麦肯锡-供应链物流供应链管理-流程与绩效
合集下载
麦肯锡供应链管理-流程与绩效
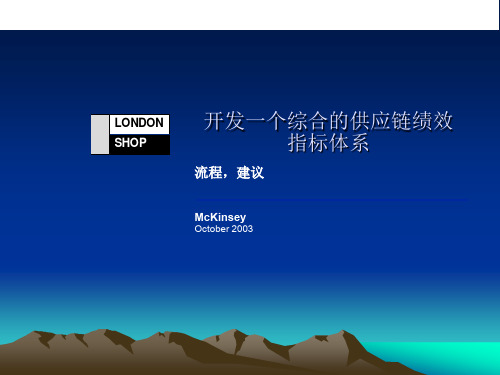
关注
沟通
通过交互式 沟通和教育, 发展面向目 标测的评估
没有一个“正确”的答案Biblioteka 这份资料只是正确导向的第一步
我们采用通用的供应链架构作为
我们分析问题的基础. . .
供应链架构
预测与采购计划
采购
供应商
集成的供应链管理
采购物流
信息流
生产 维护 库存管理
客户服务
市场销售
销售物流
客户
这种框架与CoE POV一致,并且与供应链库存数据库的诊断框架类似。
LONDON SHOP
开发一个综合的供应链绩效 指标体系
流程,建议
THE
McKinsey
October 2003
这份资料概述了一些能用来评估 供应链绩效的指标
• 供应链CoE的目标就是确定一个测试供应 链框架能力的基准:
– 在项目中,与常用的衡量指标作对比 – 用一致的形式获取更多的基准数据
• 伦敦商店的任务
质量
• 从订单下达到货物接收的时间 • 供应商准时送货的%
到期日之前处理应付款的%
• 1–30 天内处理应付款的% • 31–60 天内处理应付款的% • 61–90 天内处理应付款的% • 90 天之后处理应付款的% • 通过 EDI与供应商联系的% • 开发/商谈一个协议的时间平均时
总采购价值 供应商根据订单 生产过程
90%的活跃供(数量和质量) 中的产品 应商的比例 供货的比例 缺陷率
客户满意的 比率
维护
库存管理 市场销售 客户服务 销售物流
订单商品 入库比例
需要核 实的市 场销售
KPIs
客户对服 按客户订单(数
务满意的 量和质量)交货
Mckinsey方法论-供应链管理-流程与绩效
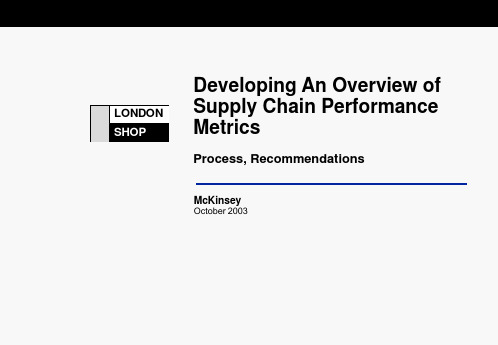
McKinsey • Proprietary and Confidential
LShop/Ldn/22Oct97Rp-fc/kf
-6-
. . . and concluded there are three strategic objectives we should focus on when analysing the supply chain
Strategic objectives:
Supply Chain Framework Quality
Information Flow Forecasting & Production Planning Customer Service Products/services according to customer expectations
Manufacturing
Purchasing Inbound Logistics Maintenance Marketing & Sales Outbound Logistics
Time
On agreed time
Integrated Supply Chain Management NB: Boundaries
LONDON SHOP
Developing An Overview of Supply Chain Performance Metrics
Process, Recommendations
McKinsey
October 2003
THE
This document gives an overview of the different metrics that can be used to measure supply chain performance
LShop/Ldn/22Oct97Rp-fc/kf
-6-
. . . and concluded there are three strategic objectives we should focus on when analysing the supply chain
Strategic objectives:
Supply Chain Framework Quality
Information Flow Forecasting & Production Planning Customer Service Products/services according to customer expectations
Manufacturing
Purchasing Inbound Logistics Maintenance Marketing & Sales Outbound Logistics
Time
On agreed time
Integrated Supply Chain Management NB: Boundaries
LONDON SHOP
Developing An Overview of Supply Chain Performance Metrics
Process, Recommendations
McKinsey
October 2003
THE
This document gives an overview of the different metrics that can be used to measure supply chain performance
流程管理-麦肯锡供应链管理流程与绩效 精品001
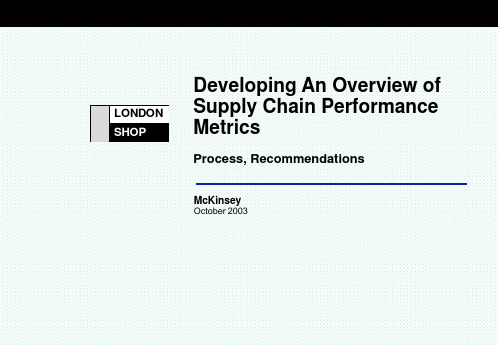
Performance measurement is an important but complex subject
Companies see the need for metrics. . .
• “If you can’t measure, you can’t manage, you can’t motivate”
Focus
. . . but developing the “right” set of metrics is a challenge
• No commonly used “model”.
• Business issues that warrant performance measurement:
– Differ between industries. – Differ within industry. – Change overtime.
chain. – Suggest how the supply chain CoE should continue concerning this topic.
We used information from several sources during our project
• Internal and external documents:
• The London Shop’s task:
– Develop an overview of the different metrics to measure supply chain performance. – Select the most important metrics that can be used across industries. – Discuss how the most important metrics link other operational metrics within each stage of the supply
流程管理-麦肯锡供应链管理流程与绩效 精品002
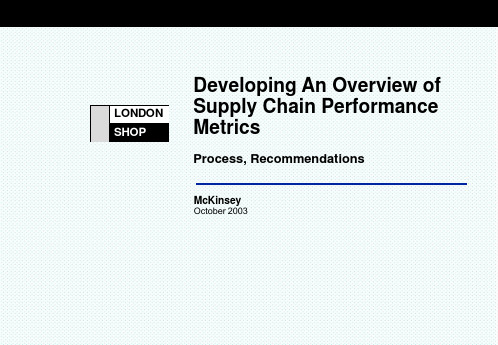
– Supply chain benchmarks and best practice (Dow rethane & Epoxy April 1995). – Supply Chain Benchmark Assessment (March 1997). – Supply chain appraisal and benchmarks: (client X September 1997).
LONDON SHOP
Developing An Overview of Supply Chain Performance Metrics
Process, Recommendations
THE
McKinsey
October 2003
This document gives an overview of the different metrics that can be used to measure supply chain performance
• Establishing the proper measures within an organisation enhances continuous
Linking strategy to action
Accountability
Assigning accountability to take action when needed
• The Supply Chain CoE’s objective is to define a benchmarking framework capable of:
– Comparing generic metric performances for use on projects. – Capturing further benchmarking data in a consistent format.
LONDON SHOP
Developing An Overview of Supply Chain Performance Metrics
Process, Recommendations
THE
McKinsey
October 2003
This document gives an overview of the different metrics that can be used to measure supply chain performance
• Establishing the proper measures within an organisation enhances continuous
Linking strategy to action
Accountability
Assigning accountability to take action when needed
• The Supply Chain CoE’s objective is to define a benchmarking framework capable of:
– Comparing generic metric performances for use on projects. – Capturing further benchmarking data in a consistent format.
麦肯锡供应链管理-流程与绩效(英文原版)
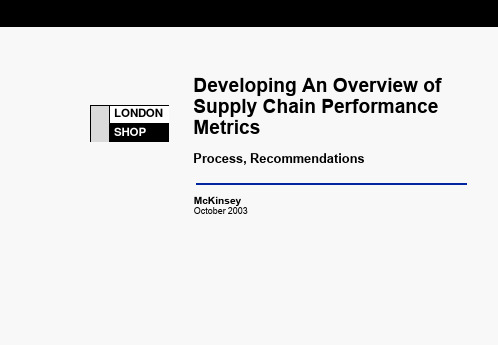
LShop/Ldn/22Oct97Rp-fc/kf
-6-
. . . and concluded there are three strategic objectives we should focus on when analysing the supply chain
Supply Chain Framework
LShop/Ldn/22Oct97Rp-fc/kf
-3-
Possible data sources
• CIPS (UK):
Purchasing (& Supply Chain).
• APICS (US):
Supply Chain.
• CAPS (US):
Purchasing & Supply Chain (US & Legal):
• Respect all sources of data:
Blind-sided
Intuition Qualitative
Opinion
Discussion Survey
Functional Measures
• Understand their relationships—the “causal tree”:
interactive communication and
education
There is no one “right” answer
This document’s an initial step in the right direction.
McKinsey • Proprietary and Confidential
• Internal and external documents:
-6-
. . . and concluded there are three strategic objectives we should focus on when analysing the supply chain
Supply Chain Framework
LShop/Ldn/22Oct97Rp-fc/kf
-3-
Possible data sources
• CIPS (UK):
Purchasing (& Supply Chain).
• APICS (US):
Supply Chain.
• CAPS (US):
Purchasing & Supply Chain (US & Legal):
• Respect all sources of data:
Blind-sided
Intuition Qualitative
Opinion
Discussion Survey
Functional Measures
• Understand their relationships—the “causal tree”:
interactive communication and
education
There is no one “right” answer
This document’s an initial step in the right direction.
McKinsey • Proprietary and Confidential
• Internal and external documents:
麦肯锡供应链管理-流程与绩效英文原版

• The Supply Chain CoE’s objective is to define a benchmarking framework capable of:
– Comparing generic metric performances for use on projects. – Capturing further benchmarking data in a consistent format.
chain. – Suggest how the supply chain CoE should continue concerning this topic.
McKinsey • Proprietary and Confidential
LShop/Ldn/22Oct97Rp-fc/kf
-2-
We used information from several sources during our project
Customer service cost
The complete picture can be found in the appendix.
McKinsey • Proprietary and Confidential
LShop/Ldn/22Oct97Rp-fc/kf
-8-
Making their client specific warrants attention
interactive communication and
education
There is no one “right” answer
This document’s an initial step in the right direction.
– Comparing generic metric performances for use on projects. – Capturing further benchmarking data in a consistent format.
chain. – Suggest how the supply chain CoE should continue concerning this topic.
McKinsey • Proprietary and Confidential
LShop/Ldn/22Oct97Rp-fc/kf
-2-
We used information from several sources during our project
Customer service cost
The complete picture can be found in the appendix.
McKinsey • Proprietary and Confidential
LShop/Ldn/22Oct97Rp-fc/kf
-8-
Making their client specific warrants attention
interactive communication and
education
There is no one “right” answer
This document’s an initial step in the right direction.
麦肯锡供应链管理-流程与绩效(英文原版)

chain. – Suggest how the supply chain CoE should continue concerning this topic.
McKinsey • Proprietary and Confidential
LShop/Ldn/22Oct97Rp-fc/kf
-2-
We used information from several sources during our project
– Supply chain benchmarks and best practice (Dow Polyurethane & Epoxy April 1995). – Supply Chain Benchmark Assessment (March 1997). – Supply chain appraisal and benchmarks: (client X September 1997).
• Internal and external documents:
– High level benchmarking framework for supply chain performance (H .Cook): • Shop Study (March 1997) accessing information from available experts and past projects.
LShop/Ldn/22Oct97Rp-fc/kf
-6-
. . . and concluded there are three strategic objectives we should focus on when analysing the supply chain
McKinsey • Proprietary and Confidential
LShop/Ldn/22Oct97Rp-fc/kf
-2-
We used information from several sources during our project
– Supply chain benchmarks and best practice (Dow Polyurethane & Epoxy April 1995). – Supply Chain Benchmark Assessment (March 1997). – Supply chain appraisal and benchmarks: (client X September 1997).
• Internal and external documents:
– High level benchmarking framework for supply chain performance (H .Cook): • Shop Study (March 1997) accessing information from available experts and past projects.
LShop/Ldn/22Oct97Rp-fc/kf
-6-
. . . and concluded there are three strategic objectives we should focus on when analysing the supply chain
麦肯锡供应链管理-流程与绩效英文原版

• Internal and external documents:
– High level benchmarking framework for supply chain performance (H .Cook): • Shop Study (March 1997) accessing information from available experts and past projects.
• The London Shop’s task:
– Develop an overview of the different metrics to measure supply chain performance. – Select the most important metrics that can be used across industries. – Discuss how the most important metrics link other operational metrics within each stage of the supply
Accountability
Assigning accountability to take action when needed
Focus
. . . but developing the “right” set of metrics is a challenge
• No commonly used “model”.
• Discussions with supply chain CoE:
– Graham Colclough. – Andrew Morgan. – Lee Sherman. – Deborah Huff (Cap McKinsey).
– High level benchmarking framework for supply chain performance (H .Cook): • Shop Study (March 1997) accessing information from available experts and past projects.
• The London Shop’s task:
– Develop an overview of the different metrics to measure supply chain performance. – Select the most important metrics that can be used across industries. – Discuss how the most important metrics link other operational metrics within each stage of the supply
Accountability
Assigning accountability to take action when needed
Focus
. . . but developing the “right” set of metrics is a challenge
• No commonly used “model”.
• Discussions with supply chain CoE:
– Graham Colclough. – Andrew Morgan. – Lee Sherman. – Deborah Huff (Cap McKinsey).