官方所发布的RoHS2.0 FAQ所述:自2013年1月2日起,CE标识将成为产品符合RoHS2.0的唯一标识。
4、电子电气设备应在投放市场之前正确加贴CE标志的同时制造商应撰写相应的技术文档和EU符合性声明。
在电子电气设备投放市场后,制造商及其授权代表/进口商应留存EU符合性声明及技术文档至少10年。
金属rohs测试标准

金属rohs测试标准金属ROHS测试标准。
金属ROHS测试标准是指对金属材料中的有害物质进行检测的标准,其目的是保护人类健康和环境安全。
ROHS指的是限制使用某些有害物质(Restriction of Hazardous Substances),是欧盟针对电子电气产品的指令,旨在限制电子电气产品中的有害物质含量,其中包括铅、汞、镉、六价铬、多溴联苯和多溴二苯醚等物质。
金属ROHS测试标准主要针对金属材料中的有害物质含量进行检测,以确保产品符合环保要求,不会对人体和环境造成危害。
金属材料广泛应用于电子电气产品、汽车零部件、家用电器等领域,因此金属ROHS测试标准对于保障产品质量和用户健康至关重要。
金属ROHS测试标准通常包括对金属材料中有害物质的含量进行检测,如铅含量、镉含量、汞含量等。
测试方法通常采用X射线荧光光谱仪(XRF)进行快速分析,也可以采用化学分析方法进行准确测定。
测试标准通常遵循国际上通用的标准,如欧盟ROHS指令、美国ASTM标准等。
金属ROHS测试标准的制定和执行,对于企业来说具有重要意义。
一方面,金属ROHS测试标准是企业产品出口到欧盟等国家的必备条件,只有通过了ROHS测试的产品才能获得进入欧盟市场的资格。
另一方面,金属ROHS测试标准也是企业履行社会责任、保护用户健康的重要手段,通过严格执行ROHS测试标准,可以确保企业生产的产品符合环保要求,不会对用户和环境造成危害。
在执行金属ROHS测试标准时,企业需要重视以下几个方面。
首先,企业需要建立健全的金属材料采购管理体系,确保采购的金属材料符合ROHS要求。
其次,企业需要建立完善的金属ROHS测试实验室,配备先进的测试设备和专业的技术人员,确保测试结果的准确性和可靠性。
最后,企业需要建立完善的金属ROHS测试记录和档案管理制度,确保测试数据的可追溯性和可控性。
总之,金属ROHS测试标准对于企业来说具有重要意义,不仅是产品出口的必备条件,更是企业履行社会责任、保护用户健康的重要手段。
ROHS十项检测

ROHS六项+新增ROHS四项介绍第一部分 ROHS六项介绍RoHS认证是《电气、电子设备中限制使用某些有害物质指令》(The restriction of the use of certain hazardous substances in electrical and electronic equipment)的英文缩写。
rohs认证也叫做环保认证,是符合欧美标准的。
其规定,在电气、电子产品中如含有铅、镉、汞、六价铬、多溴二苯醚和多溴联苯等有害重金属的,欧盟从2006年7月1日将禁止进口.了解其他相关及检测请进个人主页一、有害物质是指哪些RoHS一共列出六种有害物质,包括:铅(Pb)、镉(Cd)、汞(Hg)、六价铬(Cr6+)、多溴联苯(PBB) 、多溴二苯醚(PBDE)。
RoHS指令限制使用以下六类有害物质1 水银(汞)使用该物质的例子:温控器、传感器、开关和继电器、灯泡2 铅使用该物质的例子:焊料、玻璃、PVC稳定剂3 镉使用该物质的例子:开关、弹簧、连接器、外壳和PCB、触头、电池4 铬(六价)使用该物质的例子:金属附腐蚀涂层5 多溴联苯(PBB)使用该物质的例子:阻燃剂,PCB、连接器、塑料外壳6 多溴二苯醚(PBDE)使用该物质的例子:阻燃剂,PCB、连接器、塑料外壳二、为什么要推出RoHS首次注意到电气、电子设备中含有对人体健康有害的重金属是2000年荷兰在一批市场销售的游戏机的电缆中发现镉。
事实上,电气电子产品在生产中目前大量使用的焊锡、包装箱印刷的油墨都含有铅等有害重金属。
三、何时实施RoHS欧盟于2006年7月1日起开始实施RoHS,对使用或含有重金属以及多溴二苯醚PBDE,多溴联苯PBB等阻燃剂的电气电子产品将不允许进入欧盟市场。
四、RoHS指令的函盖范围RoHS指令的函盖范围为AC1000V、DC1500V以下的由目录所列出的电子、电气产品:1、大型家用电器:冰箱、洗衣机、微波炉、空调等2、小型家用电器:吸尘器、电熨斗、电吹风、烤箱、钟表等3、IT及通讯仪器:计算机、传真机、电话机、手机等4、民用装置:收音机、电视机、录象机、乐器等5、照明器具:除家庭用照明外的荧光灯等,照明控制装置6、电动工具:电钻、车床、焊接、喷雾器等7、玩具/娱乐、体育器械:电动车、电视游戏机、自动赌博机等8、医疗器械:放射线治疗仪、心电图测试仪、分析仪器等9、监视/控制装置:烟雾探测器、恒温箱、工厂用监视控制机等10、自动售货机 ,它不仅包括整机产品,而且包括生产整机所使用的零部件、原材料及包装件,关系到整个生产链。
RoHS检测服务项目.

4、5、 6、 7、 8、RoHS 检测服务项目:RoHS 佥测实验室拥有符合国际标准的全套RoHS 佥测设备:气相色谱-质谱联用仪、电感耦合等离子体发射光谱仪、紫外-可见分光光度计、 能量色散X-荧光光谱仪等,为企业提供铅、汞、镉、六价铬、多溴联苯 及多溴联苯醚六种有害物质的检测和评估服务。
RoHS 佥测实验室作为第三方检测公证服务机构,我们遵循客观、求实、科学、公正的服务原则,严格 执行检测技术标准和规范、遵守保密制度,保护客户的资料,为客户提供优质、快速、准确的检测服务。
可提供的检测服务项目1.室内(车内)环境空气质量检测甲醛、氨、苯及苯系物、挥发性有机物、臭氧、二氧化硫、氮氧化物、新风量、二氧化碳、一氧化碳、微生物等。
中央空调 系统微生物污染监测。
2 .建筑和装饰材料有害物质 甲醛、挥发性有机物。
3 •工矿企业三废”污染监测工业废气、食堂油烟、污染源废气、厂界空气、工业废水、生活废水中有机、无机污染物监测分析;生产车间空气有机、无 机污染物监测分析;固体废弃物检测。
未知物剖析中心”技术人员具有多年从事该项目的经验,技术水平和能力属国内一流。
通过综合性的分离和检测手段对未知物进行定 性鉴定与定量分析,为科研及生产中新产品研发、调整产品配方、改进生产工艺提供科学依据。
/质谱联用仪(GC-MS )、红外光谱仪(IR )、凝胶GPC )等有机化学结构分析仪器,以及等离子发射光谱仪( ICP-AES )、原子吸收光谱仪、原子荧光光谱仪、 X 射线荧光光谱仪等无机分析仪器。
主要剖析业务油漆稀释剂,天那水,脱漆剂,电子、纺织、印刷行业用溶剂。
气雾剂、光亮剂、杀虫剂、脱模剂、润滑剂、致冷剂、空气清新剂。
各种助剂:电子行业(助焊剂)、纺织行业、涂料、塑料加工行业所用的助剂:乳化剂、润湿分散剂、消泡剂、阻燃剂 等;电镀(锌、铜、铬、镍、贵重金属)助剂分析:前处理添加剂、光亮剂、辅助光亮剂等。
纺织、皮革助剂分析:柔软剂、匀染剂、整理剂等。
rohs12项限制物质
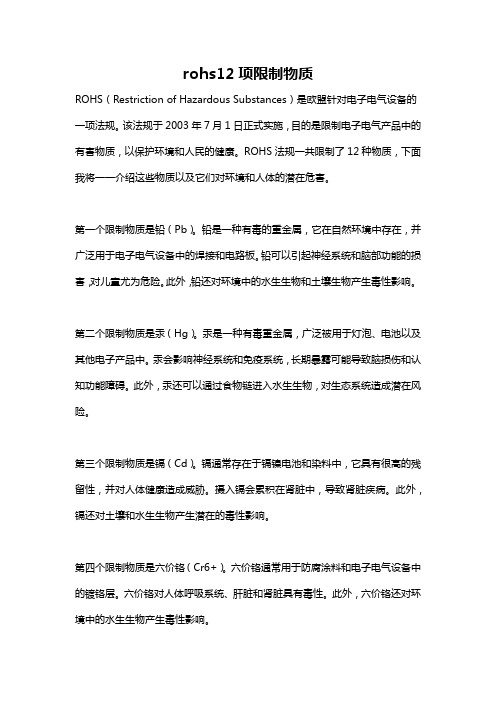
rohs12项限制物质ROHS(Restriction of Hazardous Substances)是欧盟针对电子电气设备的一项法规。
该法规于2003年7月1日正式实施,目的是限制电子电气产品中的有害物质,以保护环境和人民的健康。
ROHS法规一共限制了12种物质,下面我将一一介绍这些物质以及它们对环境和人体的潜在危害。
第一个限制物质是铅(Pb)。
铅是一种有毒的重金属,它在自然环境中存在,并广泛用于电子电气设备中的焊接和电路板。
铅可以引起神经系统和脑部功能的损害,对儿童尤为危险。
此外,铅还对环境中的水生生物和土壤生物产生毒性影响。
第二个限制物质是汞(Hg)。
汞是一种有毒重金属,广泛被用于灯泡、电池以及其他电子产品中。
汞会影响神经系统和免疫系统,长期暴露可能导致脑损伤和认知功能障碍。
此外,汞还可以通过食物链进入水生生物,对生态系统造成潜在风险。
第三个限制物质是镉(Cd)。
镉通常存在于镉镍电池和染料中,它具有很高的残留性,并对人体健康造成威胁。
摄入镉会累积在肾脏中,导致肾脏疾病。
此外,镉还对土壤和水生生物产生潜在的毒性影响。
第四个限制物质是六价铬(Cr6+)。
六价铬通常用于防腐涂料和电子电气设备中的镀铬层。
六价铬对人体呼吸系统、肝脏和肾脏具有毒性。
此外,六价铬还对环境中的水生生物产生毒性影响。
第五个限制物质是多溴联苯(PBBs)。
多溴联苯一度广泛用于塑料,如电子电气设备的外壳和线缆中。
它具有高毒性和长期残留性,对人体的神经、免疫和内分泌系统产生危害。
此外,多溴联苯还可以通过食物链进入水生生物和陆地生态系统。
第六个限制物质是多溴二苯醚(PBDEs)。
多溴二苯醚广泛用于电子产品和家具中的阻燃剂。
它们具有持久性有机污染物特征,对人体内分泌系统和神经系统产生潜在危害。
此外,多溴二苯醚还对水生生物和陆地生态系统产生毒性影响。
第七个限制物质是邻苯二甲酸酯(DEHP)。
邻苯二甲酸酯是一种常用的可塑剂,广泛应用于电子电气产品的塑料和橡胶制造中。
中国rohs测试方法
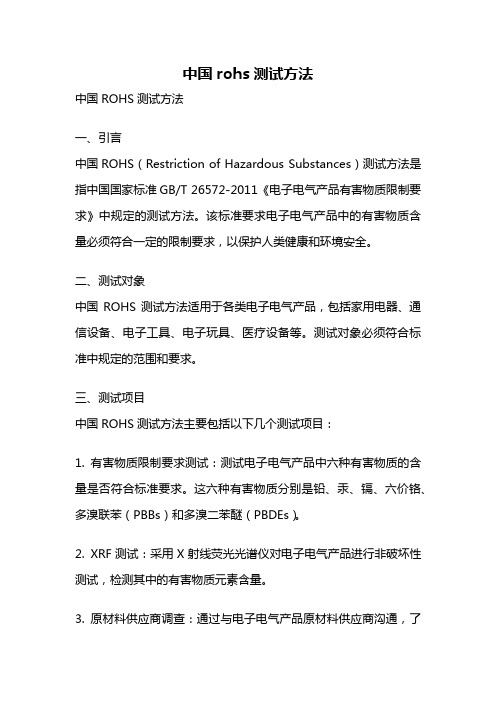
中国rohs测试方法中国ROHS测试方法一、引言中国ROHS(Restriction of Hazardous Substances)测试方法是指中国国家标准GB/T 26572-2011《电子电气产品有害物质限制要求》中规定的测试方法。
该标准要求电子电气产品中的有害物质含量必须符合一定的限制要求,以保护人类健康和环境安全。
二、测试对象中国ROHS测试方法适用于各类电子电气产品,包括家用电器、通信设备、电子工具、电子玩具、医疗设备等。
测试对象必须符合标准中规定的范围和要求。
三、测试项目中国ROHS测试方法主要包括以下几个测试项目:1. 有害物质限制要求测试:测试电子电气产品中六种有害物质的含量是否符合标准要求。
这六种有害物质分别是铅、汞、镉、六价铬、多溴联苯(PBBs)和多溴二苯醚(PBDEs)。
2. XRF测试:采用X射线荧光光谱仪对电子电气产品进行非破坏性测试,检测其中的有害物质元素含量。
3. 原材料供应商调查:通过与电子电气产品原材料供应商沟通,了解其原材料是否符合有害物质限制要求。
4. 高温烘箱测试:将电子电气产品置于高温烘箱中进行加热,测试其在高温环境下是否会释放出有害物质。
5. 高温蒸汽测试:将电子电气产品置于高温蒸汽中进行暴露,测试其在高温湿热环境下是否会释放出有害物质。
6. 持久性有机污染物(POP)测试:测试电子电气产品中是否含有持久性有机污染物,如多氯联苯(PCBs)和多氯二苯醚(PCDFs)等。
四、测试流程中国ROHS测试方法的测试流程如下:1. 收集样品:从市场或生产线上收集代表性的电子电气产品样品。
2. 样品准备:按照标准要求对样品进行准备,包括去除外包装、清洗和切割等。
3. 测试设备校准:对测试设备进行校准,确保测试结果准确可靠。
4. 测试参数设定:根据标准要求,设定测试参数,如测试温度、湿度、加热时间等。
5. 进行测试:按照测试要求,对样品进行有害物质含量测试、XRF测试、高温烘箱测试、高温蒸汽测试和POP测试等。
欧盟RoHS2.0测试10项分别是测试哪些项目
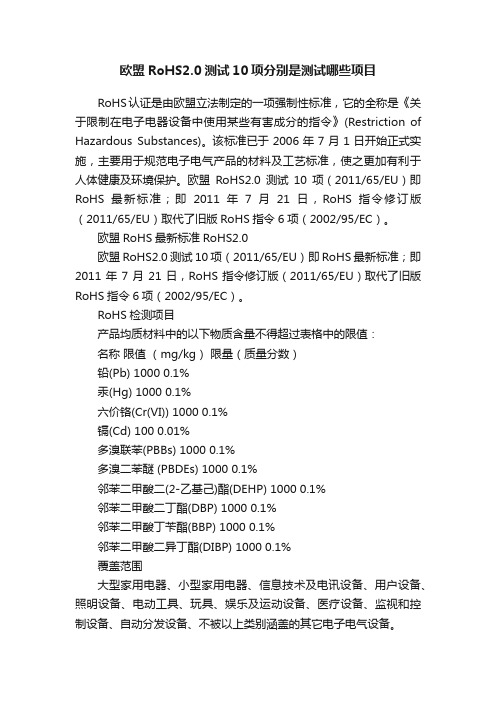
欧盟RoHS2.0测试10项分别是测试哪些项目RoHS认证是由欧盟立法制定的一项强制性标准,它的全称是《关于限制在电子电器设备中使用某些有害成分的指令》(Restriction of Hazardous Substances)。
该标准已于2006年7月1日开始正式实施,主要用于规范电子电气产品的材料及工艺标准,使之更加有利于人体健康及环境保护。
欧盟RoHS2.0测试10项(2011/65/EU)即RoHS最新标准;即2011年7月21日,RoHS指令修订版(2011/65/EU)取代了旧版RoHS指令6项(2002/95/EC)。
欧盟RoHS最新标准RoHS2.0欧盟RoHS2.0测试10项(2011/65/EU)即RoHS最新标准;即2011年7月21日,RoHS指令修订版(2011/65/EU)取代了旧版RoHS指令6项(2002/95/EC)。
RoHS检测项目产品均质材料中的以下物质含量不得超过表格中的限值:名称限值(mg/kg)限量(质量分数)铅(Pb) 1000 0.1%汞(Hg) 1000 0.1%六价铬(Cr(VI)) 1000 0.1%镉(Cd) 100 0.01%多溴联苯(PBBs) 1000 0.1%多溴二苯醚 (PBDEs) 1000 0.1%邻苯二甲酸二(2-乙基己)酯(DEHP) 1000 0.1%邻苯二甲酸二丁酯(DBP) 1000 0.1%邻苯二甲酸丁苄酯(BBP) 1000 0.1%邻苯二甲酸二异丁酯(DIBP) 1000 0.1%覆盖范围大型家用电器、小型家用电器、信息技术及电讯设备、用户设备、照明设备、电动工具、玩具、娱乐及运动设备、医疗设备、监视和控制设备、自动分发设备、不被以上类别涵盖的其它电子电气设备。
RoHS检测周期:常规测试周期为5个工作日。
RoHS检测方法:针对美国和欧盟RoHS以及全球其他市场,采用IEC 62321系列标准进行测试;针对中国RoHS,采用GB/T 26125测试方法。
- 1、下载文档前请自行甄别文档内容的完整性,平台不提供额外的编辑、内容补充、找答案等附加服务。
- 2、"仅部分预览"的文档,不可在线预览部分如存在完整性等问题,可反馈申请退款(可完整预览的文档不适用该条件!)。
- 3、如文档侵犯您的权益,请联系客服反馈,我们会尽快为您处理(人工客服工作时间:9:00-18:30)。
95.0
(首选)电子电气设备中使用的材料(RoHS检测)
化学分析实验室
六价铬
IEC 62321:2008
4.0
150.0
(首选)电子电气设备中使用的材料(RoHS检测)
化学分析实验室
镉
IEC 62321:2008
4.0
95.0
(首选)电子电气设备中使用的材料(RoHS检测)
化学分析实验室
汞
IEC 62321:2008
RoHS金属材料-检测项目整合列表
金属材料是指金属元素或以金属元素为主构成的具有金属特性的材料的统称。包括纯金属、合金、金属材料金属间化合物和特种金属材料等。(注:金属氧化物(如氧化铝)不属于金属材料)
套餐名:RoHS金属材料
项目名称
标准名称
检测周期
检测价格
适用产品范围
检测实验室
铅
IEC 62321:2008
4.0
95.0
(首选)电子电气设备中使用的材料(RoHS检测)
化学ቤተ መጻሕፍቲ ባይዱ析实验室