浅谈粉体性能指标在各工业的应用
粉体技术及设备现状与发展

粉体技术及设备现状与发展一、引言粉体技术是一门研究粉体物料的制备、加工、表征和应用的学科,广泛应用于化工、冶金、材料、能源等领域。
本文将详细介绍粉体技术及设备的现状与发展。
二、粉体技术的定义和特点粉体是指颗粒尺寸在1微米至1毫米之间的固体物料。
粉体技术是通过物料的细化、混合、分散和改性等工艺,使得粉体具有特定的物理和化学性质,以满足特定的工艺和应用要求。
粉体技术的特点包括粒度小、比表面积大、流动性好、分散性强等。
三、粉体技术的应用领域1. 化工领域:粉体技术在化工领域广泛应用于催化剂、吸附剂、颜料、涂料、染料等的制备与应用。
2. 冶金领域:粉体冶金技术是一种利用粉末作为原料,通过压制、烧结等工艺制备金属和合金制品的技术。
3. 材料领域:粉体技术在材料领域应用广泛,如陶瓷材料、复合材料、纳米材料等的制备与加工。
4. 能源领域:粉体技术在能源领域主要应用于燃烧、电池、储能材料等方面。
四、粉体技术的制备方法1. 粉碎法:通过机械力对物料进行破碎、粉碎,得到所需的粉体。
2. 分散法:通过悬浮剂、分散剂等对物料进行分散处理,使其呈现出均匀分散的状态。
3. 气相法:通过气相反应或气相沉积等方法,将气体中的物质转化为粉体。
4. 液相法:通过溶液中的沉淀、结晶等过程,制备出所需的粉体。
五、粉体技术设备的分类和特点1. 粉碎设备:包括破碎机、磨粉机等,用于物料的粉碎和细化。
2. 分散设备:包括搅拌机、分散机等,用于物料的分散和混合。
3. 干燥设备:包括喷雾干燥机、流化床干燥机等,用于物料的干燥和除湿。
4. 烧结设备:包括烧结炉、烧结机等,用于物料的烧结和热处理。
5. 表征设备:包括粒度分析仪、比表面积仪等,用于对粉体物料进行表征和分析。
六、粉体技术设备的发展趋势1. 自动化程度的提高:随着科技的发展,粉体技术设备将越来越多地采用自动化、智能化的控制系统,提高生产效率和产品质量。
2. 绿色环保的要求:粉体技术设备将越来越注重节能减排、资源循环利用等环保要求,以适应可持续发展的需要。
【精品文章】简析高纯氧化铝粉体的应用领域

简析高纯氧化铝粉体的应用领域
高纯氧化铝具有多孔性、高分散性、绝缘性、耐热性等特点,优势特征为卓越的硬度、高亮度、隔电性(非导体)、超级耐磨损性和高耐腐蚀性的特性。
通常所说的高纯氧化铝是指纯度99.9%以上,且粒度均匀的超微粉体材料。
一般而言3N的氧化铝粉体主要用于先进陶瓷,4N高纯氧化铝主要用于荧光粉,5N高纯氧化铝则广泛应用于蓝宝石晶体、锂电池隔膜、高级陶瓷、等离子显示屏(PDP)荧光粉及一些高性能材料等领域。
下文将对高纯氧化铝粉体的具体应用情况及其相关指标做简单说明。
图1 高纯氧化铝粉体
一、高纯氧化铝的应用
1、氧化铝单晶蓝宝石的应用
氧化铝单晶作为一种优良透波材料,在紫外、可见光、红外波段、微波都具有良好的透过率,可以满足多模式复合制导(电视、红外成像、雷达等)的要求,在军事工业等领域被用作窗口材料及整流罩部件,在光电通讯领域作为重要的窗口材料使用。
大尺寸蓝宝石单晶,其内部缺陷很少,没有晶界、孔隙等散射源,强度的损失很小,透波率很高,是目前透波部件的首选材料。
由于蓝宝石电绝缘、透明、易导热、硬度高,因此可以用来作为集成电路的衬底材料,可广泛用于发光二极管(LED)及微电子电路,从而替代高价的氮化硅衬底,制作超高速集成电路。
此外,蓝宝石可以做成光学传感器以及其它一些光学通信和光波导器。
超细粉体技术及应用现状

超细粉体技术及应用现状超细粉体不仅本身是一种功能材料,而且为新的功能材料的复合与开发展现了广阔的应用前景。
超细粉体由于粒度细、分布窄、质量均匀,因而具有比表面积大、表面活性高、化学反应速度快、溶解速度快、烧结体强度大以及独特的电性、磁性、光学性等,因而广泛应用于许多技术领域。
1、材料领域在电子信息行业中,将γ-F2O3超微粉用于磁性材料,可使得开发的录音带、录像带等磁记录产品具有稳定性好、图像清晰、信噪比高、失真小等优点。
在磁记录元件的涂层中用LaF3超细粉作为固体润滑剂,可使涂层及磁头寿命提高100多倍。
2、轻工、化工领域由氮化硅超细粉为原料制造的复合材料材,抗裂系数、抗折强度、耐压强度和硬度都都较好,在各工业行业中制造滑动轴承、滚动轴承用滚珠、俄罗斯产离心泵用端部密封件、切削工具、耐磨喷嘴、透平的叶片及耐火制品等。
钛酸四丁酯制备二氧化钛胶体,利用旋涂法形成透明的二氧化钛薄膜,并研究了影响成膜的因素。
结果表明表面活性剂能够改善膜的均匀度和增大薄膜的表面粗糙度。
光电性能测试发现薄膜厚度、薄膜表面粗糙度、烧结温度以及烧结时间等是影响二氧化钛薄膜光电性能的重要因素。
利用份菁作敏化剂,敏化后二氧化钛薄膜的光电性能得到很大的改善。
利用电泳法制备出大范围内均匀度好的TiO2超微粒薄膜。
用于新型太阳能电池,不仅能满足薄膜电极要有一定的厚度、大面积平整度好以及粗糙度因子高等要求,而且所需实验设备简单,操作方便,具有较高的实用价值。
3、中医药领域目前中药的超微粉碎以单味中药的粉碎研究较多,研究结果表明超微粉碎技术能够增加中药的溶出量,溶出率,有效成分的溶出和生物利用度。
而中药复方的超微粉碎主要是就其有效成分的溶出量,制剂稳定性以及是否提高药理作用等方面进行研究,另外,还有对超细粉在仁术健胃颗粒中的应用的研究,结果表明超微粉碎有利于制剂的成型,改善颗粒剂的稳定性和口感。
4、食品工业领域果蔬超微粉可作为食品原料添加到糖果、糕点、果冻、果酱、冰淇淋、奶制品、方便食品等多种食品中,增加食品的营养,增进食品的色香味,改善食品的品质,增添食品的品种。
粉体技术在无机材料领域的应用

粉体技术在无机材料领域的应用第一篇:粉体技术在无机材料领域的应用粉体技术在无机材料领域的应用摘要:以玻璃、水泥、陶瓷为主的传统无机材料已经满足不了时代的需求,新兴的粉体技术给无机材料的应用注入了新的活力。
本文主要总结了粉体技术对传统无机材料性能的改善以及在矿物加工方面的影响,特别是纳米粉体拓宽了无机材料在能源、环保、催化方面的应用。
关键词:矿物加工水泥粉体精细陶瓷纳米粉体Abstract:Mainly glass, cement, ceramic traditional inorganic material already can't satisfy the demand of The Times, the emerging technology of powder to the application of inorganic materials has injected new vitality.This paper mainly summarizes the to improve the performance of powder technology in the traditional inorganic materials and the influence of the mineral processing, especially nano widened the inorganic materials in energy, environmental protection, catalytic applications.Key words:Mineral processing cement powder fine ceramic nano powder引言粉体技术是随着近代科技的发展而发展起来的一门新兴科学技术,它是物理、化学、化工、机械、冶金、材料、生物、信息控制等学科的交叉学科。
粉体技术在无机材料领域的应用2
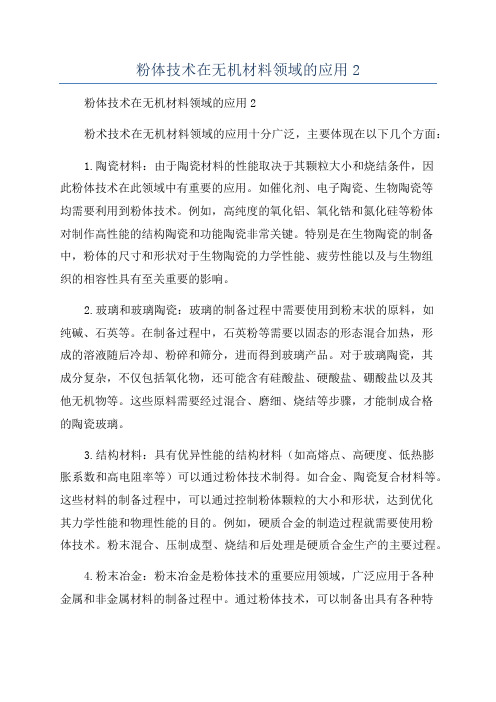
粉体技术在无机材料领域的应用2粉体技术在无机材料领域的应用2粉术技术在无机材料领域的应用十分广泛,主要体现在以下几个方面:1.陶瓷材料:由于陶瓷材料的性能取决于其颗粒大小和烧结条件,因此粉体技术在此领域中有重要的应用。
如催化剂、电子陶瓷、生物陶瓷等均需要利用到粉体技术。
例如,高纯度的氧化铝、氧化锆和氮化硅等粉体对制作高性能的结构陶瓷和功能陶瓷非常关键。
特别是在生物陶瓷的制备中,粉体的尺寸和形状对于生物陶瓷的力学性能、疲劳性能以及与生物组织的相容性具有至关重要的影响。
2.玻璃和玻璃陶瓷:玻璃的制备过程中需要使用到粉末状的原料,如纯碱、石英等。
在制备过程中,石英粉等需要以固态的形态混合加热,形成的溶液随后冷却、粉碎和筛分,进而得到玻璃产品。
对于玻璃陶瓷,其成分复杂,不仅包括氧化物,还可能含有硅酸盐、硬酸盐、硼酸盐以及其他无机物等。
这些原料需要经过混合、磨细、烧结等步骤,才能制成合格的陶瓷玻璃。
3.结构材料:具有优异性能的结构材料(如高熔点、高硬度、低热膨胀系数和高电阻率等)可以通过粉体技术制得。
如合金、陶瓷复合材料等。
这些材料的制备过程中,可以通过控制粉体颗粒的大小和形状,达到优化其力学性能和物理性能的目的。
例如,硬质合金的制造过程就需要使用粉体技术。
粉末混合、压制成型、烧结和后处理是硬质合金生产的主要过程。
4.粉末冶金:粉末冶金是粉体技术的重要应用领域,广泛应用于各种金属和非金属材料的制备过程中。
通过粉体技术,可以制备出具有各种特殊性能的新型材料,例如超细颗粒材料、纳米材料、多孔材料、复合材料等。
5.无机化工产品:许多无机化工产品,如颜料、填充剂、触媒等,其性质和应用效果也大大取决于粉末的性质。
例如,一些颜料就是由超微粉末制成,其颜色、饱和度和稳定性都与粉末的特性有关。
6.新能源材料:太阳能电池、燃料电池等新型能源装置的关键部件,电池电极就是由粉体材料制成的。
设计和制备这些粉体材料,需要将粉末的化学成分、颗粒形状和大小以及其在电极中的分布等因素考虑进去。
浅谈粉体粒度对各行业的应用影响
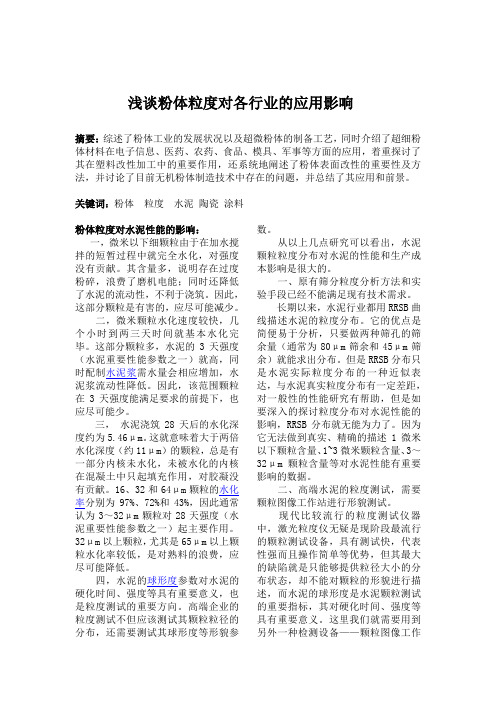
浅谈粉体粒度对各行业的应用影响摘要:综述了粉体工业的发展状况以及超微粉体的制备工艺,同时介绍了超细粉体材料在电子信息、医药、农药、食品、模具、军事等方面的应用,着重探讨了其在塑料改性加工中的重要作用,还系统地阐述了粉体表面改性的重要性及方法,并讨论了目前无机粉体制造技术中存在的问题,并总结了其应用和前景。
关键词:粉体粒度水泥陶瓷涂料粉体粒度对水泥性能的影响:一,微米以下细颗粒由于在加水搅拌的短暂过程中就完全水化,对强度没有贡献。
其含量多,说明存在过度粉碎,浪费了磨机电能;同时还降低了水泥的流动性,不利于浇筑。
因此,这部分颗粒是有害的,应尽可能减少。
二,微米颗粒水化速度较快,几个小时到两三天时间就基本水化完毕。
这部分颗粒多,水泥的3天强度(水泥重要性能参数之一)就高,同时配制水泥浆需水量会相应增加,水泥浆流动性降低。
因此,该范围颗粒在3天强度能满足要求的前提下,也应尽可能少。
三,水泥浇筑28天后的水化深度约为5.46μm。
这就意味着大于两倍水化深度(约11μm)的颗粒,总是有一部分内核未水化,未被水化的内核在混凝土中只起填充作用,对胶凝没有贡献。
16、32和64μm颗粒的水化率分别为97%、72%和43%,因此通常认为3~32μm颗粒对28天强度(水泥重要性能参数之一)起主要作用。
32μm以上颗粒,尤其是65μm以上颗粒水化率较低,是对熟料的浪费,应尽可能降低。
四,水泥的球形度参数对水泥的硬化时间、强度等具有重要意义,也是粒度测试的重要方向。
高端企业的粒度测试不但应该测试其颗粒粒径的分布,还需要测试其球形度等形貌参数。
从以上几点研究可以看出,水泥颗粒粒度分布对水泥的性能和生产成本影响是很大的。
一、原有筛分粒度分析方法和实验手段已经不能满足现有技术需求。
长期以来,水泥行业都用RRSB曲线描述水泥的粒度分布。
它的优点是简便易于分析,只要做两种筛孔的筛余量(通常为80μm筛余和45μm筛余)就能求出分布。
粉体技术在冶金工业中的应用

粉体技术在冶金工业中的应用粉末冶金是一门研究制造各种金属粉末以及粉末的原料通过成型、烧结和必要的后续处理制取金属材料和制品的科学技术。
1910年粉末可煅钨的出现标志着近代粉末冶金技术的诞生,其后30年粉末制品开始走向工业化和应用阶段,如:金属过滤器、烧结摩擦片、硬质合金等。
二战后是以一般的熔铸和加工法难以做成的粉末高速工具钢、不锈钢和高温合金为特征。
粉末冶金与传统的热机械加工法结合,有使现代不可或缺的材料优肯由粉末直接生产出来,而且性能大大超过熔铸材料。
工艺的优越性1.能制造处熔铸方法无法获得的材料和制品2.某些粉末冶金材料性能优于同成分熔铸金属3.粉末冶金经济效益好粉末冶金中的粉体技术1.原料制备的粉体技术原料制备主要包括:粉体退火、筛分、混合制粒、加润滑剂(1)退火粉体退火可使氧化物还原,降低碳和其他杂质的含量,提高粉体的纯度,消除粉体加工硬化、稳定粉体晶体结构,一般用还原性气氛,有时可以用惰性或真空。
(2)筛分用标准筛网制成筛子和振动筛筛分,其目的是吧颗粒大小不同的原始粉末进行分级(3)加成型剂、润滑剂在压制成型前粉体混合料中常添加一些改善压制过程的物质。
为了降低成型时粉末颗粒与模壁和模冲间摩擦,减少压模磨损和有利于脱模,常加入润滑剂。
(4)混合混合是将二种或二种以上不同成分的粉末混合均匀的过程。
混合主要以机械法为主成型工艺中的粉体技术粉末成型方法很多,根据成型时是否以外部施加压力可分为1:压制成型:如挤压、振动压制。
2:无压成型:如粉浆浇注、松装烧结、粉浆涂敷。
(1)金属粉末压制现象粉末在压模内所受压力的分布是不均匀的,因为粉末颗粒之间彼此摩擦、相互锲住,使得压力沿模向比传递比垂直方向困难的多,粉末在模壁压制过程中产生摩擦力,此力使压坯各部分致密度有所不同。
(2)金属粉末压制时的位移与变形粉末在压模内经受压力后就变得较密实且具有一定的形状和强度,这是由于在压制过程中,粉末之间空间大大降低,彼此接触显著增加。
粉体技术在制药工业中的应用分析
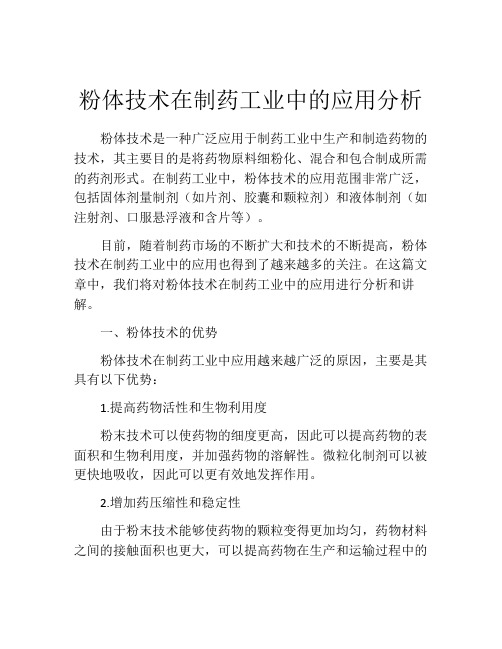
粉体技术在制药工业中的应用分析粉体技术是一种广泛应用于制药工业中生产和制造药物的技术,其主要目的是将药物原料细粉化、混合和包合制成所需的药剂形式。
在制药工业中,粉体技术的应用范围非常广泛,包括固体剂量制剂(如片剂、胶囊和颗粒剂)和液体制剂(如注射剂、口服悬浮液和含片等)。
目前,随着制药市场的不断扩大和技术的不断提高,粉体技术在制药工业中的应用也得到了越来越多的关注。
在这篇文章中,我们将对粉体技术在制药工业中的应用进行分析和讲解。
一、粉体技术的优势粉体技术在制药工业中应用越来越广泛的原因,主要是其具有以下优势:1.提高药物活性和生物利用度粉末技术可以使药物的细度更高,因此可以提高药物的表面积和生物利用度,并加强药物的溶解性。
微粒化制剂可以被更快地吸收,因此可以更有效地发挥作用。
2.增加药压缩性和稳定性由于粉末技术能够使药物的颗粒变得更加均匀,药物材料之间的接触面积也更大,可以提高药物在生产和运输过程中的稳定性。
同时,通过控制粉末技术的工艺参数,也可以增加药物的压缩性,从而提高药物的制造效率。
3.提高药物的可控性粉末技术可以使药物成分更加均匀地混合,从而提高药物的可控性。
这对制药行业那些需要精确测量的药物非常重要,粉末技术能够确保药物中各种成分的准确性。
4.适合于多种药物形式粉末技术可以生产各种药物形式,如胶囊、片剂、散粉和液体制剂等,因此适用范围也更加广泛。
二、各种粉体技术的应用1.喷雾干燥技术喷雾干燥技术是目前应用最广泛的粉体技术之一。
该技术可以将液态药物蒸发成微粒,从而制成干燥的粉末。
喷雾干燥技术不仅可以应用于制造固体剂量制剂,如颗粒和胶囊,同时也可用于制造食品添加剂、化妆品和工业原料等。
2.冷冻干燥技术冷冻干燥技术主要用于制造混合物和具有敏感成分的药物。
该技术可以将溶液或混合物通过冷冻去除多余的水分,然后将其真空蒸发干燥,从而制成粉末。
冷冻干燥技术可以减小药物在干燥过程中的分解和降解,从而提高药物的稳定性。
- 1、下载文档前请自行甄别文档内容的完整性,平台不提供额外的编辑、内容补充、找答案等附加服务。
- 2、"仅部分预览"的文档,不可在线预览部分如存在完整性等问题,可反馈申请退款(可完整预览的文档不适用该条件!)。
- 3、如文档侵犯您的权益,请联系客服反馈,我们会尽快为您处理(人工客服工作时间:9:00-18:30)。
浅谈粉体性能指标在各工业的应用王庆贺合肥学院10化工系粉体1班摘要:随着现代工业的发展,技术的要求越来越来高,粉体技术作为近年来备受瞩的新兴技术,在各工业领域的应用越来越广泛,也越来越重要,人们对粒度指标的要求越来越高,同时也出现了新型的,集多门现代科学于一体的粒度测量仪器,粉体粒度指标在工业各个方面都有应用,例如日化工业,医药制造,水泥,陶瓷材料等。
粉体是粉体产业产品最重要的技术指标,随着科学技术的发展。
关键词:粉体指标日化工业医药制造水泥陶瓷一、粉体的基本概念和性质1.1粉体的基本概念粉体是指无数个固体粒子的集合体,粉体学是研究粉体的基本性质及其应用的科学。
粒子是粉体运动的最小单元,通常所说的“粉”、“粒”都属于粉体的范畴,通常将≤100 μm 的粒子叫”,>100 μm 的粒子叫“粒”。
组成粉体的单元粒子可能是单体的结晶,称为一级粒子;也可能是多个单体粒子聚结在一起的粒子,称为二级粒子。
在制药行业中,常用的粒子大小范围为从药物原料粉的 1 μm 到片剂的10 mm。
1.2 粉体的性质物态有3 种,即固体、液体、气体。
液体与气体具有流动性,而固体没有流动性;但把固体粉碎成颗粒的聚集体之后则具有与液体相类似的流动性,具有与气体相类似的压缩性,也具有固体的抗形变能力,所以有人把粉体列为“第四种物态”来进行研究[2]。
粉体的基本性质有:粒度及粒度分布、粒子的形态、比表面积、空隙率与密度、流动性与充填性、吸湿性等。
在粉体的处理过程中,第2 期崔福德等: 粉体技术在制药工业中的应用69 即使是单一物质,如果组成粉体的各个单元粒子的形状、大小、粘附性等不同,粉体整体的性质将产生很大的差异。
因此很难将粉体的各种性质如气体、液体那样用数学模式来描述或定义。
但是粉体技术也能为固体制剂的处方设计、生产过程以及质量控制等诸方面提供重要的理论依据和试验方法. 二、粉体在化妆品总的应用彩妆按照分散技术不同,可分类为粉体(powder)彩妆、乳化彩妆、油分散彩妆。
粉体的作用是,为化妆品赋予色调,或构成产品的骨骼。
本文欲从粉体的基本特性着手,带大家了解使用在化妆品上的粉体的特性及功能、用于改善粉体的功能的表面处理方法。
2.1. 化妆品用粉体的特性化妆品用的粉体可以分为无机颜料(体质颜料、白色颜料、彩色颜料)、有机颜料、天然颜料、珠光颜料等等。
体质颜料:是构成骨骼的原料,以天然的粘土矿物如云母、滑石粉最具有代表性,另外还有高岭土(kaolin)、碳酸钙、碳酸镁等等。
有机颜料:以tar color为代表,可分为染料、色淀颜料、颜料等3个类别。
染料(Dye):溶于水或者溶剂,具有染色功能的原料。
按照发色团的化学构造分类(水溶性染料、油溶性染料)。
颜料(Pigments):色素自身构造不携带可溶性基,不溶于水、油、溶媒等。
按构造可分类为偶氮(Azo)系、靛蓝(indigo)系、酞花菁(Phthalocyanine)系颜料等。
与色淀颜料相比,着色力、隐蔽力、耐光性能好。
色淀颜料(Lake):在燃料上使用了沉淀剂,结合金属盐或特殊的有机酸,进行不溶性处理的色素。
随着合成技术的进步,不断有新色素被开发出来,但化妆品配方上只有那些安全性(Safety)得到充分验证的色素才可以使用。
无机颜料(Inorganic Pigment):又称为矿物性颜料,以前是粉碎天然矿物当颜料使用,但现在多数是使用合成出来的无机化合物。
优点是耐光、耐热性能良好,不溶于有机溶媒。
缺点是鲜明感与着色力较有机颜料弱(Iron Oxides,Ultramarines,Chrom oxide greens,TiO2,ZnO,Chromium hydroxide green)。
虽然与有机颜料相比,无机颜料的颜色种类少,但也广泛应用在各种粉底液、粉、眼影等彩妆产品上。
天然色素:从动植物提取的色素,与合成色素相比着色力、耐光、耐热、耐药品性能弱。
彩妆上广泛应用到的胭脂红(carmine),因胭脂虫的栖息地——亚马逊被不断破坏而被迫减产。
珠光(Pearl Pigment):应用于需要闪亮和光泽的唇膏、指甲油、眼影、腮红等产品,近来还应用到粉饼、隔离霜、粉底液、化妆水、面霜、睫毛膏等产品上。
2.2 为了改善粉体特性而进行的表面处理大部分的颜料表面都带有氢氧基,因为这种特性,化妆层很容易被人体的汗水或皮脂弄花。
为了改善这种现象,可以使用表面处理物质与氢氧基进行化学结合,让颜料表面拥有疏水性。
对颜料进行表面处理的另外一个目的是,提升原料的分散性,改善原料的耐光性、耐溶剂性、抑制表面活性等方面问题,并赋予新的使用感或特性(见表4)。
颜料表面处理技术始于70年代中期的日本,在80年代以后普及全球。
以上简述了粉体的基本特性。
我们在进行化妆品配方研发时,应充分理解各种粉体的特性,按照不同国家或地区消费者喜好的彩妆流行,选用不同的粉体原料。
目前,随着科技的进步,粉体的开发已经开始结合地质学、光学、食品工程、医药等其他领域的技术,展现出新的生命力。
三、粉体性质对制剂工艺的影响3.1 对混合均匀度的影响固体药物制剂产品往往由多种成分混合而成,如复方制剂或加入的药用辅料等。
为了保证制剂中药物含量的均匀性,需对各个成分进行粉碎、过筛使成一定粒度的粉末之后进行混合。
从粉体性质的角度考虑,影响混合均匀度的因素有:a.粒子的大小:粉体的混合虽然达不到像溶液的分子混合程度,但只要各组分的粒径足够小,且粒子间作用力足够小时就可达到较理想的均匀度;b.各组分间粒径差与密度差:在混合过程中,粒径较大的颗粒上浮,粒径较小的颗粒下漏;密度较大的颗粒下沉,密度较小的颗粒上浮。
不仅给混合过程带来困难,而且已混合好的物料也能在输送过程中再次分离。
因此混合过程中应尽量使混合物料的密度和粒度相接近;c.粒子形态和表面状态:形态不规则、表面不光滑的粒子混合时虽不易混合均匀,但一旦混合后不易分离,易于保持均匀的混合状态;但在混合物中混有表面光滑的球状颗粒时其流动性过强而易于分离出来;d.静电性和表面能:混合过程往往在粉末状态下进行,如果空气状态比较干燥(如相对湿度小于40%)就容易产生静电而聚集;粉末状态的表面能较大也易于聚集,使混合带来较大的困难。
这种情况发生时宜采用过筛混合法,使聚集的粉末团在过筛过程中破碎,并加入润滑剂或表面活性剂以防止粉末聚集。
3.2 对固体制剂分剂量的影响片剂、胶囊剂、冲剂等固体制剂在生产中为了快速而自动分剂量一般采用容积法,因此固体物料的流动性、充填性对分剂量的准确性产生重要影响。
3.2.1 流动性影响粉体的流动性与粒子大小、粒度分布、粒子形态、表面状态、堆密度等有关,可用休止角[ α]、内部摩擦角[ θ]、剪切粘着力[ C] 、久野—川北方程的参数[ K、a、b] 、流动指数综合指数[ I]法等评价。
常用的方法是测休止角,一般认为休止角α<30°时流动性很好,α>45°时流动性差。
但实际生产中α<40°就可满足分剂量的生产要求。
通常可以采用以下方法改善粉体的流动:a.造粒:粉体过细,分散度和表面自由能很高,容易发生自发的附着和凝聚从而影响其流动性,造粒后表面能小、不易聚集,可以改善流动性。
一般情况下,粒径小于100 μm 时流动性差,大于200 μm时流动性较好,如粉末状乳糖,粒径小于74 μm 时,休止角为60°、堆密度为0.34 g·cm-3,流动性很差;但制成粒径在149~420 μm 的颗粒后其堆密度变为0.5 g·cm-3、休止角为38°,大大改善了乳糖的流动性;b.增大颗粒密度:颗粒自重大于粒子间粘着力时可以流动,粘着力大于颗粒自重时不易流动,显然密度大的粒子群其流动性好。
如果采用不同造粒方法或不同种类、不同量的粘合剂,就可以改变物料的堆密度,从而改善流动性。
生产时堆密度大于0.4 g·cm-3 可满足较好的流动性;c.加入助流剂:滑石粉、微粉硅胶等粉末附着在颗粒表面可以大大改善物料的流动性,但不能加入过多,过多反而降低流动性,常用范围为0.1%~2%。
优质微粉硅胶的粒径极细,其比表面积高达200 m2·g-1 以上,用量仅为颗粒量的0.1% 即可取得满意的效果。
另外,加入药物或辅料的细粉也可以产生助流剂的作用。
但是关于装量均一性与粉体流动性之间的关系,有不同的看法。
流动性差的粉体由于密度差异,装量差异会较大;流动性好的粉体不能充分振实,也能会导致较大的装量差异;也有人认为粉体的流动性与装量差异无关。
Linda A.Felton 等[3]考察了微晶纤维素(MCC)和硅酸化微晶纤维素(SMCC)填充硬胶囊的载药量和装量差异。
结果表明,密度较大、流动性好的SMCC 载药量大,装量差异小,但发现流动性不同的几种处方装量差异并不显著。
3.2.2 充填性影响粉体的充填性是粉体集合体的基本性质,在胶囊、片剂的装填过程中具有重要的意义。
物料颗粒的大小、形状、粒度分布、堆密度及空隙率等可直观地反映出其充填性。
当颗粒的粒度分布很宽时,由于大、小粒子易发生分离现象而使堆密度产生差异,充填不均匀,容易造成分剂量的差异;3.3 对压缩成形性的影响压缩成形性表示粉体在压力下减少体积、紧密结合形成一定形状的能力。
压缩成形性的评价方法很多,如压痕硬度、径向抗张强度、轴向强度、弯曲强度、破碎功等,也有在粉末的压缩过程中测定应力缓和值、粘结指数、脆碎指数、可压性参数等,其中最常用而简便的方法是测定其径向破碎力——硬度,与单位面积的破碎力——抗张强度。
四、粉体性质对制剂质量的影响4.1粉体性质对制剂质量的影响固体制剂的最终命运是崩解、释药和被人体吸收,其中崩解是药物溶出及发挥疗效的首要条件,而崩解的前提则是药物制剂必须能被水溶液所润湿。
因此水渗入片剂内部的速度与程度对崩解起到决定性作用,而这又与片剂的孔隙径、孔隙数目以及毛细管壁的润湿性等有关。
片剂的孔隙率不但与物料性质有关,即易产生塑性变形的物质压片后孔隙率小难以崩解,弹性变形的物料压缩后孔隙率较大易于崩解;还与压缩过程有关,在一定压力范围内,压力越大,压缩时间越长,片剂的孔隙率越小,越难以崩解。
物料的润湿性很差,将很难使水通过毛细管渗入到片剂内部,则片剂难以崩解。
常用于润滑剂的硬脂酸镁具有较强的疏水性,用量不当会严影响片剂的崩解度,必要时可加入表面活性剂以改善片剂的润湿性,促进水的渗入而加快崩解速度和溶出度。
如用阿拉伯胶作粘合剂,喷雾干燥,可提高水杨酸的溶出度;磺胺药物加泊洛沙姆可显著增加溶出度;脂溶性药物同乳糖混合,也可提高药物的溶出度[4]。
4.2对生物利用度和疗效的影响临床上,药物不论以何种形式给药,药物粒径的大小都会影响药物从剂型中的释放,进而影响到疗效。