航煤加氢资料
FRIPP煤油加氢技术交流概述

馏程范围,℃ 硫,μg/g 硫醇硫,μg/g 博士试验
赛波特颜色
原料油 1.6 290 4.0 120
152~224
1075 14
127
1
通过
+20 +30
加氢生成油 1.2 0.8 0.8 0.8 290 290 240 240 4.5 2.5 4.0 2.5 80 150 80 150
58 8.2 422 354 2.8 2.8 5.6 3.1 通过 通过 通过 通过 +30 +30 +30 +30
工艺条件
压力,MPa 反应温度,℃ 体积空速,h-1 氢油体积比
油品性质
馏程范围,℃ 硫,μg/g 硫醇硫,μg/g 博士试验
赛波特颜色
原料油
146~240 1196 102
+24
加氢生成油 1.2 1.2 0.8 240 290 260 4.0 4.0 3.0 80 80 100
357 3 通过
+30
催化剂应具有高活性和活性稳定性
煤油加氢技术交流稿
FRIPP
FRIPP常规航煤加氢催化剂
FH-98A催化剂是针对二次加氢汽煤 柴油馏分开发的催化剂,主要目的是 深度脱氮、解决油品安定性
煤油加氢技术交流稿
FRIPP
FRIPP常规航煤加氢催化剂
FH-98A催化剂 载体:Si-Al 化学组成:W-Ni
赛氏比色
+21
>+30
+22
>+30
硫醇硫,μg/g
103
2
74
2
硫,μg/g
1169.2
14.7
航煤加氢资料

能耗指标及计算表/ d/ d# |) V: L) V6 T4 H, |
序 0 T; \" S+ X- F% d4 N5 x b$ O
号
项目
年消耗量
能耗指标
能耗+ {) g; A+ e0 h7 ?) `: V7 r1 ?
单位
数量
单位
系数
MJ/a
1
循环水
万吨
45.70
ห้องสมุดไป่ตู้
千焦/吨
6.38
191.47
3
电
万度
233.5
千焦/度
11.84
2765.77! |" }4 `( E {3 y4
K8 u
4
燃料气
万吨
78.96
千焦/吨
39.464
3115.84
5
氮气
万标米 3
2.6
千焦/标米 3
6.28
16.35
6
净化风
万标米 3
75.60
千焦/标米 3
1.59
120.2 d* a) \,
[, U) s5 R
7
蒸汽(1.0MPa)
(5)
燃料气系统 6 b6 k. B' }* X {% I( A: a8 f
燃料气自装置外系统来部分至加热炉作燃料气,另一部分至(1001-D-101)作保护气。
(6)
氮气系统 1 Y% l+ C) g) w
低压氮气(0.85MPa)由系统进入装置各用氮点。
高压氮气(2.5MPa)进入装置各用氮点。1 M2 ~6 G0 [5 @2 m0 @
万吨
0.17
千焦/吨
3182
航煤加氢装置流程介绍

航煤加氢装置流程介绍
航煤加氢装置是用于将航煤(船上燃料)转化为液化天然气(LNG)的设备。
其工艺流程大致如下:
1. 航煤进料:将航煤从船上转移到航煤加氢装置中。
2. 预处理:将航煤经过粉碎、干燥、筛分等预处理工序,减少杂质含量。
3. 加氢:将预处理好的航煤与氢气混合在一起,在高温高压下进行加氢反应。
4. 分离:通过蒸馏、压缩等方式将LNG和水分离。
5. 冷却:将分离后的LNG进行冷却,使其达到储存和运输要求的温度。
6. 储存和运输:将LNG储存在液化气船或液化气罐车中,运往目的地。
请注意,这只是航煤加氢装置的大致流程,具体的工艺可能因生产厂家而异。
航煤加氢资料

装置基本原理介绍加氢精制是在一定的温度、压力、氢油比和空速条件下,借助催化剂的作用,将油品(直馏航煤)中的硫、氮、氧化合物转化成易除去的H2S、NH3、H2O而脱除,并将油品中的杂质如重金属截留在催化剂中。
同时烯烃、芳烃得到饱和,从而得到安定性、燃烧性都较好的产品。
, u- Z0 j/ D" s2 w4 J. f/ g脱硫硫化物的存在影响了油品的性质,给油品的加工和使用带来了许多危害:对机械设备的腐蚀,给炼油过程增加困难,降低油品的质量,燃料燃烧造成环境污染等。
其中,有代表的含硫化合物主要有硫醇、硫醚、二硫化物和噻吩等。
9 {5 S; D' ^1 i1 i; XRSH+H2→RH+ H2S' }8 K5 \7 N0 D7 I脱氮含氮化合物对产品质量的稳定性有较大危害,并且在燃烧时会排放出NOX 污染环境。
石油产品中的含氮化合物主要是杂环化合物,非杂环化合物较少。
2 R" T! {0 K2 a/ ]$ P: d! SR NH2 + H2 RH + NH3% V A- _. a- x' O脱氧RCH2OOH + 2 H2 RH3 + 2H2O' C3 `3 I7 `, i. A* }烯烃、芳烃的饱和; n7 \0 y a) \$ U& u6 C1 R7 m9 M- z" nRˊCH=CHˊR RˊCH2¬¬-CH2Rˊx8 r0 W4 ~! B7 d- _! M3 p7 L: U8 H. O7 M4 u工艺流程说明反应部分直馏航煤自原料罐区及常压装置来经原料油过滤器(1001-SR-101A/B)原料油脱水器(1001-D-104)进入原料缓冲罐(1001-D-101)。
经加氢进料泵(1001-P-101A/B)升压至约与氢气混合,然后经反应流出物/反应进料换热器(1001-E-101A/B/C/D)壳程,换热后进入加热炉(1001-F-101)加热至反应所需的温度进入反应器(1001-R-101)。
航煤液相加氢技术的研究及应用

航煤液相加氢技术的研究及应用摘要煤液相加氢技术是将煤经过加氢、改性、裂解的过程在液相中生成液体燃料,包括半熟油、微烃油、芳香油。
煤液相加氢技术在研究及应用方面近年来取得一定的进展,但仍存在工艺结构复杂、生产率低、成本高等问题,加之原料煤质量及污染物含量各异,技术应用仍较有限。
因此,研究以改善原料质量、提高加氢裂解及精制工艺,提高生产效率及洁净度,降低生产成本等在加强对煤液相加氢技术的研究及应用,是十分必要的。
一、煤液相加氢的原理及目的煤液相加氢是指将原料煤在液相中接受加氢、改性、裂解这些反应处理,形成液态燃料的技术。
其中,煤的原子量通过原子量变大、难解部分向热稳定原子量小、容易解离的小分子物质产生裂解,主要从煤中获得半熟油、微烃油和芳香油等液态燃料,从而起到加工优质液体燃料的作用。
煤液相加氢是把原料煤经过加氢、改性、裂解反应处理,从而生成优质液体燃料的技术,主要用于解决煤炭质量较差、污染物含量较高等不足,实现节能降耗及环保的目的。
它还可以起到准化能源的作用,增强燃料的耐久性,提高汽车性能,减少汽车机油、润滑油的消耗,从而节约能源消耗。
(1)煤深加工技术研究。
包括对煤的质量组成、表征参数及加工特性的较全面的研究,以优化煤的深加工技术,特别是煤液相加氢技术的技术性评价,把握煤的质量条件和加工技术要点,制定加工的实施方案;(2)煤液相加氢条件优化研究。
包括煤液相加氢反应器的设计、加氢剂量及反氢条件的优化、反应器介质温度和压力条件及时间的选择等;(3)煤液相加氢产物分离技术研究。
包括研究各液态燃料及污柩物的分离技术、优化分离技术、开发新型材料等研究工作。
(1)液体燃料的生产应用。
可获得优质的半熟油、微烃油、芳香油等液体燃料,生产出符合国家标准的柴油和汽油;(2)煤液相加氢技术在能源利用方面的应用。
可以起到准化能源的效果,提高燃料的抗磨耐久性、抗热性等特性,提高汽车性能,减少汽车机油、润滑油的消耗,从而省事能源消耗。
加氢裂化装置优化运行生产航煤技术攻关

加氢裂化装置优化运行生产航煤技术攻关随着我国对航空煤油需求的不断增加,加氢裂化装置的优化运行生产对于航煤技术攻关变得尤为重要。
加氢裂化技术是航煤生产中的关键环节,其优化运行将直接影响航煤质量和产量。
为了提高航煤的质量和产量,降低生产成本,我国科研人员不断进行技术攻关,积极寻求技术创新,推动加氢裂化装置的优化运行生产。
一、加氢裂化技术在航煤生产中的地位加氢裂化技术是将原油或者重质油转化成航空煤油的主要方法之一,也是目前航煤生产中使用最为广泛的技术之一。
加氢裂化技术可以将原油中的重质烃类分子在催化剂的作用下裂解成较轻质的烃类物质,可提高航煤的产量、改善航煤的质量、降低航煤的硫含量、降低航煤的芳烃和烯烃含量,保障航煤的需求。
加氢裂化技术在航煤生产中的地位非常重要。
随着对航煤的需求不断增加,对加氢裂化装置的技术要求也在不断提高,如何实现加氢裂化装置的优化运行已成为当前航煤技术攻关的重要课题。
二、加氢裂化装置存在的问题1. 催化剂的选择问题:催化剂是加氢裂化装置的重要组成部分,直接影响加氢裂化反应的效率和产物的质量。
目前,我国在加氢裂化催化剂研究上与国际先进水平还存在一定差距,催化剂的稳定性和活性需要进一步提高。
2. 操作参数的优化问题:加氢裂化装置的操作参数对于反应效率和产物质量也有着重要的影响,而当前加氢裂化装置在运行过程中,参数调节仍然存在很多困难,导致反应效率和产品质量不能得到最大程度的提高。
3. 能源消耗问题:加氢裂化装置的运行需要耗费大量的能源,目前仍缺乏有效的节能减排技术,导致能源消耗较大。
以上问题的存在导致了加氢裂化装置在航煤生产中的运行存在一定的问题和障碍,严重影响了航煤的产量和质量。
如何解决这些问题,实现加氢裂化装置的优化运行,成为当前航煤技术攻关的重点和难点。
为了解决加氢裂化装置存在的问题,提高航煤的产量和质量,我国科研人员积极开展技术攻关,推动加氢裂化装置的优化运行生产。
主要进行以下几方面的技术攻关:1. 催化剂的研发和优化:加氢裂化装置中的催化剂是影响航煤质量和产量的关键因素之一。
航煤加氢装置操作基础知识
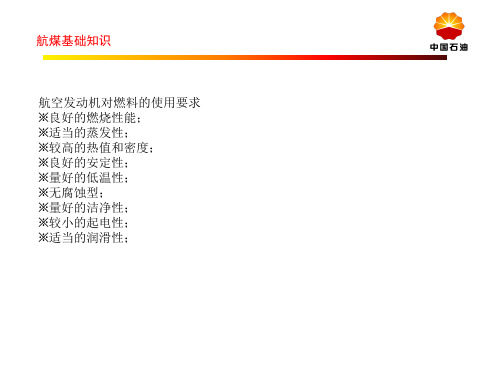
(4).喷气燃料的安定性 喷气燃料的安定性包括储存安定性和热安定性。 储存安定性 喷气燃料在储存过程中容易变化的质量指标有胶质,酸度及颜色等。胶质和酸
喷气燃料燃烧时,首要的是易于起动和燃烧稳定,其次是要求燃烧完全。所谓 燃烧完全度是指单位质量燃料燃烧时实际放出的热量占燃料净热值的百分 率,它直接影响到飞机的动力性能、航程远近和经济性能。
燃料燃烧的完全度一方面受进气压力、进气温度和飞行高度等工作条件的影响 ,另一方面也受燃料的粘度、蒸发性和化学组成的影响,现将后者分述如 下:
(2).喷气燃料形成积碳的倾向
喷气燃料在燃烧过程中会产生炭质微粒,炭质微粒积聚在喷嘴、火焰 筒壁上就形成积炭。喷嘴上的积炭会恶化燃料的雾化质量,使燃 烧过程变坏。积炭附在火焰筒的部分壁上,会使火焰筒因受热不 均匀而变形,甚至产生裂纹。此外,在发动机工作时,火焰筒壁 上剥落下来的积炭碎片会进入涡轮,擦伤叶片。
b.辉光值
当燃料的生炭性强时,其燃气流中的炭粒就多,炽热的炭粒能使火焰 的亮度增加,热辐射加强。辉光值是在一定的火焰辐射强度(相当 于四氢萘烟点时的辐射强度)下,将试验燃料和两个标准燃料分别 在灯中燃烧,比较火焰的温度升高(温升)多少而得出的。生炭性 强的燃料,达到同样辐射强度的火焰温升小,辉光值也小;生炭 性小的燃料,火焰温升大,辉光值也大。对于碳数相同的烃类而 言,烷烃的辉光值最大,环烷烃的居中,芳烃的最小。
喷气燃料燃烧时在发动机中生成积炭的倾向,与燃烧室的构造、发动 机工作条件及燃料的性质都有关系。就燃料而言,其化学组成对 生成积炭的影响最大。在喷气发动机中最容易生成积炭的成分是 芳香烃,尤其是双环芳香烃。为此,在喷气燃料的质量标准中除 限制芳香烃含量外,还规定萘系烃的体积分数不大于3.0%。
基于原油性质变化的航煤加氢装置节能优化经验阐述

基于原油性质变化的航煤加氢装置节能优化经验阐述随着航空业的蓬勃发展,航空煤油(航煤)需求日益增加,为了满足航空运输的需求,航空煤油的生产也在不断增加。
在航煤的生产过程中,加氢装置是非常重要的一环,它可以通过加氢使得原油中的硫、氮和重金属等元素得到脱除,从而保证航空煤油的质量,同时也降低了燃油的环境污染。
随着原油性质的变化,加氢装置在节能方面也面临着一些挑战。
本文将从原油性质变化的角度出发,结合实际案例,探讨航煤加氢装置的节能优化经验。
1. 航煤加氢装置的工作原理航煤加氢装置是利用氢气与原油中的硫、氮和重金属等元素进行反应,生成较为洁净的燃料。
在加氢的过程中,首先将含硫、含氮和重金属的原油通过加热器升温至加氢反应的最佳温度区间,然后送入加氢反应器中与氢气进行反应。
接着,通过冷却器将反应后的产物进行冷却,最后通过分离器将产生的硫、氮和重金属的化合物进行分离,从而得到较为洁净的航煤。
整个加氢过程需要消耗大量的能量,因此如何优化加氢装置的节能效果成为了工程师们的关注焦点。
2. 原油性质变化对加氢装置的影响原油的性质受多种因素影响,如地质条件、原油产地等。
而原油中的硫含量、氮含量等指标则直接影响加氢过程的能耗。
通常情况下,硫含量高的原油需要更多的氢气参与加氢反应,因此能耗也会相应增加。
而随着原油资源的逐渐枯竭,更多的是深度加工含硫、难处理的原油,这使得加氢装置的工作条件更加苛刻,能耗也大大增加。
不同的原油特性也会导致加氢装置的操作参数取值不同。
这包括了反应温度、压力等参数的设定,而这些参数的变化会直接影响到加氢过程的能耗。
3. 航煤加氢装置的节能优化经验(1)合理选择原油在实际生产中,根据原油的性质进行选择,优先选择含硫含量低、易处理的原油,这可以有效降低加氢装置的能耗。
还可以考虑对原油进行混合,通过控制不同原油的比例来达到降低加氢能耗的效果。
(2)优化加氢反应条件根据原油的性质和厂家实际情况,对加氢反应条件进行优化。
- 1、下载文档前请自行甄别文档内容的完整性,平台不提供额外的编辑、内容补充、找答案等附加服务。
- 2、"仅部分预览"的文档,不可在线预览部分如存在完整性等问题,可反馈申请退款(可完整预览的文档不适用该条件!)。
- 3、如文档侵犯您的权益,请联系客服反馈,我们会尽快为您处理(人工客服工作时间:9:00-18:30)。
1.1 装置基本原理介绍加氢精制是在一定的温度、压力、氢油比和空速条件下,借助催化剂的作用,将油品(直馏航煤)中的硫、氮、氧化合物转化成易除去的H2S、NH3、H2O 而脱除,并将油品中的杂质如重金属截留在催化剂中。
同时烯烃、芳烃得到饱和,从而得到安定性、燃烧性都较好的产品。
, u- Z0 j/ D" s2 w4 J. f/ g1.1.1 脱硫硫化物的存在影响了油品的性质,给油品的加工和使用带来了许多危害:对机械设备的腐蚀,给炼油过程增加困难,降低油品的质量,燃料燃烧造成环境污染等。
其中,有代表的含硫化合物主要有硫醇、硫醚、二硫化物和噻吩等。
9 {5 S; D' A1 i1 i; XRSH+H古RH+ H2S' }8 K37 NO D7 I1.1.2 脱氮含氮化合物对产品质量的稳定性有较大危害,并且在燃烧时会排放出NOX 污染环境。
石油产品中的含氮化合物主要是杂环化合物,非杂环化合物较少。
2 R" T! {O K2 a/ ]$ P: d! SR NH2 + H2 RH + NH3% V A- _. a- x' O1.1.3 脱氧RCH2OOH + 2 H2 RH3 + 2H2O' C3、3 I7 ', i. A* }1.1.4 烯烃、芳烃的饱和; n7 \O y a) \$ U& u6 C1 R7 m9 M- z" nR/ CH=CH R R/ CH2¬&nOECH2R,x8 r0 W4 ~! B7 d- _! M3 p7 L: U8 H. O7 M4 u1.2 工艺流程说明1.2.1 反应部分直馏航煤自原料罐区及常压装置来经原料油过滤器( 1001 —SR- 101A/B)原料油脱水器(1001 —D—104)进入原料缓冲罐(1001 —D—101 )。
经加氢进料泵(1001 —P—101A/B ) 升压至约 2.7Mpa 与氢气混合,然后经反应流出物/反应进料换热器( 1001—E—101A/B/C/D) 壳程,换热后进入加热炉( 1 001 —F—1 01 )加热至反应所需的温度进入反应器( 1001—R—1 01 ) 。
混氢原料在催化剂的作用下进行加氢反应,反应产物与反应进料换热后经空冷器(1001—A —101)冷却到50C,进入低压分离器(1001 —D—102)分离出大部分的生成油进入分馏部分,低分顶部出来的循环氢与装置外来新氢混合经循环氢分液罐( 1001 —D—103)脱液经循环氢压缩机 ( 1001 —K—101A/B )增压后与原料混合进入反应系统。
6 m o6 U0 p) m$ c+ A# d1.2.2 分馏部分W8 I. i g" Y- A( v3 C' I自反应系统来的生成油经精制航煤/低分油换热器 (1002—E—201A/B/C/D )壳程与精制航煤换热进入分馏塔(1002 —C—201 )第25层塔盘。
塔顶油气经空冷器(1002 —A—201)与分馏塔顶后冷器(1002 —E—202)冷凝后入分馏塔顶回流罐(1002 — D —201)分出气/液两相。
气相与柴油加氢精制装置塔顶气体合并后,送去轻烃回收装置;液相分出污水后经分馏塔顶回流泵(1002 —P —201A/B)提高压力后一部分作为塔顶回流,控制塔顶温度。
一部分与柴油加氢精制装置石脑油合并送出装置作重整进料。
塔底油一路经分馏塔底重沸器(1002 —E—204)壳程,与柴油加氢装置来的精制柴油换热后返回塔底,另一路经精制航煤泵 ( 1002 —P—202A/B ) 升压后经精制航煤/低分油换热器与低分油换热,经空冷( 1002 —A—202)和后冷器(1002—E—203)冷却至40 C后配入一定比例的抗氧剂经精制航煤过滤器( 1002 —SR- 201A/B ) 和精制航煤脱水器(1002 — D —204)作为产品送出装置去罐区。
也可混入精柴出装置。
航煤出装置前需要在线加入抗氧化剂。
装置内设抗氧剂配制罐( 1002-D-202)、抗氧剂中间罐(1002-D-203)和抗氧剂计量泵(1002-P-203A/B )。
有关抗氧化剂的配制设备需放置在避风避雨场所。
抗氧化剂母液配制浓度10g/L,抗氧剂配制罐(1002-D-202)每罐加抗氧剂25Kg。
& \! [8 @9 T# Q6 ~! {) o' u1.2.3 催化剂活化流程+ m% X' W6 G: C- r- t& l为了提高催化剂活性,新鲜的或再生后的催化剂在使用前都必须进行活化。
设计采用液相活化方法,以直馏煤油为活化油。
催化剂进行活化时,系统内氢气经循环氢压缩机按正常操作路线进行循环,活化油经原料泵升压进入反应系统,按催化剂活化升温曲线的要求,控制反应升温速度至催化剂活化结束。
催化剂活化结束后,活化油通过不合格油线退出装置。
1.2.4 公用工程部分工艺流程(1)净化风和非净化风系统$ ]/ A( o' [7 z0 a" |0 . 7 MPa的净化压缩空气自净化风供风系统来,进入净化压缩空气罐(903 —D- 307)稳压后至气动阀及各仪表用点。
非净化风自装置外来进入装置后引至各软管站。
(2)新鲜水系统* C/ E! k3 ]1 i7 C. x新鲜水自新鲜水管网来进入装置各用水点。
(3)循环水系统’K- Y% s R* l& L3 A循环冷水自循环水供水系统来,并联进入装置各冷却水用点,换热后的循环热水再汇成一路出装置。
(4)I.OMPa蒸汽系统I.OMPa蒸汽系统自管网来至各用汽点、吹扫点、加热器。
:J' _5 t- O+ k1 A2 T(5)燃料气系统 6 b6 k. B' }* X {% 1( A: a8 f燃料气自装置外系统来部分至加热炉作燃料气,另一部分至( 1001 —D—101)作保护气。
(6)氮气系统 1 Y% 1+ C) g) w低压氮气(0.85MPa)由系统进入装置各用氮点。
高压氮气(2.5MPa)进入装置各用氮点。
1 M2 ~6 GO [5 @2 m0 @3 o6 K( g- B9 K# I. a% ?. ?4 v6 T1.3物料平衡原料产品性质1.3.1 物料平衡见表1.3-1表 1.3-1* e. L# B! H7 j+ k$ W t物料平衡w% 初期末期入方:原料油100.000 100.000H2 (化学耗氢) 0.067 0.0652 B$ i. U6 c s5 F1 P小计100.067 100.065出方: 4 \# p7 X G& JH2S 0.046 0.044航煤馏分100.021 100.021小计100.067 100.065( Y' y) G" y:门;B1.3.2 原料、产品性质及主要技术规格 5 f) c6 N8 O+ \) B, n6 y3 a1 L(1)原料)t2 A. ]5 i. b5 H* s" _①原料油该装置原料油为直馏航煤,其边界条件如下:+ w# '( j8 M* c' M$ R进装置温度:常压蒸馏装置直供原料时为50 C罐区供原料时为40 C进装置压力:0.6 MPa(G)性质见表1.3-2表 1.3-20 G: G5 J+ \2 i2 J$ _项目直馏航煤密度kg/m3 775 〜8303 C8 c3 W- F! 1+ A4 @1 y! ~- 15 R" o硫,g/g 1450; o: J. F2 11 Z( o1 \硫醇性硫,g/g 105$ s# _4 e. | q" j; t; H冰点,C 匕50倾点,C -60烟点,mm 31馏程(ASTM D86), C 8 [# A* Q# P+ E v3 w( U2% /5% 133166# D1 t# U8 r) f9 A4 {10%/30% 177/191)乙t' d7 m$ z50%/70% 202/21490%/95% 232/241$ F6 o3 J0 }! z5 V, t98% 252②新氢该装置所用新氢由重整装置提供,其边界条件如下:进装置温度:40 C进装置压力: 2.0MPa(G), D3 H; }+ X7 Q v6 p组成见表1.3-3组成见表1.3-3组成H2 C1 C2 C3 iC4 nC4 iC5 C6+V% 91.35 2.67 2.71 2.18 0.47 0.35 0.11 0.16; N a$ A% n, \5 {# ~8 F9 V(2)产品规格! R$ U# I0 L/ 15 G& | B# p①石脑油 1 0% V2 x! '& ~4 \4 F/ {' y该装置产生的少量石脑油与柴油加氢精制装置产生的石脑油汇合后送至重整装置。
②航煤)T, _% T! {9 s5 W& F, _该装置主要产品为优质3号喷气燃料,其质量满足GB6537-94要求,预期产品性质见,?! D' 05 P" b/ n3 E0 a表 1.3-4表 1.3-43 t8 L0 S( r, Y7 p3 C控制项目单位控制指标颜色(赛氏比色) 号透明无溶解水及悬浮物,R; X. Z" R5 o* Z& i: 0* L8 g总酸值mgKOH/g w 0.0152 D; '% @% F: U芳烃含量%(V/V)w 20烯烃含量%(V/V)w 5.0. r) B! t Z! {+ '总硫含量%(m/m)w 0.20硫醇性硫%(m/m)通过.c- k8 ?- e0 A或博士试验通过/ B' q & |; G y8 g4 M+ U10%回收温度C W0550%回收温度C W32终馏点 C <300残留量%(V/V)< 1.5' x0 h. W u+ p; L' {水反应界面情况级<1 b! _& X* L( |" t( [% H3 @电导率(20 C)pS/m50 〜450实际胶质mg/100ml< 7* J# y2 T: }6 v闪点C為8' f% E$ y# X6 i, u密度(20 C)kg/m3775〜830冰点C<47粘度,20 C mm2/s昌.25粘度,-20 C mm2/s<8# D! h) W$ K# S0 {9 O; j: g 净热值MJ/kg> 42.8烟点mm >25或烟点最小为20mm时,萘烃含量%(V/V) > 3.0铜片腐蚀银片腐蚀热安定性(100 C, 2h)(50 C, 4h)(260C, 2.5h),压力降<1 ; p7 x" B0 g( t<1KPa < 3.3+ Y7 H# I) @# I管壁评级<3,且无孔雀蓝色或异常沉淀物.c; G' A0 N1 w) 1+ H/ _9 nMg/l 报告序0 T; \" S+ X- F% d4 N5 x b$ O号项年消耗量能耗指标能耗+ {) g; A+ e0 h7 ?)':V7 r1 ?单位数量单位系数MJ/1循环水万吨45.70千焦/吨 6.38191.473电万度233.5千焦/度11.84 2765.77! |"}4 '(E K8 u4燃料气万吨78.96千焦/吨39.4643115.845氮气万标米3 2.6千焦/标米3 6.2816.356净化风万标米375.60 千焦/标米3 1.59120.2d* [,U) s5 R7蒸汽(1.0MPa) 万吨0.17千焦/吨3182534.58 8凝结水万吨-0.17千焦/吨320.3-53.18能耗合计422.29. }9 A$ [3 k- y9 N4 Z! A单位能耗10.09X104kcal/t' s# }( p8h",g/ D+ ]. y* }5 {9 K$ j2 T' a* j" R5 D# C {3 y4 a) \,固体颗粒污染物含量3 k' f7 z H, Q'K C3 | H3 \, d8 i1.4 能耗指标$ v; @" H: @) _, A7 d* i7 V 能耗指标及计算表/ d/ d# |) V: L) V6 T4 H, |.H% w7 Q9 h) U/ F1.5装置设计的主要操作条件1.5.1 反应温度加氢反应的温度是根据催化剂和油品的性质决定的,提高反应温度会加快加氢精制的反应速度,生成油的含硫及含氮量会降低,只要能达到所要求的加氢深度,反应温度就不要再提因为反应温度过高裂解反应加快,精制油的溴价反而上升,气体产率增加,温度过高对催化剂寿命及设备都有不利的影响,所以必须根据原料油的性质和产品的要求等条件来确定适宜的反应温度。