聚氨酯发泡工艺简介
聚氨酯发泡固化原理
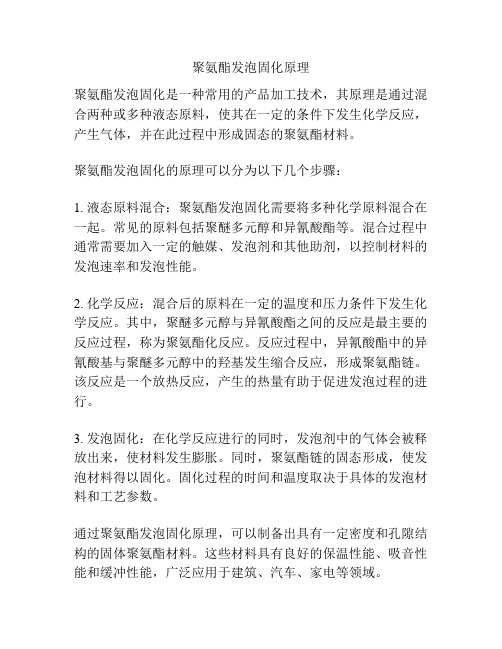
聚氨酯发泡固化原理
聚氨酯发泡固化是一种常用的产品加工技术,其原理是通过混合两种或多种液态原料,使其在一定的条件下发生化学反应,产生气体,并在此过程中形成固态的聚氨酯材料。
聚氨酯发泡固化的原理可以分为以下几个步骤:
1. 液态原料混合:聚氨酯发泡固化需要将多种化学原料混合在一起。
常见的原料包括聚醚多元醇和异氰酸酯等。
混合过程中通常需要加入一定的触媒、发泡剂和其他助剂,以控制材料的发泡速率和发泡性能。
2. 化学反应:混合后的原料在一定的温度和压力条件下发生化学反应。
其中,聚醚多元醇与异氰酸酯之间的反应是最主要的反应过程,称为聚氨酯化反应。
反应过程中,异氰酸酯中的异氰酸基与聚醚多元醇中的羟基发生缩合反应,形成聚氨酯链。
该反应是一个放热反应,产生的热量有助于促进发泡过程的进行。
3. 发泡固化:在化学反应进行的同时,发泡剂中的气体会被释放出来,使材料发生膨胀。
同时,聚氨酯链的固态形成,使发泡材料得以固化。
固化过程的时间和温度取决于具体的发泡材料和工艺参数。
通过聚氨酯发泡固化原理,可以制备出具有一定密度和孔隙结构的固体聚氨酯材料。
这些材料具有良好的保温性能、吸音性能和缓冲性能,广泛应用于建筑、汽车、家电等领域。
聚氨酯泡沫生产工艺

聚氨酯泡沫生产工艺
聚氨酯泡沫是一种常见的绝缘材料和填充材料,具有轻质、隔音、隔热、耐用等特点。
其生产工艺主要包括原料准备、反应混合、发泡、硬化和加工等环节。
首先,原料准备是聚氨酯泡沫生产的第一步。
常见的原料包括多元醇、异氰酸酯、发泡剂、催化剂、表面活性剂等。
这些原料需要按照一定比例进行配比,并且需要保证其质量和纯度。
接下来,原料进行反应混合。
首先将多元醇与异氰酸酯进行混合,形成聚合反应。
催化剂和表面活性剂的添加可以促进反应的进行,并提高聚氨酯泡沫的物理性能。
然后,将反应混合物进行发泡。
在混合过程中加入发泡剂,通过空气的释放形成气泡,使混合物膨胀成泡沫状。
发泡剂的添加量和质量直接影响到泡沫的发泡性能和质量。
发泡完成后,泡沫需要经过硬化。
这个过程需要一定的时间,以便让泡沫中的化学反应充分进行,使泡沫能够形成坚固的结构。
硬化时间一般需要几小时到几天不等,具体时间取决于泡沫的厚度和环境温度。
最后,经过硬化的聚氨酯泡沫可以进行加工和成型。
泡沫可以根据需要进行切割、打磨、抛光等加工,以适应不同的使用需求。
此外,聚氨酯泡沫还可以进行表面处理,如涂覆、印刷等,以提高其外观和使用性能。
综上所述,聚氨酯泡沫生产工艺涉及原料准备、反应混合、发泡、硬化和加工等多个环节。
合理控制每个环节的操作和参数,可以生产出质量优良的聚氨酯泡沫产品。
聚氨酯发泡工艺流程

聚氨酯发泡工艺流程
《聚氨酯发泡工艺流程》
聚氨酯是一种重要的高分子材料,具有优异的性能,被广泛应用于建筑、汽车、家具、鞋材等领域。
而聚氨酯发泡工艺是其重要的加工方式之一,能够使聚氨酯材料具有轻质、保温、隔热、防水等特性。
聚氨酯发泡工艺流程一般包括原料准备、混合、充填、固化等步骤。
首先是原料准备,通常包括聚醚多元醇、异氰酸酯等原料。
然后是混合,将聚醚多元醇和异氰酸酯按一定比例混合,并在一定温度和压力下进行反应,产生气体和形成泡沫。
接下来是充填,将混合好的原料充填进模具中,在模具内部形成固化泡沫。
最后是固化,即让充填好的原料在一定的温度和湿度条件下进行固化,使泡沫成型。
在整个聚氨酯发泡工艺流程中,需要严格控制原料的配比、混合过程的温度和压力、充填时的速度和模具的设计等因素,才能够获得高质量的聚氨酯发泡制品。
同时,还需要考虑产品的后续处理,如切割、包装等环节。
总之,聚氨酯发泡工艺流程是一项复杂的加工过程,需要严格的控制和操作,但是得到的聚氨酯发泡制品具有轻质、保温、隔热、防水等优异性能,能够满足各种应用领域的需求。
PU发泡工艺介绍
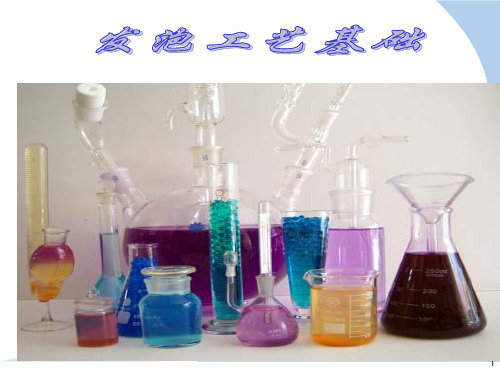
聚氨酯原材料-ISO部分
• TDI&MDI: • 为了降低成本可在TDI内加入MDI。
• TDI&MDI:
•
有TDI+MDI组合而成;加入的 MDI比
例不同,有TM70/30,TM80/20等不同配比,
按具体的配方而定。
15
聚氨酯原材料-聚醚组合料
• 聚醚多元醇 • 我们现在使用的GP-1618、ZS-104
氢氧化铝 防老剂 链增长剂:三乙醇胺(我们使用的) 颜料 脱模剂
11
聚氨酯原材料-ISO部分
TDI:甲苯二异腈酸酯
MDI:多亚甲基多苯基多异腈酸酯
12
聚氨酯原材料-ISO部分
TDI(甲苯二异氰酸酯):主要有2,4-和2, 6-异构体。工业上主要有三种产品, T100,T80/20,T65/35
2、新制的泡沫需在自然状态下熟化72小时方可取样, 取样应放在恒温恒湿内(GB/T2918规定的温度是 23±2℃,相对湿度50±5%)。
32
发泡测试标准
硬度:压陷硬度(ILD)、压缩硬度(CLD) 这两种测试方法的主要区别是泡沫塑料的加载面积,在ILD试验
中样件受压面积是323CM2,而CLD是将整个样件进行压缩。在此,我 们只讨论ILD试验方法。 在ILD试验中,试样大小是38*38*50mm,试验的压头直径200mm(压头 底边有R=10的圆角),支撑板开有6mm的孔,孔间距20mm。压头加压 速度(100±20)mm/min,首先以5N的压力作为下压零点,从零点开 始下压试样厚度的70%,再以同样的速度卸荷,重复加压、卸荷三次, 作为预压,重复预压三次后立即以相同的速度压陷试样,压头压入试 样的厚度分别为25±1%、65±1%,到达变形量之后保持30±1s记录相 对压陷值,记下的值即为该压陷变量下的压陷硬度。
聚氨酯发泡技术

聚氨酯发泡技术
聚氨酯发泡技术是一种由聚氨酯原料,以及各种增塑剂、发泡剂、润湿剂、抗氧化剂、催化剂等复合而成的生产工艺。
它具有自主发泡性能,不需要外界加热即可实现空气及水分子体系中的渗透发泡,可得到有一定强度、密度和结构的发泡体,并可添加一些特殊功能性添加剂,使发泡材料具有抗水性、耐油性、耐酸碱性、抗紫外线老化性等特点,从而在保证发泡体结构稳定性的前提下具有良好的耐久性和耐用性。
聚氨酯发泡技术是一项先进的发泡技术,它的发泡过程采用的是自主发泡的原理,即聚氨酯原料在凝固时,由于其内部的发泡剂、催化剂等物质的作用,会形成小气泡,从而形成具有一定强度、密度和结构的发泡体,从而使发泡材料具有良好的抗水性、耐油性、耐酸碱性、抗紫外线老化性等特点,从而在保证发泡体结构稳定性的前提下具有良好的耐久性和耐用性。
聚氨酯发泡技术具有良好的发泡效果,可以生产出空心、多孔、可塑性好的发泡体,从而为实现结构密闭性、抗紫外线老化性、隔热性等特殊应用和要求提供有效的解决方案。
此外,聚氨酯发泡技术还具有良好的环保性,可以有效避免环境污染,符合相关的环境保护法规,被广泛应用于汽车、建筑、包装、冰箱、冷库等领域。
聚氨酯发泡技术的优点还有:发泡过程简单,可以节省大量的能源;发泡原料和发泡工艺可根据实际需要进行调整,生产出各种规格不同的发泡体;发泡体具有良好的机械性能,弹性大,耐受冲击;发泡过程中产生的CO2也可以有效利用,从而降低环境污染等。
总之,聚氨酯发泡技术具有发泡效果好、环保性强、耐用度高、可塑性良好等优点,广泛应用于汽车、建筑、包装、冰箱、冷库等领域,被认为是一种绿色环保的发泡技术。
聚氨酯发泡胶生产工艺

聚氨酯发泡胶生产工艺
聚氨酯发泡胶是一种常用于填充、密封、粘接和隔绝的材料,具有较高的弹性和耐热性。
其生产工艺主要包括原料配制、发泡剂添加、混合、注射、固化和成品包装等环节。
首先是原料配制。
聚氨酯发泡胶的制作需要将TDI(对苯二甲酸酐)、甘油、水等原料按照一定比例配制。
其中,TDI是主
要的反应物,质量控制特别重要。
其次是发泡剂添加。
在原料配制过程中加入适量的发泡剂,如水或其他气化剂。
发泡剂的添加量决定了胶体内部的孔隙率和发泡程度,对产品性能有很大影响。
然后是混合。
将原料配制好的胶体与发泡剂充分混合,以确保各个组分均匀分散。
混合的方式通常是利用搅拌器进行搅拌,确保组分混合均匀。
接下来是注射。
将混合好的胶体注入模具中。
模具的形状决定了成品的形状,可以根据需要设计。
注射时要确保注入胶体的均匀性和快速性,以免影响产品质量。
然后是固化。
注入胶体后,需要待胶体在模具中固化一段时间,使其变得具有一定的强度和稳定性。
固化时间一般较长,可以根据具体情况进行调整。
最后是成品包装。
胶体固化后,可以将成品从模具中取出,并进行包装。
包装通常采用透明泡沫袋、塑料袋等包装材料,以
防止湿气和灰尘对产品的影响。
通过以上的工艺步骤,聚氨酯发泡胶的生产就完成了。
整个过程需要仔细控制各个环节的质量和时机,以确保最终产品的品质和性能。
同时,还需注意生产过程中的安全性和环境保护,合理利用原料并减少废弃物的产生。
PU发泡工艺介绍
PU发泡工艺介绍PU(Polyurethane)是一种具有众多优良性能的聚氨酯材料,其广泛应用于建筑、汽车、航空航天、家电、电子等领域。
而PU发泡工艺是将PU材料通过特定的工艺进行发泡制造,以实现材料的轻量化和良好的绝缘性能。
下面将对PU发泡工艺进行详细介绍。
PU发泡工艺主要包括原料配制、混合与反应、发泡加工、硬化和成型等环节。
首先,原料配制是指将PU材料的主体成分聚醋酸酯(Polyol)和异氰酸酯(Isocyanate)按照一定比例进行混合。
混合与反应环节中,将配制好的主材与辅助材料(如发泡剂、催化剂、稳定剂等)与机械设备进行充分混合搅拌,以促使材料发生反应,并产生气体,从而形成泡沫结构。
发泡加工阶段,经过一系列工艺操作,如调整温度、压力、密度等参数,对PU材料进行发泡加工,以获得所需的产品形状和尺寸。
硬化阶段是指将发泡完毕的PU材料进行定型和固化,使其具备一定的强度和稳定性。
最后,成型阶段是将硬化的PU材料进行剪裁、冲压、压延等工艺,通过模具来完成最终产品的成型。
首先,PU发泡工艺可以制造轻质的材料,具有较低的密度。
这是由于PU材料中的发泡剂释放出的气体可以形成许多微小的气泡,从而使材料的密度降低。
其次,PU发泡工艺可以实现材料的良好绝缘性能。
PU泡沫是一种封闭细胞,具有良好的隔热、隔音和耐火性能,广泛应用于建筑和电子领域。
再次,PU发泡工艺可以制作各种复杂形状的产品。
PU材料具有优良的可塑性和可加工性,可以通过调整发泡工艺参数和选择合适的模具来生产各种形状、尺寸和硬度的成品。
此外,PU发泡工艺还具有可持续发展的优势。
PU材料可以通过循环利用和再生利用来降低对环境的影响。
同时,PU发泡工艺可以有效减少材料的使用量,从而实现资源节约。
在应用方面,PU发泡工艺广泛应用于建筑、汽车、航空航天、家电、电子等领域。
在建筑领域,PU发泡材料可用于墙体隔热、屋顶保温、地板隔音等。
在汽车行业,PU发泡材料可用于制造汽车座椅、车门内饰等零部件。
pu发泡工艺技术
pu发泡工艺技术PU发泡工艺技术是一种利用聚氨酯材料进行发泡制作的技术。
该技术可以使用于各种行业和领域,如建筑、汽车、家具、电子等。
在PU发泡工艺技术中,聚氨酯材料是通过化学反应组成的,形成一个具有轻质孔隙结构的发泡体。
PU发泡工艺技术主要包括材料准备、混合、注塑、发泡、固化等步骤。
首先,需要准备好聚氨酯材料,通常是由两种液体材料混合而成的。
然后,将这两种液体材料按一定比例混合,使其达到适合发泡的状态。
接下来,将混合的材料注入模具中。
模具可以根据需要制作成任何形状,以满足产品的要求。
在注塑过程中,材料开始发生变化,逐渐充满整个模具,并形成一个密闭的空腔。
在发泡阶段,注塑的材料会发生化学反应,产生气体,使整个空腔膨胀。
这样,PU发泡材料就形成了一个轻质、高强度的聚氨酯泡沫。
最后,通过固化工艺,使聚氨酯泡沫发泡体完全固化。
固化的时间和温度取决于具体的产品要求和材料性质。
完成固化后,就可以将PU发泡制品取出模具,得到成品。
PU发泡工艺技术具有许多优点。
首先,PU发泡材料具有优良的绝缘性能,可以在电子领域中广泛应用。
其次,由于聚氨酯材料的性质可调,可以制作出各种不同硬度、厚度和形状的产品。
另外,PU发泡材料重量轻、强度高,可以减少产品的重量和成本。
PU发泡工艺技术的应用范围很广。
在建筑领域,可以用来制作隔热材料、隔音材料和防水材料等。
在汽车领域,可以用于制作车座、车门和车顶等。
在家具领域,可以用于制作床垫、沙发和椅子等。
此外,PU发泡材料还可以用于制作包装材料、运动器材和医疗器械等。
总之,PU发泡工艺技术是一种十分重要且具有广泛应用的技术。
它通过化学反应和物理变化,将聚氨酯材料转化为轻质、高强度的泡沫制品。
这种技术不仅可以满足各种行业和领域的需求,同时也具有良好的环保性能。
随着科学技术的不断进步,PU发泡工艺技术将在更多领域中发挥作用,为人们的生活带来更多便利和舒适。
PU发泡工艺介绍解析
20
聚氨酯化学:A料跟B料之比
对于座椅泡沫而言(TDI系统及TDI&MDI系统)来说, 其对应关系为:
A料 P1:100
B料(软泡) 30-50
B料(硬泡)
根据实际羟值和水份计算,通常要 远高于软泡
21
聚醚组合料
2、新制的泡沫需在自然状态下熟化72小时方可取 样,取样应放在恒温恒湿内(GB/T2918规定的温 度是23±2℃,相对湿度50±5%)。
31
发泡测试标准
硬度:压陷硬度(ILD)、压缩硬度(CLD) 这两种测试方法的主要区别是泡沫塑料的加载面积,在ILD试验中
样件受压面积是323CM2,而CLD是将整个样件进行压缩。在此,我 们只讨论ILD试验方法。 在ILD试验中,试样大小是38*38*50mm,试验的压头直径200mm (压头底边有R=10的圆角),支撑板开有6mm的孔,孔间距20mm。 压头加压速度(100±20)mm/min,首先以5N的压力作为下压零点, 从零点开始下压试样厚度的70%,再以同样的速度卸荷,重复加压、 卸荷三次,作为预压,重复预压三次后立即以相同的速度压陷试样, 压头压入试样的厚度分别为25±1%、65±1%,到达变形量之后保持 30±1s记录相对压陷值,记下的值即为该压陷变量下的压陷硬度。
3
聚氨酯定义
➢主链上含有--NHCO-- 基团聚合物通称为聚 氨酯甲酸酯简称为聚氨酯。
➢简称PU。
4
聚氨酯分类
➢根据原料不同和配方的变化,分为软质、 半硬质和硬质泡沫。
软质:座椅,头枕,海绵… 半硬质:扶手,方向盘; 硬质:方向盘芯、冷库保温防水。
聚氨酯发泡工艺详解
聚氨酯发泡工艺一、发泡聚氨酯的优点/Article26079.html发泡聚氨酯由双组分组成,甲组分为多元醇,乙组分为异氰酸酯,施工时两组分进入喷涂机械中混合喷出,呈雾状,一分钟发泡凝固成型。
这种材料近几年才引进,用于建筑保温防水经过二、三年的使用,有较多的了解,优点很多,使用范围很广。
1.保温性能好。
导热系数0. 025左右,比聚苯板还好,是目前建筑保温较好的材料。
2.防水性能好。
泡沫孔是封闭的,封闭率达95% ,雨水不会从孔间渗过去。
3.因现场喷涂,形成整体防水层,没有接缝,任何高分子卷材所不及,减少维修工作量。
4.粘结性能好。
能够和木材、金属、砖石、玻璃等材料粘结得非常牢固,不怕大风揭起。
5.用于新作屋面或旧屋面维修都很适宜特别是旧屋面返修,不必铲除原有的防水层和保温层,只需清除表面的灰、砂杂物,即可喷涂。
6.施工简便速度快。
每日每工可喷200多平米,有利于抢进度。
7.收头构造简单。
喷涂发泡聚氨酯收头,不用特别处理,大为简化。
如使用卷材,在女儿墙处,需留凹槽,收头在凹槽内;若不能留凹槽,需用扁铁封钉收头,还要涂嵌缝膏。
8.经济效益好。
如果把保温层和防水层分开,不仅造价高,而且工期长,而发泡聚氨酯一次成活。
9.耐老化好。
据国外已用工程总结和研究测试获知,耐老化年限可达30年之久。
二、发泡聚氨酯的应用1.平屋面防水保温不上人屋面加喷一道彩色涂料,作为保护层;上人屋面,在上坐浆铺面砖。
2.瓦顶坡屋面将发泡聚氨酯喷在望板下沿,瓦块座浆在望板上,不会发生滑动。
3.墙体保温发泡聚氨酯用作墙体保温更具优越性装。
配式大墙板,喷在板肋间,粘结好又严密。
如用空心砌块,可将发泡聚氨酯喷在孔洞内,塞充饱满冻库的墙壁,喷涂尤佳。
目前墙体改革很关键的是保温技术,发泡聚氨酯可以大展宏图。
4.地下室外墙保温防水,是发泡聚氨酯大显身手的部位,既能保温、防水,又省去其他保护层,一举二得。
三、发泡聚氨酯的缺点虽然发泡聚氨酯有如此多的优越性,但也不是万能的,存在短处和不适宜之处。
- 1、下载文档前请自行甄别文档内容的完整性,平台不提供额外的编辑、内容补充、找答案等附加服务。
- 2、"仅部分预览"的文档,不可在线预览部分如存在完整性等问题,可反馈申请退款(可完整预览的文档不适用该条件!)。
- 3、如文档侵犯您的权益,请联系客服反馈,我们会尽快为您处理(人工客服工作时间:9:00-18:30)。
聚氨酯发泡工艺简介聚氨酯硬泡生产工艺硬泡成型工艺聚氨酯硬泡的基本生产方法聚氨酯硬泡一般为室温发泡,成型工艺比较简单。
按施工机械化程度可分为手工发泡和机械发泡。
根据发泡时的压力,可分为高压发泡和低压发泡。
按成型方式可分为浇注发泡和喷涂发泡。
浇注发泡按具体应用领域、制品形状又可分为块状发泡、模塑发泡、保温壳体浇注等。
根据发泡体系可发为HCFC 发泡体系、戊烷发泡体系和水发泡体系等,不同的发泡体系对设备的要求不一样。
按是否连续化生产可分为间歇法和连续法。
间歇法适合于小批量生产。
连续法适合于大规模生产,采用流水线生产方法,效率高。
按操作步骤中是否需预聚可分为一步法和预聚法(或半预聚法)。
1.手工发泡及机械发泡在不具备发泡机、模具数量少和泡沫制品的需要量不大时可采用手工浇注的方法成型。
手工发泡劳动生产率低,原料利用率低,有不少原料粘附在容器壁上。
成品率也较低。
开发新配方,以及生产之前对原料体系进行例行检测和配方调试,一般需先在实验室进行小试,即进行手工发泡试验。
在生产中,这种方法只适用于小规模现场临时施工、生产少量不定型产品或制作一些泡沫塑料样品。
手工发泡大致分几步:(1) 确定配方,计算制品的体积,根据密度计算用料量,根据制品总用料量一般要求过量5%~15%。
(2) 清理模具、涂脱模剂、模具预热。
(3) 称料,搅拌混合,浇注,熟化,脱模。
手工浇注的混合步骤为:将各种原料精确称量后,将多元醇及助剂预混合,多元醇预混物及多异氰酸酯分别置于不同的容器中,然后将这些原料混合均匀,立即注入模具或需要充填泡沫塑料的空间中去,经化学反应并发泡后即得到泡沫塑料。
在我国,一些中小型工厂中手工发泡仍占有重要的地位。
手工浇注也是机械浇注的基础。
但在批量大、模具多的情况下手工浇注是不合适的。
批量生产、规模化施工,一般采用发泡机机械化操作,效率高。
2.一步法及预聚法目前,硬质聚氨酯泡沫塑料都是用一步法生产的,也就是各种原料进行混合后发泡成型。
为了生产的方便,目前不少厂家把聚醚多元醇或(及)其它多元醇、催化剂、泡沫稳定剂、发泡剂等原料预混在一起,称之为“ 白料”,使用时与粗MDI(俗称“ 黑料” )以双组分形式混合发泡,仍属于“ 一步法”,因为在混合发泡之前没有发生化学反应。
早期的聚氨酯硬泡采用预聚法生产。
这是因为当时所用的多异氰酸酯原料为TDI-80。
由于TDI 粘度小,与多元醇的粘度不匹配;TDI 在高温下挥发性大;且与多元醇、水等反应放热量大,若用一步法生产操作困难,故当时多用预聚法。
若把全部TDI 和多元醇反应,制得的端异氰酸酯基预聚体粘度很高,使用不便。
硬泡生产中所指的预聚法实际上是“ 半预聚法”。
即首先TDI与部分多元醇反应,制成的预聚体中NCO 的质量分数一般为20%~25%。
由于TDI大大过量,预聚体的粘度较低。
预聚体再和聚酯或聚醚多元醇、发泡剂、表面活性剂、催化剂等混合,经过发泡反应而制得硬质泡沫塑料。
预聚法优点是:发泡缓和,泡沫中心温度低,适合于模制品;缺点是:步骤复杂、物料流动性差,对薄壁制品及形状复杂的制品不适用。
自从聚合MDI 开发成功后,TDI 已基本上不再用作硬质泡沫塑料的原料,一步法随之取代了预聚法。
浇注成型工艺浇注发泡是聚氨酯硬泡常用的成型方法,即就是将各种原料混合均匀后,注入模具或制件的空腔内发泡成型。
聚氨酯硬泡的浇注成型可采用手工发泡或机械发泡,机械发泡可采用间歇法及连续法发泡方式。
机械浇注发泡的原理和手工发泡的相似,差别在于手工发泡是将各种原料依次称入容器中,搅拌混合;而机械浇注发泡则是由计量泵按配方比例连续将原料输入发泡机的混合室快速混合。
硬泡浇注方式适用于生产块状硬泡、硬泡模塑制品,在制件的空腔内填充泡沫,以及其它的现场浇注泡沫。
块状硬泡及模塑发泡块状硬质泡沫塑料指尺寸较大的硬泡块坯,一般可用间隙式浇注或用连续发泡机生产。
块状硬泡切割后制成一定形状的制品。
模塑硬泡一般指在模具中直接浇注成型的硬泡制品。
块状硬泡的生产方法和连续法块状软泡及箱式发泡软泡相似。
原料中可加入一定量的固体粉状或糊状填料。
块状硬泡在模具顶上常装有一定重量的浮动盖板。
反应物料量按模具体积和所需泡沫塑料密度计算,另加3%~5%比较合适。
这种情况下,泡沫上升受到浮动盖板限制,结构更为均匀,各向异性程度减小。
也可用自由发泡生产块状硬泡,即在没有顶盖的箱体内发泡,泡沫密度由配方决定。
小体积(体积小于0.5 m3,厚度不大于10cm)聚氨酯硬泡生产配方及工艺目前已经成熟,国内普遍采用。
大体积块状硬泡发泡工艺难度较大,国内生产厂家少。
在大体积聚氨酯硬泡生产中,应注意防止泡沫内部产生的热量积聚而引起烧芯。
一般需控制原料中的水分,不用水发泡以减少热量的产生,尽量采用物理发泡剂以吸收反应热,降低发泡原料的料温。
间隙式箱式发泡和模塑发泡,发泡过程大致是这样的:多元醇、发泡剂、催化剂等原料精确计量后置于一容器中预混合均匀,加入异氰酸酯后立即充分混合均匀,具有流动性的反应物料注入模具,经化学反应并发泡成型。
箱式块状发泡工艺的优点是投资少,灵活性大。
一个模具每小时一般可生产两块硬泡。
缺点是原料损耗大,劳动生产率低。
模塑发泡是在有一定强度的密闭模具(如密闭的箱体)内发泡,密度由配方用量和设定的模具体积来决定。
一般用于生产一些小型硬泡制品,如整皮硬泡、结构硬泡等。
模塑发泡的模具要求能承受一定的模内压力。
原料的过填充量根据要求的密度及整皮质量而定。
大体积块状泡沫一般需用发泡机混合与浇注物料。
高、低压发泡机均可。
机械发泡,发泡料的乳白时间远比搅拌式混合的短。
因此,生产大块泡沫塑料,最好选用大输出量发泡机。
连续法生产块状硬泡的过程与块状软泡的相似,所用发泡机,其原理和外观也与生产软泡的机器相似。
如Planibloc平顶发泡装置也适用于生产块状硬泡。
浇注成型中的注意事项浇注发泡成型的催化剂以胺类催化剂为主,可采用延迟性胺类催化剂延长乳白时间,满足对模具的填充要求,这类催化剂可提高原料体系的流动性,但不影响其固化性。
异氰酸酯指数稍大于100,如105。
浇注发泡成型过程中,原料温度与环境温度直接影响泡沫塑料制品的质量。
环境温度以20~30℃为宜,原料温度可控制在20~30℃或稍高一些。
温度过高或过低都不易得到高质量的制品。
对船舶、车辆等大型制品现场浇注成型,难以控制环境温度,则可适当控制原料温度并调节催化剂用量。
对模具的要求是结构合理,拆装方便,重量轻,耐一定压力,并且内表面还要有较好的光洁度。
同时还要根据模具的大小和不同的形状,在合适的位置钻多个排气孔。
制造模具的材质一般是铝合金,有时也用钢模。
模具温度的高低直接影响反应热移走的速度。
模温低,发泡倍率小,制品密度大,表皮厚;模温高则相反。
为制得高质量的泡沫塑料制品,一般将模温控制在40~50℃范围。
料温和模温较低时,化学反应进行缓慢,泡沫固化时间长;温度高,则固化时间短。
在注入模具内发泡时,应在脱模前将模具与制品一起放在较高温度环境下熟化,让化学反应进行完全。
若过早脱模,则熟化不充分,泡沫会变形。
原料品种与制件形状尺寸不同,所需的熟化时间和温度也不同。
一般模塑泡沫在模具中需固化10min 后才能脱模。
由于混合时间短,混合效率是需重视的因素。
手工浇注发泡,搅拌器应有足够的功率和转速。
混合得均匀,泡沫孔细而均匀,质量好;混合不好,泡孔粗而不均匀,甚至在局部范围内出现化学组成不符合配方要求的现象,大大影响制品质量。
聚氨酯硬泡喷涂成型聚氨酯硬泡喷涂发泡成型即是将双组分组合料迅速混合后直接喷射到物件表面而发泡成型。
喷涂是聚氨酯硬泡是一种重要的施工方法,可用于冷库、粮库、住宅及厂房屋顶、墙体、贮罐等领域的保温层施工,应用已逐渐普及。
喷涂发泡成型的优点是:不需要模具;无论是在水平面还是垂直面、顶面,无论是在形状简单的物体表面或者还是复杂的表面,都可通过喷涂方法形成硬质聚氨酯泡沫塑料保温层;劳动生产率高;喷涂发泡所得的硬质聚氨酯泡沫塑料无接缝,绝热效果好,兼具一定的防水功能。
低压及高压喷涂一般按喷涂设备压力分为低压喷涂和高压喷涂,高压喷涂发泡按提供压力的介质种类又分为气压型和液压型高压喷涂工艺。
低压喷涂发泡是靠柱塞泵将聚氨酯泡沫组合料“ 白料” (即组合聚醚)、“ 黑料” (即聚合MDI)这两种原料从原料桶内抽出并输送到喷枪枪嘴,然后靠压缩空气将黑白两种原料从喷枪嘴中吹出的同时使之混合发泡。
低压喷涂发泡的缺点是:原材料损耗大,污染环境;黑白两种原料容易互串而造成枪嘴、管道堵塞,每次停机都要手工清洗枪嘴;另外压缩空气压力不稳定,混合效果时好时坏,影响发泡质量,喷涂表面不光滑。
但低压喷涂发泡设备价格较高压机低。
低压喷涂发泡施工是一般先开空气压缩机,调节空气压力和流量到所需值,然后开动计量泵开始喷涂施工,枪口与被喷涂面距离300~500mm,以流量1~ 2 kg/min、喷枪移动速度0.5~0.8 s/m 为宜。
喷涂结束时先停泵,再停压缩空气,拆喷枪,用溶剂清洗之。
高压喷涂发泡,物料在空间很小的混合室内高速撞击并剧烈旋转剪切,混合非常充分。
高速运动的物料在喷枪口形成细雾状液滴,均匀地喷射到物件表面。
高压型喷涂发泡设备与低压型喷涂发泡设备相比,具有压力波动小、喷涂雾化效果好、属无气喷涂、原料浪费少、污染小、喷枪自清洁等一系列优点。
目前国内高压喷涂设备主要来自美国Glas-Craft公司、Graco 公司、Gusmer 等公司。
进口的高压喷涂机有的带可控加热器,可把黑白料加热(最高达70℃)。
为了方便施工,在主加热器与喷枪之间配备长管。
为防止两个发泡料组分在流经长管道时冷却降温,长管外面包有保温层,内有温度补偿加热器,以保证黑料、白料达到设定的温度。
选择合适的喷涂发泡设备,是控制硬质聚氨酯喷涂泡沫平整度及泡沫质量的关键之一。
高压喷涂发泡效果明显优于低压喷涂发泡。
喷涂发泡工艺对原料的要求①毒性小,喷涂发泡时,原料喷散成很细的液滴,为减少对环境的污染和操作人员的健康,除发泡剂外,其它原料中的低沸点成分应严加控制,臭味大的叔胺催化剂尽量少用。
特别是聚合MDI 中,易挥发低相对分子质量的异氰酸酯含量要控制在很低范围内。
②粘度小,有利于在极短时间内混合均匀。
③催化剂活性要大,因为喷涂发泡工艺要求反应速度较快,泡沫应很快固化,不流淌。
一般选用三亚乙基二胺、二月桂酸二丁基锡等催化剂。
具有催化作用的叔胺类多元醇,如由乙二胺与环氧丙烷反应制得的俗称“ 胺醚” 的多元醇,常常用于喷涂发泡。
组合料的固化速度应调节在适当的范围,如乳白时间3~5s,不粘时间10~20 s。
这样,能保证反应液混合后立即在喷射面固化,形成泡沫塑料。
这一点,对由下往上的顶部喷涂特别重要。
关于喷涂发泡的环境条件,有几点应注意。