失效分析技术基本知识和应用
失效分析

失效分析提高机械产品信誉,必须使机械产品牢固可靠,可是在技术上要求机械产品达到100%的可靠性是不可能的,所以要求尽可能地降低机械产品的事故率。
因为机械产品在使用过程中常常发生断裂、变形、磨损、腐蚀等失效现象的发生,找出失效原因和提出改进措施,必须开展失效分析实例的研究。
目前,随着现代科学技术的飞跃发展,失效分析已经成为一门综合性学科。
它不仅与断裂力学、断裂物理、断口学等学科相关联,而且还涉及产品质量全面管理等领域。
失效1失效的基本概念失效是指机械或机械零件在使用过程中(或者是在使用前的试验过程中),由于尺寸、形状、材料的性能或组织发生变化而引起的机械或机械零件部件不能完满地完成指定的功能,或者机械构件丧失了原设计功能的现象。
常见的失效形式可分为下列四种:弹性变形失效;塑性变形失效;破断或断裂失效;材料变化引起的失效。
机械或机械零部件失效部位可出现如下两种情况:物体内部缺陷引起的失效;物体表面缺陷引起的失效。
2 失效的形式及其类型失效的分类比较复杂,在这里不可能一一作介绍,本文按失效机理将失效分为:断裂失效;变形失效;磨损失效;腐蚀失效等四种类型。
(1)断裂失效(其中包括破断失效)断裂是指金属,或合金材料,或机械产品的一个具有有限面积的几何表面的分离过程。
它是个动态的变化过程,包括裂纹的萌生及扩展过程。
断裂失效是指机械构件由于断裂而引起的机械设备产品不能完成原设计所指定的功能。
断裂失效类型有如下几种:①解理断裂失效;②韧窝破断失效;③准解理断裂失效;④滑移分离失效;⑤疲劳断裂失效;⑥蠕变断裂失效;⑦应力腐蚀断裂失效;⑧液态或固态金属脆性断裂失效;⑨氢脆断裂失效;⑩沿晶断裂失效;○11其他断裂失效等。
(2)变形失效所谓变形通常是指机械构件在外力作用下,其形状和尺寸发生变化的现象。
从微观上讲是指金属材料在外力作用下,其晶格产生畸变。
若外力消除,晶格畸变亦消除时,这种变形为弹性变形;若外力消除,晶格不能恢复原样,即畸变不能消除时,称这种变形为塑性变形。
失效分析知识点

失效分析知识点第一章概论1.失效的定义:当这些零件失去其应有的功能时,则称该零件失效。
2.失效三种情况:(1).零件由于断裂、腐蚀、磨损、变形等从而完全丧失其功能;(2).零件在外部环境作用下,部分的失去其原有功能,虽然能工作,但不能完成规定功能,如由于磨损导致尺寸超差等;(3).零件能够工作,也能完成规定功能,但继续使用时,不能确保安全可靠性。
3. 失效分析定义:对失效产品为寻找失效原因和预防措施所进行的一切技术活动。
也就是研究失效的特征和规律,从而找出失效的模式和原因。
4. 失效分析过程:事前分析(预防失效事件的发生)、事中分析(防止运行中设备发生故障)、事后分析(找出某个系统或零件失效的原因)。
5. 失效分析的意义:(1).失效分析的社会经济效益:失效将造成巨大的经济损失;质量低劣、寿命短导致重大经济损失;提高设备运行和使用的安全性。
(2).失效分析有助于提高管理水平和促进产品质量提高;(3).失效分析有助于分清责任和保护用户(生产者)利益;(4).失效分析是修订产品技术规范及标准的依据;(5).失效分析对材料科学与工程的促进作用:材料强度与断裂;材料开发与工程应用。
第二章失效分析基础知识一.机械零件失效形式与来源:1.按照失效的外部形态分类:(1)过量变形失效:扭曲、拉长等。
原因:在一定载荷下发生过量变形,零件失去应有功能不能正常使用。
(2)断裂失效:一次加载断裂(静载荷):由于载荷或应力超过当时材料的承载能力而引起;环境介质引起的断裂:环境介质和应力共同作用引起的低应力脆断;疲劳断裂(交变载荷):由于周期作用力引起的低应力破坏。
(3)表面损伤失效:磨损:由于两物体接触表面在接触应力下有相对运动,造成材料流失所引起的一种失效形式;腐蚀: 环境气氛的化学和电化学作用引起。
(4).注:断裂的其他分类断裂时变形量大小:脆性断裂、延性断裂;裂纹走向与晶相组织的关系:穿晶断裂、沿晶断裂;2.失效的来源:(1).设计的问题:高应力部位存在沟槽、机械缺口及圆角半径过小等;应力计算错误;设计判据不正确。
失效分析基础知识
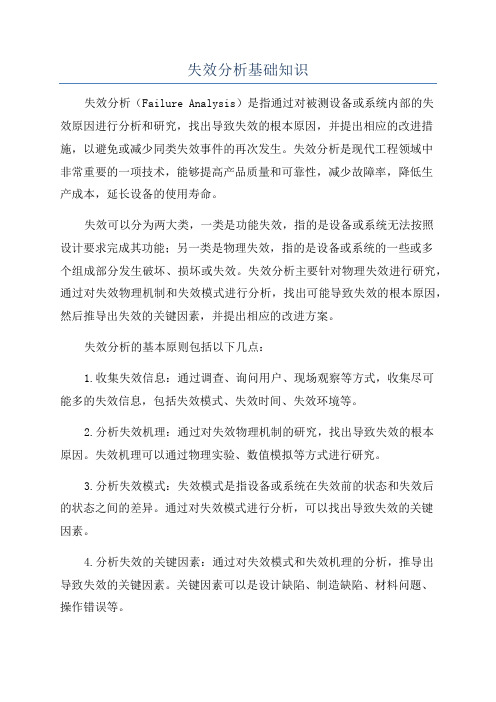
失效分析基础知识失效分析(Failure Analysis)是指通过对被测设备或系统内部的失效原因进行分析和研究,找出导致失效的根本原因,并提出相应的改进措施,以避免或减少同类失效事件的再次发生。
失效分析是现代工程领域中非常重要的一项技术,能够提高产品质量和可靠性,减少故障率,降低生产成本,延长设备的使用寿命。
失效可以分为两大类,一类是功能失效,指的是设备或系统无法按照设计要求完成其功能;另一类是物理失效,指的是设备或系统的一些或多个组成部分发生破坏、损坏或失效。
失效分析主要针对物理失效进行研究,通过对失效物理机制和失效模式进行分析,找出可能导致失效的根本原因,然后推导出失效的关键因素,并提出相应的改进方案。
失效分析的基本原则包括以下几点:1.收集失效信息:通过调查、询问用户、现场观察等方式,收集尽可能多的失效信息,包括失效模式、失效时间、失效环境等。
2.分析失效机理:通过对失效物理机制的研究,找出导致失效的根本原因。
失效机理可以通过物理实验、数值模拟等方式进行研究。
3.分析失效模式:失效模式是指设备或系统在失效前的状态和失效后的状态之间的差异。
通过对失效模式进行分析,可以找出导致失效的关键因素。
4.分析失效的关键因素:通过对失效模式和失效机理的分析,推导出导致失效的关键因素。
关键因素可以是设计缺陷、制造缺陷、材料问题、操作错误等。
5.提出改进措施:根据分析结果,提出相应的改进措施,包括设计改进、制造改进、材料改进、操作改进等。
改进措施应该能够消除或减少导致失效的关键因素,从而提高设备或系统的可靠性和安全性。
失效分析常用的方法和技术包括材料分析、断口分析、显微分析、化学分析、热分析、电子显微镜观察等。
这些方法和技术可以帮助工程师深入了解失效的原因和机制,从而提出有效的改进措施。
失效分析在工程领域中具有广泛的应用,包括电子设备、机械设备、化工设备、航空航天设备等各个领域。
通过对失效进行分析和研究,可以提高产品的可靠性和质量,减少故障率,降低生产成本,延长设备的使用寿命。
失效分析基础课件

失效影响评估方法
采用定性和定量评估方法 ,如风险矩阵、故障树分 析等,对失效影响进行评 估。
失效模式与影响分析的实践方法
收集数据
收集产品或系统的使用数据、 维护数据、故障数据等。
分析失效原因
根据分析模型,分析失效的原 因和机理。
制定分析计划
明确分析目标、范围和时间计 划。
建立分析模型
根据实际情况建立适当的分析 模型,如故障树模型、事件树 模型等。
。
监控改进效果
对改进后的产品进行监控,确 保改进措施有效,持续改进产
品质量。
案例分析:失效分析在产品质量改进中的应用
案例一
某电子产品在生产过程中出现大量失效现象,通过失效分析发现是某元器件质量问题导致 的。针对这一问题,企业更换了该元器件供应商,并对生产线进行了优化,有效提高了产 品质量。
案例二
某机械产品在使用过程中频繁出现故障,通过失效分析发现是设计缺陷导致的。企业针对 这一问题对产品设计进行了改进,并加强了生产过程中的质量控制,有效减少了故障率。
常见失效原因及其应对措施
机械疲劳
磨损
由于长时间或高频率的机械应力作用导致 的失效。应对措施包括优化设计、减少应 力集中、提高材料强度等。
由于摩擦或侵蚀导致的失效。应对措施包 括选用耐磨材料、降低摩擦系数、定期维 护等。
腐蚀
老化
由于化学或电化学反应导致的失效。应对 措施包括选用耐腐蚀材料、控制环境湿度 、定期清理等。
多学科交叉
失效分析涉及多个学科领域,如材料科学、机械 工程、电子工程等,未来将更加注重多学科交叉 ,综合应用各领域知识。
在线监测和预测
实时在线监测技术将得到更广泛应用,实现对产 品失效的实时预警和预测,提前发现潜在问题。
失效分析基础知识.doc
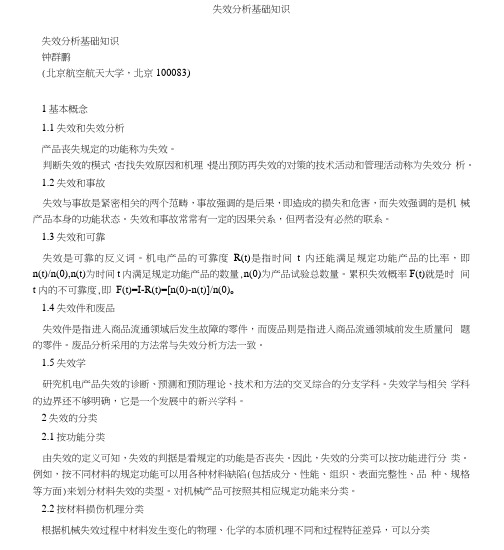
失效分析基础知识失效分析基础知识钟群鹏(北京航空航天大学,北京100083)1基本概念1.1失效和失效分析产品丧失规定的功能称为失效。
判断失效的模式,杏找失效原因和机理,提出预防再失效的对策的技术活动和管理活动称为失效分析。
1.2失效和事故失效与事故是紧密相关的两个范畴,事故强调的是后果,即造成的损失和危害,而失效强调的是机械产品本身的功能状态。
失效和事故常常有一定的因果关系,但两者没有必然的联系。
1.3失效和可靠失效是可靠的反义词。
机电产品的可靠度R(t)是指时间t内还能满足规定功能产品的比率,即n(t)/n(0),n(t)为时间t内满足规定功能产品的数量,n(0)为产品试验总数量。
累积失效概率F(t)就是时间t 内的不可靠度,即F(t)=I-R(t)=[n(0)-n(t)]/n(0)o1.4失效件和废品失效件是指进入商品流通领域后发生故障的零件,而废品则是指进入商品流通领域前发生质量问题的零件。
废品分析采用的方法常与失效分析方法一致。
1.5失效学研究机电产品失效的诊断、预测和预防理论、技术和方法的交叉综合的分支学科。
失效学与相关学科的边界还不够明确,它是一个发展中的新兴学科。
2失效的分类2.1按功能分类由失效的定义可知,失效的判据是看规定的功能是否丧失。
因此,失效的分类可以按功能进行分类。
例如,按不同材料的规定功能可以用各种材料缺陷(包括成分、性能、组织、表面完整性、品种、规格等方面)来划分材料失效的类型。
对机械产品可按照其相应规定功能来分类。
2.2按材料损伤机理分类根据机械失效过程中材料发生变化的物理、化学的本质机理不同和过程特征差异,可以分类如图1所示。
图1失效的分类2.3按机械失效的时间特征分类(1)早期失效可分为偶然早期失效和耗损期失效。
(2)突发失效可分为渐进(渐变)失效和间歇失效。
2.4按机械失效的后果分类(1)部分失效(2)完全失效(3)轻度失效(4)危险性(严重)失效(5)灾难性(致命)失效3失效分析的分类失效分析的分类一般按分析的目的不同可分为:(1)狭义的失效分析主要目的在于找出引起产品失效的直接原因。
失效分析技术

1.1 失效分析的基本概念
目的: 确定失效模式和失效机理,提出纠正 措施,防止这种失效模式和失效机理重复出 现。
失效模式:指观察到的失效现象、失效形式, 如开路、短路、参数漂移、功能失效等。
失效机理:指失效的物理化学过程,如疲劳、 腐蚀和过应力等。
引起开路失效的主要原因:
过电损伤、静电击穿(SEM、图示仪)、金 属电迁移、金属的化学腐蚀、压焊点脱落、 闩锁效应。
1.4.2收集失效现场数据的主要内容
失效环境、失效应力、失效发生期以及失效 样品在失效前后的电测试结果。
失效环境包括:温度、湿度、电源环境、 元器件在电路图上的位置和所受电偏置的 情况。
失效应力包括:电应力、温度应力、机械 应力、气候应力和辐射应力。
失效发生期包括:失效样品的经历、失效 时间处于早期失效、随机失效或磨损失效。
(ESD)、闩锁(Latch up)等。 2、应力-时间模型 (适于缓慢退化)
失效原因:应力的时间积累效应,特性变化 超差。
例如:金属电迁移、腐蚀、热疲劳等。
3、温度应力-时间模型 反应速度符合下面的规律
dM
பைடு நூலகம்
E
Ae kT
dt
(M是温度敏感参数,E是 与失效机理有关的激活能)
积分
E
M t M 0 Ae kT (t t0 )
(﹡十度法则:从室温开始,每提高10度,寿命减半)
产品平均寿命的估算
dM
L C
dt
lnL
E
L AekT
E
B
ln L B
kT
1
1
T1
T2
1.2失效分析的重要意义
电子元器件研制阶段 纠正设计和研制中的错误,缩短研制周期
失效分析基本常识以及操作流程概要
失效分析基本常识以及操作流程概要失效分析是一种通过对可能导致系统、设备或产品失效的原因进行分析,找出失效根本原因并采取措施来防止或解决失效问题的方法。
它是广泛应用于各个行业的一种科学技术手段,可以提高产品和系统的可靠性、安全性和稳定性。
失效分析的基本常识包括以下几个方面:1.失效模式与失效机理:失效模式是指系统、设备或产品发生失效的表现形式,如断裂、腐蚀或短路等。
失效机理是导致失效发生的物理或化学过程,如疲劳、腐蚀或热膨胀等。
2.失效根本原因:失效根本原因是导致失效机理发生的根本问题,可以是设计缺陷、材料问题、工艺不良或使用误操作等。
3.失效分析方法:失效分析可以采用多种方法,如故障树分析、事件树分析、失效模式与效应分析(FMEA)和故障模式与效应分析(FMECA)等。
这些方法可以帮助确定失效发生的可能原因、失效的后果以及防止或解决失效的措施。
4.失效分析工具:失效分析可以借助一些工具来进行,如故障记录、故障数据分析、实验测试和仿真模拟等。
这些工具可以提供有关失效发生的详细信息,以便进行有效的分析和解决。
失效分析的操作流程概要如下:1.收集失效信息:首先需要收集与失效相关的信息,包括失效模式、失效机理、失效数据和相关报告等。
2.确定失效根本原因:通过对失效信息进行分析,确定失效的根本原因。
可以采用故障树分析等方法来帮助确定可能的失效原因。
3.评估失效后果:评估失效的后果,包括人员伤害、财产损失和环境影响等。
可以采用FMEA和FMECA等方法来评估失效的后果。
4.制定措施:根据失效的根本原因和后果,制定相应的措施来防止或解决失效问题。
这些措施可以包括改进设计、优化工艺、更换材料或提供培训等。
5.实施措施:根据制定的措施,进行实施。
这可能涉及到产品的改进、工艺的优化或操作人员的培训等。
6.监控效果:监控实施措施的效果,以确保达到预期的目标。
如果发现新的失效问题,需要重新进行失效分析并制定相应的措施。
失效分析在产品设计中的作用
失效分析的流程
收集失效数据
通过实验、测试、用户反馈等方式收集失效案 例。
失效模式识别
对收集到的失效数据进行分类和模式识别,确 定失效模式。
原因分析
分析失效模式产生的原因,包括设计、材料、 工艺、环境等因素。
失效分析的方法
故障树分析法
通过建立故障树,对系统失效进 行逻辑分析和原因推断。
失效模式影响分析法
通过失效分析,可以了解产品在不同使用条件下的寿命,从而为产品设计提供依据,确保产品在预期使用条件下 具有较长的使用寿命。
评估产品可靠性和安全性
失效分析可以评估产品的可靠性和安全性,发现潜在的失效模式和原因,为改进产品设计提供依据,提高产品的 可靠性和安全性。
提高产品设计质量
优化产品设计
通过失效分析,可以发现产品设计的 不足之处,提出改进措施,优化产品 设计,提高产品的设计质量。
通过失效分析,可以发现产品中潜在的薄弱环节,从而优化 设计,提高产品的可靠性和稳定性。
提高产品质量
失效分析有助于识别产品中存在的问题,及时改进设计,从 而提高产品质量,降低产品故障率。
降低维护成本
通过失效分析,可以预测产品的寿命和维修周期,合理安排 维护和更换计划,从而降低维护成本。
案例二:机械产品失效分析
确保产品符合设计要求
失效分析可以评估产品是否符合设计 要求,发现产品设计中的缺陷或不符 合设计要求的地方,及时进行修正, 确保产品设计的有效性。
优化产品设计方案
确定最佳设计方案
通过失效分析,可以比较不同设计方案之间的优劣,确定最佳设计方案,提高 产品的性能和可靠性。
减少设计风险
失效分析可以评估不同设计方案的风险,避免设计中的潜在风险,减少产品设 计方案的失败概率。
失效分析基本常识以和操作流程图
7/26/2019
25
6.0 操作流程-6
上传到OA存档/供查阅
7/26/2019
26
7.0 注意事项
先了解再鉴定 先方案再操作 先无损再破坏
先了解准确、详尽的使用 信息,通常需要使用方配 合。
根据失效现象,制定方案 后再进行分析。检查分析 过程中可以修订分析方案。
失效分析的基本原则。先 确认所有无损检验完成后, 在进行半破坏和破坏分析。
提交分析报告
任务来源 分析过程
背景描述
分析结果
记录和图片 综合评审
分析实质原因 提出纠正措施
工艺
设计结构 材料
测试方法 使用条件 质量控制
7/26/2019
21
6.0 操作流程-1
7/26/2019
22
6.0 操作流程-2
7/26/2019
23
6.0 操作流程-3
7/26/2019
24
6.0 操作流程-4
先观察后测试
先进行外观检查再做参数 测试和功能测试。
7/26/2019
27
7.0 注意事项
先宏观再微观
先检查整体外观和功能, 再检查局部外观与功能。
先简单再复杂
先做简单的项目分析,再 进行复杂的项目分析。
先静态后动态 先恢复再分解
7/26/2019
先做空载和常温等常规测 试,再模拟使用条件测试。
先进行模拟实验,尽力恢 复失效功能或参数,再做 分层解剖检查分析。
机械应力的过程。
常见的失效机理有:
表面劣化
插芯端面磨损
材料缺陷
芯片偏心量超标
体内劣化
芯片透镜脏污
设计缺陷
镜架漏光
2失效分析的基本理论和技术
损伤容限设计原则在寿命预估中未考虑裂纹的萌生阶段
4 失效预防与失效评估
耐久性设计
建立在安全寿命设计基础之上 吸收了损伤容限设计的优点 引入了经济维修的概念 利用“概率”方法估算结构使用寿命及维修周期
⑥做分析结论并写出有建设性意见的报告
第二讲 失效分析的基本理论和技术
2. 裂纹分析
裂纹和断口是表述断裂失效过程不同阶段的术语。 在力的作用下,零件表面或内部的连续性遭到破坏而未最
终破断之前称为裂纹,最终破断的断裂面称为断口。 断裂经历裂纹的萌生、扩展直至最终破断等不同阶段。
断裂过程的每一阶段会在断口上留下相应的痕迹、形 貌与特征。
断口分析技术一般应包括分析对象的确定与显示技术、观 察与照相记录技术、识别与诊断技术,定性与定量分析技 术以及仪器与设备的使用技术等。
1 断口观察的原则
目的性与客观性 全面性和典型性 受动性与主动性 感性因素与理性因素
2 断口宏观分析 • 断口宏观分析:指在各种不同照明条件下用肉眼、放大镜和 体视显微镜等对断口进行直接观察与分析。
安全寿命设计并不能保证安全
4 失效预防与失效评估 经典疲劳强度理论
名义应力应变法、局部应力应变法
并未造成事故,但却严重影响飞行训练
许多疲劳裂纹
需对结构进行复杂的检测和维修,使飞 机的经济性变差
可能因少数飞机的个别部件裂纹不可修 理,而使大批飞机提前退役,更会造成极大 的资源浪费
4 失效预防与失效评估 损伤容限设计
但是,一旦造成失效必定造成不同程度上 的损失,有些事故要从根本上进行解决需要付 出诸如改进设计、更换材料等巨大代价。
- 1、下载文档前请自行甄别文档内容的完整性,平台不提供额外的编辑、内容补充、找答案等附加服务。
- 2、"仅部分预览"的文档,不可在线预览部分如存在完整性等问题,可反馈申请退款(可完整预览的文档不适用该条件!)。
- 3、如文档侵犯您的权益,请联系客服反馈,我们会尽快为您处理(人工客服工作时间:9:00-18:30)。
▪ (2)按断裂路径分为穿晶、沿晶和混晶断裂; ▪ (3)按断裂性质分为韧性断裂、脆性断裂和
疲劳断裂。
▪ 在失效分析实践中大都采用这种分类法。
▪ 断裂失效分析是从分析断口的宏观 与微观特征入手,确定断裂失效模式,分析 研究断口形貌特征与材料组织和性能、 零件的受力状态以及环境条件(如温度、 介质等)等之间的关系,揭示断裂失效机理、 原因与规律,进而采取改进措施与预防对 策。
▪ 脆性断裂有解理特征,断口宏观上有闪 闪发光的小刻画或人字。山形花纹,而 微观上有河流条纹、舌状花样等。
▪ 疲劳断裂断口宏观上有时可见沙滩条纹, 微观上有疲劳辉纹。
c. 断口上的粗糙度
▪ 断口的表面实际上由许多微小的 小断面构成,其大小、高度差决 定着断口的粗糙度。不同材料、 不同断裂方式,其断口粗糙度也 不同。
▪ 韧性材料的拉伸断口往往呈杯锥状或呈 45°切断的外形,它的塑性变形是以缩 颈的方式表现出来。即断口与拉伸轴向 最大正应力交角是45°。
▪ 脆性材料的拉伸断口一般与最大拉伸正 应力垂直,断口表面平齐,断口边缘通 常没有剪切“唇口”。断口附近没有缩 颈现象。
▪ 韧性材料的扭转断口呈切断型。 断口与扭转正应力交角也是45°。
▪ 脆性材料的扭转断口呈麻花状, 在纯扭矩的作用下,沿与最大主 应力垂直的方向分离。
e.断口上的冶金缺陷
▪ 夹杂、 ▪ 分层、 ▪ 晶粒粗大、 ▪ 白点、白斑、 ▪ 氧化膜 ▪ 疏松、 ▪ 气孔、 ▪ 撕裂等, ▪ 这些冶金缺陷常可在失效件断口上经宏观或微
观观察而发现。
(3) 断口的宏观观察与微观观察
▪ 剖面观察可观察二次裂纹尖端塑 性区的形态、显微硬度变化、合 金元素有无变化情况等。应用剖 面技术,可帮助分析研究断裂原 因Байду номын сангаас机理之间的关系。
2 韧性断裂失效分析
▪ 2.1 概述 ▪ 韧性断裂又叫延性断裂和塑性
断裂,即零件断裂之前,在断裂部位 出现较为明显的塑性变形。在工程 结构中,韧性断裂一般表现为过载断 裂,即零件危险截面处所承受的实际 应力超过了材料的屈服强度或强度 极限而发生的断裂。
▪ ①断口的宏观观察
▪
指用肉眼、放大镜、低
倍串的光学显微镜(体视显微
镜) ,这是断口分析的第一步和
基础。
▪ 通过宏观观察收集了断口上的宏观信息, 则可初步确定断裂的性质(脆性断裂、 韧性断裂、疲劳断裂、应力腐蚀断裂 等),可以分析裂源的位置和裂纹扩展 方向,可以判断冶金质量和热处理质量 等。
▪ 观察时先用肉眼和低倍率放大镜 观察断口各区的概貌和相互关系, 然后选择细节、加大微细结构。 宏观观察时,尽可能拍照记录。
(2)断口分析的依据
▪ a.断口的颜色与光泽 ▪ 观察断口表面光泽与颜色时,主要观
察有无氧化色的痕迹、有无夹杂物的特殊 色彩与其他颜色。是红锈、黄锈或是其他 颜色的锈蚀灰色的金属光泽、发蓝颜色 (或呈深紫色、紫黑色金属光泽)等。有无 腐蚀是否有深.
▪ 例如,高温工作下的断裂构件,从断口 的颜色可以判断裂纹形成的过程和发展 速度,深黄色是先裂的,蓝色是后裂的; 若两种颜色的距离很靠近,可判断的速 度很快。
▪ 又如,钢件断口若是深灰色的金属光泽, 是钢材的原色,是纯机械断口;断口有 红锈是富氧条件腐蚀的 ;断口有黑锈是 缺氧条件腐蚀的 等
b.断口上的花纹
▪ 不同的断裂类型,在断口上留下 不同形貌的花纹。这些花纹是丰 富多彩的,很多与自然景观相似, 并以其命名。
▪ 韧性断裂宏观有纤维状断口,微观上则 多有韧窝或蛇行花样等。
▪ ②断口的微观观察
▪
用显微镜对断口进行高
放大倍率的观察,用金相显微镜
及扫描电镜的为多。
▪ 断口微观观察包括断口表面的直接 观察及断口剖面的观察。通过微观 观察进一步核实宏观观察收集的信 息,确定断裂的性质、裂源的位置 及裂纹走向、扩展速度,找出断裂 原因及机理等。
▪ 观察时要注意防止片面性;识别 假象、要有真实性;收集的代表 性等。
▪ 一般来说,属于剪切型的韧性断裂的剪 切唇比较光滑;而正断型的纤维区则较 粗糙。
▪ 属于脆性断裂的解理断裂形成的结晶状 断口较粗糙,而准解理断裂形成的瓷状 断口则较光滑。
▪ 疲劳断口的粗糙度与裂纹扩展速度有关 (成正比),扩展速度越快,断口越粗糙。
d. 断口与最大正应力的交角
▪ 不同的应力状态,不同的材料及 外界环境,断口与最大正应力的 交角是不同的。
失效分析技术基本 知识和应用
▪ 引言
一. 断裂失效分析
▪ 机械产品的失效一般可分为非断裂失效与 断裂失效两大类。非断裂失效一般包括磨 损失效、腐蚀失效、变形失效及功能退化 失效等。
▪ 断裂失效是机械产品最主要和最具危险性 的失效,其分类比较复杂,一般有如下几种:
▪ (1)按断裂机理分为、韧窝断裂、蠕变断裂、 解理与准解理断裂、沿晶断裂和疲劳断裂;
▪ 在正常情况下,机载零件的设计都将零 件危险截面处的实际应力控制在材料的 屈服强度以下,一般不会出现韧性断裂失 效。但是,由于机械产品在经历设计、用 材、加工制造、装配直至使用维修的全 过程中,存在着众多环节和各种复杂因素, 因而机械零件的韧性断裂失效至今仍难 完全避免。
▪ ③剖面观察
▪
截取剖面要求有一定的方
向,通常是用与断口表面垂直的平
面来截取(截取时注意保护断口表
面不受任何损伤),垂直于断口表
面有两种切法。
▪ ⅰ.平行裂纹扩展方向截取,则可研 究断裂过程。因为在断口的剖面上, 能包含断裂不同的各区域。
▪ ⅱ.垂直裂纹扩展方向截取,在一定 位置的断口削面上,可研究某一特 定位置的区域。
1. 断口分析
(1)断口分析的重要性
▪ 在断口上忠实地记录了金属断裂时的全过程, 即裂纹的产生、扩展直至开裂;外部因素对裂 纹萌生的影响及材料本身的缺陷对裂纹萌生的 促进作用;
▪ 同时也记录着裂纹扩展的途径、扩展过程及内 外因素对裂纹扩展的影响。简言之,断口上记 录着与裂纹有关的各种信息,通过对这些信息 的分析,可以找出断裂的原因及影响因素。因 此,断口分析在断裂失效分析中占据着特殊重 要的地位。可以说断口分析是断裂失效分析的 核心,同时又是断裂失效分析的向导,指引失 效分析少走弯路。