什么是自润滑导柱导套成套性
轴承自润滑工作原理
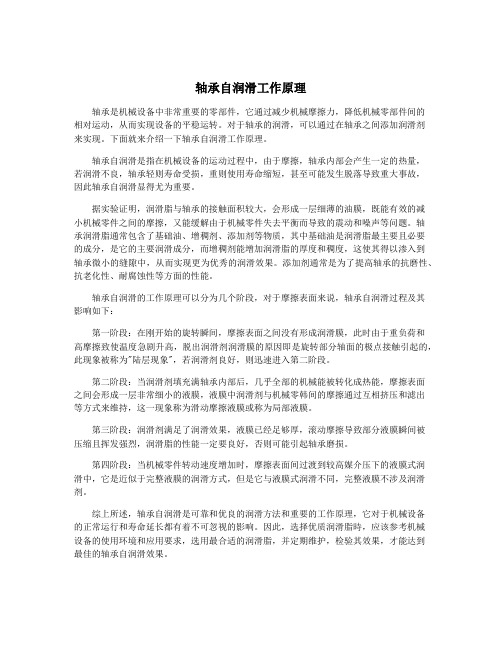
轴承自润滑工作原理轴承是机械设备中非常重要的零部件,它通过减少机械摩擦力,降低机械零部件间的相对运动,从而实现设备的平稳运转。
对于轴承的润滑,可以通过在轴承之间添加润滑剂来实现。
下面就来介绍一下轴承自润滑工作原理。
轴承自润滑是指在机械设备的运动过程中,由于摩擦,轴承内部会产生一定的热量,若润滑不良,轴承轻则寿命受损,重则使用寿命缩短,甚至可能发生脱落导致重大事故,因此轴承自润滑显得尤为重要。
据实验证明,润滑脂与轴承的接触面积较大,会形成一层细薄的油膜,既能有效的减小机械零件之间的摩擦,又能缓解由于机械零件失去平衡而导致的震动和噪声等问题。
轴承润滑脂通常包含了基础油、增稠剂、添加剂等物质,其中基础油是润滑脂最主要且必要的成分,是它的主要润滑成分,而增稠剂能增加润滑脂的厚度和稠度,这使其得以渗入到轴承微小的缝隙中,从而实现更为优秀的润滑效果。
添加剂通常是为了提高轴承的抗磨性、抗老化性、耐腐蚀性等方面的性能。
轴承自润滑的工作原理可以分为几个阶段,对于摩擦表面来说,轴承自润滑过程及其影响如下:第一阶段:在刚开始的旋转瞬间,摩擦表面之间没有形成润滑膜,此时由于重负荷和高摩擦致使温度急剧升高,脱出润滑剂润滑膜的原因即是旋转部分轴面的极点接触引起的,此现象被称为"陆层现象",若润滑剂良好,则迅速进入第二阶段。
第二阶段:当润滑剂填充满轴承内部后,几乎全部的机械能被转化成热能,摩擦表面之间会形成一层非常细小的液膜,液膜中润滑剂与机械零韩间的摩擦通过互相挤压和滤出等方式来维持,这一现象称为滑动摩擦液膜或称为局部液膜。
第三阶段:润滑剂满足了润滑效果,液膜已经足够厚,滚动摩擦导致部分液膜瞬间被压缩且挥发强烈,润滑脂的性能一定要良好,否则可能引起轴承磨损。
第四阶段:当机械零件转动速度增加时,摩擦表面间过渡到较高媒介压下的液膜式润滑中,它是近似于完整液膜的润滑方式,但是它与液膜式润滑不同,完整液膜不涉及润滑剂。
模具的导柱和导套的特点和功用
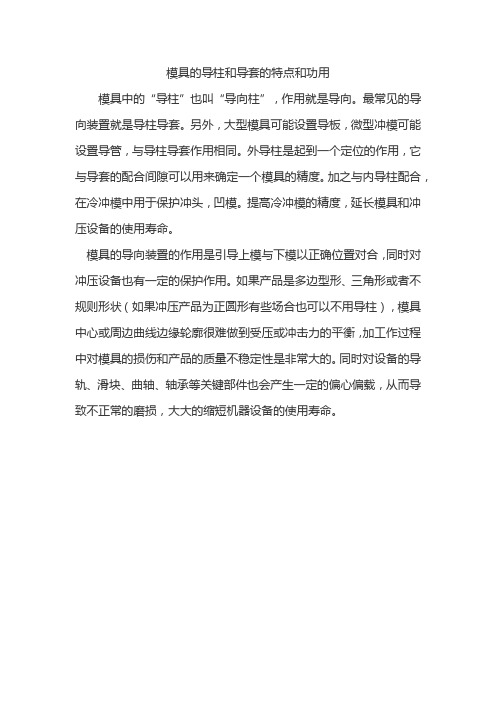
模具的导柱和导套的特点和功用
模具中的“导柱”也叫“导向柱”,作用就是导向。
最常见的导向装置就是导柱导套。
另外,大型模具可能设置导板,微型冲模可能设置导管,与导柱导套作用相同。
外导柱是起到一个定位的作用,它与导套的配合间隙可以用来确定一个模具的精度。
加之与内导柱配合,在冷冲模中用于保护冲头,凹模。
提高冷冲模的精度,延长模具和冲压设备的使用寿命。
模具的导向装置的作用是引导上模与下模以正确位置对合,同时对冲压设备也有一定的保护作用。
如果产品是多边型形、三角形或者不规则形状(如果冲压产品为正圆形有些场合也可以不用导柱),模具中心或周边曲线边缘轮廓很难做到受压或冲击力的平衡,加工作过程中对模具的损伤和产品的质量不稳定性是非常大的。
同时对设备的导轨、滑块、曲轴、轴承等关键部件也会产生一定的偏心偏载,从而导致不正常的磨损,大大的缩短机器设备的使用寿命。
IKO自润直线导轨E系列
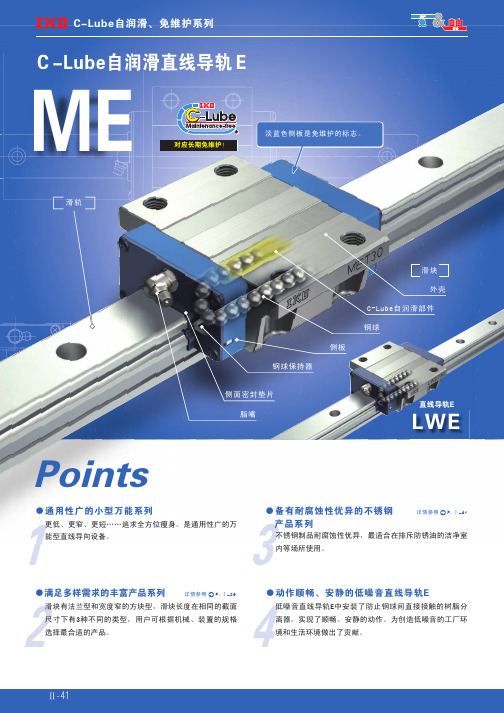
9 49
最大长度(3)
1 200 (1 600)
1 200 (1 960)
1 200 (1 960)
1 200 (1 960)
注(1) 指定连接规格的滑轨(辅助标记“/T”)时,请注意连接部位的E尺寸。 (2) 不适用于带有防尘罩安装用内螺纹(辅助标记“/J”)的规格。 (3) 可制作到括号内的最大长度,需要时请向͋ 咨询。 备注1. 只列出了代表性的公称型号,可适用于同一大小尺寸的所有型号。 2. 不管是哪个系列以及所搭配的滑块是什么形式,滑轨单件的形式标记均请注明“LWE”。 3. 两端的E尺寸如果没有注明,则为在E的基准尺寸范围内的相同尺寸。需要变更时,请注明特别配置的指定滑轨安装孔位置“/E”。详细内容请参照Ⅲ-29页。
:C
:无标记
:G
所适用的滑块的形式和大小尺寸请参照表1。
15、20、25、30、35、45
所适用的滑块的形式和大小尺寸请参照表1。
:C○
成套产品时表示1根滑轨所搭配的滑块个数。滑块单件时,仅指 定“C1”。
:R○
滑轨的长度以毫米为单位表示。
标准长度和最大长度请参照表2.1、表2.2。
碳素钢制 不锈钢制
公称型号
ME 15
LWE 15 LWE 15…Q
160( 3) 220( 4) 280( 5) 340( 6) 460( 8) 640(11) 820(14)
以上 不到
60 20
6 36
1 600 (2 980)
ME 20 LWE 20 LWE 20…Q
220( 4) 280( 5) 340( 6) 460( 8) 640(11) 820(14) 1 000(17) 1 240(21)
自润滑滑动轴承
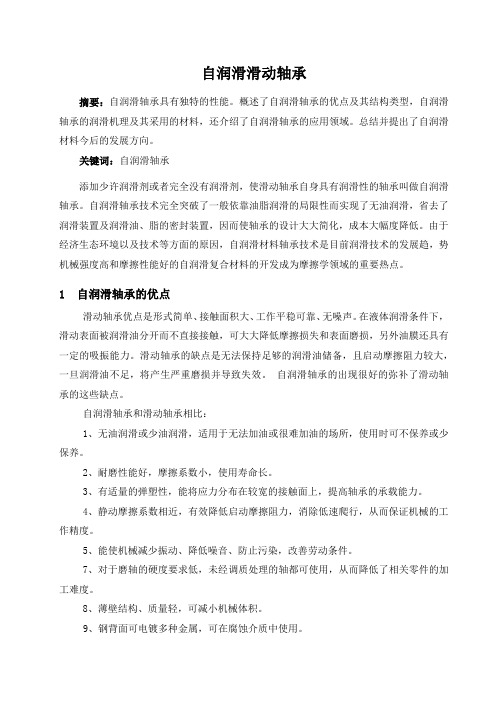
自润滑滑动轴承摘要:自润滑轴承具有独特的性能。
概述了自润滑轴承的优点及其结构类型,自润滑轴承的润滑机理及其采用的材料,还介绍了自润滑轴承的应用领域。
总结并提出了自润滑材料今后的发展方向。
关键词:自润滑轴承添加少许润滑剂或者完全没有润滑剂,使滑动轴承自身具有润滑性的轴承叫做自润滑轴承。
自润滑轴承技术完全突破了一般依靠油脂润滑的局限性而实现了无油润滑,省去了润滑装置及润滑油、脂的密封装置,因而使轴承的设计大大简化,成本大幅度降低。
由于经济生态环境以及技术等方面的原因,自润滑材料轴承技术是目前润滑技术的发展趋,势机械强度高和摩擦性能好的自润滑复合材料的开发成为摩擦学领域的重要热点。
1 自润滑轴承的优点滑动轴承优点是形式简单、接触面积大、工作平稳可靠、无噪声。
在液体润滑条件下,滑动表面被润滑油分开而不直接接触,可大大降低摩擦损失和表面磨损,另外油膜还具有一定的吸振能力。
滑动轴承的缺点是无法保持足够的润滑油储备,且启动摩擦阻力较大,一旦润滑油不足,将产生严重磨损并导致失效。
自润滑轴承的出现很好的弥补了滑动轴承的这些缺点。
自润滑轴承和滑动轴承相比:1、无油润滑或少油润滑,适用于无法加油或很难加油的场所,使用时可不保养或少保养。
2、耐磨性能好,摩擦系数小,使用寿命长。
3、有适量的弹塑性,能将应力分布在较宽的接触面上,提高轴承的承载能力。
4、静动摩擦系数相近,有效降低启动摩擦阻力,消除低速爬行,从而保证机械的工作精度。
5、能使机械减少振动、降低噪音、防止污染,改善劳动条件。
7、对于磨轴的硬度要求低,未经调质处理的轴都可使用,从而降低了相关零件的加工难度。
8、薄壁结构、质量轻,可减小机械体积。
9、钢背面可电镀多种金属,可在腐蚀介质中使用。
2 自润滑轴承的分类及其润滑材料自润滑轴承从结构型式上大致可以分为复合型、干膜型和镶嵌型三种形式。
复合型是将固体润滑剂粉末用树脂、沥青等作粘结剂经固化而成的轴承。
干膜型自润滑轴承就是在轴承的滑动摩擦面上,用粘涂敷结、烧结、电镀、溅射、化学生成等方法形成一层固体润滑膜的轴承,其关键是这层干膜润滑层的减摩性能和使用寿命。
冲压模具导柱导套标准

冲压模具导柱导套标准一、导套的定义和作用导套是冲压模具中的一个重要组成部分,主要用于引导导柱的运动和定位。
它通过在导柱和模板之间形成一定的间隙,保持导柱的运动平稳并减少摩擦阻力,提高模具的工作精度和寿命。
二、导套的分类根据不同的标准和用途,导套可以分为以下几类: 1. 普通导套:用于一般的冲压模具,材质通常为低碳钢或合金钢。
2. 高硬度导套:用于冲压材料较硬的模具,材质通常为高速钢或硬质合金。
3. 自润滑导套:表面涂覆一层含有固体润滑剂的涂层,可降低摩擦系数和磨损,提高模具使用寿命。
4. 紧密耦合导套:导套与导柱之间采用螺纹结构,可实现导套与导柱的紧密耦合,提高导向精度和稳定性。
三、导套的主要标准1.外径尺寸:导套的外径尺寸应符合模具的设计要求,保证导套与孔配合良好,不产生过度间隙或过紧现象。
2.内径尺寸:导套的内径尺寸应与导柱配合,确保导柱的运动自由且不产生明显的摩擦。
3.长度尺寸:导套的长度应根据模具的结构确定,通常为导柱长度加上适当的冗余长度,以方便维修和更换导套。
4.材料硬度:导套的材料硬度应根据冲压材料的硬度和模具工作条件进行选择,以确保导套的耐磨性和寿命。
5.表面光洁度:导套的表面光洁度应满足模具的要求,以便保证导柱的润滑和运动平稳。
四、导套的选用与安装注意事项1.根据模具的要求选择合适的导套类型和材料,确保导套与模具的配合精度和可靠性。
2.安装导套时,要保证导套的安装面与模板的安装面平行,避免产生倾斜或偏移,影响导柱的运动。
3.在安装过程中,要注意导套的定位孔与模板的定位柱的配合,确保导套的位置准确,避免产生倾斜或偏移。
4.导套安装后,要进行必要的润滑和清洁工作,以保证导柱的顺畅运动和导套的使用寿命。
5.定期检查导套的磨损情况,如有必要及时更换,以避免因导套磨损而导致模具的工作精度下降和工作效率降低。
五、导套维护与保养1.建立导套的使用档案,记录导套的使用寿命、更换情况和维修记录,及时制定维护计划和更换周期。
自润滑轴套的生产工艺流程
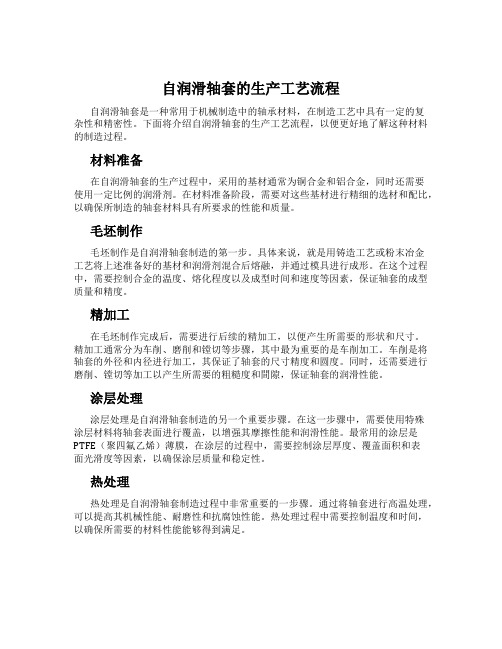
自润滑轴套的生产工艺流程自润滑轴套是一种常用于机械制造中的轴承材料,在制造工艺中具有一定的复杂性和精密性。
下面将介绍自润滑轴套的生产工艺流程,以便更好地了解这种材料的制造过程。
材料准备在自润滑轴套的生产过程中,采用的基材通常为铜合金和铝合金,同时还需要使用一定比例的润滑剂。
在材料准备阶段,需要对这些基材进行精细的选材和配比,以确保所制造的轴套材料具有所要求的性能和质量。
毛坯制作毛坯制作是自润滑轴套制造的第一步。
具体来说,就是用铸造工艺或粉末冶金工艺将上述准备好的基材和润滑剂混合后熔融,并通过模具进行成形。
在这个过程中,需要控制合金的温度、熔化程度以及成型时间和速度等因素,保证轴套的成型质量和精度。
精加工在毛坯制作完成后,需要进行后续的精加工,以便产生所需要的形状和尺寸。
精加工通常分为车削、磨削和镗切等步骤,其中最为重要的是车削加工。
车削是将轴套的外径和内径进行加工,其保证了轴套的尺寸精度和圆度。
同时,还需要进行磨削、镗切等加工以产生所需要的粗糙度和間隙,保证轴套的润滑性能。
涂层处理涂层处理是自润滑轴套制造的另一个重要步骤。
在这一步骤中,需要使用特殊涂层材料将轴套表面进行覆盖,以增强其摩擦性能和润滑性能。
最常用的涂层是PTFE(聚四氟乙烯)薄膜,在涂层的过程中,需要控制涂层厚度、覆盖面积和表面光滑度等因素,以确保涂层质量和稳定性。
热处理热处理是自润滑轴套制造过程中非常重要的一步骤。
通过将轴套进行高温处理,可以提高其机械性能、耐磨性和抗腐蚀性能。
热处理过程中需要控制温度和时间,以确保所需要的材料性能能够得到满足。
包装与交付自润滑轴套制造的最后一步是包装与交付。
在这个阶段,需要对所制作好的轴套进行打磨、清洗和包装,以便保证其不受污染和损坏。
最终将轴套交付给客户,供其在机械制造过程中使用。
总之,在自润滑轴套的生产过程中,需要经历多个复杂的制造步骤才能够得到高质量、高性能的轴套材料。
只有经过科学的工艺流程和精细的操作,才能够保证轴套材料的稳定性和可靠性。
冲压模具名词术语大集合

冲压模具名词术语大集合(转)本文由东莞市铭青五金模具有限公司分享上模:上模是整副冲模的上半部,即安装于压力机滑块上的冲模部分。
上模座:上模座是上模最上面的板状零件,工件时紧贴压力机滑块,并通过模柄或直接与压力机滑块固定。
下模:下模是整副冲模的下半部,即安装于压力机工作台面上模具部件术语上模:上模是整副冲模的上半部,即安装于压力机滑块上的冲模部分。
上模座:上模座是上模最上面的板状零件,工件时紧贴压力机滑块,并通过模柄或直接与压力机滑块固定。
下模:下模是整副冲模的下半部,即安装于压力机工作台面上的冲模部分。
下模座:下模座是下模底面的板状零件,工作时直接固定在压力机工作台面或垫板上。
刃壁:刃壁是冲裁凹模孔刃口的侧壁。
刃口斜度:刃口斜度是冲裁凹模孔刃壁的每侧斜度。
气垫:气垫是以压缩空气为原动力的弹顶器。
反侧压块:反侧压块是从工作面的另一侧支持单向受力凸模的零件。
导套:导套是为上、下模座相对运动提供精密导向的管状零件,多数固定在上模座内,与固定在下模座的导柱配合使用。
导板:导板是带有与凸模精密滑配内孔的板状零件,用于保证凸模与凹模的相互对准,并起卸料(件)作用。
导柱:导柱是为上、下模座相对运动提供精密导向的圆柱形零件,多数固定在下模座,与固定在上模座的导套配合使用。
导正销:导正销是伸入材料孔中导正其在凹模内位置的销形零件。
导板模:导板模:板模是以导板作导向的冲模,模具使用时凸模不脱离导板。
导料板:导料板是引导条(带、卷)料进入凹模的板状导向零件。
导柱模架:导柱模架是导柱、导套相互滑动的模架。
冲模:冲模是装在压力机上用于生产冲件的工艺装备,由相互配合的上、下两部分组成。
凸模:凸模是冲模中起直接形成冲件作用的凸形工作零件,即以外形为工作表面的零件。
凹模:凹模是冲模中起直接形成冲件作用的凹形工作零件,即以内形为工作表面的零件。
防护板:防护板是防止手指或异物进入冲模危险区域的板状零件。
压料板(圈):压料板(圈)是冲模中用于压住冲压材料或工序件以控制材料流动的零件,在拉深模中,压料板多数称为压料圈。
自润滑轴套
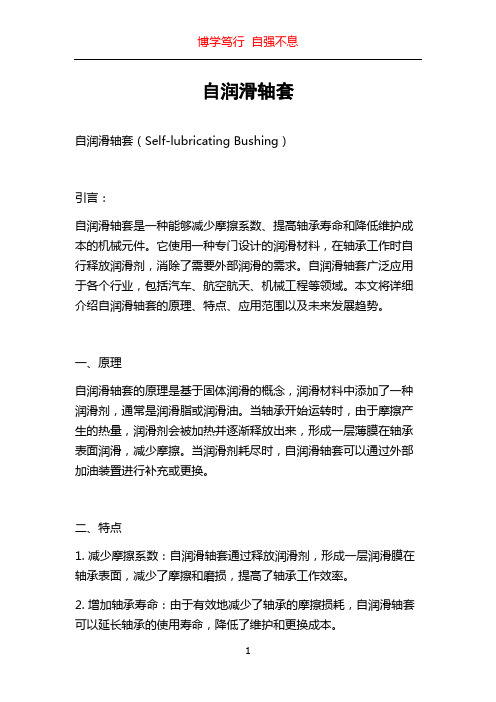
自润滑轴套自润滑轴套(Self-lubricating Bushing)引言:自润滑轴套是一种能够减少摩擦系数、提高轴承寿命和降低维护成本的机械元件。
它使用一种专门设计的润滑材料,在轴承工作时自行释放润滑剂,消除了需要外部润滑的需求。
自润滑轴套广泛应用于各个行业,包括汽车、航空航天、机械工程等领域。
本文将详细介绍自润滑轴套的原理、特点、应用范围以及未来发展趋势。
一、原理自润滑轴套的原理是基于固体润滑的概念,润滑材料中添加了一种润滑剂,通常是润滑脂或润滑油。
当轴承开始运转时,由于摩擦产生的热量,润滑剂会被加热并逐渐释放出来,形成一层薄膜在轴承表面润滑,减少摩擦。
当润滑剂耗尽时,自润滑轴套可以通过外部加油装置进行补充或更换。
二、特点1. 减少摩擦系数:自润滑轴套通过释放润滑剂,形成一层润滑膜在轴承表面,减少了摩擦和磨损,提高了轴承工作效率。
2. 增加轴承寿命:由于有效地减少了轴承的摩擦损耗,自润滑轴套可以延长轴承的使用寿命,降低了维护和更换成本。
3. 自动润滑:自润滑轴套不需要外部润滑,在轴承运行时能够自行释放润滑剂,减少了维护工作和停机时间。
4. 耐高温性能:自润滑轴套的材料通常具有较高的耐温性能,可以在高温环境下工作稳定,适用于特殊工况下的应用。
5. 良好的抗腐蚀性能:通过添加特殊的材料,自润滑轴套能够抵抗腐蚀和化学品的侵蚀,适用于恶劣环境的使用。
三、应用范围1. 汽车行业:自润滑轴套在汽车发动机、变速器、传动系统等关键部位的轴承中广泛应用。
由于汽车工况复杂、工作温度高,自润滑轴套的优势得到了更大程度的发挥,提高了汽车的性能和可靠性。
2. 航空航天行业:自润滑轴套被广泛应用于飞机发动机、液压系统、飞行控制系统等关键部件的轴承中。
在高空、超音速等极端工况下,自润滑轴套能够稳定运行,确保了航空器的安全性。
3. 机械工程行业:自润滑轴套在机械设备的轴承中起到了重要的作用。
例如,自润滑轴套可以用于提升机械、输送设备、旋转机械等需要频繁运动的部位,减少了维护工作和材料费用。
- 1、下载文档前请自行甄别文档内容的完整性,平台不提供额外的编辑、内容补充、找答案等附加服务。
- 2、"仅部分预览"的文档,不可在线预览部分如存在完整性等问题,可反馈申请退款(可完整预览的文档不适用该条件!)。
- 3、如文档侵犯您的权益,请联系客服反馈,我们会尽快为您处理(人工客服工作时间:9:00-18:30)。
什么是自润滑导柱导套成套性??
自润滑导柱导套成套性是什么意思呢?自润滑导柱导套的成套性包括两个方面:一是冲模零件的成套性;二是冲压工序的成套性。
冲模零件的成套性,就是毛坯成套地供应,初加工和二次加工成套地投人和交出,一套冲模由一个钳工小组负责精加工至装配完成。
冲压工序的成套性,是指一个冲压制件各工序所需要的几套冲模,“成套”地由一个调整小组负责调整。
不了解冲模的单件生产特性及其装配的复杂性,往往会片面地强调零件的作业计划性而将冲模零件编制成一定的工序路线,以为这样冲模零件会按照作业计划的路线如同流水生产一样一个个地装配起来成为一套完整的冲模。
但是由于冲模零件大都不是互换的,在装配中有很大的机动性和灵活性,而它的生产方式又是个体的,如果按照这种方式组织生产,其结果便会造成工序间无人负责、零件装配不拢、零件丢失等混乱现象。
在组织大规模生产、冲模数量众多时,情况就更为严重。
因此,冲模生产中每个过程都应由专人负责掌握其成套性。
一个自润滑导柱导套的成品,往往不只是由一套冲模就能完成的,有的需两套、三套甚至更多的冲模来完成。
在调整过程或制造过程中,前后工序的冲模有不可分割的联系,因此在调整中必须保持工序的成套性,数道工序的冲模应由一个调整组负责顺序地进行完整的调整。