球化处理工艺
球墨铸铁的球化与孕育处理工艺
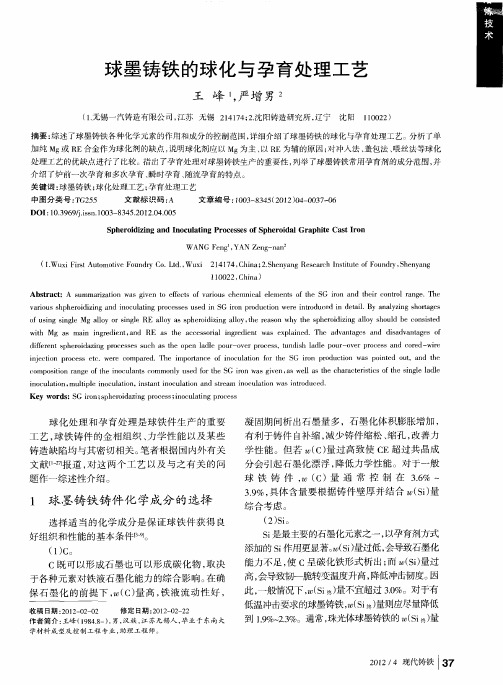
( )。 5 S
c 强烈促进形成碳化物, r 稳定珠光体 。 r c 的 加 入能提 高强 度 和硬 度 , 加 入量 以不 出现 游离 但
碳 化物 为 限 , 于高 韧性铁 素 体球 墨铸 铁要 严 格 对
限 制 ( r 量 。对 于珠 光 体 球 墨 铸 铁 , C) 当加 入 ( r量 02 03 C ) .%~ . %时 , 即可起 到 显 著 的稳 定 珠
10 2 ) 10 2
摘要 : 综述 了球墨铸铁各种化学元素的作 用和成分 的控制范 围, 细介绍 了球墨铸铁 的球化与孕育处理工艺 。 详 分析 了单 加 纯 Mg R 或 E合金作为球化剂的缺点 , 明球化剂应 以 Mg为主 、 R 说 以 E为辅 的原 因 ; 对冲入法 、 盖包法 、 喂丝法等球化 处理工 艺的优缺点进行 了比较 。 出了孕育处理对球墨铸铁生产的重要性 , 指 列举 了球墨铸铁 常用孕育剂的成分范围, 并 介绍 了炉前一次孕育和多次孕育 、 瞬时孕育 、 随流孕育的特点 。 关键词 : 球墨铸铁 ; 球化处理工艺 ; 孕育处理工艺 中图分类号 :G 5 T 25 文献标 识码 : A 文章编号 :0 3 84 (0 2 0 — 0 7 0 10 — 3 5 2 1 )4 0 3 — 6
往需要 进行脱 S处理 ;感 应 电炉熔 炼 由于不用焦 炭, 原铁液 州 S量一般在 0 1% ̄ . %。 () . 5 0 3 不需要进 0 0
R E元 素 中和 , 则会 引起球 化不 良。 E与 s 否 R b并
用 还可 以改 善大 断面件 的球 化 。
( 1微量 干扰 元素 。 1) 球 墨铸 铁 中常存 在 一 些 非 特 意加 入 的微 量
球墨铸铁的球化与孕育处理工艺
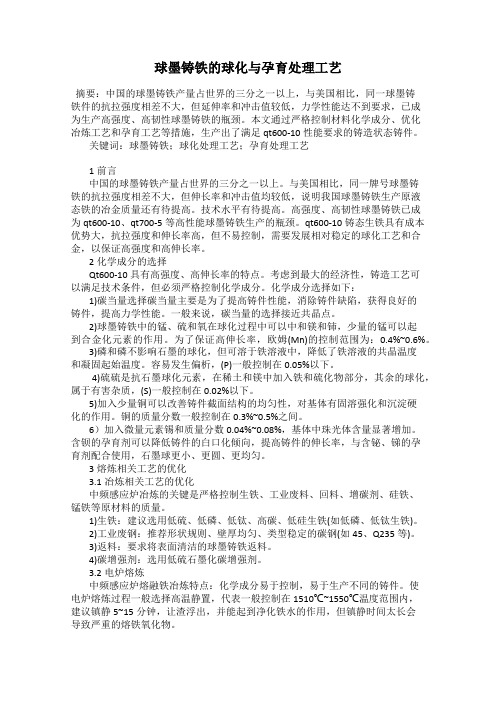
球墨铸铁的球化与孕育处理工艺摘要:中国的球墨铸铁产量占世界的三分之一以上,与美国相比,同一球墨铸铁件的抗拉强度相差不大,但延伸率和冲击值较低,力学性能达不到要求,已成为生产高强度、高韧性球墨铸铁的瓶颈。
本文通过严格控制材料化学成分、优化冶炼工艺和孕育工艺等措施,生产出了满足qt600-10性能要求的铸造状态铸件。
关键词:球墨铸铁;球化处理工艺;孕育处理工艺1前言中国的球墨铸铁产量占世界的三分之一以上。
与美国相比,同一牌号球墨铸铁的抗拉强度相差不大,但伸长率和冲击值均较低,说明我国球墨铸铁生产原液态铁的冶金质量还有待提高。
技术水平有待提高。
高强度、高韧性球墨铸铁已成为qt600-10、qt700-5等高性能球墨铸铁生产的瓶颈。
qt600-10铸态生铁具有成本优势大,抗拉强度和伸长率高,但不易控制,需要发展相对稳定的球化工艺和合金,以保证高强度和高伸长率。
2化学成分的选择Qt600-10具有高强度、高伸长率的特点。
考虑到最大的经济性,铸造工艺可以满足技术条件,但必须严格控制化学成分。
化学成分选择如下:1)碳当量选择碳当量主要是为了提高铸件性能,消除铸件缺陷,获得良好的铸件,提高力学性能。
一般来说,碳当量的选择接近共晶点。
2)球墨铸铁中的锰、硫和氧在球化过程中可以中和镁和铈,少量的锰可以起到合金化元素的作用。
为了保证高伸长率,欧姆(Mn)的控制范围为:0.4%~0.6%。
3)磷和磷不影响石墨的球化,但可溶于铁溶液中,降低了铁溶液的共晶温度和凝固起始温度。
容易发生偏析,(P)一般控制在0.05%以下。
4)硫硫是抗石墨球化元素,在稀土和镁中加入铁和硫化物部分,其余的球化,属于有害杂质,(S)一般控制在0.02%以下。
5)加入少量铜可以改善铸件截面结构的均匀性,对基体有固溶强化和沉淀硬化的作用。
铜的质量分数一般控制在0.3%~0.5%之间。
6)加入微量元素锡和质量分数0.04%~0.08%,基体中珠光体含量显著增加。
关于球墨铸铁球化处理工艺的探讨 高才炜
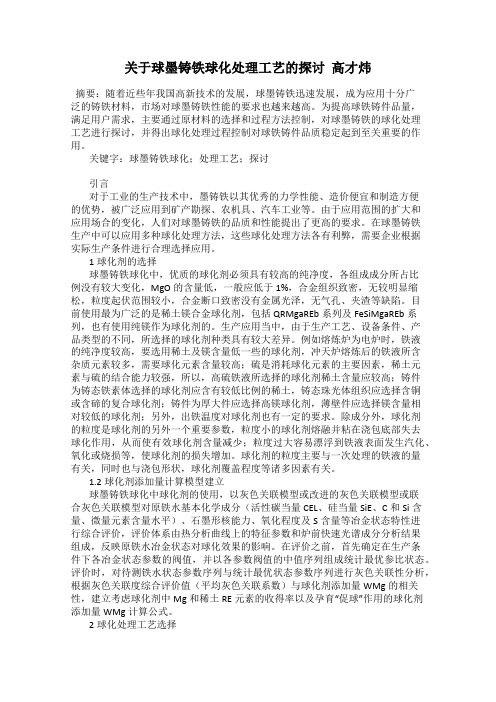
3.1原、辅材料选择
球磨铸铁对于原材料的选择过程中,熔炼高韧性球墨铸铁的主要材料是废钢(低碳钢)、增碳剂、硅铁、回炉料、球化剂、孕育剂等。原材料应无油、无锈、低锰、低硫、成分明确。
3.2熔炼操作
接下来的熔炼操作需要按比例称料,然后按顺序向中频电炉内加料,加料顺序为:回炉料→废钢→增碳剂→硅铁→回炉料→废钢。送电开始熔炼。全部炉料添加完毕,升温至1480~1500℃,增碳时间5~10min,扒渣取样进行光谱分析。若成分符合原铁液成分要求,调至1430~1470℃的工艺温度,开始出铁球化处理。若成分不满足要求,按比例调整成分,取样化验,直至满足要求为止,升温至工艺要求的球化温度出铁。
2.2冲入法
儿冲入法是在我国当前的工业技术中最广泛的球化处理方法,通常是使用堤坝式球化处理包。为了降低铁液和镁之间反应的剧烈程度以及镁蒸气的挥发速率,冲入法通常使用含镁量较低的合金球化剂。冲入法在所有球化处理方法当中具有高的应用比例,主要原因为设备成本低、处理方法简单、对操作的要求较低,不需要复杂的技术支持,生产过程比较灵活。冲入法的不足之处在于生产环境恶劣,并造成严重污染。同时球化合金的效率低,烧损严重,造成资源浪费。另外,冲入法所用的合金一般要求高硅,这会导致铁液的增硅幅度很高,甚至达到0.8%,以上两个因素结合使得铁液的精确控制无法实现。
1.2球化剂添加量计算模型建立
球墨铸铁球化中球化剂的使用,以灰色关联模型或改进的灰色关联模型或联合灰色关联模型对原铁水基本化学成分(活性碳当量CEL、硅当量SiE、C和Si含量、微量元素含量水平)、石墨形核能力、氧化程度及S含量等冶金状态特性进行综合评价,评价体系由热分析曲线上的特征参数和炉前快速光谱成分分析结果组成,反映原铁水冶金状态对球化效果的影响。在评价之前,首先确定在生产条件下各冶金状态参数的阀值,并以各参数阀值的中值序列组成统计最优参比状态。评价时,对待测铁水状态参数序列与统计最优状态参数序列进行灰色关联性分析,根据灰色关联度综合评价值(平均灰色关联系数)与球化剂添加量WMg的相关性,建立考虑球化剂中Mg和稀土RE元素的收得率以及孕育“促球”作用的球化剂添加量WMg计算公式。
球化退火与软化退火
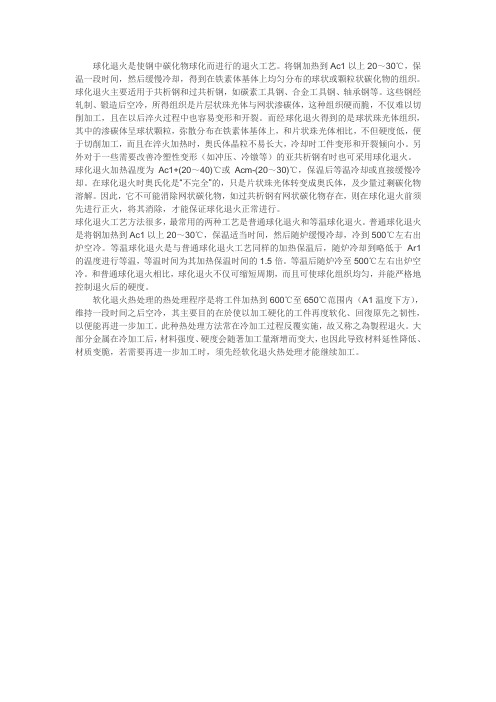
球化退火是使钢中碳化物球化而进行的退火工艺。
将钢加热到Ac1以上20~30℃,保温一段时间,然后缓慢冷却,得到在铁素体基体上均匀分布的球状或颗粒状碳化物的组织。
球化退火主要适用于共析钢和过共析钢,如碳素工具钢、合金工具钢、轴承钢等。
这些钢经轧制、锻造后空冷,所得组织是片层状珠光体与网状渗碳体,这种组织硬而脆,不仅难以切削加工,且在以后淬火过程中也容易变形和开裂。
而经球化退火得到的是球状珠光体组织,其中的渗碳体呈球状颗粒,弥散分布在铁素体基体上,和片状珠光体相比,不但硬度低,便于切削加工,而且在淬火加热时,奥氏体晶粒不易长大,冷却时工件变形和开裂倾向小。
另外对于一些需要改善冷塑性变形(如冲压、冷镦等)的亚共析钢有时也可采用球化退火。
球化退火加热温度为Ac1+(20~40)℃或Acm-(20~30)℃,保温后等温冷却或直接缓慢冷却。
在球化退火时奥氏化是“不完全”的,只是片状珠光体转变成奥氏体,及少量过剩碳化物溶解。
因此,它不可能消除网状碳化物,如过共析钢有网状碳化物存在,则在球化退火前须先进行正火,将其消除,才能保证球化退火正常进行。
球化退火工艺方法很多,最常用的两种工艺是普通球化退火和等温球化退火。
普通球化退火是将钢加热到Ac1以上20~30℃,保温适当时间,然后随炉缓慢冷却,冷到500℃左右出炉空冷。
等温球化退火是与普通球化退火工艺同样的加热保温后,随炉冷却到略低于Ar1的温度进行等温,等温时间为其加热保温时间的1.5倍。
等温后随炉冷至500℃左右出炉空冷。
和普通球化退火相比,球化退火不仅可缩短周期,而且可使球化组织均匀,并能严格地控制退火后的硬度。
软化退火热处理的热处理程序是将工件加热到600℃至650℃范围内(A1温度下方),维持一段时间之后空冷,其主要目的在於使以加工硬化的工件再度软化、回復原先之韧性,以便能再进一步加工。
此种热处理方法常在冷加工过程反覆实施,故又称之為製程退火。
大部分金属在冷加工后,材料强度、硬度会随著加工量渐增而变大,也因此导致材料延性降低、材质变脆,若需要再进一步加工时,须先经软化退火热处理才能继续加工。
球化退火介绍

提问者: 映月沙丘- 江湖新秀最佳答案球化退火球化退火是使钢中碳化物球化而进行的退火工艺。
将钢加热到Ac1以上20~30℃,保温一段时间,然后缓慢冷却,得到在铁素体基体上均匀分布的球状或颗粒状碳化物的组织。
球化退火主要适用于共析钢和过共析钢,如碳素工具钢、合金工具钢、轴承钢等。
这些钢经轧制、锻造后空冷,所得组织是片层状珠光体与网状渗碳体,这种组织硬而脆,不仅难以切削加工,且在以后淬火过程中也容易变形和开裂。
而经球化退火得到的是球状珠光体组织,其中的渗碳体呈球状颗粒,弥散分布在铁素体基体上,和片状珠光体相比,不但硬度低,便于切削加工,而且在淬火加热时,奥氏体晶粒不易长大,冷却时工件变形和开裂倾向小。
另外对于一些需要改善冷塑性变形(如冲压、冷镦等)的亚共析钢有时也可采用球化退火。
球化退火加热温度为Ac1+(20~40)℃或Acm-(20~30)℃,保温后等温冷却或直接缓慢冷却。
在球化退火时奥氏化是“不完全”的,只是片状珠光体转变成奥氏体,及少量过剩碳化物溶解。
因此,它不可能消除网状碳化物,如过共析钢有网状碳化物存在,则在球化退火前须先进行正火,将其消除,才能保证球化退火正常进行。
球化退火工艺方法很多,最常用的两种工艺是普通球化退火和等温球化退火。
普通球化退火是将钢加热到Ac1以上20~30℃,保温适当时间,然后随炉缓慢冷却,冷到500℃左右出炉空冷。
等温球化退火是与普通球化退火工艺同样的加热保温后,随炉冷却到略低于Ar1的温度进行等温,等温时间为其加热保温时间的1.5倍。
等温后随炉冷至500℃左右出炉空冷。
和普通球化退火相比,球化退火不仅可缩短周期,而且可使球化组织均匀,并能严格地控制退火后的硬度。
合金钢的球化和石墨化
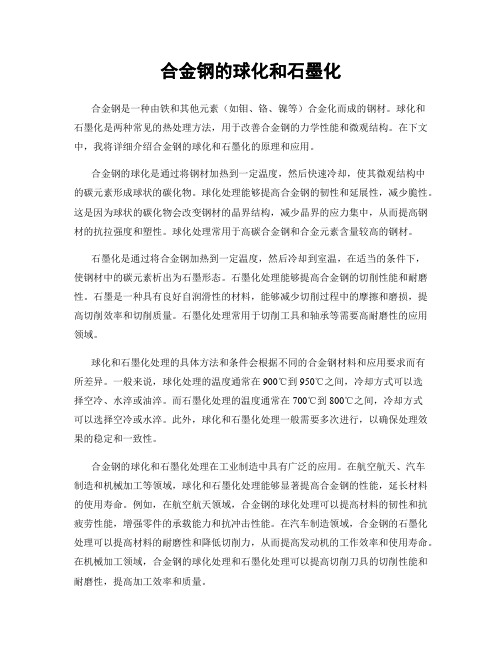
合金钢的球化和石墨化合金钢是一种由铁和其他元素(如钼、铬、镍等)合金化而成的钢材。
球化和石墨化是两种常见的热处理方法,用于改善合金钢的力学性能和微观结构。
在下文中,我将详细介绍合金钢的球化和石墨化的原理和应用。
合金钢的球化是通过将钢材加热到一定温度,然后快速冷却,使其微观结构中的碳元素形成球状的碳化物。
球化处理能够提高合金钢的韧性和延展性,减少脆性。
这是因为球状的碳化物会改变钢材的晶界结构,减少晶界的应力集中,从而提高钢材的抗拉强度和塑性。
球化处理常用于高碳合金钢和合金元素含量较高的钢材。
石墨化是通过将合金钢加热到一定温度,然后冷却到室温,在适当的条件下,使钢材中的碳元素析出为石墨形态。
石墨化处理能够提高合金钢的切削性能和耐磨性。
石墨是一种具有良好自润滑性的材料,能够减少切削过程中的摩擦和磨损,提高切削效率和切削质量。
石墨化处理常用于切削工具和轴承等需要高耐磨性的应用领域。
球化和石墨化处理的具体方法和条件会根据不同的合金钢材料和应用要求而有所差异。
一般来说,球化处理的温度通常在900℃到950℃之间,冷却方式可以选择空冷、水淬或油淬。
而石墨化处理的温度通常在700℃到800℃之间,冷却方式可以选择空冷或水淬。
此外,球化和石墨化处理一般需要多次进行,以确保处理效果的稳定和一致性。
合金钢的球化和石墨化处理在工业制造中具有广泛的应用。
在航空航天、汽车制造和机械加工等领域,球化和石墨化处理能够显著提高合金钢的性能,延长材料的使用寿命。
例如,在航空航天领域,合金钢的球化处理可以提高材料的韧性和抗疲劳性能,增强零件的承载能力和抗冲击性能。
在汽车制造领域,合金钢的石墨化处理可以提高材料的耐磨性和降低切削力,从而提高发动机的工作效率和使用寿命。
在机械加工领域,合金钢的球化处理和石墨化处理可以提高切削刀具的切削性能和耐磨性,提高加工效率和质量。
总结起来,合金钢的球化和石墨化处理是一种重要的热处理方法,能够显著改善钢材的力学性能和微观结构。
《球化处理工艺》课件
合作与交流
强调了加强国际合作与 交流,共同推动球化处 理工艺技术的发展和应
用的重要性。
THANKS
[ 感谢观看 ]
生产过程的自动化与智能化
总结词
通过自动化与智能化技术,可以提高生产效率、降低 能耗、减少人工干预,进一步优化球化处理工艺。
详细描述
随着自动化与智能化技术的不断发展,越来越多的企 业开始将这些技术应用于球化处理工艺中。通过自动 化技术,可以实现生产过程的自动化控制,提高生产 效率;通过智能化技术,可以对生产过程进行实时监 控和预测,及时发现和解决潜在问题,降低能耗和减 少人工干预。这些技术的运用,可以进一步优化球化 处理工艺,提高企业的生产效率和产品质量。
球化处理工艺的应用范围
球化处理工艺广泛应用于铸铁 制品的生产,如机床、汽车、 拖拉机等机械制造业中。
由于球化处理工艺可以提高铸 铁制品的力学性能和耐磨性, 因此可以延长其使用寿命,提 高产品质量。
此外,球化处理工艺还可以应 用于其他金属材料的处理,如 钢、铝合金等。
CHAPTER 02
球化处理工艺流程
预处理
去除杂质
在球化处理前,需要对原材料进 行严格筛选,去除其中的杂质和 有害元素,以确保球化处理的质 量和效果。
破碎与筛分
对于大块的原材料,需要进行破 碎和筛分,使其达到合适的粒度 和分布,以便于后续的球化处理 。
球化剂的选择与配置
根据原材料性质选择合适的球化剂
不同的原材料需要不同的球化剂,选择合适的球化剂是保证球化处理效果的关 键。
CHAPTER 06
案例分析
某公司球化处理工艺的应用实例
案例概述
工艺流程
某公司在生产过程中采用了球化处理工艺 ,有效地提高了产品质量和生产效率。
铸造合金熔炼之球化处理工艺介绍
提高产品质量:球化处理工艺可以提高产品的机械性能和耐磨性,从而提高产品质量。
减少环境污染:球化处理工艺可以减少生产过程中的废气和废水排放,从而减少环境污染。
04
谢谢
02
温度控制:控制熔融金属的温度,使球化剂充分反应
03
球化处理时间:控制球化处理的时间,使球状组织充分形成
04
球化处理后处理:球化处理后进行脱氧、脱硫等处理,提高金属性能
05
球化处理工艺流程
原材料准备
准备铸造合金材料,如铁、碳、硅等
准备球化剂,如镁、稀土等
准备孕育剂,如硅铁、硅钙等
准备脱氧剂,如铝、钛等
04
球化处理可以改善金属的加工性能,提高生产效率。
球化处理的目的
改善合金的组织结构,提高其力学性能
01
降低合金的脆性,提高其韧性和延展性
02
改善合金的耐磨性和耐腐蚀性
03
提高合金的加工性能,便于加工成型
04
球化处理的方法
球化剂加入:将球化剂加入熔融金属中,使金属形成球状组织
01
搅拌:通过搅拌使球化剂均匀分布,形成球状组织
02
03
04
球化温度的控制
球化温度是球化处理工艺的关键因素之一
球化温度过高会导致球化不良,影响合金性能
球化温度过低会导致球化不完全,影响合金的力学性能
球化温度需要根据合金的成分和生产工艺进行精确控制,以保证合金的性能和品质
01
02
03
04
球化时间的控制
01
球化时间的长短直接影响球化效果
02
球化时间过短,球化效果不佳,影响产品质量
浇铸:将熔融的铁合金倒入模具中,冷却成型
球化处理工艺
加盖铁液包示意图
盖包法球化处理时,球化合金的加入与冲入法 相同,然后将包盖安放在铁液包上,并使其周边封好. 出铁时,将铁液以较大液流注入包盖浇口盆内(保证 铁液在盆内的高度在5~15mm),铁液会通过包盖一 侧的注孔(注孔不得直接对准合金堆放处)流入包 内.这样可使外界的气体与包内完全隔离,减少镁的 氧化烧损,提高镁的吸收率(一般在60℅~65℅以上), 改善劳动环境.球化反应结束后,去除包盖.
球墨铸铁的一关键环节
———球化处理工艺
继此, 转包法、盖包法和包芯喂线法在我国 先后得到了推广和应用.现在我就生产中常 见的球化处理方法作个简要介绍:
(一)压力加镁法 (二)冲入法 (三)转包法 (四)盖包法 (五)包芯线喂线法
(一)压力加镁法
压力加镁法是五十外代就已经开始釆用的 一种球化处理方法,它的基本原理是,当物体周 围介质的压力增加时,该物质的沸腾温度相应 提高,例如,当铁液表面的压力达到0.9MPa时, 镁的沸腾温度提高到1400℃左右,若使球化处 理温度略高于该温度,则镁在铁液中刚刚气化, 产生一定的翻腾,有利于镁的吸收,同时减少了 气化烧损,因而可以有效提高镁的吸收率.
冲入法球化处理前,就将球化处理包预热到暗红色, 预热的目的是减少铁液热量损失.并且防止覆盖剂下 桩实较紧的合金粘结在包底.球化处理时,将球化合 金堆放在预热的包底,上面覆盖硅铁合金,稍加紧实, 然后再覆盖无锈铁屑,苏打等覆盖剂,铁液过高时,可 盖铁板.
这种方法的优点是,处理方式和设备简单,容易操 作,在生产中有较大的灵活性,一般可使用含镁量较 低(<10℅)的各种合金球化剂.但是该工艺在球化处 理过程中镁光,烟尘非常大,劳动环境差,镁的吸收率 不太高,球化剂消耗量大,球化效果及球铁性能不太 稳定.目前应该改进冲入法或换用其它球化处理工艺.
42CrMo材料球化退火工艺
42CrMo球化退火工艺:42CrMo有较高的淬透性,较好的强度和韧性,可用于较大截面与高强度的零件.球化退火是为了得到粒状珠光体组织.但得到粒状珠光体组织不一定要进行球化退火,采用淬火得到马氏体或贝氏体,再经高温回火使碳化物析出并球化的方法同样可达到目的.这种工艺得到的粒状珠光体较均匀,比较容易控制硬度.时间较短.工艺重显性好.C 0.38-0.43Si 0.15-0.35Mn 0.75-1.00Cr 0.8-1.10Mo 0.15-0.25S <0.040P <0.035球化退火是使钢中碳化物球化而进行的退火工艺。
将钢加热到Ac1以上20~30℃,保温一段时间,然后缓慢冷却,得到在铁素体基体上均匀分布的球状或颗粒状碳化物的组织。
球化退火主要适用于共析钢和过共析钢,如碳素工具钢、合金工具钢、轴承钢等。
这些钢经轧制、锻造后空冷,所得组织是片层状珠光体与网状渗碳体,这种组织硬而脆,不仅难以切削加工,且在以后淬火过程中也容易变形和开裂。
而经球化退火得到的是球状珠光体组织,其中的渗碳体呈球状颗粒,弥散分布在铁素体基体上,和片状珠光体相比,不但硬度低,便于切削加工,而且在淬火加热时,奥氏体晶粒不易长大,冷却时工件变形和开裂倾向小。
另外对于一些需要改善冷塑性变形(如冲压、冷镦等)的亚共析钢有时也可采用球化退火。
球化退火加热温度为Ac1+(20~40)℃或Acm-(20~30)℃,保温后等温冷却或直接缓慢冷却。
在球化退火时奥氏化是“不完全”的,只是片状珠光体转变成奥氏体,及少量过剩碳化物溶解。
因此,它不可能消除网状碳化物,如过共析钢有网状碳化物存在,则在球化退火前须先进行正火,将其消除,才能保证球化退火正常进行。
球化退火工艺方法很多,最常用的两种工艺是普通球化退火和等温球化退火。
普通球化退火是将钢加热到Ac1以上20~30℃,保温适当时间,然后随炉缓慢冷却,冷到500℃左右出炉空冷。
等温球化退火是与普通球化退火工艺同样的加热保温后,随炉冷却到略低于Ar1的温度进行等温,等温时间为其加热保温时间的1.5倍。
- 1、下载文档前请自行甄别文档内容的完整性,平台不提供额外的编辑、内容补充、找答案等附加服务。
- 2、"仅部分预览"的文档,不可在线预览部分如存在完整性等问题,可反馈申请退款(可完整预览的文档不适用该条件!)。
- 3、如文档侵犯您的权益,请联系客服反馈,我们会尽快为您处理(人工客服工作时间:9:00-18:30)。
1/球化处理工艺
对球墨铸铁曲轴其球化处理工艺非常重要,曲轴的力学性能主要依靠球化质量来保证,我们选用低镁球化剂,球化反应比较平缓,铁水一次出完,球化效果比较好。
具体球化、覆盖等工艺改进如下。
球化剂(5%-7%Mg)→铁屑覆盖(1.5-2kg)→加铁水(400 g)一球化反应(50-70s)。
2/孕育处理工艺
加硅铁(一次孕育)→浇包加硅铁粉(二次孕育)→浇注随铁水流孕育(三次孕育)。
3 曲轴的清理
曲轴浇注后,大约在50~60min,可以翻箱倒铁丸取件,铸件冷却到50℃以下,可以去除冒口和浇注系统,曲轴用悬挂式抛丸机进行表面抛丸,每组20件,大约抛丸15min左右,曲轴表面要达到无粘砂,光亮为好。
采用电动角磨机和风动工具清理飞边毛刺。
4.1铁水的检验
要铸造优质的曲轴,必须保证铁水质量,特别是铁水的化学成分,其次是铁水的出炉温度(球化处理时铁水温度)和浇注温度。
铁水化学成分检验元素及检验频次见表4。
在重要铸件生产中,对材质要求高,如球墨铸铁要求P≯0.04%、S≯0.02%,铸钢要求P、S均≯0.025%,采用热分析技术及时准确控制C、Si含量,。