新编印制电路板故障排除手册
印制电路板网印中常见故障的排除方法

p n i gt a u e o . o g wi a eu e r h e n t f h r f s in o CB t r t h t r l n t o i n h t r t t h s c me b Aln t h v s d f en w e ep o e so f h ot o t P p n e o i t mae i , e a t
Ne i st e um m ii rBr a tPr nt he M di Fa la e kdo wn
Qi h n C eg
A src b t t P n t mae h l t nc a shth i ut or( C )s si e c o i dailb a i r to k e e r is r a te r ib ad P B ia t e co p tt c c motn l t n s n l e i er c a t t t
pcb故障排除手册

《新编印制电路板故障排除手册》一、基材部分1 问题:印制板制造过程基板尺寸的变化原因解决方法(1)经纬方向差异造成基板尺寸变化;由于剪切时,未注意纤维方向,造成剪切应力残留在基板内,一旦释放,直接影响基板尺寸的收缩。
(1)确定经纬方向的变化规律,按照收缩率在底片上进行补偿(光绘前进行此项工作)。
同时剪切时按纤维方向加工,或按生产厂商在基板上提供的字符标志进行加工(一般是字符的竖方向为基板的纵方向)。
(2)基板表面铜箔部分被蚀刻掉对基板的变化限制,当应力消除时产生尺寸变化。
(2)在设计电路时应尽量使整个板面分布均匀。
如果不可能也要必须在空间留下过渡段(不影响电路位置为主)。
这由于板材采用玻璃布结构中经纬纱密度的差异而导致板材经纬向强度的差异。
(3)刷板时由于采用压力过大,致使产生压拉应力导致基板变形。
(3)应采用试刷,使工艺参数处在最佳状态,然后进行刷板。
对薄型基材,清洁处理时应采用化学清洗工艺或电解工艺方法。
(4)基板中树脂未完全固化,导致尺寸变化。
(4)采取烘烤方法解决。
特别是钻孔前进行烘烤,温度1200C、4小时,以确保树脂固化,减少由于冷热的影响,导致基板尺寸的变形。
(5)特别是多层板在层压前,存放的条件差,使薄基板或半固化片吸湿,造成尺寸稳定性差。
(5)内层经氧化处理的基材,必须进行烘烤以除去湿气。
并将处理好的基板存放在真空干燥箱内,以免再次吸湿。
(6)多层板经压合时,过度流胶造成玻璃布形变所致。
(6)需进行工艺试压,调整工艺参数然后进行压制。
同时还可以根据半固化片的特性,选择合适的流胶量。
2 问题:基板或层压后的多层基板产生弯曲(BOW)与翘曲(TWIST)。
原因:解决方法:(1)特别是薄基板的放置是垂直式易造成长期应力叠加所致。
(1)对于薄型基材应采取水平放置确保基板内部任何方向应力均匀,使基板尺寸变化很小。
还必须注意以原包装形式存放在平整的货架上,切记勿堆高重压。
(2)热熔或热风整平后,冷却速度太快,或采用冷却工艺不当所致。
变频器印制电路板故障维修方法变频器_软启动器

变频器印制电路板故障修理方法 - 变频器_软启动器变频器的故障现象有很多,而对于修理者最重要的就是找到故障点,有针对性地处理问题。
除了阅历,把握正确的检查方法是格外必要的。
下面主要介绍变频器印制电路板问题点查找以及修理方法。
1、故障推断⑴排解了主回路器件的故障后,如还不能使变频器正常工作,最为简洁有效的推断是拆下印制板看一下正、反面有无明显的元件变色、印制线变色、局部烧毁。
⑵一般变频器上的印制板主要有驱动板、主控板、显示板,依据变频器故障表现特征,使用换板方式推断哪块板有毛病。
对其他印制板,如吸取板、GE 板、风机电源板等,因电路简洁可用万用表快速查出故障。
⑶印制板在有电路图时按图检查各电源电压,用示波器检查各点波形,先从后级,渐渐往前级检查;在没有电路图时,接受比较法,对有几路相同的部分进行比较,将故障板与好板对比查出不同点,再作分析即可找到损坏的器件。
2、故障缘由⑴元器件本身质量和寿命造成损坏,特殊是功率较大的器件,损坏的概率更大。
⑵元器件因过热或过电压损坏,变压器断线,电解电容器干枯、漏电,电阻长期高温而变值。
⑶因环境温度、湿度、水露、灰尘引起印制板腐蚀击穿绝缘漏电等损坏。
⑷因模块损坏导致驱动印制板上的元件和印制线损坏。
⑸因接插件接触不良、单片机、存储器受干扰晶振失效。
⑹原有程序因用户自行调乱,不能工作。
3、修理方法⑴对印制板修理需有电路图、电源、万用表、示波器、全套焊接拆装工具,以及日积月累的阅历,才会比较快速地找到损坏之处。
⑵印制板表面有防护漆等涂层,检测时要认真用针状测笔接触到被测金属,防止误判。
由于元件过热和过电压简洁造成元件损坏,所以对于下列部位要求高度留意,首先检查: 开关电源的开关管、开关变压器、过电压吸取元件、功率器件、脉冲变压器、高压隔离用的光耦合器、过电压吸取或缓冲吸取板及所属元件、充电电阻、场效应管或IGBT管、稳压管或稳压集成电路。
⑶印制板的更换会因版本不同而带来麻烦,因此若确定要换板,就要看版号标识是否全都,如不全都而发生了障碍,就要向制造商了解清楚。
电路板故障维修手册

电路板故障维修手册在现代科技高度发达的社会中,电路板被广泛应用于各个行业和领域,它是电子产品中不可或缺的重要组成部分。
然而,由于各种原因,电路板故障是一个常见且困扰人们的问题。
为了帮助大家更好地理解和解决电路板故障,本手册将详细介绍电路板故障的常见类型、诊断方法和维修技巧。
一、常见的电路板故障类型1.电源问题:电源电压异常、电源接触不良等。
2.元件故障:电容量变小、电阻值偏离正常范围、二极管失效等。
3.连接问题:焊点异常、插头松动等。
4.短路问题:电路板上两个或多个不应该相连的点发生了短路。
5.开路问题:电路板上两个相应相连的点断开了。
二、电路板故障的诊断方法1.外观检查:首先检查电路板的外观,寻找烧焦、腐蚀或其他物理损伤等迹象。
2.测量电压:使用万用表进行电压测量,判断电源电压是否正常。
3.测量电流:通过对电路板的电流进行测量,判断是否存在短路或其他异常情况。
4.替换元件:对于疑似故障的元件,可以尝试替换为新的元件,观察问题是否得到解决。
5.信号跟踪:利用示波器等仪器对电路板上的信号进行跟踪,找出信号中断或异常的位置。
三、电路板故障的维修技巧1.焊接技巧:掌握良好的焊接技巧,确保焊点牢固可靠。
2.元件更换:在更换元件时,要注意选择合适的替代元件,并注意正确安装。
3.短路处理:对于存在短路的问题,可以使用隔离纸或覆铜网进行隔离。
4.测试设备:准备好常用的测试设备,例如万用表、示波器等,便于故障的诊断和维修。
5.防护措施:在维修电路板时,要注意安全防护,避免触电和其他意外伤害。
总结:电路板故障维修需要一定的技术和经验,除了上述提到的常见故障类型、诊断方法和维修技巧外,实际维修过程中还需要根据具体情况做出判断和处理。
如果遇到复杂的故障问题,建议向专业维修人员寻求帮助。
希望本手册能够为大家在电路板故障维修方面提供一定的参考和指导,让我们更好地应对和解决电路板故障问题。
印刷电路板焊锡常见问题及解决方案

印刷电路板焊锡常见问题及解决方案印刷电路板的焊锡作业永远有不良焊点的问题存在,而这种问题曾出不穷,似乎永远都会有新问题出现应接不暇,因此我们整理出一些规,可做为找出问题所在依据。
PCB板上的问题常是由焊锡作业中造成的,但在确定是焊锡作业造成问题以前,应先考虑其他各种因故,再考虑焊锡作业,焊锡作业之间题大多出在材料的变化及操作条件改变,我们整理出下列最常见的问题焊点,如锡尖、不沾锡、锡点过大、绿漆上有锡丝、白班、锡孔等。
1、沾锡不良*这种情况是不可接受的缺点,在焊点上只有部分沾锡,如果是在裸铜面上焊接,可看到某些完全不同的现象,很容易分辨出来。
分析其产生原因及改善方式如下:*外界的污染物如油、脂、臘等,此类污染物通常可用溶剂清洗。
些类污染物有时是在印刷助焊剂时沾上的,可用打磨方式支除,但必须非常小心,不可残留打磨粉末在表面。
*Silicon Oil通常用于脱模及润滑之用,常会在PCB板及零件脚上发现,而SiliconOil等要非常小心,如使用SiliconOiL当作抗氧化油,亦常会发生问题因为SiliconOil会蒸发SiliconOil 会蒸发,沾露在PCB板上而造成沾锡不良。
*严重氧化,通常是由于宁存状况不佳或PCB板制程上有问题,发生严重氧化后,助焊剂是无法去除的,因些出现沾锡不良。
氧化轻微两次焊锡可解决此问题。
*涂敷焊剂方式不正确,造成原因为发泡气压不稳定或不足,致使*泡沫高度不稳或不均匀而使PCB板部份无法涂敷上助焊剂。
焊锡时间不足或温度不够,会造成沾锡不良,因为熔锡需要足够的温度及时间于元件脚和PCB接触,才能形成良好的焊点。
2、局部粘锡不良些种现象与粘锡不良相似,不同的是局部粘锡不良的情况,不会露铜面,只有薄薄的一会焊锡无法形成饱满的焊点,其形成原因于粘锡不良相似。
两次焊锡出许无法改善些状况,必须用焊锡剥除剂除去焊锡,重新清洁表面再做焊锡。
电镀时污染未清理干净,亦会产生局部沾锡不良,此类问题,宜送回PCB板厂家重新处理。
印制电路板故障排除手册(doc 22页)
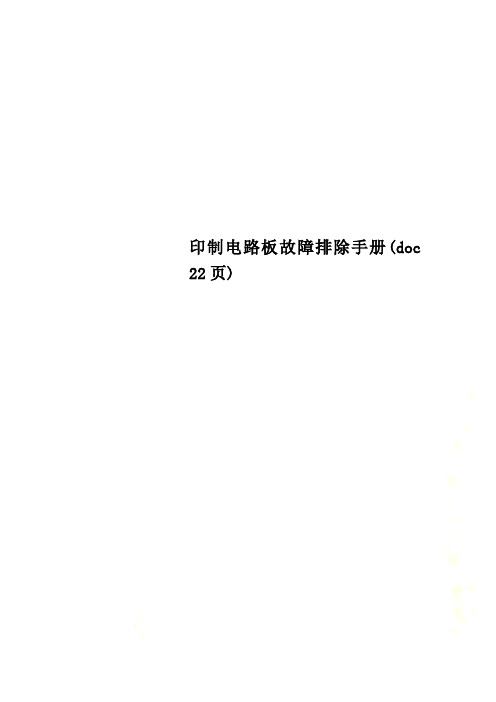
印制电路板故障排除手册(doc 22页)原因解决方法(1)定影液过旧银粉沉淀加重底片发雾。
(1)更换新定影液。
(2)定影时间不足,造成底色不够透明。
(2)定影时间保持60秒以上。
4.问题:照相底片变色原因解决方法(1)定影后清洗不充分。
(1)定影后需用大量流动水清洗,最好保持20分钟以上。
B.原片复制作业1.问题:经翻制的重氮底片图形变形即全部导线变细而不整齐原因解决方法(1)曝光参数选择不当。
(1)根据底片状态,进行优化曝光时间。
(2)原底片的光密度未达到工艺数据。
(2)测定光密度,使明处达到Dmax4.0数据以上;未要求透明部分其光密在Dmin0.2以下。
2.问题:经翻制的重氮底片其边缘局部导线宽度变细而不整齐原因解决方法(1)曝光机光源的工艺参数不正确。
(1)采用仪器测量紫外光源灯能量的衰减,如超过使用寿命应进行更换。
(2)需翻的重氮片面积超出曝光框之最佳范围。
(2)根据生产情况缩小拼版面积或由于光源太近,将光源提高以拉开与曝光台面的适当的距离,确保大尺寸的底片处于良好的感光区域内。
3.问题:经翻制的重氮片全部或局部解像度不良原因解决方法(1)原采用的底片品质差。
(1)检查原底片线路边缘的成像状态,采取工艺措施改进。
(2)曝光机台面抽真空系统发生故障。
(2)认真检查导气管道是否有气孔或破损。
(3)曝光过程中底片有气泡存在。
(3)检查曝光机台面是否沾有灰粒;检查子片与曝光机台面所垫黑纸是否有凹蚀或折痕。
4.问题:经翻制的重氮底片导线变宽,透明区域不足(即Dmin数据过大)原因解决方法(1)选择的曝光工艺参数不当。
(1) A.选择适当的曝光时间。
B.可能重氮片存放环境接近氨水或有氨气存在,造成不同程度的显影所至。
5.问题:经翻制的重氮底片遮光区域不足(Dmax数据过低)原因解决方法(1)翻制重氮底片时,显影不正确。
(1) A.检查显影机是否发生故障。
B.检查氨水供应系统,测定浓度是否在Be‘26(即比重为1.22)以上。
印制电路板各类故障原因及解决方法梳理

印制电路板各类故障原因及解决方法梳理一、基材部分1 问题:印制板制造过程基板尺寸的变化原因解决方法(1)经纬方向差异造成基板尺寸变化;由于剪切时,未注意纤维方向,造成剪切应力残留在基板内,一旦释放,直接影响基板尺寸的收缩。
(1) 确定经纬方向的变化规律,按照收缩率在底片上进行补偿(光绘前进行此项工作)。
同时剪切时按纤维方向加工,或按生产厂商在基板上提供的字符标志进行加工(一般是字符的竖方向为基板的纵方向)。
(2)基板表面铜箔部分被蚀刻掉对基板的变化限制,当应力消除时产生尺寸变化。
(2)在设计电路时应尽量使整个板面分布均匀。
如果不可能也要必须在空间留下过渡段(不影响电路位置为主)。
这由于板材采用玻璃布结构中经纬纱密度的差异而导致板材经纬向强度的差异。
(3)刷板时由于采用压力过大,致使产生压拉应力导致基板变形。
(3)应采用试刷,使工艺参数处在最佳状态,然后进行刷板。
对薄型基材,清洁处理时应采用化学清洗工艺或电解工艺方法。
(4)基板中树脂未完全固化,导致尺寸变化。
(4)采取烘烤方法解决。
特别是钻孔前进行烘烤,温度1200C、4小时,以确保树脂固化,减少由于冷热的影响,导致基板尺寸的变形。
(5)特别是多层板在层压前,存放的条件差,使薄基板或半固化片吸湿,造成尺寸稳定性差。
(5)内层经氧化处理的基材,必须进行烘烤以除去湿气。
并将处理好的基板存放在真空干燥箱内,以免再次吸湿。
(6)多层板经压合时,过度流胶造成玻璃布形变所致。
(6)需进行工艺试压,调整工艺参数然后进行压制。
同时还可以根据半固化片的特性,选择合适的流胶量。
2 问题:基板或层压后的多层基板产生弯曲(BOW)与翘曲(TWIST)。
原因:解决方法:(1)特别是薄基板的放置是垂直式易造成长期应力叠加所致。
(1)对于薄型基材应采取水平放置确保基板内部任何方向应力均匀,使基板尺寸变化很小。
还必须注意以原包装形式存放在平整的货架上,切记勿堆高重压。
(2)热熔或热风整平后,冷却速度太快,或采用冷却工艺不当所致。
印刷电路板pcb制程的常见问题及解决方法
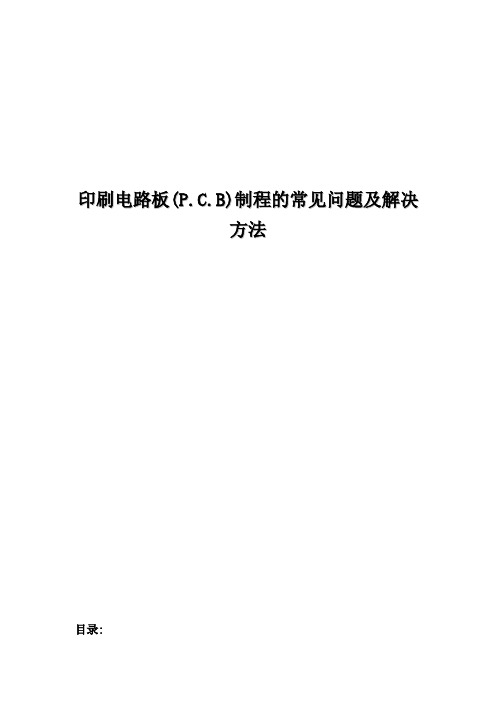
A预烘
1、温度过低
*加强预烘条件控制
2、时间不够
*加强预烘条件控制
B曝光
1、曝光量不足(阻焊表面也有受损、发白等现象)
*加强曝光条件控制
2、真空度差
*改善曝光框架状况,使用导气条等
C显影
1、显影液浓度过高
*调整浓度至正常值
2、显影液温度过高
*调整温度至正常值
3、显影速度过慢
*加强显影条件的控制
4、喷嘴压力过高
问题
原因
解决办法
涂覆层厚度不均匀
①抗蚀剂粘度太高
②网印速度太慢
①加稀释剂调至正常粘度
②加大网印速度,并保证速度均匀一致。
涂覆层厚度太厚或太薄
网版目数选择不当
选择合适的网目数丝网
针孔
①抗蚀剂有不明油脂
②空气中有微粒
③板面不干净
①换新的抗蚀剂并用丙酮彻底清洗
②保证操作间空气洁净度
③检查板面,清洁板面。
曝光时粘生产底版
2)生产底版最小光密度太大,使紫外光受阻。
曝光前检查生产底版。
3)显影液温度过高或显影时间太长。
调整显影液温度及显影时的传送速度。
(6)图形镀铜与基体铜结合不牢或图像有缺陷
原因
解决方法
1)显影不彻底有余胶。
加强显影并注意显影后清洗。
2)图像上有修板液或污物。
修板时戴细纱手套,并注意不要使修板液污染线路图像。
2.调整固化温度
3.检查烘箱的抽风是否正常
4.检查表面处理及处理后的印,制板状况
5.调换贯孔所需的印料
*调整压力
阻焊膜气泡
A丝网
1、丝网未经脱脂或清洁不够
*丝网使用前彻底脱脂、清洁
- 1、下载文档前请自行甄别文档内容的完整性,平台不提供额外的编辑、内容补充、找答案等附加服务。
- 2、"仅部分预览"的文档,不可在线预览部分如存在完整性等问题,可反馈申请退款(可完整预览的文档不适用该条件!)。
- 3、如文档侵犯您的权益,请联系客服反馈,我们会尽快为您处理(人工客服工作时间:9:00-18:30)。
《新编印制电路板故障排除手册》源明绪言根据目前印制电路板制造技术的发展趋势,印制电路板的制造难度越来越高,品质要求也越来越严格。
为确保印制电路板的高质量和高稳定性,实现全面质量管理和环境控制,必须充分了解印制电路板制造技术的特性,但印制电路板制造技术是综合性的技术结晶,它涉及到物理、化学、光学、光化学、高分子、流体力学、化学动力学等诸多方面的基础知识,如材料的结构、成份和性能:工艺装备的精度、稳定性、效率、加工质量;工艺方法的可行性;检测手段的精度与高可靠性及环境中的温度、湿度、洁净度等问题。
这些问题都会直接和间接地影响到印制电路板的品质。
由于涉及到的方面与问题比较多,就很容易产生形形色色的质量缺陷。
为确保“预防为主,解决问题为辅”的原则的贯彻执行,必须认真地了解各工序最容易出现及产生的质量问题,快速地采取工艺措施加以排除,确保生产能顺利地进行。
为此,特收集、汇总和整理有关这方面的材料,编辑这本《印制电路板故障排除手册》供同行参考。
一、基材部分1 问题:印制板制造过程基板尺寸的变化原因解决方法(1)经纬方向差异造成基板尺寸变化;由于剪切时,未注意纤维方向,造成剪切应力残留在基板内,一旦释放,直接影响基板尺寸的收缩。
(1)确定经纬方向的变化规律,按照收缩率在底片上进行补偿(光绘前进行此项工作)。
同时剪切时按纤维方向加工,或按生产厂商在基板上提供的字符标志进行加工(一般是字符的竖方向为基板的纵方向)。
(2)基板表面铜箔部分被蚀刻掉对基板的变化限制,当应力消除时产生尺寸变化。
(2)在设计电路时应尽量使整个板面分布均匀。
如果不可能也要必须在空间留下过渡段(不影响电路位置为主)。
这由于板材采用玻璃布结构中经纬纱密度的差异而导致板材经纬向强度的差异。
(3)刷板时由于采用压力过大,致使产生压拉应力导致基板变形。
(3)应采用试刷,使工艺参数处在最佳状态,然后进行刷板。
对薄型基材,清洁处理时应采用化学清洗工艺或电解工艺方法。
(4)基板中树脂未完全固化,导致尺寸变化。
(4)采取烘烤方法解决。
特别是钻孔前进行烘烤,温度1200C、4小时,以确保树脂固化,减少由于冷热的影响,导致基板尺寸的变形。
(5)特别是多层板在层压前,存放的条件差,使薄基板或半固化片吸湿,造成尺寸稳定性(5)内层经氧化处理的基材,必须进行烘烤以除去湿气。
并将处理好的基板存放在真空干燥箱内,以免再次吸湿。
差。
(6)多层板经压合时,过度流胶造成玻璃布形变所致。
(6)需进行工艺试压,调整工艺参数然后进行压制。
同时还可以根据半固化片的特性,选择合适的流胶量。
2 问题:基板或层压后的多层基板产生弯曲(BOW)与翘曲(TWIST)。
原因:解决方法:(1)特别是薄基板的放置是垂直式易造成长期应力叠加所致。
(1)对于薄型基材应采取水平放置确保基板内部任何方向应力均匀,使基板尺寸变化很小。
还必须注意以原包装形式存放在平整的货架上,切记勿堆高重压。
(2)热熔或热风整平后,冷却速度太快,或采用冷却工艺不当所致。
(2)放置在专用的冷却板上自然冷却至室温。
(3)基板在进行处理过程中,较长时间内处于冷热交变的状态下进行处理,再加基板内应力分布不均,引起基板弯曲或翘曲。
(3)采取工艺措施确保基板在冷热交变时,调节冷、热变换速度,以避免急骤冷或热。
(4)基板固化不足,造成内应力集中,致使基板本身产生弯曲或翘曲。
(4)A。
重新按热压工艺方法进行固化处理。
B。
为减少基板的残余应力,改善印制板制造中的尺寸稳定性与产生翘曲形变,通常采用预烘工艺即在温度120-1400C 2-4小时(根据板厚、尺寸、数量等加以选择)。
(5)基板上下面结构的差异即铜箔厚度不同所至。
(5)应根据层压原理,使两面不同厚度的铜箔产生的差异,转成采取不同的半固化片厚度来解决。
3 问题:基板表面出现浅坑或多层板内层有空洞与外来夹杂物。
原因:解决方法:(1)铜箔内存有铜瘤或树脂突起及外来颗粒叠压所至。
(1)原材料问题,需向供应商提出更换。
(2)经蚀刻后发现基板表面透明状,经切片是空洞。
(2)同上处理方法解决之。
(3)特别是经蚀刻后的薄基材有黑色斑点即粒子状态。
(3)按上述办法处理。
4 问题:基板铜表面常出现的缺陷原因:解决方法:(1)铜箔出现凹点或凹坑,这是由于叠层压制时所使用的工具表面上存有外来杂质。
(1)改善叠层和压合环境,达到洁净度指标要求。
(2)铜箔表面出现凹点与胶点,是由于所采用压板模具压制和叠层时,存有外来杂质直接影响所至。
(2)认真检查模具表面状态,改善叠层间和压制间工作环境达到工艺要求的指标。
(3)在制造过程中,所使用的工具不适合导致铜箔表面状态差。
(3)改进操作方法,选择合适的工艺方法。
(4)经压制的多层板表面铜箔出现折痕,是因为叠层在压制时滑动与流胶不当所至。
(4)叠层时要特别注意层与层间的位置准确性,避免送入压机过程中滑动。
直接接触铜箔表面的不锈钢板,要特小心放置并保持平整.(5)基板表面出现胶点,可能是叠层时胶屑落在钢板表面或铜表面上所造成的。
(5)为防止胶屑脱落,可将半固化片边缘进行热合处理。
(6)铜箔表面有针孔造成压制时熔融的胶向外溢出所至。
(6)首先对进厂的铜箔进行背光检查,合格后必须严格的保管,避免折痕或撕裂等。
5 问题:板材内出现白点或白斑原因:解决方法:(1)板材经受不适当的机械外力的冲击造成局部树脂与玻璃纤维的分离而成白斑。
(1)从工艺上采取措施,尽量减少或降低机械加工过度的振动现象以减少机械外力的作用。
(2)局部板材受到含氟化学药品的渗入,而对玻璃纤维布织点的浸蚀,形成有规律性的白点(较为严重时可看出呈方形)。
(2)特别是在退锡铅合金镀层时,易发生在镀金插头片与插头片之间,须注意选择适宜的退锡铅药水及操作工艺。
(3)板材受到不当的热应力作用也会造成白点、白斑。
(3)特别是热风整平、红外热熔等如控制失灵,会造成热应力的作用导致基板内产生缺陷。
二照相底片制作工艺A .光绘制作底片1.问题:底片发雾,反差不好原因解决方法(1)旧显影液,显影时间过长。
(1)采用新显影液,显影时间短,底片反差好(即黑度好)。
(2)显影时间过长。
(2)缩短显影时间。
2.问题:底片导线边缘光晕大原因解决方法(1)显影液温度过高造成过显。
(1)控制显影液温度在工艺范围内。
3.问题:底片透明处显得不够与发雾原因解决方法(1)定影液过旧银粉沉淀加重底片发雾。
(1)更换新定影液。
(2)定影时间不足,造成底色不够透明。
(2)定影时间保持60秒以上。
4.问题:照相底片变色原因解决方法(1)定影后清洗不充分。
(1)定影后需用大量流动水清洗,最好保持20分钟以上。
B.原片复制作业1.问题:经翻制的重氮底片图形变形即全部导线变细而不整齐原因解决方法(1)曝光参数选择不当。
(1)根据底片状态,进行优化曝光时间。
(2)原底片的光密度未达到工艺数据。
(2)测定光密度,使明处达到Dmax4.0数据以上;未要求透明部分其光密在Dmin0.2以下。
2.问题:经翻制的重氮底片其边缘局部导线宽度变细而不整齐原因解决方法(1)曝光机光源的工艺参数不正确。
(1)采用仪器测量紫外光源灯能量的衰减,如超过使用寿命应进行更换。
(2)需翻的重氮片面积超出曝光框之最佳范围。
(2)根据生产情况缩小拼版面积或由于光源太近,将光源提高以拉开与曝光台面的适当的距离,确保大尺寸的底片处于良好的感光区域内。
3.问题:经翻制的重氮片全部或局部解像度不良原因解决方法(1)原采用的底片品质差。
(1)检查原底片线路边缘的成像状态,采取工艺措施改进。
(2)曝光机台面抽真空系统发生故障。
(2)认真检查导气管道是否有气孔或破损。
(3)曝光过程中底片有气泡存在。
(3)检查曝光机台面是否沾有灰粒;检查子片与曝光机台面所垫黑纸是否有凹蚀或折痕。
4.问题:经翻制的重氮底片导线变宽,透明区域不足(即Dmin数据过大)原因解决方法(1)选择的曝光工艺参数不当。
(1) A.选择适当的曝光时间。
B.可能重氮片存放环境接近氨水或有氨气存在,造成不同程度的显影所至。
5.问题:经翻制的重氮底片遮光区域不足(Dmax数据过低)原因解决方法(1)翻制重氮底片时,显影不正确。
(1) A.检查显影机是否发生故障。
B.检查氨水供应系统,测定浓度是否在Be‘26(即比重为1.22)以上。
(2)原重氮片材质差。
(2)测定原底片材料的光密度Dmax是否在4.0以上。
6.问题:经翻制的重氮底片暗区遮光性能低Dmax偶而不足原因解决方法(1)经翻制重氮片显影不正确。
(1)检查氨气显影机故障状态,并进行调整。
(2)原底片材料存放环境不良。
(2)按底片材料说明书要求存放,特别要避免光直照或接近氨水存放处。
(3)操作显影机不当。
(3)特别要检查显影机输送带的温度,采用感温变色的特用贴纸检测,应符合工艺要求(非氨水槽中控温器)。
7.问题:经翻制的重氮片图形区域出现针孔或破洞原因解决方法(1)曝光区域内有灰尘或尘粒存在。
(1)特别要仔细检查曝光台面、原始底片及新重氮片表面干净情况,并进行擦试。
(2)原始底片品质不良。
(2)在透图台面检查,并进行仔细的修补(需要证明原始底片质量时可采取重新翻制第二张,核查对比如相同,可证明之)。
(3)所使用的重氮片品质有问题。
(3)采取将未曝光的原始重氮片直接氨气显影,使全片呈遮光的深棕色,再仔细检查是否有针孔与破洞,如有,就可证明之。
8.问题:经翻制的重氮片发生变形走样原因解决方法(1)环境温湿度控制不严。
(1) A.加装温湿度控制器,调节室内达到工艺要求范围内。
B.作业环境温湿度控制:温度为20-270C;湿度40-70%。
精度要求高的底片,其湿度控制在55-60%RH。
(2)经显定影后,干燥过程控制不当。
(2)按照工艺要求将底片水平放置进行吹风、干燥。
不宜吊挂晾干,这样,易变形。
(3)翻制前重氮片稳定处理不当。
(3)应在底片存放间环境下存放24小时,进行稳定处理。
C.黑白底片翻制工艺1.问题:经翻制的黑白底片全部导线宽度变细而不齐原因解决方法(1)曝光工艺参数选择不当。
(1)首先检查正翻负或负翻正是否曝光过度,应根据实际进行修正。
(2)原底片品质不良。
(2)检查原底片光密度,特别是“遮光密度”是否太低。
(3)翻制过程显影控制有问题。
(3)检查显影液浓度和装置。
2.问题:经翻制的底片其外缘导线宽度变细而不整齐原因解决方法(1)曝光设备校验过期。
(1)重新根据工艺要求进行校验,检查光源能量是否在技术要求之内。
(2)光源太接近较大尺寸底片。
(2)重新调整光源距离或改用大型曝光机。
(3)光源反射器距离与角度失调。
(3)重新调节“反射罩面”的距离与角度。
3.问题:经翻制底片解像度不理想,全片导线边缘不锐利原因解决方法(1)原底片品质不佳。
(1)检查原始底片导线边缘状态。