【机械类文献翻译】冲压成形特点与板材冲压成形性能
中英文翻译---冲压成形的特点与板材冲压成形性能
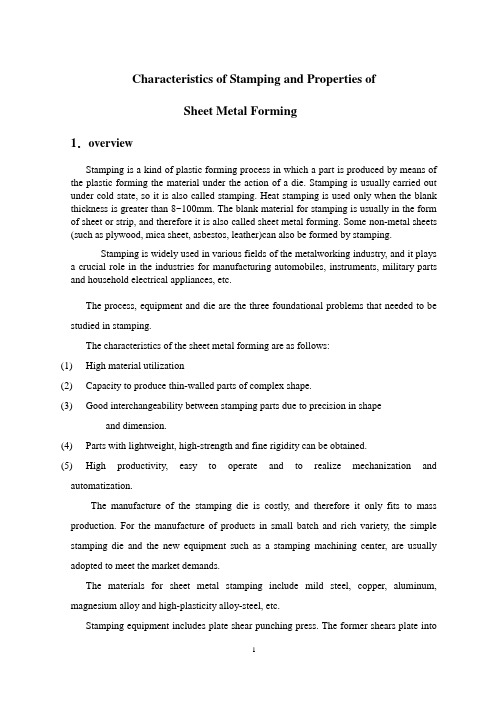
Characteristics of Stamping and Properties ofSheet Metal Forming1.overviewStamping is a kind of plastic forming process in which a part is produced by means of the plastic forming the material under the action of a die. Stamping is usually carried out under cold state, so it is also called stamping. Heat stamping is used only when the blank thickness is greater than 8~100mm. The blank material for stamping is usually in the form of sheet or strip, and therefore it is also called sheet metal forming. Some non-metal sheets (such as plywood, mica sheet, asbestos, leather)can also be formed by stamping.Stamping is widely used in various fields of the metalworking industry, and it plays a crucial role in the industries for manufacturing automobiles, instruments, military parts and household electrical appliances, etc.The process, equipment and die are the three foundational problems that needed to be studied in stamping.The characteristics of the sheet metal forming are as follows:(1)High material utilization(2)Capacity to produce thin-walled parts of complex shape.(3)Good interchangeability between stamping parts due to precision in shapeand dimension.(4)Parts with lightweight, high-strength and fine rigidity can be obtained.(5)High productivity, easy to operate and to realize mechanization and automatization.The manufacture of the stamping die is costly, and therefore it only fits to mass production. For the manufacture of products in small batch and rich variety, the simple stamping die and the new equipment such as a stamping machining center, are usually adopted to meet the market demands.The materials for sheet metal stamping include mild steel, copper, aluminum, magnesium alloy and high-plasticity alloy-steel, etc.Stamping equipment includes plate shear punching press. The former shears plate intostrips with a definite width, which would be pressed later. The later can be used both in shearing and forming.2.Characteristics of stamping formingThere are various processes of stamping forming with different working patterns and names. But these processes are similar to each other in plastic deformation. There are following conspicuous characteristics in stamping:(1).The force per unit area perpendicular to the blank surface is not large but is enough to cause the material plastic deformation. It is much less than the inner stresses on the plate plane directions. In most cases stamping forming can be treated approximately as that of the plane stress state to simplify vastly the theoretical analysis and the calculation of the process parameters.(2).Due to the small relative thickness, the anti-instability capability of the blank is weak under compressive stress. As a result, the stamping process is difficult to proceed successfully without using the anti-instability device (such as blank holder). Therefore the varieties of the stamping processes dominated by tensile stress are more than dominated by compressive stress.(3).During stamping forming, the inner stress of the blank is equal to or sometimes less than the yield stress of the material. In this point, the stamping is different from the bulk forming. During stamping forming, the influence of the hydrostatic pressure of the stress state in the deformation zone to the forming limit and the deformation resistance is not so important as to the bulk forming. In some circumstances, such influence may be neglected. Even in the case when this influence should be considered, the treating method is also different from that of bulk forming.(4).In stamping forming, the restrain action of the die to the blank is not severs as in the case of the bulk forming (such as die forging). In bulk forming, the constraint forming is proceeded by the die with exactly the same shape of the part. Whereas in stamping, in most cases, the blank has a certain degree of freedom, only one surface of the blank contacts with the die. In some extra cases, such as the forming of the blank on thedeforming zone contact with the die. The deformation in these regions are caused and controlled by the die applying an external force to its adjacent area.Due to the characteristics of stamping deformation and mechanics mentioned above, the stamping technique is different form the bulk metal forming:(1).The importance or the strength and rigidity of the die in stamping forming is less than that in bulk forming because the blank can be formed without applying large pressure per unit area on its surface. Instead, the techniques of the simple die and the pneumatic and hydraulic forming are developed.(2).Due to the plane stress or simple strain state in comparison with bulk forming, more research on deformation or force and power parameters has been done. Stamping forming can be performed by more reasonable scientific methods. Based on the real time measurement and analysis on the sheet metal properties and stamping parameters, by means of computer and some modern testing apparatus, research on the intellectualized control of stamping process is also in proceeding.(3).It is shown that there is a close relationship between stamping forming and raw material. The research on the properties of the stamping forming, that is, forming ability and shape stability, has become a key point in stamping technology development, but also enhances the manufacturing technique of iron and steel industry, and provides a reliable foundation for increasing sheet metal quality.3.Categories of stamping formingMany deformation processes can be done by stamping, the basic processes of the stamping can be divided into two kinds: cutting and forming.Cutting is a shearing process that one part of the blank is cut from the other. It mainly includes blanking, punching, trimming, parting and shaving, where punching and blanking are the most widely used. Forming is a process that one part of the blank has some displacement from the other. It mainly includes deep drawing, bending, local forming, bulging, flanging, necking, sizing and spinning.In substance, stamping forming is such that the plastic deformation occurs in thedeformation zone of the stamping blank caused by the external force. The stress state and deformation characteristic of the deformation zone are the basic factors to decide the properties of the stamping forming. Based on the stress state and deformation characteristics of the deformation zone, the forming methods can be divided into several categories with the same forming properties and be studied systematically.The deformation zone in almost all types of stamping forming is in the plane stress state. Usually there is no force or only small force applied on the blank surface. When is assumed that the stress perpendicular to the blank surface equals to zero, two principal stresses perpendicular to each other and act on the blank surface produce the plastic deformation of the material. Due to the small thickness of the blank, it is assumed approximately the two principal stresses distribute uniformly along the thickness direction. Based on this analysis, the stress state and the deformation characteristics of the deformation zone in all kinds of stamping forming can be denoted by the points in the coordinates of the plane principal stresses and the coordinates of the corresponding plane principal strains.4.Raw materials for stamping formingThere are a lot of raw materials used in stamping forming, and the properties of these materials may have large difference. The stamping forming can be succeeded only by determining the stamping method, the forming parameters and the die structures according to the properties and characteristics of the raw materials. The deformation of the blank during stamping forming has been investigated quite thoroughly. The relationships between the material properties decided by the chemistry component and structure of the material and the stamping forming has been established clearly. Not only the proper material can be selected based on the working condition and usage demand, but also the new material can be developed according to the demands of the blank properties during processing the stamping part. This is an important domain in stamping forming research. The research on the material properties for stamping forming is as follows:(1).Definition of the stamping property of the material.(2).Method to judge the stamping property of the material, find parameters to express the definitely material property of the stamping forming, establish the relationship between the property parameters and the practical stamping forming, and investigate the testing methods of the property parameters.(3).Establish the relationship among the chemical component, structure, manufacturing process and stamping property.The raw materials for stamping forming mainly include various metals and nonmetal plate. Sheet metal includes both ferrous and nonferrous metals. Although a lot of sheet metals are used in stamping forming, the most widely used materials are steel, stainless steel, aluminum alloy and various composite metal plates.5.Stamping forming property of sheet metal and its assessing method The stamping forming property of the sheet metal is the adaptation capability of the sheet metal to stamping forming. It has crucial meaning to the investigation of the stamping forming property of the sheet metal. In order to produce stamping forming parts with most scientific, economic and rational stamping forming process and forming parameters, it is necessary to understand clearly the properties of the sheet metal, so as to utilize the potential of the sheet metal fully in the production. On the other hand, to select plate material accurately and rationally in accordance with the characteristics of the shape and dimension of the stamping forming part and its forming technique is also necessary so that a scientific understanding and accurate judgment to the stamping forming properties of the sheet metal may be achieved.There are direct and indirect testing methods to assess the stamping property of the sheet metal.Practicality stamping test is the most direct method to assess stamping forming property of the sheet metal. This test is done exactly in the same condition as actual production by using the practical equipment and dies. Surely, this test result is most reliable. But this kind of assessing method is not comprehensively applicable, and cannot be shared as a commonly used standard between factories.The simulation test is a kind of assessing method that after simplifying and summing up actual stamping forming methods, as well as eliminating many trivial factors, the stamping properties of the sheet metal are assessed, based on simplified axial-symmetric forming method under the same deformation and stress states between the testing plate and the actual forming states. In order to guarantee the reliability and generality of simulation results, a lot of factors are regulated in detail, such as the shape and dimension of tools for test, blank dimension and testing conditions(stamping velocity, lubrication method and blank holding force, etc).Indirect testing method is also called basic testing method its characteristic is to connect analysis and research on fundamental property and principle of the sheet metal during plastic deformation, and with the plastic deformation parameters of the sheet metal in actual stamping forming, and then to establish the relationship between the indirect testing results(indirect testing value) and the actual stamping forming property (forming parameters). Because the shape and dimension of the specimen and the loading pattern of the indirect testing are different from the actual stamping forming, the deformation characteristics and stress states of the indirect test are different from those of the actual one. So, the results obtained form the indirect test are not the stamping forming parameters, but are the fundamental parameters that can be used to represent the stamping forming property of the sheet metal.冲压成形的特点与板材冲压成形性能1.概述冲压是通过模具使板材产生塑性变形而获得成品零件的一次成形工艺方法。
2冲压成形的特点与基本规律分析

2冲压成形的特色与基本规律2.1冲压成形的特色(1)平面应力状态多大部分的冲压变形都能够近似作为平面应力状态办理。
(2)伸长类变形多以拉应力作用为主的伸长类冲压成形多于以压应力为主的压缩类成形。
(3)静水压力影响小板料冲压成形时,毛坯中的内应力数值靠近或等于资料的折服应力。
(4)模具的拘束作用小大部分状况下板料毛坯都存在必定自由度,经常只有一侧表面与模具接触。
冲压技术的研究方向:(1) 冲压成形理论研究模拟板料的塑性变形过程,实现优化设计。
(2) 冲压工艺研究精细冲压、软模成形、高能高速成形、超塑性成形及无模多点成形等。
(3) 冲压模具研究资料技术、热办理、表面技术、加工技术、检测技术及模具 CAD/CAM 技术等。
(4) 资料性能研究板材成形性、形状冻结性。
2.2冲压成形中毛坯的剖析·20 ·冲压工艺与模具设计塑性变形区——应力状态知足折服准则的地区(正在产生塑性变形的地区)不变形区——没有知足折服准则的地区(不会产生塑性变形)已变形区——已经达成了塑性变形的地区待变形区——暂不变形的地区传力区——将冲模的作使劲传达给变形区的区域冲压成形过程是不停变化的连续过程,各个地区之间能够互相转变。
(a) 拉伸(b) 再次拉伸(c) 翻边(d) 缩口图 2.1冲压毛坯剖析2.3冲压变形的分类·20 ·第 2 章冲压成形的特色与基本规律·21··21··22 ·冲压工艺与模具设计图 2.2冲压应力争图 2.3冲压应变图吉田变形分类:拉深,胀形,翻孔,曲折区分冲压工艺成形地区有三个基本参数,即拉深系数 d/D0(纵坐标);翻边系数d0/d(横坐标);轴对称冲压件的旋转角θ , θ <360o 时属不关闭冲压成形。
·22 ·第 2 章冲压成形的特色与基本规律·23·1.当拉深系数 d/ D0 从 0 增添到 1.0 时,胀形、翻边和扩孔工艺均转变成拉深,2.当翻边系数 d0/d 从 0 增添到 1.0 时,成形工艺由胀形转变成扩孔,尔后又变成翻边。
第6章 冲压性能及成形极限

b b0 R b t ln t t0 ln
R 、n 是板料两个特定成形指标; R 平面内易于变形,厚度减薄轻。 1 R R00 R900 R450 7、凸耳参数( 面内异性系数) 2 该值大,拉深件口部严重不平齐,需修边切除。
用杯底破裂时杯口平均直径评价称为ccv分散性颈缩diffusenecking载荷开始随变形增大而减小由于应变硬化这种颈缩在一定尺寸范围内可以转移使材料在这个范围内产生亚稳定的塑性流动故载荷下降比较缓慢
第六章 冲压性能与成形极限
一、冲压性能一般概念
1、冲压成形性能:板料对冲压成形工艺的适应能力。 2、拉伸失稳: 板料在拉应力作用下局部出现颈缩或破裂的现象。 3、压缩失稳: 板料在压应力作用下起皱的现象。 4、成形极限: 板料发生失稳前可以达到大的最大变形程度。 5、总体成形极限:板料失稳前某些特定的总体尺寸可以达到的最大变化程 度,如极限拉深系数、极限翻边系数、极限胀形高度等。 6、局部成形极限:板料失稳前局部尺寸可以达到的最大变化程 度,如局部 极限应变。 7、成形极限图: (Forming Limit Diagrams , 简称FLD ) 。由不同应变路径 下的局部极限应变构成的曲线或条带形区域。它全面反 映了板料在单向或双向拉应力作用下抵抗颈缩或破裂的 能力。
4、总延伸率 t (lt l0 ) / l0 总延伸率大 ,变形程度大,抗破裂性好 d log n 5、应变硬化指数 n n K d log
n 值不仅提高局部应变能力,且使应变均匀。 n 值大增大成形极限 分散性颈缩失稳 1 n 集中性颈缩失稳 1 2n
6、塑性应变比(厚向异性系数)R
五、冲压成形性能试验方法与指标
冲压成形与板材冲压
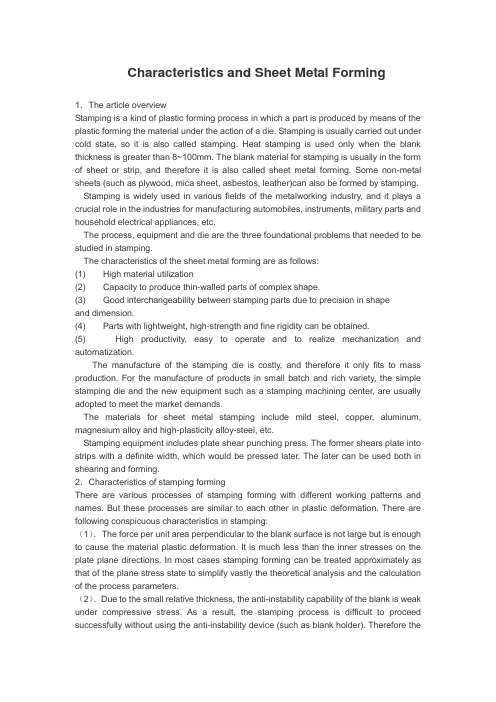
Characteristics and Sheet Metal Forming1.The article overviewStamping is a kind of plastic forming process in which a part is produced by means of the plastic forming the material under the action of a die. Stamping is usually carried out under cold state, so it is also called stamping. Heat stamping is used only when the blank thickness is greater than 8~100mm. The blank material for stamping is usually in the form of sheet or strip, and therefore it is also called sheet metal forming. Some non-metal sheets (such as plywood, mica sheet, asbestos, leather)can also be formed by stamping. Stamping is widely used in various fields of the metalworking industry, and it plays a crucial role in the industries for manufacturing automobiles, instruments, military parts and household electrical appliances, etc.The process, equipment and die are the three foundational problems that needed to be studied in stamping.The characteristics of the sheet metal forming are as follows:(1) High material utilization(2) Capacity to produce thin-walled parts of complex shape.(3) Good interchangeability between stamping parts due to precision in shapeand dimension.(4) Parts with lightweight, high-strength and fine rigidity can be obtained.(5) High productivity, easy to operate and to realize mechanization and automatization.The manufacture of the stamping die is costly, and therefore it only fits to mass production. For the manufacture of products in small batch and rich variety, the simple stamping die and the new equipment such as a stamping machining center, are usually adopted to meet the market demands.The materials for sheet metal stamping include mild steel, copper, aluminum, magnesium alloy and high-plasticity alloy-steel, etc.Stamping equipment includes plate shear punching press. The former shears plate into strips with a definite width, which would be pressed later. The later can be used both in shearing and forming.2.Characteristics of stamping formingThere are various processes of stamping forming with different working patterns and names. But these processes are similar to each other in plastic deformation. There are following conspicuous characteristics in stamping:(1).The force per unit area perpendicular to the blank surface is not large but is enough to cause the material plastic deformation. It is much less than the inner stresses on the plate plane directions. In most cases stamping forming can be treated approximately as that of the plane stress state to simplify vastly the theoretical analysis and the calculation of the process parameters.(2).Due to the small relative thickness, the anti-instability capability of the blank is weak under compressive stress. As a result, the stamping process is difficult to proceed successfully without using the anti-instability device (such as blank holder). Therefore thevarieties of the stamping processes dominated by tensile stress are more than dominated by compressive stress.(3).During stamping forming, the inner stress of the blank is equal to or sometimes less than the yield stress of the material. In this point, the stamping is different from the bulk forming. During stamping forming, the influence of the hydrostatic pressure of the stress state in the deformation zone to the forming limit and the deformation resistance is not so important as to the bulk forming. In some circumstances, such influence may be neglected. Even in the case when this influence should be considered, the treating method is also different from that of bulk forming.(4).In stamping forming, the restrain action of the die to the blank is not severs as in the case of the bulk forming (such as die forging). In bulk forming, the constraint forming is proceeded by the die with exactly the same shape of the part. Whereas in stamping, in most cases, the blank has a certain degree of freedom, only one surface of the blank contacts with the die. In some extra cases, such as the forming of the blank on the deforming zone contact with the die. The deformation in these regions are caused and controlled by the die applying an external force to its adjacent area.Due to the characteristics of stamping deformation and mechanics mentioned above, the stamping technique is different form the bulk metal forming:(1).The importance or the strength and rigidity of the die in stamping forming is less than that in bulk forming because the blank can be formed without applying large pressure per unit area on its surface. Instead, the techniques of the simple die and the pneumatic and hydraulic forming are developed.(2).Due to the plane stress or simple strain state in comparison with bulk forming, more research on deformation or force and power parameters has been done. Stamping forming can be performed by more reasonable scientific methods. Based on the real time measurement and analysis on the sheet metal properties and stamping parameters, by means of computer and some modern testing apparatus, research on the intellectualized control of stamping process is also in proceeding.(3).It is shown that there is a close relationship between stamping forming and raw material. The research on the properties of the stamping forming, that is, forming ability and shape stability, has become a key point in stamping technology development, but also enhances the manufacturing technique of iron and steel industry, and provides a reliable foundation for increasing sheet metal quality.3.Categories of stamping formingMany deformation processes can be done by stamping, the basic processes of the stamping can be divided into two kinds: cutting and forming.Cutting is a shearing process that one part of the blank is cut from the other. It mainly includes blanking, punching, trimming, parting and shaving, where punching and blanking are the most widely used. Forming is a process that one part of the blank has some displacement from the other. It mainly includes deep drawing, bending, local forming, bulging, flanging, necking, sizing and spinning.In substance, stamping forming is such that the plastic deformation occurs in the deformation zone of the stamping blank caused by the external force. The stress state and deformation characteristic of the deformation zone are the basic factors to decide theproperties of the stamping forming. Based on the stress state and deformation characteristics of the deformation zone, the forming methods can be divided into several categories with the same forming properties and be studied systematically.The deformation zone in almost all types of stamping forming is in the plane stress state. Usually there is no force or only small force applied on the blank surface. When is assumed that the stress perpendicular to the blank surface equals to zero, two principal stresses perpendicular to each other and act on the blank surface produce the plastic deformation of the material. Due to the small thickness of the blank, it is assumed approximately the two principal stresses distribute uniformly along the thickness direction. Based on this analysis, the stress state and the deformation characteristics of the deformation zone in all kinds of stamping forming can be denoted by the points in the coordinates of the plane principal stresses and the coordinates of the corresponding plane principal strains.4.Raw materials for stamping formingThere are a lot of raw materials used in stamping forming, and the properties of these materials may have large difference. The stamping forming can be succeeded only by determining the stamping method, the forming parameters and the die structures according to the properties and characteristics of the raw materials. The deformation of the blank during stamping forming has been investigated quite thoroughly. The relationships between the material properties decided by the chemistry component and structure of the material and the stamping forming has been established clearly. Not only the proper material can be selected based on the working condition and usage demand, but also the new material can be developed according to the demands of the blank properties during processing the stamping part. This is an important domain in stamping forming research. The research on the material properties for stamping forming is as follows:(1).Definition of the stamping property of the material.(2).Method to judge the stamping property of the material, find parameters to express the definitely material property of the stamping forming, establish the relationship between the property parameters and the practical stamping forming, and investigate the testing methods of the property parameters.(3).Establish the relationship among the chemical component, structure, manufacturing process and stamping property.The raw materials for stamping forming mainly include various metals and nonmetal plate. Sheet metal includes both ferrous and nonferrous metals. Although a lot of sheet metals are used in stamping forming, the most widely used materials are steel, stainless steel, aluminum alloy and various composite metal plates.5.Stamping forming property of sheet metal and its assessing methodThe stamping forming property of the sheet metal is the adaptation capability of the sheet metal to stamping forming. It has crucial meaning to the investigation of the stamping forming property of the sheet metal. In order to produce stamping forming parts with most scientific, economic and rational stamping forming process and forming parameters, it is necessary to understand clearly the properties of the sheet metal, so as to utilize the potential of the sheet metal fully in the production. On the other hand, toselect plate material accurately and rationally in accordance with the characteristics of the shape and dimension of the stamping forming part and its forming technique is also necessary so that a scientific understanding and accurate judgment to the stamping forming properties of the sheet metal may be achieved.There are direct and indirect testing methods to assess the stamping property of the sheet metal.Practicality stamping test is the most direct method to assess stamping forming property of the sheet metal. This test is done exactly in the same condition as actual production by using the practical equipment and dies. Surely, this test result is most reliable. But this kind of assessing method is not comprehensively applicable, and cannot be shared as a commonly used standard between factories.The simulation test is a kind of assessing method that after simplifying and summing up actual stamping forming methods, as well as eliminating many trivial factors, the stamping properties of the sheet metal are assessed, based on simplified axial-symmetric forming method under the same deformation and stress states between the testing plate and the actual forming states. In order to guarantee the reliability and generality of simulation results, a lot of factors are regulated in detail, such as the shape and dimension of tools for test, blank dimension and testing conditions(stamping velocity, lubrication method and blank holding force, etc).Indirect testing method is also called basic testing method its characteristic is to connect analysis and research on fundamental property and principle of the sheet metal during plastic deformation, and with the plastic deformation parameters of the sheet metal in actual stamping forming, and then to establish the relationship between the indirect testing results(indirect testing value) and the actual stamping forming property (forming parameters). Because the shape and dimension of the specimen and the loading pattern of the indirect testing are different from the actual stamping forming, the deformation characteristics and stress states of the indirect test are different from those of the actual one. So, the results obtained form the indirect test are not the stamping forming parameters, but are the fundamental parameters that can be used to represent the stamping forming property of the sheet metal.。
什么是冲压特点及应用

什么是冲压特点及应用冲压(Stamping)是一种广泛应用于金属加工工艺中的成型方法。
通过将金属板材或带材放入冲压机的模具,利用模具的动作使得材料产生塑性变形,从而获得所需的零件形状。
冲压具有许多独特的特点和广泛的应用领域。
首先,冲压具有高效的生产能力。
冲压机通常采用连续工作方式,可以在一分钟内进行多次冲压操作。
此外,模具设计精确,能够实现高度自动化生产,大大提高了生产效率。
冲压还可以在一次操作中完成多个工序,如冲孔、折弯、成形、拉延等,从而使得生产过程更加有效率。
其次,冲压能够实现高精度的加工。
冲压的模具通常采用高精度的数控设备制造,能够保证零件尺寸的精确度和形状的一致性。
由于冲压操作是在封闭模具中进行的,所以可以有效地避免材料的回弹和变形,从而保证零件的几何形状和尺寸精度。
另外,冲压还具有较好的材料利用率。
在冲压加工过程中,通过合理的布局和排样来最大限度地利用金属板材的原材料。
此外,冲压还可以通过优化模具设计和工艺参数来减少废品产生,并实现材料的节约和资源的可持续利用。
冲压具有广泛的应用领域。
首先,在汽车制造领域,冲压技术广泛应用于车身、车门、车顶、行李箱等零部件的制造。
冲压能够满足汽车零部件的高强度、高精度和高品质要求,提高汽车的安全性和舒适性。
其次,在家电和电子领域,冲压技术通常用于制造电视机壳、洗衣机外壳、冰箱门板等产品。
冲压能够快速、高效地生产大批量的金属零件,满足家电和电子产品的外观要求和性能要求。
此外,冲压还广泛应用于航空航天、建筑、工程机械和家具等领域。
冲压技术虽然具有许多优点,但也存在一些挑战和难点。
首先,冲压模具的制造和维护成本较高。
模具的设计和制造需要大量的人力和物力投入,而且需要具备高水平的技术和经验。
此外,冲压过程中模具的磨损和损坏比较常见,需要定期进行维护和更换,增加了生产成本和周期。
其次,冲压加工过程中产生的噪音、振动和废气对环境和工人的健康造成一定的影响。
因此,需要采取适当的措施来降低冲压过程中的噪音污染和环境污染。
冲压成型工艺特点
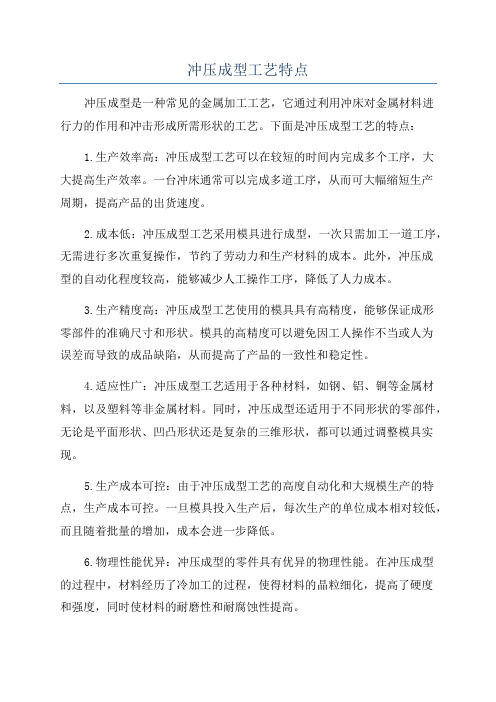
冲压成型工艺特点冲压成型是一种常见的金属加工工艺,它通过利用冲床对金属材料进行力的作用和冲击形成所需形状的工艺。
下面是冲压成型工艺的特点:1.生产效率高:冲压成型工艺可以在较短的时间内完成多个工序,大大提高生产效率。
一台冲床通常可以完成多道工序,从而可大幅缩短生产周期,提高产品的出货速度。
2.成本低:冲压成型工艺采用模具进行成型,一次只需加工一道工序,无需进行多次重复操作,节约了劳动力和生产材料的成本。
此外,冲压成型的自动化程度较高,能够减少人工操作工序,降低了人力成本。
3.生产精度高:冲压成型工艺使用的模具具有高精度,能够保证成形零部件的准确尺寸和形状。
模具的高精度可以避免因工人操作不当或人为误差而导致的成品缺陷,从而提高了产品的一致性和稳定性。
4.适应性广:冲压成型工艺适用于各种材料,如钢、铝、铜等金属材料,以及塑料等非金属材料。
同时,冲压成型还适用于不同形状的零部件,无论是平面形状、凹凸形状还是复杂的三维形状,都可以通过调整模具实现。
5.生产成本可控:由于冲压成型工艺的高度自动化和大规模生产的特点,生产成本可控。
一旦模具投入生产后,每次生产的单位成本相对较低,而且随着批量的增加,成本会进一步降低。
6.物理性能优异:冲压成型的零件具有优异的物理性能。
在冲压成型的过程中,材料经历了冷加工的过程,使得材料的晶粒细化,提高了硬度和强度,同时使材料的耐磨性和耐腐蚀性提高。
7.可实现多种复杂加工:冲压成型工艺可以实现多种复杂的加工,如切割、冲孔、贴合、打凸处理等。
通过调整模具和工艺参数,可以实现对材料进行多方向、多角度的加工,能够满足复杂零部件的加工要求。
8.环保节能:冲压成型工艺不需要使用大量的切削液和冷却液,减少了切削液和冷却液的消耗和处理成本。
此外,由于冲压成型工艺不会产生废气和废水,无需进行处理和排放,更加符合环保要求。
总之,冲压成型工艺具有高效、低成本、高精度、广泛适应性和优异的物理性能等特点,被广泛应用于各个行业的零部件制造过程中。
冲压成型工艺定义、特点及基本要求

冲压成型工艺定义、特点及基本要求冲压成型工艺定义:冲压工艺是通过模具对毛坯施加外力,使之产生塑性变形或分离,从而获得一定尺寸、形状和性能的工件的加工方法。
冲压工艺的应用范围十分广泛,既可以加工金属板料、棒料,也可以加工多种非金属材料。
由于加工通常是在常温下进行的,故又称为冷冲压。
固定台冲压工艺的特点:1、用冷冲压加工方法可以得到形状复杂、用其他加工方法难以加工的工件,如薄壳零件等。
冷冲压件的尺寸精度是由模具保证的,因此,尺寸稳定,互换性好。
2、材料利用率高,工件重量轻、刚性好、强度高、冲压过程耗能少。
因此,工件的成本较低。
3、操作简单、劳动强度低、易于实现机械化和自动化、生产率高。
4、冲压加工中所用的模具结构一般比较复杂,生产周期较长、成本较高冲压材料的基本要求:冲压所用的材料,不仅要满足产品设计的技术要求,还应当满足冲压工艺的要求和冲压后的加工要求(如切削加工、电镀、焊接等)。
冲压工艺对材料的基本要求主要有:对冲压成形性能的要求:对于成形工序,为了有利于冲压变形和制件质量的提高,材料应具有:良好的塑性(均匀伸长率δb高)、屈强比(σs/σb)小、板厚方向性系数大、板平面方向性系数小、材料的屈服强度与弹性模量的比值(σs /E)小。
对于分离工序,并不需要材料有很好的塑性,但应具有一定的塑性。
塑性越好的材料,越不易分离。
对材料厚度公差的要求:材料的厚度公差应符合国家规定标准。
因为一定的模具间隙适用于一定厚度的材料,材料厚度公差太大,不仅直接影响制件的质量,还可能导致模具和冲床的损坏。
固定台冲床对表面质量的要求材料的表面应光洁平整,无分层和机械性质的损伤,无锈斑、氧化皮及其它附着物。
表面质量好的材料,冲压时不易破裂,不易擦伤模具,工件表面质量也好。
冲压成形概述

汽车主要零件
2.1 冲压成形特点与分类
2.2 冲压模具设计与制造的内容 2.3 冲压常用材料 2.4 冲压设备简介
1、什么是冲压?
冲压是将各种不同规格的板料或坯料(金 属或非金属),在室温下对其施加压力(如 通过压力机及模具等),使之变形或分离, 以获得各种形状零件的一种加工工艺。 冲压工艺是塑性加工的基本方法之一。它主 要用于加工板料零件,所以有时也称之为板 料冲压。 冲压不仅可以加工金属板料,而且也可以加 工非金属板料。
2.4 冲压设备简介
机械压力机:曲柄压力机和摩擦压力机 液压压力机
机械压力机应用最广泛
曲柄压力机最为常见
1、曲柄压力机
– 传动系统:电机、皮带、皮带轮、齿轮、 传动轴等
– 工作机构:曲柄、连轴、滑块等 – 机身:将所有部分联成一个整体
一些压力机还设有顶出机构、压边装置
1、曲柄压力机
曲柄压力机
* 扩口 —— 将空心件口部直径扩大
Special forming
* 缩口 —— 将空心件口部直径缩小 * 旋压 —— 毛料随旋压机主轴旋转,赶棒加
压于毛坯,使毛坯逐渐紧贴模具以获得所需 形状和尺寸的制件,有时也称为赶形
* 强力旋压 —— 在旋转状态下,用辊轮 使毛坯逐步成形的方法,有时也称为旋 薄
– 工作原理 – 模具安装 – 滑块往复运
动完成生产 所需的操作
1、曲柄压力机
曲柄压力机
闭式冲床
开式冲床
1、曲柄压力机
曲柄压力机 闭式冲床
特点:
– 前后送料(操作与安 装模具都不方便)
– 床身刚度大 – 适合:
精度要求高的轻型压 力机
一般要求的中、大型 压力机
1、曲柄压力机
- 1、下载文档前请自行甄别文档内容的完整性,平台不提供额外的编辑、内容补充、找答案等附加服务。
- 2、"仅部分预览"的文档,不可在线预览部分如存在完整性等问题,可反馈申请退款(可完整预览的文档不适用该条件!)。
- 3、如文档侵犯您的权益,请联系客服反馈,我们会尽快为您处理(人工客服工作时间:9:00-18:30)。
Characteristics of Stamping and Properties of Sheet MetalFormingStamping is a kind of plastic forming process in which a part is produced by means of the plastic forming of the material under the action of a die.Stamping is usually carried out under cold state,so it is also called cold stamping.Heat stamping is used only when the blank thickness is greater than 8~1 00mm.The blank material for stamping is usually in the from sheet or strip,and therefore it is also called sheet metal forming.Some non—metal sheets(such as plywood,mica sheet,asbestos,leather)can also be formed by stamping.Stamping is widely used in various of the metalworking industry, and it plays a crucial role in the industries for manufacturing automobiles, instruments,military parts and household electrical appliances,etc.The process,equipment and die are the three foundational problems that needed t0 be studied in stamping.The characteristics of the sheet metal forming are as follows:(1)High material utilization.(2)Capacity to produce thin—walled parts of complex shape.(3)Good interchangeability between stamping parts due to precision in shape and dimension.(4)Parts with lightweight,high—strength and fine rigidity can be obtained.(5)High productivity,easy to operate and to realize mechanization and automatizationThe manufacture of the stamping die is costly,and therefore it only fits t0 mass production.For the manufacture of products in small batch and rich variety,the simple stamping die and the new equipment such as a stamping machining center,are usually adopted to meet he market demands.The materials for sheet metal stamping include mi ld steel,copper,aluminum,magnesium alloy and high-plasticity alloy—steel,etc.Stamping equipment includes plate shear and punching press.The former shears plate into strips with a definite width,which would be pressed later.The later can be used both in shearing and forming.1.1 Characteristics of stamping formingThere are various processes of stamping forming with different working patterns and names.But these processes are similar to each other in plastic deformation.There are following conspicuous characteristics in stamping:(1)The force per unit area perpendicular to the blank surface is not large but is enough tocause the material plastic deformation.I t is much less than the inner stresses on the plate plane directions.In most cases stamping forming can be treated approximately as that of the plane stress state to simplify vastly the theoretical analysis and the calculation of the process parameters.(2)Due to the small relative thickness,the anti-instability capability of the blank is weak under compressive stress.As a result,the stamping process is difficult to proceed successfully without using the anti-instability device(such as blank holder).Therefore the variety of the stamping processes dominated by tensile stress are more than those dominated by compressive stress.(3)During stamping forming,the Inner stress of the blank is equal to or sometimes less than the yield stress of the material.In this point,the stamping is different from the bulk forming.During stamping forming,the influence of the hydrostatic pressure of the stress state in the deformation zone to the forming limit and the def6nmation resistance is not so important as to the bulk forming.In some circumstances,such influence may be neglected.Even in the case when this influence should be considered,the treating meth()d is also different from that of bulk forming.(4)In stamping forming,the restrain action of the die to the blank is not severe as in the case of the bulk forming(such as die forging).In bulk forming,the constraint forming is proceeded by the die with exactly the same shape of the part.Whereas in stamping,in most cases,the blank has a certain degree of freedom,only one surface of the blank contacts with the die.In some extra cases,such as the forming of the suspended region of sphere or cone,and curling at the end of tube,neither sides of the blank on the deforming zone con-tact with the die.The deformation in these regions are caused and controlled the die applying an external force to its adjacent area.Due to the characteristics of stamping deformation and mechanics mentioned above,the stamping technique is different from the bulk metal forming:(1)The importance of the strength and rigidity of the die in stamping forming is less than that in bulk forming because the blank can be formed without applying large pressure unit area on its surface.Instead,the techniques of the simple die and the pneumatic and hydraulic forming are developed.(2)Due to the plane stress or simple strain state in comparison with bulk forming,more research on deformation or force and power parameters has been done.Stamping forming can be performed by more reasonable scientific methods.Based on the real time measurement and analysis on the sheet metal properties and stamping parameters.by means of computer and some modem testing apparatus research on the intellectualized control of stamping process isalso in proceeding .(3)It is shown that there is a close relationship between stamping forming and raw material-The research on the properties of the stamping forming ,that is ,forming ab1ityand shape stability .has become a key point in stamping technology .The research on the properties of the sheet metal stamping not only meets the need of the stamping technology development ,but also enhances the manufacturing technique of iron and steel industry 。