陶瓷工业热工设备
陶瓷窑炉的节能技术

陶瓷窑炉的节能技术推荐本文□ 曾令可刘涛王慧刘平安摘要随着“十一五”节能专项规划的出台,国家对高能耗高排放产业的改革势在必行。
陶瓷产业正是高能耗、高污染的行业,必然是改革的重点领域,节能减排也必将是陶瓷产业的大势所趋。
本文详细综述了当前陶瓷窑炉一些先进的节能技术,并对未来节能的发展方向提出了一些展望。
关键词陶瓷窑炉,能耗,节能技术1前言众所周知,国家“十一五”计划中明确提出了“十一五”节能专项规划,要求调整产业结构、能源结构,遏制高能耗高污染行业过快增长,大力推进节能工作,而陶瓷产业正是高能耗、高污染的行业,尤其是对资源的消耗和环境的污染都非常严重,属于政府和大众“紧盯”的行业之一。
在佛山,建筑陶瓷行业的节能、排放和环保问题显得尤为严重,在2007年,在佛山216家能源审计不合格企业的黑名单中,陶瓷企业赫然占了84家,陶瓷企业的变革必然首当其冲。
为此,国家出台了一系列的强制性节能措施,如开征燃油税、环境税,建立政府节能减排工作问责制和一票否决制等机制,以此强制性督促陶瓷产业进行节能改革。
中国陶瓷工业的能源利用率与国外相比,差距较大。
发达国家的能源利用率一般高达50%以上,美国达57%,而我国仅为28%~30%。
在陶瓷工业的一般工艺流程中,能耗主要体现在原料的加工、成形、干燥与烧成这四部分。
其中干燥和烧成工序,两者的能耗约占80%。
在建筑卫生陶瓷方面,国内外能耗存在着一定的差距,如表1所示。
以日用陶瓷在国内烧成能耗的状况为例,燃煤隧道窑为41816~54361kJ/kg瓷,折合1.42~1.85kg标准煤/kg瓷;燃油隧道窑为33453~45998kJ/kg瓷,折合1.14~1.57kg标准煤/kg 瓷;燃气隧道窑为29271~39725kJ/kg瓷,折合1.00~1.35kg标准煤/kg瓷。
而国外窑炉以气体燃料为主,烧成能耗为12545~25090kJ/kg瓷,折合0.43~0.86kg标准煤/kg瓷,烧成能耗只有我国的一半左右[1]。
无机非金属材料热工设备(姜洪舟版)全书配套课件

水泥生产的过程是要经过“二磨一烧”:即生料磨,水泥 窑 和水泥磨。其中水泥窑系统是将水泥生料在高温下烧成为 水泥熟料的热工设备,是水泥生产中的一个极为重要的关键环 节。
水泥熟料的烧制过程: 预热阶段(室温~900℃):生料中残余水的排除,500 ℃结构水
排出,随着生料升温,少量MgCO3分解。
根据窑头空气量进行计算:
V1K V2 K VLOK M yrVa0
2.2悬浮预热器——旋风筒
2.2.1旋风预热器的工作原理
(1)生料粉在废气中分散与悬浮
(2)气、固之间换热 (在联结管道内完成) (3)气、固相的分离,生料粉的收集 (在旋风筒内完成)
2.2悬浮预热器——旋风筒
向下旋转的气流——被称为 外旋流。 向上旋转的气流——被称为 内旋流。 旋风筒内的流畅是三维流场: 切向分速度、径向分速度、轴 向分速度
10000 ( L1 L2 ) e (%) L1 (100 L2 )
(2)真实分解率: 生料在预热器内预热和分解的真实数据,不考虑飞灰对所取 样品分解率的影响.
et e 100m fh (e fh e)(100 L1 ) 10000 L1e fh (%) e 100m fh (100 L1 )(L2 L fh ) L1 (100 L2 ) (%)
燃烧带单位截面面积、单位时间内所承受的热量 Q yr qA ( kJ / m 2 h) Di2 4
3)回转窑内燃烧带的表面热力强度(燃烧带的表面热负荷)
燃烧带单位表面面积、单位时间内所承受的热量
qF Qyr (kJ / m 2 h)
Di Li
4)回转窑内燃烧带的容积热力强度(燃烧带的容积热负荷) 燃烧带单位容积、单位时间内所承受的热量
工业炉

热工理论在工业窑炉中的应用摘要:工业炉窑的发展与生产工艺密切相关。
为发展新型无机材料及其各类复合材料,目前在科研工作中也发展了一些规模较小的各种炉子。
全面掌握热工理论是控制,改进,设计,提高工业窑炉效率的的关键。
如降低制品热耗,提高传热速率,减少热损失,窑内气体运动合理,减少气体穿越物料的阻力损失,保证燃料在炉内的充分燃烧问题。
关键字:伯努利方程式热传导热对流热工理论工业炉窑正文传热学在窑炉设备中的应用:传热学是研究不同温度的物体,或同一物体的不同部分之间热量传递规律的学科,在冶金和硅酸盐工业中存在许多传热现象。
传热的基本方式有热传导、热对流和热辐射三种。
传热的基本方式有热传导、热对流和热辐射三种。
热传导是指在不涉及物质转移的情况下,热量从物体中温度较高的部位传递给相邻的温度较低的部位,或从高温物体传递给相接触的低温物体的过程,简称导热。
热对流是指不同温度的流体各部分由相对运动引起的热量交换。
工程上广泛遇到的对流换热,是指流体与其接触的固体壁面之间的换热过程,它是热传导和热对流综合作用的结果。
决定换热强度的主要因素是对流的运动情况。
热辐射是指物体因自身具有温度而辐射出能量的现象。
它是波长在0.1~100微米之间的电磁辐射,因此与其他传热方式不同,热量可以在没有中间介质的真空中直接传递。
太阳就是以辐射方式向地球传递巨大能量的。
每一物体都具有与其绝对温度的四次方成比例的热辐射能力,也能吸收周围环境对它的辐射热。
辐射和吸收所综合导致的热量转移称为热辐射传热学科在很多高技术领域里同样发挥着重要的和无法替代的作用。
(1)人类征服天空和宇宙空间的不懈努力以及所取得的巨大成果,是当今世界上各领域高技术、新材料研究最集中的体现。
其中传热学所起的作用功不可没。
据美国航空和宇宙航行局(NASA)所作的技术分析,美国航天飞机的技术关键只有一个半,这半个是大推力的液氢—液氧火箭发动机(其中自然与传热有密切的关系),而那一个关键则是所谓“热防护系统”(TPS),即指以航天飞机外表面的防热瓦为主的整个热防护结构。
传统梭式窑与全自动梭式窑的性能对比研究

1前言随着“中国制造2025”的号角吹响,工业化4.0叠加智能化、数字化在陶瓷窑炉行业掀起浪潮。
传统陶瓷窑炉能耗大、污染强、烧成差的劣势一方面掣肘企业无力发展,也倒逼窑炉研发领域不断创新,持续改良。
梭式窑是一种对产品适应性强且满足个性化需求的小型热工设备,相对于隧道窑、辊道窑,梭式窑体积小,结构紧凑,在较小的烧成空间要根据陶瓷的烧成温度迅速升温至1000℃左右,再急冷到500℃至600℃,前后温差变化很大,故对梭式窑的燃烧控制系统和冷却通风系统要求较高。
传统的梭式窑采用自吸式烧嘴,自动化程度低,在陶瓷烧制过程中窑工通过手动调节燃气管道阀门和排烟挡板控制窑温度,费时费力且产品质量得不到保障,应用而生的现代全自动梭式窑补上其短板,一是采用动力式烧嘴交错布置,控制烧成温度;二是采用流体仿真技术模拟不同工况从而确定合理参数范围,优化窑炉结构;三是采用PLC 对梭式窑窑内温度、气氛、压力控制调节,达到针对不同产品的不同烧制要求。
2传统梭式窑李昊奇,汪和平,陆琳,宫小龙,汤宇(景德镇陶瓷大学材料科学与工程学院,景德镇333001)日用瓷等小型陶瓷的非连续性窑炉。
结构紧凑、产品适应性强的传统梭式窑和控制精准、烧成确定性强的全自动梭式窑在控制方式、热能利用方面存在诸多差异。
本文利用PLC 控制、流体动力仿真学,研究对比传统梭式窑与全自动梭式窑在温度控制、能耗大小。
为不同需求,不同应用条件下使用梭式窑的企业、个人提供理论指导。
PLC 控制;温度控制;能耗,男,甘肃白银人,1997年生,硕士研究生,主要从事热工设备及理论研究,Email :****************;,男,1971年生,硕士,教授。
Email :***************机械与设备Machine &Equipments Reserved.传统梭式窑是典型的间歇式倒焰窑炉。
通俗讲,是一种烧制陶瓷过程不连续、燃烧火焰在窑内流动过程是向上至拱顶后又向下流动的热工设备,大体结构分为:窑室,窑车、燃烧系统、排烟系统。
窑炉设计

景德镇陶瓷学院《窑炉课程设计》说明书题目:年产860万件汤盘天然气隧道窑设计说明书目录前言一、设计任务书 (4)二、烧成制度的确定2.1 温度制度的确定 (5)三、窑体主要尺寸的计算..3.1棚板和立柱的选择 (5)3.2窑长及各带长的确定 (5)3.2.1 装车方法 (5)3.2.2 窑车尺寸确定 (6)3.2.3窑内宽、内高、全高、全宽的确定 (6)3.2.4 窑长的确定 (7)3.2.5 全窑各带长的确定 (7)四、工作系统的确定4.1 排烟系统 (7)4.2 燃烧系统 (8)4.3 冷却系统 (8)4.4 传动系统 (8)4.5 窑体的附属结构 (8)五、窑体材料及厚度的选择 (8)六、燃料燃烧计算 (12)七、物料平衡计算 (13)八、热平衡计算 (14)九.冷却带的热平衡计算 (18)十、烧嘴的选用 (21)十一、心得体会 (22)十二、参考文献 (23)前言隧道窑是耐火材料、陶瓷和建筑材料工业中最常见的连续式烧成设备。
是以一条类似铁路隧道的长通道为主体,通道两侧用耐火材料和保温材料砌成窑墙,上面为由耐火材料和保温材料砌成的窑顶,下部为由沿窑内轨道移动的窑车构成的窑底形成的一种烧成过程。
随着经济的不断发展,陶瓷工业在人民生产、生活中都占有重要的地位。
陶瓷的发展与窑炉的改革密切相关,某一种特定的窑炉可以烧制出其他窑炉所不能烧制的产品,而有时需要一种特定的产品,就需要对其窑炉的条件加以限制,因此,配方和烧成是陶瓷制品优化的两个重量级过程,每个过程都必须精益求精,才能得到良好,称心的陶瓷制品。
隧道窑是现代化的连续式烧成的热工设备,以窑车为运载工具,具有生产质量稳定、产量大、消耗低的特点,最适合于工艺成熟批量生产的日用瓷。
由于现在能源价格不断上涨,为了节约成本,更好的赢取经济利益,就需要窑炉在烧成过程中严格的控制温度制度、气氛制度,压力制度,提高生产效率及质量,更好的向环保节能型窑炉方向发展。
自吸式烧嘴梭式窑
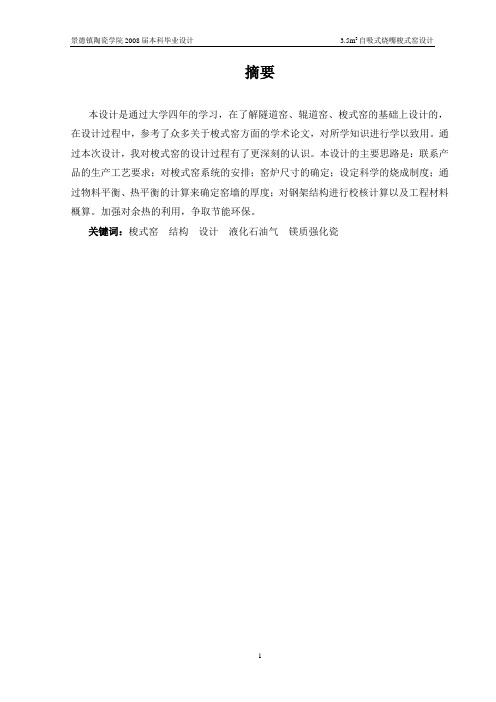
摘要本设计是通过大学四年的学习,在了解隧道窑、辊道窑、梭式窑的基础上设计的,在设计过程中,参考了众多关于梭式窑方面的学术论文,对所学知识进行学以致用。
通过本次设计,我对梭式窑的设计过程有了更深刻的认识。
本设计的主要思路是:联系产品的生产工艺要求;对梭式窑系统的安排;窑炉尺寸的确定;设定科学的烧成制度;通过物料平衡、热平衡的计算来确定窑墙的厚度;对钢架结构进行校核计算以及工程材料概算。
加强对余热的利用,争取节能环保。
关键词:梭式窑结构设计液化石油气镁质强化瓷Astract前言3.5 m3自吸式烧嘴梭式窑是一种新型的高温间歇窑,该窑升温快、温差小、烧成温度升温速度可调范围宽、气氛可调、产品烧成质量高,是目前大多数工业陶瓷、特种陶瓷及耐火烧成首选热工设备之一。
该窑采用先进的全纤维梭式窑,减轻窑炉负重,减少蓄热,减少对钢架的使用,达到烧成质量高,燃料消耗少,占地面积小,投资节省的目的,可取得良好的经济效益。
该窑以燃烧热值高,污染少的液化石油气为燃料,可实现无匣明焰烧成,热利用率大大提高,同时自然冷却,不需要任何动力,有显著的节能效果和推广价值。
该窑设计力求从实际出发,结合镁质强化瓷的生产工艺要求,制定出科学合理的烧成制度,设计出一个性能稳定、节能、高效、环保、寿命长的全纤维梭式窑。
该窑主要技术特征内空尺寸:1800 mm ⨯1300 mm ⨯1500 mm(不含火位)窑体尺寸:2490 mm ⨯2200 mm ⨯2485 mm窑车尺寸:1800⨯1300产品种类:高档瓷最高烧成温度:1300℃烧成方式:明焰裸烧烧成周期:10个小时耗气量:约150kg窑体结构:钢框架内衬耐火纤维窑内气氛:还原气氛燃料种类:液化石油气烧嘴类型:自吸式燃气烧嘴烧嘴数目:6对窑车数目:1热电偶:铂铑—铂窑内贴多晶莫来石纤维,减轻重量、减少蓄热、升温快、提高能量利用率。
1、设计任务书及原始资料1.1 设计任务书院(系)热能工程系 2008年1月10日1.2 原始资料 产品名称:镁质强化瓷产品规格:Φ198 mm ⨯高111 mm 坯体总线收缩率:14.33% 入窑水份:2% 产品合格率:98%膨胀系数:6810/C -⨯︒颗粒大小:<10m μ以下的颗粒占70%左右 最高温度1300C ︒保持6分钟后停火表1—1 镁质强化瓷坯体化学组成第2章窑体主要尺寸的确定2.1 入窑坯体尺寸:Φ198 mm ⨯高111 mm坯体总线收缩率:14.33%出窑坯体尺寸:Φ170mm ⨯95 mm2.2 预选硼板尺寸及装窑方式:选用薄型SIC硼板,硼板尺寸为620mm⨯405mm⨯10mm装窑方式:硼板间留20mm宽的火道,坯体间留10mm的火道。
年产九万件卫生瓷器隧道窑的设计 计算书

年产九万件卫生瓷器隧道窑的设计+计算书摘要:隧道窑是现代化的连续式烧成的热工设备,广泛用于陶瓷产品的焙烧生产。
本设计为年产九万件卫生瓷器隧道窑的设计,通过分析国内外典型的陶瓷隧道窑。
设计了一条普通窑车隧道窑,总长34.5米,内宽0.8米,烧成温度是1220℃。
燃料采用清洁环保天然气,采用明焰裸烧工艺。
燃烧产物与制品直接接触,热交换充分,制品受热均匀,可以实现低温快烧,降低单位燃耗,提高产量,并使用了较为传统的筑炉材料,合理地控制了窑炉的造价。
针对隧道窑进行了主要尺寸的确定,燃料燃烧计算,热量衡算,在此基础上通过分析工艺流程,确定了工作系统,并对工艺设备进行了计算和选择,绘制工作系统图等、并编制了设计说明书和计算书。
12790关键词:隧道窑;热量衡算;工艺设计The design of tunnel kiln with the annual production capacity of 90000 large ceramic sanitary wareAbstract: The tunnel kiln is the modern thermal equipment with continuous firing, widely used in the roasting production of ceramic products.Through the analysis of the domestic and foreign typical ceramics tunnel kiln, I make the design of tunnel kiln with the annual output of 90000 large ceramic sanitary ware. It is a common kiln car of tunnel kiln, which total length is 34.5 meters within 0.8 meters wide and the firing temperature is 1220℃. The design use natural gas as fuel, which is clean and green, using the flame bare firing process. Combustion products and products direct contact, heat exchange is fully, and the product is heated evenly, which can achieve rapid firing of low temperature, reduce unit fuel consumption, increase production. And use a more traditional furnace building materials, which will reasonably control the cost of the kiln. According to the tunnel kiln determine its main size, fuel burning calculation, heat balance calculations, based on this through theanalysis process flow, calculate and choose the process equipment, draw work system graph, and compiled the design specifications and calculations.2.5.3工作系统112.6窑体材料和厚度确定122.7燃料燃烧计算132.7.1燃烧所需空气量计算132.7.2烟气量计算132.7.3燃烧温度计算142.8预热带平衡计算142.8.1确定热平衡计算的基准、范围142.8.2热平衡示意图142.8.3热收入项目152.8.4热收入项目172.8.5列热平衡方程式212.9冷却带平衡计算222.9.1热收入项目232.9.2热支出项目232.9.3热支出项目282.10烧嘴的选用及燃烧室的计算292.11烟道和管道计算,阻力计算和风机选型30 2.11.1烟道和管道计算302.11.2阻力计算312.11.3风机选型333工程概算353.1建筑材料的概算353.1.1粘土砖的概算353.1.2轻质粘土砖的概算373.1.3粒状高炉渣373.1.4红砖概算374经济衡算38烧成在陶瓷生产中是非常重要的一道工序。
陶瓷窑炉及设计 第二章辊道窑1

SUST
9
陶瓷窑炉与设计----第二章 辊道窑
由于上述优点,再配合低温快烧技术,更充分的发挥了辊道窑的技术优 势,使其成为陶瓷墙地砖和其它扁平产品的理想烧成设备
SUST
10
陶瓷窑炉与设计----第二章 辊道窑
SUST
11
陶瓷窑炉与设计----第二章 辊道窑
2. 结构
现代辊道窑结构: 窑体、 燃烧系统、 运载装置、 入出窑机组、 钢结构 自动控制系统
SUST
3
陶瓷窑炉与设计----第二章 辊道窑
(4)按产品加热方式分: 隔焰(辐射)辊道窑 半隔焰(辐射、对流)辊道窑
(5)按窑顶结构分: 盖板辊道窑、拱顶辊道窑、吊顶辊道窑
辊道窑和隧道窑一样,也属于逆流操作的热工设备, 坯体在窑内与气流运动方向相反
SUST
4
陶瓷窑炉与设计----第二章 辊道窑
双层辊道窑
5
陶瓷窑炉与设计----第二章 辊道窑
SUST
6
陶瓷窑炉与设计----第二章 辊道窑
SUST
7
陶瓷窑炉与设计----第二章 辊道窑
工作层多用轻质高铝砖; 保温层用保温隔热材料:隔 热棉、耐火棉等 保护层:一般用钢结构
SUST
8
陶瓷窑炉与设计----第二章 辊道窑
1.2辊道窑的特点
(1)窑内温度均匀,坯体上下和横向温差小。用天然气或净化煤气做燃 料,可在辊底上下设置烧嘴,使产品上下同时加热,受热均匀; (2)微机监控、自动记录温度,窑内烧成带上下温度波动范围<±2℃, 横向温度波动范围<10℃,保证了产品的质量,缩短了产品的烧成周期; (3)实现了生产机械化和自动化并同其它生产设备组成完整的现代化生 产线; (4)单位产品燃耗低、成本低。不用窑车、匣钵等耐火材料,降低了单 位产品的燃料消耗和产品成本。
- 1、下载文档前请自行甄别文档内容的完整性,平台不提供额外的编辑、内容补充、找答案等附加服务。
- 2、"仅部分预览"的文档,不可在线预览部分如存在完整性等问题,可反馈申请退款(可完整预览的文档不适用该条件!)。
- 3、如文档侵犯您的权益,请联系客服反馈,我们会尽快为您处理(人工客服工作时间:9:00-18:30)。
热工设备 第三章 隧道窑 烧成过程 1、20-200℃预热排除残余水分 2、200-500℃排除结构水 3、500-600℃石英晶型转化:β-SiO2→α-SiO2,体积膨胀控制不当(温度不均)导致开裂 4、600-1050 ℃氧化阶段: 硫化铁、有机物中碳的氧化,碳酸盐分解等 5、1050-1200 ℃还原阶段: 氧化铁还原为氧化亚铁 6、1200-1300 ℃烧结阶段: 7、冷却阶段:①1300-700 ℃急冷段 ②700-400 ℃ 缓冷段 石英晶型转化 ③400-80 ℃
烧成制度的确定原则 包括:温度制度 气氛制度 压力制度
1、合理的温度变化速率:考虑制品内部温度均匀及物理-化学变化所需时间 2、适宜的保温时间 3、气氛控制: 4、合理的压力制度:
烧成制度举例P5
耐火材料的主要性能 1、耐火度:高温下抵抗熔化的能力(三角锥试样软化) 2、荷重软化点:在一定压强下加热,发生变形和坍塌时的温度 3、热稳定性(温度急变抵抗性、抗热震性):热震试验 4、抗氧化腐蚀性 5高温体积稳定性:在高温下长期使用,抵抗体积不可逆变化的能力(用残余收缩/膨胀表示)
1、粘土砖:弱酸性耐火材料,热稳定性较好,荷重软化开始温度1250-1300℃,使用温度1300 ℃以下。 2、半硅砖:半酸性耐火材料,荷重软化开始温度高于粘土砖,但热稳定性比粘土砖稍差。 3、高铝砖:耐火度及荷重软化温度高于粘土砖,抗化学腐蚀性较好,但热稳定性稍差,使用温度1400-1600 ℃ 。 4、硅砖:酸性耐火材料,荷重软化开始温度高,热稳定性差,不适于间歇式窑炉。 5、镁砖:碱性耐火材料,耐火度很高,荷重软化温度低,热稳定性差。 6、镁硅砖:荷重软化开始温度较镁砖略高 7、镁铝砖:耐火度很高,荷重软化温度和热稳定性均好于镁砖,使用温度1700-1900 ℃。 8、刚玉砖:使用温度1800 ℃以下。 9、碳化硅耐火制品:导热系数高,高荷重软化温度和热稳定性,高的抗渣性和耐磨性。(可用于匣钵、棚板、隔焰板等) 10、含锆耐火材料及其它
砌窑用耐火混凝土 1、矾土水泥耐火混凝土(1300-1400℃) 2、磷酸盐耐火混凝土(1400-1600 ℃ ) 3、镁质耐火混凝土(1800 ℃ )
砌窑用隔热材料 1、轻质耐火砖:制造耐火砖时加入特殊发泡物质,生成多孔的轻质耐火砖强度低、耐磨性和热稳定性差,不能直接与火焰接触。 2、高铝空心球砖:高温绝热性好、收缩性小、强度大、耐磨性好、抗腐蚀性强。 3、硅酸铝耐火纤维(陶瓷棉):高耐火度、低导热系数、低蓄热量、轻质、吸音、耐热冲击、耐腐蚀等。 4、其它
工作系统及分带 1、分带: 预热带、烧成带、冷却带 2、流程: 坯体:预热带(烟气预热)→烧成带(火焰及燃烧产物加热烧成)→冷却带(冷空气) 燃烧产物:烧成带→预热带→排烟口→支烟道→主烟道→烟囱→窑外 空气:冷却带(被加热) →烧成带(作为助燃空气) →抽出(用于干燥或气幕) 3、工作系统 ①简单窑工作系统,无鼓风机和抽风机,只依靠烟囱吸入空气。结构简单,但温度分布不均,烧成温度低。 ②一般窑工作系统(如图1-3) 烧油或气自燃烧室喷入烧成带,用风机控制压力。 少/无冷风进入烧成带,燃烧温度高并维持气氛。温度均匀、低热耗。 ③隔焰窑工作系统 烟气不进入隧道而在隔焰道中流动换热。
隧道窑利用烟气预热坯体,利用产品冷却加热空气,且为连续性窑,窑墙、窑顶温度不变,热耗低。
隧道窑结构 窑体:窑体是由窑墙、窑顶和窑车衬砖围成码烧坯体的空间。 燃烧装置:包括燃烧室,烧嘴。 通风设备:排烟系统,气幕,气体的循环装置,冷却系统。 窑内输送设备:窑车、推板、输送带等。 窑体结构图 1- 烧嘴;2-烧嘴砖;3-燃烧室;4-窑墙;5-拱顶 窑墙:作用:分隔,支撑,保温。性能:耐温,强度,隔热。窑墙尺寸应为窑砖尺寸整数倍。 窑顶 结构如图:
1-拱顶;2-拱脚;3-拱脚梁;4-立柱;5-拉杆;6-检查坑;R-拱半径;B-跨度;α-拱心角;S-拱厚;f-拱高
类型有:半圆拱f=(1/2)B 标准拱(1/3~7/3) 倾斜拱(1/8~1/10) 平拱(0) f=拱高,B=跨度 窑顶需具备的性质: 1、 耐高温,积散热小具有一定机械强度。 2、 结构好不漏气,坚固耐用。 3、 质量小,减轻窑墙负荷。 4、 横推力小,少用钢材 5、 减少窑内气体分层。
检查坑道:①作用:清理、冷却、检查、处理故障等 ②缺点:增加基建费用 窑门:升降式,进口设施内外双重门。出口设置一道窑门。 隧道窑进车段最好用金属卷帘式窑门。下缘接窑车上,进入车位后松开连接装置。外卷帘门返回,放下内卷帘门,新一车进入。
砂封:窑车上钢制裙板+窑墙上砂封遭构成砂封。群板插入窑内两侧墙上砂封槽中。 作用:隔断窑车上下空间,不使冷空气漏入窑内和热气体漏出。需由窑墙上加砂管定时补充
另:曲折封闭:防止高温部分热量直接辐射给窑车金属部分,并增加漏气阻力,在窑墙与窑车衬砖之间作成曲折封闭。
推车机:使窑车在窑内移动,推动应平稳。油压推车机:由油泵,推进器组成。 连续推车:产品温度均匀上升,推车慢,平稳。 若预热带使用高速调温烧嘴,料垛间有对准喷嘴的气体循环空隙则需要间歇推车。
燃烧设备: ⑴燃烧室的布置: ① 集中或分散(视窑尺寸、气氛而定) 集中布置易于操作和自动调节。分散布置燃烧室,利于保证窑内温度均匀性。 ② 相对或相错(高速烧嘴多为相错) 相对布置:砌筑简单易于安置钢架结构,但喷火口两侧料垛温度较高,烧成带长度上出现温差,喷出火焰长而速度高产生火焰冲击的不良影响 相错布置:窑内气体循环,使温度进一步均匀。间距一个到半个车位,料垛留适当气体通道,或喷火口对装载制品的下部或垫砖通道。 ③一排或二排 烧煤气的隧道窑采用上下两层烧嘴。料垛较密,棚板装车造成上下气体沟通困难,避免下部温度高于上部。窑体断面较大,煤气或油可以采用顶烧式烧嘴。
燃烧室的种类:分为烧煤,烧重油,烧煤气的燃烧室。 烧嘴的种类:① 燃气烧嘴:烧煤气压力不高,使用短焰烧嘴,低压涡流式烧嘴。 天然煤气或液化石油气:使用喷射式无焰烧嘴。高速烧嘴。 ② 燃油烧嘴:要求有一定调节范围,雾化要好,雾滴小而均匀,与空气混合好,火焰软而短不直接冲刷制品或匣钵,扩散角适当20°~30°
排烟系统:包括烟气由窑内向窑外排出锁经过的排烟口,支烟道,排烟机,烟囱等。 1、排烟口:分布于预热带全长的70%,控制各点的烟气流量。排烟口的面积应等于支烟道的总截面积,等于主烟道的截面积,等于烟囱出口截面积。 2、支烟道:联接排烟口和主烟道。 3、主烟道:汇集各支烟道的烟气送入烟囱 布置方式:主烟道穿过窑底与另一侧主烟道会合然后进烟囱。 两侧主烟道平行至窑头会合再进烟囱。此种烟囱高度较低。 4、排烟机和烟囱:自然抽风的窑炉:烟囱作用有①造成足够的抽力能克服窑内阻力②将烟气送到足够高的地方避免污染住宅区。 机械通风的窑炉:照顾卫生条件,烟气也不能放在低空。 烟囱至少高于附近100m范围内最高屋顶3m。 气幕、搅动循环装置 气幕:在隧道窑横截面上自窑顶及两侧窑墙上喷射多股气流进入窑内形成的一片气体幕帘。 搅动气幕:位于预热带,克服预热带气体分层,预热带处于负压,易漏入冷风使热空气向上。可用高速调温烧嘴代替搅动气幕。90°垂直向下或者120-180°逆烟气流动方向喷出 封闭气幕:位于预热带窑头,窑头形成正压,避免冷空气进入窑内。连续推车时在窑顶做成出车方向的45°缝隙,喷出气流阻止热烟气外溢。在两侧窑墙上作出进车方向的45°缝隙,喷出气流阻止冷气入窑。 循环气幕:利用轴流风机或喷射泵使窑内烟气循环流动,达到均匀窑温的目的。 气氛幕:在气氛改变的地方,设置氧化气幕。 急冷阻挡气幕:起急冷和阻挡作用。缩短烧成时间提高产品质量,在冷却带700°以前急冷。
冷却系统: 1、直接冷却的冷却带结构 P29页图 2、设引射装置的冷却带结构:若烧嘴喷出速度不高,另外采用喷射泵引流 P29页图 3、窑顶和侧墙急冷气幕 4、间接冷却结构 冷空气鼓入两侧窑墙空隙、夹壁及窑顶双层拱内,并抽出这些热空气作为气幕、二次风及干燥用。 不可使用装设余热锅炉或水汽锅间接冷却。 钢架结构: 用于克服拱顶的横推力。 窑炉基础: 作用:支持窑体所受重力。 结构形式:①灰土窑基②毛石窑基③砖层窑基④有检查坑道的窑基
隧道窑工作原理 窑内气体流动 (一)压头对气体流动的影响 1、位压头: hp = (ρg - ρa) g z 2、静压头: hs=pg-pa 3、动压头: hd = 1/2ρω2 4、阻力损失压头: 克服预热带气体分层,减少上下温差的方法: ① 窑的结构上:预热带采用平顶或低于烧成带;两侧窑墙上部向内倾斜;适当缩短窑长;适当降低窑的高度,减低几何压头的影响;烟气排出口开在下部近车台面处,迫使烟气多次向下流动;设立封闭气幕,搅动气幕,循环气流装置;提高气体流速增加动压的作用。 ② 窑车结构;减轻窑车重量减少窑车吸热;车上砌有气体通道气体能够通过提高隧道下部温度;严密窑车接头、砂封板和窑墙 曲折密封。 ③ 码坯方法:料垛码的上密下稀,增加上部阻力减少下部阻力,使热气体多向下流;适当稀码料垛,减少窑内阻力,减少预热带负压,减少冷风漏入量。 (二)料垛码法对气体流动的影响(见上条) 隧道窑内的传热 (一)气体对流传热 (二)料垛空隙尺寸与对流传热的关系 (三)明焰窑内的气体辐射 (四)料垛空隙尺寸与辐射传热的关系 (五)匣钵对传热的影响 (六)明焰窑内的综合传热 (七)隔焰窑内的传热 (八)窑车的积热和散热 (九)制品的加热和冷却 操作控制 各带温度控制 (一)预热带温度控制 1、调节排烟闸 2、气幕调节 3、提高密封性 4、合理码坯 (二)烧成带温度控制 1、燃烧温度 实际火焰温度应高于制品烧成温度50~100℃。 2、火焰温度点 最高温度点控制在最末一二对烧嘴之间。前移使保温时间过长,制品过烧。 (三)冷却带温度控制 700℃之前急冷,靠急冷阻挡气幕喷入的冷空气将产品急冷。 烧成带的气氛控制 1、通过控制燃料与空气比例实现气氛控制 2、气氛控制与温度控制密切相关。烧氧化气氛时原料空气过多,如果维持燃料不变而减少过多空气则火焰温度提高,减少空气至空气过剩系数接近与1时温度最高。 压力控制:服务于温度制度和气氛制度的实现 隧道窑设计:包括1、窑体主要尺寸及结构计算;2、燃料燃烧及燃烧设备的计算;3、通风设备及其他附属设施计算。对于大件产品,先确定窑车的尺寸,根据每车制品的装载量直接求出要的长度和各带长度,再根据窑车宽和制品的尺寸,确定窑的内宽和内高。 工作系统的确定:包括燃烧系统和通风系统,原则是满足制品的焙烧要求,减少窑内温差温差,加速传热和充分利用余热,便于施工以及操作控制等。 窑体材料及厚度的确定:确定原则:根据各段温度,按照对窑墙、窑顶的要求,并考虑砖型、外型整齐及经济性。 燃料燃烧计算:包括:燃烧所需空气量,燃烧生成烟气量,实际燃烧温度。 经验数据决定燃料消耗量 预热带和烧成带的热平衡计算: 热平衡计算分两部分:①预热带和烧成带的热平衡,计算每小时热耗(目的:计算燃料消耗量)②冷却带热平衡,计算冷空气鼓入量和热风抽出量。 将预热带和烧成带合并而将冷却带独立的原因:燃料消耗发出之热是用于制品自入窑起至最高烧成温度为止的全部化学反应,而进入冷却带,不但不要供给热量,产品还有热量放出,所以分开计算。 计算之前确定:①热平衡计算基准1h,0℃。②热平衡计算范围③热平衡示意图。