整线设备稼动率与节拍分析
生产稼动率与OEE
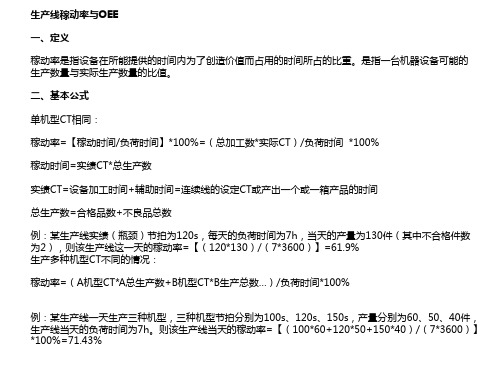
例:某生产线一天生产三种机型,三种机型节拍分别为100s、120s、150s,产量分别为60、50、40件, 生产线当天的负荷时间为7h。则该生产线当天的稼动率=【(100*60+120*50+150*40)/(7*3600)】 *100%=71.43%
三、OEE与稼动率的区别
OEE定义:OEE是Overall Equipment Effectiveness(全局设备效率)的缩写。一般,每一个生产设备都有 自己的理论产能,要实现这一理论产能必须保证没有任何干扰和质量损耗。OEE就是用来表现实际的生产能 力相对于理论产能的比率,它是一个独立的测量工具。
OEE计算实例:
设某设备某天工作时间为8H,班前计划停机10min,故障停机30 min,设备调整35 min,产品的理论加工 周期为1min/件,一天共加工产品400件,有20件废品,求这台设备的OEE。
根据上面可知: 计划运行时间=8*60-10=470(min) 实际运行时间=470-30-35=405(min) 时间利用率=405/470=0.86(86%) 性能利用率=400/405=0.98(98%) 良品率=(400-20)/400=0.95(95%)OEE=有效率*表现性*质量指数=80%
生产线稼动率与OEE
一、定义
稼动率是指设备在所能提供的时间内为了创造价值而占用的时间所占的比重。是指一台机器设备可能的 生产数量与实际生产数量的比值。
二、基本公式
单机型CT相同:
稼动率=【稼动时间/负荷时间】*100%=(总加工数*实际CT)/负荷时间 *100%
稼动时间=实绩CT*总生产数
实绩CT=设备加工时间+辅助时间=连续线的设定CT或产出一个或一箱产品的时间
自动化机械加工生产线节拍分析
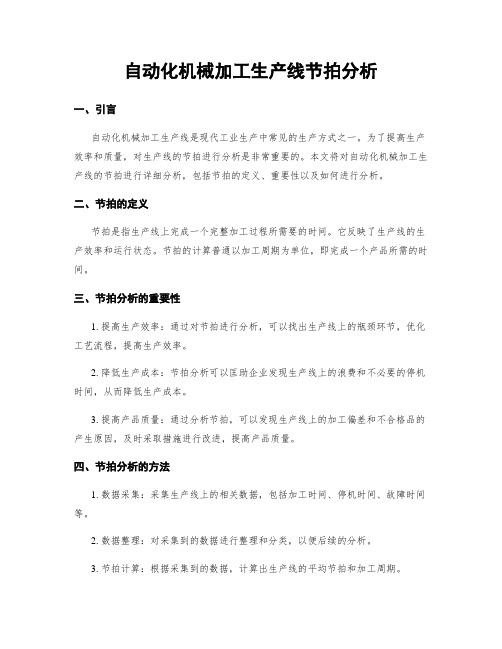
自动化机械加工生产线节拍分析一、引言自动化机械加工生产线是现代工业生产中常见的生产方式之一。
为了提高生产效率和质量,对生产线的节拍进行分析是非常重要的。
本文将对自动化机械加工生产线的节拍进行详细分析,包括节拍的定义、重要性以及如何进行分析。
二、节拍的定义节拍是指生产线上完成一个完整加工过程所需要的时间。
它反映了生产线的生产效率和运行状态。
节拍的计算普通以加工周期为单位,即完成一个产品所需的时间。
三、节拍分析的重要性1. 提高生产效率:通过对节拍进行分析,可以找出生产线上的瓶颈环节,优化工艺流程,提高生产效率。
2. 降低生产成本:节拍分析可以匡助企业发现生产线上的浪费和不必要的停机时间,从而降低生产成本。
3. 提高产品质量:通过分析节拍,可以发现生产线上的加工偏差和不合格品的产生原因,及时采取措施进行改进,提高产品质量。
四、节拍分析的方法1. 数据采集:采集生产线上的相关数据,包括加工时间、停机时间、故障时间等。
2. 数据整理:对采集到的数据进行整理和分类,以便后续的分析。
3. 节拍计算:根据采集到的数据,计算出生产线的平均节拍和加工周期。
4. 节拍对照分析:将不同时间段、不同工序的节拍进行对照,找出差异和规律。
5. 节拍优化措施:根据分析结果,制定相应的优化措施,如改进工艺流程、提高设备效率等。
6. 实施和监控:将优化措施付诸实施,并进行监控和评估,确保效果的持续改进。
五、案例分析以某汽车零部件生产线为例,进行节拍分析。
该生产线由自动化机械设备组成,包括车床、冲床、铣床等。
1. 数据采集:采集生产线上的加工时间、停机时间、故障时间等数据。
例如,车床加工时间为10分钟,停机时间为5分钟,故障时间为2分钟。
2. 数据整理:将采集到的数据整理为表格或者图表,以便后续的分析。
3. 节拍计算:根据采集到的数据,计算出生产线的平均节拍和加工周期。
例如,车床的平均节拍为17分钟(加工时间+停机时间+故障时间)。
稼动率与设备总合效率(OEE)分析
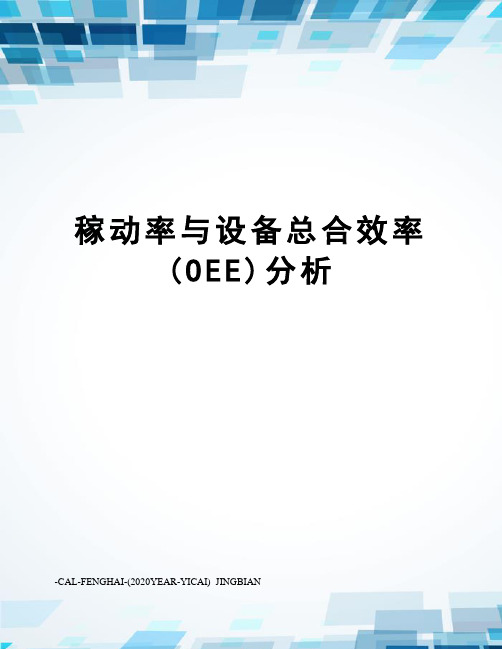
稼动率与设备总合效率(O E E)分析-CAL-FENGHAI-(2020YEAR-YICAI)_JINGBIAN稼动率与设备综合效率分析如果您被问到「我们部门的稼动率为90%,你们厂里是多少」,您可知道其所谓的稼动率定义为何90%这数字代表的是好是坏呢基本上稼动率有数种不同的定义,在此略加解释:1、时间稼动率首先定义最大操作时间,指的是设备可用的最大时间,若设备本身为厂内自购,且可完全由厂内自主使用,则最大操作时间一般为日历时间;而负荷时间则为设备可稼动的时间,乃是最大操作时间扣除停机(Shutdown, SD)损失,停机损失乃是计画上的休止时间,如休假、教育训练、保养等。
而稼动时间则是负荷时间扣除停止时间,而停止时间包括批次转换及制程异常、设备异常停止及修复时间。
最大操作时间:设备可用的最大时间负荷时间:最大操作时间扣除停机(Shutdown, SD)损失;这里的停机损失是计划是可预见的为客观实际的事实:如班前后会,保养、吃饭时间,日历时间或法定假日等。
停机(Shutdown, SD)损失:计画上的休止时间,如休假、教育训练、保养等稼动时间:负荷时间扣除停止时间停止时间:包括批次转换及制程异常、设备异常停止及修复时间。
由以上的定义,即可算出最常用的稼动率定义-设备稼动率(也称为时间稼动率),其公式为时间稼动率=稼动时间 / 负荷时间也可等于(操作时间/计划工作时间)目的:减少停止时间!!!通过资源整合,管理优化,进行资源充分利用,降低成本,提高效率。
2、性能稼动率/实质稼动率/速度稼动率时间稼动率并无法完全表现设备对生产的贡献程度;例如,相同的设备,相等的稼动时间,可能因效率的不同,而有不同的产能,此类效率降低的损失则称为性能损失。
在此定义速度稼动率如下:速度稼动率=基准周期时间/ 实际周期时间其中,基准周期时间:设备原设计产出单位产量所需的时间。
实际周期时间:目前设备实际产出单位产量所需的时间。
稼动率 讲解

设备嫁动率=设备运行时间/工作时间*100%运行时间为设备开机时间工作时间为上班的时间。
比如SMT一班为12小时,因维修停了1小时,则设备嫁动率=11/12*100%=91。
7%。
稼动率是一个重要的指标,论坛上虽已类似的帖子,但因部分段落字体损坏而影响了对全文的理解,这里再重发一贴。
如果您被问到“我们部门的稼动率为90%,你们厂里是多少?”,您可知道其所谓的稼动率定义为何?90%这数字代表的是好?是坏呢?基本上稼动率有数种不同的定义,在此略加解释:1、时间稼动率首先定义最大操作时间,指的是设备可用的最大时间,若设备本身为厂内自购,且可完全由厂内自主使用,则最大操作时间一般为日历时间;而负荷时间则为设备可稼动的时间,乃是最大操作时间扣除停机(Shutdown,SD)损失,停机损失乃是计画上的休止时间,如休假、教育训练、保养等。
而稼动时间则是负荷时间扣除停止时间,而停止时间包括批次转换及制程异常、设备异常停止及修复时间。
最大操作时间:设备可用的最大时间负荷时间:最大操作时间扣除停机(Shutdown, SD)损失;停机(Shutdown, SD)损失:计画上的休止时间,如休假、教育训练、保养等稼动时间:负荷时间扣除停止时间停止时间:包括批次转换及制程异常、设备异常停止及修复时间。
由以上的定义,即可算出最常用的稼动率定义-设备稼动率(也称为时间稼动率),其公式为时间稼动率=稼动时间/ 负荷时间目的:减少停止时间!通过资源整合,管理优化,进行资源充分利用,降低成本,提高效率。
2、性能稼动率/实质稼动率/速度稼动率时间稼动率并无法完全表现设备对生产的贡献程度;例如,相同的设备,相等的稼动时间,可能因效率的不同,而有不同的产能,此类效率降低的损失则称为性能损失。
在此定义速度稼动率如下:速度稼动率=基准周期时间/ 实际周期时间其中,基准周期时间:设备原设计产出单位产量所需的时间。
实际周期时间:目前设备实际产出单位产量所需的时间。
机台利用率及稼动率

机台利用率及稼动率
机台利用率和稼动率是生产管理中常用的两个指标,它们分别反映了设备的使用效率和生产能力。
机台利用率是指设备在计划时间内实际被使用的时间所占的比例,计算公式为:机台利用率 = 实际使用时间 / 计划时间× 100%。
这个指标主要用于评估设备的使用效率,即设备在计划时间内被充分利用的程度。
如果机台利用率较低,说明设备存在闲置或浪费的情况,需要进行优化和调整。
稼动率则是指设备在计划时间内实际生产出的产品数量与理论最大生产量之比,计算公式为:稼动率 = 实际生产量 / 理论最大生产量× 100%。
这个指标主要用于评估设备的生产能力,即设备在计划时间内能够实际生产出的产品数量。
如果稼动率较低,说明设备的生产能力存在瓶颈或不足,需要进行改进或升级。
需要注意的是,机台利用率和稼动率虽然都是反映设备使用效率和生产能力的指标,但它们的关注点不同。
机台利用率更侧重于设备的时间利用,而稼动率更侧重于设备的产量利用。
因此,在实际应用中,需要根据具体情况选择合适的指标进行评估和优化。
以上信息仅供参考,如有需要,建议咨询生产管理领域的专业人士。
稼动率分析与改善

三稼动率分析与改善从综合效率的计算公式(4-8)可以看出,要提升效率,可以从提升作业能率和提升稼动率入手。
首先来分析如何提升稼动率。
从表4-1中可以看出,提升稼动率,就是要减少损失时间,而损失时间又由除外时间与异常时间组成。
基中,除外时间只只能尽量缩短,但往往是必不可少的,因此提升稼动率的主要着眼点即为异常时间的降低。
1异常时间的种类拨所谓的异常时间(或称异常工时),是指造成制造部门停工或生产进度延迟的情形。
由此而产生的时间浪费。
由表面膜势得知,异常时间一般包括:①计划异常因生产计划临时变更或安排失误等导致的异常。
②物料异常因物料供应不及时(断料)、物料品质问题等导致的异常。
(3)设备异常因设备、工装不足或故障等原因而导致的异常。
(4)品质异常因制程中出现了品质问题而导致的异常,也称制程异常。
(5)机种异常因产品设计或其他技术性问题而导致的异常,也称产品异常或技术异常。
(6)水电异常因水、气、电等导致的异常。
2、异常的处理流程(1)异常发生时,发生部门的制造主管应立即与生技单位或相关责任单位联络,共同研拟对策加以处理。
(2)一般应先采取应急对策,并加以执行,以尽快恢复生产,降低异常时间的影响。
(3)在异常处理同时或异常排除之后,由制造部门填具生产异常报告单(如表4-7),并转责任单位。
(4)责任单位填写异常处理之根本对策,以防止异常重复发生。
(5)制造单位、责任单位依据该单作后续追踪工作、确认是否得到改善。
(6)财务部门依该异常单作为制造费用统计之凭证,并作为向厂商索赔之依据。
(7)生管部门依异常状况作为生产进度管制控制点,并作为生产计划调度之参考。
3、异常工时计算规定(1)当所发生的异常,导致生产现场部分或全部人员完全停工等待时,异常工时之影响以100%计算。
(2)当所发生的异常,导致生产现场需增加人力投入,采取临时应急对策处理该异常时,异常工时之影响以实际增加投入的工时为准。
(3)当所发生之异常,导致生产现场作业速度放慢(可能同时也增加人力投入)时,异常工时之影响度以实际影响比例计算。
机器设备稼动率基础知识
价值稼动时间与设备综合效率
性能稼动时间表示设备产出产品的时间,但 无法表示设备产出良率的好坏,因此定义 “价值稼动时间”来表示真正能产出良品的 有价值时间,其定义如下: 价值稼动时间﹦性能稼动时间x良品率 而设备的有效使用程度则依“设备综合效率” 来判定,其定义如下: 设备综合效率=时间稼动率x性能稼动率x良品率
1次/周 1次/周 1次/周 1次/周 1次/周 1次/周 1次/周 1次/周 每次
1.计划保养损失...因年度保养之计划SD保养与定期检修所造成的停工损失。 2.生产调整损失...因供需问题而调整生产计划的时间损失。 3.设备故障损失...设备和机器突然丧失既定的功能,所造成的停机损失。 4.制品故障损失...制程中物质的化学、物理、物性因操作错误,或外界干扰而产生变化, 造成工厂停工之损失。 5.固定生产损失...启动、停止及切换之调整所造成的损失。 6.非固定生产损失..因工厂设备问题或生产了异常之批量,而使产量下降之时间损失。 7.工程不良损失...生产出不良品所造成的损失,以及报废品造成物的损失,及次级品的损失。 8.再稼工损失....因工程中不良,再退回前工程所造成之再稼工損失。
设备综合效率时间稼动率x性能稼动率x良品率设备综合效率时间稼动率性能稼动率良品率时间稼动率负荷时间停止时间负荷时间100性能稼动率实际产出量理论产出量100良品率良品数良品出货数不良品數返修数100暂停件数未满10分钟之暂停故障件数设备故障件数10分钟以上生产线停止件数mtbf稼动时间设备故障件数100mttr设备故障停止时间设备故障件数100新设备的停止故障件数新设备之初期流动时间故障件数每次1
二. 稼动率定义
图一
参考设备稼动与损失关系图(上图),首先顶一最大操作时间,指的是设 备可用的最大时间,最大操作时间一般为日历时间(自然月,每天24H); 而负荷时间则为设备可稼动的时间,则是最大操作时间扣除停机损失,停 机损失一般是说计划中的休息时间,如休假、培训、保养等。 由以上的定义,即可算出最常用的稼动率定义---设备稼动率(也叫做时间 稼动率),其公式为 时间稼动率 = 稼动时间 / 负荷时间*100%
设备稼动率
稼动率“稼动率”英文称作activation或utilization,是指设备在所能提供的时间内为了创造价值而占用的时间所占的比重OEE的组成包含三大指标:时间稼动率(可用率),性能稼动率(表现指数),良品率(质量指数)OEE=时间稼动率 x 性能稼动率 x 良品率(OEE=可用率*表现指数*质量指数)时间稼动率=(负荷时间-停机时间)/负荷时间性能稼动率=理论节拍时间*投入数量/稼动时间良品率=(投入数量-不良数量)/投入数量概念说明:计划作业时间=上,下班时间减去用餐时间实际作业时间= 计划作业时间-提前停止时间(或+延时时间)负荷时间 = 实际作业时间 - 计划停止时间。
计划停止时间包含早晚例会、休息时间、始业点检、安全点检、自主保全、体制展开、试作、计划停止时间等时间稼动时间= 负荷时间-停线时间:工具更换、调整、故障停止、上下流等待、质量维持、确认、工件不良、操作失误、作业缓滞停止等时间净稼动时间=稼动时间-(实际节拍-理论节拍)x产量节拍:生产一个单位制品需要的时间间隔理论(计划)节拍:以设计部门设定的参数为依据,或者依据需求量与人员的匹配,决定生产单个产品所需的时间.制订生产计划时,拿来作为标准的依据,以决定生产产品的理论数量。
实际节拍:因作业环境和限制条件等影响,实际稼动的平均时间.速度稼动率 = 理论节拍/实际节拍*100%净稼动率 = 速度稼动率 ×纯稼动率 = 理论节拍×生产数量/稼动时间*100%时间稼动率 =(负荷时间 - 停止时间)/负荷时间*100%良品率 =(投入数量 - 不良数量)/投入数量*100% = 良品数量/投入数量 *100%计算方法编辑稼动率时间稼动率是指相对于生产时间(负荷时间),实际生产物品的时间(稼动时间)所占的比率。
是以机器设备的稼动时间除以最大负荷时间而得。
而稼动时间是指负荷时间减掉换模、换刀具、故障、调整等的时间。
因此要提高稼动率,就必须要减少换模具、换刀具、故障、调整的损失时间。
年度稼动率总结(3篇)
第1篇一、引言稼动率,即设备稼动率,是衡量企业生产设备运行效率的重要指标。
它反映了设备在一定时间内的实际运行时间与理论运行时间的比值。
对于企业而言,提高稼动率意味着更高的生产效率、更低的成本和更优的市场竞争力。
本报告将总结过去一年的稼动率情况,分析原因,并提出改进措施。
二、稼动率概述1. 定义稼动率是指在一定时间内,设备实际运行时间与理论运行时间的比值。
计算公式为:稼动率 = 实际运行时间 / 理论运行时间× 100%2. 影响因素影响稼动率的因素有很多,主要包括以下几个方面:(1)设备维护:设备维护不及时、维护质量不高,会导致设备故障率上升,从而降低稼动率。
(2)生产计划:生产计划不合理,会导致设备闲置或过度使用,影响稼动率。
(3)人员操作:操作人员技能水平不高、操作不规范,容易导致设备故障,降低稼动率。
(4)原材料供应:原材料供应不稳定、质量不合格,会影响生产进度,降低稼动率。
(5)市场需求:市场需求波动较大,导致生产计划调整频繁,影响稼动率。
三、年度稼动率分析1. 总体情况在过去的一年里,我国企业稼动率总体呈现以下特点:(1)稼动率水平有所提高:与上一年度相比,企业稼动率平均水平有所上升。
(2)行业间差异明显:不同行业稼动率水平存在较大差异,制造业、电子行业等高技术产业稼动率较高,而传统行业稼动率较低。
(3)区域分布不均衡:东部沿海地区企业稼动率普遍较高,中西部地区企业稼动率相对较低。
2. 具体分析(1)设备维护方面在过去的一年里,企业对设备维护的重视程度有所提高,设备故障率有所下降,但仍有部分企业设备维护工作不到位,导致稼动率降低。
(2)生产计划方面部分企业生产计划不合理,导致设备闲置或过度使用,影响稼动率。
此外,市场需求波动较大,导致生产计划调整频繁,对稼动率产生一定影响。
(3)人员操作方面企业对操作人员的培训力度有所加强,操作人员技能水平有所提高,但仍有个别企业操作人员技能水平不高,导致设备故障,影响稼动率。
稼动率的概念与计算
稼动率的概念与计算稼动率是生产线、设备或工人工作时间实际产出与可用工作时间之比,用来衡量生产资源利用率的指标。
它可以帮助企业评估生产效率,发现潜在的浪费和低效环节,并对生产计划进行调整和优化。
稼动率的计算方法包括两个要素:生产时间和产出时间。
生产时间是指设备或人力在指定时间段内的实际工作时间,产出时间是指在生产时间内,实际产生产品的时间。
稼动率计算的公式为:稼动率=(产出时间/生产时间)×100%以下是一种加强版的稼动率计算方法,通过引入更多细分指标来更全面地评估生产资源的利用情况:1.总稼动率:该指标反映了整个生产过程中所有资源的综合利用情况。
计算方法为:总稼动率=(总产出时间/总生产时间)×100%。
总生产时间是指生产线或工作站累计的工作时间,总产出时间是指所有产品在生产线上实际产生的时间。
2.单机稼动率:该指标用于评估单个设备或工作站的利用率。
计算方法为:单机稼动率=(设备产出时间/设备工作时间)×100%。
设备工作时间是指设备在生产线上累计的工作时间,设备产出时间是指设备在工作时间内实际产生产品的时间。
3.单人稼动率:该指标用于评估每个工人的利用率。
计算方法为:单人稼动率=(工人产出时间/工人工作时间)×100%。
工人工作时间是指工人在生产线上累计的工作时间,工人产出时间是指工人在工作时间内实际产生产品的时间。
4.指定时间段稼动率:该指标用于评估一些特定时间段内的生产资源利用状况。
计算方法为:指定时间段稼动率=(指定时间段产出时间/指定时间段生产时间)×100%。
指定时间段生产时间是指在指定的时间段内,生产线或工作站的累计工作时间,指定时间段产出时间是指在该时间段内实际产生产品的时间。
这些细分指标可以提供更详细的信息,帮助企业发现生产线或设备的短板,进一步分析产能利用率的问题,并对生产计划进行调整和优化。
同时,稼动率还可以与其他生产绩效指标(如良品率、生产效率等)相结合,为企业提供全面的生产管理数据,促进生产过程的改进和效率提升。
- 1、下载文档前请自行甄别文档内容的完整性,平台不提供额外的编辑、内容补充、找答案等附加服务。
- 2、"仅部分预览"的文档,不可在线预览部分如存在完整性等问题,可反馈申请退款(可完整预览的文档不适用该条件!)。
- 3、如文档侵犯您的权益,请联系客服反馈,我们会尽快为您处理(人工客服工作时间:9:00-18:30)。
整线设备稼动率与节拍分析
【摘要】稼动率和节拍是设备管理中的重要参数,稼动率越高,节拍越小,单位时间产能越大。
一般谈论稼动率和节拍都是针对特定设备,能不能整线考虑呢?本文着重介绍了稼动率与节拍定义、稼动率与节拍局限性、稼动率与节拍引申,讨论及具体的实施方法。
【关键词】稼动率;节拍;CIM;抗挠动;INTER-FACE;CF
引言
一般谈论稼动率和节拍都是针对特定设备,能不能整线考虑呢?由此引发怎样对整条生产线快速方便进行设备稼动率与生产节拍统计的思考。
一、稼动率与节拍定义
稼动率是指相对于生产时间,实际生产产品的时间所占的比率。
是以机器设备的稼动时间除以最大负荷时间而得。
另外,如果设备实际产出单位产量所需的时间(以下简称实际节拍)>设备设计产出单位产量所需的时间(以下简称设计节拍),即使稼动率提高,规定时间内并不一定能生产出足够产品,反之亦然。
提升稼动率与降低实际节拍必不可少。
二、稼动率与节拍局限性
如果整线考虑稼动率与节拍,就会发现存在着以下问题:
(1)以前我们讨论稼动率与生产节拍缺少整线设备的考虑,即使考虑也是各单台机台稼动统计汇总数据,这些数据体现不出自动化生产线的抗挠动能力,对整线产能提升缺乏指导意义。
(2)整线设备并不一定由同一厂家生产,设备重要程度不同,发生问题频度与解决问题的耗时不同也即不同设备稼动率与节拍要求不一定相同。
(3)同一时间段有一台以上设备出故障,按单台基准统计整线稼动率不能准确反映实际状况。
实际生产特别是产能提升阶段这种情况很普遍。
(4)如果以单台设备稼动率与节拍分析整线数据,就要统计各单台设备数据,还要监控整线机台是否在相同时间重叠停机(泛指宕机,待机,停机等不运转状态,下同),还要考虑到整线的抗挠动能力。
以上要耗费较多人力。
三、稼动率与节拍引申,讨论
自动化生产线生产中产品一件接一件向下游流动,我们可以将整线看作一台
大设备组针对整条生产线进行数据分析,下面以CF黄光制程BM线举例介绍。
如图1所示,产品经由以下设备(A→B→C→D→E→F→G→H→I→J→K→L→M→N→A)的顺序流动,这样就可以以设备A的出片即设备B的入片间隔看作生产线节拍,如果下游设备任何一台有停机,因软体设备间INTER-FACE信号作用,上游设备也会相应停机,信号一直向上游传递到设备A,这时设备A发出下游投入禁止信号,当下游故障机台回复且将产线内部缓存清理到一定水位时设备A下游投入禁止信号解除,继续流片。
整线合理设置缓存BUF,如果时间较短或产线缓存BUF水位设置得当,停机设备复机后产线继续流动时停机信号还没有传递到设备A就已经内部消化掉,这样就不会影响整线的流动-这就是自动生产线抗挠动能力。
根据以上,以CF黄光制程BM线为例,选定时间段统计分析:如图2所示。
1.图2是CF黄光制程BM线设备B一天的入片节拍,这里因为设计节拍为35S,且产线已经基本正常,故以50秒作为节拍分界点,节拍50秒以内(含50秒)算生产线正常,超过50秒算异常。
2.对比设计节拍(这里为35S),实际节拍会大小不一,且没有规律,但正常情况下实际节拍<2倍设计节拍(70S),大多节拍会靠近设计节拍(如图2所示),我们以2倍设计节拍作为下游设备不在运转状态与正常运转节拍生产的分界点(根据实际情况可灵活设定)。
所以选定时间段的生产时间就是<2倍设计节拍生产物品所耗用的时间总和。
3.选定时间段中黄光制程BM线设备B第一枚入片时间与最后一枚入片时间间隔作为稼动时间。
4.这样整线稼动率={<2倍设计节拍生产产品所耗用的时间总和/设备B第一枚入片时间与最后一枚入片时间间隔。
}
5.实际生产节拍={<2倍设计节拍生产物品所耗用的时间总和/此段时间生产的产品数}
综合以上,要提高产能需进行以下:
(1)减少下游设备停机时间:整线分析下游设备A下游投入限制报警的时间总和。
根据设备A下游投入限制报警时间节点,可以方便查找到下游影响产量的机台,针对性处理。
(2)没有导致设备A下游投入限制报警的下游设备报警不会影响稼动率,所以要合理安排缓存BUF的上下调剂水位,增强产线抗扰动能力。
(3)优化各单台设备动作与上下游INTERFACE信号,减少设备单台节拍进而减小实际生产节拍。
四、具体实施方法
(1)在自动化生产线上有针对性选择单台机台做为整线替代研究对象。
一般选择入口或出口处的连线机台。
(2)统计所选机台入口处产品投入间隔,一般机台PLC都有记录功能,但存储空间不大,这需要我们通过软件处理到PC端。
(3)PLC软件增加所选机台下游投入限制(选择入口机台)或上游待料(选择出口机台)警告,产线不能按设定节拍(在1倍和2倍设计节拍之间)生产时发出警告并可节拍恢复后自动解除,同2)项所述,也需要将记录数据处理到PC 端。
(4)统计下游游投入限制或上游待料发生时间及耗时时间。
(5)由2)项取得的数据大小不一,无规律,但大部分靠近整线设计节拍值。
以CF黄光制程BM线为例(图2):整线节拍=(29*3+30*3+31*3+32*6+33*13+34*240+35*939+36*319+37*144+38*129+39*8 9+40*61+41*54+42*16+43*16+44*4+45*3+46*3+47*6+48*1+49*1+50*4)/(3+3+3+6+13+240+939+319+144+129+89+61+54+16+16+4+3+3+6+1+1+4)=36秒。
(6)以CF黄光制程BM线为例:因为生产线连续运转,设备运转总时间=1天=86400秒。
所以BM线稼动率(图2)=(29*3+30*3+31*3+32*6+33*13+34*240+35*939+36*319+37*144+38*129+39*8 9+40*61+41*54+42*16+43*16+44*4+45*3+46*3+47*6+48*1+49*1+50*4)*100/86400=86.13%。
(7)稼动率的损失主要是下游游投入限制或上游待料警告的耗时,根据警告发生时间和时长匹配到具体的单台设备,转换为单台设备分析。
(8)归纳整理整线稼动率与节拍及影响因素,方法很多。
本公司以CIM系统表格形式输出如图3所示。
步骤:设定开始时间点→设定结束时间→点设定节拍分界点→选择线体→选择整线替代机台→选择警告产生机台→按“Search”生成所需表格。
五、结语
以上讨论与实例分析可知:整线分析稼动率与节拍完全可行。
适用范围也非常广泛;实现方法多样,方便,成本低廉。