轧辊产生微裂纹原因
轧辊爆裂原因

轧辊爆裂是轧制生产中常见的一种失效形式,可能会导致严重的生产事故和经济损失。
以下是几种可能导致轧辊爆裂的原因:
1. 轧辊材质不适:轧辊材质应该具有高的强度、韧性和耐磨性。
如果材料不符合轧辊的使用要求,则会引起轧辊疲劳失效和裂纹扩展,导致轧辊爆裂。
2. 轧辊表面缺陷:轧辊表面缺陷、裂纹、凹坑等缺陷也可能导致爆裂。
这些缺陷将在轧制过程中扩展并使轧辊破裂。
3. 轧辊使用过程中温度过高:过高的轧辊表面温度会使轧辊产生变形和热疲劳裂纹,最终导致轧辊爆裂。
4. 轧辊使用寿命过长:轧辊在使用过程中会不可避免地出现疲劳损伤和磨损,长期使用可能导致轧辊的强度减小,出现裂纹和爆裂。
5. 非正常操作:轧辊在使用过程中需要严格遵循规定的操作程序和参数范围。
如果操作不当,例如过多受力或者运转速度过快,就有可能导致轧辊疲劳损伤和爆裂。
综上所述,预防轧辊爆裂需要严格控制轧辊的材质、缺陷、温度、使用寿命和操作规范,定期检测和维修轧辊以及合理调整轧制过程参数等措施。
热轧轧辊剥落或断裂的原因及预防方法探究

热轧轧辊剥落或断裂的原因及预防方法探究热轧轧辊在钢铁生产中起着至关重要的作用,是完成金属板材加工的重要设备之一。
在使用过程中,热轧轧辊剥落或断裂的现象时有发生,给生产带来了严重的影响。
针对这一问题,本文将从热轧轧辊剥落或断裂的原因及预防方法进行探究,以期为相关企业提供参考。
一、热轧轧辊剥落或断裂的原因1. 设备质量不达标热轧轧辊作为重要的设备之一,其质量必须达到相应的标准。
如果生产厂家在生产过程中使用了劣质的材料或者工艺不合格,就会导致轧辊的质量不达标,容易出现剥落或断裂的现象。
2. 设备磨损严重长时间的使用会造成轧辊表面的磨损,特别是在高温、高压力的环境下,磨损会更加严重。
一旦轧辊表面磨损过度,就会影响其正常的工作状态,进而产生剥落或断裂的风险。
3. 工艺参数设置不当热轧轧辊在使用过程中,需要根据所加工金属的性质和厚度等因素设置相应的工艺参数,如温度、压力等。
如果工艺参数设置不当,就会导致轧辊在工作过程中承受过大的压力或温度,从而容易出现剥落或断裂的情况。
4. 操作不当操作人员在使用热轧轧辊的过程中,如果操作不当,容易对设备造成损坏。
比如在装卸轧辊时使用不当的工具或方法,会导致轧辊受力不均,从而产生损坏的可能性。
5. 周期性检修不足热轧轧辊作为重要设备,需要定期进行检修和维护工作。
如果企业在这方面投入不足,就会导致轧辊出现各种问题,包括剥落或断裂现象。
二、预防方法探究1. 选购正规厂家生产的轧辊企业在选购热轧轧辊时,应该选择质量可靠的正规厂家生产的产品,避免使用劣质轧辊。
2. 定期维护检修企业应该对热轧轧辊进行定期的维护检修工作,包括表面磨损的修复、工艺参数的调整和润滑等工作,以确保轧辊处于最佳的工作状态。
3. 合理设置工艺参数在使用热轧轧辊时,企业应该合理设置工艺参数,根据加工的金属材料性质和厚度等因素进行调整,避免出现过大的压力或温度对轧辊造成损坏。
4. 加强操作培训企业应该加强对操作人员的培训,提高其对热轧轧辊设备的操作技能和安全意识,避免因为操作不当对轧辊造成损坏。
冷轧工作辊裂纹及剥落原因及预防

图 4 表层裂纹引起的剥落 海滩痕
图 3 机械裂纹
预防机械裂纹的措施有 3 个。1)确保带钢表面清洁无 异物,减少杂物介入。2)提高轧材表面质量,减少氧化皮残 留。3)加强乳化液检测系统和平衡过滤系统的点检。总之, 通过控制酸洗原料、乳化液指标、轧辊冷却等,可以减少轧 制过程中出现打滑、辊印、局部热擦伤等缺陷,提高板材表 面质量,减少轧机事故停机,同时降低辊耗。
一般情况下,打滑、粘钢等轧制事故,会引起辊身一条 母线上或者辊身局部区域内深度和开口都较大的裂纹,一旦 发生该类事故,则必须马上停止轧制,将轧辊换下,并对事 故辊进行严格的超声波、涡流探伤和磨削处理,必须保证表 面裂纹完全消除,并利用超声波探伤,检测轧辊内部的情况。
伤。4)对每支磨削完成的轧辊采用涡流探伤或表波探伤进行 检测,要确保每支要上机的轧辊不存在任何导致疲劳剥落的 可能性。
1.2 热裂纹
在生产过程中由于辊面局部温升快,最高温度超过轧辊 材质热处理工艺的最终回火温度,冷却后相当于再次回火, 表面硬度下降形成软点区,由于其与周边热膨胀系数不同, 这部分应力叠加,导致薄弱环节产生细小的网状裂纹 [1]。一 般情况下网状裂纹深度较浅,约 1.2 mm 以下(如图 2 所示)。 虽然这些裂纹深度浅,但是如果不及时处理和维护,在后期 的生产轧制中,受到外力、热应力等综合影响,很容易发展 成为如辊面粗化、辊面小掉肉等缺陷,严重时会引起辊面剥 落或断辊,所以一旦发现该类缺陷,在使用过程中重点关注 并及时处理。
2.2 材质缺陷引发的剥落
在制造轧辊的过程中,一些不规则的材料在坯料内有 可能成为轧辊内部残留的夹杂物。这些夹杂物可能是耐火材 料、残渣,也可能是坯料本身的的局部偏析和孔隙等 [3]。这 些内部缺陷,在轧辊使用过程中,都可能成为应力集中的根 源,最终将导致轧辊辊身剥落严重,甚至会出现断辊。轧辊 表层下缺陷引发的剥落,大部分在断裂面上呈现出类似鱼眼 纹,很容易进行辨别,如图 5 所示。可以看出该疲劳是从单 点开始蔓延的,并产生波浪状近似椭圆形的疲劳痕迹。这种 疲劳痕迹只有内部材料缺陷引发的迹象,并没有任何其它剥 落的源头。
轧辊产生微裂纹原因
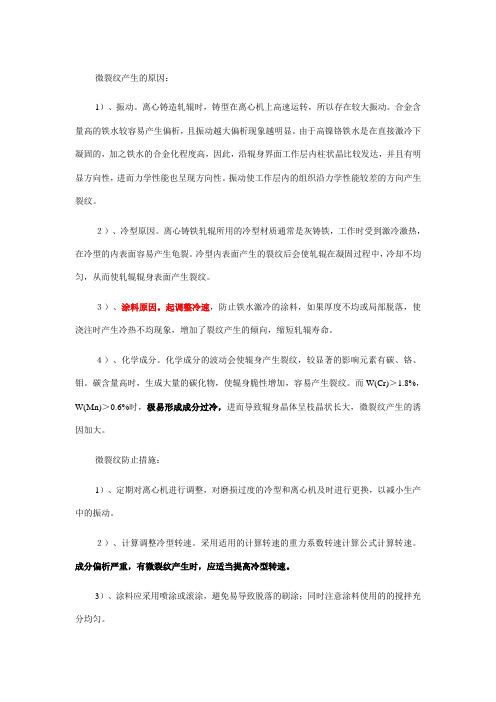
微裂纹产生的原因:1)、振动。
离心铸造轧辊时,铸型在离心机上高速运转,所以存在较大振动。
合金含量高的铁水较容易产生偏析,且振动越大偏析现象越明显。
由于高镍铬铁水是在直接激冷下凝固的,加之铁水的合金化程度高,因此,沿辊身界面工作层内柱状晶比较发达,并且有明显方向性,进而力学性能也呈现方向性。
振动使工作层内的组织沿力学性能较差的方向产生裂纹。
2)、冷型原因。
离心铸铁轧辊所用的冷型材质通常是灰铸铁,工作时受到激冷激热,在冷型的内表面容易产生龟裂。
冷型内表面产生的裂纹后会使轧辊在凝固过程中,冷却不均匀,从而使轧辊辊身表面产生裂纹。
3)、涂料原因。
起调整冷速,防止铁水激冷的涂料,如果厚度不均或局部脱落,使浇注时产生冷热不均现象,增加了裂纹产生的倾向,缩短轧辊寿命。
4)、化学成分。
化学成分的波动会使辊身产生裂纹,较显著的影响元素有碳、铬、钼。
碳含量高时,生成大量的碳化物,使辊身脆性增加,容易产生裂纹。
而W(Cr)>1.8%,W(Mn)>0.6%时,极易形成成分过冷,进而导致辊身晶体呈枝晶状长大,微裂纹产生的诱因加大。
微裂纹防止措施:1)、定期对离心机进行调整,对磨损过度的冷型和离心机及时进行更换,以减小生产中的振动。
2)、计算调整冷型转速。
采用适用的计算转速的重力系数转速计算公式计算转速。
成分偏析严重,有微裂纹产生时,应适当提高冷型转速。
3)、涂料应采用喷涂或滚涂,避免易导致脱落的刷涂;同时注意涂料使用的的搅拌充分均匀。
4)、严控轧辊化学成分,控制W(C):3.0-3.5%;W(Cr):1.6-1.8%;W(Mn):0.2-0.6%。
冷轧生产企业轧辊缺陷产生原因及防范措施

冷轧生产企业轧辊缺陷产生原因及防范措施轧辊是轧钢生产中的一种大型工具,其性能与质量将直接影响轧机产量和产品质量,其消耗在轧钢生产中占很大比例。
因此,轧辊的使用与管理在冷轧的生产中至关重要。
本文所列舉的冷连轧机为四机架六辊UCM(Universal Crown Mill)轧机,设计产量为152.8万t,其技术从国外成套引进,是目前国内装备水平较高的冷轧机之一。
自投产以后,多次与国内外的轧辊专家进行了技术交流,以提高轧辊的使用和管理水平。
研究冷轧辊缺陷产生的原因,并采取相应的具体措施,以便降低轧辊消耗,对降低成本和稳定生产有着重要的意义。
1冷轧辊缺陷的主要形式当前我们所使用轧辊来自于日立金属、美国电钢、英国轧辊、中国一重、邢台轧辊和常冶轧辊等几家轧辊生产制造厂,其材质为3Cr,5Cr和4CrMo锻钢。
目前出现的轧辊缺陷按照所产生的形态可以分成软点、剥落(爆辊)和内部裂纹等三大类。
1·1 轧辊软点轧辊表面的某些地方会显示出比轧辊表面其它地方硬度值变化较大情况。
通常这些软点区域的硬度值要比基体材料的硬度低20HS。
一般情况下软点区域用肉眼是分辨不出来的,但是经过硝酸酒精腐蚀以后,就会显示出来,呈现一片暗色区域(见图1所示)。
在某些情况下,软点疵瑕也可以保持有硬化情况和回火色(兰色/棕色)。
1·2 轧辊剥落轧辊剥落就是指轧辊辊身的某个区域从辊身上分离出来的现象。
剥落按照产生的原因不同可分成下述几类。
1.2.1 轧辊表面剥落轧辊表面剥落可通过裂纹表面的“破损”轨迹来鉴别。
这种疲劳“破损”轨迹的显著特征是具有典型疲劳痕(海滩纹见图2所示)或在疲劳裂纹面上的“扇形”裂纹流线。
疲劳“破损”轨迹蔓延的方向与轧制时轧辊旋转的方向相反。
1.2.2 接触应力引发的剥落由于轧机的负荷以及轧辊在接触点上的局部挤压,造成的最大组合剪切应力(通常称作“赫兹应力”)位于轧辊表面之下的某个较小区域中。
多处的裂纹可以引发并在赫兹应力超过轧辊的抗拉强度时,在表面之下位置发生弥散,导致剥落的产生,这会通过两种模式发生。
锻钢轧辊缺陷产生的原因及对策

锻钢轧辊在轧制中出现问题的原因及对策目录页数1. 引言 42. 轧辊表面迹象A. 夹杂5~6B. 橘皮状轧辊表面7~8C. 辊印9~12D. 软点13~18E. 热裂纹i. 热轧机工作辊19ii. 冷轧机工作辊20~273. 剥落A. 表面迹像28~46B. 表皮下引发i. 与材质有关47~49ii. 接触应力a. 一般机理50~52b. 冷轧机工作辊53~61c. 热轧机工作辊62~64d. 支撑辊65~704. 辊颈断裂A. 表面迹像71~72i. 辊颈应力计算73~77B. 表皮下引发i. 轧辊设计或材料质量78~81C. 辊颈修复82~85D. 瞬时发生i. 深置缺陷86~87ii. 轧机过载88~905. 辊身断裂A. 疲劳--- 深置缺陷91~93B. 瞬时i. 轧机过载94~95ii. 深置缺陷96~976. 轧辊检测98A. 涡流探伤99~100B. 表面波超声波探伤101~105C. 着色渗入探伤106~108D. 刻蚀探伤109~111E. 磁粉探伤112~113F. 硬度检验114~1187. 轧辊处理和储存1198. 轧辊各部位的英文名称120~121引言在轧钢生产中的轧辊性能及质量直接影响轧机产量和产品质量。
因为轧辊采购费用在轧钢厂生产成本中占有较大比重,也是影响轧制成本的重要因素。
本书的目的是针对锻钢轧辊在轧制中可能出现的相关问题,并就问题的类型,特徵,样例(照片,图解),产生机理及预防措施等进行分析。
仅供有关人员参考。
锻造轧辊的无损探伤(NTD)对轧辊生产厂家和轧辊用户都非常重要。
轧辊生产厂家在轧辊热处理以及随后的精加工之前用NDT无损探伤,来确认轧辊的表面和内部是否合格。
轧辊用户(轧辊车间)利用NDT无损探伤确保研磨切削部分满足进一步使用之前的轧辊表面要求。
NDT 无损探伤以及其应用,可以作为最佳化轧辊维护过程的管理方法之一。
轧辊的处理和储存也是轧辊问题发生的因素。
冷轧辊常见缺陷及产生原因是什么

冷轧辊运行中常见的缺陷及产生原因如下:
格坑。
带钢焊缝质量不好,或表面有异物。
粘辊。
局部压下量过大,断片、堆钢、折叠,带钢板形不好或辊身表面硬度低。
裂纹。
粘辊等过热缺陷造成局部压下过大,冷却不好,轧辊表面杂物粗大。
勒辊。
辊身两端压下不一致,带钢浪形、跑偏、辊身表面硬度低。
大面积带状剥落。
由于轧辊辊身有微裂纹,在循环轧制应力的作用下,经过二次疲劳裂纹的发展造成。
掉肉。
辊身表面有微裂纹,辊身表层局部严重过热,辊身表层有大夹杂物等缺陷在轧制应力作用下,经疲劳裂纹发展成掉肉。
辊身两侧环状裂纹。
轧制时,两端压下严重不均,轧辊淬火质量不好。
工作辊轴承抱辊。
轴承润滑不好,未及时加油,轴承密封不好,辊身两端压下严重压偏。
断辊。
轧辊内部残余拉应力大,轧辊中心有裂纹等缺陷,辊身两端压下严重。
热轧轧辊的失效原因及科学预防

热轧轧辊的失效原因及科学预防摘要轧辊的失效形式主要包括剥落、断裂、裂纹等,无论哪种失效都会影响轧辊的使用寿命。
因此,为延长轧辊使用寿命、降低轧辊消耗,必须要针对不同的失效原因,采取科学性、针对性的预防措施。
基于此,本文对轧辊失效的原因进行了阐述,并分析了科学的预防措施,旨在为提高轧辊的使用寿命,提升轧辊质量,提供参考借鉴。
关键词轧辊失效;应力;剥落;裂纹;预防1 轧辊常见失效形式及原因1.1 剥落剥落的发生不是瞬间的,而是需要一个疲劳的过程,轧辊的非正常失效形式中剥落占比达60%~70%,属于较为严重的生产事故,严重时会导致轧辊报废。
其主要形式及原因为:首先,马鞍形剥落。
在对薄而硬的带钢进行轧制时,由于压下比大,使得在承受较大负荷的作用下而产生交变应力、残留应力及热应力,会使拉应力变大,一旦超过轧辊芯部材质的疲劳极限,就会导致出现微裂纹。
裂纹的进一步蔓延,就会表现在辊身表面,致使产生马鞍形剥落。
其次,带状疲劳剥落。
轧辊局部过大超负荷运转时,当大于轧辊外层的抗剪切强度极限时,就会出现裂纹,在进行轧制过程中,持续的疲劳状态会引发裂纹的增多,致使辊身局部出现大面积剥落。
另外,对于服役期较长的工作辊和支承辊,中间磨损量大于两端磨损量,致使辊身两端交变剪应力不断增大,加速了疲劳破坏,从而产生带状疲劳剥落。
另外,表层/芯部结合层处脱落。
在发生轧制事故时,局部出现过大负荷,导致外部与芯部材质出现脱落,随着这一分割面的逐渐延伸,一旦达到临界尺寸,就会出现二次脱落。
这种形式的剥落出现通常有以下几种情况,表层和芯部间有氧化层残留,结合层留有杂质、碳化物或是气孔等。
1.2 断裂轧制过程中的断辊事故时有发生,断裂通常发生在辊身、辊颈及轴头部位。
当钢种以及生产工艺存在差异時,断裂的部位也会出现差异。
通常,断辊是由于疲劳裂纹所致,也可能会出现一次性脆断,具体分析如下:(1)内因在轧辊的材质内部存在缺陷时,引发轧辊断裂的可能性也会增大,例如,钢材球化率低、渗碳体数量过高、局部晶粒不均匀以及结构疏松等缺陷,非正常情况下的芯部组织致使机械性能降低,在承受的热应力大于材料抗拉强度时,轧辊内部的材质出现局部裂纹,裂纹逐步蔓延最终导致轧辊断裂。
- 1、下载文档前请自行甄别文档内容的完整性,平台不提供额外的编辑、内容补充、找答案等附加服务。
- 2、"仅部分预览"的文档,不可在线预览部分如存在完整性等问题,可反馈申请退款(可完整预览的文档不适用该条件!)。
- 3、如文档侵犯您的权益,请联系客服反馈,我们会尽快为您处理(人工客服工作时间:9:00-18:30)。
微裂纹产生的原因:
1)、振动。
离心铸造轧辊时,铸型在离心机上高速运转,所以存在较大振动。
合金含量高的铁水较容易产生偏析,且振动越大偏析现象越明显。
由于高镍铬铁水是在直接激冷下凝固的,加之铁水的合金化程度高,因此,沿辊身界面工作层内柱状晶比较发达,并且有明显方向性,进而力学性能也呈现方向性。
振动使工作层内的组织沿力学性能较差的方向产生裂纹。
2)、冷型原因。
离心铸铁轧辊所用的冷型材质通常是灰铸铁,工作时受到激冷激热,在冷型的内表面容易产生龟裂。
冷型内表面产生的裂纹后会使轧辊在凝固过程中,冷却不均匀,从而使轧辊辊身表面产生裂纹。
3)、涂料原因。
起调整冷速,防止铁水激冷的涂料,如果厚度不均或局部脱落,使浇注时产生冷热不均现象,增加了裂纹产生的倾向,缩短轧辊寿命。
4)、化学成分。
化学成分的波动会使辊身产生裂纹,较显著的影响元素有碳、铬、钼。
碳含量高时,生成大量的碳化物,使辊身脆性增加,容易产生裂纹。
而W(Cr)>1.8%,W(Mn)>0.6%时,极易形成成分过冷,进而导致辊身晶体呈枝晶状长大,微裂纹产生的诱因加大。
微裂纹防止措施:
1)、定期对离心机进行调整,对磨损过度的冷型和离心机及时进行更换,以减小生产中的振动。
2)、计算调整冷型转速。
采用适用的计算转速的重力系数转速计算公式计算转速。
成分偏析严重,有微裂纹产生时,应适当提高冷型转速。
3)、涂料应采用喷涂或滚涂,避免易导致脱落的刷涂;同时注意涂料使用的的搅拌充分均匀。
4)、严控轧辊化学成分,控制W(C):3.0-3.5%;W(Cr):1.6-1.8%;W(Mn):0.2-0.6%。