中冶赛迪转底炉回收工艺助力钢企绿色发展
钢铁冶炼废弃物处理的新技术
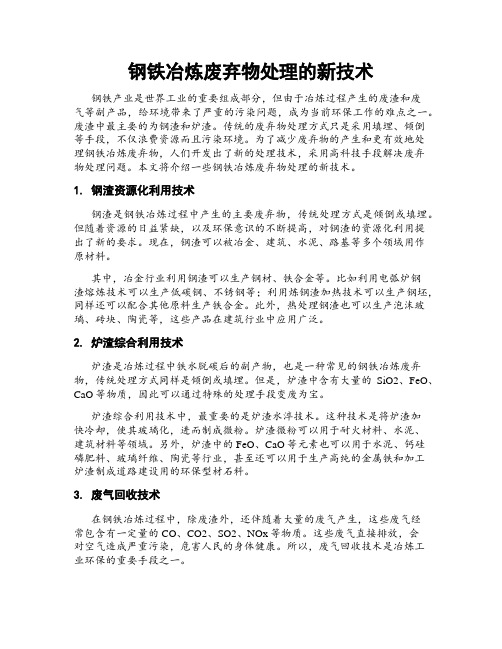
钢铁冶炼废弃物处理的新技术钢铁产业是世界工业的重要组成部分,但由于冶炼过程产生的废渣和废气等副产品,给环境带来了严重的污染问题,成为当前环保工作的难点之一。
废渣中最主要的为钢渣和炉渣。
传统的废弃物处理方式只是采用填埋、倾倒等手段,不仅浪费资源而且污染环境。
为了减少废弃物的产生和更有效地处理钢铁冶炼废弃物,人们开发出了新的处理技术,采用高科技手段解决废弃物处理问题。
本文将介绍一些钢铁冶炼废弃物处理的新技术。
1. 钢渣资源化利用技术钢渣是钢铁冶炼过程中产生的主要废弃物,传统处理方式是倾倒或填埋。
但随着资源的日益紧缺,以及环保意识的不断提高,对钢渣的资源化利用提出了新的要求。
现在,钢渣可以被冶金、建筑、水泥、路基等多个领域用作原材料。
其中,冶金行业利用钢渣可以生产钢材、铁合金等。
比如利用电弧炉钢渣熔炼技术可以生产低碳钢、不锈钢等;利用炼钢渣加热技术可以生产钢坯,同样还可以配合其他原料生产铁合金。
此外,热处理钢渣也可以生产泡沫玻璃、砖块、陶瓷等,这些产品在建筑行业中应用广泛。
2. 炉渣综合利用技术炉渣是冶炼过程中铁水脱碳后的副产物,也是一种常见的钢铁冶炼废弃物,传统处理方式同样是倾倒或填埋。
但是,炉渣中含有大量的SiO2、FeO、CaO等物质,因此可以通过特殊的处理手段变废为宝。
炉渣综合利用技术中,最重要的是炉渣水淬技术。
这种技术是将炉渣加快冷却,使其玻璃化,进而制成微粉。
炉渣微粉可以用于耐火材料、水泥、建筑材料等领域。
另外,炉渣中的FeO、CaO等元素也可以用于水泥、钙硅磷肥料、玻璃纤维、陶瓷等行业,甚至还可以用于生产高纯的金属铁和加工炉渣制成道路建设用的环保型材石料。
3. 废气回收技术在钢铁冶炼过程中,除废渣外,还伴随着大量的废气产生,这些废气经常包含有一定量的CO、CO2、SO2、NOx等物质。
这些废气直接排放,会对空气造成严重污染,危害人民的身体健康。
所以,废气回收技术是冶炼工业环保的重要手段之一。
钢铁炉窑协同利用危废有利条件以及转炉冶炼造渣工艺介绍-概述说明以及解释
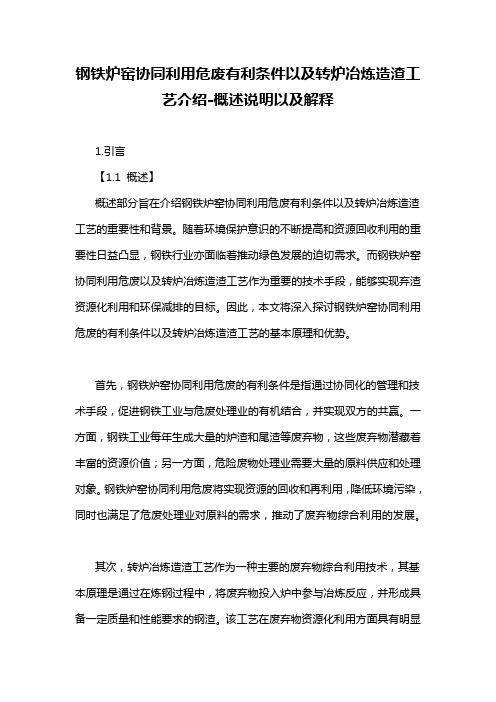
钢铁炉窑协同利用危废有利条件以及转炉冶炼造渣工艺介绍-概述说明以及解释1.引言【1.1 概述】概述部分旨在介绍钢铁炉窑协同利用危废有利条件以及转炉冶炼造渣工艺的重要性和背景。
随着环境保护意识的不断提高和资源回收利用的重要性日益凸显,钢铁行业亦面临着推动绿色发展的迫切需求。
而钢铁炉窑协同利用危废以及转炉冶炼造渣工艺作为重要的技术手段,能够实现弃渣资源化利用和环保减排的目标。
因此,本文将深入探讨钢铁炉窑协同利用危废的有利条件以及转炉冶炼造渣工艺的基本原理和优势。
首先,钢铁炉窑协同利用危废的有利条件是指通过协同化的管理和技术手段,促进钢铁工业与危废处理业的有机结合,并实现双方的共赢。
一方面,钢铁工业每年生成大量的炉渣和尾渣等废弃物,这些废弃物潜藏着丰富的资源价值;另一方面,危险废物处理业需要大量的原料供应和处理对象。
钢铁炉窑协同利用危废将实现资源的回收和再利用,降低环境污染,同时也满足了危废处理业对原料的需求,推动了废弃物综合利用的发展。
其次,转炉冶炼造渣工艺作为一种主要的废弃物综合利用技术,其基本原理是通过在炼钢过程中,将废弃物投入炉中参与冶炼反应,并形成具备一定质量和性能要求的钢渣。
该工艺在废弃物资源化利用方面具有明显的优势。
首先,转炉冶炼造渣工艺能够有效降低工业废弃物的排放,减少环境污染。
其次,该工艺可提高炼钢过程的热效率,节约能源和原料,降低生产成本。
此外,通过合理选择废弃物的投入量和掺入时间,还可以改善钢渣的化学成分和物理性能,提高冶炼效果。
综上所述,钢铁炉窑协同利用危废的有利条件以及转炉冶炼造渣工艺是实现钢铁工业绿色发展和废弃物综合利用的重要手段。
本文将深入研究该工艺的具体环保减排效益、资源回收利用效果以及其在转炉冶炼中的应用等方面,以期为钢铁行业的可持续发展提供借鉴和参考。
1.2 文章结构本文将从以下两个方面对钢铁炉窑协同利用危废的有利条件以及转炉冶炼造渣工艺进行介绍和探讨。
首先,将详细阐述钢铁炉窑协同利用危废的环保减排效益和资源回收利用方面的优势。
钢铁行业的绿色制造减少碳排放和资源消耗的创新方法

钢铁行业的绿色制造减少碳排放和资源消耗的创新方法随着环境问题的日益凸显,各行业都在积极探索绿色制造的创新方法。
作为一个重要的基础产业,钢铁行业在减少碳排放和资源消耗方面也做出了积极的努力。
本文将探讨钢铁行业在绿色制造方面的创新方法,以减少碳排放和资源消耗,以此为环保事业作出贡献。
1. 利用清洁能源进行钢铁生产传统的钢铁生产过程依赖于高耗能的煤炭和高排放的燃料。
然而,随着清洁能源技术的发展,钢铁企业已经开始采用可再生能源进行生产,例如风能和太阳能等。
不仅可以减少碳排放,还可以降低对传统能源的依赖,从而减少资源消耗。
2. 采用高效节能的制造工艺在钢铁生产的每个环节中,都存在着能够提升能效和减少能耗的创新技术。
例如,在炼铁过程中,引入高温炼铁技术和氧气富氧炉等高效节能的设备,可以减少单位产品的能耗。
此外,使用更加精细化的生产工艺,可以提高资源利用率,减少废料产生,从而降低了资源消耗。
3. 推广循环经济模式循环经济模式在钢铁行业中的推广,可以大幅度减少资源消耗和环境污染。
通过回收废钢和废渣等副产品,进行再生利用和资源回收,可以降低对原材料的需求,减少废弃物的排放。
同时,循环经济模式还可以促进产业链的良性发展,提高钢铁企业的整体竞争力。
4. 加强碳排放管控和减排技术研发钢铁行业是一个碳排放量较大的行业,减少碳排放对于环境保护至关重要。
钢铁企业应加强碳排放管控,制定严格的环保标准,并通过先进的减排技术进行落地实施。
例如,在高炉煤气净化和焦化废气处理过程中,采用高效的脱硫、脱氮和脱硝技术,可以显著减少二氧化碳等温室气体的排放。
5. 推动绿色供应链管理绿色供应链管理是指在产品的整个生命周期中,从供应商到制造商再到消费者,通过合理的物流和运输方式,减少碳排放和资源浪费。
钢铁企业可以与供应商建立密切合作关系,优化供应链,选择能源效率高、环保的原材料供应商,以降低对资源的依赖,减少运输过程中的能耗和碳排放。
总结起来,钢铁行业的绿色制造减少碳排放和资源消耗的创新方法包括利用清洁能源、采用高效节能的工艺、推广循环经济模式、加强碳排放管控和减排技术研发以及推动绿色供应链管理。
钢铁行业如何实现节能减排目标

钢铁行业如何实现节能减排目标钢铁行业作为能源消耗和污染物排放的大户,实现节能减排目标对于可持续发展至关重要。
在全球气候变化的背景下,减少能源消耗和降低污染物排放已经成为钢铁行业面临的紧迫任务。
本文将探讨钢铁行业实现节能减排目标的多种途径和方法。
首先,技术创新是钢铁行业实现节能减排的关键。
先进的生产技术能够显著提高能源利用效率,减少污染物排放。
例如,采用新型的炼铁技术,如COREX 和FINEX 工艺,可以减少焦炭的使用,从而降低能源消耗和二氧化碳排放。
在炼钢环节,推广转炉负能炼钢技术,通过回收转炉煤气和蒸汽等二次能源,实现能源的自给自足甚至向外输出。
此外,电炉炼钢技术的不断改进,如超高功率电炉和直流电炉的应用,能够提高电能利用率,减少电力消耗。
在钢铁生产过程中,余热余能的回收利用也是实现节能减排的重要手段。
高温的高炉煤气、转炉煤气和焦炉煤气可以用于发电,既满足了企业自身的用电需求,又减少了对外部电网的依赖。
同时,高温的钢坯和轧钢过程中产生的余热可以通过余热锅炉回收,用于供暖或生产蒸汽。
对于压力能的回收,如高炉顶压余压发电(TRT)技术,可以将高炉炉顶煤气的压力能转化为电能。
这些余热余能的回收利用不仅降低了能源消耗,还为企业带来了可观的经济效益。
优化能源管理是实现节能减排的重要环节。
钢铁企业应建立完善的能源管理体系,对能源的购入、存储、使用和回收进行全过程监控和管理。
通过能源计量和统计分析,找出能源消耗的重点环节和设备,制定针对性的节能措施。
同时,加强能源调度和优化,合理安排生产计划,避免设备的空转和低负荷运行,提高能源利用的整体效率。
加强原材料的管理也有助于节能减排。
选用优质的铁矿石和煤炭等原材料,可以提高生产效率,降低能源消耗和污染物排放。
此外,提高原材料的利用率,减少废料的产生,也是节约能源和资源的重要途径。
例如,通过优化选矿工艺,提高铁矿石的品位,减少炼铁过程中的渣量;在炼焦过程中,采用配煤技术,提高煤炭的利用效率,降低焦炭的消耗。
转底炉直接还原铜渣回收铁、锌技术

pr o c e s s o f RHF d ir e c t r e d uc t i on a nd g a s m e l i t ng s e pa r a t i on. t h e r e c o ve r y r a io t i s m o r e t h a n 93 %
pi l o t e x pe im e r nt s ho we d t h a t a mo l t e n i r o n wi t h a p u it r y mo r e t ha n 94% ma s s c a n be g a i ne d rom f t he c o p pe r s l a g by
转 底炉 直 接还 原 铜 渣 回收铁 、锌 技 术
曹志成 ,孙体 昌 ,吴道 洪 ,薛 逊 ,刘 占华
( 1 .北京科技大学 金属矿 山高效开采与安全教育部重点实验室 ,北京 1 0 0 0 8 3 ; 2 北京神雾环境 能源科技集 团股份有 限公 司 ,北京 1 0 2 2 0 0 ) 摘 要 :采用转底炉直接还原工艺 ,将铜渣含碳球团在高温条件下直接还原得到金属化球团和高品位氧化锌
z i nc o x i d e d us t c a n be ob t a i n e d f r o m t h e c a r bo n b e a in r g pe l l e t s o f c o p pe r s l a g a t a h i g h t e mpe r a t u r e.The i r on c a n be r e c ov e r e d b y me l in t g o r g r i nd ing /m a g ne t i c s e pa r a t i on me t hod a s a r a w ma t e r i a l f o r s t e e l be a ing t c op pe r .Re s u l t s o f t h e
转底炉处理冶金固废的节能研究与应用
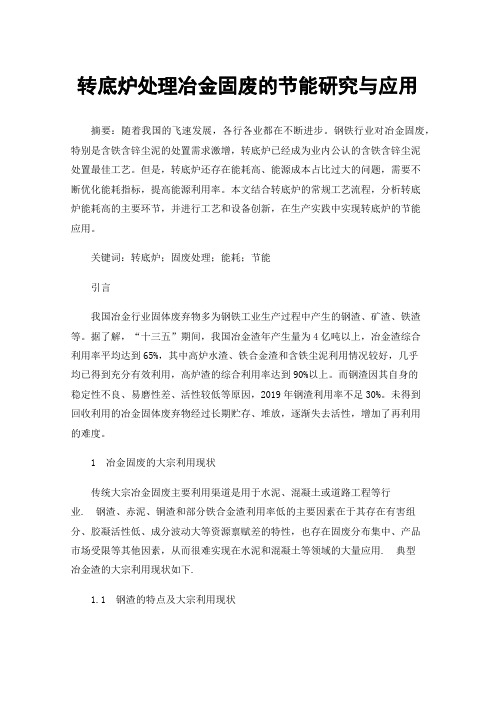
转底炉处理冶金固废的节能研究与应用摘要:随着我国的飞速发展,各行各业都在不断进步。
钢铁行业对冶金固废,特别是含铁含锌尘泥的处置需求激增,转底炉已经成为业内公认的含铁含锌尘泥处置最佳工艺。
但是,转底炉还存在能耗高、能源成本占比过大的问题,需要不断优化能耗指标,提高能源利用率。
本文结合转底炉的常规工艺流程,分析转底炉能耗高的主要环节,并进行工艺和设备创新,在生产实践中实现转底炉的节能应用。
关键词:转底炉;固废处理;能耗;节能引言我国冶金行业固体废弃物多为钢铁工业生产过程中产生的钢渣、矿渣、铁渣等。
据了解,“十三五”期间,我国冶金渣年产生量为4亿吨以上,冶金渣综合利用率平均达到65%,其中高炉水渣、铁合金渣和含铁尘泥利用情况较好,几乎均已得到充分有效利用,高炉渣的综合利用率达到90%以上。
而钢渣因其自身的稳定性不良、易磨性差、活性较低等原因,2019年钢渣利用率不足30%。
未得到回收利用的冶金固体废弃物经过长期贮存、堆放,逐渐失去活性,增加了再利用的难度。
1 冶金固废的大宗利用现状传统大宗冶金固废主要利用渠道是用于水泥、混凝土或道路工程等行业. 钢渣、赤泥、铜渣和部分铁合金渣利用率低的主要因素在于其存在有害组分、胶凝活性低、成分波动大等资源禀赋差的特性,也存在固废分布集中、产品市场受限等其他因素,从而很难实现在水泥和混凝土等领域的大量应用. 典型冶金渣的大宗利用现状如下.1.1 钢渣的特点及大宗利用现状钢渣种类多样,除了转炉炼钢过程排放的转炉钢渣,其他还有电炉炼钢过程排放的电炉钢渣、不锈钢冶炼过程排放的不锈钢钢渣,也有企业把铁水预处理、精炼等炼钢相关工艺排放的预处理渣、精炼渣、铸余渣等也算作钢渣. 部分钢铁厂将这些废渣全部排放到渣场处理,不同的废渣被混合,大大增加了钢渣的利用难度。
在我国,目前约90%的粗钢采用转炉炼钢工艺生产,钢渣中转炉钢渣对应占比接近90%. 钢渣处理主要经过热态钢渣冷却和冷渣破碎磁选工艺,以实现回收10%~15%具有经济价值的铁质组分,同时剩余85%左右难以利用的钢渣尾渣. 通常所说的钢渣即是指这部分磁选后的转炉钢渣尾渣.1.2赤泥的特点及大宗利用现状我国赤泥以拜耳法赤泥为主,其组分以氧化硅、氧化铁、氧化铝、氧化钠和氧化钙为主,还含有Cr、Cd、Mn、Pb或As等重金属元素. 其中,赤泥中氧化钠质量分数在7%~16%,pH值为9.7~12.8.赤泥的高碱性是其形成危害和难以资源化利用的主要原因. 赤泥碱性物质分为可溶性碱和化学结合碱. 可溶性碱包括NaOH、Na2CO3、NaAl(OH)4等,通过水洗仅能去除部分可溶性碱,仍有部分残留在赤泥难溶固相表面并随赤泥堆存. 结合碱多存在于赤泥难溶固相中,如方钠石(Na8Al6Si6O24·(OH)2(H2O)2)、钙石(Na6Ca2Al6Si6O24(CO3)2 2H2O)等,这类含水矿物并不稳定,存在一定的溶解平衡,从而导致赤泥仍然具有碱性但难以通过水洗直接去除.在硅酸盐水泥中,一方面游离的Na+会在毛细力作用下向外迁移,另一方面硅酸盐水泥中大量的Ca2+进一步取代硅酸盐中的Na+,加剧了Na+的溶出和返碱,这导致赤泥建材产品广泛存在返碱防霜问题,因而产品中不能大量掺入赤泥. 此外,水泥混凝土及制品中大量的Na+还会进一步与骨料中的SiO2发生碱骨料反应,生成水化凝胶而使得体积膨胀,材料结构被破坏,导致建筑产品开裂、耐久性能恶化. 因此,赤泥在普通水泥混凝土类建筑材料中难以大量利用。
冶炼炉渣干法粒化余热回收技术
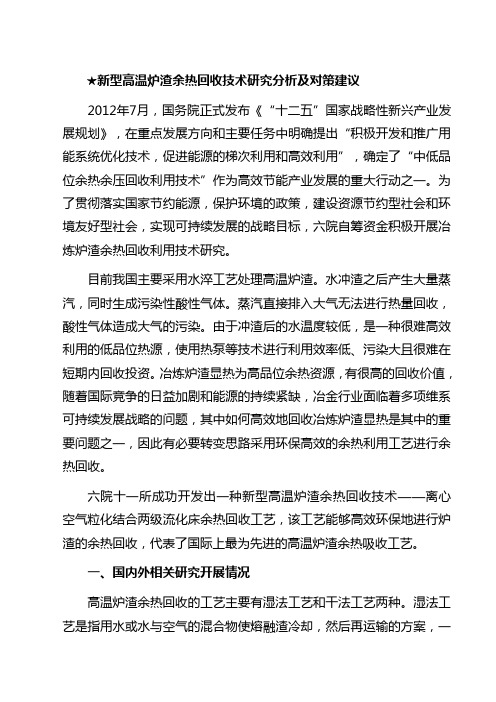
★新型高温炉渣余热回收技术研究分析及对策建议2012年7月,国务院正式发布《“十二五”国家战略性新兴产业发展规划》,在重点发展方向和主要任务中明确提出“积极开发和推广用能系统优化技术,促进能源的梯次利用和高效利用”,确定了“中低品位余热余压回收利用技术”作为高效节能产业发展的重大行动之一。
为了贯彻落实国家节约能源,保护环境的政策,建设资源节约型社会和环境友好型社会,实现可持续发展的战略目标,六院自筹资金积极开展冶炼炉渣余热回收利用技术研究。
目前我国主要采用水淬工艺处理高温炉渣。
水冲渣之后产生大量蒸汽,同时生成污染性酸性气体。
蒸汽直接排入大气无法进行热量回收,酸性气体造成大气的污染。
由于冲渣后的水温度较低,是一种很难高效利用的低品位热源,使用热泵等技术进行利用效率低、污染大且很难在短期内回收投资。
冶炼炉渣显热为高品位余热资源,有很高的回收价值,随着国际竞争的日益加剧和能源的持续紧缺,冶金行业面临着多项维系可持续发展战略的问题,其中如何高效地回收冶炼炉渣显热是其中的重要问题之一,因此有必要转变思路采用环保高效的余热利用工艺进行余热回收。
六院十一所成功开发出一种新型高温炉渣余热回收技术——离心空气粒化结合两级流化床余热回收工艺,该工艺能够高效环保地进行炉渣的余热回收,代表了国际上最为先进的高温炉渣余热吸收工艺。
一、国内外相关研究开展情况高温炉渣余热回收的工艺主要有湿法工艺和干法工艺两种。
湿法工艺是指用水或水与空气的混合物使熔融渣冷却,然后再运输的方案,一般也称为水淬工艺。
干法工艺即依靠高压空气或其他方法实现熔融金属冷却、粒化的工艺。
湿法处理工艺是将高炉渣作为一种材料来加以利用,并没有对其余热量进行充分的利用。
从节能和环保的角度来看,湿法工艺都无法避免处理渣耗水量大的问题。
干式粒化工艺是在不消耗新水的情况下,利用高炉渣与传热介质直接或间接接触进行的高炉渣粒化和显热回收的工艺,几乎没有有害气体排出,是一种环境友好的新式处理工艺。
钢铁行业的节能减排技术了解如何应用节能减排技术提升钢铁生产效率

钢铁行业的节能减排技术了解如何应用节能减排技术提升钢铁生产效率为了应对全球气候变化和环境保护的需求,各行各业都在积极推动节能减排技术的应用,而钢铁行业作为高能耗、高排放的重工业也不例外。
本文将讨论钢铁行业中的节能减排技术,并阐述如何通过应用这些技术来提升钢铁生产效率。
一、炼铁工艺中的节能减排技术1. 高炉煤气回收利用技术在传统炼铁过程中,炉排出的煤气往往直接排放,造成了能源的浪费和环境污染。
而采用高炉煤气回收利用技术,可以将煤气中的有价值组分回收利用,用于发电或热能回收,降低能源消耗,同时减少二氧化碳等污染物的排放。
2. 废热回收利用技术钢铁生产中会产生大量的废热,如果不进行有效的利用,不仅会浪费能源,还会对环境造成负面影响。
采用废热回收利用技术,可以将废热转换成电能或者用于提供热水、供暖等方面,从而实现能源的再利用和节约。
二、钢铁生产过程中的节能减排技术1. 高效燃烧技术在钢铁生产过程中,燃烧是不可避免的环节,但传统的燃烧方式存在能量利用率低、污染物排放高等问题。
使用高效燃烧技术,如喷煤、高温燃烧等,可以提高燃烧效率,减少能源消耗,同时也减少了污染物的产生。
2. 脱硫脱硝技术钢铁生产中常常伴随着废气中的硫化物和氮氧化物排放,对环境造成了严重影响。
脱硫脱硝技术的应用,可以有效地降低废气中的硫化物和氮氧化物含量,减少对大气造成的污染,保护环境。
三、节能减排技术对钢铁生产效率的提升1. 能源利用效率的提高通过采用上述节能减排技术,钢铁企业可以提高能源利用效率,充分利用废气、废热等资源,实现能源的循环利用。
这不仅减少了能源的消耗和成本,还提高了钢铁生产的经济效益。
2. 生产质量的提升节能减排技术的应用使得钢铁行业能够更加环保,降低了废气和废水的排放,减少了对环境的污染。
这不仅有利于企业树立良好的形象,增强市场竞争力,还有助于提升产品的质量和附加值。
3. 资源的可持续利用传统的钢铁生产方式往往会浪费大量的资源,而节能减排技术的应用可以使得资源得到更加合理的利用。
- 1、下载文档前请自行甄别文档内容的完整性,平台不提供额外的编辑、内容补充、找答案等附加服务。
- 2、"仅部分预览"的文档,不可在线预览部分如存在完整性等问题,可反馈申请退款(可完整预览的文档不适用该条件!)。
- 3、如文档侵犯您的权益,请联系客服反馈,我们会尽快为您处理(人工客服工作时间:9:00-18:30)。
2012年第4期 钢 铁 技 术 ·17·
3 结论
传统的板坯连铸机二冷设计方法通常采用基于适当的比水量并按一定分配比例进行各二冷分区的水量设计,其合理性强烈取决于工程师的设计经验和专业认知,具有明显的主观性和随意性,对于连铸专业工程设计流程的标准化和模块化工作是一个较大的技术障碍。
CISDI_SCSD R2011的成功开发和应用对这一不利状况进行了根本的扭转,其深入全面的理论基础和逻辑严密的计算方法为实现板坯连铸工程设计由传统的经验模式转变为先进的科学模式提供了必要的条件和手段,在板坯连铸机工程设计领域具有较大的实用价值和推广空间,同时也可广泛应用于现有板坯连铸机的技术优化和改造。
参考文献
[1] 冯科, 韩志伟, 王勇等. 板坯连铸浇铸过程通用仿真
分析软件的开发与应用[J]. 铸造技术, 2007, 28 (9): 1245 – 1250
[2] 冯科, 韩志伟, 王勇等. 基于枝晶粗化和反向扩散的
二元合金微观偏析数学模型[J]. 铸造, 2006, 55 (7): 699-703
(收稿日期:2012-11-02)
~·~·~·~·~~·~·~·~·~·~·~·~·~·~·~·~·~·~·~·~·~·~·~·~·简讯·
中冶赛迪转底炉回收工艺助力钢企绿色发展
8月14日,重庆市科委组织专家对赛迪工业炉和股份公司联合承担的重庆市科技攻关项目“钢铁厂含锌、铁粉尘的转底炉回收工艺研究”进行了结题验收审查。
会上,来自重庆大学和重庆钢铁集团等单位的评审专家一致认为项目组出色地完成了科研任务,时间进度及考核指标均得到有效执行和完成,科研成果已经成功推广到工程项目中,评审专家一致同意该项目通过结题验收。
赛迪工业炉对转底炉工艺进行了深入的研究,已完成半工业化中试平台建设。
工艺研究已实现冶金含锌尘泥的锌脱除率达90%,金属化率达70%以上,为钢铁企业提供了一条循环经济绿色发展路线,为钢铁企业解决内部锌循环富集、降低环境污染提供了有效途径。
目前,赛迪工业炉已获得某公司转底炉固废处理总承包项目,实现了成果产业化应用,并正向多个工程推广,具有广阔的市场应用前景。