保护渣和精炼渣资料(东北大学)
结晶器保护渣

目录
1.保护渣的冶金功能 5.保护渣对铸坯质量的影响
2.保护渣的基本特性
6.保护渣的选择和使用
3.保护渣的类型
7.保护渣的性能评价
4.保护渣和连铸浇注条件之间的关系
保 护 渣 作 用 机 理
保护渣在结晶器中的行为:
加入保护渣
钢水提供热量
形成三层结构
保护渣的铺展性
保 护 渣 作 用 机 理
保护渣使用过程中需要测定的参数:
6
. 保 护 渣 的 选 择 和 使 用 1. 2. 3. 4. 5. 6. 7. 8. 9. 測結晶器中總熱流值 結晶器銅板溫度變化與其位置和時間的關係 保護渣消耗量與澆鑄拉速的關係 保護渣在彎月面區的積聚(渣圈問題) 檢測鑄胚在彎月面的振痕 結晶器和鑄胚間的摩擦力和拉速的關係 鑄胚表面溫度在長度和寬度的變化 裂紋的類型,頻率和嚴重性 可見氧化物缺陷的頻率
不大于350x10-3N/m
弯月面曲率半 界面特性 径
吸收夹杂物能 力 吸收夹杂后性能稳 定 夹渣
保护渣种类
优点
缺点 铺展性差、污 染环境、易吸 水
应用
粉状保护渣
3 . 保 护 渣 的 类 型
颗粒保护渣 预熔型保护渣 发热型保护渣 高速连铸保护 渣 表面无缺陷铸 坯保护渣 特殊钢连铸保 护渣 无氟保护渣 流动性强、成 分均匀,耗量 少 成渣均匀性好 形成液渣快 满足高速连铸 能减少铸坯表 面缺陷 减少钢液增碳 减少水污染、 降低铸坯夹杂
含氟量的选择:
6
. 保 护 渣 的 选 择 和 使 用 连铸结晶器保护渣中一般是依赖氟化物来调 节熔点、黏度。 a、浇注过程中保护渣中的氟化物大约有20%~30%溶 入二冷水中,造成水污染,如果循环使用会腐 蚀铸机,降低铸机寿命。 b、污染环境,对人体有害; c、F-是侵蚀浸入式水口的主要成分。 一般来说F-含量要控制在10%以下,不得 大于15%,如果是采用低氟或者无氟保护渣, 二冷水的成本可节约90%,而且由于减轻了铸 机的腐蚀,使得设备维修成本降低,喷嘴寿命 延长。
第四章 精炼渣系选择

钢中的酸溶铝[Al]S不会还原渣中的(SiO2),这时(SiO2)不会成为供氧源。
钢铁冶金研究所&特殊钢冶金学术方向
各精炼渣系脱硫能力的比较
LF炉精炼过程的脱硫的热力学参数主要有钢水中的溶解氧 含量和渣中的 CaO 活度(即作用浓度)。脱硫的表达式为: (CaO) +[S] = (CaS) + [O]
<0.1 -
♣ 几个主要结构单元的作用浓度
结构单元 作用浓度 A B 山 阳 东北大学 CaO N1 0.1641 0.2348 0.3676 0.3495 SiO2 N2 0.0005 0.0005 0.0002 0.0001 Al2O3 N3 0.0102 0.0097 0.0084 0.0238 MgO N4 0.2162 0.1145 0.0468 0.0598 MgO· Al2O3 N10 - - - 0.0598
钢铁冶金研究所&特殊钢冶金学术方向
精炼渣系选择的实验
小盖 炉盖 发热体 炉管 耐火砖 精炼渣 石墨坩埚 MgO坩埚 钢水
实验渣系及结果
实验号 1# 2# 3# 4# 5# 6# 7# 8# CaO 45~50 54~57 50~60 50~55 45~50 55~60 45~50 50~55 SiO2 20~25 10~15 13~17 10~15 20~25 13~15 20~25 5~10 Al2O3 24~27 24~27 10~15 13~17 13~17 13~17 25~30 25~33 MgO 3~7 3~7 2~6 8~12 8~12 3~8 3~7 5~10 CaF2 0 0 0 5~10 3~8 5~10 0 0 R=(CaO/SiO2) 2 4 4 4.2 2.2 4.5 2 >5 T.O 0.002 0.0013 0.0016 0.0015 0.002 0.0011 0.0015 0.0011
保护渣简介

保护渣简介保护渣的性能测定一、保护渣的作用1)绝热保温向结晶器液面加固体保护渣覆盖其表面,减少钢液热损失。
由于保护渣的三层结构,钢液通过保护渣的散热量,比裸露状态的散热量要小10倍左右,从而避免了钢液面的冷凝结壳。
尤其是浸入式水口外壁四周覆盖了一层渣膜,减少了相应位置冷钢的聚集。
2)隔绝空气,防止钢液的二次氧化保护渣均匀地覆盖在结晶器钢液表面,阻止了空气与钢液的直接接触,再加上保护渣中碳粉的氧化产物和碳酸盐受热分解溢出的气体,可驱赶弯月面处的空气,有效地避免了钢液的二次氧化。
3)吸收非金属夹杂物,净化钢液加入的保护渣在钢液面上形成一层液渣,具有良好的吸附和溶解从钢液中上浮的夹杂物,达到清洁钢液作用。
4)在铸坯凝固坯壳与结晶器内壁间形成润滑渣膜在结晶器的弯月面处有保护渣的液渣存在,由于结晶器的振动和结晶器壁与坯壳间气隙的毛细管作用。
将液渣吸入,并填充于气隙之中,形成渣膜。
在正常情况下,与坯壳接触的一侧,由于温度高,渣膜仍保持足够的流动性,在结晶器壁与坯壳之间起着良好的润滑作用,防止了铸坯与结晶器壁的粘结;减少了拉坯阻力;渣膜厚度一般在50~200μm5)改善了结晶器与坯壳间的传热在结晶器内,由于钢液凝固形成的凝固收缩,铸坯凝固壳脱离结晶器壁产生了气隙,使热阻增加,影响铸坯的散热。
保护渣的液渣均匀的充满气隙,减小了气隙的热阻。
据实测,气隙中充满空气时导热系数仅为0.09W/m·K,而充满渣膜时的导热系数为1.2W/m·K,由此可见,渣膜的导热系数是充满空气时的13倍。
由于气隙充满渣膜,明显地改善了结晶器的传热,使坯壳得以均匀生长。
二、保护渣的构成1)液渣层当固体粉状或粒状保护渣加入结晶器后与钢液面相接触,由于保护渣的熔点只有1050℃~1100℃,因而靠钢液提供的热量使部分保护渣熔化,形成液熔化速度主要靠保护渣中配入的碳成分来调节。
炭质材料与保护渣基料间的界面张力较大,基料熔化后,对炭质材料不润湿,不吸收。
熔渣

电渣重熔渣 铜闪速炉熔炼渣
0~10 28~38
0~30 2~12
0~20 5~15
38~54
0~15 1~3
铅鼓风炉熔炼渣 19~35 3~5 0~20 28~40 3~5
CaF2 45
Fe3O4 1
S 0.2~0 Pb 1~3
锡反射炉熔炼渣 19~24 8~10 1.5~6 45~50
Sn 7~9
高钛渣
2.8~5.6
2~6
0.3~1.2 2.7~6.5 2~5.6
1~1.5
TiO2 82~
4
§ 一、 基本概念 1
Molten Slag
通常由五、六种或更多的氧化物组成。
熔
含量最多的氧化物通常只有三种,其总含量可达80%
渣 以上。
理
多数有色冶金炉渣和钢渣的主要氧化物是:
论
CaO、SiO2 、FeO
型
➢ 造锍熔炼:铜、镍的硫化物与炉料中铁的的硫化物熔融在 一起,形成熔锍;铁的氧化物则与造渣熔剂SiO2及其他脉
石成分形成熔渣。
7
§ 一、 基本概念 1 2、精炼渣
Molten Slag
✓ 是粗金属精炼过程的产物。
熔
✓ 主要作用——捕集粗金属中杂质元素的氧化产物,使之与主
渣
金属分离。
理
➢ 例如,炼钢时,加入的造渣熔剂,与原料中杂质元素的氧化 产物融合成炉渣,除硫、磷,吸收非金属夹杂。
及 模
高炉渣和某些有色冶金炉渣的主要氧化物为: CaO、SiO2 、Al2O3
型
常含有其他化合物,如氟化物、硫化物等。
5
§ 一、 基本概念
1
熔渣主要来源:
Molten Slag
保护渣的物化性能

关键词 保护渣的性能, 摩擦力 , 润滑 中图分类号 T77 文献标识码 B F7
If ec o mo f x pre o h f t n poet s te c o n une l l l f d r u i n r i i
b t en a d d od ew e s n a m l t r n
熔渣的赫度, 通过旋转赫度计已测得
保护渣的赫度一温度曲线; 存在液态渣膜的区域, 由渣膜分布状 态界定;
. 、. _ __.
S— ,
函,
_已 过 算 膜 动 度 布 到 a通计渣流速分得。 x y
固体摩擦力 对于固态渣膜润滑区, 铸坯与结晶器间的固体 摩擦力由库仑定律计算得到, 具体表达式见式 2 0
钢铁行业全球化竞争和兼并的日 益加剧使得钢 铁行业投资趋向于产品质量、 生产效率和环保等三
个方面〔。 ’ 为此, ] 以高拉速、 高连浇率、 高作业率、
及高质量为特征的高效连铸成为钢铁企业在激烈的 世界钢铁市场竞争中立于不败之地的必然需要。 高速连铸过程中, 由于结晶器振频的提高, 单位 时间流人结晶器与铸坯间保护渣量相应减少, 结晶 器与铸坯间保护渣渣膜的均匀性及稳定性下降, 使 铸坯与结晶器之间的摩擦力增大, 茹结性拉漏事故
r = '寸 . J d L 1 s 1
S , ac
l05
0
10 15 10 1 0 1 0 2 0 1 5 1 0 1 5 2 0 3 0 3 0
_
, a ,_ v .
凝固大摩擦力关系图
保
护
渣 导致铸坯与结晶器间的摩擦增大。
素有关。这些因素包括与材料有关的热物理准数、 热传递准数、 机械性能准数及接触点宏观和微观几 何准数等。在计算铸坯与结晶器间的摩擦力时, 人
保护渣
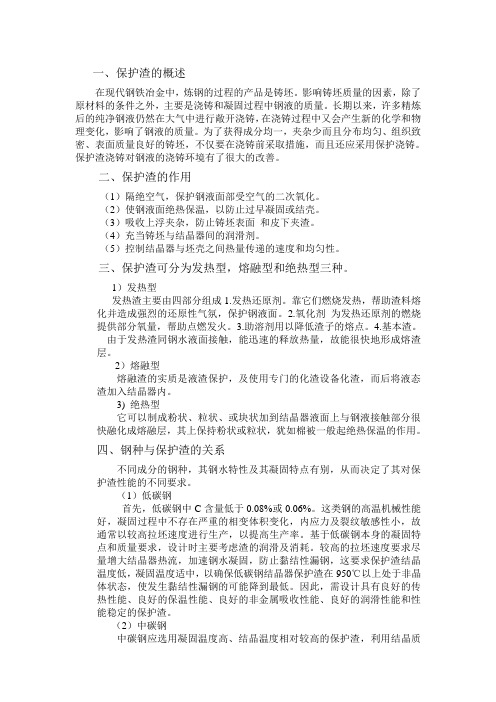
一、保护渣的概述在现代钢铁冶金中,炼钢的过程的产品是铸坯。
影响铸坯质量的因素,除了原材料的条件之外,主要是浇铸和凝固过程中钢液的质量。
长期以来,许多精炼后的纯净钢液仍然在大气中进行敞开浇铸,在浇铸过程中又会产生新的化学和物理变化,影响了钢液的质量。
为了获得成分均一,夹杂少而且分布均匀、组织致密、表面质量良好的铸坯,不仅要在浇铸前采取措施,而且还应采用保护浇铸。
保护渣浇铸对钢液的浇铸环境有了很大的改善。
二、保护渣的作用(1)隔绝空气,保护钢液面部受空气的二次氧化。
(2)使钢液面绝热保温,以防止过早凝固或结壳。
(3)吸收上浮夹杂,防止铸坯表面和皮下夹渣。
(4)充当铸坯与结晶器间的润滑剂。
(5)控制结晶器与坯壳之间热量传递的速度和均匀性。
三、保护渣可分为发热型,熔融型和绝热型三种。
1)发热型发热渣主要由四部分组成1.发热还原剂。
靠它们燃烧发热,帮助渣料熔化并造成强烈的还原性气氛,保护钢液面。
2.氧化剂为发热还原剂的燃烧提供部分氧量,帮助点燃发火。
3.助溶剂用以降低渣子的熔点。
4.基本渣。
由于发热渣同钢水液面接触,能迅速的释放热量,故能很快地形成熔渣层。
2)熔融型熔融渣的实质是液渣保护,及使用专门的化渣设备化渣,而后将液态渣加入结晶器内。
3) 绝热型它可以制成粉状、粒状、或块状加到结晶器液面上与钢液接触部分很快融化成熔融层,其上保持粉状或粒状,犹如棉被一般起绝热保温的作用。
四、钢种与保护渣的关系不同成分的钢种,其钢水特性及其凝固特点有别,从而决定了其对保护渣性能的不同要求。
(1)低碳钢首先,低碳钢中C含量低于0.08%或0.06%。
这类钢的高温机械性能好,凝固过程中不存在严重的相变体积变化,内应力及裂纹敏感性小,故通常以较高拉坯速度进行生产,以提高生产率。
基于低碳钢本身的凝固特点和质量要求,设计时主要考虑渣的润滑及消耗。
较高的拉坯速度要求尽量增大结晶器热流,加速钢水凝固,防止黏结性漏钢,这要求保护渣结晶温度低,凝固温度适中,以确保低碳钢结晶器保护渣在950℃以上处于非晶体状态,使发生黏结性漏钢的可能降到最低。
保护渣相关知识

浇注过程中覆盖在钢锭模或结晶器内钢液面上稳定浇注操作和改善钢表面质量的一种合成渣。
保护渣按使用范围可分为模注保护渣和连铸保护渣。
浇注过程钢表面产生的缺陷如重皮、翻皮、夹渣、裂纹等,往往都与保护渣性能及操作有关。
渣保护浇注是钢浇注中最常用、最有效的一种工艺。
保护渣在浇注过程中的功能有:(1)防止钢水再氧化;(2)减少钢液面的热损失,防止钢液面过早凝固结壳;(3)溶解吸收钢水表面的夹杂;(4)控制钢坯的传热速度,减少钢坯凝固层厚度方向上的温度梯度产生的热应力;(5)在结晶器与坯壳之间起润滑作用。
对模注保护渣来说主要是前3种功能,而连铸保护渣则具有所有的功能。
模注保护渣可分为上注保护渣和下注保护渣,按其性能有绝热型与吸收型两种。
模注保护渣与连铸保护渣按原料及制备方法不同,有以发电厂飞灰或石墨矿粉等为基的粉状保护渣,合成保护渣,预烧结、预熔保护渣与颗粒保护渣。
使用最广泛的是合成的粉状保护渣和颗粒保护渣。
保护渣的成分通常是以二氧化硅一氧化钙三氧化二铝为基,添加适量的碱土氧化物(如Na2O、Li2O、K2O等)、氟化物(如CaF2、NaF等)及碳质材料(如石墨、焦炭、石油焦及碳化合物等)。
保护渣的主要理化性能有:熔融温度、熔融速度、黏度、表面张力、结晶温度等。
在使用过程中还要求其具有铺展性、保温性、吸收夹杂物的能力,以及化学反应性等。
这些性能与保护渣的原料和熔剂的种类、配比及粉体特性有关。
常用熔剂有苏打、冰晶石、硼砂及氟化物等。
它们均能有效降低熔融温度,加快熔融速度,得到适宜的黏度。
碳是保护渣中不可缺少的材料,它有效调节熔化速度,改善烧结倾向,提高粉渣的保温性能,控制熔渣的氧化性。
当浇注时,模注保护渣以袋装或吊挂方式加入钢锭模内,其加入方法如图。
模注保护渣一旦与钢水接触,立即被加热、熔融、烧结。
在钢液面上形成三层结构,在靠近钢液面上为熔融层,熔融层上为烧结层,最上面是粉状层。
粉状层起着隔热保温作用,熔融层可以减少从大气中吸收氧、氢、氮等气体,溶解吸收夹杂物,渗入到钢锭模与凝固层缝隙中形成渣膜,有效改善传热及表面质量。
连铸保护渣概述
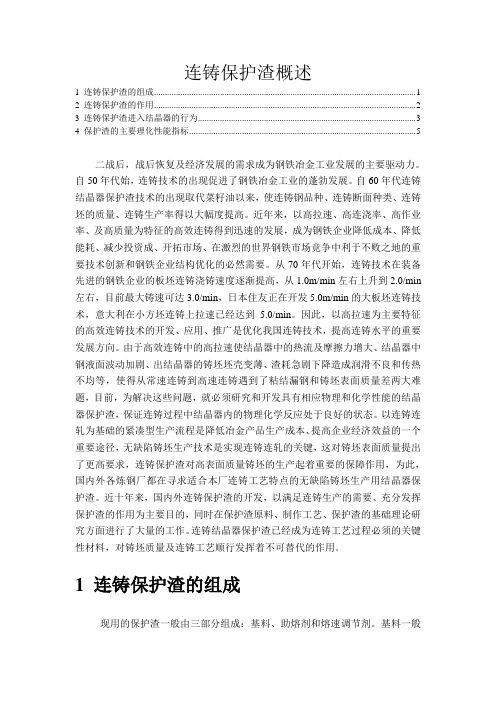
连铸保护渣概述1 连铸保护渣的组成 (1)2 连铸保护渣的作用 (2)3 连铸保护渣进入结晶器的行为 (3)4 保护渣的主要理化性能指标 (5)二战后,战后恢复及经济发展的需求成为钢铁冶金工业发展的主要驱动力。
自50年代始,连铸技术的出现促进了钢铁冶金工业的蓬勃发展。
自60年代连铸结晶器保护渣技术的出现取代菜籽油以来,使连铸钢品种、连铸断面种类、连铸坯的质量、连铸生产率得以大幅度提高。
近年来,以高拉速、高连浇率、高作业率、及高质量为特征的高效连铸得到迅速的发展,成为钢铁企业降低成本、降低能耗、减少投资成、开拓市场、在激烈的世界钢铁市场竞争中利于不败之地的重要技术创新和钢铁企业结构优化的必然需要。
从70年代开始,连铸技术在装备先进的钢铁企业的板坯连铸浇铸速度逐渐提高,从1.0m/min左右上升到2.0/min 左右,目前最大铸速可达3.0/min,日本住友正在开发5.0m/min的大板坯连铸技术,意大利在小方坯连铸上拉速已经达到 5.0/min。
因此,以高拉速为主要特征的高效连铸技术的开发、应用、推广是优化我国连铸技术,提高连铸水平的重要发展方向。
由于高效连铸中的高拉速使结晶器中的热流及摩擦力增大、结晶器中钢液面波动加剧、出结晶器的铸坯坯壳变薄、渣耗急剧下降造成润滑不良和传热不均等,使得从常速连铸到高速连铸遇到了粘结漏钢和铸坯表面质量差两大难题,目前,为解决这些问题,就必须研究和开发具有相应物理和化学性能的结晶器保护渣,保证连铸过程中结晶器内的物理化学反应处于良好的状态。
以连铸连轧为基础的紧凑型生产流程是降低冶金产品生产成本、提高企业经济效益的一个重要途径,无缺陷铸坯生产技术是实现连铸连轧的关键,这对铸坯表面质量提出了更高要求,连铸保护渣对高表面质量铸坯的生产起着重要的保障作用,为此,国内外各炼钢厂都在寻求适合本厂连铸工艺特点的无缺陷铸坯生产用结晶器保护渣。
近十年来,国内外连铸保护渣的开发,以满足连铸生产的需要、充分发挥保护渣的作用为主要目的,同时在保护渣原料、制作工艺、保护渣的基础理论研究方面进行了大量的工作。
- 1、下载文档前请自行甄别文档内容的完整性,平台不提供额外的编辑、内容补充、找答案等附加服务。
- 2、"仅部分预览"的文档,不可在线预览部分如存在完整性等问题,可反馈申请退款(可完整预览的文档不适用该条件!)。
- 3、如文档侵犯您的权益,请联系客服反馈,我们会尽快为您处理(人工客服工作时间:9:00-18:30)。
-4-
1.1.1 高碱度渣精炼 在研究钢液二次精炼的脱硫、脱磷的处理方法时,提高了高纯度钢的精炼效果。这 时所使用的工业熔剂是 CaO 系,由于钢液用铝脱氧,实际上生成了 CaO—Al2O3 渣系。 近年来,LF 法率先使用这种炉渣精炼高纯度钢。CaO—Al2O3 系熔渣在还原气氛下使 用,首先考虑脱硫反应,测定了 CaO—Al2O3 中溶解耐火材料的 CaO—Al2O3--MgO 和 混入炼钢炉渣的 CaO—Al2O3—SiO2 系熔渣的硫容量。实验用渣系的成份及其硫含量见 表 1.。 表 1 CaO—Al2O3 渣系的试验结果 熔炼 炉次
55-Cl 55-1 55-4 60-Cl 60-2 60-4 65-Cl 65-2 65-3
温度 /K
1823 1822 1823 1867 1867 1867 1928 1922 1922
接触气体的分压(室温) /Pa Pco Pco2 Pso2 PAr
0.250 5 ×10 0.248 5 ×10 0.167 5 ×10 0.251 5 ×10 0.249 5 ×10 0.166 5 ×10 0.168 5 ×10 0.249 5 ×10 0.250 5 ×10 0.249 5 ×10 0.247 5 ×10 0.166 5 ×10 0.250 5 ×10 0.248 5 ×10 0.166 5 ×10 0.167 5 ×10 0.248 5 ×10 0.249 5 ×10 0.010 5 ×10 0.010 5 ×10 0.013 5 ×10 0.010 5 ×10 0.010 5 ×10 0.013 5 ×10 0.013 5 ×10 0.010 5 ×10 0.010 5 ×10 0.489 5 ×10 0.485 5 ×10 0.652 5 ×10 0.490 5 ×10 0.485 5 ×10 0.652 5 ×10 0.658 5 ×10 0.488 5 ×10 0.490 5 ×10
MgO
0.14 0.04 0.04 0.02 0.03 0.02
S
0.526 0.365 0.019 0.426 0.107 0.019 0.326
0.05 1.49
0.076 0.033
对于 CaO--Al2O3--SiO2 渣系而言,NCaO/Nsio2 一定时,NAl2O3 减少,硫容量 Cs 都呈单 调增加,当 NAl O 一定时,NCaO/Nsio2 减小,即 CaO--Al2O3 渣中的 CaO 用 SiO2 置换,则硫
LF 炉精炼渣对 GCr15 非金属夹杂物影响的研究 .................................... 13 LF 炉精炼渣的冶金特性研究 ................................................................ 14 精炼渣的脱硫特性 ............................................................................ 14 精炼渣的脱氧特性 ............................................................................ 15 精炼渣碱度对脱氧和脱硫的影响 ................................................... 18 LF 精炼合成渣的研究及精炼工艺的优化 ........................................... 19 精炼合成渣的成份选择 .................................................................... 20 精炼合成渣的配制 ............................................................................ 26 1.1.2 LF 炉精炼工艺的优化 ............................................................. 29 1.2 高碱度精炼渣冶炼轴承钢中夹杂物的研究 .................................. 31 1.2.1 研究方法的确定 ...................................................................... 31 1.2.2 显微夹杂物的数量和尺寸 ..................................................... 32 1.2.3 显微夹杂物的类型 .................................................................. 33 1.2.4 精炼炉渣对轴承钢中夹杂物的影响 ..................................... 36 2 洁净钢连铸工艺的研究............................................................................. 37 2.1.1 中间包覆盖剂 .......................................................................... 37 2.2 GCr15 大方坯结晶器保护渣的研究 ................................................. 38 2.2.1 保护渣的粘度对大方坯表面质量的影响 ............................ 38 2.2.2 保护渣熔化温度对大方坯表面质量的影响 ........................ 39 2.2.3 保护渣熔速对大方坯表面质量的影响................................. 40
2 3
容量 Cs 的减小倾向比 CaO—Al2O3—MgO 更加严重。 硫容量与温度有关,温度越高,硫容量越大。渣中 CaO 浓度越大,硫容量越大; 当 NAl O 一定时,CaO—Al2O3 渣中的 CaO 用 MgO 置换,硫容量减小。用 SiO2 置换 CaO,硫
2 3
容量更加减小;当 NCaO/ NAl O 时,混入 MgO 也不会减小 CaO--Al2O3 渣系的脱硫能力。然
炉渣成份(质量分数)/% CaO
58.17 .16 38.36 59.48 48.38 36.84 57.61 48.65 41.71
-lgCs
2.238 2.399 3.748 2.050 2.648 3.479 1.869 2.440 2.808
Al2O3
39.93 41.86 58.21 39.65 50.39 61.18 37.03 46.13 54.71
2 3 2
50 分钟,再经 RH 真空循环脱气处理 20—30 分钟。所以,含高 CaO 的精炼渣处理轴 承钢液,带来两个主要结果。一是脱硫效率高,钢中硫含量降到如此之低的程度; 二是在精炼过程中 CaO 被还原,钢中含钙量增加,至使不变形的球状夹杂物升高。 表 2 日本山阳 LF 炉精炼渣的化学成份(%) CaO 57.8 酸性渣处理 在改善夹杂物性质和形态方面,碱性炉衬下冶炼的钢液,经酸性渣处理能够得 到很好的效果。渣料的熔点不大于钢的熔点,密度也小于钢的密度,形成的渣实际 上不含有钙和镁,它们和钢中所有的夹杂发生作用,一部分夹杂上浮到钢液表面, 其余则转化为可塑性加工的夹杂物。 酸性合成渣料当 MnO 约 60%,SiO2 约 40%(质量比 MnO:SiO2=3:2)时,存在一个 低熔点区,这个低熔点区相当狭小,其成份范围相应为 MnO 约 45%--75%,SiO2 约为 55%--25%。如果除 MnO 和 SiO2 外还含有其它组元,如 Al2O3,则低熔点区可以扩大到含 MnO 约 10%—90%,SiO2 约 90%--10%(MnO:SiO2=1:9—9:1,特别适用的混合渣的成份 在图 1 的 A—B—C—D 点的范围内,这些点的三角座标上的位置为: A 点:MnO 60%,SiO2 10%,Al2O3 0%,相当于质量比 MnO :SiO2 :Al2O3 =9:1:0; B 点:MnO 50%,SiO2 10%,Al2O3 40%,相当于质量比 MnO :SiO2 :Al2O3 =5:1:4; C 点:MnO 10%,SiO2 50%,Al2O3 40%,相当于质量比 MnO :SiO2 :Al2O3 =1:5:4; SiO2 13.3 Al2O3 15.8 MgO 4.3 MnO < 0.1 TFe 0.6 Cr2O3 < 0.1 P2O5 < 0.1 CaF2 7.8 S 1.1
-3-
摘
要
开发出了轴承钢高碱度精炼渣,R=3.5—4.0;合理地运用了钢包吹氩技术,有效地 控制了钢内夹杂物;特别是在连铸工艺上自主开发了大容量中间包覆盖剂,达到了一定 的碱度,具有吸附夹杂物的能力。将上述技术组合以及无氧化保护技术的应用,达到了 100%无氧化浇钢。使轴承钢在浇钢过程中增氧在 2—3ppm 以下。 与国际发达国家相比,我国钢铁工业目前存在的主要差距为: 1)关键钢材的品种不足,质量水平不高。 2)技术经济水平不高。 3)污染严重资源综合利用率不高。 迎接二十一世纪世界钢铁工业新的挑战 具体特点如下: 1)调整企业结构,实现专业化生产 2)建立洁净钢生产体系,提高产品质量 精炼炉渣对轴承钢夹杂物的影响 在传统的炼钢方法中,有所谓酸性钢和碱性之分。二者的组织性能和可塑性都 不尽相同。瑞典 SKF 公司生产的轴承钢及其轴承以其质量优异而闻名于世,究其原 因在于生产方法。长期以来,SKF 公司采用酸性平炉生产轴承钢,一直延续到 70 年 代后期。由于酸性平炉不能去除硫、磷等杂质,对原材料要求极为苛刻,且生产效 率低、成本高,该公司从 60 年代中期就开始研究碱性电弧炉精炼工艺,开发出了 SKFMR 法,取代了酸性平炉工艺。 如何改变碱性炼钢生产效率低的特点,提高碱性钢的性能是国内外冶金者长期 努力的方向[57]。即:既降低钢中的氧含量,又要改善夹杂物的性质和形态。因 此,轴承钢的炉外精炼承担着完成两项任务的使命:一是要减少夹杂物的数量,特 别是减少氧化物夹杂物的数量;二是改善夹杂物的形态和性质(提高塑性夹杂物的 比例,最大限度地减少或消除 CaO 型的球状夹杂物)。降低氧化物夹杂的数量也就 是降低了钢中的氧含量,改善夹杂物的性质和形态主要取决于精炼渣的化学成份。 国内外的生产实践证实,各种炉外精炼方法(真空的或非真空的)加强了对钢液的 搅拌,就能够有效地将氧含量降到很低的程度。这里,氧化物夹杂的数量主要是指 Al2O3 夹杂的数量大大减少。然而要有效降低 A 类夹杂物和 D 类夹杂物的数量则主要 依赖于精炼渣的化学成份。