多孔冲裁模设计说明书
课程设计冲裁模具设计说明书
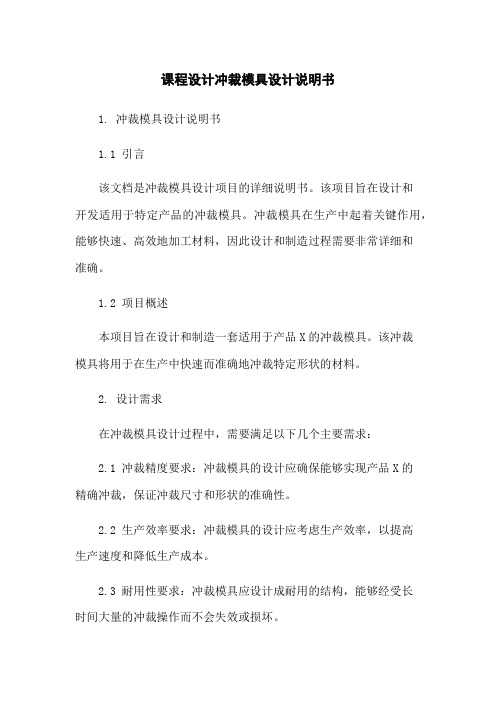
课程设计冲裁模具设计说明书1. 冲裁模具设计说明书1.1 引言该文档是冲裁模具设计项目的详细说明书。
该项目旨在设计和开发适用于特定产品的冲裁模具。
冲裁模具在生产中起着关键作用,能够快速、高效地加工材料,因此设计和制造过程需要非常详细和准确。
1.2 项目概述本项目旨在设计和制造一套适用于产品X的冲裁模具。
该冲裁模具将用于在生产中快速而准确地冲裁特定形状的材料。
2. 设计需求在冲裁模具设计过程中,需要满足以下几个主要需求:2.1 冲裁精度要求:冲裁模具的设计应确保能够实现产品X的精确冲裁,保证冲裁尺寸和形状的准确性。
2.2 生产效率要求:冲裁模具的设计应考虑生产效率,以提高生产速度和降低生产成本。
2.3 耐用性要求:冲裁模具应设计成耐用的结构,能够经受长时间大量的冲裁操作而不会失效或损坏。
2.4 安全性要求:冲裁模具的设计应考虑操作人员的安全,减少意外事故的发生。
3. 冲裁模具设计流程3.1 初步设计:根据产品X的要求,进行初步的冲裁模具设计,包括模具整体结构和基本尺寸的确定。
3.2 详细设计:在初步设计的基础上,进行详细的冲裁模具设计,包括冲头、冲座、导向系统、定位系统和冲裁力传递系统等的设计。
3.3 材料选型:根据冲裁模具的使用需求和工作环境,选择合适的材料进行模具的制造。
3.4 制造和装配:根据详细设计稿和选定的材料,进行冲裁模具的制造和装配工作。
3.5 调试和测试:完成冲裁模具的制造和装配后,进行调试和测试,确保冲裁模具的性能和精度满足要求。
4. 法律名词及注释4.1 版权:指对原创作品拥有的法律保护权。
4.2专利:指对发明创造的保护权,使得他人不得未经许可制造、使用或销售该发明。
4.3 商标:指用于区分商品或服务来源的标识,例如商标名称、商标图案等。
5. 附件本文档涉及以下附件:5.1 冲裁模具初步设计图稿5.2 冲裁模具详细设计图稿5.3 冲裁模具制造和装配过程的照片和记录。
冲裁模(冲压模具)课程设计 说明书

弓形连接固定片复合模设计零件名称:弓形连接固定片生产批量:中批量材料:零件材料为08钢,厚度为1.5mm图1-1一、零件工艺性分析弓形双孔连接固定块片是家用发电风扇中的一连接固定零件,零件的精度要求较低,具有较高的强度和刚度。
外形最大尺寸为70mm,属于小型零件。
该零件应中批量生产,外精度不高,只需平整,外轮廓是该零件需要保证的重点。
该零件用到的冲压工序有冲孔、落料,因此可设计冲孔落料复合模生产此零件。
二、工序设计及工艺计算1、排样毛坯最大尺寸70mm,不算太小,为保证冲裁件的质量,模具寿命和操作方便,采用有搭边,单排排样,如下图2-1所示,冲裁件之间的搭边值a=1.5mm,冲裁件与条料件侧边之间的搭边值a=2.3mm。
1图2-1-1计算条料的宽度:B=70+2×2.3+c=74.7(mm)其中c为调料可能的摆动量,c=0.1mm计算条料的步距:A=20+1.5=21.5(mm)图2-1-2一个步距内材料的材料利用率:η=985.182/(74.7*21.5)×100%= 61.34%2、压力中心确定和压力机的选择(1)、冲裁力的计算冲裁力 F p=Lt σb Kp (2-2-1) 其中:由图2-2知,周长L=213.057mm;=900Mpa, 此时,Kp=1,则:材料:08F钢板,查表,σbFp=213.057X1X900X1=191.75(kN) (2-2-2) 根据以上模具结构类型,采用弹性卸料和漏料出件,卸料力F q=KF,取K=0.05,则:F q =0.05×191.75=9.59(kN) (2-2-3)推料力Fq1=nK1Fp,去凹模刃壁垂直部分高度h=5mm,t=1mm,n=5/1=5;取K1=0.06,则:F q1=5X0.06X191.75=57.53(kN) (2-2-4)顶件力Fq2=K2Fp,K2=0.06,则:Fq2=0.06X191.75=11.51 (kN) (2-2-5) 本套模具用到的由压力机提供的有冲裁力和推料力,因此:总冲压力F=FP+ F q1总=191.75+57.53=249.28(kN) (2-2-6) (2)、压力中心的确定压力中心在两小圆垂直中心线上(3)、压力机的选择,取系数为1.3,则选用的压力机公称压力P≥(1.1~1.3) F总=1.3×249.28=324(kN)P≥1.3F总初选压力机公称吨位为400kN,型号为J23-40,其主要工艺参数如下:公称压力:400KN;滑块行程:100mm;行程次数:80次∕分;最大闭合高度:300mm;最大装模高度:220mm;闭合高度调节量:80mm;工作台尺寸(前后×左右):150mm×300mm;模柄孔尺寸:直径50mm,深度70mm;工作垫板:厚度80mm,孔径200mm;电动机功率:1.5kW。
冲裁模具课程设计说明书
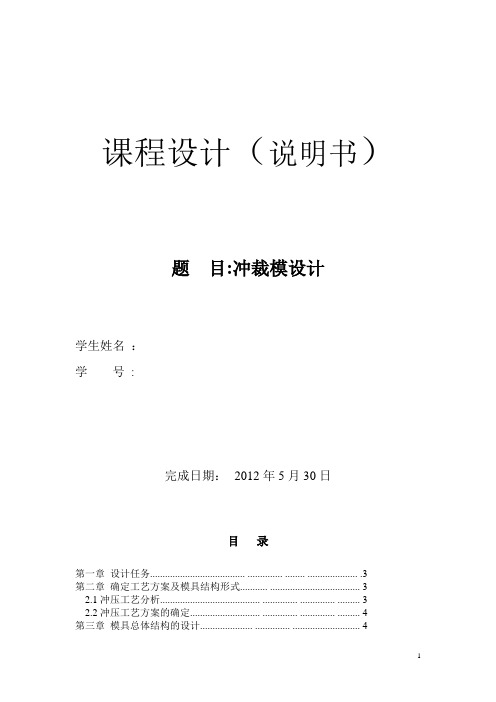
课程设计(说明书)题目:冲裁模设计学生姓名:学号:完成日期:2012年5月30日目录第一章设计任务...................................... .............. ........ .................... .3第二章确定工艺方案及模具结构形式........... (3)2.1冲压工艺分析........................................ .............. .............. (3)2.2冲压工艺方案的确定............................ .............. .............. (4)第三章模具总体结构的设计..................... .............. (4)3.1模具类型的确定........................... .............. . (4)3.2定位方式的选择........................... .............. . (5)3.3卸料装置的选择.......................... .............. .. (5)3.4导向装置的确定........................... .............. . (5)第四章排样图设计............................... .............. ................................ .5 4.1排样相关尺寸的计算.................... .............. .. (5)4.2绘制排样图.................................... .............. .............. .. (5)第五章主要工艺计算............................. .............. . (6)5.1压力中心的计算............................ .............. .. (6)5.2冲压力的计算................................ .............. ............................ .. .6 5.3工作零件刃口尺寸计算................... .............. .. (8)第六章主要零件结构尺寸的设计.............. .............. ......................... .9 6.1凹模结构的设计..................................... .............. ..... .............. (9)6.2凸模结构的设计.................................... .............. ................ . (11)6.3定位零件的设计................................... .............. .............. (15)6.4卸料装置的设计.............................. ....... .. ......... (15)6.5销钉和螺钉的设计.............................................. ................... .. (15)6.6模柄的确定.......................................... ............ ..................... . . (15)6.7矩形垫板的确定.......................................... ............ ............. . . (15)6.8弹性卸料装置的确定...................................... ...................... . . (16)6.9矩形固定板的确定................................... ...... ...................... . . (16)6.10导料板的确定 (16)第七章模架及其它零件的设计................... ............. . (18)第八章冲压设备的选用................................ ............. . (19)8.1压力机的选择...................................... .............. .................... .. (19)8.2模具的闭合高度的计算...................... .............. . (20)第九章固定方式的确定............................. .............. (20)9.1凸和凹模的固定................................ .............. ...................... . (20)9.2确定装配基准................................... .............. ...................... (20)第十章绘制模具装配图.............. ........... .............. .............. ......... ... . (21)结束语 (23)参考文献 (24)第一章设计任务冲压工艺及模具设计材料:Q235 厚度:3mm图1 零件图第二章确定工艺方案及模具结构形式2、1冲压工艺分析该该零件材料为Q235,料厚为3mm,制件的尺寸精度为IT7级,生产批量为中批量。
冲裁模具设计计算说明(doc 12页)

冲裁模具设计计算说明(doc 12页)毕业论文论文名称垫圈冲压模具设计系别机械系专业模具设计及制造班级08 模具四(二)班姓名马贤明设计任务书(一)课程设计的原始资料及设计技术要求零件名称:垫圈零件所用材料:Q235材料厚度:0.5mm生产批量:大批量(二)课程设计工作内容及完成时间1.分析零件的成型工艺性2.工艺方案和模具零件结构尺寸的确定3.压力机的选用4.绘制模具装配图5.绘制模具零件图6.编制设计说明书(三)主要参考资料、文献1.《冲压工艺与模具设计》机械工业出版社2.《冲压模具设计手册》机械工业出版社3.《冲压成型工艺与模具设计》高等教育出版社4.CAD、Pro/E、CAM等软件工具书5.机械制图、公差、金属材料与热处理等书冲裁模具设计计算说明书一、冲压工艺介绍冲压工艺是塑性加工的基本加工方法之一。
它主要用于加工板料零件,所以有时也叫板料冲压。
冲压不仅可以加工金属板料,而且也可以加工非金属板料。
冲压加工时,板料在模具的作用下,于其内部产生使之变形的内力。
当内力的作用达到一定程度时,板料毛胚或毛胚的某个部位便会产生与内力的作用性质相对应的变形,从而获得一定的形状,尺寸和性能的零件。
冲压生产靠模具与设备完成加工过程,所以它的生产效率高,而且由于操作简便,也便于实现机械化和自动化。
利用模具加工,可以获得其他加工方法所不能或难以制造的,形状复杂的零件。
冲压产品的尺寸精度是由模具保证的,所以质量稳定,一般不需要经过机械加工便可以使用。
冲压加工一般不需要加热毛胚,也不像切削加工那样大量的切削材料,所以它不但节能,而且节约材料。
冲压产品的表面质量比较好,使用的原材料是冶金工厂大量生产的轧制板料或带料,在冲压过程中材料表面而不受破坏。
因此,冲压工艺是一种产品质量好而且成本低的加工工艺。
用它生产的产品一般还具有重量轻且刚性好的特点。
冲压加工在汽车、拖拉机、电机、电器、仪器、仪表、各种民用轻工产品以及航空、航天和兵工等的生产方面占据十分重要的地位。
冲裁模设计说明书
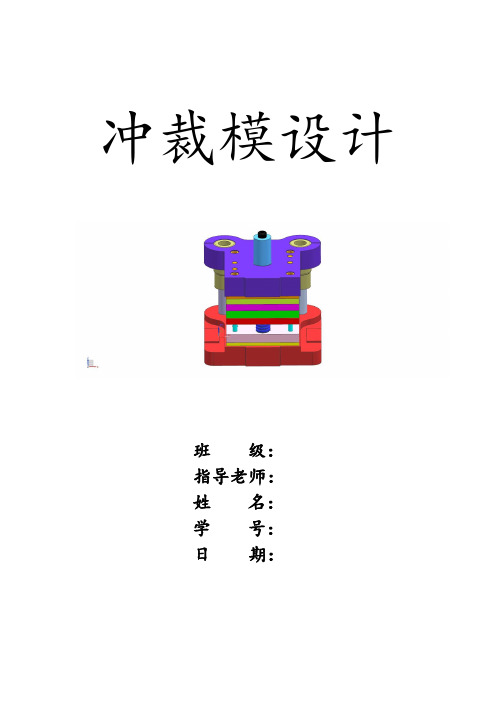
冲裁模设计班级:指导老师:姓名:学号:日期:目录一、冲压件工艺分析及工艺方案确定二、排样设计三、零件刃口尺寸计算四、零件冲压力的计算五、其他模具零件结构设计六、模具的总体设计七、总结1.1.设计题目设计—工件零件图如下图1所示冲裁件,材料为Q235,厚度为2mm,大批量生产。
试制订工件冲压工艺规程,设计其模具、贬值模具零件的加工工艺规程。
生产批量:大批量材料:Q235t=2mm1.2.冲压件工艺分析①材料:该冲裁件的材料为Q235是普通碳素钢,具有较好的可冲压性能。
②零件结构:该冲裁件结构简单,形状对称,比较适合冲裁。
③尺寸精度:零件图上未注公差的尺寸,属自由尺寸,可按IT14级确定工件尺寸的公差。
查公差表得各尺寸公差为:零件外形:600-0.74mmφ200-0.52 mm140-0.43mm零件内形:Φ8.50+0.36mm孔中心距:40±0.15mm结论:适合冲裁1.3.零件冲裁工艺方案制订1.3.1冲裁工艺方案(1)采用单一工序的冲压方法;即落料在冲2-φ8.5的孔(2)采用复合工序的冲压方法:即冲2-φ8.5的孔和落料外形在同一副模具同一工位的一次冲压行程中完成。
(3)采用级进工序的冲压方法:即在同一副模具的不同工位上先后连续完成2-φ8.5的孔→落料外形。
1.3.2 冲裁工艺方案分析(1)第一种方案的优点是模具设计、制造简单、周期短,模具结构简单,因此模具和制件的制造成本均低,但因采用两副模具分别进行落料和冲孔,其冲压生产率低,不能满足大批量生产的需求。
(2)第二种方案的有点事冲压的生产效率较高,且制件的平整度较高。
但模具结构较第一种方案复杂,因此设计制造周期较长,模具成本高。
(3)第三种方案的优点是冲压生产过程易于实现机械化,生产效率较高。
但模具结构较第一种方案复杂,因此设计制造周期较长,模具成本高。
综合以上分析,以满足制件质量和生产纲领为主要因素,因此采用第二种方案。
2.1冲裁件的排样2.1.1冲裁搭边值的确定零件材料厚为2mm,由表2-10可查得,工件间搭边值a1=2.0mm,沿边搭边值a=2.2mm2.2.2材料利用率的计算(1)材料宽度尺寸的确定因材料厚度为2mm,查表得△=0.6,竖排:B=(L+2a) 0﹣△步距h=20+2=22mmB=(60+2×2.2)0-0.6=(64.40-0.6)mm(2)材料利用率的计算η=S S ×100%=×S A B×100% S=819.76mm S 0=64.4×22=1416.8mm① 板料利用率 η=S S ×100%=819.761416.8×100%≈57.8%板料厚度t=2mm ,从附录E 中查出,板料长为1500,宽为500 500B =条 得:1张板可以裁7条1500h=条 得:1条可以冲68个 ② 条料的利用率 n 条=×ns L B×100%≈57.7%③ 板料的利用率 η板=×n s S 板×100%≈52%3.1零件的刃口尺寸计算凸模与凹模配合加工时,凹凸模刃口尺寸的计算由附录N 按IT14级查得60为(0.74) 40为±0.15 20为(0.52) φ8.5为(0.36)14为(0.4)查表2-19取:60、40、φ8.5、14、φ20取x=0.5查表2-18,取Ⅲ型断面Z max =18%×2=0.36 Z min =14%×2=0.28 ①模具磨损刃口尺寸变大的 落料:A d = (A max -X △)0+δdD60=(60-0.5×0.74)0+0.74/4=59.630+0.185mm D14=(14-0.5×0.43)0+0.43/4=13.7850+0.1075mm Dφ20=(20-0.5×0.52)0+0.52/4=19.740+0.13mm ②模具磨损刃口尺寸变小的冲孔:B d=(B min+X△)0-δddφ8.5=(8.5+0.5×0.36)0-0.36/4=8.680-0.09③模具磨损刃口尺寸不变化的C d=C平均±0.125△=(40±0.0375)mmC d=C40=40±0.38压力中心位于制件形心(0.0)5.1凹凸模结构设计5.1.1(1)落料凹模板尺寸:(查表2-27得)K复合=0.28mm凹模板厚度:H=kb(≥15mm)H=0.28×60=16mm凹模板壁厚:C≥(1.5~2)H=(1.5~2)×16=(24~32)mm 实取C=28mm凹模板边长:L=b+2c=60+2×28=116mm查标准GBZ858、1-81,T10A故确定凹模板外形为125×125×16,材料为T10A的矩形凹模板(2)凹凸模尺寸凹凸模长度为:L=h1+h2+h=16+10+24=50mm其中h1→凹凸模固定板厚度h2→弹性卸料版厚度h→增加长度凹凸模外刃口间薄壁校核:根据冲数件结构凹凸模内外刃口最小壁厚为7mm,根据强度要求,该壁厚为4.9mm即可,故该凹凸模强度足够。
冲裁模说明书
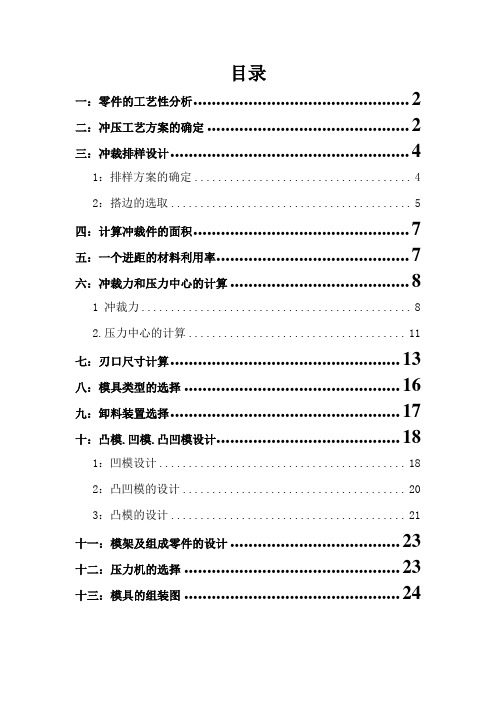
目录一:零件的工艺性分析 (2)二:冲压工艺方案的确定 (2)三:冲裁排样设计 (4)1:排样方案的确定 (4)2:搭边的选取 (5)四:计算冲裁件的面积 (7)五:一个进距的材料利用率 (7)六:冲裁力和压力中心的计算 (8)1 冲裁力 (8)2.压力中心的计算 (11)七:刃口尺寸计算 (13)八:模具类型的选择 (16)九:卸料装置选择 (17)十:凸模.凹模.凸凹模设计 (18)1:凹模设计 (18)2:凸凹模的设计 (20)3:凸模的设计 (21)十一:模架及组成零件的设计 (23)十二:压力机的选择 (23)十三:模具的组装图 (24)一:零件的工艺性分析根据制件的材料、厚度、形状及尺寸,在进行冲裁工艺和模具设计时应注意以下几点:(1)冲裁件虽尺寸不大,形状简单,但要保证制件的尺寸公差,尤其是对空和槽的位置的确定。
板材的尺寸还是一个总要点。
(2)凸凹模的制造尺寸要按落料部分以落料凹模为基准计算 ,落料凸模按间隙值配制;冲孔部分以冲孔凸模为基准计算,冲孔凹模按间隙值配制。
既以落料凹模、冲孔凸模为基准,凸凹模按间隙值配制。
二:冲压工艺方案的确定该工件包括冲孔、落料两个基本工序,可以有以下三种方案:方案一:先落料,后冲孔,采用单工序模生产;方案二:落料—冲孔复合冲压,采用复合模生产;方案三:冲孔—落料连续冲裁,采用级进模生产。
三种方案比较见表2.1表2.1三种方案的比较方案一模具结构简单,但需要两道工序,两副模具,生产率较低,难以满足该零件的年产量要求。
方案二只需一套模具,冲压件的形位精度容易保证,且生产率也高。
尽管模具结构较方案一复杂,但由于零件的几何形状简单,模具制造并不困难。
方案三也只需要一副模具,生产率也高,但零件的冲压精度较差。
欲保证冲压件的形位精度,需要在模具上设置导正销导正,故模具制造安装较复合模复杂,且成本高。
通过对上述三种方案的分析比较,该件的冲压生产采用方案二为佳。
三:冲裁排样设计1:排样方案的确定排样是指冲裁零件在条料、带料或板料上布置的方法。
多孔冲裁模设计说明书
课程编号:青岛理工大学专业课程设计说明书设计人:许广良专业班级:材料073学号: ********* 指导教师:***日期: 2010年1月 7日目录一序言 (3)二设计任务书及零件图 (5)三零件的工艺性分析 (6)四冲裁零件工艺方案的确定 (7)五压力计算与压力机的选择 (9)六模具刃口尺寸和公差的计算 (11)七凸模与凹模的结构设计 (14)八模具总体设计及主要零部件设计 (19)九其他需要说明的内容 (20)十参考资料 (21)一序言21世纪,现代工业的迅猛发展使冲压技术得到越来越广泛的应用,随之而来的便是对冲压模具设计与制造的要求越来越高。
冲压模具是冲压生产的主要工艺设备,其设计是否合理对冲压件的表面质量、尺寸精度、生产率以及经济效益等影响巨大。
因此,研究冲压模具的各项技术指标,对冲压模具设计和冲压技术发展是十分必要的。
我们这次课程设计的任务是设计一套简单冲裁模具,即由老师给出零件及生产要求与精度要求,在老师的指导下设计出一套符合要求的冲裁模。
由于是初次设计,经验不足,因此在设计过程中难免走了不少弯路,犯了不少错误,但是这些都将成为我们以后进行设计的宝贵经验。
虽已经过多次计算、修改,但仍可能还存有疏漏和不当之处,敬请批评、指出。
在此次设计过程中,得到了郑少梅老师的和广大同学的热心帮助,获益非浅,在此表示衷心的感谢。
二设计任务书及产品图2.1 已知:(1)产品零件图:图2-1零件图主视图图2-2零件图俯视图零件图(2)生产批量:大批量(3)零件材料:08钢(4)材料厚度:2.0mm2.2 求作:(1)进行冲压工艺性分析(从材料、零件结构、尺寸精度几个方面进行)(2)确定工艺方案及模具结构类型(3)进行相关工艺计算,包括:①冲压力计算及压力中心的确定;②凸凹模刃口尺寸计算;③模具零件结构尺寸计算;④设备选择等。
(4)绘制模具总装配图;(5)绘制工作零件及主要零件的零件图;(6)编写课程设计说明书;2.3 要求:根据所设计工件的尺寸、形状、批量等原始数据和要求,每人独立设计、绘制完成一套冲压模具。
冲孔模具设计说明书
冲孔模具设计说明书冲孔模具设计说明书1.引言本文档旨在说明冲孔模具的设计方案,并提供详细的设计要求和规范,以确保模具的性能和质量满足相关标准和要求。
2.设计目标在开始设计冲孔模具之前,首先要明确设计的目标,包括但不限于:- 冲孔模具的应用领域和用途- 冲孔模具的材料和制造工艺要求- 冲孔模具的几何形状和尺寸限制- 冲孔模具的使用寿命和维护要求3.冲孔模具的结构设计3.1 模具整体结构描述冲孔模具的整体结构,包括上模、下模和导向系统等。
对每个部分要求进行详细说明,包括材料选择、尺寸设计、配合要求等。
3.2 冲孔系统详细描述冲孔系统的设计要求,包括冲头、油缸、冲座等。
对每个组成部分进行细化说明,包括材料选择、尺寸设计、配合要求等。
3.3 技术参数列出冲孔模具的技术参数要求,包括最大冲孔力、冲床适配范围、模具重量等。
4.材料选择和加工工艺4.1 冲孔模具材料选择根据冲孔模具的应用和工作环境,选择合适的材料。
说明材料的物理性质、化学成分和机械性能要求。
4.2 冲孔模具的加工工艺描述冲孔模具的制造过程,包括数控加工、热处理、抛光等。
对每个工艺步骤进行细化说明,包括设备要求、工艺参数和工艺流程等。
5.模具试制和测试5.1 模具试制描述冲孔模具的试制过程,包括制造和装配。
对试制过程中可能遇到的问题进行分析和解决方案的提供。
5.2 模具测试列出冲孔模具的测试要求和方法,包括尺寸检测、冲床适配性测试、冲孔力测试等。
提供测试数据和结果分析。
6.模具维护和保养提供冲孔模具的维护和保养指南,包括清洁、润滑、防锈等。
对维护周期和方法进行详细说明。
7.附件本文档涉及的附件包括但不限于图纸和设计图。
8.法律名词及注释对文档中涉及的法律名词进行解释和注释,以确保读者对相关法律要求的理解。
冲裁模(冲压模具)课程设计说明书_图文.
由图 7-1 三维装配图的(a)图知,模具闭合高度为 H=191mm。
七、模具装配及爆炸图(a) 16图 7-1 三维装配图(b)图 7-2 三维爆炸图八、设计感悟设计心得体会一个多星期的课程设计结束了,在这些天内,我学到了很多的知识,让我对模具设计与制造有了一个更清晰的了解,更坚定了自己对模具行业的信心。
17第一周前两天,我在图书馆查看了大量的参考书,看到了了很多冲压模具。
通过筛选,找出了与本次课程设计相关的几本参考书,作为本次课程设计的工具。
第三天开始,我开始计算相关数据。
本次课程设计,我决定使用计算机辅助设计,一来锻炼我计算机应用能力和打字速度,二可以将我近几个月学习的三维制图软件 creo 应用于实践,更加科学的设计模具,完成本次课程设计。
在大家都在绘图室手工绘图的时候,我在宿舍用计算机还原设计的模具零件,生成三维模型。
然后装配成模具,校核相关尺寸,看其是否发生干涉。
确保结构和原理正确后,我开始用 creo 将模具零件生成二维工程图。
而二维工程图完成后,时间已经进入了课程设计的第四天。
接下来要做的,就是将二维工程图转化为符合国家标准的二维工程图纸。
这就用到了二维制图软件 AutoCAD。
将工程图转换成.dwg 格式,然后用 AutoCAD 打开修改加工。
等一切完成后,一个星期过去了。
从第二周开始,我将撰写课程设计说明书。
我打字速度比较慢,所以这个要花费些时间,不过还好,前期已经把各种数据整理完毕,剩下的只是打字和文字处理了。
花了三天时间整理好了课程设计说明书。
在本次课程设计中,刘伟老师给了很多原理上的指导,纠正了很多错误,在这里表示衷心的感谢。
本次课程设计我感到学以致用的快乐,另外,不可否认,我的计算机辅助设计能力还有非常大的提升空间,当更加努力学习才是。
九、参考文献 [1] 杨占尧.冲压模具典型结构图例.北京:化学工业出版社,2007. [2] 郑家贤.冲压工艺与模具设计.北京:机械工业出版社,2005. [3] 肖祥芷,王孝培.中国模具设计大点.北京:江西科学技术出版社,2003. [4] 卢金封主编.冲压工艺模具学.北京:机械工业出版社,1998. [5] 陈金德主编.材料成型工程.西安:西安交通大学出版社,2000. [6] 范宏才主编.现代锻压机械.北京:机械工业出版社,1994. 18。
冲裁模(冲压模具)课程设计说明书
模具设计的具体步骤
确定冲裁模的类型和尺寸 设计冲裁模的轮廓和结构 确定冲裁模的冲压力和冲压速度
设计冲裁模的模具材料和热处理工艺 设计冲裁模的冷却系统和润滑系统 设计冲裁模的模具寿命和维护保养方法
冲裁模的制造工艺
冲裁模的设计:根据产品要求进行设计,包括尺寸、形状、材料等 冲裁模的制造:采用数控机床进行加工,保证精度和效率 冲裁模的装配:将各个部件组装成完整的冲裁模 冲裁模的调试:在装配完成后进行调试,确保其性能和精度达到要求
采用环保材料和工艺, 减少对环境的影响
提高冲裁模的自动化 程度,降低人工成本
提高模具寿命的方法和途径
优化模具设计: 合理选择材料、 结构、尺寸等, 提高模具的强度 和耐磨性
提高加工精度: 采用先进的加工 技术和设备,提 高模具的加工精 度,减少误差
加强维护保养: 定期检查、清洗、 润滑模具,及时 发现并处理模具 的磨损和损坏
冲裁模的使用和维护
冲裁模的使用 步骤:安装、 调试、运行、
停机
冲裁模的维护 方法:定期检 查、清洁、润 滑、更换易损
件
冲裁模的安全 操作:遵守操 作规程,注意
安全防护
冲裁模的常见 故障及处理方 法:如卡模、 漏油、噪音等, 需及时处理, 确保生产安全
常见问题的处理和解决方法
冲裁模调试过程中, 如果出现模具损坏, 应及时更换或修复。
设计前的准备工作
确定冲裁模的用途和功能 收集冲裁模的设计要求和技术参数 确定冲裁模的材料和尺寸 准备冲裁模的设计图纸和工具
模具设计的基本流程
确定冲裁 模的设计 要求
设计冲裁 模的尺寸 和形状
确定冲裁 模的材料 和加工工 艺
设计冲裁 模的装配 和调试方 法
- 1、下载文档前请自行甄别文档内容的完整性,平台不提供额外的编辑、内容补充、找答案等附加服务。
- 2、"仅部分预览"的文档,不可在线预览部分如存在完整性等问题,可反馈申请退款(可完整预览的文档不适用该条件!)。
- 3、如文档侵犯您的权益,请联系客服反馈,我们会尽快为您处理(人工客服工作时间:9:00-18:30)。
课程编号:青岛理工大学专业课程设计说明书设计人:许广良专业班级:材料073学号: ********* 指导教师:***日期: 2010年1月 7日目录一序言 (3)二设计任务书及零件图 (5)三零件的工艺性分析 (6)四冲裁零件工艺方案的确定 (7)五压力计算与压力机的选择 (9)六模具刃口尺寸和公差的计算 (11)七凸模与凹模的结构设计 (14)八模具总体设计及主要零部件设计 (19)九其他需要说明的内容 (20)十参考资料 (21)一序言21世纪,现代工业的迅猛发展使冲压技术得到越来越广泛的应用,随之而来的便是对冲压模具设计与制造的要求越来越高。
冲压模具是冲压生产的主要工艺设备,其设计是否合理对冲压件的表面质量、尺寸精度、生产率以及经济效益等影响巨大。
因此,研究冲压模具的各项技术指标,对冲压模具设计和冲压技术发展是十分必要的。
我们这次课程设计的任务是设计一套简单冲裁模具,即由老师给出零件及生产要求与精度要求,在老师的指导下设计出一套符合要求的冲裁模。
由于是初次设计,经验不足,因此在设计过程中难免走了不少弯路,犯了不少错误,但是这些都将成为我们以后进行设计的宝贵经验。
虽已经过多次计算、修改,但仍可能还存有疏漏和不当之处,敬请批评、指出。
在此次设计过程中,得到了郑少梅老师的和广大同学的热心帮助,获益非浅,在此表示衷心的感谢。
二设计任务书及产品图2.1 已知:(1)产品零件图:图2-1零件图主视图图2-2零件图俯视图零件图(2)生产批量:大批量(3)零件材料:08钢(4)材料厚度:2.0mm2.2 求作:(1)进行冲压工艺性分析(从材料、零件结构、尺寸精度几个方面进行)(2)确定工艺方案及模具结构类型(3)进行相关工艺计算,包括:①冲压力计算及压力中心的确定;②凸凹模刃口尺寸计算;③模具零件结构尺寸计算;④设备选择等。
(4)绘制模具总装配图;(5)绘制工作零件及主要零件的零件图;(6)编写课程设计说明书;2.3 要求:根据所设计工件的尺寸、形状、批量等原始数据和要求,每人独立设计、绘制完成一套冲压模具。
包括:(1)模具装配图1张(按照1:1比例,或适当比例);(2)模具工作零件图2-3张(按照1:1比例,或适当比例);(3)设计说明书1份;三零件的工艺性分析由工件图可见,该工件的加工涉及到落料、拉深、冲孔三种工序内容。
根据变形特点,对于带孔的拉深件,尤其是当孔到直壁的距离较近时,一般应先拉深后冲孔。
因此此次课程设计的模具为在落料和拉深之后使用的冲孔模。
3.1 冲裁件的结构工艺性分析冲裁件的形状应尽可能简单、对称、避免复杂形状的曲线,在许可的情况下,把冲裁件设计成少或无废料形状,以减少废料。
对于所冲孔直径为10mm,在手册中查得,一般冲孔模对该种材料可以冲压的最小孔径为d t,t=2mm,因而该孔符合工艺要求。
为:查手册知,冲裁件上的孔与孔、或孔与边缘的距离b、b1≥,mmmmb0.3≥。
而零件上各孔的孔边距均大于最小孔边距。
以上各项分析b21均符合冲裁工艺要求,故可以采用多孔冲裁模进行加工。
3.2冲裁件的尺寸精度和表面粗糙度分析冲裁件的精度要求,应在经济精度范围内,对于普通冲裁件,其经济精度不高于IT12,冲孔件比落料件高一级。
如果工件精度高于上述要求,则需要在冲裁后整修或采用精密冲裁。
3.3冲裁件的尺寸基准分析冲裁件的尺寸基准应尽可能和制模的定位基准重合,以避免产生基准不重合误差。
孔位尺寸基准应尽量选择在冲裁过程中始终不参加变形的面或线上,且不要与参加变形的部位联系起来。
本次设计中的零件为冲孔件,其精度采用IT14级,满足冲裁工艺性的要求。
冲裁件的材料为08钢,屈服强度为196 MPa,弹性模量为186错误!未找到引用源。
MPa,抗剪强度为255~353MPa,抗拉强度为324~441 MPa。
综合以上各方面情况,可以确定零件主要冲压工序的工艺性良好。
四、冲裁零件工艺方案的确定由工件图可见,该工件的加工涉及到落料、拉深、冲孔三种工序内容。
根据变形特点,对于带孔的拉深件,尤其是当孔到直壁的距离较近时,一般应先拉深后冲孔。
因此此次课程设计的模具为在落料和拉深之后使用的冲孔模。
所给零件所需的基本工序为冲孔,可以拟定出如下六种工艺方案:方案一:刚性卸料板+后侧导柱模架。
方案二:刚性卸料板+对角导柱模架。
方案三:刚性卸料板+中间导柱模架。
方案四:弹性卸料板+后侧导柱模架。
方案五:弹性卸料板+对角导柱模架。
方案六:弹性卸料板+中间导柱模架。
根据所给零件的结构与材料情况,模具的受力状况,以及生产的经济性,本模具选用适合于单个半成品件冲裁的弹性卸料板+中间导柱标准模架,即方案六。
这种模架的导柱安装在模具中心对称位置,冲压时可防止由于偏心力矩而引起的模具偏斜,并且便于在卸料板上安装导套。
五 压力计算、压力中心的确定及压力机的选择5.1 冲压力计算 因该冲裁件的结构简单,几何结构呈中心对称形式,故凸模采用水平布置。
5.1.1 冲裁力的计算mmL 63102=⨯=π,mm t 2=,MPa b 380=σ,⎪⎭⎫ ⎝⎛=⨯⨯=⨯⨯=KN t L F b 880.47380263σ. 5.1.2 卸料力的计算F K F 卸卸=,查《模具设计应用实例》表2-15,取45.0=卸K ;故()N F 214747880045.0=⨯=卸5.1.3 推件力的计算选如下图所示的凹模刃口形式,取mm h 6=(当t=(0.5-5)mm 时,h=(5-10)mm).则个3==th n ;查《模具设计应用实例》表2-15,05.0=推K ; 故()N F 72004788005.03=⨯⨯=推;选择冲床的总冲压力为:()KN F F F F 2.57=++=推卸总5.2 压力中心的确定因为冲裁件呈中心对称形结构,材料密度均匀,所以压力中心选在工件的中心 位置即可.5.3 压力机的选择查表选用开式双柱可倾压力机J23-16: 公称压力:160KN 滑块行程:55mm 最大闭合高度:220mm 闭合高度调节量:45mm 滑块中心线至床身距离:160mm 工作台尺寸:mm mm 450300⨯ 垫板厚度:40mm模柄孔尺寸:mm mm 6040⨯φ六 模具刃口尺寸和公差的计算6.1 计算凸凹模刃口据《模具设计应用实例》表2-10查得间隙值 mm Z 22.0min = ,mm Z 26.0max = 据《模具设计应用实例》表2-12查得凸凹模的制造公差 mm 02.0=凸δ, mm 02.0=凹δ校核:mm Z Z 04.0min max =-,mm Z Z 04.0min max =-, mm 04.0=+凹凸δδ 满足凹凸δδ+≥-min max Z Z 的条件,可采用凸凹模分开加工的方法。
对零件图中未注尺寸公差的尺寸,由《模具设计应用实例》树末附录D 和E 查出其极限偏差:mm20.0010+φ查《模具设计应用实例》表2-13得因数X:mm 10φ孔 50.0=X6.1.1 凸模刃口尺寸的计算()0凸凸δ-∆+=X d d式中凸d -------冲孔凸模基本尺寸(mm);-------工件制造公差(mm);错误!未找到引用源。
凸δ-------凸模制造公差(mm); X--------磨损量,磨损系数为错误!未找到引用源。
:(零件精度为IT10 以上时,1=X ;零件精度为IT11~IT13时 75.0=X ;零件精度为IT14时,5.0=X 。
)工件精度为IT14,50.0=X ;mm 02.0=凸δ。
查《互换性与测量》得 24.0=∆;(表1-8) 则有()mm 002.024.05.01010-⨯+=凸φ6.1.2凹模刃口尺寸的计算()凹凸凹δ++=0min Z d d式中 错误!未找到引用源。
凸d 、 凹d ----------冲孔凸、凹模基本尺寸(mm);错误!未找到引用源。
min Z --------最小合理间隙(mm);---------工件制造公差(mm);由上面的计算过程知:mm X 5.0=;mm 02.0=凸δ,mm 02.0=凹δ 则()mm 10.2222.010100.02002.00++=+=凹φ6.2 尺寸计算依据上述计算冲裁凸凹模刃口尺寸的依据为:①冲裁变形规律,即落料件尺寸与凹模刃口尺寸相同;冲 孔尺寸与凸模刃口尺寸相同; ②零件的尺寸精度; ③合理的间隙值;④磨损规律,如圆形件凹模尺寸磨损后变大,凸模尺寸磨 损后变小,间隙磨损后变大; ⑤冲模的加工制造方法。
根据冲裁变形规律,冲孔尺寸等于凸模刃口尺寸,落料件尺寸等于凹模刃口尺寸。
在冲孔时以凸模为基准件,间隙取在凹模上,落料时以凹模为基准件,间隙取在凸模上。
新模具的间隙应是最小的合理间隙,磨损后到最大合理间隙。
一般凹模公差标注成凹δ+,凸模公差标注成凸δ-。
七 凸模与凹模的结构设计7.1 凹模的选用及设计 7.1.1 凹模的外形尺寸根据冲压件的形状,为了保证凹模有足够的强度,而采用拉深件口部朝上放置,因此凹模的外形尺寸仍可按常规进行设计。
凹模厚度 ()()mm mm Kb H 152.41042.0〈=⨯==; 凹模壁厚 ()H c 2~5.1=; 式中b-凹模最大宽度(mm ); K-因数;H-凹模厚度,其值为15~20mm ; c-凹模壁厚,其值为26~40mm ; 故取mm H 20=,mm c 40=.7.1.2 确定凹模结构形式查《中国模具设计大典》表22.5-15,选取标准件:20160160⨯⨯=⨯⨯H B L ;模具材料为T10A ,热处理为时效;根据模具结构,取凹模厚度mm H 20=,凹模壁厚mm C 40=。
凹模上各孔中心矩的制造公差应比工件精度高3-4级,其中 mm h 6=,查《冲模设计应用实例》,凹模的零件简图如下图所示:图7-1凹模主视图图7-2凹模俯视图此为柱形刃口筒形凹模,此模的特点是:刃口强度较高, 修模后刃口尺寸不变。
但孔口容易积存工件或废料,推件力大且磨损大。
适用于精度较高工件的冲裁。
当mm t 5~5.0=时,mm h 10~5=;此时mm t 2=,取mm h 6=。
7.2 凸模的选用及设计凸模的长度公式:l t t t L +++=321; 式中 L---------凸模长度(mm ); 1t --------凸模固定板厚度(mm ); 2t --------卸料板厚度(mm );3t --------导料板厚度(mm );l ---------附加长度(mm ),l 包括:凸模进凹模的深度0.5~1mm ;总修磨量6~12mm;凸模固定板于卸料板之间的安全距离,一般取15~20mm 。
由前面选取的标准件知:mm t 141= , mm t 182= , mm t 03=附加长度取 mm l 42=所以:mm l t t t L 74321=+++=。