7 WASTES
7大浪费经典介绍(中英文版)ppt课件
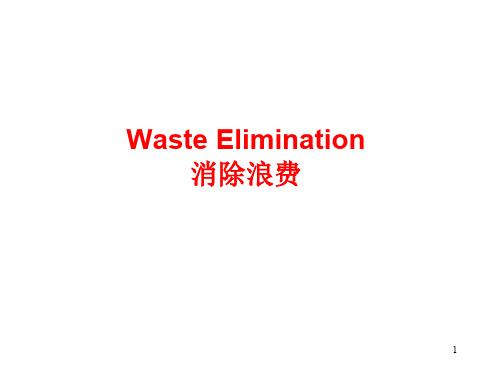
Equipment
Downtime 设备停机时间
Poor layout 糟糕的厂区布局
Supplier Quality 供应商的质量
22
Low Down Inventory To Expose Problem
通过降库存暴露问题
库存水平
维修问题 效率问题 质量问题
交货问题
23
23
Waste of Motion
• Define and discuss value added and non-value added 定义和讨论“增值”与“非增值”
• Identify and discuss ways to eliminate waste 辨认和探讨消除浪费的方法
5
5
Identification of Waste 浪费的识别
Why? 为什么?
Therefore 因此
The greater the resistance 阻力越大
4
To improve we must continuously change 要提高就必须不断改进
For every action (change) there is an equal & opposite reaction 每一次用力(改变)都会有相应的反作用力
磨削工序
11
11
Value Added – Examples
增值案例
Is it Value Added (VA) or Non-Value Added (NVA)?
请判断是否增值?
VA增值 NVA不增值 Cutting operation
切削工序
Grinding operation
Seven_Waste_七大浪废

Seven Wastes
13
Example
搬运的浪费
物料储存区距离使用单位非常远
( 仓库到针车19线有 100 米的距离 )
仓库
结果: 我们必须通知搬运员去哪里取料 我们需要额外的库存区 我们需要额外的物料搬运员和设备
Seven Wastes 14
等待的浪费
定义: 人、机器或产品在 “睡觉” 影响:时间、空间、劳力、潜在的报废、 $$$ 原因:不清楚或没有标准,布置等 • 范例 …………..?
Seven Wastes
15
Waste of Waiting (People) 人的等待
In the above photo, why was this waste generated? 在这个例子中,为什么浪费会产生呢?
Seven Wastes 16
Waste of waiting (machine) 机器的等待
Seven Wastes
29
多余制程的浪费
定义: 在加工或组装产品中,做一些对顾客品质期望不必要的操作工序 • 影响:时间、成本、劳力、$$$ • 原因:不清楚或没有标准 范例 …………..?
Seven Wastes
30
Waste of Over-Process 多余制程的浪费
What causes this waste? 计算半成品的数量. 为什么会产生这样的浪费呢 ?
•
不可避免的不增加价值活动 Incidental 没有增加价值,但在当前的技术及生产条件下无法避免的 生产活动。
•
浪费(不增加价值) Non Value Added – 没有增加价值(改变材料的形状、形式或 功能),且可以立刻消除的活动。
Seven Wastes
Walk By - 7Wastes 7种浪费
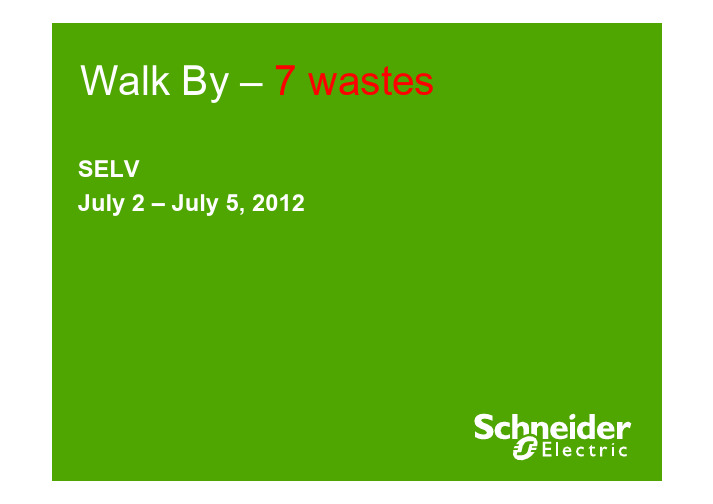
Walk By – 7 wastesSELV July 2 – July 5, 2012Walk-by / Lean Manufacturing / SPSA principle concept of Lean Manufacturing (and SPS) is that most problems are visible and the best improvement ideas will come from people going to the factory floor and observing the problems. A “Walk-by” is a special way to test our own assumptions about what is going on in the process by “seeing” the actual process running. In the SPS, this is the first part of the concept “I SEE, I DO”. More often than not, when we actually “see”, we see that something else is going on than what we expected. The regular Walk-by is, finally, to check whether progress is happening at the desired pace. Walk-by is an essential responsibility of all MBC and DVC employees.Schneider Electric - GST \ SPS – G. PARRINI – 2010 2Walk-by is an essential part of the SPS assessmentWalk-by, during an SPS assessment, is a good opportunity to have the vision of the factory floor from the eyes of a person unfamiliar to the plant. Assessors are not safety experts but each time they “walk-by” they look for safety issues. Most of the issues seen are not expert related issues but simple observations of behavior that could be seen at one moment and may not be observed later. The Schneider plant of Pisek gives the name “Ghost” to those issues highlighted during a Walk-bySchneider Electric - GST \ SPS – G. PARRINI – 20103Walk by is also an extremely effective tool for the identification of waste●During the walk-by…● We see ● We ask why? ●And most of the time the reply is: “That’s an exceptional situation, you will not see it again tomorrow” This is not an acceptable response to a “why” question!Schneider Electric - GST \ SPS – G. PARRINI – 201047 Main wastes (MUDA)WaitingTTransport & HandlingWOverproductionO O D5IInventoryOver processingMMotion Defects & ReworkSchneider Electric - GST \ SPS – G. PARRINI – 2010Waste: Transportation● Two seconds of value added timeWeld Parts, place in bin Move & place bin on trolley Transport trolley to Warehouse Move bins to pallet Wrap pallet● Opportunity to reduce waste, reduce NPV costsTransport pallet to Rack Transport pallet from rack Put in shipping lane Transport pallet to truckSchneider Electric - GST \ SPS – G. PARRINI – 20106Waste: Transportation● Waste of labor ● What if ???????● Subcon shipped 12 trays already on a trolley? ● How much NPV labor can be saved? ● NPV at subcon and in warehouse.“White poles” from subcon received in trays on pallets 120,000 poles per day Trays on the pallet Trays are transferred from pallet to trolley Total number of trolleys Motions per trolley: 1 pull of 7 trays, manual move of 572 poles per tray1,667 trays 7 trays per stack 12 trays per trolley 139 2-3 “pulls” per trolleySchneider Electric - GST \ SPS – G. PARRINI – 20107Waste: Transportation● Is this optimized? Is this productive?Schneider Electric - GST \ SPS – G. PARRINI – 20108Waste: Inventory● Waste of inventory always leads to wasted floor space (square meters)Schneider Electric - GST \ SPS – G. PARRINI – 20109Waste: Inventory● Waste of inventory always leads● Waste of space ● Waste of Moving / TransportationSchneider Electric - GST \ SPS – G. PARRINI – 201010Waste: Motion●Operator must manually remove the welded part before putting in the new parts to be welded●67 Welders do not have auto eject●Time lost = .5 –1.0 secondsExample of Potential Savings Calculation Average welds per machine:5,800X 3 Shifts 17,400X 60 machines 1,044,000Manual eject time .5 seconds Totalopportunity 8,700 minutes 145 hoursCurrent Time spent (60 people X 3 shifts X 8 hours 1,440 hoursProductivity10%Waste: Waiting●Every day that I went to the floor there was a different cell stopped and people waiting.Waitin gWaitin gWaitin gWaitin gIf you have a flexibleworkforce, can’t we findWaitin g Waitin gsomething else for the people to do?Waste: Overproduction●Finished goods inventory–in the factory!!!●It cannot be MTO if you have stock!●MTO MOQ Must = 1Waste: Over-processing●Inspection: human visual inspectionis only good to about 5000 PPM●If we have advancedAutomated equipment, whydo we need a finished goodsampling plan ?●It is hard to be so good●You have an excellent plant●So what does SELV do to improve?See the waste●Even the smallest waste, multiplied many times, can equal huge savings.Challenge everything●Tribal Knowledge & Assumptions●When you are good….●And you have been doing many things the same for along time●It is sometimes hard to question what you are doing.●Challenge everything, challenge the processes,challenge the rules●Think creatively●There is no such thing as a dumb idea.Be creative●“We can’t because…”●The biggest waste in every company is the waste of our employee’s creativity●Involve all of your employees in the change process●Leverage their collective intelligence and their experience●Never talk about why you can not do something●Always talk about how you can do it.Benchmark●Against the best, not the others ●Against internal, but also external。
7S要点简述
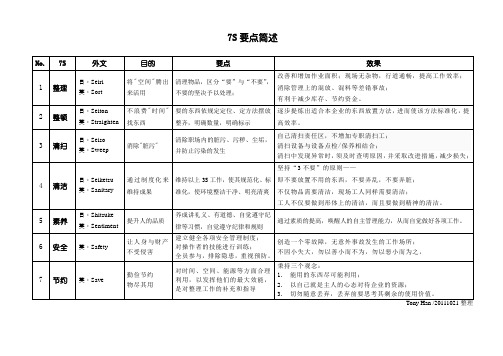
清洁
日:Seiketsu
英:Sanitary
通过制度化来维持成果
维持以上3S工作,使其规范化、标准化,使环境整洁干净、明亮清爽
坚持“3不要”的原则——
即不要放置不用的东西,不要弄乱,不要弄脏;
不仅物品需要清洁,现场工人同样需要清洁;
工人不仅要做到形体上的清洁,而且要做到精神的清洁。
5
素养
日:Shitsuke
7S要点简述
No.
7S
外文
目的
要点
效果
1
整理
日:Seiri
英:Sort
将"空间"腾出来活用
清理物品,区分“要”与“不要”,不要的坚决予以处理;
改善和增加作业面积;现场无杂物,行道通畅,提高工作效有利于减少库存、节约资金。
2
整顿
日:Seiton
英:Straighten
不因小失大,勿以善小而不为,勿以恶小而为之,
7
节约
英:Save
勤俭节约
物尽其用
对时间、空间、能源等方面合理利用,以发挥他们的最大效能,是对整理工作的补充和指导
秉持三个观念:
1.能用的东西尽可能利用;
2.以自己就是主人的心态对待企业的资源;
3.切勿随意丢弃,丢弃前要思考其剩余的使用价值。
Tony Han /20111021整理
英:Sentiment
提升人的品质
养成讲礼义、有道德、自觉遵守纪律等习惯,自觉遵守纪律和规则
通过素质的提高,唤醒人的自主管理能力,从而自觉做好各项工作。
6
安全
英:Safety
让人身与财产不受侵害
建立健全各项安全管理制度;
对操作者的技能进行训练;
LEAN专用词
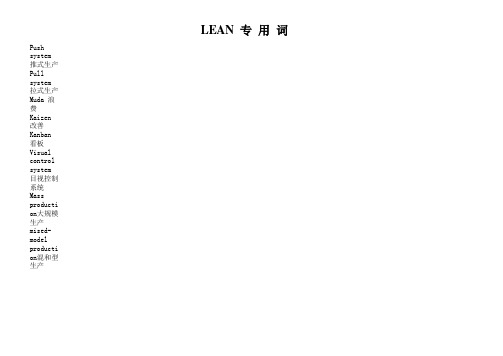
Push system 推式生产 Pull system 拉式生产 Muda 浪费 Kaizen 改善 Kanban 看板Visual control system 目视控制系统 Mass production大规模生产 mised-model production混和型生产one piece flow 单件流程 water spider水蜘蛛 mistake-proofing错误校正 Red tag 红牌TT(Takt time)生产节奏 WIP(work in process) 库存 VSM(value steam map)价值溪流图表格明细:標准作業票Standard Work Sheet多能工表Multi Skilled Sheet改善事例记录本Kaizen Event Record价值流程图Value Stream/Process Flow Chart快速换模/线查核表Quick change over checklist每小時生產管理表EVN Hourly Production Management Sheet生產狀況趨勢圖Production Trend Chart上游单位评估记录表The Status of up stream sub cell/supplier measured材料需求表Material requirement listseven muda七大浪费the seven wastes are overproduction in excess of demand, waiting for the next processing step, unnecessarytransprot of materials, overprocessing of parts due to poor tool and product design, inventories greater than the absolute minimum needed, unnecessary movement by employees during the course of their word,and theproduction of defective partsCEDAC 鱼骨图cause-and -effect diagram with the addition of cards): a significant enhancement to the widely usedIsakawa"fishbone"diagramming technique for problem solvingQCO (Quick Changeover) 快速转换:the installation of a new tool in a metalworking machine.A changeover begins after the last good piece off onerun has been produced(and inspected, if necessary, to confirm that it is good) and ends when the first goodpiece off the new run is producedNon-value-adding非增值Any activity in a production process that is considered wasteful; which is th say, any activity that does notchange material of does not add information to a product or service in a way that the end-user values enoughto pay for.BCS(Build Customer Schedule)计划执行率D2D(Dock to Dock)生産前導時間:a tactical measurement used to indicate the veocity of material in the production process starting with the receipet of raw materials to the shipment of that meterial to a customer orderRFT(right the first time)一次达标率MLT( Manufacturing lead time)制造期:the amount of time nominally taken from the issuance of raw material through the prodution process to thecompletion of the saleable productTPM(Total Productive Maintenance)全员生产保全A Japanese Kaizen Strategy focus on improving the efficiency of machine to gain the overall profit of thecompanyfocused equipment improvement聚焦设备改进:an approach, applied in the later stages of total productive maintenance, that focuses on specific equipment proameters of capabilities so as to improve the overall equipment effectiveness.OEE(overall equipment effectiveness)设备总体有效性the primary metric of total productive maintenance that indicates a single piece of equipment's actualcontribution as a percentage of its potential to add value to the value streamMatrix diagram矩阵图:a graph used to show the relationship between two or more diffrerent factors。
waste是什么意思

waste是什么意思waste表达的意思有很多种,那么你知道waste做动词,名词和形容词分别都有哪些意思吗?下面店铺为大家带来waste的英语意思解释和英语例句,欢迎大家一起学习!waste作名词的意思:浪费,白费,挥霍钱财;废料,废品waste作动词的意思:浪费;徒劳;(使)损耗;(使)消瘦waste作形容词的意思:废弃的,无用的,荒芜的waste的英语音标:英 [weist] 美 [west]waste的时态:现在分词: wasting过去式: wasted过去分词: wastedwaste的英语例句:1. Solid low-level waste will be disposed of deep underground.放射性水平低的固体废料将做地下深埋处理。
2. They make compost out of all kinds of waste.他们用各种废料制造堆肥。
3. Overcrowding has taxed the city's ability to deal with waste.人口过多使得城市的垃圾处理能力达到了极限。
4. The ability to separate out reusable elements from other waste is crucial.能从其他废料中分离出可重复利用成分是很关键的。
5. I think that is a total waste of money.我认为那完全是浪费金钱。
6. The aphid is now laying waste to the wheat and barley fields.蚜虫正在毁掉一片片的小麦和大麦田地。
7. I'm not one to waste time on just anyone.我可不是个随便浪费时间在任何人身上的人。
8. You could waste your whole life on a pipe-dream.白日梦会荒废你一生。
Seven MODAS七种浪费
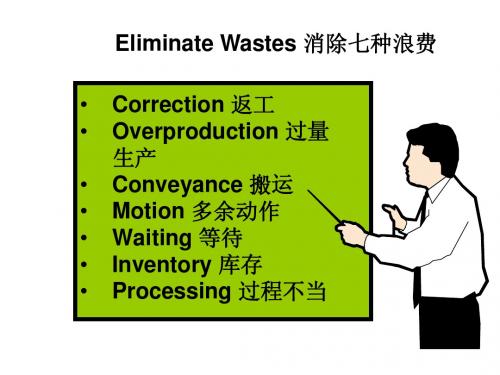
Eliminate Wastes 消除七种浪费 • • • • • • • Correction 返工 Overproduction 过量 生产 Conveyance 搬运 Motion 多余动作 Waiting 等待 Inventory 库存 Processing 过程不当
Definition of Wastes 什么是浪 费?
一切物料搬运
活动
Waste of Material Movement Conveyance 物料搬运
Characteristics特征:
• • • • • Extra Fork Trucks Multiple Storage Locations Extra Facility Space Incorrect Inventory Counts Opportunity for Damage 多余的叉车,空间,物品损坏
• Incapable Processes / 能力不足 • Operator Control Error / 操作不当 • Insufficient Training / 培训不足
7SEA
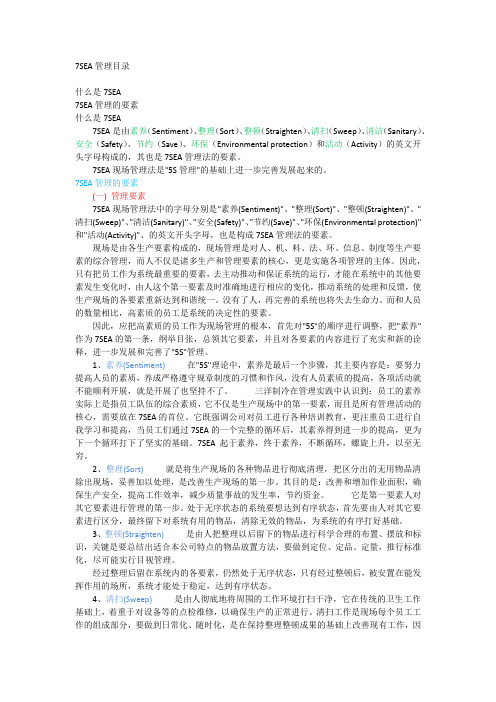
7SEA管理目录什么是7SEA7SEA管理的要素什么是7SEA7SEA是由素养(Sentiment)、整理(Sort)、整顿(Straighten)、清扫(Sweep)、清洁(Sanitary)、安全(Safety)、节约(Save)、环保(Environmental protection)和活动(Activity)的英文开头字母构成的,其也是7SEA管理法的要素。
7SEA现场管理法是"5S管理"的基础上进一步完善发展起来的。
7SEA管理的要素(一) 管理要素7SEA现场管理法中的字母分别是"素养(Sentiment)"、"整理(Sort)"、"整顿(Straighten)"、"清扫(Sweep)"、"清洁(Sanitary)"、"安全(Safety)"、"节约(Save)"、"环保(Environmental protection)"和"活动(Activity)"、的英文开头字母,也是构成7SEA管理法的要素。
现场是由各生产要素构成的,现场管理是对人、机、料、法、环、信息、制度等生产要素的综合管理,而人不仅是诸多生产和管理要素的核心,更是实施各项管理的主体。
因此,只有把员工作为系统最重要的要素,去主动推动和保证系统的运行,才能在系统中的其他要素发生变化时,由人这个第一要素及时准确地进行相应的变化,推动系统的处理和反馈,使生产现场的各要素重新达到和谐统一。
没有了人,再完善的系统也将失去生命力。
而和人员的数量相比,高素质的员工是系统的决定性的要素。
因此,应把高素质的员工作为现场管理的根本,首先对"5S"的顺序进行调整,把"素养"作为7SEA的第一条,纲举目张,总领其它要素,并且对各要素的内容进行了充实和新的诠释,进一步发展和完善了"5S"管理。
- 1、下载文档前请自行甄别文档内容的完整性,平台不提供额外的编辑、内容补充、找答案等附加服务。
- 2、"仅部分预览"的文档,不可在线预览部分如存在完整性等问题,可反馈申请退款(可完整预览的文档不适用该条件!)。
- 3、如文档侵犯您的权益,请联系客服反馈,我们会尽快为您处理(人工客服工作时间:9:00-18:30)。
Over Processing
Are we applying too much ? Do we do this too often ? Is that fettling / grinding really necessary ? Are those protectors really needed ? Do we need a stud & nut – would a bolt be adequate? Is all that packaging necessary?
7 WASTE MODULE V1.0
ESAB CENTRAL LEAN OFFICE
Waiting
This is usually the easiest waste to see
Don’t have operators waiting for machines
ESAB CENTRAL LEAN OFFICE 7 WASTE MODULE V1.0
2
Process and Method Waste
Long changeover Poor workplace design No maintenance Temporary storage Equipment problems Unsafe methods Operator motion
3
Micro waste within process
ESAB CENTRAL LEAN OFFICE 7 WASTE MODULE V1.0
Transportation
• All material movement or handling is considered non-value added by the customer. Transportation, does not add value and should be minimized or eliminated. • Causes: – Batch processing – Poor layout/distance between operations – Long changeovers – Large lots – Finite storage areas – LIFO vs. FIFO
ESAB CENTRAL LEAN OFFICE
7 WASTE MODULE V1.0
Inventory
Turn product into CASH, reduce inventory, minimize buffers
ESAB CENTRAL LEAN OFFICE
7 WASTE MODULE V1.0
• Why is this??
ESAB CENTRAL LEAN OFFICE
7 WASTE MODULE V1.0
Remember ....
Total Cost Model
Raw Material Material
Housekeeping
The Good Ship?? Finished Product to Customer
7 WASTE MODULE V1.0
The Irony of Inventory
• Organisations that suffer from material & part shortages and have a poor delivery performance can usually be found to have excessive inventory levels.
7 WASTE MODULE V1.0
Waste Defined
• Activities that absorb resources but create no value • Also known as the 3Ms Muda The 7 deadly wastes Mura Unevenness of processes Muri Over burden of people or machines
Bending and reaching Double handling Excess walking Looking for stock Looking for tools Paperwork Speeds and feeds No standardised work
ESAB CENTRAL LEAN OFFICE
Sea of Inventory
Product
Absenteeism
Delivery Transportation
Breakdown
Transportation
INVENTORY HIDES PROBLEMS
ESAB CENTRAL LEAN OFFICE 7 WASTE MODULE V1.0
Time
ESAB CENTRAL LEAN OFFICE 7 WASTE MODULE V1.0
Over processing
• Effort which adds no value to a product or service, enhancements which are ‘invisible’ to the customer. • Work which could be combined with another process. • Causes: – That’s the way we’ve always done it – Improper fixtures, tools, jigs – No standard work – Misuse of materials – Mistakes in process – Excessive checking – Closed-minded thinking – Poor layout
ESAB CENTRAL LEAN OFFICE 7 WASTE MODULE V1.0
Waste – (MUDA)
7 DEADLY WASTES
• Transport • Inventory • Motion • Waiting • Over Production • Over Processing • Defects
Excessive Inventory
• Excessive raw, WIP or finished goods inventory is wasteful • Inventory should exist for two reasons: – Buffer, required to maintain throughput in an environment where variation is present – Satisfy customer demand • Reducing variation enables inventory reduction
Waiting
• Idle time – any idle time such as watching equipment, waiting for inspection, waiting for raw material, waiting for maintenance, waiting for paper work… • Causes: – When two dependent activities are not fully synchronized – Insufficient amount of storage containers – Poor layout – Poor work balance – Unreliable equipment
7 WASTES
ESAB CENTRAL LEAN OFFICE
7 WASTE MODULE V1.0
3 Levels of waste
1
Gross Waste
W.I.P PLANT LAYOUT REJECTS RETURNS REWORKS DAMAGED PRODUCTS CONTAINER SIZE BATCH SIZE POOR LIGHTING DIRTY EQUIPMENT MATERIAL DELIVERED TO POINT OF USE
• Causes: – Inventory is viewed as security (just in case) – Process not capable – No standard practices, lack of adherence – Poorly performing suppliers – Ineffective maintenance – Long setup times – Lack of workplace organization – Poor forecasting and production planning/scheduling – Lack of training – Producing to speculative demand (forecast) – Departmental layouts
CommunicationImຫໍສະໝຸດ alanceProblems
Manpower
Service
Motion
Take the work to the operator not the operator to the work
Eliminate walking Use pouches & dollies Everything within arms reach one at a time Parts orientation
ESAB CENTRAL LEAN OFFICE
7 WASTE MODULE V1.0