第五章间歇式操作反应器
间歇操作釜式反应器的设计—反应器流动模型

1、返混及其对反应过程的影响
(2)返混对反应过程的影响
间歇釜式反应器存在剧烈的搅拌与混合,但不会导 致高浓度的消失。
间歇釜式反应器中彼此混合的物料是在同一时刻进入反 应器的,在反应器中同样条件下经历了相同的反应时间 ,具有相同的性质和浓度,这种浓度相同的物料之间的 混合,不会使原有的高浓度消失。
它造成了反应物高浓度的迅速消失,导致反应器的生产 能力下降。
流型
一、流型
流型与搅拌的关系
流型与搅拌效果、搅拌功率的关 系十分密切。搅拌器的改进和新 型搅拌器的开发往往从流型着手 。
搅拌机顶插式中心安装 立式圆筒的三种基本流型
流型决定因素
取决于搅拌器的形式、搅拌容器和内 构件几何特征,以及流体性质、搅拌 器转速等因素。
图3 搅拌器与流型 (c) 切向流
(c)切向流
无挡板的容器内,流体绕 轴作旋转运动,流速高时 液体表面会形成漩涡,流 体从桨叶周围周向卷吸至 桨叶区的流量很小,混 合效果很差。
上述三种流型通常同时存在
轴向流与径向流对混合起主要作用
切向流应加以抑制
采用挡板可削弱切向流, 增强轴向流和径向流
除中心安装的搅拌机外,还有偏心式、底插式、侧插式、斜插式、卧式 等安装方式。
返混及其对反应过程的影响
1、返混及其对反应过程的影响
(1)返混
返混不是一般意义上的混合,它专指不同时刻进入反应器
的物料之间的混合,是逆向的混合,或者说是不同年龄质 点之间的混合。返混改变了反应器内的浓度分布,使器内 反应物的浓度下降,反应产物的浓度上升。 返混是连续化后才出现的一种混合现象。 间歇反应器中不存在返混,理想置换反应器是没有返混
化学反应工程1_7章部分答案
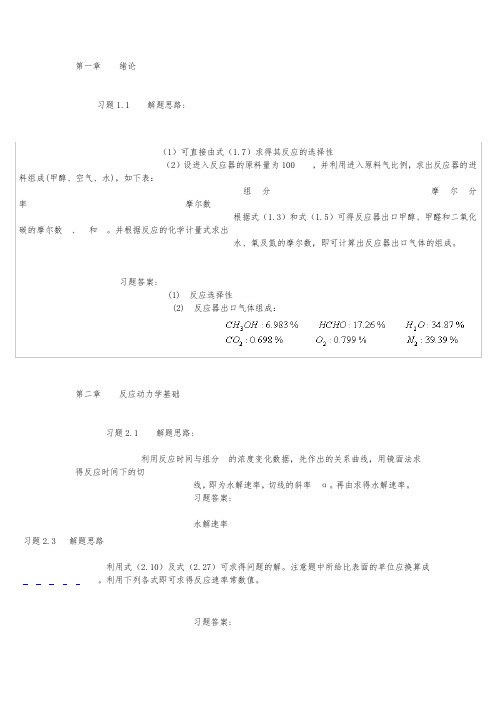
第一章绪论习题1.1 解题思路:(1)可直接由式(1.7)求得其反应的选择性(2)设进入反应器的原料量为100 ,并利用进入原料气比例,求出反应器的进料组成(甲醇、空气、水),如下表:组分摩尔分率摩尔数根据式(1.3)和式(1.5)可得反应器出口甲醇、甲醛和二氧化碳的摩尔数、和。
并根据反应的化学计量式求出水、氧及氮的摩尔数,即可计算出反应器出口气体的组成。
习题答案:(1) 反应选择性(2) 反应器出口气体组成:第二章反应动力学基础习题2.1 解题思路:利用反应时间与组分的浓度变化数据,先作出的关系曲线,用镜面法求得反应时间下的切线,即为水解速率,切线的斜率α。
再由求得水解速率。
习题答案:水解速率习题2.3 解题思路利用式(2.10)及式(2.27)可求得问题的解。
注意题中所给比表面的单位应换算成。
利用下列各式即可求得反应速率常数值。
习题答案:(1)反应体积为基准(2)反应相界面积为基准(3)分压表示物系组成(4)摩尔浓度表示物系组成习题2.9 解题思路:是个平行反应,反应物A的消耗速率为两反应速率之和,即利用式(2.6)积分就可求出反应时间。
习题答案:反应时间习题2.11 解题思路:(1)恒容过程,将反应式简化为:用下式描述其反应速率方程:设为理想气体,首先求出反应物A的初始浓度,然后再计算反应物A的消耗速率亚硝酸乙酯的分解速率即是反应物A的消耗速率,利用化学计量式即可求得乙醇的生成速率。
(2)恒压过程,由于反应前后摩尔数有变化,是个变容过程,由式(2.49)可求得总摩尔数的变化。
这里反应物是纯A,故有:由式(2.52)可求得反应物A的瞬时浓度,进一步可求得反应物的消耗速率由化学计量关系求出乙醇的生成速率。
习题答案:(1)亚硝酸乙酯的分解速率乙醇的生成速率(2)乙醇的生成速率第三章釜式反应器习题3.1 解题思路:(1)首先要确定1级反应的速率方程式,然后利用式(3.8)即可求得反应时间。
(2)理解间歇反应器的反应时间取决于反应状态,即反应物初始浓度、反应温度和转化率,与反应器的体积大小无关习题答案:(1)反应时间t=169.6min.(2)因间歇反应器的反应时间与反应器的体积无关,故反应时间仍为169.6min.习题3.5 解题思路:(1)因为B过量,与速率常数k 合并成,故速率式变为对于恒容过程,反应物A和产物C的速率式可用式(2.6)的形式表示。
第五章5 分程控制控制系统
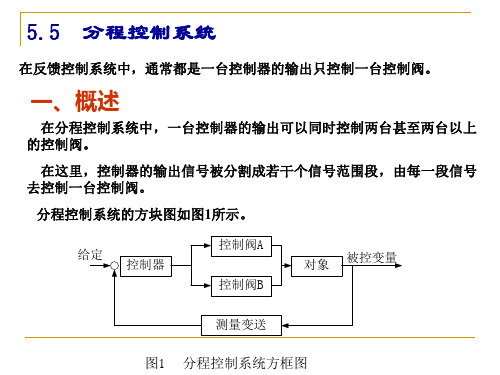
图1
分程控制系统方框图
分程控制系统中控制器输出信号的分段一般是由附设在控制阀上的阀门定
位器来实现的。阀门定位器相当于一台可变放大系数,且零点可以调整的放
大器。 阀门定位器可以将控制器的输出压力分成几段信号区间。不同段内的压力
有相应的阀门定位器转化为0.02~0.1MPa信号压力,使控制阀全程动作。
例如:A和B两个控制阀 要求:A阀在控制器输出信号压力为0.02~0.06MPa信号压力,使控制 阀全程动作。 A阀上的阀门定位器对应的输出压力为0.02MPa~0.1MPa,B阀上则在控制 器输出压力为0.06MPa~0.1MPa时通过附设在上面的阀门定位器使之也刚好走 完全程。 即,当控制其输出信号小于0.06MPa时,A阀动作,B阀不动作; 当信号大于0.06MPa时,A阀已动至极限,B阀开始动作。
一类是两个控制阀异向动作: 即随着控制器输出信号的增大成减小,一个控制阀开大,另 一个控制阀则关小,如图8—37所示,其中图(a)是A为气关阀、B 为气开阀的情况。图(b)是A为气开阀、B为气关阀的情况。
分程阀同向或异向动作的选择问题,要根据生产工艺的实际需要 来确定。
二、分程控制的应用场合
1.用于扩大控制阀的可调范围,改善控制品质
TCபைடு நூலகம்冷水
A B 蒸汽
FVA:气闭
FVB:气开
TC:反作用
1.反应开始前升温阶段→T测<给定值→TC↑→A阀↓ →( A阀 全关时)B阀↑ →蒸汽加热, T↑→ 达到反应温度时,反应开 始; 2.反应开始后T↑ → T测.>给定值→TC↓ →B阀↓(B阀全关时) A阀↑→ T↓,冷却水把反应热带走,使反应釜温度恒定,反 应继续进行。
5.5
分程控制系统
间歇釜式反应器

计算方法
1、已知V0与 ,根据已有的设备容积V,求算需用设备个数n 按设计任务每天需要操作的总次数为: α =
24V0 24V0 = VR V
β= 每个设备每天能操作的批数为:
n' =
24 24 = t τ +τ '
则需用设备个数为:
α V0 (τ + τ ') = β V
VR = V = V0 (τ + τ ' ) / n '
物料衡算式 依 据:质量守衡定律。 基 准: 取温度、浓度等参数保持不变的单元体积和 单元时间作为空间基准和时间基准。 衡算式:对任一组分A在单元时间Δτ、单元体积ΔV内: [A的积累量]=[A的进入量] [A的离开量] [A的反应量] [A的积累量]=[A的进入量]-[A的离开量]-[A的反应量] 的积累量]=[A的进入量 的离开量 的反应量 目的:给出反应物浓度或转化率随反应器内位置或时 间变化的函数关系。
热量衡算式 (1)依 据: 能量守衡定律。 (2)基 准: 取温度、浓度等参数保持不变的单元体积和单元时间作为 空间基准和时间基准。 (3)衡算式 在单元时间Δτ、单元体积ΔV内(以放热反应为例): [积累的热量]=[原料带入的热量]+[反应产生的热量]-[出料带走的热量]积累的热量]=[原料带入的热量]+[反应产生的热量] 出料带走的热量] ]=[原料带入的热量]+[反应产生的热量 [传给环境或热载体的热量] 传给环境或热载体的热量] (4)目的:给出温度随反应器内位置或时间变化的函数关系。
BR体积和数量求算 体积和数量求算
已知条件 每天处理物料总体积VD(或反应物料每小时体积流量V0)
Vρ
操作周期——指生产第一线一批料的全部操作时间,由反应时 间(生产时间)τ和非生产时间τ‘ 组成。 反应时间理论上可以用动力学方程式计算,也可根据实际情 况定。 设备装料系数——设备中物料所占体积与设备实际容积之比, 其具体数值根据实际情况而变化,参见表3-1。
第五章 间歇式操作反应器

回顾一下:生化反应器中可进行的反应类型? 再想想:反应器可采取的操作方式?
2、研究反应器的目的?
◆研究生化反应器的基本反应规律
◆研究生化反应器的基本传递规律 ◆研究生化反应器的设计内容及方法
上一内容
下一内容
回主目录
返回
2013-7-25
第5章 间歇式操作反应器>>5.1生化反应器设计概论
上一内容 下一内容 回主目录
返回
2013-7-25
第5章 间歇式操作反应器>>5.1生化反应器设计概论
5.1.1 生化反应器的分类
( 生化反应器可从不同角度分类)
2、按操作方式分类 ■间歇反应器(分批操作反应器):底物一次加入反应器,在反应过
程中无底物和产物的输入和输出,底物和产物的浓度随反应时间变化。
上一内容
下一内容
回主目录
返回
2013-7-25
第5章 间歇式操作反应器>>5.1生化反应器设计概论
5.1.2 生化反应器的基本设计方程
反应器计算的基本内容 确定最佳操作条件与控制方式 操作条件,如反应器的进口物料配比、流量、温度、压 力和最终转化率等工艺条件,直接影响反应器的反应结果,
也影响反应器的生产能力。对正在运行的装置,因原料组
对细胞,有
体系内累 进入体系 离开体系 体系内生 积细胞质量 细胞质量 细胞质量 长细胞质量
上一内容
下一内容
回主目录
返回
2013-7-25
第5章 生化反应器设计与分析>>5.1生化反应器设计概论
间歇釜式反应器BR
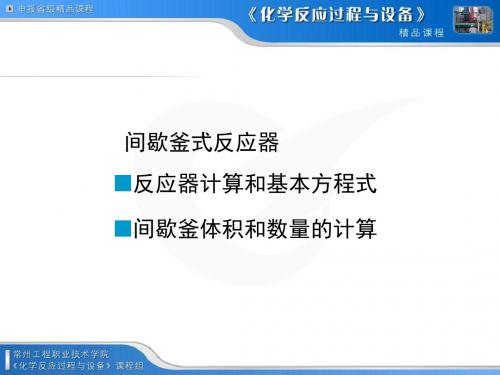
反应器计算的基本方程
反应器计算可以采用经验法和数学模型法。经验计算法是根据已有的 装置生产定额,进行相同生产条件、相同结构生产装置的工艺计算。经 验计算法的局限性很大,只能在相近条件下进行反应器体积的估算。 如果改变反应过程的条件或改变反应器结构,以改进反应器的设计, 或者进一步确定反应器的最优结构、操作条件,经验计算法是不适用的, 这时应该用数学模型法计算。根据小型实验建立的数学模型(一般需经 中试验证),结合一定的求解条件——边界条件和初始条件,预计大型
釜内各点物料的浓度、温度、反应速度相同,随时间而
变,生产周期存在反应时间(生产时间)τ和非生产时间 τ‘。 其结构简单、操作方便、灵活性大、应用广泛。但是
设备生产效率低、不易保持每批质量稳定、高转化率下体
积较大。一般用于液—液相、气—液相等系统,如染料、
医药、农药等小批量多品种的行业。
热量衡算式
(1)依 据: 能量守衡定律。 (2)基 准: 取温度、浓度等参数保持不变的单元体积和单元时间作为 空间基准和时间基准。 (3)衡算式 在单元时间Δτ、单元体积ΔV内(以放热反应为例): [积累的热量]=[原料带入的热量]+[反应产生的热量]-[出料带走的热量][传给环境或热载体的热量] (4)目的:给出温度随反应器内位置或时间变化的函数关系。
设备的行为,实现工程计算。
数学模型法计算的基础是描述化学过程本质的动力学模型以及反映 传递过程特性的传递模型。基本方法是以实验事实为基础,建立上 述模型,并建立相应的求解边界条件,然后求解。
反应器计算的基本方程包括
描述浓度变化的物料衡算式;
描述温度变化的能量衡算式; 描述压力变化的动量衡算式; 描述反应速率变化的动力学方程式。
间歇釜式反应器的特点及其应用
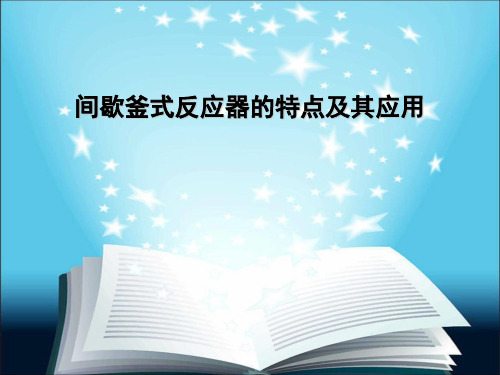
• 例题:萘磺化反应器体积的计算。萘磺化生产2萘磺酸,然后通过碱熔得2-萘酚。已知2-萘酚的 收率按萘计为75%,2-萘酚的纯度为99%,工业 萘纯度为98.4%,密度为963kg/m3.磺化剂为98% 硫酸,密度为1.84.萘与磺酸的摩尔比为1:1.07. 每批磺化操作周期为3.67h。萘磺化釜的装料系数 为0.7.年产2-萘酚4000t,年工作日330天。
4390
The end,thank you!
• 应用: • 适用于多品种、小批量生产 • 适应于各种不同相态组合的反应物料 • 几乎所有有机合成的单元操作
反应体积VR
• 反应体积是指设备中物料所占体积,又称有效体 积。
• 确定反应器体积的容积V的前提是确定反应器的 有效容积
• 如果由生产任务确定的VR F单Vt, 位时间的物料处理量为 FV,操作时间为t‘(包括反应时间t和辅助操作时 间t0),则反应器的有效容积V:R FV t,
间歇釜式反应器的特点及其应用
目录
特点
例题分析
• 特点: • 反应物料一次加入,产物一次取出 • 结构简单、加工方便,传质、传热效率高 • 同一瞬间反应器内各点温度、浓度分布均匀 • 非稳态操作,反应过程中,温度、浓度、反应速
度随着反应时间而变
• 操作灵活性大,便于控制和改变反应条件 • 辅助时间占的比例大,劳动强度高,生H2SO4
→
→
根据生产任务,每小时需处理工业萘的体积为:
4000 103 0.99 128 1 1000 626 L 330 24 144 0.75 0.984 963
每小时需要处理的硫酸体积为: 4000 10 3 0.99 98 1.07 1 1000 270 L
反应器操作与控制基础知识—反应器的操作方式
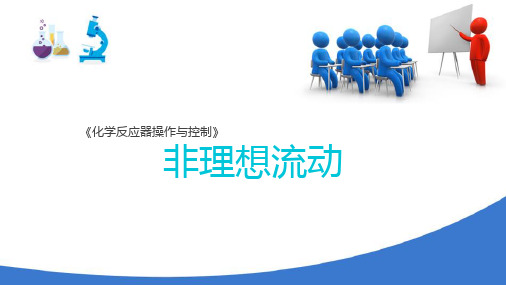
①是一非定态过程,反应器内物系组 成随时间而改变
②适合于小批量、多品种的产品生产
③不易实现自动化控制,劳动力多
④设备简单
⑤设备利用率低
二、操作方式的特点—— 2.连续操作的特点
二、操作方式的特点——2.连续操作的特点
连续操作的一般流程
01
连续进料
02
03
连续反应
连续出料
温度等的控制
二、操作方式的特点——2.连续操作的特点
连连续式式 操操作作方方 式式
的的特特 点点
①多属于定态操作,反应器内各种物系参数 不随时间而变,但随位置而变
②适合于大规模生产
③便于实现自动化控制,品质量均一
④设备结构复杂
⑤设备利用率高
二、操作方式的特点——3.半连续(半间歇)操作的特点
原料与产物只要其中的一种为连续输入或输出而其余则为分 批加入或卸出的操作均属半连续操作,相应的反应器称为半连续反 应器或半间歇反应器。
《化学反应器操作与控制》
非理想流动
非理想流动模型
理想流动模型
理想置换模型
(a) 间接换热式
二、操作方式的特点——1.间歇操作的特点
二、操作方式的特点——1.间歇操作的特点
间歇操作的一般流程
01
02
03
04
05
06
准备
投料
升温
反应
出料
清洗
关键步骤
二、操作方式的特点——1.间歇操作的特点
间歇式 操作方式
半连续操作具有连续操作和间歇操作的某些特征: 有连续流动的物料,也有分批加入或卸出的物料,因此半连
续反应器的反应物系组成必然既随时间而改变,也随反应器内的位 置而改变。
- 1、下载文档前请自行甄别文档内容的完整性,平台不提供额外的编辑、内容补充、找答案等附加服务。
- 2、"仅部分预览"的文档,不可在线预览部分如存在完整性等问题,可反馈申请退款(可完整预览的文档不适用该条件!)。
- 3、如文档侵犯您的权益,请联系客服反馈,我们会尽快为您处理(人工客服工作时间:9:00-18:30)。
N
推动力 阻力
ci
c 1
c * ci 1
c *c 1 H
KL (c * c)
kL
kG
kL kG
对于易溶气体,如氨气溶于水中时,液膜的传质阻力相对于气膜可忽略 对于难溶气体,如氧气溶于水中时,气膜的传质阻力相对于液膜可忽略
当1 kL
1 HkG
N
kL (c * c)
1 cX
dcX
maxt r
A ln
cX cX0
Bln
YX/ScS0 (cX cX0 ) YX /ScS0
A YX/SKS YX/ScS0 cX0 YX / cS S0 cX0
B
YX /SKS
YX / cS S0 cX0
4 最优反应时间的确定
FP
VR c P tr tb
dFP dtr
(1 L )VRrS
LVR
dcS dt
t r
L 1 L
cS dcS cS0 rS
cS0 L XS dXS
1 L 0 rS
cS0
VL VP
XS dXS 0 rS
如反应速本以单位催化剂的质量来定义,并表示为rSW,则有
t r
cS0
VL W
XS dXS 0 rSW
通常当酶反应为一级反应,即cS<<K m时.内扩散有效因子η 与转化率Xs的大小无关,等于常数。此时有:
rmax t r
(1
L
L
)
K
M
ln
cS0 cS
1 KM ln 1 XS
当固定化酶的颗粒很小,内扩散的影响可以忽略时, 有效因子η =1,则反应时间可由下式计算,即
rmax
tr
(1 L ) L
cS0 XS
KM
ln
1 1 XS
3 细胞反应过程
rX
dcX dt
cX
1
cS
cS0
YX / S
(cX
cX0 )
max
cS0
1 YX /S
(cX
cX0 )
KS
cS0
1 YX /S
(cX
cX0
)
max
YX
YX /SKS
/ ScS0 YX
(cX cX0 ) /ScS0 (cX
cX0
)
maxtr
cX cX0
YX/SKS YX/ScS0 (cX cX0 ) YX/ cS S0 (cX cX0 )
②较适合反应速率较慢的生物反应。由于多数生 物反应的速率较化学反应慢,故工业过程使用 具有间歇操作特征的大容量生物反应器。
③分批进行的过程染菌率较低。
缺点
① 间歇操作反应器的缺点是.这种操作需要一 定的辅助操作时间,生产效率较低;
② 细胞或酶的反应环境随时间改变,产物生成 速率与反应时间有关;
③ 下游产物分离必须分批进行等。
式中:K-稠度系数;n-流动特性指数
特点:K越大,流体越粘稠;n值越小,流体的非牛顿
特性越明显。
a
K n1
2 涨塑性流体(膨胀型) 流动特性表达式:=K n (n>1); n值越大,流体的非牛顿特性越明显。
a
K n1
3 宾汉(Bingham)塑型流体
流动特性表达式: = 0+ 式中: 0-屈服应力; -刚度系数 特点:当< 0 时,流体不发生流动。
生物反应速度
反
反 反反 应
应 应应 器
2 基本设计方程
器 器器 操 型 结体 作 式 构积 方
式
生物反应器设计的主要目标是寻求反应目的产物的高
生成速率和高浓度,从而达到优质高产低成本的目的。
生物反应器设计的基本内容包括:
①选择合适的反应器型式与操作方式。即根据生物催化剂和生 物反应动力学特征,以及物料的特性和生产工艺特点,选择 合理的结构类型、流动方式和相关的传递过程条件;
营养物质的种类和浓度、培养温度、pH、有害代谢物的 积累、挥发性中间代谢物的损失等等。
三.氧的传递过程
(1)气相扩散到气-液界面阻力R1; (2)通过气液界面的阻力R2; (3)通过滞流区的阻力R3; (4)液相传递阻力R4;
(5)细胞团外液膜阻力R5; (6)液体与细胞团界面阻力R6; (7)细胞之间的扩散阻力R7; (8)进入细胞的阻力R8
tr
cS0
X S dX S 0 rS
表示反应组分转化至一定程度所需的反应时间,它取
决于反应速率的大小,反应速率越大,反应时间越小
1 均相酶反应过程
如酶反应为单底物无抑制反应,且动力学关系符合M-M方
程
rp
k2cE0
cS
cS KM
rP ,m a x
cS
cS KM
(5)
tr
cS0
XS 0
几种酶反应器
几种细胞反应器
生物反应器分析(优化和放大)与设计
生物反应器的选型与几何尺寸确定及运行模式
生物反应器设计、
优化与放大
反 应
反 应
反 应
反 应 器
器 器器操
型 式Βιβλιοθήκη 结 构体 积作 方 式
传递特性、流动与混合特性
生物反应动力学
( 微本 观征 动动 力力 学学 )
( 总宏 包观 动动 力力 学学 )
当颗粒所占的体积分率较大时,可按下式计算。
s=L(1+2.5+7.352)
4.3.3 流体的剪切作用 4.3.3.1 机械搅拌的剪切力
ISF uL 2nd
x D d
对于处于较高雷诺数(ReM>>625)的反应器系统.这时可得df/d=0.625
(3)最小湍流漩涡长度
4.3.3.2 气流搅拌的剪切力
(即全混流和平推流)。 ➢实际的连续流动反应器的流动和混合状态处于它
们之间,为非理想流动,对生物反应器进行这种 分类有利于对反应器进行模拟与放大。
➢根据反应器的结构:包括罐式、管式、塔式、 膜式等。 ➢若根据反应器所需能量的输入方式不同来分, 则有通过机械搅拌输入能量的机械搅拌反应器、 利用气体喷射动能的气流搅拌反应器和利用泵对 液体的喷射作用而使液体强制循环的反应器。
Da
rO 2 ,max KO2 kLa
氧的传递速率与氧的消耗速率的关系
六.最低溶氧浓度
(OUR )* (qO2cX )* (OTR )max
(OTR)max kLa(cO* L cOL,min)
cOL,min
cO* L(1
(qO2cX )* kLacO* L
)
4.4.3影响氧传递的因素
两别同时乘以a(单位体积反应液中气液比表面积)
Na kLa(c*c)
kLa------体积传质系数
五.氧传递对细胞生长的影响
dcOL dt
OTR
RO2
kLa(cO* L
cOL ) qO2 cX
RO2
qO2 cX
qO2,m ax
cOL KO2 cOL
cX
kLa(cO* L cOL )
tr
1 kd
ln 1
kd K2cE0
cS0 XS
cEKM
ln
1 1 XS
举例5-1
2 固定化酶反应过程
假定反应过程发生在固定化酶颗粒内,反应速率不受外扩 散限制,但受内扩散限制。 设反应器中的空隙串(液相体积/反应器有效体积)为L,则 固定化酶颗粒所占的体积分数为(1- L)。 在单位时间内、反应器中底物的消耗量为(1- L)VRrS,累 积项则为反应器内液相中底物随时间的变化率为 LVRdcS/dt
第四章 生物反应器的操作模型
4.1 操作模型概论
分类与特征
➢ 按照生物反应过程所使用的生物催化剂不同:酶 反应器;细胞生物反应器
➢ 根据反应器物料的加入和排出方式的不同:间歇 反应器;连续反应器;半间歇半连续反应器
➢ 根据生物催化剂在反应器的分布力式:生物团块 反应器;生物膜反应器
➢根据相态来分:有均相反应器;非均相反应器。 ➢理想的机械搅拌反应器和理想管式反应器的流型
4.3.2 影响流变性质的因素
下图是金色链霉菌发酵液的稠度系数K和流动特性指数n 随发酵时间的变化情况。
当发酵液中的颗粒呈球形或接近球形,且其浓度较低时,悬 浮液一般为牛顿流体,其粘度可根据Einstein公式计算:
s=L(1+2.5)
式中:s-悬浮液粘度;
L-悬浮液中纯液相粘度;
-颗粒的体积分率。
V间歇反应釜 V0CA0
dx x Af
A
0 rA
VCSTR
V0CA0 (XAf CA0 ) rAf
4.2 间歇式操作反应器的设计
4.2.1 间歇式操作的特点
✓ 非稳态过程 ✓ 所有物料具有相同的停留时间和反应时间 ✓ 随着反应的进行,反应器的效率将降低
优点
①较适合多品种、小批量的生产过程。有不少生 物制品是小批量生产的,因此使用同一台反应 装置,可进行多品种的生产。
当cS0>>Km时,即反应呈零级反应特征时:
rmax t r cS0 XS cS0 cS
KM (k2 k1) / k1 KS (k1) / k1 KM KS k2 / k1
对于存在酶失活的反应,如果符合一级失活模 型.则有:
rmax K2cE K2cE0 exp( kd t r )
4 凯松(Casson)流体
流动特性表达式:0.5= 00.5+Kc 0.5
Kc-凯松粘度
总之,流体特性因素都会对生化反应器内的质量与 热量传递、混合特性及菌体生长等产生影响,这给 工艺过程控制与设备放大带来困难。