物料仓储系统风险评估
采购周总结物料供应稳定性与风险评估
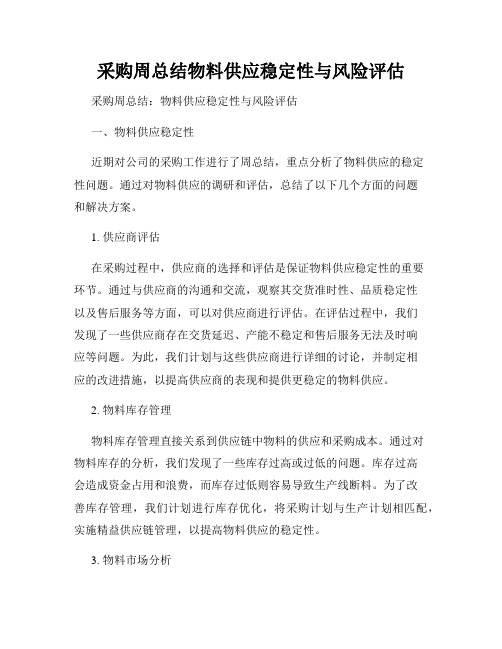
采购周总结物料供应稳定性与风险评估采购周总结:物料供应稳定性与风险评估一、物料供应稳定性近期对公司的采购工作进行了周总结,重点分析了物料供应的稳定性问题。
通过对物料供应的调研和评估,总结了以下几个方面的问题和解决方案。
1. 供应商评估在采购过程中,供应商的选择和评估是保证物料供应稳定性的重要环节。
通过与供应商的沟通和交流,观察其交货准时性、品质稳定性以及售后服务等方面,可以对供应商进行评估。
在评估过程中,我们发现了一些供应商存在交货延迟、产能不稳定和售后服务无法及时响应等问题。
为此,我们计划与这些供应商进行详细的讨论,并制定相应的改进措施,以提高供应商的表现和提供更稳定的物料供应。
2. 物料库存管理物料库存管理直接关系到供应链中物料的供应和采购成本。
通过对物料库存的分析,我们发现了一些库存过高或过低的问题。
库存过高会造成资金占用和浪费,而库存过低则容易导致生产线断料。
为了改善库存管理,我们计划进行库存优化,将采购计划与生产计划相匹配,实施精益供应链管理,以提高物料供应的稳定性。
3. 物料市场分析对物料市场的分析可以帮助我们了解市场供需关系,评估供应商的竞争力以及未来可能出现的风险。
通过对物料市场的不断监测和分析,我们可以及时应对市场波动,保障物料供应的稳定性。
在本周的分析中,我们发现一些原材料价格上涨的趋势,为了降低采购成本,我们将积极寻找替代品或者与供应商进行谈判。
二、物料供应风险评估除了物料供应稳定性,我们还对物料供应的风险进行了评估,以建立风险应对机制,保障采购工作的顺利进行。
1. 天气风险天气因素(如台风、暴雨)可能导致供应链中的物流运输中断或延迟。
我们将密切关注天气情况,与物流供应商保持紧密联系,并制定应急措施,以减少由于天气原因造成的物料供应风险。
2. 突发事件风险突发事件(如地震、火灾)可能对供应链中的生产和物流环节造成不可预测的干扰。
我们将与企业安全部门密切合作,建立应急预案,以确保在突发事件发生时能够快速应对,保障物料供应的稳定性。
物料管理中的供应商风险评估与管理

物料管理中的供应商风险评估与管理引言在物料管理的过程中,供应商的选择和管理是非常关键的环节。
一个好的供应商能够稳定地提供高质量的物料,并且能够及时配送,满足企业生产和运营的需求。
然而,供应商也存在一定的风险,比如质量问题、交货延迟、安全隐患等。
因此,对供应商进行风险评估和管理是必要的。
本文将介绍物料管理中的供应商风险评估与管理的重要性,以及常用的评估方法和管理策略。
供应商风险评估的重要性供应商风险评估是为了确定供应商在物料管理中可能面临的风险和隐患,并采取相应的措施进行管理和控制。
一个完善的供应商风险评估体系可以帮助企业识别高风险和低风险的供应商,避免和降低潜在的风险,保障物料的质量和供应的稳定性。
以下是供应商风险评估的重要性:1.保障物料质量:通过对供应商的质量管理体系进行评估,可以避免采购到质量不合格的物料,降低因质量问题带来的生产损失和返工成本。
2.提升供应的稳定性:评估供应商的生产能力和供应能力,可以减少交货延迟的风险,确保物料的及时供应,避免生产线的中断和产品的积压。
3.避免合规风险:评估供应商的环境、安全和社会责任管理能力,可以预防潜在的合规问题,避免因供应商的违法违规行为给企业造成的法律责任和声誉损失。
供应商风险评估的方法1. 供应商信用评估采用供应商信用评估的方法,可以了解供应商的财务状况、信用记录和商业信誉等方面的情况。
常用的评估指标包括供应商的信用报告、供应商的经营年限、供应商的资产负债表等。
通过供应商信用评估,可以初步判断供应商的可靠性和稳定性。
2. 供应商质量评估供应商的质量评估是评估供应商在生产过程中是否符合相关质量标准和要求的过程。
常用的评估方法包括对供应商的生产工艺和检验流程进行审核,抽样检验供应商提供的样品,以及对供应商的质量管理体系进行评估。
通过供应商质量评估,可以判断供应商的质量水平和管理能力。
3. 供应商供应能力评估供应商的供应能力评估是评估供应商在供应物料方面的能力和稳定性的过程。
仓库管理制度风险评估

仓库管理制度风险评估仓库管理制度是企业运作中非常重要的一环。
它是指企业为科学、高效地管理仓库而制定的一系列制度和规定。
在今天的商业环境中,仓库管理的风险与挑战也随之增加。
因此,对仓库管理制度进行风险评估变得至关重要。
本文将对仓库管理制度风险进行评估,并提出相应的解决方案。
一、仓库管理制度风险评估的重要性仓库作为企业重要的物流环节,直接关系到产品的存储、配送和售后服务质量。
在仓库管理中,不合理的制度和规定可能会带来一系列的风险和问题。
例如,物品丢失、过期、破损等情况可能会发生,给企业造成损失。
因此,建立健全的仓库管理制度风险评估机制,可以帮助企业及时发现问题,并采取相应的措施来降低风险和提升管理水平。
二、仓库管理制度风险评估的方法和指标为了准确评估仓库管理制度的风险,可以采用以下方法和指标:1. 风险识别:对仓库管理过程中可能存在的各种风险进行识别和分类,例如货物丢失、库存过多或过少、仓库环境不佳等。
2. 风险评估:对已识别的风险进行评估,包括评估风险的概率和影响程度。
可以使用评估矩阵或其他评估工具进行量化评估。
3. 风险优先级确定:根据评估结果,确定风险的优先级。
重要性高的风险需要优先解决,以确保仓库管理的稳定和正常运行。
4. 解决方案制定:针对每个风险,制定相应的解决方案。
解决方案可以包括调整制度规定、加强员工培训、优化仓库布局等。
5. 监控和改进:建立监控机制,及时发现并跟踪风险的变化。
在实际操作中,根据情况对解决方案进行调整和改进,以确保仓库管理风险得到有效控制。
三、仓库管理制度风险评估案例分析以某电子产品仓库管理制度风险评估为例,以下为具体评估和解决方案:1. 风险识别:识别出货物过期、货物丢失和库存过多三个主要风险。
2. 风险评估:分别对三个风险进行评估,得出风险概率和影响程度,并综合计算得出风险等级。
3. 风险优先级确定:根据风险等级确定优先级。
结果显示,货物过期风险最为严重,需要优先解决。
物料供应商风险评估报告

【最新资料,WORD文档,可编辑修改】目录1、概述2、目的3、风险评估3.1、风险识别3.2、风险评价3.3、风险评价4、风险等级确认5、风险控制6、结论1、概述:1.1、供应商评估是保证物料采购的关键过程,通过对物料供应商的资质文件审核、供应商GMP法规的执行情况、质量风险管理体系、人员、设施设备、投诉、调查、变更管理、与企业沟通、环保健康安全、运输管理等一系列过程控制;是保证物料进厂合格的管理过程,是有效降低物料采购风险的控制方法。
1.2、根据物料对产品质量影响风险程度,结合公司产品确定物料的安全级别,其A级物料如下:对直接影响药品质量的主要原辅料,经风险分析后定为A级。
原料有氯化钠、葡萄糖、甲硝唑、XXXX、XXXX、氟罗沙星、XXXX、XXX、中药材及中药饮片。
辅料有盐酸、氢氧化钠、乳酸、枸橼酸、依地酸钙钠、盐酸半胱氨酸、焦亚硫酸钠、磷酸二氢钠、磷酸氢二钠、空心胶囊、硬脂酸镁、药用糊精、药用淀粉、蔗糖、滑石粉、微晶纤维素、包衣粉。
2、目的:建立A级物料供应商存在和可能发生的风险进行评估,确定风险等级;并采取措施将风险控制在可接受范围内。
3、物料供应商风险评估:3.1、风险识别:A级物料是影响产品质量的关键物料,其物料供应商存在的风险程度直接影响物料产品质量风险程度。
是物料供应商风险评估的重点。
根据对物料产品的质量影响情况和其他风险影响分析物料供应供应商可能存在的风险点如下:3.1.1、政策法规3.1.2、产品质量3.2、对物料供应供应商风险点进行分析,以上风险点存在风险因素:3.2.1、政策法规影响的风险因素3.2.1.1、资质批准文件3.2.1.2、产品质量标准3.2.1.3、经营授权书3.2.2、产品质量影响的风险因素3.2.2.1、人员与机构3.2.2.2、厂房和设施、设备3.2.2.3、物料管理3.2.2.4、生产管理3.2.2.5、质量控制管理3.2.2.6、产品包装与运输3.2.2.7、质量管理体系3.3、风险分析:3.3.1、风险等级判定标准:用定量分级RPN风险优先数量等级判定(危害 :存在风险项目较多,并且不能有效控制风险,从而影响其物料质量,最终影响到我公司产品的质量。
物料供应商风险评估报告

物料供应商风险评估报告XXXX 有限公司目录1、目的 (1)2、风险评估小组成员与分工 (1)3、范围 (1)4、可接受标准 (1)5、物料供应商分级 (1)5.1 风险识别 (1)5.2 风险分析 (2)5.3 风险评估 (2)5.4 风险控制 (2)5.5 物料供应商的分级 (3)5.6 风险控制措施的确认及剩余风险的确认 (7)5.7 偏差及处理 (8)6、结论 (8)7、风险评估报告的审批 (9)1、目的物料是保证药品质量的基本要素之一, 物料的管理特别是供应商的管理在制药企业 质量管理过程中起着越来越重要的作用, 供应商的管理体系能够确保在药品生产过程中 使用质量合格的物料和优质的服务。
供应商的管理是物料管理的源头, 也是产品质量持 续稳定的关键一环,因此对供应商应严格管理,降低其质量风险,保证药品质量。
企业根据物料性质、物料用量以及将物料对于产品质量影响程度综合考虑物料风 险,对物料进行分级, 根据风险评估的结果确认不同级别物料的供应商潜在的风险,从 而制定相应的控制措施以最大限度地降低风险。
依据对物料供应商的风险识别和风险评估, 确定不同级别供应商的管理体系, 同时 对经确认及采取管理措施后的供应商剩余风险再评价, 证实对供应商的风险已进行了有 效管理。
2、风险评估小组成员与分工3、范围本风险评估合用于物料供应商的风险评估。
4、可接受标准除非另有说明,本评估报告执行公司《质量风险管理制度》(编号: SMP-ZL-003) 中制定的风险评价/风险可接受准则。
5、物料供应商风险评定及控制 5.1 风险识别目的: 目的是针对风险疑问或者问题,获得已知和潜在的危(wei )险清单。
方法: 企业根据物料性质、 物料用量以及将物料对于产品质量影响程度综合考虑物料风 险,在物料管理中,供应商的管理和控制标准等是重要环节,采用失败模式效果分析职责组织风险评估小组对风险进行评估确认, 编制并提交风 险评估报告。
物料部门风险评估报告
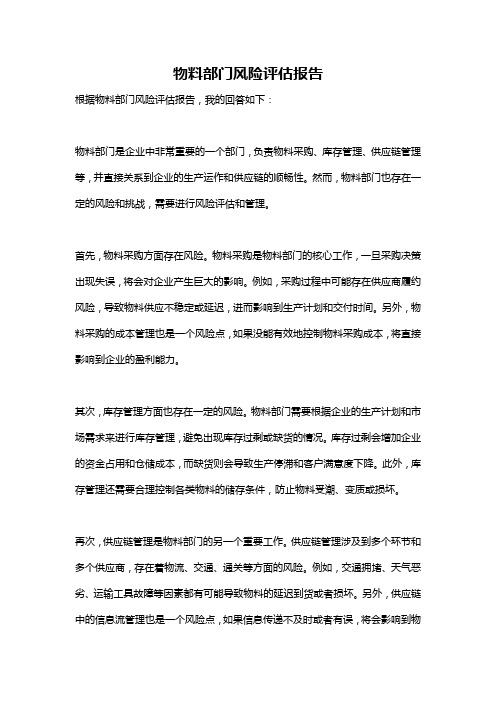
物料部门风险评估报告根据物料部门风险评估报告,我的回答如下:物料部门是企业中非常重要的一个部门,负责物料采购、库存管理、供应链管理等,并直接关系到企业的生产运作和供应链的顺畅性。
然而,物料部门也存在一定的风险和挑战,需要进行风险评估和管理。
首先,物料采购方面存在风险。
物料采购是物料部门的核心工作,一旦采购决策出现失误,将会对企业产生巨大的影响。
例如,采购过程中可能存在供应商履约风险,导致物料供应不稳定或延迟,进而影响到生产计划和交付时间。
另外,物料采购的成本管理也是一个风险点,如果没能有效地控制物料采购成本,将直接影响到企业的盈利能力。
其次,库存管理方面也存在一定的风险。
物料部门需要根据企业的生产计划和市场需求来进行库存管理,避免出现库存过剩或缺货的情况。
库存过剩会增加企业的资金占用和仓储成本,而缺货则会导致生产停滞和客户满意度下降。
此外,库存管理还需要合理控制各类物料的储存条件,防止物料受潮、变质或损坏。
再次,供应链管理是物料部门的另一个重要工作。
供应链管理涉及到多个环节和多个供应商,存在着物流、交通、通关等方面的风险。
例如,交通拥堵、天气恶劣、运输工具故障等因素都有可能导致物料的延迟到货或者损坏。
另外,供应链中的信息流管理也是一个风险点,如果信息传递不及时或者有误,将会影响到物料的采购和供应计划。
除了以上风险外,物料部门还可能面临人员流失风险。
物料部门一般需要具备一定的专业知识和技能,特别是在供应链和采购方面。
如果物料部门的核心人员流失,并且没有及时进行人员补充和培训,将对物料部门的正常运转和业务发展造成较大的影响。
针对以上风险,物料部门可以采取以下措施进行风险管理:首先,在物料采购方面,建立供应商评估制度,评估供应商的能力和履约情况,并与供应商签订明确的合同和协议。
同时,引入采购管理系统,实现采购过程的自动化和规范化,减少人为错误和风险。
其次,在库存管理方面,建立合理的库存管理制度,根据生产计划和市场需求进行库存控制。
#仓库与物料系统风险评估应用案例 FMEA实例分析
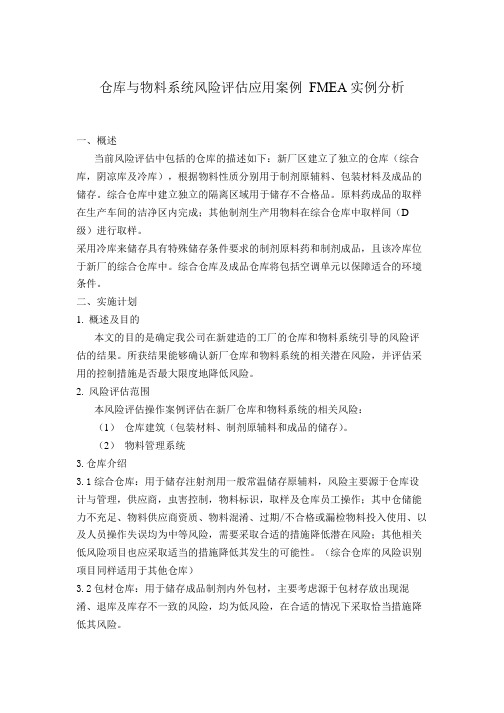
仓库与物料系统风险评估应用案例FMEA实例分析一、概述当前风险评估中包括的仓库的描述如下:新厂区建立了独立的仓库(综合库,阴凉库及冷库),根据物料性质分别用于制剂原辅料、包装材料及成品的储存。
综合仓库中建立独立的隔离区域用于储存不合格品。
原料药成品的取样在生产车间的洁净区内完成;其他制剂生产用物料在综合仓库中取样间(D 级)进行取样。
采用冷库来储存具有特殊储存条件要求的制剂原料药和制剂成品,且该冷库位于新厂的综合仓库中。
综合仓库及成品仓库将包括空调单元以保障适合的环境条件。
二、实施计划1. 概述及目的本文的目的是确定我公司在新建造的工厂的仓库和物料系统引导的风险评估的结果。
所获结果能够确认新厂仓库和物料系统的相关潜在风险,并评估采用的控制措施是否最大限度地降低风险。
2. 风险评估范围本风险评估操作案例评估在新厂仓库和物料系统的相关风险:(1)仓库建筑(包装材料、制剂原辅料和成品的储存)。
(2)物料管理系统3.仓库介绍3.1综合仓库:用于储存注射剂用一般常温储存原辅料,风险主要源于仓库设计与管理,供应商,虫害控制,物料标识,取样及仓库员工操作;其中仓储能力不充足、物料供应商资质、物料混淆、过期/不合格或漏检物料投入使用、以及人员操作失误均为中等风险,需要采取合适的措施降低潜在风险;其他相关低风险项目也应采取适当的措施降低其发生的可能性。
(综合仓库的风险识别项目同样适用于其他仓库)3.2包材仓库:用于储存成品制剂内外包材,主要考虑源于包材存放出现混淆、退库及库存不一致的风险,均为低风险,在合适的情况下采取恰当措施降低其风险。
3.3阴凉库:用于常温条件下存放的成品储存,针对成品阴凉库而言,成品出货批次混淆、产品质量及下游客户资质均有中等程度的风险,需要采取合适的措施控制潜在风险,减少对成品质量或企业经济造成负面影响。
3.4冷库:用于储存对温度敏感的注射剂用原料药(*****)与成品冻干粉(*****),基于产品特性,冷库设计及人员操作均有中等程度的风险,需要采取合适的措施控制风险等级,降低对产品潜在的风险。
物料安全等级风险评估报告

1.概述:根据《药品生产质量管理规范》2010年修订第X章第X条规定:应当根据科学知识及经验对物料供应商进行评估,以确定物料的安全等级而进行的风险评估。
2.目的:通过风险评估,确认本公司药品生产使用物料的安全等级。
3.范围:本企业药品生产过程中使用所有物料。
4.风险评估:
根据物料的安全等级分为A、B、C三级:
A级:对药品质量及安全用药有重要影响。
B级:对药品质量及安全用药有影响,但程度有限。
C级:对药品质量及安全用药有基本没有影响。
合格物料供应商安全等级风险评估
主要物料供应商评估表
表单使用说明
1、上述资源商评价表各项评价指标总分为100分,根据得分确定供应商等级;
计算公式:
供应商总得分=总体情况得分+ 生产制造得分+ 技术研发得分+ 质量管理得分+ 物流交货得分+ 原材料采购得分+ 环保安全得分
评分时应注意以下事项:
●质量保证部组织相关部门对供应商进行评分时,对于每一评分项应有足够的事例或者数据作为支撑,并随打分结果一起提交;
●评分由质量保证组织供应、仓库部等部门举行,可以研讨会的形式进行;
●对于不能明确作出评分决定的事项(如数据不足等),可由部门联合讨论后决定,并进行必要的补充说明和标注;
2、公司对供应商分为3个等级,其对应标准如下:。
- 1、下载文档前请自行甄别文档内容的完整性,平台不提供额外的编辑、内容补充、找答案等附加服务。
- 2、"仅部分预览"的文档,不可在线预览部分如存在完整性等问题,可反馈申请退款(可完整预览的文档不适用该条件!)。
- 3、如文档侵犯您的权益,请联系客服反馈,我们会尽快为您处理(人工客服工作时间:9:00-18:30)。
实例一
物料仓储系统风险分析报告
目录
一、简介 (2)
二、成立风险管理小组 (2)
三、流程及日程安排 (2)
四、现状调查 (3)
五、风险识别 (9)
六、风险分析及评价 (8)
七、风险控制 (33)
八、总结和结论 (36)
九、附件 (36)
十、变更历史 (36)
一、简介
以下为物料仓储系统操作简要流程图:
物料仓储系统风险分析工作由2011年11月09日开始,至11月30日结束,参与部门包括质量部、后勤部。
现将风险分析工作总结如下。
二、成立风险管理小组
三、流程及日程安排
1.风险评估流程图:
采用EU GMP2008-附录20《质量风险管理》以及ICH-Q9《质量风险管理》指南的流程对物料仓储系统进行风险评估。
①、现状调查:收集物料仓储系统的相关信息,包括库区分布、设施、物料接收、物料贮存、物料发放流程控制点,岗位人员配置情况及控制参数等。
②、风险识别:根据物料仓储系统实际情况、操作流程等信息,分析仓储系统可能出现的失效模式,失效模式可能产生的影响、危害,危害的严重程度、发生的可能性、可检测性等,并计算各种失效模式的风险指数,根据风险指数的大小进行排序、分级。
③、风险分析:针对风险等级为高、中级的失效模式分析失效原因,对失效原因发生的可能性、可检测性进行调查、评估,制作失效原因的风险指数排序表,对失效原因进行风险分级。
④、风险评价:确定可接受风险的RPN值,并确定必须制定改进措施的失效原因。
⑤、风险控制:针对失效原因制定改进措施,对改进措施实施后仍残留的风险进行预评估。
应将所有失效原因的风险指数(RPN 值)降至可接受水平,否则需重新进行风险分析、评价、控制的循环。
⑥、总结报告:当风险降至可接受水平后,对风险分析全过程进行总结,形成书面报告。
2.日程安排
四、现状调查
2011年11月09日,由风险管理小组共同完成了对物料仓储系统当前现状的调查,现将调查情况汇总如下。
1、库区及设施布局
以下为物料仓储系统库区分布图及设施分布简图。
以下为包材库区平面图(一):
以下为包材库区平面图(二):
以下为原辅料库区平面图:
2、物料库区硬件设施
库区设有空调、排风机、除湿机,确保所有物料贮存符合要求。
库区温度超标,可开启空调降温除湿,待温度下降到合格范围内关闭空调;库区湿度超标,可开启除湿机、排风机,对与外界通风换气,降低湿度。
电子灭蚊器,驱除飞行类昆虫;电子驱虫器驱除爬行类昆虫;挡鼠板阻挡爬行类昆虫通过缝隙进入库区;捕鼠笼起到抓捕鼠类的作用,防止物料被虫鼠损坏污染。
3、物料接收、贮存、发放操作流程
物料接收与贮存:对物料进行初验,初验合格后办理入库送检,根据检验结果更换物料状态标示。
具体流程如下:
发放:物料库管员根据车间领料员开具的领料单发放物料,库管员收到领料单后审核其品名、规格、数量是否正确,在领料单上填写正确的数量,进厂编号、批号、厂家等信息及检验报告单,一并交车间领料员及生产岗位。
具体流程如下:
4、温湿度控制点
5、状态标识
物料仓储系统设有三色状态标识和物料库存货位卡:黄色待验,绿色合格,红色不合格。
物料库存货位卡:标明物料名称、规格、批号、进厂编码、货位、有效期、生产厂家、供货商、取样日期、取样件数、取样数量、合格件数、合格数量、合格日期、复验日期、复验合格日期。
6、物料仓储系统人员情况
物料仓储系统共有员工27人:其中状态工11人,清洁工3人,库管员13人。
状态工三班制,其余为常白班。
所有人员均经培训后上岗,培训内容包括岗位操作规程、安全操作规程等。
五、风险识别
2011年11月11日,物料仓储系统风险管理小组召开了第二次会议,对物料仓储系统可能出现的失效模式进行分析、讨论。
物料接收,来源必须是质量部批准的供应商,专门的物料卸货区域停靠。
原辅料、直接接触药品的内包装材料初验内容应包括:包装形式、外包装清洁度、密封度、完整性、凭证齐全性、原辅料贮藏条件、原辅料批准文号、有效期、有无破损等;印刷性包装材料必须与药品监督管理部门批准的内容、式样、文字相一致,应与质量部签发印刷性包装材料使用通知单核对。
物料接收工作流程为:到货→外观质量验收→票据验收→数量验收→卸货。
物料贮存,堆码要求:应离墙(原辅料要求离地)、分批号堆码,批次之间留有一定距离,做到后整前零、左右对齐、每垛定量,使物料便于取样检验、盘点、出入和运输要求,防止倒下伤人及其他损失发生;固体、液体、化学性质相反物料应分开贮存,以避免相互污染;挥发性物料应设专库贮存,并安装有排风设施,其贮存条件应避免污染其他物料;有毒、易燃、易爆、易挥发、易制毒化
学品的物料应按其性质另行贮存。
根据物料仓储特点及要求,以及GMP对物料的储存的要求,风险管理小组判断:物料仓储系统中人员,物料接收,物料储存,物料发放流程中,主要风险来源于各流程的操作。
风险管理小组成员使用头脑风暴法,分析了物料仓储系统可能出现的各种偏离正常的偏差,即潜在的失效模式、失效模式可能造成的影响、该影响对产品质量、安全造成的危害以及这些危害的严重程度、危害发生的可能性及可检测性。
(见表一:物料仓储系统潜在失效模式及分析表)
六、风险分析及评价
由于同一种失效模式,可能会对产品质量造成不同影响,而每种影响对使用者健康、安全造成危害的严重程度不一样,危害发生的可能性及可检测性均有差异,故我们取每种不同影响中RNP值最大的作为该种失效模式最终的RPN值,根据RPN值的大小对潜在的失效模式进行排序、分级,最终完成表二:物料仓储系统失效模式风险指数排序表
表二:物料仓储系统失效模式风险指数排序表
说明:RPN值在64以下,风险等级为低;在64~384,风险等级为中等;在384以上风险等级为高。
SO值在30以上,风险等级为高,在30以下,风险等级为低
七、风险控制
2011年11月16日,小组召开第四次会议,讨论失效原因的控制措施,完成了表三:失效原因控制措施及残留风险评估。
物料仓储系统风险分析报告G23-R002 错误!未找到引用
源。
页码:24/38
从以上表格中可看出,如按建议采取的措施去实施,理论分析各失效原因的风险指数均可降至可接受水平。
八、总结和结论
通过本次活动,我们对物料存储系统可能导致产品质量问题的风险进行了识别、分析、制定了控制措施,提高了物料储存系统质量保证能力,对于保证产品质量起到了重要作用。
通过上述分析,可以得出以下结论:
1.我们对仓储系统所有操作规程、中高风险的预防措施以及质量控制手段在内的整个生产质量体系是根据消除、控制上述风险设计并实施的,质量体系可控;
2.对中高风险采取措施,每月将不定期对其效果进行检查,如未达到预期效果,即风险没有降至可接受水平,应重新制定措施;
3.如物料仓储系统有任何环境、设备、参数等的变更以及在监控过程中出现任何偏差,应重新对其进行风险评估。
九、附件
十、变更历史
变更前版本号变更后版本号变更原因变更批准日期--- --- --- ---。