重油催化裂化基础知识
重油催化裂化

重油催化裂化(residue fluid catalytIC cracking,即RFCC)工艺的产品是市场极需的高辛烷值汽油馏分,轻柴油馏分和石油化学工业需要的气体原料。
由于该工艺采用了分子筛催化剂、提升管反应器和钝化剂等,使产品分布接近一般流化催化裂化工艺。
但是重油原料中一般有30%~50%的廉价减压渣油,因此,重油流化催化裂化工艺的经济性明显优于一般流化催化工艺,是近年来得到迅速发展的重油加工技术。
㈠重油催化裂化的原料所谓重油是指常压渣油、减压渣油的脱沥青油以及减压渣油、加氢脱金属或脱硫渣油所组成的混合油。
典型的重油是馏程大于350℃的常压渣油或加氢脱硫常压渣油。
与减压馏分相比,重油催化裂化原料油存在如下特点:①粘度大,沸点高;②多环芳香性物质含量高;③重金属含量高;④含硫、氮化合物较多。
因此,用重油为原料进行催化裂化时会出现焦炭产率高,催化剂重金属污染严重以及产物硫、氮含量较高等问题。
㈡重油催化裂化的操作条件为了尽量降低焦炭产率,重油催化裂化在操作条件上采取如下措施:1、改善原料油的雾化和汽化由于渣油在催化裂化过程中呈气液相混合状态,当液相渣油与热催化剂接触时,被催化剂吸附并进入颗粒内部的微孔,进而裂化成焦炭,会使生焦量上升,催化活性下降。
因此可见,为了减少催化剂上的生焦量,必须尽可能地减少液相部分的比例,所以要强化催化裂化前期过程中的雾化和蒸发过程,提高气化率,减少液固反应。
2、采用较高的反应温度和较短的反应时间当反应温度提高时,原料的裂化反应加快较多,而生焦反应则加快较少。
与此同时,当温度提高时,会促使热裂化反应的加剧,从而使重油催化裂化气体中C1、C2增加,C3、C4 减少。
所以宜采用较高反应温度和较短的反应时间。
㈢重油催化裂化催化剂重油催化裂化要求其催化剂具有较高的热稳定性和水热稳定性,并且有较强的抗重金属污染的能力。
所以,目前主要采用Y型沸石分子筛和超稳Y型沸石分子筛催化剂。
㈣重油催化裂化工艺1、重油催化裂化工艺与一般催化裂化工艺的异同点两工艺既有相同的部分,亦有不同之处,完全是由于原料不同造成的。
催化裂化
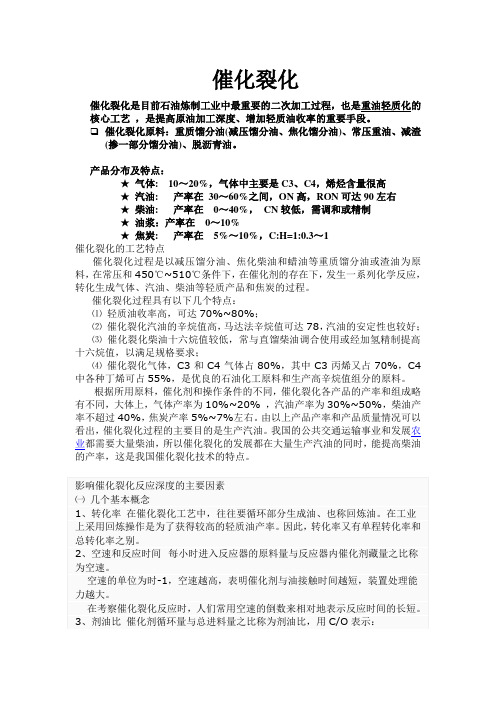
催化裂化催化裂化是目前石油炼制工业中最重要的二次加工过程,也是重油轻质化的核心工艺,是提高原油加工深度、增加轻质油收率的重要手段。
催化裂化原料:重质馏分油(减压馏分油、焦化馏分油)、常压重油、减渣(掺一部分馏分油)、脱沥青油。
产品分布及特点:★气体: 10~20%,气体中主要是C3、C4,烯烃含量很高★汽油: 产率在30~60%之间,ON高,RON可达90左右★柴油: 产率在0~40%,CN较低,需调和或精制★油浆:产率在0~10%★焦炭: 产率在5%~10%,C:H=1:0.3~1催化裂化的工艺特点催化裂化过程是以减压馏分油、焦化柴油和蜡油等重质馏分油或渣油为原料,在常压和450℃~510℃条件下,在催化剂的存在下,发生一系列化学反应,转化生成气体、汽油、柴油等轻质产品和焦炭的过程。
催化裂化过程具有以下几个特点:⑴轻质油收率高,可达70%~80%;⑵催化裂化汽油的辛烷值高,马达法辛烷值可达78,汽油的安定性也较好;⑶催化裂化柴油十六烷值较低,常与直馏柴油调合使用或经加氢精制提高十六烷值,以满足规格要求;⑷催化裂化气体,C3和C4气体占80%,其中C3丙烯又占70%,C4中各种丁烯可占55%,是优良的石油化工原料和生产高辛烷值组分的原料。
根据所用原料,催化剂和操作条件的不同,催化裂化各产品的产率和组成略有不同,大体上,气体产率为10%~20% ,汽油产率为30%~50%,柴油产率不超过40%,焦炭产率5%~7%左右。
由以上产品产率和产品质量情况可以看出,催化裂化过程的主要目的是生产汽油。
我国的公共交通运输事业和发展农业都需要大量柴油,所以催化裂化的发展都在大量生产汽油的同时,能提高柴油的产率,这是我国催化裂化技术的特点。
在同一条件下,剂油比大,表明原料油能与更多的催化剂接触。
㈡影响催化裂化反应深度的主要因素影响催化裂化反应转化率的主要因素有:原料性质、反应温度、反应压力、反应时间。
1、原料油的性质原料油性质主要是其化学组成。
炼油工艺学第十章 催化裂化第一节 催化裂化概述

炼油工艺学
7
催化裂化技术今后的发展方向: ① ② ③ ④ 加工重质原料 降低能耗 减少环境污染 适应多种生产需要的催化剂和工艺
⑤
过程模拟和计算机应用
2019/2/16
炼油工艺学
8
三、工艺流程概述
包括:反应-再生系统、分馏系统、吸收-稳定系 统、再 生烟气的能量回收系统和液化气、 汽油的脱硫精制等
技术发展:反应-再生型式(工艺)和催化剂性能 两个方面
2019/2/16 炼油工艺学 5
催化裂化的发展可以分成以下几个阶段:
1.天然白土和固定床催化裂化
2.合成硅铝催化剂和移动床催化裂化 ① ② 移动床催化裂化 流化床催化裂化
3.分子筛催化剂和提升管催化裂化
2019/2/16
炼油工艺学
6
2019/2/16
2019/2/16 炼油工艺学 2
一、催化裂化的原料和产品
催化裂化是目前石油炼制工业中最重要的二次加工过程, 也是重油轻质化的核心工艺 催化裂化是提高原油加工深度、增加轻质油收率的重要 手段 催化裂化于19化馏分油)、
常压重油、减渣(掺一部分馏分油)、脱沥青油
2019/2/16
炼油工艺学
14
低温高压 防热
提高C3回收率 的关键
高温低压 吸热
提高C4回收率 的关键
2019/2/16
炼油工艺学
15
2019/2/16
炼油工艺学
16
四、提升管催化裂化装置的类型
催化裂化的反应 -再生系统有多种形式,如高
低并列式、同轴式、两段提升管催化裂化等
至于分馏系统和吸收 -稳定系统,在各催化裂
提高富气压缩机的入口压力以降低气压机的功率损耗
重质油催化裂化化学

• 含硫化合物对于原料油的反应性能也有相 当的影响。硫对催化剂也是暂时的毒物, 会降低其活性和转化为汽油的选择性,同 时使干气产率增大,
•
影响催化裂化过程中硫在产物中分布的 重要因素是含硫化合物的组成结构。研究 表明,在催化裂化条件下,硫醚类化合物 绝大部分裂化生成H2S;而噻吩类化合物中 除有一部分也裂化开环生成H2S外,有些经 侧链断裂反应进入轻质产物,与芳香环并 合的噻吩类化合物则易于缩合进入焦炭。
• 2. 多环的芳香性物质含量高 • 重质油中含有较多的多环芳香烃以及胶质 和沥青质,这些组分易于吸附在催化剂表面 而生焦。 • 对于此类重质原料油,一般是以其残炭值 来衡量它在催化剂上的生焦倾向,有的则 认为应依据其中庚烷沥青质含量。
• 3. 重金属含量高 • 前已述及,原油中的镍、钒等重金属绝大 部分集中在其渣油中。这些金属在催化裂 化反应时绝大部分沉积于催化剂表面,并随 着催化剂的循环而不断积累,使其活性和选 择性逐渐下降。
•
由此可见,单个提升管反应器的高度过高,也 就是反应时间过长是不利的。为此,对于过高的 提升管反应器,有的采用在适当的高度注入诸如 冷态的直馏或催化汽油馏分等难裂解的所谓“中 止剂”,降低反应器上段的温度,以抑制轻质产 物的二次裂化。 为了避免轻质产物的过度裂化和降低汽油的烯 烃含量,近年来出现了许多相关的新技术,包括 用两个提升管反应器以多种方式进行组合,或将 一个提升管分区以不同条件进行反应等各种新工 艺。
三、重油催化裂化原料氢碳比的 影响及杂原子在产物中的分布
• 1.原料氢碳比的影响 • 大庆、胜利、孤岛、大港、华北和辽河 6种 减压渣油的在性质和组成结构上差别很大 的23个抽出油油样的催化裂化产物分布数 据,可以看出汽油的产率基本与原料油的 氢碳比呈线性关系,同时,焦炭产率与原 料油的氢碳比也基本呈线性关系。
催化裂化知识

催化裂化知识催化裂化是一种重要的炼油工艺,通过催化剂的作用将重质石油馏分转化为轻质产品。
在催化裂化过程中,石油馏分经过加热后与催化剂接触,发生裂化反应,生成较轻质的烃类化合物。
催化裂化技术广泛应用于石油炼制行业,使得石油资源得以充分利用。
催化裂化的原理是通过催化剂的作用降低反应的活化能,加快反应速率。
催化剂是一种能够提供活性位点的物质,它能够吸附反应物分子并改变其化学键,从而促进反应的进行。
常用的催化剂有酸性催化剂、碱性催化剂和金属催化剂等。
在催化裂化过程中,石油馏分首先被预热至适宜的温度,然后进入催化剂床层。
在催化剂的作用下,石油馏分中的大分子化合物发生裂化反应,生成烃类产品。
裂化反应主要包括裂解、重排和异构化等过程。
裂解是指将长链烃分子裂解为短链烃分子,重排是指短链烃分子发生位置变化,异构化是指短链烃分子发生结构变化。
催化裂化的反应条件主要包括温度、压力和催化剂的选择等。
温度是影响催化裂化反应速率和产物分布的重要因素。
适宜的温度能够提高反应速率,但过高的温度会导致生成焦炭等副产物。
压力对催化裂化反应的影响相对较小,一般较低的压力即可满足反应的需求。
催化剂的选择对反应的效果有着重要影响,不同的催化剂对产品分布、产率和选择性有不同的影响。
催化裂化技术的应用使得石油炼制过程更加灵活多样,能够根据市场需求灵活调整产品结构。
通过合理的催化剂设计和反应条件控制,可以实现不同产品的选择性裂化。
催化裂化不仅能够提高汽油产率,还能够产生重要的石化原料,如乙烯、丙烯等。
催化裂化技术的发展也为石油炼制行业的绿色转型提供了重要支持。
然而,催化裂化过程中也存在一些问题。
首先,催化剂的失活是一个严重的问题,随着反应的进行,催化剂会逐渐失去活性,需要定期更换。
其次,催化裂化反应的过程较复杂,需要综合考虑反应的热力学和动力学特性,以及催化剂的选择和反应条件的控制。
此外,催化裂化过程中还会产生大量的副产物,如焦炭和烟气,对环境造成一定的污染。
炼油催化裂化理论知识
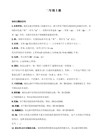
第二部分基础理论知识第二章炼油催化裂化理论知识2.1概述2.1.1催化裂化发展过程1938年4月6日年世界上第一套固定床催化裂化工业化装置问世,这是炼油工艺的重大发展,然而它存在一系列无法克服的缺点:设备结构复杂,操作繁琐,控制困难。
要克服固定床的缺点,需要两项革新,即催化剂在反应和再生操作之间循环和减小催化剂的粒径。
第一项革新结果出现了移动床,两项革新的结合得到了流化床。
本世纪40年代相继出现了移动床催化裂化和流化床催化裂化装置。
60年代中期出现的分子筛型催化剂带来了重大突破,成为催化技术发展的里程碑。
我国第一套移动床催化裂化装置是由前苏联设计并于1958年投产的。
1964年建成第二套,以后我国自己开发了流化催化裂化装置,故以后移动床催化裂化装置就不再建设了,这两套移动床催化裂化装置也于80年代改为流化催化裂化装置。
我国流化催化裂化的发展始于60年代,1965年5月5日,我国第一套0.6Mt /a同高并列式流化催化裂化装置在抚顺石油二厂建成投产,标志着我国炼油工业进入一个新阶段。
30多年来,我国流化催化裂化在炼油工业中一直处于重要地位,目前仍在发展。
到1993年底统计我国催化裂化装置的能力为5000余万吨/年,仅次于美国,位居世界第二。
随着石油资源的短缺和原油日趋变重,流化催化裂化在加工重质原料方面也取得了进展。
催化裂化掺炼渣油,提高轻质油收率最为显著,我国经过“六五”重大技术攻关,攻克了再生器的内外取热设施,渣油雾化技术,提升管出口快速分离技术,抗重金属污染催化剂等一系列技术难关。
目前,我国渣油催化裂化技术已发展成多种形式,有带内外取热的单段再生,不带取热的两段再生,带外取热的两段再生等。
到1993年底,石化总公司50套催化裂化装置,已有33套掺炼了渣油,掺炼量达到919万吨,渣油掺炼比达到了24.38%,已成为我国重要的渣油转化装置对提高轻质油收率,增加经济效益,起到非常重要的作用。
尽管催化裂化装置具有漫长的历史,但他远非一个完整的技术。
催化裂化学习资料
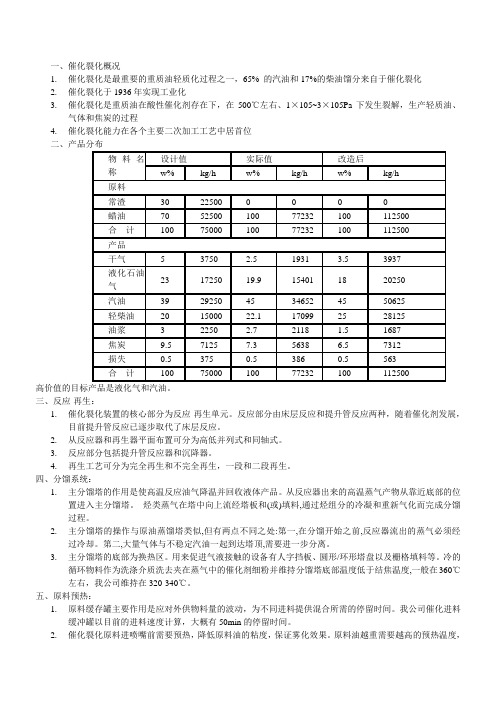
一、催化裂化概况1.催化裂化是最重要的重质油轻质化过程之一,65% 的汽油和17%的柴油馏分来自于催化裂化2.催化裂化于1936年实现工业化3.催化裂化是重质油在酸性催化剂存在下,在500℃左右、1×105~3×105Pa下发生裂解,生产轻质油、气体和焦炭的过程4.催化裂化能力在各个主要二次加工工艺中居首位高价值的目标产品是液化气和汽油。
三、反应-再生:1.催化裂化装置的核心部分为反应-再生单元。
反应部分由床层反应和提升管反应两种,随着催化剂发展,目前提升管反应已逐步取代了床层反应。
2.从反应器和再生器平面布置可分为高低并列式和同轴式。
3.反应部分包括提升管反应器和沉降器。
4.再生工艺可分为完全再生和不完全再生,一段和二段再生。
四、分馏系统:1.主分馏塔的作用是使高温反应油气降温并回收液体产品。
从反应器出来的高温蒸气产物从靠近底部的位置进入主分馏塔。
烃类蒸气在塔中向上流经塔板和(或)填料,通过烃组分的冷凝和重新气化而完成分馏过程。
2.主分馏塔的操作与原油蒸馏塔类似,但有两点不同之处:第一,在分馏开始之前,反应器流出的蒸气必须经过冷却。
第二,大量气体与不稳定汽油一起到达塔顶,需要进一步分离。
3.主分馏塔的底部为换热区。
用来促进气液接触的设备有人字挡板、圆形/环形塔盘以及栅格填料等。
冷的循环物料作为洗涤介质洗去夹在蒸气中的催化剂细粉并维持分馏塔底部温度低于结焦温度,一般在360℃左右,我公司维持在320-340℃。
五、原料预热:1.原料缓存罐主要作用是应对外供物料量的波动,为不同进料提供混合所需的停留时间。
我公司催化进料缓冲罐以目前的进料速度计算,大概有50min的停留时间。
2.催化裂化原料进喷嘴前需要预热,降低原料油的粘度,保证雾化效果。
原料油越重需要越高的预热温度,以降低粘度。
过高的温度会降低剂油比,对产品分布有一定影响。
六、进料喷嘴—提升管:1.大多数FCC装置进料喷嘴是“升高”型的,位于提升管底部之上5-12m的位置(我公司约7m),提供催化剂分散流化空间。
催化催化裂化技术

催化催化裂化技术催化裂化技术是一种重要的炼油工艺,可以将重质石油馏分转化为高附加值的轻质产品。
本文将从催化裂化技术的原理、应用和发展前景等方面进行探讨,以期为读者提供对该技术的全面了解。
一、催化裂化技术的原理催化裂化技术是通过催化剂的作用将重质石油馏分分解为较轻的产品。
其主要原理是在高温和高压的条件下,将原料油与催化剂接触,使其发生裂化反应。
这种反应可以将长链烃分子裂解成短链烃分子,从而提高汽油和燃料油的产率。
催化裂化反应主要分为两个阶段:热裂化和催化裂化。
在热裂化阶段,原料油在高温下分解成烃气和液体烃。
然后,在催化剂的作用下,烃气和液体烃进一步反应,生成较轻的产品,如汽油、液化气和柴油等。
二、催化裂化技术的应用催化裂化技术在炼油行业中具有广泛的应用。
首先,它可以提高汽油的产率。
由于汽车的普及,对汽油的需求量不断增加。
催化裂化技术可以将重质石油馏分转化为轻质的汽油,从而满足市场需求。
催化裂化技术可以生产出高质量的柴油。
在催化裂化过程中,石油馏分中的硫、氮和金属等杂质可以得到有效去除,从而提高柴油的质量。
这对于减少柴油排放的污染物具有重要意义。
催化裂化技术还可以生产出液化气、石脑油和石化原料等产品。
这些产品在化工、冶金和化肥等行业中具有广泛的应用。
三、催化裂化技术的发展前景随着能源需求的增加和石油资源的日益枯竭,催化裂化技术在未来的发展前景十分广阔。
一方面,随着汽车工业的高速发展,对汽油的需求将持续增加,催化裂化技术将成为满足市场需求的重要手段。
另一方面,随着环境保护意识的提高,对燃料油质量的要求也越来越高。
催化裂化技术可以提高燃料油的质量,减少对环境的污染,因此在未来的发展中具有重要的作用。
随着科技的不断进步,催化剂的研发和改进也将推动催化裂化技术的发展。
新型的催化剂可以提高反应的选择性和活性,从而提高产品的产率和质量。
催化裂化技术作为一种重要的炼油工艺,在提高石油产品产率和质量方面具有重要的作用。
- 1、下载文档前请自行甄别文档内容的完整性,平台不提供额外的编辑、内容补充、找答案等附加服务。
- 2、"仅部分预览"的文档,不可在线预览部分如存在完整性等问题,可反馈申请退款(可完整预览的文档不适用该条件!)。
- 3、如文档侵犯您的权益,请联系客服反馈,我们会尽快为您处理(人工客服工作时间:9:00-18:30)。
重油催化裂化基础知识广州石化总厂炼油厂重油催化裂化车间编一九八八年十二月第一章概述第一节催化裂化在炼油工业生产中的作用催化裂化是炼油工业中使重质原料变成有价值产品的重要加工方法之一。
它不仅能将廉价的重质原料变成高价、优质、市场需要的产品,而且现代化的催化裂化装置具有结构简单,原料广泛(从瓦斯油到常压重油),运转周期长、操作灵活(可按多产汽油、多产柴油,多产气体等多种生产方法操作),催化剂多种多样,(可按原料性质和产品需要选择合适的催化剂),操作简便和操作费用低等优点,因此,它在炼油工业中得到广泛的应用。
第二节催化裂化生产发展概况早在1936年美国纽约美孚真空油公司(、)正式建立了工业规模的固定床催化裂化装置。
由于所产汽油的产率与辛烷值均比热裂化高得多,因而一开始就受到人们的重视,并促进了汽车工业发展。
如图所示,片状催化剂放在反应器内不动,反应和再生过程交替地在同一设备中进行、属于间歇式操作,为了使整个装置能连续生产,就需要用几个反应器轮流地进行反应和再生,而且再生时放出大量热量还要有复杂的取热设施。
由于固定床催化裂化的设备结构复杂,钢材用量多、生产连续性差、产品收率与性质不稳定,后为移动床和流化床催化裂化所代替。
第一套移动床催化裂化装置和第一套流化床催化裂化(简称装置都是1942年在美国投产的。
固定床反应器移动床催化裂化的优点是使反应连续化。
它们的反应和再生过程分别在不同的两个设备中进行,催化裂化在反应器和再生器之间循环流动,实现了生产连续化。
它使用直径约为3毫米的小球型催化剂。
起初是用机械提升的方法在两器间运送催化剂,后来改为空气提升,生产能力较固定床大为提高、空气产品质量也得到了改善。
由于催化剂在反应器和再生器内靠重力向下移动、速度很缓慢,所以对设备磨损很小,但移动床的设备仍较复杂,耗钢量仍较大,特别是处理量在80万吨/年以上的大型装置、移动床远不如流化床优越。
因此现代的大型催化裂化装置都是采用流化床。
流化催化裂化()的优点是:原料选择范围比较宽、主要产品汽油的收率和质量都比较高,装置处理量大,经济上更有利,热能的利用比较合理和设备的结构比较简单,工艺过程简单,操作容易灵活性大。
四十多年来,开发了很多型式。
但按反应器和再生器的相对位置和结构的不同分为两大类:其一是反应器和再生器处于分开位置的并列式。
早期的并列式大多是两器布置在一个水平上,称为同度并列式。
六十年代后期,由于分子筛催化剂的应用,提升管反应器得到很大发展,为了满足提升管长度的要求,大多采用高低并列式。
反应器位置较高,再生器位置较低,另一类是反应器和再生器重叠在一起的同轴式。
并列式可以埃索公司五十年代初期的Ⅳ型装置为代表。
这种型号的装置共建了40套。
它是由四十年代的Ⅰ、Ⅱ和Ⅲ型装置发展起来的。
Ⅰ型装置是最初的一种工业化型式,于1942年5月在美国巴吞鲁()炼油厂首次建成投产,处理能力为65万吨/年。
以后又陆续建成了两套。
Ⅰ型属于上流式,装置有上流式反应和再生两大部分。
系统内所有循环的催化剂都是自下而上地通过反应器和再生器,反应时,催化剂,反应产品和烟道气一起从反应器顶部出来。
这样类型的装置有许多缺点,例如:催化剂输送管线过长,压力降比较大;催化剂的粉碎严重,损失较大;装置过高,达60m,比较笨重;操作弹性小,只能加工轻质原料等,由于有这么多缺点,所以Ⅰ型装置很快就改进为Ⅱ型装置。
Ⅱ型装置属于下流式。
第一套Ⅱ型装置于1944年投产,陆续建成31套。
与Ⅰ型装置相比,其主要改进是:(1)、催化剂由反应器和再生器的西部引出,因此简化了催化剂的输送系统。
(2)、反应器和再生器中保持密相床层。
(3)、催化剂的输送由滑阀来控制。
(4)、装置的高度由Ⅰ型60米降低到50-55米,因而节约了钢材和投资。
Ⅲ型装置又是型的改进型式,第一套与1947年建成投产,其特点如下:(1)、再生器的操作压力比Ⅰ、Ⅱ型再生的操作压力为10-30千帕(表),而反应器的操作压力为80-120千帕(表),因此为了防止油气倒窜,再生器的位置就得比反应器高得多,才能保证再生器的立管有足够的压头(立管长23-25米)。
在Ⅲ型设计中,自动控制和滑阀结构有较大的改进,可使再生器的操作压力提高,并和反应器的操作压力相接近。
这样,两器就可以并列地放置在高度差不多相同的位置上,因此Ⅲ型的高度就由Ⅱ型的50-55米,降低到37-40m。
这不仅可以节约钢材,而且也给操作和检修带来很多方便。
(2)、反应器和再生器内的旋风分离器,由Ⅱ型的一级改为二级,同时,由于采用了微球催化剂,旋风分离器的效率大大提高,这样就可以取消除尘器。
Ⅳ型装置第一套于1951年投产。
其所需的钢材和投资比Ⅱ型节省20%,主要特点如下:(1)、催化剂由U型管密相输送。
(2)、反应器和再生器之间的催化剂循环、主要由改变U型管两端的催化剂密度来调节,不像Ⅱ、Ⅲ型靠滑阀来调节。
(3)、由反应器输送到再生器的催化剂,不是通过再生器的分布板、而是直接由密相提升管送入分布板上的流化床,因此可以减少分布板的腐蚀。
同轴式装置可以凯洛格公司的正流式A、B和C等三种型式为代表。
环球油品公司烟囱式的也是同轴式的一种。
第一套A型正流式装置于1951年在加拿大建成,处理能力为15万吨/年。
同年在美国的庞卡成()建成第二套,处理能力41.7万吨/年。
以后又陆续建成了四套。
使这种型式的装置总数达到6套,A型正流式的装置特点是:(1)、反应器位于再生器顶部,催化剂输送管线全在两器之内。
(2)、提升管和立管中的催化剂流量都是由塞阀控制。
(3)、反应器的旋风分离器只有一级。
(4)、反应器的操作压力为70-90千帕(表),再生器的操作压力为120-130千帕(表)。
由于再生器的压力比较高,当时又没有考虑发到烟道气能量回收的问题,故主风机动力消耗比较大,这是A型装置的主要缺点之一。
第一套B型正流式装置于1953年末投产,以后又陆续兴建了这种型式的装置总计15套。
B型和A型装置的主要差别是B型的再生器装在反应器之上,操作压力比较低,为50-60千帕(表),动力消耗比较省。
第一套C型正流式装置于1963年投产,在美国石油公司()德克萨斯炼油厂。
处理能力为247.9万吨/年。
这样装置共建成10套,其主要特点是:(1)、反应器装在再生器之上;增设了一氧化碳锅炉和气体透平,为回收烟道气的余热和动力。
(2)第一次采用两根提升管,将新鲜原料和回炼油分别在提升管内进行选择型的裂化。
属于同轴式的环球油品公司的烟囱式装置共建成72套。
第一套这样的装置于1947年投产。
这种装置的反应器位于再生器之上。
待生催化剂通过外部的汽提,经过蒸汽汽提后,流过外部的立管和滑阀,进入再生器。
再生催化剂也是经由外部的提管和滑阀送入反应器的。
催化剂的循环量靠滑阀来调节。
相对来说我国对催化裂化技术的开发、应用起步较晚主要因为五十年代中国一直被世人认为是贫油国,当时我国的石油与石油产品主要依靠从苏联进口,进入六十年代以后,由于大庆油田的开发、原有产品大幅度上升,达到自给自足。
1961年,国家科委组织各有关部部委根据世界先进炼油技术的发展趋势,制定了五个炼油工业的重点攻关项目,被称为“五朵金花”、催化裂化为其中的“朵”,在全国各部门的协作努力下,1965年5月在抚顺二厂建成了我国第一套年处理为60万吨的流化催化裂化装置,目前已建成大小30余套装置。
催化裂化技术的发展与催化剂的不断改进和提高也是分不开的。
最初固定床所用的催化剂是经过活化处理的天然白土、质量很差。
1940年开始采用工人合成的硅酸铝催化剂。
流化床所用的催化剂,先是由小球催化剂磨碎成不规则形状的细粉,以后出现了微球状催化剂。
到1964年又制成了质量更好的分子筛催化剂,这样,由于催化剂的发展,使催化裂化的优越性又大为提高。
与此同时,流化床催化裂化工业装置逐渐推广采用提升管反应器,代替原来的床层反应器,采用高温短接触,以充分发挥分子筛催化剂的特点,并克服了床层反应的特点,使装置改造后生产能力大幅度增加,汽油产率显著提高,产品质量也得到进一步改善。
第二节催化裂化的主要特点1、催化剂需不断地再生催化裂化是靠催化剂的作用在一定温度(460~530℃)条件下,使原料油经过一系列化学反应,裂化成轻质油产品,流化催化裂化的催化剂是固体。
原料油在与催化剂接触反应时,总是要生成一些焦炭,沉积在催化剂表面上,并且很快地使催化剂失去活性。
因此,必须不断地空气把沉积在催化剂表面上的焦炭烧掉,以恢复它的活性,这个步骤叫做催化剂再生。
再生过程催化剂又可用来继续进行裂化反应。
这种不断地循环反应和再生的过程是催化裂化产生装置的主要部分。
热裂化是不用催化剂而完全靠把原料油加热到一定的高温进行裂化的。
这两种裂化方法的化学原理有根本的区别,生产操作条件和设备也很不相同。
正因为催化裂化用了催化剂,而使它具有许多超过热裂化的显著优点。
2、产品质量好催化裂化所产生汽油辛烷值高,可达80(马达法)以上安定性也比较好、适于作高压缩比汽油发动机(如高级小轿车)的燃料不宜发生炸震现象,耗油少而岀大力。
催化裂化汽油经过适当的精制还能作航空汽油的基础油。
催化理化柴油含芳烃多,十元烷值比直馏柴油低,用作油品发动机燃料,常常需要和直馏柴油等调合使用。
但是它所含的芳烃如果用抽提方式分离出来是石油化学工业的宝贵原料。
用催化裂化柴油深度加氢还可以生产大比重优质喷气机燃料。
3、轻质油和石油化工原料高催化裂化的汽油、柴油产率一般总共可达80%左右,比热裂化高得多,热裂化只有65-70%。
此外,催化裂化还生产大量的液化气,它是丙烷丙烯和丁烯丁烷的混合物,一般产率为10%左右,高的可达20%以上。
其中含有大量丙烯和丁烯,合计约占液化气的70%(),即占原料油的70%左右,其中丙烯产率约为3%,而混合丁烯的产率约为4%,它们是宝贵的石油化工原料,可以生产合成橡胶,合成纤维,合成树脂等合成产品和各种有机溶剂等。
如果一座年处理量为120万吨的催化裂化装置,所产的丙烯都用于生产晴纤维时,则可以产人造毛二万四千吨,丙烯可以生产聚丙烯塑料,环氧树脂、异丙醇、丁醇、辛醇、丙酮等重要的化工产品;正丁烯和正丁烷经脱氢生产的丁二烯是合成各种橡胶的主要原料,正丁烯还用可以生产仲丁醇和甲乙酮等溶剂;液化气中分离岀的异丁烯也是宝贵的化工原料,可以生产聚异丁烯,能作橡胶,也可制成润滑油的添加剂。
异丁烯和各种丁烯一起经烷基化能生产工业异辛烷,是制取航空汽油和高级车用汽油所需的高辛烷值组分。
100吨催化裂化原料可生产3~4吨工业异辛烷,即等于提高汽油生产率3~4%。
催化裂化干气可以作合成氨的原料,它含有一部分乙烯,干气经次氨化法可以制取环氧乙烷,再进一步生产乙二醇、甘醇和乙醇胺等重要的化工产品。
有此可见,催化裂化不仅是生产发动机燃料——轻质石油产品的重要炼油装置,而且可生产大量的石油化工原料。