16.7F绝缘真空浸漆工艺守则
浸漆工表面处理作业安全技术操作规程

浸漆工表面处理作业安全技术操作规程第一章总则
第一条为了保障浸漆工表面处理作业的安全和顺利进行,保护作业人员的人身安全和财产安全,本规程制定。
第二章尺限
第二条浸漆工表面处理作业是指对工件、产品的表面进行处理的工艺过程。
包括喷砂、喷漆、喷涂、喷镀等表面处理方法。
第三章组织
第三条每个浸漆工表面处理作业单位应当建立相应的安全技术操作规程,并定期进行培训,使每个作业人员熟悉安全操作规程。
第四章岗位
第四条每个浸漆工表面处理作业单位应当设立明确的岗位职责和操作流程。
第五章安全设施
第五条每个浸漆工表面处理作业单位应当配备相应的安全设施,包括通风系统、防爆设施、个体防护设备等。
第六章作业规范
第六条每个浸漆工表面处理作业人员应当按照规定的工艺和操作流程进行作业,严禁擅自修改和调整操作参数。
第七章安全检查
第七条每个浸漆工表面处理作业单位应当定期进行安全检查,发现问题及时整改。
第八章突发事件应急处置
第八条每个浸漆工表面处理作业单位应当制定相应的应急预案,熟悉安全抢险操作流程。
第九章禁止事项
第九条禁止将易燃易爆物品带入作业现场;禁止在作业现场吸烟、乱丢废弃物品等行为。
第十章违章处罚
第十条对于违反本规程的浸漆工表面处理作业人员,应当按照相应的违章处罚措施进行处理。
第十一章附则
第十一条本规程适用于所有浸漆工表面处理作业单位,每个单位应根据自身情况进行相应的调整和完善。
现将浸漆工表面处理作业安全技术操作规程进行如上制定。
2-绝缘浸漆操作规程
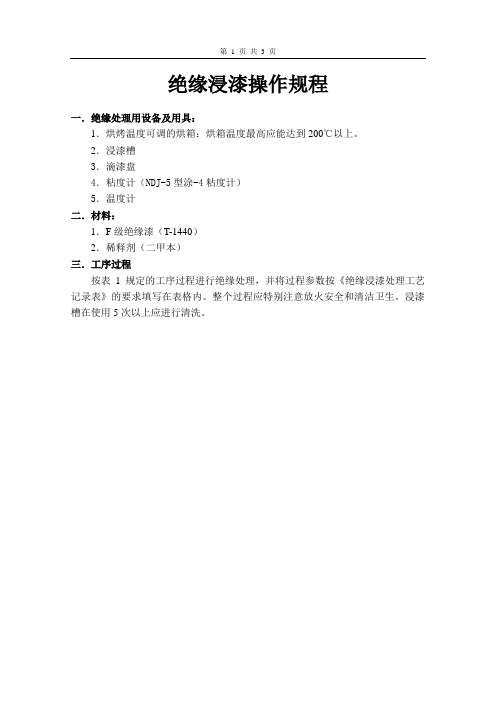
洪 干
1.工件(线圈,机芯)全部滴干后,放入烘箱内。
2.关闭烘箱门,打开电源。
3.升温至80±5℃,恒温1小时。
4.升温至90±5℃,恒温1小时。
5.升温至100±5℃,恒温1小时。
6.升温至120±5℃,恒温1小时。
7.升温至150±5℃,恒温1小时。
8.断开电源,将温控器调至70℃,确保安全。
表1
序号
项目
内容
一
预热工序
1.工件(线圈,机芯)放在烘箱的架子上。
2.清理灰尘,油污。
3.检验烘箱是否工作正常。
4.将放入烘箱的工件(线圈,机芯)型号,数量记录详细。
5.合上开关,温度控制在110℃~120℃。
6.温度控制在110℃~120℃。,烘焙2~3小时。
二
冷却工序
1.将烘箱断电,打开烘箱门使工件(线圈,机芯)自然冷却到50℃~60℃。
28
22
∣
26
20
∣
24
18
∣
22
16
∣
20
14
∣
18
2.把漆搅拌均匀,并测量漆周围的室温。
3.用粘度计测量漆的粘度,至少测两次。
4.按表2要求调好粘度。
三
浸漆工序
1.将工件(线圈,机芯)慢慢放入浸漆槽内。
2.漆表面要高于工件(线圈,机芯)上表面100~200mm。
3.浸漆到不再产生气泡为止,但是时间不得少于15分钟。
4.将工件(线圈,机芯)取出进行滴漆,到没有余漆下流为止,但不得少于8小时。
9.自然冷却至80℃以下可开烘箱门。
10.取出工件(线圈,机芯)。
表2
F级绝缘漆粘度对照表
常温℃
F级绝缘浸漆工艺守则

F级绝缘浸漆工艺守则1范围本标准规定了隔爆型三相异步电动机F级绝缘浸漆材料、设备与工具、工艺准备、工艺过程、质量检查和注意事项等内容。
本标准适用于机座63~355隔爆型电机绕组真空浸漆绝缘处理。
2材料2.1 浸漆材料:1140-U型不饱和聚酯无溶剂浸漆树脂(F级)或1140-E型环氧树脂无溶剂浸漆树脂(F级)。
2.2 稀释、清洗材料:苯乙烯(95%)。
3设备与工具3.1 烘房:工作温度范围可控制为50℃~150℃,最大温度不超过±5℃,设备配有强迫循环通风,控制温度及测量工件绝缘电阻的装置。
3.2 浸漆用设施:浸漆罐、贮漆罐、真空泵、调合罐、抽真空脱气保管罐、泵及过滤3.3 浸漆干燥专用工位器具。
3.4 搬运工具:平车、吊车等。
3.5 仪表:温度、测量或记录仪、粘度计(4号杯)、秒表、酒精温度计(0℃~100℃)、500V兆欧表。
3.6 净化绕组绝缘设备:吹风机(或空气压缩机、吸尘器)。
3.7 刮漆工具:铲刀、刮刀等。
4工艺准备4.1 检查所用材料、设备、装置、计量仪和有关器具应符合使用要求。
4.2 检查有绕组定子铁心其绕组端部绝缘不应有损伤和污迹,对引出线破坏、线圈碰伤、露铜、槽楔滑出、绑扎松开等工件应予以修整。
4.3 用吹风机(或空气压缩机、吸尘器)清理工件内、外表面。
4.4 配漆4.4.1 将单组份无溶剂浸渍树脂倒入漆缸,对采用双组份或多组份浸渍树脂应按规定比例将各组份搅拌均匀后再倒入漆缸,或将各组份倒入漆缸用搅拌工具搅拌,并应保证均匀。
4.4.2 测量绝缘漆的粘度:先用温度表测量漆温,然后用粘度计(4号杯)测量漆的粘度(在漆面下约100mm处取样二次,求平均值)并调节到规定的数值做好记录。
查对漆的粘温关系,对应23℃±1℃时;第一次浸漆:20s~35s第二次浸漆:30s~45s15 工艺过程5.1 白坯预烘;5.1.1 将待预烘的工件装上平车,注意每批预烘的有绕组定子铁心其规格应接近,尺寸较大的工件应堆放在干燥条件较好的位置,工件堆放的方位和数量应不防碍烘房内良好通风和温度均匀。
真空浸漆操作规程

真空浸漆操作规程
1.操作人员在工作时,必须使用规定发放的劳保用品。
2.非操作人员未经许可,不准进入工作场地。
3.工作场地应通风良好、清洁干燥、道路畅通,绝缘漆应放置干凉通风处。
4.经常检查浸烘罐底部坑地,如有积水应及时排放。
5.操作人员在作业时严格遵守工艺守则,按“绝缘处理记录卡”认真记录,仔细观察控制台各种数据,如有异常,及时停机处理。
6.一号真空泵在工作前必须检查是否有水,油杯油位高度应占油杯高度1/2以上。
真空泵起动前先开水阀,开油杯阀,开一号真空泵进气阀,关进气口排气阀。
真空泵停机前,关一号真空泵进气阀,开一号真空泵排气阀排气,停泵,关油杯阀,10分钟后关水阀(进水总阀、真空泵冷却水阀)。
二号真空泵启动前稍微开二号真空泵排气阀。
7.浸烘罐停机工作一星期时,必须对储漆罐抽真空,抽真空至压力表显示为-0.07Mpa,打开液位指示底阀,对储漆罐内浸渍漆搅拌5分钟。
8.维修人员必须按真空泵使用说明书规定进行定期保养和维护。
9.浸渍漆粘度增加时,一般添加新漆,不允许随便加稀释剂。
10.在冬天停机时,水管应放水防冻。
11.操作人员每月必须对全部仪器、容器、管道及真空泵进行清理,去除油污、漆污、灰尘等。
16.7F绝缘真空浸漆工艺守则
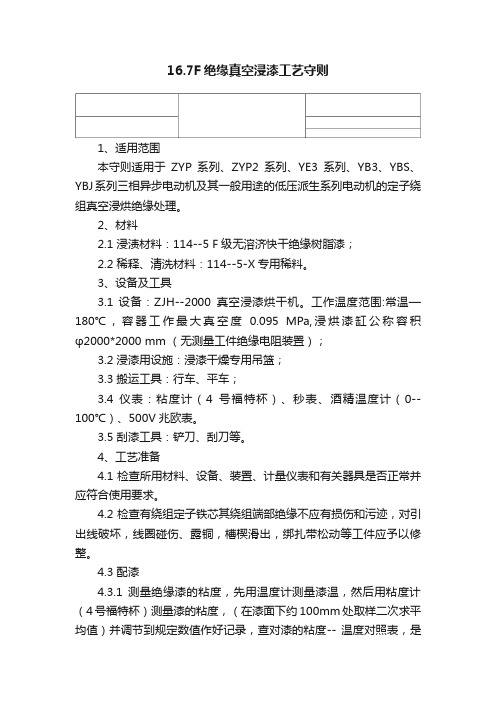
16.7F绝缘真空浸漆工艺守则1、适用范围本守则适用于ZYP系列、ZYP2系列、YE3系列、YB3、YBS、YBJ系列三相异步电动机及其一般用途的低压派生系列电动机的定子绕组真空浸烘绝缘处理。
2、材料2.1 浸渍材料:114--5 F级无溶济快干绝缘树脂漆;2.2 稀释、清洗材料:114--5-X专用稀料。
3、设备及工具3.1 设备:ZJH--2000真空浸漆烘干机。
工作温度范围:常温—180℃,容器工作最大真空度0.095 MPa,浸烘漆缸公称容积φ2000*2000 mm (无测量工件绝缘电阻装置);3.2 浸漆用设施:浸漆干燥专用吊篮;3.3 搬运工具:行车、平车;3.4 仪表:粘度计(4号福特杯)、秒表、酒精温度计(0--100℃)、500V兆欧表。
3.5 刮漆工具:铲刀、刮刀等。
4、工艺准备4.1 检查所用材料、设备、装置、计量仪表和有关器具是否正常并应符合使用要求。
4.2 检查有绕组定子铁芯其绕组端部绝缘不应有损伤和污迹,对引出线破坏,线圈碰伤、露铜,槽楔滑出,绑扎带松动等工件应予以修整。
4.3 配漆4.3.1 测量绝缘漆的粘度,先用温度计测量漆温,然后用粘度计(4号福特杯)测量漆的粘度,(在漆面下约100mm处取样二次求平均值)并调节到规定数值作好记录,查对漆的粘度-- 温度对照表,是否相符。
5、工艺过程5.1 白坯预烘5.1.1 将待预烘的工件装上吊篮,应注意每批预烘的有绕组定子,其规格应接近。
5.1.2 将装有待烘工件的吊篮分别放入浸烘罐中,将浸烘罐加盖封闭,开始加热预烘去潮,温度达到100℃开始抽真空,真空度达0.095 MPa ,抽真空时间30min 左右,停止加热保温,每隔0.5-1h用500V 兆欧表测量绝缘电阻,直到绝缘电阻升高并连续稳定为止。
绝缘电阻值和预烘时间按表1之规定。
5.2 真空压力浸漆5.2.1 待浸渍罐温度降到40-45℃时,保持最大真空度,将贮存灌中绝缘漆放入浸渍罐中(开启阀门时先小后大,以防漆冲入真空泵),待工件全部浸入漆中(漆面应高出工件表面100mm 左右)。
真空浸漆烘干操作规程

真空浸漆烘干操作规程一、工艺准备1、先用棉布蘸酒精将定子外表面擦拭干净。
2、用测量杯把漆从储漆罐内取出,用温度计检测绝缘漆的温度用,4#粘度计检测粘度,粘度误差范围±2s。
对照“漆温度-粘度对照表”要求,加适量稀释剂调整。
3、检查有绕组定子铁芯,其绕组端部绝缘不应有损伤和污迹,对引出线损坏、线圈碰伤、露铜、槽楔滑出、绑扎带松开等工件,应予以修整。
4、用吹风机清理干净定子内、外表面。
二、工艺过程1、预烘:把定子放入浸漆缸内关闭缸盖,打开1号阀门和2号阀门。
启动风机,等风机运行2分钟后在启动电热器。
升温到60-80度后保温30分钟,停止加热。
2、浸漆:等缸内温度降到50度后关闭风机同时关闭1号和2号阀门。
起动真空泵抽缸内真空,待缸内真空度达到-0.08Mpa以下关闭真空泵,打开输漆阀输漆至工件上方至少50mm,关闭进漆阀,真空度-0.08Mpa以下浸漆5分钟后解除真空。
解除真空后,常压浸漆至少5分钟。
3、回漆:起动真空泵抽储漆灌抽真空打开回漆阀门,回漆完成后关闭真空泵。
4、滴干:滴净定子上的余漆,滴漆时间至少在60-90分钟,滴漆完成后将滴下余漆抽回储漆灌。
5、清洗:打开清洗灌阀门,输入稀释剂于浸漆缸底部浸泡5-10分钟,完成浸泡缸底后起动真空泵抽稀释剂储存灌真空,打开清洗阀门将稀释剂抽回稀释剂储存灌内。
抽完稀释剂后关闭真空泵。
6、固化:打开1号和2号阀门,启动风机,等风机运行2分钟后在启动电热器,浸漆缸温度达到140度,保温3.5-4小时。
保温完成后关闭电热器,待缸内温度降到100度以下后,开启缸盖取出定子。
三、注意事项1、每次浸漆前都要进行检查和调整漆的粘度。
2、定子预烘后浸漆时定子温度不能高于45度,否则引起漆的胶凝。
3、烘干过程中,不允许打开炉门。
如停电,温度降低应延长时间,保证烘干。
4、工作场地严禁烟火,保持清洁,配备消防灭火装置。
5、要严格执行工艺参数,并做好过程工艺参数监控记录。
真空浸漆或真空压力浸漆
真空浸漆或真空压力浸漆(VPI)工艺规程1 适用范围本工艺适用于B、F、H级交直流电机绕组绝缘和半成品电机绝缘的浸漆。
2 浸漆材料2.1通用7122 无溶剂快干树脂2.2稀释剂:苯乙烯要求:浸漆材料进厂时,需要有产品合格证和使用说明书及检验报告。
3工艺准备3.1 设备检查:检查设备、仪器、仪表等是否正常。
3.2 配漆:单组分包装时可直接加入漆槽;双组分包装时,将甲、乙组份加入漆槽中并搅拌均匀,加入比例为1大桶甲组分(180KG)配1小桶乙组分(12KG)。
3.3 调节粘度:配好的漆应保持粘度在30~80秒(20℃,4#粘度杯),如粘度大于80秒最好加入新漆稀释,或加5~10%稀释剂调节。
3.4 凝胶时间:应该不大于15分钟,一般保持在2~8分钟(140℃),当凝胶时间小于2分钟时,应向技术负责人报告。
2.5 工件检查:检查待浸工件是否经试验合格,绕组及绝缘有无损伤,工件表面是否洁净等。
4 工艺过程4.1普通浸漆4.1.1 预烘:将工件推入干燥炉升温至120℃取出冷却,干燥炉继续升温至150℃保温。
4.1.2 浸漆:待工件冷却至表面温度小于40℃(如无表面温度计以手触摸工件表面不烫手为宜)后即可放入浸漆槽浸漆,工件浸入液面下至少10cm,浸漆时间不少于30分钟,至无气泡冒出。
4.1.3 滴干:将工件取出滴干不少于30分钟,至无漆液滴下。
4.1.4 干燥:工件余漆经清理后(需要时)推入干燥炉中,干燥炉温度设定为150℃,待炉温升至140℃以上后2小时开始每隔1小时测一次热态绝缘电阻,待绝缘电阻稳定在1MΩ上1小时以后方可出炉,根据工件大小,此时间参数一般为150℃3~6小时。
5.2 VPI浸漆工艺5.2.1预烘:将工件推入干燥炉升温至100℃~130℃,保温2~4小时,取出冷却至50℃以下进罐。
注意工件浸入液面下至少10cm。
5.2.2真空去湿5.2.2.1手动扳开(1)号压缩空气阀,在工控机上开(30)号密封圈充气阀,进行工件真空去湿。
真空浸漆设备操作规程
真空浸漆(VDI)设备操作规程1合上电源1.1按照《真空泵使用说明书》检查真空泵是否在正转状态。
1.2检查液压泵是否在正转(顺时针)状态。
2绝缘漆的加注2.1启动真空泵,开4#真空总阀、9#储漆罐真空阀,对储漆罐抽真空;当真空表示数达到-0.08~0.096MPa时,关闭4#真空总阀,停真空泵,打开3#阀门,进入空气后及时关闭。
2.2用带钢丝的软管套在7#储漆罐放空阀的接管上,打开7#阀对储漆罐进行加1040酚醛改性聚酯浸渍漆。
在加漆过程中,注意真空度低于-0.06MPa时,应关闭7#储漆罐放空阀,启动真空泵,开4#真空总阀。
待当真空度至-0.09MPa时,关闭4#真空总阀,停真空泵,打开3#阀门,进入空气后及时关闭。
然后开7#阀,继续加漆至储漆罐玻璃计液位上限的2/3为止。
3稀释剂的加注3.1启动真空泵,开4#真空总阀、19#清洗回收缸真空阀,对清洗回收缸抽真空;当真空表示数达到-0.08~0.096MPa时,关闭4#真空总阀,停真空泵,打开3#阀门,进入空气后及时关闭。
3.2用带钢丝的软管套在14#清洗回收缸放空阀的接管上,打开14#阀对清洗回收缸进行加稀释剂二甲苯。
在加清洗剂过程中,注意真空度低于-0.06MPa时,应关闭14#清洗回收缸放空阀,启动真空泵,开4#真空总阀。
待当真空度至-0.09MPa时,关闭4#真空总阀,停真空泵,打开3#阀门,进入空气后及时关闭。
然后开14#阀,继续加清洗剂至清洗回收缸玻璃管上限的2/3为止。
4操作流程(以A缸为例)4.1抽真空去湿启动液压泵,松开浸漆缸缸盖上的锁紧卡口,开盖;,将工件置于浸漆缸中,合上缸盖,锁紧卡口。
开盖及关盖时一人操作,避免多人操作时误操作开4#真空总阀、A5#浸漆缸真空阀,启动真空泵,对(A)浸漆缸抽真空;当真空表示数达到-0.08~0.096MPa时,延时约1分钟后关闭4#真空总阀,停真空泵;打开3#阀门,进入空气后及时关闭,根据工件大小及线圈线径保持真空约5分钟~30分钟。
真空含浸工艺规范
电子器件真空含浸工艺规程本规程适用于电子器件真空含浸,以达到绝缘防潮,提高机械强度等性能。
1设备、仪表、工具设备:QF-620真空含浸设备,QFHD 3000×940红外线恒温烘道。
仪表:密度计工具:帆布手套、瓷缸、单面刀片、毛刷2材料J13快干漆J13专用稀释剂3工艺准备J13快干漆甲乙两组,分别按1:1的比例配兑后,加入J13稀释剂用调料棒搅拌均匀。
用密度计测量漆液粘度,需要达到0.86~0.9之间范围。
启动真空含浸设备、红外线烘道电源。
红外线烘道温度设置在110±10度。
4工艺过程将产品整齐摆放在浸筛上,关闭真空含浸设备顶盖,并确保处于密闭状态。
开启真空阀门、漆槽阀门,启动真空泵,将漆液从漆槽吸入漆缸使用漆液高于线圈并低于产品插针根部。
待漆液适量后关闭阀门,继续抽真空,待气压升到0.04~0.06MPa后,停止抽真空。
保持真空3秒后打开气压阀门,让漆缸内气压恢复到正常气压。
开启漆槽阀门,让漆液回到漆槽后关闭漆槽阀门、大气阀门,开启真空阀门,再次启动真空泵,二次真空时间为60秒,然后停止工作真空泵,关闭真空阀门。
开启大气阀门漆缸内大气压恢复正常后打开设备顶盖,取出产品摆放在漆架上滴尽漆滴。
若磁芯表面未浸上漆,可用毛笔刷浸漆后均匀涂抹在磁芯表面。
浸漆后的产品,单层整齐摆放在筛网上,产品不能重叠,以避免产品无法全部烘干。
将滴尽漆滴的产品放入已经预热的红外线烘道进行烘烤,烘烤时间为40~60分钟。
烘干后的产品摆放到周转盒内,检查产品插针和骨架支撑点处不能有漆瘤。
检查合格的产品注入下一道工序。
5注意事项5.1配漆比例、漆液浓度、产品烘干时间、烘烤温度应严格遵守工艺参数。
5.2作好相关的参数记录,每4小时检查一次烘道温度。
5.3下班前关闭电源,待温度降到60度以下,方可离开。
5.4按照设备保养要求定期设备保养维护。
编制:核准:日期:2011-3-1。
真空浸漆设备操作规范
SHENZHEN YAMAXI ELECTRONICS CO., LTD.
DOC.NO 文件编号: YMXTBPE-0006 TITLE:
题 目:真空浸漆设备安全操作规范
真空浸漆设备操作规范:
一、目的:建立此文件旨在正常,合理,安全的使用机器,保证产品浸漆质量,保障人
员安全,合理维护,保障机器使用寿命及可靠性。
拟制: 日期: 审核: 日期: 批准: 日期:
第 2 页,共 2 页
真空浸漆设备操作规范:
1、真空浸漆设备,使用的绝缘漆及有机溶液,均为易燃易爆物品,生产现场严禁烟 火。如有发现严重处理当事人及现场管理人员。 2、操作设备前务必认真学习设备使用说明书,使用及检修此设备的人员,必需为设 备供货方培训合格的人员且专人操作。设备发生非正常情况时应立即查清原因,并排除 故障,记录台账、确认正常后方可使用。 3、定期对真空泵进行加油。真空泵使用参照真空泵使用说明书,并注意真空泵旋转 方向,并注意真空泵旋转方向,冷却水量应充足,最佳温度为15℃以下。气温低于0℃时 应放水防冻。 4、检查液压油油箱内油面高度;液压泵是否在正转(顺时针)状态。 5、使用前检查各管道是否存在堵塞现象。 6、储漆罐玻璃计液位不超过液位中心线2/3。
第 1 页,共 2 页
深圳市雅玛西电子有限公司
SHENZHEN YAMAXI ELECTRONICS CO., LTD.
DOC.NO 文件编号: YMXTBPE-0006 TITLE:
题 目:真空浸漆设备安全操作规范
7、观察清洗剂的颜色和储量,调整清洗剂储罐内溶剂液的高度,以防清洗剂不足锥 底平面清洗不完全;颜色太深时及时更换。 8、检查控制柜指示灯是否正常;检查真空表和油压表是否工作正常。 9、每班生产后,对浸漆缸和管路应及时清洗。设备停用10日以上,应开机检查疏通 管路。 10、操作人员必须佩带防、适用范围:真空浸漆设备
- 1、下载文档前请自行甄别文档内容的完整性,平台不提供额外的编辑、内容补充、找答案等附加服务。
- 2、"仅部分预览"的文档,不可在线预览部分如存在完整性等问题,可反馈申请退款(可完整预览的文档不适用该条件!)。
- 3、如文档侵犯您的权益,请联系客服反馈,我们会尽快为您处理(人工客服工作时间:9:00-18:30)。
1、适用范围
本守则适用于ZYP系列、ZYP2系列、YE3系列、YB3、YBS、YBJ系列三相异步电动机及其一般用途的低压派生系列电动机的定子绕组真空浸烘绝缘处理。
2、材料
2.1 浸渍材料:114--5 F级无溶济快干绝缘树脂漆;
2.2 稀释、清洗材料:114--5-X专用稀料。
3、设备及工具
3.1 设备:ZJH--2000真空浸漆烘干机。
工作温度范围:常温—180℃,容器工作最大真空度0.095 MPa,浸烘漆缸公称容积φ2000*2000 mm (无测量工件绝缘电阻装置);
3.2 浸漆用设施:浸漆干燥专用吊篮;
3.3 搬运工具:行车、平车;
3.4 仪表:粘度计(4号福特杯)、秒表、酒精温度计(0--100℃)、500V兆欧表。
3.5 刮漆工具:铲刀、刮刀等。
4、工艺准备
4.1 检查所用材料、设备、装置、计量仪表和有关器具是否正常并应符合使用要求。
4.2 检查有绕组定子铁芯其绕组端部绝缘不应有损伤和污迹,对引出线破坏,线圈碰伤、露铜,槽楔滑出,绑扎带松动等工件应予以修整。
4.3 配漆
4.3.1 测量绝缘漆的粘度,先用温度计测量漆温,然后用粘度计(4号福特杯)测量漆的粘度,(在漆面下约100mm处取样二次求平均值)并调节到规定数值作好记录,查对漆的粘度-- 温度对照表,是否相符。
5、工艺过程
5.1 白坯预烘
5.1.1 将待预烘的工件装上吊篮,应注意每批预烘的有绕组定子,其规格应接近。
5.1.2 将装有待烘工件的吊篮分别放入浸烘罐中,将浸烘罐加盖封闭,开始加热预烘去潮,温度达到100℃开始抽真空,真空度达0.095 MPa ,抽真空时间30min 左右,停止加热保温,每隔0.5-1h用500V兆欧表测量绝缘电阻,直到绝缘电阻升高并连续稳定为止。
绝缘电阻值和预烘时间按表1之规定。
5.2 真空压力浸漆
5.2.1 待浸渍罐温度降到40-45℃时,保持最大真空度,将贮存灌中绝缘漆放入浸渍罐中(开启阀门时先小后大,以防漆冲入真空泵),待工件全部浸入漆中(漆面应高出工件表面100mm 左右)。
待液面无气泡冒出后解除真空,将漆抽回贮存灌。
参数见表1。
5.3 滴漆
5.3.1 浸渍后的工件必须按表1规定的时间进行滴漆,然后用清洗罐中的全部清洗剂清洗浸渍罐底部滴下的余漆,清洗完毕解除真空抽回清洗剂。
5.4 烘焙
5.4.1 升温:当温度升到100℃时,停止加热,抽真空30min 。
5.4.2 继续加热固化,当温度达到140±5℃时,保温1.5--3 h (烘焙干燥时间绝缘电阻的测定按表1规定执行),停止加热,待温度降至100℃左右时,开盖吊出吊篮。
5.4.3 工件出炉出检查其内、外表漆膜是否均匀,如有漆瘤及漆膜过厚影响装配时,应趁热铲除漆瘤或刮漆,同时应分开引接线。
6、质量检查
6.1 预烘、浸漆、滴漆、烘焙的工艺参数应符合表1之规定,其绝缘电阻应符合要求。
6.2 烘干后绕组表面漆膜色泽均匀一致,手触漆膜应不粘手,并稍有弹性,表面无裂纹和皱纹,其端部无变形,端部铜线无磕碰、露铜、引接线分开,槽楔无错位。
6.3 工件干燥后,经检验人员检验合格,并在浸烘记录上签字后方可转入下道工序。
7、安全注意事项
7.1 浸漆场所应保持通风良好,清洁干净。
严禁烟火及堆放易燃物品,并备有必要的消防器
7.2 使用真空设备,车间内应闻不到溶剂气味,如果发现有溶剂气味,应立即检查设备各阀门有无泄漏,并予以排除。
7.3 电器控制系统及电机每班使用时,注意其运行情况,如发现异常或停电、停机时,必须立即关闭阀(1),打开阀(2)。
防止可燃气体串入加热器发生危险。
7.4 加热器通电前,必须先启动鼓风机3--5min ,将混入热风机中溶剂气体吹散,然后再开加热器,加热时进口温度应低于350℃,防止爆炸事故发生。
7.5 测量绝缘漆粘度。
添加绝缘漆或溶剂时,必须停止使用加热器,以免发生危险。
7.6 班时情况是否正常,绝缘漆是否符合要求,数量是否足够,清洗剂中绝缘漆含量是否过高。
应放完冷凝器、捕集器、换热器、缓冲器等容器中积液;冷却水是否畅通;热风机、导风管、废气排入管有无堵塞等。
如有应及时清理,畅通后方可使用。
7.7 当班操作人员不得擅自离开工作岗位,以免发生意外。
8、电压为1140V的YB3系列电机定子、所有变频电机定子需经二次浸漆。
114-5F级无溶剂快干绝缘树脂漆
粘度——温度对照表
(4号福特杯)
F级绝缘漆一次真空压力浸渍、干燥工艺参数。