设备稼动率
设备稼动率

一)设备稼动率:二) 1.(最大操作时间):指的是设备可用的最大时间,若设备本身为?S内自?,且可完全由?S内自主使用,则最大操作时间一般为日历时间。
EW C 5?plb2.(负荷时间):则为设备可稼动的时间,乃是(最大操作时间)扣除停机(Shutdown,SD)损失,停机损失乃是计划上的休止时间,如休假、教育训练、保养等。
X A ^7M3.(稼动时间):则是(负荷时间) - (停线时间),而停线时间包括批次转换及制程?常、设备?常停止及修?蜁r间。
D,VPfN6\*O由以上的定义,即可算出最常用的稼动率定义—设备稼动率(也称为时间稼动率),其公式为-!.\|-4`设备稼动率= 稼动时间∕负荷时间n] ?I- R(二)性能稼动率∕?质稼动率∕速度稼动率}O jS:a1时间稼动率?K无法完全表现设备对生产的贡献程度:例如,相同的设备,相等的稼动时间,可能因效率的不同,而有不同的产能,此?效率降低的损失则称为性能损失。
在此定义速度稼动率如下:K $ L+ K:速度稼动率=基准周期时间∕?际周期时间V9Qed |[gd其中,[MBBgsapC!基准周期时间:设备原设计产出单位产量所需的时间。
z -QG 02际周期时间:目前设备?际产出单位产量所需的时间。
?K定义?质稼动率与性能稼动率如下:,] $ Z _T'质嫁动率= 生产量* ?际周期时间∕稼动时间G7p V>性能稼动率= 速度稼动率* ?质稼动率R5?G# 0性能稼动时间= 稼动时间* 性能稼动率= 稼动时间- 性能损失时间&yA n<y]F其中性能损失包括速度低落的损失与短暂停机的损失。
由以上定义可知,若性能稼动率变小,则可判定生产相关设备的效率降低。
{)& n7-Y/](三)价值嫁动时间与设备总合效率 #4Cok< C性能稼动时间表示设备产出产品的时间,但无法表示设备产出良率的好坏,因此定义「价值稼动时间」?肀硎菊嬲?墚a出良品的有价值时间,其定义如下:K9D,U8r价值稼动时间= 性能稼动时间* 良品率c84-TQ而设备的有效使用程度则以「设备总合效率」?砼卸ǎ?涠x如下:V f L b!设备总合效率= 时间稼动率* 性能稼动率* 良品率(一)想办法缩短换线时间,如果你的产品属于多产品少批量的话.换线时间将成为影响稼动率的杀手.1.提前备料,如果是Panasert及Fuji这类转塔式的机器的话,你可以在另一个Feeder Bank先装料.2.换线前技术人员需把下一个产品的程序先准备好.3.换线时人员的分配,如果一条线多机的话,每台机最好有一个技术人员.{ \ G] &((二)生产过程中,提前备料尤为重要.作业人员要主动查看哪些材料快用完了,要提前把料上到备用的Feeder上,当停机时马上把用完料的Feeder取下,把上好料的Feeder换上.如果是长批量的产品,而你的料又不多于一个Feeder Bank的Slot数的话,最好两个Feeder Bank上都放同样的料,把机器设置为自动切换模式,缺料时,机器会自动切换到另一个Feeder Bank,然后作业换料,不影响停机时间. OZRu B0e i(三)管理,分为现场作业员管理和设备管理.这就见仁见智了/在生产过程中,大家如何去优化生产线呢?也许各有各的招,各有各的办法,是否大家可以拿出来和大家分享一下,这里是小弟的一点资料,以求更多良策良方。
自动化设备的稼动率与可动率

自动化设备的稼动率与可动率一、稼动率的定义与计算方法稼动率是指设备在一定时间内正常运行的时间占总运行时间的比例,是衡量设备利用率的重要指标。
稼动率的计算公式如下:稼动率 = (设备正常运行时间 / 总运行时间) × 100%其中,设备正常运行时间是指设备在工作状态下的运行时间,不包括停机、维护、换模等非工作时间;总运行时间是指设备在一定时间段内的总运行时间。
二、可动率的定义与计算方法可动率是指设备在一定时间内能够正常运行的时间占总运行时间的比例,是衡量设备可靠性的指标。
可动率的计算公式如下:可动率 = (设备正常运行时间 / 总运行时间) × 100%与稼动率不同的是,可动率不考虑设备的非工作时间,只关注设备在工作状态下的运行时间。
三、稼动率与可动率的关系稼动率和可动率都是衡量设备利用率和可靠性的指标,但是两者的计算方法不同。
稼动率考虑了设备的非工作时间,更加综合地反映了设备的利用率;而可动率只关注设备在工作状态下的运行时间,更加专注地反映了设备的可靠性。
稼动率和可动率之间存在一定的关系,通常情况下,稼动率高的设备可动率也较高,说明设备运行稳定、可靠。
但是,稼动率高并不意味着可动率一定高,因为稼动率还受到非工作时间的影响,而可动率只关注设备在工作状态下的运行时间。
四、提高稼动率和可动率的方法1. 定期维护保养:定期对设备进行维护保养,及时发现并修复设备故障,减少设备的停机时间,提高可动率。
2. 优化生产计划:合理安排生产计划,避免生产过程中的等待时间和停机时间,提高稼动率和可动率。
3. 培训操作人员:提高操作人员的技能水平,减少操作失误和设备故障,提高稼动率和可动率。
4. 更新设备技术:及时更新设备技术,引进先进的自动化设备,提高设备的可靠性和稼动率。
5. 设备监控和预警系统:安装设备监控和预警系统,实时监测设备运行状态,及时发现并解决问题,提高稼动率和可动率。
充分利用上述方法可以有效提高自动化设备的稼动率和可动率,提高生产效率和设备利用率,降低生产成本,提升企业竞争力。
设备稼动率的计算公式举例
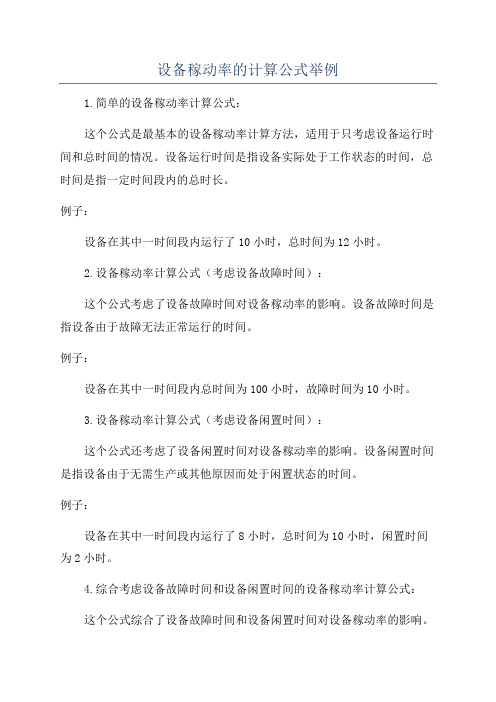
设备稼动率的计算公式举例
1.简单的设备稼动率计算公式:
这个公式是最基本的设备稼动率计算方法,适用于只考虑设备运行时间和总时间的情况。
设备运行时间是指设备实际处于工作状态的时间,总时间是指一定时间段内的总时长。
例子:
设备在其中一时间段内运行了10小时,总时间为12小时。
2.设备稼动率计算公式(考虑设备故障时间):
这个公式考虑了设备故障时间对设备稼动率的影响。
设备故障时间是指设备由于故障无法正常运行的时间。
例子:
设备在其中一时间段内总时间为100小时,故障时间为10小时。
3.设备稼动率计算公式(考虑设备闲置时间):
这个公式还考虑了设备闲置时间对设备稼动率的影响。
设备闲置时间是指设备由于无需生产或其他原因而处于闲置状态的时间。
例子:
设备在其中一时间段内运行了8小时,总时间为10小时,闲置时间为2小时。
4.综合考虑设备故障时间和设备闲置时间的设备稼动率计算公式:
这个公式综合了设备故障时间和设备闲置时间对设备稼动率的影响。
例子:
设备在其中一时间段内运行了7小时,总时间为10小时,故障时间为1小时,闲置时间为1小时。
需要注意的是,设备稼动率只是一个衡量设备利用率的指标,不能单独判断设备的运行效率,还需要结合其他指标进行综合分析。
此外,稼动率的计算公式可根据具体情况进行调整和扩展,以满足实际需求。
设备稼动率
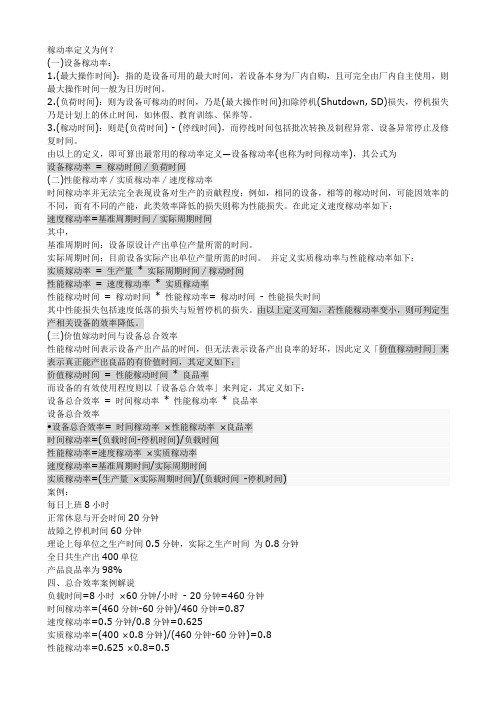
稼动率定义为何?(一)设备稼动率:1.(最大操作时间):指的是设备可用的最大时间,若设备本身为厂内自购,且可完全由厂内自主使用,则最大操作时间一般为日历时间。
2.(负荷时间):则为设备可稼动的时间,乃是(最大操作时间)扣除停机(Shutdown, SD)损失,停机损失乃是计划上的休止时间,如休假、教育训练、保养等。
3.(稼动时间):则是(负荷时间) - (停线时间),而停线时间包括批次转换及制程异常、设备异常停止及修复时间。
由以上的定义,即可算出最常用的稼动率定义—设备稼动率(也称为时间稼动率),其公式为设备稼动率= 稼动时间∕负荷时间(二)性能稼动率∕实质稼动率∕速度稼动率时间稼动率并无法完全表现设备对生产的贡献程度:例如,相同的设备,相等的稼动时间,可能因效率的不同,而有不同的产能,此类效率降低的损失则称为性能损失。
在此定义速度稼动率如下:速度稼动率=基准周期时间∕实际周期时间其中,基准周期时间:设备原设计产出单位产量所需的时间。
实际周期时间:目前设备实际产出单位产量所需的时间。
并定义实质稼动率与性能稼动率如下:实质嫁动率= 生产量* 实际周期时间∕稼动时间性能稼动率= 速度稼动率* 实质稼动率性能稼动时间= 稼动时间* 性能稼动率= 稼动时间- 性能损失时间其中性能损失包括速度低落的损失与短暂停机的损失。
由以上定义可知,若性能稼动率变小,则可判定生产相关设备的效率降低。
(三)价值嫁动时间与设备总合效率性能稼动时间表示设备产出产品的时间,但无法表示设备产出良率的好坏,因此定义「价值稼动时间」来表示真正能产出良品的有价值时间,其定义如下:价值稼动时间= 性能稼动时间* 良品率而设备的有效使用程度则以「设备总合效率」来判定,其定义如下:设备总合效率= 时间稼动率* 性能稼动率* 良品率设备总合效率•设备总合效率= 时间稼动率×性能稼动率×良品率时间稼动率=(负载时间-停机时间)/负载时间性能稼动率=速度稼动率×实质稼动率速度稼动率=基准周期时间/实际周期时间实质稼动率=(生产量×实际周期时间)/(负载时间-停机时间)案例:每日上班8小时正常休息与开会时间20分钟故障之停机时间60分钟理论上每单位之生产时间0.5分钟,实际之生产时间为0.8分钟全日共生产出400单位产品良品率为98%四、总合效率案例解说负载时间=8小时×60分钟/小时- 20分钟=460分钟时间稼动率=(460分钟-60分钟)/460分钟=0.87速度稼动率=0.5分钟/0.8分钟=0.625实质稼动率=(400 ×0.8分钟)/(460分钟-60分钟)=0.8性能稼动率=0.625 ×0.8=0.5设备总合效率=0.87 ×0.5 ×0.98=42.6%节录自台湾的网站,谢谢你的问题,让我收获良多.......... /微笑设备总合效率•设备总合效率= 时间稼动率×性能稼动率×良品率时间稼动率=(负载时间-停机时间)/负载时间性能稼动率=速度稼动率×实质稼动率速度稼动率=基准周期时间/实际周期时间实质稼动率=(生产量×实际周期时间)/(负载时间-停机时间) 总合效率案例案例:每日上班8小时正常休息与开会时间20分钟故障之停机时间60分钟理论上每单位之生产时间0.5分钟,实际之生产时间为0.8分钟全日共生产出400单位产品良品率为98%四、总合效率案例解说负载时间=8小时×60分钟/小时- 20分钟=460分钟时间稼动率=(460分钟-60分钟)/460分钟=0.87速度稼动率=0.5分钟/0.8分钟=0.625实质稼动率=(400 ×0.8分钟)/(460分钟-60分钟)=0.8性能稼动率=0.625 ×0.8=0.5设备总合效率=0.87 ×0.5 ×0.98=42.6%。
自动化设备的稼动率与可动率
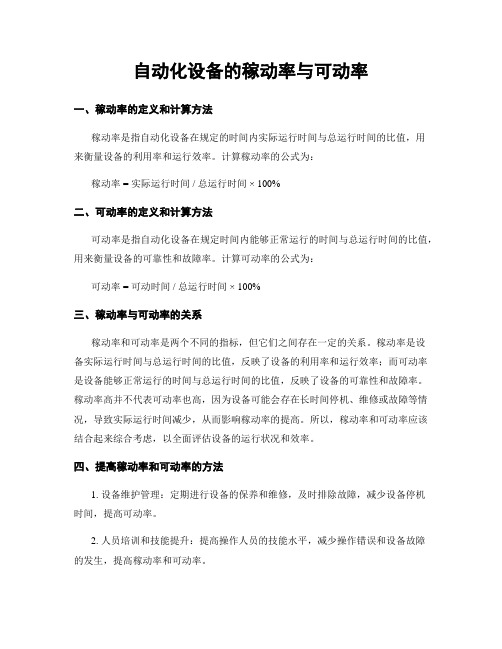
自动化设备的稼动率与可动率一、稼动率的定义和计算方法稼动率是指自动化设备在规定的时间内实际运行时间与总运行时间的比值,用来衡量设备的利用率和运行效率。
计算稼动率的公式为:稼动率 = 实际运行时间 / 总运行时间 × 100%二、可动率的定义和计算方法可动率是指自动化设备在规定时间内能够正常运行的时间与总运行时间的比值,用来衡量设备的可靠性和故障率。
计算可动率的公式为:可动率 = 可动时间 / 总运行时间 × 100%三、稼动率与可动率的关系稼动率和可动率是两个不同的指标,但它们之间存在一定的关系。
稼动率是设备实际运行时间与总运行时间的比值,反映了设备的利用率和运行效率;而可动率是设备能够正常运行的时间与总运行时间的比值,反映了设备的可靠性和故障率。
稼动率高并不代表可动率也高,因为设备可能会存在长时间停机、维修或故障等情况,导致实际运行时间减少,从而影响稼动率的提高。
所以,稼动率和可动率应该结合起来综合考虑,以全面评估设备的运行状况和效率。
四、提高稼动率和可动率的方法1. 设备维护管理:定期进行设备的保养和维修,及时排除故障,减少设备停机时间,提高可动率。
2. 人员培训和技能提升:提高操作人员的技能水平,减少操作错误和设备故障的发生,提高稼动率和可动率。
3. 设备改进与升级:根据设备的实际情况,进行设备改进和升级,提高设备的可靠性和运行效率。
4. 数据分析与优化:通过对设备运行数据的分析,找出设备运行中存在的问题和瓶颈,进行优化和改进,提高稼动率和可动率。
5. 预防性维护:采取预防性维护措施,提前检测和排除潜在故障,减少设备的故障率和停机时间,提高可动率。
6. 设备备件管理:合理管理设备备件,确保备件的及时供应和更换,减少设备故障对稼动率和可动率的影响。
五、案例分析以某生产企业的自动化生产线为例,该生产线总运行时间为720小时,实际运行时间为600小时,可动时间为650小时。
根据上述定义和计算方法,可以得出以下结果:稼动率 = 600小时 / 720小时 × 100% = 83.33%可动率 = 650小时 / 720小时 × 100% = 90.28%根据计算结果可知,该生产线的稼动率为83.33%,说明设备的利用率和运行效率较高;可动率为90.28%,说明设备的可靠性和故障率较低。
稼动率 讲解

设备嫁动率=设备运行时间/工作时间*100%运行时间为设备开机时间工作时间为上班的时间。
比如SMT一班为12小时,因维修停了1小时,则设备嫁动率=11/12*100%=91。
7%。
稼动率是一个重要的指标,论坛上虽已类似的帖子,但因部分段落字体损坏而影响了对全文的理解,这里再重发一贴。
如果您被问到“我们部门的稼动率为90%,你们厂里是多少?”,您可知道其所谓的稼动率定义为何?90%这数字代表的是好?是坏呢?基本上稼动率有数种不同的定义,在此略加解释:1、时间稼动率首先定义最大操作时间,指的是设备可用的最大时间,若设备本身为厂内自购,且可完全由厂内自主使用,则最大操作时间一般为日历时间;而负荷时间则为设备可稼动的时间,乃是最大操作时间扣除停机(Shutdown,SD)损失,停机损失乃是计画上的休止时间,如休假、教育训练、保养等。
而稼动时间则是负荷时间扣除停止时间,而停止时间包括批次转换及制程异常、设备异常停止及修复时间。
最大操作时间:设备可用的最大时间负荷时间:最大操作时间扣除停机(Shutdown, SD)损失;停机(Shutdown, SD)损失:计画上的休止时间,如休假、教育训练、保养等稼动时间:负荷时间扣除停止时间停止时间:包括批次转换及制程异常、设备异常停止及修复时间。
由以上的定义,即可算出最常用的稼动率定义-设备稼动率(也称为时间稼动率),其公式为时间稼动率=稼动时间/ 负荷时间目的:减少停止时间!通过资源整合,管理优化,进行资源充分利用,降低成本,提高效率。
2、性能稼动率/实质稼动率/速度稼动率时间稼动率并无法完全表现设备对生产的贡献程度;例如,相同的设备,相等的稼动时间,可能因效率的不同,而有不同的产能,此类效率降低的损失则称为性能损失。
在此定义速度稼动率如下:速度稼动率=基准周期时间/ 实际周期时间其中,基准周期时间:设备原设计产出单位产量所需的时间。
实际周期时间:目前设备实际产出单位产量所需的时间。
自动化设备的稼动率与可动率
自动化设备的稼动率与可动率引言概述:自动化设备在现代工业生产中起着至关重要的作用,其稼动率和可动率是评估设备运行效率和性能的重要指标。
稼动率是指设备实际运行时间与计划运行时间的比值,反映了设备的利用率;可动率是指设备在正常工作条件下能够正常运行的时间与总运行时间的比值,反映了设备的可靠性和稳定性。
本文将分析自动化设备的稼动率与可动率之间的关系,并探讨如何提高设备的稼动率和可动率。
一、稼动率与可动率的定义及关系1.1 稼动率的定义:稼动率是指设备实际运行时间与计划运行时间的比值,通常以百分比表示。
1.2 可动率的定义:可动率是指设备在正常工作条件下能够正常运行的时间与总运行时间的比值,通常以百分比表示。
1.3 关系分析:稼动率和可动率是相互关联的,稼动率的提高通常伴随着可动率的提高,反之亦然。
稼动率高意味着设备的利用率高,可动率高意味着设备的可靠性和稳定性高,两者相辅相成。
二、影响稼动率和可动率的因素2.1 设备质量:设备质量直接影响设备的可动率,优质的设备更加稳定可靠,从而提高可动率。
2.2 维护保养:定期维护保养可以有效提高设备的稼动率和可动率,减少设备故障和停机时间。
2.3 操作管理:科学的操作管理可以提高设备的稼动率和可动率,减少人为因素对设备性能的影响。
三、提高稼动率和可动率的方法3.1 定期维护保养:定期对设备进行维护保养,及时发现和处理设备故障,提高设备的可动率。
3.2 优化生产计划:合理安排生产计划,减少设备的闲置时间,提高设备的稼动率。
3.3 培训操作人员:对操作人员进行培训,提高其操作技能和意识,减少操作失误,提高设备的稼动率和可动率。
四、案例分析:提高稼动率和可动率的成功经验4.1 公司A采取定期维护保养措施,成功提高了设备的可动率,减少了设备故障和停机时间。
4.2 公司B优化了生产计划,有效减少了设备的闲置时间,提高了设备的稼动率。
4.3 公司C注重培训操作人员,提高了操作人员的技能和意识,减少了操作失误,提高了设备的稼动率和可动率。
设备稼动率计算公式
设备稼动率计算公式
设备稼动率计算是企业监控设备效率的一种重要指标,也是企业生产效率的重要参考指标。
它是指设备在运行时间内实际生产产品的数量与其理论可生产的产品数量的比值,是衡量设备运行效率的一个指标。
设备稼动率的计算公式为:设备稼动率 = 实际产量/理论产量
实际产量是指在一定时间内,设备实际运行的时间内,完成的产品数量;而理论产量是指在特定的时间内,设备理论上可以完成的产品数量。
设备稼动率的计算要求企业把握时间,因此,企业在处理设备稼动率时,应注意时间管理,做好设备运行时间的安排和调度,充分发挥设备的最大运行效率,以提高设备稼动率。
此外,企业在提高设备稼动率时,还应该加强设备的维护和保养,保证,设备的健康运行,以降低设备的故障率,提高设备的运行效率,从而提高设备稼动率。
此外,企业还应加强对设备的技术培训,确保设备操作人员的技能,充分发挥设备的性能,从而提高设备稼动率。
通过以上措施,企业可以有效提高设备稼动率,有效提高企业的生
产效率,实现企业的可持续发展。
自动化设备的稼动率与可动率
自动化设备的稼动率与可动率自动化设备的稼动率与可动率是衡量设备运行效率和生产能力的重要指标。
稼动率是指设备在一定时间内运行的时间与总时间的比值,可动率是指设备在一定时间内能够正常运行的时间与总时间的比值。
本文将详细介绍自动化设备的稼动率与可动率的定义、计算方法以及影响因素。
一、稼动率和可动率的定义和计算方法1. 稼动率的定义和计算方法稼动率是指设备在一定时间内实际运行的时间与总时间的比值,通常以百分比表示。
稼动率的计算公式如下:稼动率 = (设备运行时间 / 总时间) × 100%其中,设备运行时间是指设备正常运行的时间,不包括停机、维修和故障等非运行时间;总时间是指设备应该运行的总时间,包括设备运行时间和非运行时间。
2. 可动率的定义和计算方法可动率是指设备在一定时间内能够正常运行的时间与总时间的比值,通常以百分比表示。
可动率的计算公式如下:可动率 = (设备正常运行时间 / 总时间) × 100%其中,设备正常运行时间是指设备在一定时间内没有发生停机、维修和故障等非正常运行情况的时间;总时间是指设备应该运行的总时间,包括设备正常运行时间和非正常运行时间。
二、影响稼动率和可动率的因素1. 设备故障率和维修时间设备故障率是指设备在一定时间内发生故障的频率,维修时间是指修复设备故障所需的时间。
设备故障率高、维修时间长会导致设备的非正常运行时间增加,从而降低稼动率和可动率。
2. 生产计划和调度安排合理的生产计划和调度安排可以避免设备闲置和过载运行的情况,提高设备的稼动率和可动率。
同时,合理的停机维护计划可以减少设备的非正常运行时间,提高可动率。
3. 设备质量和性能设备质量和性能直接影响设备的稳定性和可靠性。
高质量、高性能的设备更容易保持正常运行状态,降低故障率和维修时间,提高稼动率和可动率。
4. 操作人员的技能和管理水平操作人员的技能和管理水平对设备的运行效率和稳定性有重要影响。
自动化设备的稼动率与可动率
自动化设备的稼动率与可动率一、引言自动化设备的稼动率与可动率是衡量设备运行效率和生产能力的重要指标。
稼动率指设备实际运行时间与总运行时间之比,反映了设备的利用率和运行效率;可动率指设备实际运行时间与理论运行时间之比,反映了设备的可靠性和可用性。
本文将详细介绍自动化设备的稼动率与可动率的计算方法和影响因素,并提出一些提高稼动率与可动率的措施。
二、自动化设备的稼动率计算方法稼动率的计算公式为:稼动率 = (设备实际运行时间 / 总运行时间) × 100%其中,设备实际运行时间指设备正常运行的时间,不包括停机维修、待料等非生产时间;总运行时间指设备应该运行的总时间,包括生产时间和非生产时间。
三、自动化设备的可动率计算方法可动率的计算公式为:可动率 = (设备实际运行时间 / 理论运行时间) × 100%其中,理论运行时间指设备在正常运行情况下应该运行的时间,不包括停机维修、待料等非生产时间。
四、影响自动化设备稼动率与可动率的因素1. 设备故障:设备故障会导致停机维修时间增加,降低稼动率与可动率。
2. 人为因素:操作不当、维护不及时等人为因素也会对稼动率与可动率产生负面影响。
3. 原材料供应:原材料供应不及时或者质量不稳定会导致设备停机待料,降低稼动率与可动率。
4. 生产计划安排:合理的生产计划安排可以最大程度地提高设备的稼动率与可动率。
五、提高自动化设备稼动率与可动率的措施1. 加强设备维护:定期进行设备维护保养,提高设备的可靠性和稳定性,减少故障发生的可能性。
2. 培训操作人员:加强对操作人员的培训,提高其操作技能和维护意识,减少人为因素对设备稼动率与可动率的影响。
3. 优化供应链管理:与供应商建立良好的合作关系,确保原材料供应的稳定性和及时性。
4. 制定合理的生产计划:根据市场需求和设备运行情况,制定合理的生产计划,避免产能过剩或者产能不足的情况发生。
六、结论自动化设备的稼动率与可动率是衡量设备运行效率和生产能力的重要指标。
- 1、下载文档前请自行甄别文档内容的完整性,平台不提供额外的编辑、内容补充、找答案等附加服务。
- 2、"仅部分预览"的文档,不可在线预览部分如存在完整性等问题,可反馈申请退款(可完整预览的文档不适用该条件!)。
- 3、如文档侵犯您的权益,请联系客服反馈,我们会尽快为您处理(人工客服工作时间:9:00-18:30)。
质量 1%
工艺 5%
四月份
研发 生产部
物控 4%
2%
9%
设备 46%
模具 33%
设备 模具 工艺 质量
研发
五月份
2%
生产部 质量 物控 2%
5% 0%
采购部 1%
工艺 24%
设备 31%
模具 35%
设备 模具 工艺 质量
物控 3%
质量 2%
生 六月份 研发 产 0% 部 采购部
4% 4%
其他 2%
工艺 7%
100.0% 90.0% 80.0%
70.0% 60.0% 50.0% 40.0% 30.0%
20.0% 10.0% 0.0%
? 本次课题症结:吸塑机链条、 U壳皮带线、门发地环线链条、 箱发夹具减速机
6
活动目标
根据现状调查结果设定活动目标:
活动目标:四大设备7月份设备停机 时间减少30%,即4850分钟
设备 47%
模具 31%
经小组成员共同讨论选定课题:如何做好设备预防检修
4
现状调查
1.11年4-6月份
根据上述图表分析,得出要提高公司设备的稼动率重点解决解决吸塑、U壳、门发 箱发的设备停机时间。
5
现状调查
2、进一步解析
设备停机时间分析柏拉图
700 600 500 400 300 200 100
7
预期效益
预计活动后,单台设备平均稼动率可达到95%以上。
创维“质量先锋”QC小组成果展示
8
谢谢 合作 !
小组介绍
小 组 名 :“ 步步高” QC小组
成立日期:2011.7.1
小组类型:效率提升型
注册日期: 2011.7.1
注册编号:
活动期间:
活动次数:
出勤率:
活动课题:提高设备稼动率
1
小组介绍
组长:黄如 职责:统筹所有 设备预防检修
组员:张有定 职务:设备维修
组员:肖章斌 职务:设备维修
小组人员合照
0
箱发B2#减速器U壳坏皮带门断发三工链条位断链U条壳故折障U大 26工臂位 四断工链门位条 发断 下七模工维位修抓U紧 壳 三销 上 工坏 料 位机 定台 位断 汽 四缸 工箱故 位发障 链9条0度工故箱转位障发盘模小故温车障机链,条真松空2动6泵工故位箱障小发车压门脱发合轨2机6故工障位枪头箱坏箱发发皮流带水坏线故障 三
组员:夏春晓 职务:设备维修
组员:郭国鹏 职务:设备维修
2ቤተ መጻሕፍቲ ባይዱ
小组介绍
序号 姓名
性别
文化 程度
所学专业
公司职务
小组分工
1 黄如
男 中技
钳工
设备主管
组长
2 张有定 男 高中
电工
电工
组员
3 肖章斌 男 高中
电工
维修工程师
组员
4 夏春晓 男 高中 机械维修
维修工
组员
5 郭国鹏 男 大专 机电一体化 实习生
组员
3
选题理由
11年4-6月份实际情况
1、设备预防检修不到位,重复发生的故障较多。 2、全员参与设备预防检修能力实施不到位。 3、四、五、六月份设备停机总时间分别为6197分钟、6712分钟、6925分钟,
停机时间长。 4、四、五、六月份设备停机影响生产时间占总停机时间的比例分别为46%、31%
47%,影响比重较大。