冲裁模设计说明
冲裁模设计说明书

目录第一部分:设计任务书 (2)第二部分:设计过程 (3)①设计依据、原始数据 (3)②零件冲压加工工艺分析 (3)③确定零件的冲压工艺方案 (4)④排样设计 (5)⑤绘制排样图 (6)⑥冲裁工艺力的计算 (7)⑦模具压力中心的确定 (9)⑧刃口尺寸计算 (10)⑨模具零件结构尺寸的确定 (13)⑩模具装配及固定 (14)11设备选择 (10)第三部分:设计总结 (14)第四部分:参考资料 (15)设计任务书工件的形状和尺寸如下图所示:工件:垫圈材料:A3号钢料厚:2mm要求设计一副模具,大量加工上述零件,内容包括:工艺设计和模具设计两部分。
工艺设计部分包括:对冲压件进行工艺性分析;进行必要的工艺计算。
模具设计部分包括:根据所给课题进行冲压模具结构设计,进行必要的模具设计计算,绘制出模具的装配图、及模具非标零件的零件图;拟订模具工作零件的加工工艺写课程设计《设计说明书》一份,详细地陈述设计过程,如模具结构的方案分析及各种设计计算过程等。
设计说明书要求内容完整,计算过程正确,条理清晰,层次清楚。
第二部分:设计的具体过程一、设计依据、原始数据工件:垫圈材料:A3号钢料厚:2mm二、零件冲压加工工艺分析冲裁件的工艺性是指冲裁件对冲裁工艺的适应性。
一般情况下,对冲裁件工艺性影响最大的是几何形状、尺寸和精度要求。
良好的冲裁工艺性应能满足材料较省、工序较少、模具加工较易、寿命较高、操作方便及产品质量稳定等要求。
1冲裁件工艺性分析零件的加工涉及冲孔和落料两道工序。
冲裁件为自由公差,因此采用IT14级符合要求冲裁件孔的最小尺寸模具凸模的强度受冲裁件上孔的尺寸的影响,所以冲裁件上的孔不能太小,查《冲压成型工艺与模具设计》课本表3-17得有导向凸模的最小尺寸:d≥0.35tt为材料的厚度即2mm ,则d≥0.7mm因此该零件的最小孔的直径为14.5mm远大于凸模的最小直径,故凸模的强度不受冲裁件上的孔的尺寸的影响。
课程设计冲裁模具设计说明书
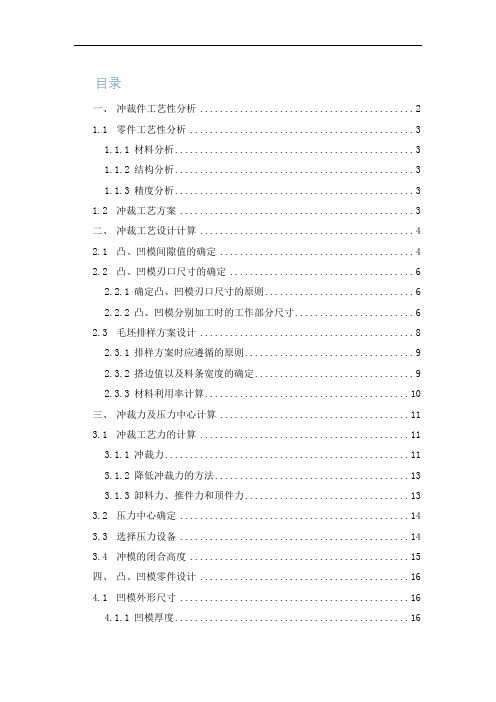
目录一、冲裁件工艺性分析 (2)1.1零件工艺性分析 (3)1.1.1材料分析 (3)1.1.2结构分析 (3)1.1.3精度分析 (3)1.2冲裁工艺方案 (3)二、冲裁工艺设计计算 (4)2.1凸、凹模间隙值的确定 (4)2.2凸、凹模刃口尺寸的确定 (6)2.2.1确定凸、凹模刃口尺寸的原则 (6)2.2.2凸、凹模分别加工时的工作部分尺寸 (6)2.3毛坯排样方案设计 (8)2.3.1排样方案时应遵循的原则 (9)2.3.2搭边值以及料条宽度的确定 (9)2.3.3材料利用率计算 (10)三、冲裁力及压力中心计算 (11)3.1冲裁工艺力的计算 (11)3.1.1冲裁力 (11)3.1.2降低冲裁力的方法 (13)3.1.3卸料力、推件力和顶件力 (13)3.2压力中心确定 (14)3.3选择压力设备 (14)3.4冲模的闭合高度 (15)四、凸、凹模零件设计 (16)4.1凹模外形尺寸 (16)4.1.1凹模厚度 (16)4.1.2刃口高度 (17)4.2凸凹模外形尺寸 (17)4.3冲孔凸模外形尺寸 (18)4.4凸、凹模装配结构设计 (18)4.4.1螺钉选择 (18)4.4.2定位板和定位销 (18)4.4.3螺钉定位 (19)五、模具总体结构设计 (19)5.1冲模模架标准设计 (19)5.1.1冲模模架设计 (19)5.1.2导柱及导套设计 (21)5.2模柄设计 (22)六、卸料装置和顶件装置设计 (22)6.1卸料装置设计 (22)6.2弹性元件的选择 (22)6.2.1橡胶压力P (23)6.2.2橡胶自由高度H (23)6.3顶件装置设计 (23)七、模具结构三维设计 (24)一、冲裁件工艺性分析制件零件图如图1-1所示:图1-1制件结构图1.1零件工艺性分析1.1.1材料分析304用途广泛,具有良好的耐腐蚀性,耐热性,低温强度和机械特性;冲压弯曲等热加工性好,可用于冲裁工艺。
课程设计冲裁模具设计说明书
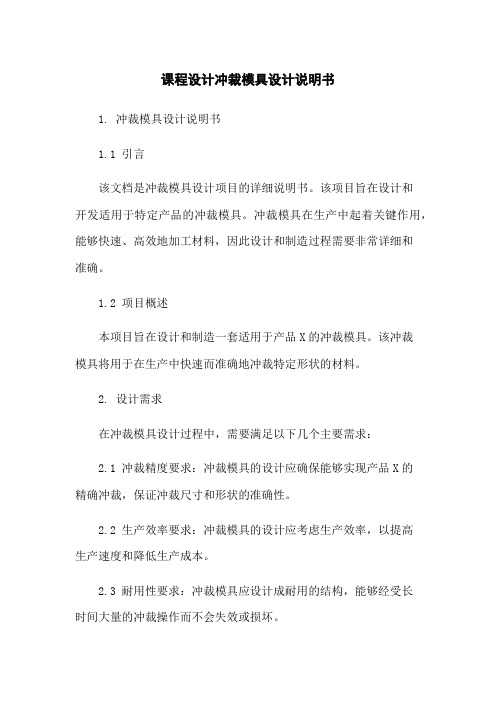
课程设计冲裁模具设计说明书1. 冲裁模具设计说明书1.1 引言该文档是冲裁模具设计项目的详细说明书。
该项目旨在设计和开发适用于特定产品的冲裁模具。
冲裁模具在生产中起着关键作用,能够快速、高效地加工材料,因此设计和制造过程需要非常详细和准确。
1.2 项目概述本项目旨在设计和制造一套适用于产品X的冲裁模具。
该冲裁模具将用于在生产中快速而准确地冲裁特定形状的材料。
2. 设计需求在冲裁模具设计过程中,需要满足以下几个主要需求:2.1 冲裁精度要求:冲裁模具的设计应确保能够实现产品X的精确冲裁,保证冲裁尺寸和形状的准确性。
2.2 生产效率要求:冲裁模具的设计应考虑生产效率,以提高生产速度和降低生产成本。
2.3 耐用性要求:冲裁模具应设计成耐用的结构,能够经受长时间大量的冲裁操作而不会失效或损坏。
2.4 安全性要求:冲裁模具的设计应考虑操作人员的安全,减少意外事故的发生。
3. 冲裁模具设计流程3.1 初步设计:根据产品X的要求,进行初步的冲裁模具设计,包括模具整体结构和基本尺寸的确定。
3.2 详细设计:在初步设计的基础上,进行详细的冲裁模具设计,包括冲头、冲座、导向系统、定位系统和冲裁力传递系统等的设计。
3.3 材料选型:根据冲裁模具的使用需求和工作环境,选择合适的材料进行模具的制造。
3.4 制造和装配:根据详细设计稿和选定的材料,进行冲裁模具的制造和装配工作。
3.5 调试和测试:完成冲裁模具的制造和装配后,进行调试和测试,确保冲裁模具的性能和精度满足要求。
4. 法律名词及注释4.1 版权:指对原创作品拥有的法律保护权。
4.2专利:指对发明创造的保护权,使得他人不得未经许可制造、使用或销售该发明。
4.3 商标:指用于区分商品或服务来源的标识,例如商标名称、商标图案等。
5. 附件本文档涉及以下附件:5.1 冲裁模具初步设计图稿5.2 冲裁模具详细设计图稿5.3 冲裁模具制造和装配过程的照片和记录。
冲裁模设计说明书
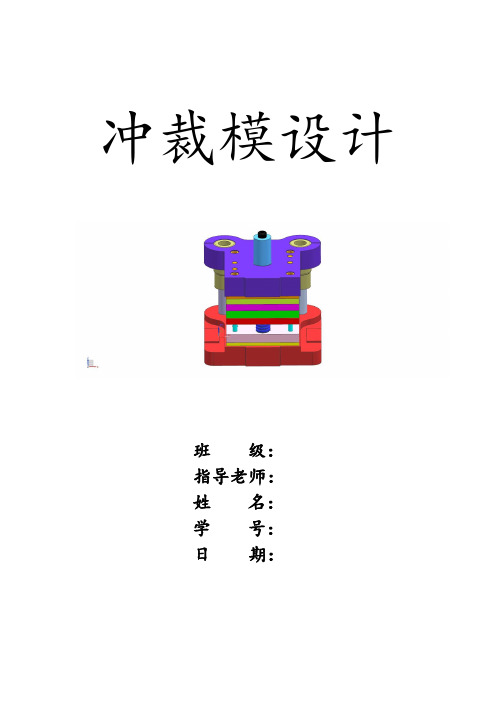
冲裁模设计班级:指导老师:姓名:学号:日期:目录一、冲压件工艺分析及工艺方案确定二、排样设计三、零件刃口尺寸计算四、零件冲压力的计算五、其他模具零件结构设计六、模具的总体设计七、总结1.1.设计题目设计—工件零件图如下图1所示冲裁件,材料为Q235,厚度为2mm,大批量生产。
试制订工件冲压工艺规程,设计其模具、贬值模具零件的加工工艺规程。
生产批量:大批量材料:Q235t=2mm1.2.冲压件工艺分析①材料:该冲裁件的材料为Q235是普通碳素钢,具有较好的可冲压性能。
②零件结构:该冲裁件结构简单,形状对称,比较适合冲裁。
③尺寸精度:零件图上未注公差的尺寸,属自由尺寸,可按IT14级确定工件尺寸的公差。
查公差表得各尺寸公差为:零件外形:600-0.74mmφ200-0.52 mm140-0.43mm零件内形:Φ8.50+0.36mm孔中心距:40±0.15mm结论:适合冲裁1.3.零件冲裁工艺方案制订1.3.1冲裁工艺方案(1)采用单一工序的冲压方法;即落料在冲2-φ8.5的孔(2)采用复合工序的冲压方法:即冲2-φ8.5的孔和落料外形在同一副模具同一工位的一次冲压行程中完成。
(3)采用级进工序的冲压方法:即在同一副模具的不同工位上先后连续完成2-φ8.5的孔→落料外形。
1.3.2 冲裁工艺方案分析(1)第一种方案的优点是模具设计、制造简单、周期短,模具结构简单,因此模具和制件的制造成本均低,但因采用两副模具分别进行落料和冲孔,其冲压生产率低,不能满足大批量生产的需求。
(2)第二种方案的有点事冲压的生产效率较高,且制件的平整度较高。
但模具结构较第一种方案复杂,因此设计制造周期较长,模具成本高。
(3)第三种方案的优点是冲压生产过程易于实现机械化,生产效率较高。
但模具结构较第一种方案复杂,因此设计制造周期较长,模具成本高。
综合以上分析,以满足制件质量和生产纲领为主要因素,因此采用第二种方案。
2.1冲裁件的排样2.1.1冲裁搭边值的确定零件材料厚为2mm,由表2-10可查得,工件间搭边值a1=2.0mm,沿边搭边值a=2.2mm2.2.2材料利用率的计算(1)材料宽度尺寸的确定因材料厚度为2mm,查表得△=0.6,竖排:B=(L+2a) 0﹣△步距h=20+2=22mmB=(60+2×2.2)0-0.6=(64.40-0.6)mm(2)材料利用率的计算η=S S ×100%=×S A B×100% S=819.76mm S 0=64.4×22=1416.8mm① 板料利用率 η=S S ×100%=819.761416.8×100%≈57.8%板料厚度t=2mm ,从附录E 中查出,板料长为1500,宽为500 500B =条 得:1张板可以裁7条1500h=条 得:1条可以冲68个 ② 条料的利用率 n 条=×ns L B×100%≈57.7%③ 板料的利用率 η板=×n s S 板×100%≈52%3.1零件的刃口尺寸计算凸模与凹模配合加工时,凹凸模刃口尺寸的计算由附录N 按IT14级查得60为(0.74) 40为±0.15 20为(0.52) φ8.5为(0.36)14为(0.4)查表2-19取:60、40、φ8.5、14、φ20取x=0.5查表2-18,取Ⅲ型断面Z max =18%×2=0.36 Z min =14%×2=0.28 ①模具磨损刃口尺寸变大的 落料:A d = (A max -X △)0+δdD60=(60-0.5×0.74)0+0.74/4=59.630+0.185mm D14=(14-0.5×0.43)0+0.43/4=13.7850+0.1075mm Dφ20=(20-0.5×0.52)0+0.52/4=19.740+0.13mm ②模具磨损刃口尺寸变小的冲孔:B d=(B min+X△)0-δddφ8.5=(8.5+0.5×0.36)0-0.36/4=8.680-0.09③模具磨损刃口尺寸不变化的C d=C平均±0.125△=(40±0.0375)mmC d=C40=40±0.38压力中心位于制件形心(0.0)5.1凹凸模结构设计5.1.1(1)落料凹模板尺寸:(查表2-27得)K复合=0.28mm凹模板厚度:H=kb(≥15mm)H=0.28×60=16mm凹模板壁厚:C≥(1.5~2)H=(1.5~2)×16=(24~32)mm 实取C=28mm凹模板边长:L=b+2c=60+2×28=116mm查标准GBZ858、1-81,T10A故确定凹模板外形为125×125×16,材料为T10A的矩形凹模板(2)凹凸模尺寸凹凸模长度为:L=h1+h2+h=16+10+24=50mm其中h1→凹凸模固定板厚度h2→弹性卸料版厚度h→增加长度凹凸模外刃口间薄壁校核:根据冲数件结构凹凸模内外刃口最小壁厚为7mm,根据强度要求,该壁厚为4.9mm即可,故该凹凸模强度足够。
垫片冲裁模设计说明书

目录§前言任务描述 (1)一. 冲压件工艺性分 (2)二. 冲压工艺方案的确定 (2)三. 主要设计计算 (2)(1)排养方式的确定以及计算 (2)(2)冲压力的计算 (2)(3)压力中心的确定及相关计算 (3)(4)工作零件刃口尺寸计算 (3)(5)卸料橡胶的设计 (4)四. 模具总体设计 (4)(1)模具类型的选择 (4)(2)定位方式的选择 (4)(3)卸料,出件方式的选择 (4)(4)导向方式选择 (5)五. 主要零部件设计 (5)(1)主要零件的结构设计 (5)a.落料凸模 (5)b.冲孔凸模 (5)c.凹模 (5)(2)定位零件的设计 (6)(3)导料板的设计 (6)(4)卸料板部件设计 (6)(5)模架及其他零部件设计 (6)六. 模具总装图 (7)七. 冲压设备的选定 (7)八. 工作零件的加工工艺 (7)九. 模具的装配 (8)十.设计小结 (9)附图装配图 (10)(参考文献) (11)冲裁模设计说明书冲裁模设计:根据给定工件图设计冲裁模具。
工件尺寸如图所示,料厚t=1, 材料:紫铜; 大批量.要求: 1.完成模具总装图(3D电子文档);2.完成总装配图,图纸符合国家制图标准;3.绘制工程图,图纸符合国家制图标准.4.编写设计说明书.(A4纸打印)工件图工件名称:垫片工件简图:如图所示生产批量:大批量工件材料:紫铜材料厚度:1 mm一. 冲压件工艺性分析此工件只有冲孔和落料两个工序。
材料为紫铜,具有良好的冲压性能,适合冲裁。
工件结果简单,有2个直径10mm的孔;孔与孔,孔与边缘之间的距离满足要求,工件的尺寸全部为自由公差,可看着IT14级,尺寸精度底,普通冲裁就能满足要求。
二. 冲压工艺方案的确定该工件包括落料冲孔两个基本工序,可有以下三种工艺方案:方案一:先落料,后冲孔。
采用单工序模生产。
方案二:落料—冲孔复合冲压。
采用复合模生产。
方案三:冲孔—落料级进冲压。
采用级进模生产。
冲裁模说明书
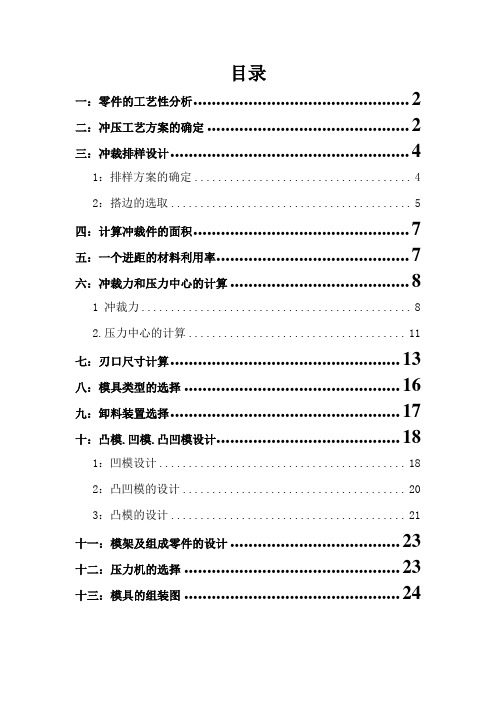
目录一:零件的工艺性分析 (2)二:冲压工艺方案的确定 (2)三:冲裁排样设计 (4)1:排样方案的确定 (4)2:搭边的选取 (5)四:计算冲裁件的面积 (7)五:一个进距的材料利用率 (7)六:冲裁力和压力中心的计算 (8)1 冲裁力 (8)2.压力中心的计算 (11)七:刃口尺寸计算 (13)八:模具类型的选择 (16)九:卸料装置选择 (17)十:凸模.凹模.凸凹模设计 (18)1:凹模设计 (18)2:凸凹模的设计 (20)3:凸模的设计 (21)十一:模架及组成零件的设计 (23)十二:压力机的选择 (23)十三:模具的组装图 (24)一:零件的工艺性分析根据制件的材料、厚度、形状及尺寸,在进行冲裁工艺和模具设计时应注意以下几点:(1)冲裁件虽尺寸不大,形状简单,但要保证制件的尺寸公差,尤其是对空和槽的位置的确定。
板材的尺寸还是一个总要点。
(2)凸凹模的制造尺寸要按落料部分以落料凹模为基准计算 ,落料凸模按间隙值配制;冲孔部分以冲孔凸模为基准计算,冲孔凹模按间隙值配制。
既以落料凹模、冲孔凸模为基准,凸凹模按间隙值配制。
二:冲压工艺方案的确定该工件包括冲孔、落料两个基本工序,可以有以下三种方案:方案一:先落料,后冲孔,采用单工序模生产;方案二:落料—冲孔复合冲压,采用复合模生产;方案三:冲孔—落料连续冲裁,采用级进模生产。
三种方案比较见表2.1表2.1三种方案的比较方案一模具结构简单,但需要两道工序,两副模具,生产率较低,难以满足该零件的年产量要求。
方案二只需一套模具,冲压件的形位精度容易保证,且生产率也高。
尽管模具结构较方案一复杂,但由于零件的几何形状简单,模具制造并不困难。
方案三也只需要一副模具,生产率也高,但零件的冲压精度较差。
欲保证冲压件的形位精度,需要在模具上设置导正销导正,故模具制造安装较复合模复杂,且成本高。
通过对上述三种方案的分析比较,该件的冲压生产采用方案二为佳。
三:冲裁排样设计1:排样方案的确定排样是指冲裁零件在条料、带料或板料上布置的方法。
冲裁模(冲压模具)课程设计说明书_图文.
由图 7-1 三维装配图的(a)图知,模具闭合高度为 H=191mm。
七、模具装配及爆炸图(a) 16图 7-1 三维装配图(b)图 7-2 三维爆炸图八、设计感悟设计心得体会一个多星期的课程设计结束了,在这些天内,我学到了很多的知识,让我对模具设计与制造有了一个更清晰的了解,更坚定了自己对模具行业的信心。
17第一周前两天,我在图书馆查看了大量的参考书,看到了了很多冲压模具。
通过筛选,找出了与本次课程设计相关的几本参考书,作为本次课程设计的工具。
第三天开始,我开始计算相关数据。
本次课程设计,我决定使用计算机辅助设计,一来锻炼我计算机应用能力和打字速度,二可以将我近几个月学习的三维制图软件 creo 应用于实践,更加科学的设计模具,完成本次课程设计。
在大家都在绘图室手工绘图的时候,我在宿舍用计算机还原设计的模具零件,生成三维模型。
然后装配成模具,校核相关尺寸,看其是否发生干涉。
确保结构和原理正确后,我开始用 creo 将模具零件生成二维工程图。
而二维工程图完成后,时间已经进入了课程设计的第四天。
接下来要做的,就是将二维工程图转化为符合国家标准的二维工程图纸。
这就用到了二维制图软件 AutoCAD。
将工程图转换成.dwg 格式,然后用 AutoCAD 打开修改加工。
等一切完成后,一个星期过去了。
从第二周开始,我将撰写课程设计说明书。
我打字速度比较慢,所以这个要花费些时间,不过还好,前期已经把各种数据整理完毕,剩下的只是打字和文字处理了。
花了三天时间整理好了课程设计说明书。
在本次课程设计中,刘伟老师给了很多原理上的指导,纠正了很多错误,在这里表示衷心的感谢。
本次课程设计我感到学以致用的快乐,另外,不可否认,我的计算机辅助设计能力还有非常大的提升空间,当更加努力学习才是。
九、参考文献 [1] 杨占尧.冲压模具典型结构图例.北京:化学工业出版社,2007. [2] 郑家贤.冲压工艺与模具设计.北京:机械工业出版社,2005. [3] 肖祥芷,王孝培.中国模具设计大点.北京:江西科学技术出版社,2003. [4] 卢金封主编.冲压工艺模具学.北京:机械工业出版社,1998. [5] 陈金德主编.材料成型工程.西安:西安交通大学出版社,2000. [6] 范宏才主编.现代锻压机械.北京:机械工业出版社,1994. 18。
冲裁模具设计说明书
车锁后盖冲裁模设计说明书院系材料科学与工程学院班级专业模具姓名学号指导教师评分日期目录第一章零件设计任务 (3)第二章冲裁件的工艺分析 (4)2.1产品结构形状分析2.2产品尺寸精度、粗糙度、断面质量分析2.3产品材料分析2.4产品产量第三章冲裁工艺方案 (5)第四章模具结构形式的选择 (7)4.1模具形式4.2定位装置4.3卸料装置4.4.导向零件4.5模架第五章冲压工艺计算: (8)5.1.排样方案分析52.计算条料宽度5.3材料利用率5.4冲压力计算5.5.压力中心的计算5.45模具工作部分尺寸及公差第六章主要零部件设计 (17)6.1.凹模的设计6.2.卸料元件的设计6.3.卸料板的设计6.4垫板:6.5冲孔凸模的设计6.6凸凹模长度确定6.7冲模闭合高度6.8压力机参数第7章模具结构图 (21)第8章引用书籍第一章零件设计任务零件简图:如图1-1 所示材料:20钢材料厚度:1.5mm图1-1 车锁后盖零件图第二章 冲裁件的工艺分析2.1产品结构形状分析该工件冲裁结构相对简单,虽非对称圆周类零件,但其边缘距离较大,无尖角狭槽,在各直线与曲线连接处均采用适宜的圆角过渡,最小圆角半径为R3,均大于其所允许的最小圆角半径。
料厚为1.5mm 满足许用壁厚要求(孔与孔之间、孔与边缘之间的壁厚),可以冲裁加工。
2.2产品尺寸精度、粗糙度、断面质量分析① 尺寸精度图中尺寸未注公差,属于自由尺寸,而普通冲裁精度要求低于IT13, 所以现产品的设计精度按IT14精度来处理,冲模可按IT11精度来制造。
查表确定公差值,最后得到零件各尺寸为:外形尺寸:087.0025.0074.003.0074.08634.5066.73----00.87--117R R φ内形尺寸:+0.520++22.2φ43.0062.002.1650位置尺寸:37.068± 26.023± 43.015± 25.02±其他尺寸:18.08±② 冲裁件断面质量一般用普通冲裁方式冲1.5mm 的金属板料,其断面粗糙度Ra<6.3um ;毛刺允许高度为240um ;本产品在断面粗糙度和毛刺允许高度上没有特殊的严格要求,冲裁件的断面质量可以保证。
冲裁模(冲压模具)课程设计说明书
模具设计的具体步骤
确定冲裁模的类型和尺寸 设计冲裁模的轮廓和结构 确定冲裁模的冲压力和冲压速度
设计冲裁模的模具材料和热处理工艺 设计冲裁模的冷却系统和润滑系统 设计冲裁模的模具寿命和维护保养方法
冲裁模的制造工艺
冲裁模的设计:根据产品要求进行设计,包括尺寸、形状、材料等 冲裁模的制造:采用数控机床进行加工,保证精度和效率 冲裁模的装配:将各个部件组装成完整的冲裁模 冲裁模的调试:在装配完成后进行调试,确保其性能和精度达到要求
采用环保材料和工艺, 减少对环境的影响
提高冲裁模的自动化 程度,降低人工成本
提高模具寿命的方法和途径
优化模具设计: 合理选择材料、 结构、尺寸等, 提高模具的强度 和耐磨性
提高加工精度: 采用先进的加工 技术和设备,提 高模具的加工精 度,减少误差
加强维护保养: 定期检查、清洗、 润滑模具,及时 发现并处理模具 的磨损和损坏
冲裁模的使用和维护
冲裁模的使用 步骤:安装、 调试、运行、
停机
冲裁模的维护 方法:定期检 查、清洁、润 滑、更换易损
件
冲裁模的安全 操作:遵守操 作规程,注意
安全防护
冲裁模的常见 故障及处理方 法:如卡模、 漏油、噪音等, 需及时处理, 确保生产安全
常见问题的处理和解决方法
冲裁模调试过程中, 如果出现模具损坏, 应及时更换或修复。
设计前的准备工作
确定冲裁模的用途和功能 收集冲裁模的设计要求和技术参数 确定冲裁模的材料和尺寸 准备冲裁模的设计图纸和工具
模具设计的基本流程
确定冲裁 模的设计 要求
设计冲裁 模的尺寸 和形状
确定冲裁 模的材料 和加工工 艺
设计冲裁 模的装配 和调试方 法
冲裁工艺及冲裁模设计
工艺性原则
冲裁模设计应满足生产 工艺要求,确保冲裁件
的质量和精度。
安全性原则
设计应确保操作安全, 防止模具使用过程中出
现危险。
经济性原则
在满足功能和安全性的 前提下,降低模具成本
。
维护性原则
设计应便于模具的安装 、调试、维修和保养。
冲裁模设计的步骤与方法
明确设计任务
了解冲裁件的结构、尺寸、材料和生产批量 等要求。
。
强度和韧性
选择具有良好强度和韧性的材 料,以确保模具在使用过程中 不易开裂或断裂。
热处理性能
选择适合的热处理工艺,以提 高模具的硬度和耐久性。
经济性
在满足性能要求的前提下,尽 量选择价格较低的材料,降低
模具成本。
03 冲裁模结构设计
冲裁模结构的选择
根据产品要求选择合适的冲裁模结构,如简单模 、连续模、复合模等。
03
固定方式。
冲裁模的装配与调试
01
根据设计图纸,正确装 配凸模、凹模、压板、 螺栓等零件。
02
检查装配后的冲裁模是 否符合设计要求,并进 行必要的调整。
03
进行试冲,检查冲裁件 的质量、尺寸精度和模 具的稳定性,对模具进 行调整优化。
04
对冲裁模进行保养和维 护,确保其长期稳定运 行。
04 冲裁模设计实例分析
Байду номын сангаас
实例一:简单冲裁模设计
总结词
结构简单、成本低、适用于中小批量生产
详细描述
简单冲裁模设计通常采用单工序模具,结构相对简单,制造成本较低,适用于中小批量生产。这种模具一般由上 模和下模组成,通过压力机将上模压下,使板料分离,完成冲裁工序。
实例二:复杂冲裁模设计
- 1、下载文档前请自行甄别文档内容的完整性,平台不提供额外的编辑、内容补充、找答案等附加服务。
- 2、"仅部分预览"的文档,不可在线预览部分如存在完整性等问题,可反馈申请退款(可完整预览的文档不适用该条件!)。
- 3、如文档侵犯您的权益,请联系客服反馈,我们会尽快为您处理(人工客服工作时间:9:00-18:30)。
冲制图3-146所示工件,材料为08钢,料厚1mm,大批量生产,试完成:
1)工艺设计
2)模具设计
3)绘制模具装配草图
1.零件的工艺性分析
(1)结构工艺性该零件结构简单,形状对称,无悬臂,孔径、孔边距均大于
1.5倍料厚,可以直接冲出,因此比较适合冲裁。
(2)精度由表3-11和表3-12可知,该零件的尺寸精度均不超过ST4等级,因此可以通过普通冲裁方式保证零件精度要求。
(3)原材料 08钢是常用的冲压材料,具有良好的塑性,(伸长率δ= 33%),屈服极限>=195MPa,适合冲裁加工。
2.工艺方案确定
该零件需要落料和冲孔两道工序完成,可采用的方案有三种:
方案一:单工序冲裁,先落料再冲孔。
方案二:复合冲裁,落料冲孔同时完成。
方案三:级进冲裁,先冲孔再落料。
由于是大批量生产,因此方案一不满足生产率的要求,方案二和方案三都具
有较高的生产效率,虽然方案三比方案二操作方便,但方案二能得到较高的精度,且由于被冲板料较薄,特别是外形与内孔的同轴度要求,因此选用方案二,即采用复合冲压。
3.模具总体设计
(1)模具类型的确定考虑操作的方便与安全性,选用倒装复合模。
(2)模具零件结构形式确定。
1)送料及定位方式。
采用手工送料,导料销导料,挡料销挡料。
2)卸料与出件方式。
采用弹性卸料装置卸料,刚性推件装置推件。
3)模架的选用。
选用中间导柱导向的滑动导向模架。
4.工艺计算
(1)排样设计根据工件形状,这里选用有废料的单排排样类型,查表3-3得搭边a1 = 1.5mm,侧搭边a = 2mm,则搭边宽度B= 40mm + 2
x 2mm = 44mm,进距S = 23.66mm + 23.66mm + 1.77mm = 49.01mm。
查
表3-4得裁板误差Δ = 0.5mm,于是得到如图所示排样图。
根据GB/T708---2006可知,这里选用的钢板规格为1420mm x 740mm,
采用横裁法,则可裁得宽度为44mm的条料32条,每条条料可冲出
零件15个。
由图3-146可计算出该零件的面积:A=1279.92mm2,则
材料利用率为
η= NA
LB
x 100% =
32 x 15 x 1279.92
1420 x 740
x 100% = 58.47%
(2)冲裁工艺力计算由于采用复合冲裁,则总的冲裁力F冲裁为
落料力F
落料和冲孔力F
冲孔
之和。
其中:
F
落料= KL
落料
tτ
b
= 1.3 x 162.0238 x 1 x 400 = 84.25kN
F
冲孔= KL
冲孔
tτ
b
= 1.3 x ( 2 x 27.6460 + 69.1150 ) x 1 x 400 = 64.69kN
则总的冲裁力
F
冲裁 = F
落料
+ F
冲孔
= 84.52kN + 64.69kN =149.21kN
F
卸 = K
卸
F
落料
= 0.045 x 84.25kN =3.79kN
F
推 = nK
推=
F
冲孔
= 6 x 0.055 x 64.69kN = 21.35kN
K
卸、K
推
由表3-8查得。
由表3-30查得凹模刃口直壁高度为5mm,则n =
5 / 0.8 ≈ 6。
(3)压力中心的计算
建立如图所示坐标系
计算落料外形压力中心由于冲裁件外形对称,压力中心位于冲裁轮廓的几何中心上,即压力中心坐标为(0,0)。
5.模具零件详细设计
(1)工作零件设计工作零件包括凸模、凹模和凸凹模。
由于零件外形不规则,其模具采用配合加工法制造,即落料时以凹模为基准,只需计算凹模刃口尺寸和公差;中间的孔以凸模为基准,只需计算凸模刃口尺寸及公差;凹凸模刃口尺寸分别与落料凹模刃口和冲孔凸模刃口的实际尺寸配作,保证单边间隙为c
min。
1)模具间隙。
由于零件有公差要求,这里选用ii类冲裁间隙,有表3-30
查得:C = (3 ~ 7) % t,即c
min = 0.03 x 1mm = 0.03mm;c
max
= 0.07 x 1mm
= 0.07mm。
2)落料凹模和冲孔凸模刃口的制造公差分别按照IT7和IT6级选取,公差值由GB/T1800.3---2009查得。
尺寸R8由冲压件尺寸公差(GB/T13914---2002)按ST7级精度查表3-11得偏差值。
落料凹模和冲孔凸模刃口尺寸计算见下表。
3)落料凹模采用整体式结构,外形为矩形,首先由经验公式计算出凹模外形
的参考尺寸,再查阅标准得到凹模外形的标准尺寸,见下表。
落料凹模材料选用Cr12,热处理60~64HRC。
4)冲孔凸模为圆形,参照JB/T5826---2008进行设计。
材料选用Cr12,热处理58~62HRC。
(2)其他板类零件的设计当落料凹模的外形尺寸确定后,即可根据凹模外形尺寸查阅有关标准或资料得到模座、固定板、垫板、卸料板的外形尺寸。
查GB/T2851---2008得:滑动导向模架中间导柱160 x 125 x(160~190)GB/T2851---2008。
为了绘图方便,还需要查出上、下模座的规格尺寸:由GB/T2855.2---2008查得:滑动导向下模座中间导柱160 x 125 x 40。
由GB/T2855.1---2008查得:滑动导向上模座中间导柱160 x 125 x 40。
查JB/T7643.2---2008得:矩形固定板160 x 125 x 16 JB/T7643.2---2008。
(凸凹模固定板)
查JB/T7643.2---2008得:矩形固定板160 x 125 x 12 JB/T7643.2---2008。
(冲孔凸模固定板)
查JB/T7643.3---2008得:矩形固定板160 x 125 x 6 JB/T7643.2---2008。
(冲孔凸模垫板)
查JB/T7643.3---2008得:矩形固定板160 x 125 x 10 JB/T7643.2---2008。
(空心垫板)
查表3-39得卸料板的厚度为14mm,则卸料板的尺寸为:160 x 125 x 14。
(3)导柱、导套的选用查GB/T2861.1---2008和GB/T2861.3---2008得:滑动导向导柱 A 25 x 150 GB/T2861.1---2008。
滑动导向导柱 A 28 x 150 GB/T2861.1---2008。
滑动导向导套 A 25 x 85 x 33 GB/T2861.3---2008。
滑动导向导套 A 28 x 85 x 33 GB/T2861.3---2008。
(4)模柄的选用根据初选设备JB23-10模柄孔的尺寸,查JB/T7646.1---2008得:压入式模柄B 40mm x 110mm。
(5)推荐块的设计推件块的外形与落料凹模孔单边保持0.1mm的间隙,推件块的内孔与冲孔凸模采用H8/f8的间隙配合,推件块的台阶高度为5mm,总高度为10.5mm。
(6)螺钉、销钉的选用查表3-43,选M6内六角圆柱头螺钉,直径为φ6mm 的圆柱形销钉。
6.设备选择及校核
(1)设备选择由前述计算出的冲裁工艺力,确定模具结构形式后,可得到总
的冲压力F
总为:F
总
= F
冲裁
+ F
卸
+ F
推
= 149.21kN + 3.79kN + 21.35kN
= 174.35kN
选择JB23-20压力机,主要参数如下:
公称压力:200kN。
最大闭合高度:250mm,闭合高度调节量:55mm。
工作台尺寸:500mm x 330mm;工作台孔尺寸:260mm x 180mm。
模柄孔尺寸:φ40mm。
(2)设备验收主要验收平面尺寸和闭合高度。
由标记为“滑动导向下模座中间导柱160 x 125 x 40 GB/T2855.2---2008”
可知,下模座平面的最大外形尺寸为:294mm x 259mm,长度方向单边小
于压力机工作台面尺寸(500 – 294)mm/2 = 103mm,下模座的平面尺寸单边大于压力机工作台孔尺寸(294 - 260)mm/2 = 17mm,因此满足模具
安装要求。
模具闭合高度为:40mm + 10mm + 6mm + 12mm + 16mm + 48mm + 40mm –
(1 + 0.5)mm = 170.9mm,小于压力机的最大闭合高度,因此所选设备合
适。
7.绘图
当上述各零件设计完成后,即可绘制模具总装配图,模具装配草图如下。