UV油墨固化常见问题解答
uv光照固化中出现的问题
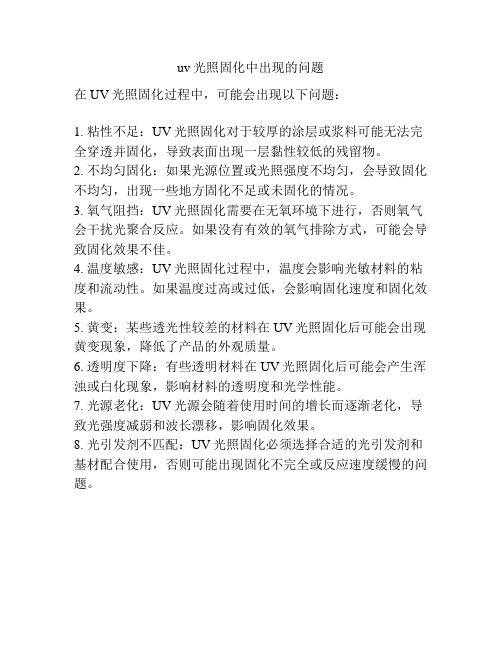
uv光照固化中出现的问题
在UV光照固化过程中,可能会出现以下问题:
1. 粘性不足:UV光照固化对于较厚的涂层或浆料可能无法完全穿透并固化,导致表面出现一层黏性较低的残留物。
2. 不均匀固化:如果光源位置或光照强度不均匀,会导致固化不均匀,出现一些地方固化不足或未固化的情况。
3. 氧气阻挡:UV光照固化需要在无氧环境下进行,否则氧气会干扰光聚合反应。
如果没有有效的氧气排除方式,可能会导致固化效果不佳。
4. 温度敏感:UV光照固化过程中,温度会影响光敏材料的粘度和流动性。
如果温度过高或过低,会影响固化速度和固化效果。
5. 黄变:某些透光性较差的材料在UV光照固化后可能会出现黄变现象,降低了产品的外观质量。
6. 透明度下降:有些透明材料在UV光照固化后可能会产生浑浊或白化现象,影响材料的透明度和光学性能。
7. 光源老化:UV光源会随着使用时间的增长而逐渐老化,导致光强度减弱和波长漂移,影响固化效果。
8. 光引发剂不匹配:UV光照固化必须选择合适的光引发剂和基材配合使用,否则可能出现固化不完全或反应速度缓慢的问题。
UV常见问题及改善对策

UV常见问题及改善对策一:光泽不好、亮度不够1 、UV光油粘度太低,涂层太薄2 、乙醇等非反应型溶剂稀释过量3 、UV 油涂布不均匀4 、纸张吸收性太强5 、网纹辊太细,供油量不足1> 、根据纸张的不同情况适当提高UV 光油的粘度和涂布量2 >、对渗透吸收性强的纸张,可先行涂布一层底油二:干燥不好、光固化不彻底、表而发粘1 、紫外灯管老化,强度减弱2 、UV 光油存储时间过长3 、非反应型稀释剂加入过多4 、机器速度过快1> 、在固化速度要求小于0. 5S 的情况下,必须保证高压汞灯的功率一般不小于120 w/cm2 >、灯管要及时更新,不要等坏了再换,必要时加入一定量的UV 光油固化促进剂,加速干燥三:印刷品表而UV光油涂不上、发花1 、UV 光油粘度低,涂层太薄2 、油墨中含调墨油或干燥油过多3 、油墨表面已晶化4 、油墨表面防粘材料(硅油、喷粉) 过多5 、涂胶网辊太细1> 、对要求UV 上光的产品印刷时必须采取相应措施,创造条件2> 、上UV 光油时适当涂厚些,必要时可通过上底油或更换特殊光油来解决问题四:UV上光涂层有白点和针孔1 、涂层太薄2 、网纹辊太细3 、非反应型稀释剂如乙醇加入量过多4 、印刷品表面粉尘较多1> 、生产环境及印刷品表而应保持护清洁,增加涂层厚度,也可加入少量平滑助剂2 >、稀释最好采用参与反应的活性稀释剂五:表而涂布不匀、有条纹及桔皮现象1 、UV 光油粘度过高2 、涂布辊太粗不光滑3 、压力大小不均匀4 、涂布量过大5 、UV 光油的流平性差1> 、降低UV 光油粘度,减少涂布量,压力调整均匀2 >、涂布辊应磨细、磨光,可加入少量流平剂六:UV光油附着力不好1 、印刷品上油墨表而晶化2 、印刷油墨中的辅助材料不合适3 、UV 光油本身粘附力不足4 、光固化条件不当1> 、印刷工艺要提前考虑上光条件2> 、已印好的产品需要涂上增强附着力的底油七:UV光油变稠、有凝胶现象1 、UV 光油存储时间过长2 、光油未能完全避光存储3 、存储温度偏高1 >、注意UV 光油的有效使用期,严格避光存储2 >、存储温度以5 一25 ℃为宜八:残留气味大1 、干燥固化不彻底2 、UV 光油抗氧干扰能力差3 、UV 光油中非反应型稀释剂加入过多1 >、UV 光油干燥固化必须彻底,加强通风2 >、必要时更换UV 光油品种。
UV油墨印刷七大问题及解决方法

UV油墨印刷七大问题及解决方法1.镜面反差效果不明显。
主要原因:①承印基材自身的光泽度不高;②磨砂油墨中填料加入量过大,完全遮盖住了基材;③填料的哑光程度不高,造成镜面基材与油墨膜面反差不强烈。
解决方法:在选取合适填料的同时,尽可能选择高光泽的镜面基材。
2.印刷品表面有花白、不着墨现象。
主要原因:①丝网目数选择不当;②基材表面有油污;③磨砂油墨中含有低挥发性的油性杂质。
解决方法:大体而言,对于颗粒直径较大的填料,若选择高目数的丝网,由于网孔较小,印刷时油墨不易通过或者通过很少,使着墨不匀,出现花白现象,而油污的存在使着墨困难或者出现斑点、花白现象,这种情况可通过选择适当的网版和相应的清洁措施来解决。
3.印刷时发生糊版现象。
主要原因:①磨砂油墨自身的黏度过大;②网距过小;③选择的丝网目数过低;④印刷压力大小不合适。
解决方法:尽量减少磨砂油墨中光固树脂的黏度,调整网版与承印物的距离,选择适当目数的丝网或调节印刷压力。
4.印刷品叠放时发生渗透现象。
主要原因:①磨砂油墨中材料自身的固化速度不够;②承印基材上有水分或其它溶剂;③固化时间过短。
解决方法:选择固化速度快的光固树脂,也可以适当增加光引发剂或光敏剂的用量,适当延长固化时间,保持基材的干燥和清洁。
5.印刷品有龟纹。
主要原因:①固化时间过长;②磨砂油墨中的树脂自身韧性欠佳;③绷网方式不适当。
解决方法:由于过长的固化时间会引发固化过度和后固化,造成龟裂。
因此应控制好固化时间,选择柔韧性较好的光固树脂和活性单体也可以改善龟纹现象。
采用斜绷网的方式来代替正绷网的方式,也可避免龟纹的产生。
6.印刷品的附着力不好。
主要原因:①由于光固树脂和活性单体经紫外光固化后不可避免地会发生体积收缩,势必影响磨砂油墨在低表面能、非极性基材上的附着力;②基材表面有硅油、喷粉、灰尘等杂质。
解决方法:对于低表面能、非极性的基材如PE、PP、PET等应预先进行电晕处理或者其它的化学、物理处理后,方可调试使用,同时保持印刷基材的清洁。
UV常见问题与解决方案

塑胶UV涂料常见问题1. 附着力不佳机理:单液型底漆与UV面漆之间不存在化学交联,基本上底漆、面漆之间的分子间作用力(包括分子间范德华力和氢键作用力),以及底漆和面漆之间的相互溶解,渗透所带来的物理锚合作用,因此要求底漆和面漆之间的配套。
底漆太硬面漆难以咬入,UV面漆溶解力太弱,不能形成良好的层间结合,底漆太软容易咬底、发花、发雾,同样面漆太厚,自由基聚合时体积收缩太大对附着力也有影响。
影响附着力的可能原因:1、底漆硬度高;涂装后放置时间太长,干得太透;铝粉漆的铝粉含量偏高或掉粉都是影响层间附着力的重要因素。
2、UV面漆原因:树脂和单体自身的粘附性不高;配方设计时官能度偏高,造成自由基聚合反应时体积收缩太大(特别是涂膜太厚时体积收缩影响附着力的现象更明显);UV固化不彻底,表干里不干,没有形成足够长的分子链。
溶剂偏弱或挥发太快、导致对底漆及塑料底材的二次溶解力不够。
表面张力太高,不能对底漆充分润湿和流平,配方设计不合理。
解决方案.1、调整底漆的硬度,提高底漆烘烤温度延长烘烤时间。
铝粉含量要控制在合理的范围,使用和UV配套的底漆系统。
2、控制好UV涂膜的体积收缩,调整溶剂的溶解力和挥发速率,调整膜厚、引发剂用量和灯功率,重新选择原材料和调整配方。
2,硬度硬度的影响因素与解决方案硬度的定义:涂层的硬度一般是指涂膜表层的铅笔测试硬度,其测试结果主要取决于涂层自身的硬度,同时也与涂膜的韧性和表面滑爽有关。
影响硬度的可能原因::底漆硬度和涂膜厚度;所选用主体UV树脂的结构和官能度,单体官能度越高硬度越高体积收缩越大,厚涂时附着力就差;配方的最终UV双键固化转化率要求UV固化时能量不小于800mj/cm2。
涂层中丙稀酸双键的交联密度大小;UV线红外流平温度和时间、UV曝光能量以及干膜厚度。
可行的解决方案:调整底漆硬度;调整面漆配方增加交联密度,但不能太高,以硬度大于H为好;增加涂膜厚度,控制在30-40um增加曝光强度,但不宜太高,否则官能团太多,交联点太多,体积收缩太大,厚涂时附着力调整红外流平温度和时间,使UV漆中溶剂在红外流平时要充分释放后再进行紫外光固化,但红外流平温度过高或时间太长也会造成UV漆咬底漆而降低整个涂层硬度。
UV常见6种故障及解决办法

现象:固化后的涂层不呈镜面。
原因1:UV光前几天黏度过高,流平性差。
解决办法:降低UV光油黏度,加入少量流平剂。
原因2:涂布辊太粗不光滑。
解决办法:涂布辊辊面应磨细、磨光。
印刷涂布胶辊要具有以下特点:
(1)橡胶硬度在50~60之间,有良好的回弹性;
(2)与油墨有良好的转移和着墨性能;
(3)具有一定的抗磨损性。
原因3:压力太小不均匀
解决办法:调整压力。
原因4:涂布量过多。
解决办法:减少涂布量。
原因5:UV涂层未固化,被别的导辊压过并反粘。
解决办法:(1)清洁干净。
(2)查明未固化原因。
原因6:由于气温低,上光油比较容易凝固,不利于上光油的正常流动,以致造成上光后的产品表面油膜不均匀。
解决办法:通常情况下,印品上光的温度控制在20左右可取得比较理想的效果。
使用上光油时应注意:
(1)了解上光油的种类、性质、效果及与其他溶剂配制时的变化情况。
(2)要针对承印物的基材和油墨表面性能选择适合性能的光油。
(3)要注意上光油的干燥性能,其干燥温度范围和干燥时间长短是不是对承印物有影响。
(4)要考虑上光材料的后加工适应性,如烫印性能,耐用摩擦性、凹凸压痕模切时的耐压性等。
(5)应选用透明度高、气味小的上光油。
UV丝印油墨印刷中应注意的问题

UV丝印油墨在印刷过程中应注意的有关问题、预防及解决办法UV油墨即UV紫外光固化油墨,分丝印、胶印、辊涂、淋涂、喷涂等几大类,此处只介绍UV丝印紫外光固化油墨。
UV丝印紫外光固化油墨,顾名思义其漆膜的形成是将UV油墨经丝网印刷于承印物表面再经UV紫外光照射而成。
而漆膜的厚度和UV紫外光能量的高低以及传送带速度的快慢将直接影响漆膜形成的好坏和UV油墨的干燥程度,从而影响承印物的整体表面效果。
因此,在大量印刷前必须严格的对承印物和UV油墨进行相关测试。
首先对承印物进行测试。
目前市场承印物主要有:普通纸张(包括金银卡纸、吸水纸、以及表面印溶剂型色墨的纸张等),PVC、PP胶片和覆膜纸(如OPP、PET等)。
根据其吸油程度不同又分为吸油纸和非吸油纸。
其中普通纸张大部分有一定的吸油性,而像PVC、PP胶片以及覆膜纸底材由于其密封性较好,故而一般不吸油。
也因此,其过UV灯后的固化程度也有一定的差别。
对普通纸张的测试主要有以下几项,无溶剂型色墨底材的附着力、吸油性,对特殊溶剂型色墨底材的附着力和胶印溶剂色墨底材在印刷UV油墨的耐温和耐化学性测试(即色变测试)。
由于普通纸张具有一定的吸油性,因此附着力都相对较好;如果纸张的吸油性太大,则可经过调整色墨的基材,则应先检测UV油的附着力方可进行批量生产印刷;对于较浅色的色墨尤其是调色底色的底材,则应检测其底墨的耐温性和耐化学性,同时检测印刷UV产品猴,是否会对底墨产生变色的影响。
一般对难附着胶印色墨底材而言,UV油墨的附着力可通过一层水性底油或调节UV油墨配方而达到要求,现主要说说后者。
检测其耐温性则应将没有印UV油的底材放进烤箱中进行烘烤,温度在120摄氏度,时间为72h烘烤不变色;检测其耐化学性,则是底材印刷UV油并过UV灯后进行顺叠和面叠(顺叠即承印面和非承印面相层叠,而面叠则是承印面和承印面错位的层叠),并置放烘箱中用5公斤左右重物压住烘箱,温度调节在90摄氏度左右,72小时底色墨不变色,UV油墨不脱落则可批量印刷。
UV常见问题解决

UV常见问题解决UV常见问题解决U.V上光工艺常见问题及解决1."麻点"现象原因:a.油墨发生了晶化现象b.表面张力值大,对墨层润湿作用不好。
解决:a.在UV油中加入5%的乳酸,破坏晶化膜或除去油质或打毛处理。
b.降低表面张力值,加入表面活性剂或表面张力值较低的溶剂。
2.条痕和起皱现象原因:a.UV油太稠,涂布量过大,主要出现在辊涂中。
解决:a.降低UV油的黏度值,加入适量的酒精溶剂稀释。
3.气泡现象原因:a.所用UV油质量不高,UV油本身含有气泡,多发生在用丝网上光中。
解决:a.换用质量高的UV油或将其静置一段时间再用。
4.桔皮现象原因:a.UV油粘度高,流平性差。
b.涂布辊太粗不光滑且涂布量过大。
c.压力大小不均匀。
解决:a.降低粘度,加入流平剂及适当的溶剂。
b.选用细的涂布辊和减少涂布量。
c.调整压力。
5.发粘现象原因:a.紫外光强度不足或机速过快。
b.UV光油存贮时间过长。
c.不参与反应的稀释剂加入过多。
解决:a.固化速度小于0.5秒机速时,紫外光功率应不小于120w/cm。
b.加入一定量的UV 光油固化促进剂或更换光油。
c.注意合理使用稀释剂。
6.附着力差,涂不上或发花现象原因:a.印刷品油墨表面产生晶化油、喷粉等,水墨中合调墨油及燥油过多。
c.UV光油粘度太小或涂层太薄。
d.涂胶网纹辊太细 e.光固化条件不合适 f.UV光油本身附着力差及印刷品材料的附着性差。
解决:a.消除晶化层,打毛处理或油脂或加入5%的乳酸。
b.选择与UV油工艺参数相匹的油墨辅材、或用布擦拭。
c.使用粘度高的UV 光油,加大涂布量。
d.换用与该UV光油相匹配的网纹辊。
e.检查是否紫外光汞灯管老化,或机速不符,选择合适的干燥条件。
f.上底胶或更换特殊的UV光油或选择表面性能好的材料。
7.光泽不好亮度不够原因:a.UV光油粘度太小,涂层太薄,涂布不均。
b.印刷材料粗糙,吸收性太强。
UV胶印工艺主要问题及解决方法

UV胶印工艺主要问题及解决方法UV胶印印品在表面质地、保护性、耐磨性和生产效率等方面具有传统胶印印品无法比拟的优势,特别是用于塑料片材、金银卡纸等非吸收性材料印刷。
这些优势使那些应用UV胶印技术的印刷企业从竞争中脱颖而出。
但UV胶印工艺比较复杂,包装印刷企业如何处理UV胶印过程中存在的问题?打算采用UV胶印的包装印刷企业应该如何做好准备?要想让UV胶印更好地发挥作用,需要解决的主要问题有如下几点。
1.设计制版制作UV印刷的设计稿必须根据工单决定输出格式,如膜面正扫或反扫,输出网线数、网线角度等。
有些特殊印件要求更高,如3D印刷的分辨力要很高,网线角度必须与承印材料匹配,避免撞网;透明塑料片材与镀铝纸常需加印白墨,应注意印刷材料伸缩的影响,预先通过修正胶片以达到最佳品质。
2.附着力由于塑料片材或金银卡纸等承印物的渗透性能很差,对油墨的吸附力很弱,所以即使使用UV油墨印刷,油墨附着力也很差,印刷质量不高。
可以通过对材料做表面处理来解决。
3.油墨乳化UV油墨的水墨平衡宽容度很窄,印刷中容易造成油墨乳化、脏版,影响印刷品质。
解决方法:降低印刷速度,把印刷速度控制在5000~8000印/小时。
4.固化程度为了提高印品颜色饱和度,在塑料片材等承印物表面进行UV印刷时,印刷压力较大,墨层较厚,网点增大严重,这就使油墨不容易固化。
为了保证印刷质量,印刷压力不能做很大的调整。
解决办法是首先适度降低印刷速度,使UV灯照射时间适当加长,让油墨彻底固化;其次是调节UV灯管和承印物之间的距离,加大UV光照射强度,使油墨固化。
UV固化的有效波长范围是200~400nm,印刷车间中一些光源的波长也在此范围内,会导致油墨表层轻微固化,所以应注意环境光对UV油墨的影响。
5.色序安排UV胶印色序安排问题比较复杂。
由于着墨原理的限制,承印物上的墨层较薄,当需要比较厚实的墨层时,印品难以达到预期的复制效果。
例如四色叠印时,通常使用的印刷色序黑、青、品红、黄色,因为黑色几乎占满了所有空间,青、品红、黄的着墨力更低,总墨量不够,就会造成颜色不饱满。
- 1、下载文档前请自行甄别文档内容的完整性,平台不提供额外的编辑、内容补充、找答案等附加服务。
- 2、"仅部分预览"的文档,不可在线预览部分如存在完整性等问题,可反馈申请退款(可完整预览的文档不适用该条件!)。
- 3、如文档侵犯您的权益,请联系客服反馈,我们会尽快为您处理(人工客服工作时间:9:00-18:30)。
Q:当油墨固化过度的时候会发生什么?
A:有一种理论认为当油墨表面被UVLED过度照射时,就会变得越来越硬。
而当人们在这层变硬的墨膜上再印刷一种油墨,并进行第二次干燥的时候,上层油墨与下层油墨之间的附着力就会变得很差。
因此UVLED固化过度的墨膜不但灵活性差,而且还容易发生表面脆化。
Q:为什么有些UV油墨的固化速度要比其他油墨快?
A:UV油墨一般是根据某些承印物的特点和某些应用的特殊要求而配制的。
从化学的角度来看,油墨的固化速度越快,它在固化后的灵活性就越差。
UV油墨中所使用的化学原料不能与承印物表面发生反应,否则就会引起开裂破碎或脱层等现象。
这种油墨的固化速度通常都比较慢。
而那些专为生产卡片或硬塑料展板而设计的油墨则不需要具有如此高的灵活性,而且根据应用需要,它们的干燥速度也比较快。
大多数油墨都是根据应用需求而设计的。
Q:为什么当我使用UV油墨的时候聚碳酸酯(PC)薄膜会发黄?
A:聚碳酸酯对波长小于320纳米的UV光比较敏感。
薄膜表面的泛黄是由光氧化引起的分子链的断裂造成的。
塑料分子键吸收紫外光能,并产生自由基,这些自由基与空气中的氧气发生反应,就会改变塑料的外观和物理特性。
Q:如何避免或消除聚碳酸酯表面的泛黄?
A:如果用UV油墨在聚碳酸酯薄膜上进行印刷,那它表面的泛黄可以减少,但不能完全消除。
使用添加了铁或镓的固化灯泡能有效减少这种泛黄的出现。
此外,恰当地对每一种墨色进行固化也有助减少承印物在紫外光下的曝光时间,并降低聚碳酸酯薄膜发生变色的可能性。
Q:我们如何确保UV油墨的恰当固化?
A:墨膜在第一次过UVLED固化机是非常重要的。
恰当的固化能最大限度地避免承印物的变形、固化过度、重新湿润和固化不足等问题,并能对油墨与幽默或涂层与涂层之间的粘性进行优化。
为了测试UV油墨的固化效率,我们可以先以承印物所能允许的最低速度开机印刷,并对先印刷好的样张进行固化。
随后,将UVLED固化机的功率设置到油墨制造商规定的数值上。
而在对黑色和白色等不易固化的颜色进行处理的时候,我们还可以适当地调高固化灯的参数。
Q:如果色彩没有重叠,我是否应该关心固化过度的问题?
A:当一个墨膜的表面吸收了过多的UV光时就会出现固化过度的问题。
如果不能及时发现个解决这个问题,墨膜表面就会变得变得越来越硬。
当然,只要我们不进行彩色叠印,就不必过于关心这个问题。
但是,我们需要考虑到另外一个重要的因素,那就是被印刷的薄膜或承印物。
UV光能影响大多数承印物表面和某些对特定波长的紫外光敏感的塑料。
这种对特定波长的敏感性加上空气中的氧气可能导致塑料表面的退化。
承印物表面的分子键可能会被破坏,并导致UV 油墨与承印物之间的附着力失效。
承印物表面功能的退化是一个循序渐进的过程,而且与其接收到的紫外光能有着直接的关系。
Q:UV油墨是绿色油墨吗,为什么?
A:与溶剂型油墨相比,UV油墨的确比较环保。
UV油墨能够100%地变成固体,这意味着油墨中的所有组份都会变成最终的墨膜。
Q:增塑剂是如何影响油墨在PVC上的附着力的?
A:增塑剂是一种能使印刷材料变得更加柔软和灵活的化学品,它在PVC(聚氯乙烯)中的使用非常普遍。
添加到柔性PVC或其他塑料中的增塑剂的类型和数量主要取决于人们对印刷材料的机械、散热和电学性能的要求。
增塑剂有可能迁移到承印物表面,并影响油墨的附着。
残留在承印物表面的增塑剂是一种污染,会降低承印物的表面能。
表面上的污染越多,表面能就越低,它对油墨的附着力也就会越小。
要想避免这种情况,人们可以在印刷之前用温和的清洗溶剂清洁承印物,以提高它们的印刷适性。
Q:油墨的粘度是如何影响印刷适性的?
A:大多数油墨都有触变性,这意味着它们的粘度会随着时间和温度的变化而变化。
此外,环境温度越高,油墨的粘度也会越低。
丝网印刷油墨一般都能在印刷机上达到良好的效果,但根据印刷机设置和印前调整的不同,偶尔也会出现印刷适性的问题。
而且油墨在印刷机上的粘度与它在墨盒里的粘度也是不同的。
油墨制造商会为自己的产品设定一个特定的粘度范围。
对于过稀或粘度过低的油墨,用户还可以适当添加增稠剂;而对于过稠或粘度过高的油墨,用户也可以添加稀释剂。
此外,你还可以联系油墨供应商,索要产品信息。
Q:影响UV油墨的稳定性或保质期的因素有哪些?
A:影响油墨稳定性的一个重要因素就是对油墨的存储。
UV油墨通常都是储存在塑料墨盒而不是金属墨盒里的,因为塑料容器具有一定的透氧性,能确保油墨表面与容器盖之间存在一定的空气间隙。
这种空气间隙——特别是空气中的氧气——有助于最大限度地减少油墨的提前交联。
除了包装以外,油墨容器的温度也对于保持它们的稳定性有着至关重要的作用。
高温会引起油墨的提前反应和交联。
对原有油墨配方的调整也有可能会影响油墨在货架上的稳定性。
添加剂,特别是催化剂和光引发剂,可能会缩短油墨的保质期。
Q:如果用氮固化单元来固化彩色UV油墨,会发生什么?
A:用氮气来固化印刷品的固化系统早在十年前就已经出现了。
这些系统主要被用在纺织品和薄膜开关的固化过程中。
人们之所以要用氮气来取代氧气,主要是因为氧气会抑制油墨的固化。
但是,由于这类系统中灯泡的光照非常有限,所以对颜料或彩色油墨的固化效果也不是很好。