电泳涂料技术
电 泳 涂 装

电泳涂装一、概述电泳涂装技术研究起于一百多年前,基于人们对金属表面防腐防锈要求的不断提高而相关表面处理工艺技术又不能较好地解决这种需求的压力下,而被逐渐研制开发。
直到60 年代才由 George Brewer 博士及福特汽车公司研制开发成功阳极电泳漆。
电泳涂装(electro-coating)是利用外加电场使悬浮于电泳液中的颜料和树脂等微粒定向迁移并沉积于电极之一的基底表面的涂装方法。
电泳涂装的原理发明于是20世纪30年代末,但开发这一技术并获得工业应用是在1963年以后,电泳涂装是近30年来发展起来的一种特殊涂膜形成方法,是对水性涂料最具有实际意义的施工工艺。
具有水溶性、无毒、易于自动化控制等特点,迅速在汽车、建材、五金、家电等行业得到广泛的应用。
电泳涂装是把工件和对应的电极放入水溶性涂料中,接上电源后,依靠电场所产生的物理化学作用,使涂料中的树脂、颜填料在以被涂物为电极的表面上均匀析出沉积形成不溶于水的漆膜的一种涂装方法。
电泳涂装是一个极为复杂的电化学反应过程,其中至少包括电泳、电沉积、电渗、电解四个过程。
电泳涂装按沉积性能可分为阳极电泳(工件是阳极,涂料是阴离子型,简称 AED)和阴极电泳(工件是阴极,涂料是阳离子型,简称 CED);按电源可分为直流电泳和交流电泳;按工艺方法又有定电压和定电流法。
二、电泳涂装的优势1 、涂膜厚度均匀,附着力强,涂装质量好,工件各个部位如内层、凹陷、焊缝等处都能获得均匀、平滑的漆膜,解决了其他涂装方法对复杂形状工件的涂装难题;在很凹的部位,即可形成完成均匀之保护膜,并可利用调整不同之操作电压,即可控制镀层的厚度,达到极高的防腐性,并消除了电镀过程中的厚薄不均电极效应,同时也消除了喷漆过程中的桔皮、流挂之故障。
2 、涂料利用率高达 95% ,与喷漆法相比,减少了材料的浪费。
3 、采用水溶性涂料,以水为溶解介质,节省了大量有机溶剂,大大降低了大气污染和环境危害。
电泳涂装工艺特点及与油漆喷涂比较

电泳涂装工艺特点及与油漆喷涂比较电泳又名电着,泳漆,电沉积。
创始于二十世纪六十年月,由福特汽车公司最先应用于汽车底漆。
由于其精彩的防腐、防锈功能,很快在军工行业得到广泛应用。
近几年由汽车行业引申到自行车、摩托车及家电、轻工饰品德业。
如:空调、彩电、洗衣机、摩托车、眼镜、锁具、灯具及饰品、发夹、领带夹等各个金属行业及铝材外表防锈行业。
由于其优良的质素和高度环保,正在逐步替代传统油漆喷涂。
工艺原理:电泳漆以离子状态分散于水中,在直流电场作用下,定向集结五金工件外表上,形成致密外表膜。
电泳特点:1.附着力强,漆膜不易脱落,连续弯折不爆皮。
2.均匀致密,工件内处任何部位漆膜厚薄皆均匀全都。
即使在很凹的部位,即可形成均匀的保护膜。
并可利用调整不同的操作电压,即可掌握镀层的厚度。
到达极高的防腐性。
消退了喷漆中会消灭的结皮,泪痕等不良故障。
3.耐蚀性佳,其他任何涂装方式的耐腐蚀性均不行与之相比较。
4.合符环保,水性涂料,无毒、无污染、无有害物质残留。
比较工程油漆喷涂电泳涂装附着力不强,易脱落强,很难脱落防府性不耐腐蚀耐腐蚀装饰性外表粗糙,平滑度低平展光滑环保性污染严峻合符环保要求电泳与喷涂的比较与区分比较工程油漆喷涂电泳涂装附着力不强,易脱落强,很难脱落防府性不耐腐蚀耐腐蚀装饰性外表粗糙,平滑度低平展光滑环保性污染严峻合符环保要求主题:电泳〔电著〕涂装进展及应用A、概述电泳涂装技术争论起于一百多年前,基于人们对金属外表防腐防锈要求的不断提高而相关表面处理工艺技术又不能较好地解决这种需求的压力下,而被渐渐研制开发。
直到60 年月才由George Brewer 博士及福特汽车公司研制开发成功阳极电泳漆。
其最早应用于福特汽车公司的涂装线,随着阳极电泳漆生产使用,日渐暴露其漆膜中包含有金属离子造成抗蚀性差的缺陷,因而,高抗蚀性的阴极电泳漆于七十年月被开发成功,并被人们等认可并大力推广应用。
之后,电泳技术进展日月异,产品品种由环氧型树脂型进展到丙烯酸型及聚氨脂型。
电泳涂装的方法与技巧

电泳涂装的方法与技巧(1)一般金属表面的电泳涂装,其工艺流程为:预清理→上线→除油→水洗→除锈→水洗→中和→水洗→磷化→水洗→钝化→电泳涂装→槽上清洗→超滤水洗→烘干→下线。
(2)被涂物的底材及前处理对电泳涂膜有极大影响。
铸件一般采用喷砂或喷丸进行除锈,前棉纱清除工件表面的灰尘,用80#~120#砂纸清除表面残留的钢丸等杂物。
钢铁表面采用除油和除锈处理,对表面要求高时,进行磷化和钝化表面处理。
黑色金属工件在阳极电泳前必须进行磷化处理,否则漆膜的耐腐蚀性能较差。
磷化处理时,一般选用锌盐磷化膜,厚度约1~2um,要求磷化膜结晶细而均匀。
(3)在过滤系统中,一般采用一级过滤,过滤器为网袋式结构,孔径为25~75um。
电泳涂料通过立式泵输送到过滤器进行过滤。
从综合更换周期和漆膜质量等因素考虑,孔径50um的过滤袋最佳,它不但能满足漆膜的质量要求,而且解决了过滤袋的堵塞问题。
(4)电泳涂装的循环系统循环量的大小,直接影响着槽液的稳定性和漆膜的质量。
加大循环量,槽液的沉淀和气泡减少;但槽液老化加快,能源消耗增加,槽液的稳定性变差。
将槽液的循环次数控制在6~8次/h较为理想,不但保证漆膜质量,而且确保槽液的稳定运行。
(5)随着生产时间的延长,阳极隔膜的阻抗会增加,有效的工作电压下降。
因此,生产中应根据电压的损失情况,逐步调高电源的工作电压,以补偿阳极隔膜的电压降。
(6)超滤系统控制工件带人的杂质离子的浓度,保证涂装质量。
在此系统的运行中应注意,系统一经运行后应连续运行,严禁间断运行,以防超滤膜干粘。
干桔后的树脂和颜料附着在超滤膜上,无法彻底清洗,将严重影响超滤膜的透水率和使用寿命。
超滤膜的出水率随运行时间而呈下降趋势,连续工作30~40天应清洗一次,以保证超滤浸洗和冲洗所需的超滤水。
(7)电泳涂装法适用于大量流水线的生产工艺。
电泳槽液的更新周期应在3个月以内。
以一年产30万份钢圈的电泳生产线为例,对槽液的科学管理极为重要,对槽液的各种参数定期进行检测,并根据检测结果对槽液进行调整和更新。
中国电泳标准
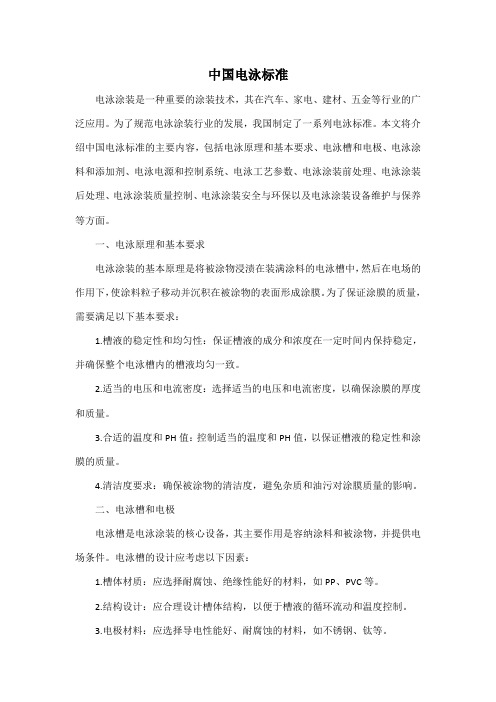
中国电泳标准电泳涂装是一种重要的涂装技术,其在汽车、家电、建材、五金等行业的广泛应用。
为了规范电泳涂装行业的发展,我国制定了一系列电泳标准。
本文将介绍中国电泳标准的主要内容,包括电泳原理和基本要求、电泳槽和电极、电泳涂料和添加剂、电泳电源和控制系统、电泳工艺参数、电泳涂装前处理、电泳涂装后处理、电泳涂装质量控制、电泳涂装安全与环保以及电泳涂装设备维护与保养等方面。
一、电泳原理和基本要求电泳涂装的基本原理是将被涂物浸渍在装满涂料的电泳槽中,然后在电场的作用下,使涂料粒子移动并沉积在被涂物的表面形成涂膜。
为了保证涂膜的质量,需要满足以下基本要求:1.槽液的稳定性和均匀性:保证槽液的成分和浓度在一定时间内保持稳定,并确保整个电泳槽内的槽液均匀一致。
2.适当的电压和电流密度:选择适当的电压和电流密度,以确保涂膜的厚度和质量。
3.合适的温度和PH值:控制适当的温度和PH值,以保证槽液的稳定性和涂膜的质量。
4.清洁度要求:确保被涂物的清洁度,避免杂质和油污对涂膜质量的影响。
二、电泳槽和电极电泳槽是电泳涂装的核心设备,其主要作用是容纳涂料和被涂物,并提供电场条件。
电泳槽的设计应考虑以下因素:1.槽体材质:应选择耐腐蚀、绝缘性能好的材料,如PP、PVC等。
2.结构设计:应合理设计槽体结构,以便于槽液的循环流动和温度控制。
3.电极材料:应选择导电性能好、耐腐蚀的材料,如不锈钢、钛等。
4.电极安装位置:应合理设计电极的安装位置,以确保电场的均匀分布。
三、电泳涂料和添加剂电泳涂料是电泳涂装的关键材料,其质量直接影响涂膜的质量。
选择合适的电泳涂料需要考虑以下因素:1.涂料成分:应选择合适的树脂、颜料、填料等成分,以保证涂膜的性能要求。
2.涂料稳定性:应确保涂料在槽液中的稳定性,避免沉淀、结块等现象。
3.涂料环保性:应选择低VOC、低甲醛等环保型涂料,以符合国家环保法规的要求。
4.添加剂的选择和使用:为了调节槽液的各项性能指标,需要选择合适的添加剂,如稳定剂、PH调节剂等。
电泳涂装工艺过程

电泳涂装工艺过程电泳涂装基本原理所谓电泳涂装,是将被涂物浸渍在水溶性涂料中作为阳极(阳极电泳),另设一与其相对应的阴极,在两极间通直流电,靠电流所产生的物理化学作用,使涂料均匀涂在被涂物上的一种涂装技术。
电泳涂装必须使用电泳漆,电泳漆通常又称水溶性涂料,电泳漆与蒸馏水必须按一定比例进行稀释,才能使用。
电泳涂装一般包括四个同时进行的过程:1、电泳:在直流电场的作用下,正,负带电胶体粒子向负,正方向运动,也称泳动。
2、电解:电极上分别进行着氧化还原反应,反而在电极上形成氧化与还原现象。
3、电沉积:由于电泳作用,移至阳极附近的带电胶体粒子在模板表体放出电子,而呈不溶状态沉积,析出的现象,此时漆膜形成。
4、电渗:在电场作用下,固相不动,而液相移动的现象。
电渗作用使漆膜内所含水份逐渐被排到涂膜外,最后形成几乎连电流也通不过去,含水率极低,电阻相当高的致密漆膜。
5、灰色环氧电泳漆为例:该电泳漆系改性环氧树脂,丁醇,乙醇胺,滑石粉,钛白粉、炭黑、高岭土的物质组成,电泳漆与蒸馏水混合后,在直流电场的作用下,即分离成带正电荷的阳离子和带负电荷的阴离子,并进行一系列复杂的物理化学胶体化学,电化学变化过程。
电泳涂装的方法及技巧(1)一般金属表面的电泳涂装,其工艺流程为:预清理→上线→除油→水洗→除锈→水洗→中和→水洗→磷化→水洗→钝化→电泳涂装→槽上清洗→超滤水洗→烘干→下线。
(2)被涂物的底材及前处理对电泳涂膜有极大影响。
铸件一般采用喷砂或喷丸进行除锈,用棉纱清除工件表面的浮尘,用80#~120#砂纸清除表面残留的钢丸等杂物。
钢铁表面采用除油和除锈处理,对表面要求过高时,进行磷化和钝化表面处理。
黑色金属工件在阳极电泳前必须进行磷化处理,否则漆膜的耐腐蚀性能较差。
磷化处理时,一般选用锌盐磷化膜,厚度约1~2μm,要求磷化膜结晶细而均匀。
(3)在过滤系统中,一般采用一级过滤,过滤器为网袋式结构,孔径为25~75μm。
电泳涂料通过立式泵输送到过滤器进行过滤。
电泳漆技术说明
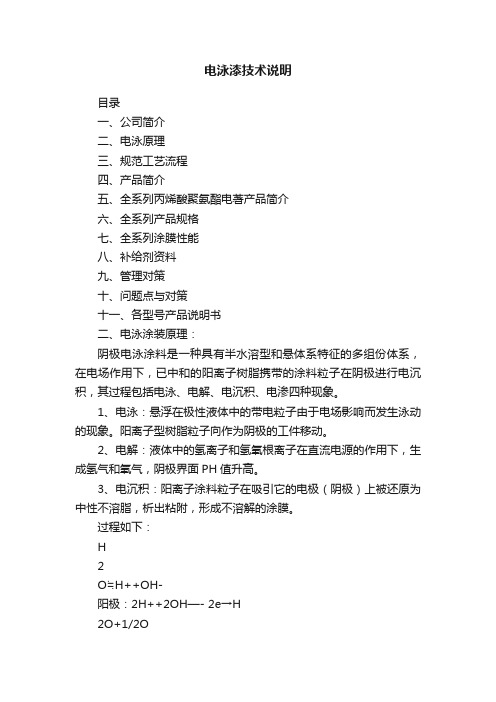
电泳漆技术说明目录一、公司简介二、电泳原理三、规范工艺流程四、产品简介五、全系列丙烯酸聚氨酯电著产品简介六、全系列产品规格七、全系列涂膜性能八、补给剂资料九、管理对策十、问题点与对策十一、各型号产品说明书二、电泳涂装原理:阴极电泳涂料是一种具有半水溶型和悬体系特征的多组份体系,在电场作用下,已中和的阳离子树脂携带的涂料粒子在阴极进行电沉积,其过程包括电泳、电解、电沉积、电渗四种现象。
1、电泳:悬浮在极性液体中的带电粒子由于电场影响而发生泳动的现象。
阳离子型树脂粒子向作为阴极的工件移动。
2、电解:液体中的氢离子和氢氧根离子在直流电源的作用下,生成氢气和氧气,阴极界面PH值升高。
3、电沉积:阳离子涂料粒子在吸引它的电极(阴极)上被还原为中性不溶脂,析出粘附,形成不溶解的涂膜。
过程如下:H2O≒H++OH-阳极:2H++2OH—- 2e→H2O+1/2O2↑+2H+阴极:2OH-+2H++2e→H2↑+2OH-R1 R 1∣∣~NH++OH-→~N↓+H2O ∣∣R 2 R24、电渗:在外电场力作用下,涂膜内部所含的水份从涂膜中渗析出来移向槽液,进行内聚部分脱水。
电渗使亲水涂膜变为憎水涂膜,脱水使涂膜致密化。
由于上述四个过程是连续进行的,获得的涂膜在烘干之前含水量在10%以下,可以直接进行水洗、烘干,最后形成连续均一的品质优良的涂膜。
三、规范工艺流程:1.环氧体系电泳流程:高温脱脂(加超声波)→常温脱脂→水洗三次→酸洗除锈→水洗三次→流动水洗→表调→磷化→水洗三次→流动水洗→纯水洗两次→电泳涂装→回收水洗三次→纯水浸洗两次→纯水喷淋→脱水剂洗/吹洗→烘干固化→成品包装2.透明有色体系电泳流程:电镀工件(抛光工件)→化学除油(加超声波)→水洗两次→电解除油→水洗三次(溢流水洗)→中和(弱酸洗)→水洗三次(溢流水洗)→纯水洗两次→电泳涂装(透明及各色)→回收纯水洗两次→纯水洗三次(溢流)→脱水剂洗→滴水(吹净水珠)→烘烤→成品包装四、产品简介:1.环氧体系电泳涂料:本公司之环氧体系电泳涂料目前主要以色浆、乳液双组份供应市场。
电泳涂装技术简介

电泳涂装技术简介电泳涂装技术是一种利用电化学原理进行涂装的方法。
它通过在电解液中将喷涂颗粒带电,然后将带电颗粒吸附在工件表面,通过电解液中的电流使喷涂颗粒形成一层均匀、致密的涂层。
电泳涂装技术具有高效、经济、环保等优点,适用于各种材料和形状的工件。
电泳涂装技术的工艺流程主要包括:预处理、电泳涂装、固化烘干和后处理。
其中,预处理是为了去除工件表面的污染物和氧化物,通常包括除油、除锈、酸洗等步骤。
电泳涂装是将工件浸入电解槽中,通过正极电源使固体颗粒带上正电荷,喷涂颗粒则带上负电荷,利用电荷的相互作用将喷涂颗粒吸附在工件表面。
固化烘干是通过烘干设备将涂层固化为连续的膜层,以提高涂膜的附着力和耐腐蚀性能。
后处理是为了提高涂层表面的光泽度和平整度,通常包括打磨、抛光等步骤。
1.高效:电泳涂装过程中,喷涂颗粒通过电流的驱动迅速吸附在工件表面,涂装速度快,生产效率高。
2.经济:电泳涂装使用的涂料利用率高,几乎没有浪费。
而且,由于涂装层均匀致密,涂料的使用量相对较少,能节约成本。
3.环保:电泳涂装过程中不需要有机溶剂,不产生挥发性有机化合物(VOC)的排放,符合环保要求。
4.均匀性好:由于电泳涂装中涂料的带电颗粒会自动流动,使得涂层分布均匀,覆盖能力强,能够涂装到工件的各个角度和细微部位。
5.附着力强:电泳涂装过程中,涂料颗粒由于带电静电相互作用的引力作用,使得涂层与工件表面吸附紧密,附着力强,不易剥落。
6.防腐性好:电泳涂装的涂料分子能充分的填充工件表面的微小空隙,并形成均匀致密的涂层,能有效地防止氧气、水分、酸碱等腐蚀因素的侵袭,具有良好的防腐性能。
电泳涂装技术在很多领域都有广泛的应用,特别是在汽车制造、家电制造、建筑材料等行业。
比如,在汽车制造领域,电泳涂装可以为汽车提供高效、均匀、耐腐蚀的外观涂装,使汽车具有更好的耐久性和抗腐蚀性能。
在家电制造领域,电泳涂装可以为家电产品提供美观的外表,同时保护产品不受潮气、腐蚀和划伤。
电泳涂装技术简介

电泳涂装技术简介目录一概述1电泳涂装的特点2电泳涂装的种类(阴极、阳极电泳驻性能比较)二电泳涂装基本原理三电泳涂装工艺及工艺管理1工件涂装前金属表面处理2电泳涂装工艺条件及重点参数管理四电泳涂装设备五电泳涂装的漆膜弊病及其防治六电泳涂料及其涂膜性能的测试方法〈操作实验〉电泳涂装技术简介一概述电泳涂装是将具有导电性的被涂工件,浸渍在装水稀释的、浓度比较低的电泳涂料槽中作为阴极(或阳极),在槽中另投置与其相对应的阳极(或阴极),在两极间通一定时间的直流电,通过物理化学作用将漆沉积在被涂工件上,形成、水不溶性膜的一种涂装方法。
1.阴极电泳涂装的特点:高效——从漆前处理到电泳底漆烘干可实现生产线化,可适用于大流水线生产。
优质——其泳透力好,提高了工件内的防腐蚀性;(其对工件内腔、焊缝、边缘等的防腐能力是其它涂装法所不能比拟的,漆膜耐盐雾试验可达成1000小时)可得到均一的膜厚,外观好。
安全——属低公害水溶性涂料,溶剂含量少,无火灾危险,尤在采用UF 装置后,涂料回收好,大大减少了对水质和大气污染。
经济——指涂料利用率高,可达%952电泳涂装的种类:电泳涂装根据涂料树脂所带电荷的种类分阴极电泳和阳极电泳。
1)阳极电泳——所用涂料树脂是由带羟基团的聚合物经胺中和成盐再水溶,树脂及颜料粒子带负电荷。
常见的有聚丁二烯阳极电泳涂料等。
2)阴极电泳——所用涂料树脂是由带胺基的碱性树脂经酸中和成盐再水溶,树脂及颜料粒子带正电荷。
常见的有环氧树脂、聚胺脂等阴极电泳涂料。
3)阴极电泳漆比较于阳极电泳漆,具有以下优点:(1)具有优良的防腐性能,对底材的附着力高,对焊缝、锐边保护更好。
根据资料统计,阴极漆膜的抗蚀能力优于阳极漆膜5~6倍。
从成本角度考虑,膜厚为10μm的阴极电泳漆漆膜,其耐盐雾试验>=400h,而膜厚为20μm的阳漆膜,其耐雾试验仅达到240-360h。
(2)阴极电泳涂料的库仑效率为阳极电泳涂料的二倍,可使耗电量减少于30%(3)阴极电泳的泳透力高,一般为阳极电泳的1.3-1.5倍,更适宜于形状复杂的工件涂装。
- 1、下载文档前请自行甄别文档内容的完整性,平台不提供额外的编辑、内容补充、找答案等附加服务。
- 2、"仅部分预览"的文档,不可在线预览部分如存在完整性等问题,可反馈申请退款(可完整预览的文档不适用该条件!)。
- 3、如文档侵犯您的权益,请联系客服反馈,我们会尽快为您处理(人工客服工作时间:9:00-18:30)。
第一章概述电泳涂料技术源自汽车工业,它是适应汽车车身的涂装技术要求、解决汽车车身底漆涂装工艺中存在的问题而开发和发展起来的新的车身涂底漆方法(含新型的电泳涂料、电泳涂装工艺和涂装设备及其配套的附属装置等),是当今汽车车身涂底漆工艺的主流涂装方法。
汽车车身“打底工艺”(即漆前表面处理工艺加涂底漆工艺)是汽车车身防腐蚀和获得优质涂层的基础,是直接影响车身使用寿命的关键工艺。
“打底工艺”所追求的目标是:①能将汽车车身的100%表面(含内腔、焊缝表面)处理完善,涂上底漆。
②底涂层的耐腐蚀应优异(达到产品设计要求),对底材的附着力强,与中涂、面漆的配套性应优良。
③底涂层的机械性能好,且平整光滑,不需打磨,为面漆创造良好的基底。
④涂装能实现自动化,且安全又环保。
⑤材料利用率高,经济性好,高效且性价比高。
在世界汽车工业100多年的历史中,汽车车身涂底漆的方法已经历刷涂、喷涂、浸涂、阴极电泳、阴极电泳等多次变革,在克服或消除前种涂底漆的方法存在的工艺问题的基础上逐步走向完善。
汽车车身的各种涂底漆方法的特征及优缺点参见表1-1。
表1-1 汽车车身涂底漆方法一览表涂装方法特征存在的工艺问题备注刷涂手工作业、工装简单 1.内腔、焊缝内涂不上漆①2.作业效率低3.漆面有刷痕仅适用于小批量,作坊式生产喷涂(空气喷涂和高压无气喷涂)适用于快干底漆(如硝基漆、双组分底漆);作业效率有较大幅度提高1.内腔、焊缝内涂不上漆①2涂着效率低;材料利用率低适用于流水作业式生产和各种底漆的涂装浸涂拖式浸涂仅浸涂车身的底部,易实现自动化1.涂膜上下不均,有流痕,采用滚动浸涂有改善2.缝隙中产生“溶落②”现象,涂膜变薄3.大槽浸漆,火灾危险大为不影响外观,在拖式浸涂后车身外面涂膜擦洗掉后再喷涂在美国曾产生一次浸涂槽火灾,促使改用水性漆。
浸涂法已被电泳涂装法淘汰滚动浸涂在浸涂和沥漆过程中车身旋转滚动,易实现自动化电泳涂装阳极电泳以车身为阳极,采用阴离子型电泳涂料,工作液为碱性,易实现自动化产生阳极溶解,涂层的耐腐蚀性差在车身涂装中已被阴极电泳涂装淘汰阴极电泳以车身为阴极,采用阳离子型电泳涂料,工作液为酸性,易实现自动化因车身为阴极,不产生阳极溶解,涂膜有耐腐蚀性高,泳透力优异已成为大量流水生产的汽车车身涂底漆的主流工艺③①内腔,缝隙内兴漆,锈蚀就从里向外烂,产生“穿孔腐蚀”,大大降低汽车车身的使用寿命。
②“溶落”现象是指浸渍到缝隙中的涂料,在烘干过程中随溶剂蒸发将涂膜洗落掉,从而使涂膜变薄、抗腐蚀性能降低。
③随着先进的输送车身机械(如旋转输送机Rodip-3和多功能穿梭机)与阴极电泳涂装工艺的配套,使汽车车身100%面积涂装完善(消除车身顶盖下的“气泡”),可克服车身主要装饰面的“L”效应,并使车身带槽液量大大减少;使阴极电泳涂装在为现今最理想的车身涂底漆工艺技术。
上述“打底工艺”所追求的五大目标几乎都能实现。
表1-1中所列的也是近100年的汽车车身涂底漆工艺的演变史,从中可看出电泳涂装法是从浸涂水性涂料工艺的基础上开发出来的新的涂装方法。
基于电泳涂装后的湿膜表面附着的槽液(浮漆)可用超滤(UF)液和纯水清洗回收,并能吹干,它克服了浸涂的“溶落”现象,确保了涂膜的均匀性和平滑性,提高了涂料利用率(达95%以上),大幅度削减了VOC (挥发性有机化合物)的排放量;消除了在槽浸漆的火灾危险性等浸涂法存在的缺点和工艺问题,致使电泳涂装法在车身涂装领域普及速度十分迅速,很快就淘汰了浸涂法。
又基于阴极电泳涂装法的泳透力好,且消除了阳极溶解这一工艺问题;涂膜的耐腐蚀性比阳极电泳涂膜成倍提高,在车身涂装领域阴极电泳涂装很快取代了阳极电泳涂装。
并随一代一代阴极电泳涂料和涂装技术的进步,高泳透力和超高涂透力阴极电泳涂料、低VOC 含量和低加热减量的阴极电泳涂料、阴极电泳涂料烘干温度低温化、耐候性阴极电泳涂料、锐边耐腐蚀性阴极电泳涂料、电泳—反渗透(ED-RO)封闭式电泳后清洗工艺等的开发应用,使阴极电泳涂装工艺成为最理想的环保友好型涂装方法,在汽车车身涂装领域至今尚无理想的可取代它的车身打底方法,并在其他工业涂装领域得到普及应用。
第一节电泳涂装的发展及电泳涂装的定义一、电泳涂装的发展历史电泳涂装的原理发明于19世纪30年代,但因当时水性涂料尚不发达而未得到工业应用。
为提高汽车车身内腔和焊缝里的防腐蚀性,美国福特汽车公司在Dr.George Breaer的领导下于1957年开始着手研究电泳涂装法,于1961年建成一条车轮阳极电泳涂装线,1963年世界上第一个用于汽车车身的电泳槽在福特汽车公司Wixom装配厂投入使用,使用的是阳极电泳漆。
电泳涂装法在实际应用中显示出的高效、优质、安全、经济等优点,受到世界各国涂装界的重视。
随着新型电泳涂料的开发和涂装技术的进步,尤其是阳离子型电泳涂料和阴极电泳涂装技术的开发(1977年世界上第一条车身阴极电泳涂装线在美国投产),电泳涂装工艺普及速度是史无前便的,在1965年只有1%的汽车车身涂底漆采用电泳涂装法,1970年为10%,1985年汽车车身阴极电泳化率达90%以上,而现今汽车车身几乎100%采用阴极电泳涂装。
并由汽车工业推广应用到建材、轻工、农机、家用电器等工业领域。
40多年的电泳涂装的发展史可划分为以下五个阶段:第一阶段:阳极电泳涂半的初级阶段(1970年以前),确立电泳涂装工艺规范,稳定和完善电泳涂装工艺,解决电泳漆膜弊病,提高泳透边、低耐腐蚀和酚醛和环氧树脂系列为代表。
第二阶段:阳极电泳涂装阶段(1970~1976年),在这期间优质的高泳透力、高耐腐蚀性的第二代阳极电泳涂料(以聚丁烯阳极电泳涂料为代表)投产使用,废除了辅助电极,起滤技术在电泳涂装工艺中获得应用,实现了闭合循环水洗系统、达到了电泳涂装工艺合理化,节省劳动力、提高了涂料利用率、减少了电泳废水污染,汽车车身的耐腐蚀性能有较在幅度的提高。
第三阶段:阴极电泳涂装替代阳极电泳涂装阶段(1977~1990年),由于阴极电泳涂料的耐腐蚀性成倍优于阳极电泳涂料,泳透力也较高,且消除了阳极溶解现象等原因,阴极电泳涂装工艺一开发成功,便获得工业应用,很快形成阴极电泳取代阳极电泳之势。
第四阶段:阴极电泳涂装工艺进一步提高完善阶段(1990~2000年),通过改进阴极电泳涂料的质量、开发新品种,完善阴极电泳涂装设备和管理自动化等措施,追求涂装无缺陷化、厚膜的均一化,以适应汽车车身涂装高质量的要求,例如厚膜阴极电泳涂料(膜厚35μm±5μm)的投产使用;在车身电泳涂装时采用顶盖电极和底电极等。
第五阶段:阴极电泳涂料的高质量、节能、环保化、涂装技术的更先进化(2000年以来)。
随着汽车市场竞争日趋激烈和各国环保法规的相继出台,近几年开发了很多阴极电泳涂料的新品种并获得工业化应用研究。
高泳透力、低溶剂含量、低温烘烤型、高锐边防腐蚀性能、无铅、无锡、耐候性能好等阴极电泳涂料都已在生产线上得到了应用;新型多功能穿梭机(Vario-Shuttle)、滚浸运输机(Ro-Dip)和倒挂升降输机制应用及电泳涂装工艺全闭合水洗系统(ED-RO)等新的涂装技术得到应用。
我国电泳涂料和涂装技术的开发也有40多年的历史,1965年上海涂料所开发成功阳极电泳涂料,随后有些油漆厂也相继试制成功。
20世纪70年代我国汽车工业中已建成几条汽车零部件和驾驶室的阳极电泳涂装线。
我国第一代阴极电泳涂料是由当时的兵器部五四研究所(现改为五九所)于是1979年首先研制成功的,并在军工产品上得到一定的应用,上海涂料所、常州涂料所、沈阳等油漆厂也做了大量的开发工作,开发的产品在生产线上得到了应用。
在六五期间我国涂料工业和汽车厂分别从日本、奥地利和英国引进阴极电泳涂料的制造技术和涂装技术,第一条现代化的大流水生产的汽车车身阴极电泳涂装生产线于1986年7月13日在中国一汽车身厂投产,随后在我国汽车工业中形成了辐射涂底漆采用阴极电泳涂装替代阳极电泳涂装之趋。
二、电泳涂装的定义(一)电泳涂装(electrophoretic coating)电泳涂装(也称作电沉积涂装)是一种特殊的涂膜形成方法,仅适用于与一般兴翻盖不同的电泳涂装专用的水性涂料(简称电泳涂料)。
它是将具有导电性的被涂物浸渍在装满水稀释的、固体分比较低的电泳涂料工作液中作为阳极(或阴极)、在电泳槽中另设置与其相对应的阴极(或阳极),在两极间直流电,在被涂物表面上析出均一、水不溶的涂膜的一种涂装方法。
(二)电泳涂装的类型根据被涂物在电泳槽中的极性和电泳涂料的种类,有两种类型电泳涂装方法。
1. 阳极电泳涂装(Anodic electrophoretic-AED)被涂物(工件)在电泳槽中作为阳极,所采用的电泳涂料是阴离子型(带负电荷),工作碱性,即采用阳极电泳涂料的涂装方法。
2. 阴极电泳涂装(Cathodic electrophoretic-CED)被涂物(工件)在电泳槽中作为阴极,所采用的电泳涂料是阳离子型(带正电荷),工作液是酸性,即采用阴极电泳涂料的涂装方法。
第二节电泳涂装的机理及特点一、电泳涂装的机理(一)、电泳涂装的四个物理化学作用电泳涂装最基本的物理原理为带电荷的涂料粒子与它所带电荷相反的电极相吸,采用直流电源,导电工件浸入电泳漆工作液中。
通电后,阳离子涂料粒子向阴极工件移动,阴离子涂料粒子向阳极工件移动,继而沉积在工件上,在表面形成均匀、连续的涂膜。
当涂膜达到一定的厚度,工件表面形成绝缘层时,“民性相吸”即停止,电泳涂装过程结束。
可以概括为下列四个物理化学作用。
1. 电解(electrotysis)任何一种导电液体在通电时产生电离分解的现象称为电解。
在电泳涂装过程中电泳涂料电解劝成阴离子型或阳离子型的胶体涂料粒子,水电解成H+和OH-,在阴极上放出氢气,在阳极上放出氧气,阳极产生溶解。
电解反应在沉积涂装中应适当控制,否则将导致不良效果(尤其在工件入槽段)。
2. 电泳(eletrophoresis)在导电介质中的带电荷的胶体粒子受电场的影响向相反电极泳动的现象称为电泳。
例如在阴极电泳涂装过程中在电场的作用下带正电胶体的涂料粒子电泳移向阴极。
3. 电沉积(eletrodeposition)涂料粒子在电极上的沉析现象称为电沉积。
在阴极电泳涂装时带正电荷的粒子在阴极上凝聚,即带正电荷尔蒙的涂料粒子到达阳极(被涂物)表面上(高碱性的界面层)得到电子,并与氢氧离子反应变成水不溶性,沉积在被涂物上。
在阳极电泳涂装时带负电荷的粒子在阳极上凝聚。
电沉积过程是电泳涂装作用中最重要的。
4. 电渗(eletroandosmosis)在用半透膜间隔的溶液的两端(阴极和阳极)通电后,低浓度和溶质向高浓度侧移动的现象称为电渗。