高硬涂层及金刚石涂层介绍
刀具涂层技术介绍
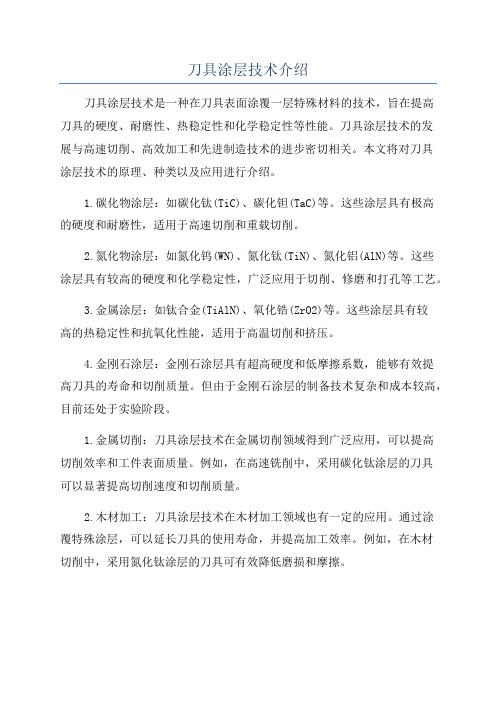
刀具涂层技术介绍刀具涂层技术是一种在刀具表面涂覆一层特殊材料的技术,旨在提高刀具的硬度、耐磨性、热稳定性和化学稳定性等性能。
刀具涂层技术的发展与高速切削、高效加工和先进制造技术的进步密切相关。
本文将对刀具涂层技术的原理、种类以及应用进行介绍。
1.碳化物涂层:如碳化钛(TiC)、碳化钽(TaC)等。
这些涂层具有极高的硬度和耐磨性,适用于高速切削和重载切削。
2.氮化物涂层:如氮化钨(WN)、氮化钛(TiN)、氮化铝(AlN)等。
这些涂层具有较高的硬度和化学稳定性,广泛应用于切削、修磨和打孔等工艺。
3.金属涂层:如钛合金(TiAlN)、氧化锆(ZrO2)等。
这些涂层具有较高的热稳定性和抗氧化性能,适用于高温切削和挤压。
4.金刚石涂层:金刚石涂层具有超高硬度和低摩擦系数,能够有效提高刀具的寿命和切削质量。
但由于金刚石涂层的制备技术复杂和成本较高,目前还处于实验阶段。
1.金属切削:刀具涂层技术在金属切削领域得到广泛应用,可以提高切削效率和工件表面质量。
例如,在高速铣削中,采用碳化钛涂层的刀具可以显著提高切削速度和切削质量。
2.木材加工:刀具涂层技术在木材加工领域也有一定的应用。
通过涂覆特殊涂层,可以延长刀具的使用寿命,并提高加工效率。
例如,在木材切削中,采用氮化钛涂层的刀具可有效降低磨损和摩擦。
3.非金属材料加工:刀具涂层技术在陶瓷、塑料、复合材料等非金属材料加工领域也得到了广泛应用。
通过涂层技术,可以改善切削表面的光洁度,并提高工件的精度和质量。
4.汽车零部件加工:在汽车零部件加工领域,刀具涂层技术可以有效提高零部件的加工精度和耐用性,适用于发动机气门、曲轴、轴承等零部件的加工。
刀具涂层技术的发展为现代制造业带来了巨大的效益。
随着材料科学、纳米技术和涂层技术的进一步发展,刀具涂层技术的性能和应用范围将会不断扩大。
预计未来刀具涂层技术将更加智能化和环保化,能够实现刀具表面的自动修复和自动调节。
这将进一步提高切削效率和加工质量,推动现代制造业的发展。
聚晶金刚石涂层的元素含量
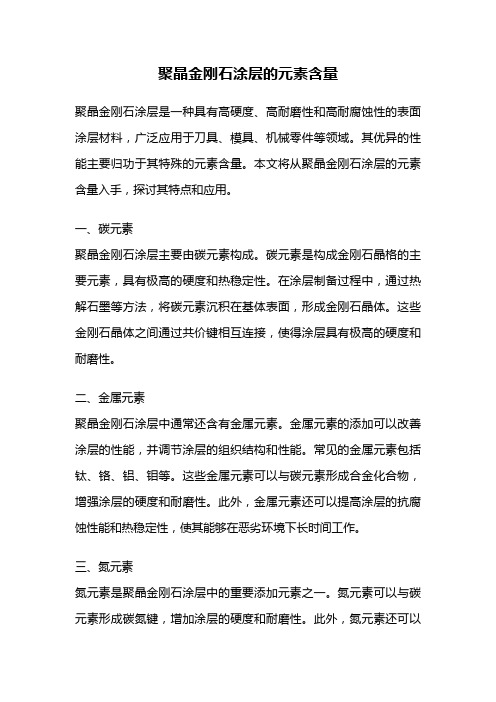
聚晶金刚石涂层的元素含量聚晶金刚石涂层是一种具有高硬度、高耐磨性和高耐腐蚀性的表面涂层材料,广泛应用于刀具、模具、机械零件等领域。
其优异的性能主要归功于其特殊的元素含量。
本文将从聚晶金刚石涂层的元素含量入手,探讨其特点和应用。
一、碳元素聚晶金刚石涂层主要由碳元素构成。
碳元素是构成金刚石晶格的主要元素,具有极高的硬度和热稳定性。
在涂层制备过程中,通过热解石墨等方法,将碳元素沉积在基体表面,形成金刚石晶体。
这些金刚石晶体之间通过共价键相互连接,使得涂层具有极高的硬度和耐磨性。
二、金属元素聚晶金刚石涂层中通常还含有金属元素。
金属元素的添加可以改善涂层的性能,并调节涂层的组织结构和性能。
常见的金属元素包括钛、铬、铝、钼等。
这些金属元素可以与碳元素形成合金化合物,增强涂层的硬度和耐磨性。
此外,金属元素还可以提高涂层的抗腐蚀性能和热稳定性,使其能够在恶劣环境下长时间工作。
三、氮元素氮元素是聚晶金刚石涂层中的重要添加元素之一。
氮元素可以与碳元素形成碳氮键,增加涂层的硬度和耐磨性。
此外,氮元素还可以提高涂层的热稳定性和抗氧化性能,使其能够在高温环境下长时间使用。
另外,氮元素还可以调节涂层的晶格结构,使其具有更好的机械性能和导热性能。
四、硅元素硅元素是聚晶金刚石涂层中的重要添加元素之一。
硅元素可以与碳元素形成硅碳键,增加涂层的硬度和耐磨性。
此外,硅元素还可以提高涂层的抗腐蚀性能和热稳定性,使其能够在恶劣环境下长时间工作。
另外,硅元素还可以调节涂层的晶格结构,使其具有更好的机械性能和导热性能。
五、其他元素除了上述几种主要元素外,聚晶金刚石涂层中还可能含有其他元素,如氧、氢、氩等。
这些元素的添加可以改善涂层的性能和结构,使其具有更好的机械性能、导热性能和抗腐蚀性能。
总结:聚晶金刚石涂层的元素含量对其性能具有重要影响。
碳元素是构成金刚石晶格的主要元素,金属元素的添加可以改善涂层的性能,氮元素和硅元素可以增加涂层的硬度和耐磨性。
刀具涂层的种类及作用介绍【汇总】

刀具涂层的种类及作用介绍内容来源网络,由深圳机械展收集整理!更多数控刀具技术展示,就在深圳机械展-刀具展区!刀具涂层的种类1氮化钛涂层(TiN)TiN是一种通用型PVD涂层,是工艺最成熟和应用最广泛的硬质涂层材料,可以提高刀具硬度并具有较高的氧化温度,适用于高速钢切削刀具或成形工具,改善其加工性能。
2氮化铬涂层(CrN)CrN涂层良好的抗粘结性使其在容易产生积屑瘤的加工中成为首选涂层。
涂覆了这种几乎无形的涂层后,高速钢刀具或硬质合金刀具和成形工具的加工性能将会大大改善。
3金刚石涂层(Diamond)CVD金刚石涂层可为非铁金属材料加工刀具提供最佳性能,是加工石墨、金属基复合材料(MMC)、高硅铝合金及许多其它高磨蚀材料的理想涂层。
适用于硬铣、攻丝和钻削加工的涂层各不相同,分别有其特定的使用场合。
此外,还可以采用多层涂层,此类涂层在表层与刀具基体之间还嵌入了其它涂层,可以进一步提高刀具的使用寿命。
4氮碳化钛涂层(TiCN)TiCN涂层中添加的碳元素可提高刀具硬度并获得更好的表面润滑性,是高速钢刀具的理想涂层。
可增加涂层的厚度,阻止裂纹的扩展,减少崩刃。
所以,目前生产的一些刀片,如瑞典Sandvik公司推荐用于加工钢料的GC4000系列刀片、中国株洲硬质合金厂生产的CN系列刀片、日本东芝公司的T715X 和T725X涂层刀片中均有TiCN涂层成份。
TiCN基涂层适于加工普通钢、合金钢、不锈钢和耐磨铸铁等材料,用它加工工件时的材料切除率可提高2~3倍。
株硬--FMA11系列面铣刀5氮铝钛或氮钛铝涂层(TiAlN/AlTiN)TiAlN/AlTiN涂层中形成的氧化铝层可以有效提高刀具的高温加工寿命。
主要用于干式或半干式切削加工的硬质合金刀具可选用该涂层。
根据涂层中所含铝和钛的比例不同,AlTiN涂层可提供比TiAlN涂层更高的表面硬度,因此它是高速加工领域又一个可行的涂层选择。
例如,美国Kennametal公司推出的H7刀片,系TiAlN涂层,是专为高速铣削合金钢、高合金钢和不锈钢等高性能材料而设计的。
刀具涂层种类
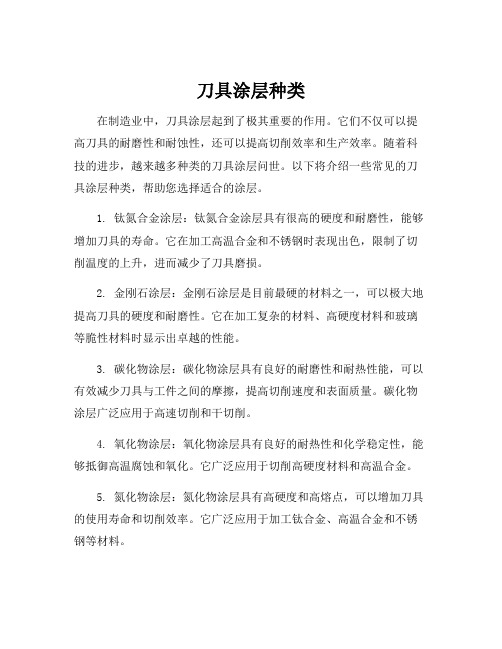
刀具涂层种类在制造业中,刀具涂层起到了极其重要的作用。
它们不仅可以提高刀具的耐磨性和耐蚀性,还可以提高切削效率和生产效率。
随着科技的进步,越来越多种类的刀具涂层问世。
以下将介绍一些常见的刀具涂层种类,帮助您选择适合的涂层。
1. 钛氮合金涂层:钛氮合金涂层具有很高的硬度和耐磨性,能够增加刀具的寿命。
它在加工高温合金和不锈钢时表现出色,限制了切削温度的上升,进而减少了刀具磨损。
2. 金刚石涂层:金刚石涂层是目前最硬的材料之一,可以极大地提高刀具的硬度和耐磨性。
它在加工复杂的材料、高硬度材料和玻璃等脆性材料时显示出卓越的性能。
3. 碳化物涂层:碳化物涂层具有良好的耐磨性和耐热性能,可以有效减少刀具与工件之间的摩擦,提高切削速度和表面质量。
碳化物涂层广泛应用于高速切削和干切削。
4. 氧化物涂层:氧化物涂层具有良好的耐热性和化学稳定性,能够抵御高温腐蚀和氧化。
它广泛应用于切削高硬度材料和高温合金。
5. 氮化物涂层:氮化物涂层具有高硬度和高熔点,可以增加刀具的使用寿命和切削效率。
它广泛应用于加工钛合金、高温合金和不锈钢等材料。
除了上述常见的涂层种类,还有许多其他创新的涂层技术不断涌现。
例如,纳米涂层技术可以在刀具表面形成纳米级的涂层,进一步提高刀具的切削性能和寿命。
此外,多层涂层和渗氮等技术也被广泛应用。
在选择刀具涂层时,需要根据具体的加工材料和加工要求来进行选择。
例如,加工高硬度材料时,可以选择金刚石涂层;加工高温合金时,可以选择氮化物或钛氮合金涂层。
此外,还需要考虑加工环境、切削速度和表面要求等因素。
综上所述,刀具涂层是提高切削效率和降低生产成本的关键技术之一。
在选择刀具涂层时,应根据具体情况进行合理选择,并及时了解新的涂层技术。
通过选择合适的刀具涂层,可以实现更高效、更稳定的加工过程,提高产品质量和生产效率。
超硬涂层知识图文并茂详解(6种)
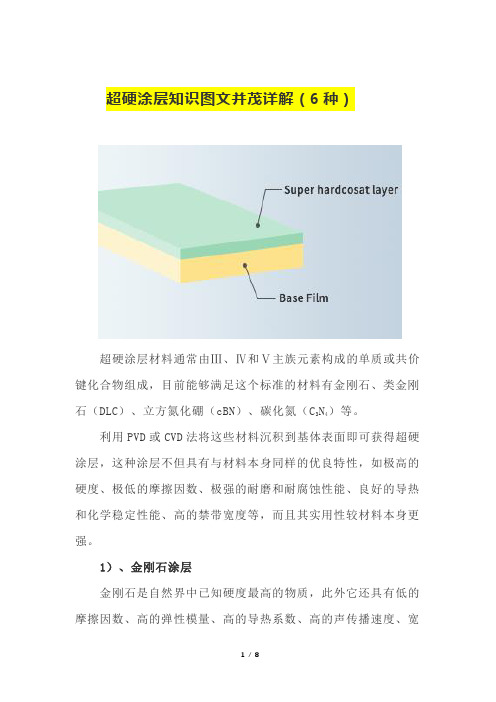
超硬涂层知识图文并茂详解(6种)超硬涂层材料通常由Ⅲ、Ⅳ和Ⅴ主族元素构成的单质或共价键化合物组成,目前能够满足这个标准的材料有金刚石、类金刚石(DLC)、立方氮化硼(cBN)、碳化氮(C3N4)等。
利用PVD或CVD法将这些材料沉积到基体表面即可获得超硬涂层,这种涂层不但具有与材料本身同样的优良特性,如极高的硬度、极低的摩擦因数、极强的耐磨和耐腐蚀性能、良好的导热和化学稳定性能、高的禁带宽度等,而且其实用性较材料本身更强。
1)、金刚石涂层金刚石是自然界中已知硬度最高的物质,此外它还具有低的摩擦因数、高的弹性模量、高的导热系数、高的声传播速度、宽的能带隙以及良好的化学稳定性等,然而天然金刚石的存量及价格限制了它的大规模商业化应用。
目前一般会采用CVD法制备金刚石涂层,它具有与天然金刚石非常相近的物理和化学性能,根据金刚石的晶粒尺寸,可以将CVD金刚石涂层分为微米晶金刚石(MCD)涂层和纳米晶金刚石(NCD)涂层,其中,晶粒尺寸小于10nm时,被称作超纳米金刚石(UNCD)涂层。
CVD金刚石涂层制备技术已取得了非常大的进展,部分产品已进入产业化推广阶段,并形成了一定的市场规模,应用领域非常多,如下图所示:2)、类金刚石(DLC)涂层利用离子束沉积技术制备了一种化学组成、光学透过率、硬度以及耐磨损等性能与金刚石相近的非晶碳涂层。
这种碳涂层具有以sp3键碳共价结合为主体,混合有sp2键碳的亚稳态长程无序立体网状结构,被称为类金刚石(DLC)涂层。
由于DLC涂层中既有类似于金刚石的sp3键合形式,又有类似于石墨的sp2键合形式,因而其结构和性能介于金刚石和石墨之间。
DLC涂层具有与金刚石涂层非常相近的性能,即极高的硬度、电阻率、导热系数、电绝缘强度、高红外透射性以及光学折射率,同时具有良好的化学稳定性和生物相容性等,在机械、电子、光学、声学、计算机以及生物医学等领域有着广阔的应用前景。
不过受沉积方式和环境的影响,DLC涂层中还可能含有氢等杂质,含各种C-H键,因此不同的制备方法和工艺条件对涂层的性能,尤其是硬度的影响很大。
金刚石涂层刀具表面处理方法

金刚石涂层刀具表面处理方法
金刚石涂层刀具是当前最先进的刀具材料,能够用于切削加工,深度加工,磨削加工等业务。
但是,由于其高硬度,往往表面会变得失光、发粗和有氧化皮,因此,金刚石涂层刀具表面处理方法成为最重要的课题。
首先,对金刚石涂层刀具表面的处理通常都要清洁后进行,以期获得最佳效果。
在这一步之前,专门的腐蚀剂可以用来去除残留的油料,令表面干净平整。
接着,用清水和肥皂水将清洗完毕的表面清洗,以去除尘土和散装颗粒杂质,待干后,可以开始表面处理。
其次,常用的表面处理方法有拉丝法、抛光法和渗透涂层法。
以拉丝法为例,其处理程序大致是先用拉丝和抛光轮,将残留在金刚石涂层刀具表面的某些物质拉丝掉;接着,用抛光轮抛光表面,使其变得光滑,并减少断层,从而提高加工精度。
此外,抛光法也可以用于对金刚石涂层刀具表面进行处理。
采用抛光头抛光表面,使抛光头更加柔软,减少材料的磨耗,同时也起到反膨胀作用,使表面变得平整光滑。
特别是在定形加工中,采用抛光法可以消除表面毛刺,减少刀具的磨耗,提高加工精度和表面质量。
最后,渗透涂层处理也是对金刚石涂层刀具表面进行处理的一种方法,它将涂料放到表面上,然后用热涂技术进行处理,使表面形成深度渗透层,有效保护刀具金刚石涂层,提高表面耐擦损性能,减少氧化反响,延长刀具寿命。
综上所述,对金刚石涂层刀具表面的处理方法有拉丝法、抛光法
和渗透涂层法,它们都可以显著提高表面光泽度,延长刀具使用寿命,提高加工精度,从而使加工质量得到大大改善。
因此,金刚石涂层刀具表面处理是十分重要的,工程师和技术人员应当正确选择和适宜的处理方法,以提高加工质量,保证产品质量。
PCD﹑PCBN刀具材料及刀具涂层
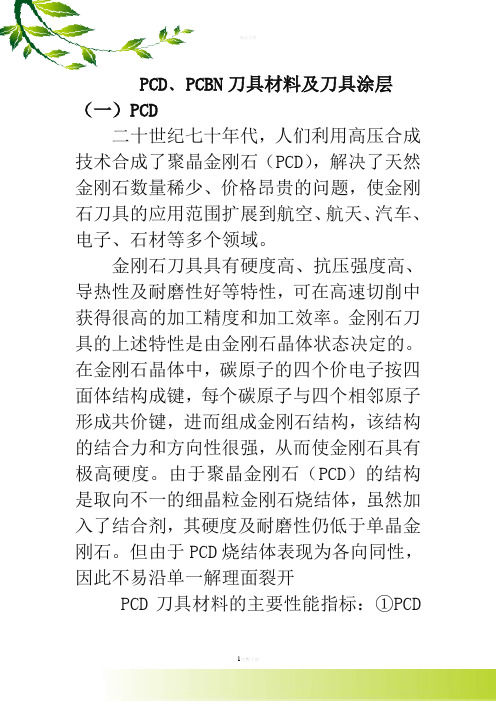
PCD﹑PCBN刀具材料及刀具涂层(一)PCD二十世纪七十年代,人们利用高压合成技术合成了聚晶金刚石(PCD),解决了天然金刚石数量稀少、价格昂贵的问题,使金刚石刀具的应用范围扩展到航空、航天、汽车、电子、石材等多个领域。
金刚石刀具具有硬度高、抗压强度高、导热性及耐磨性好等特性,可在高速切削中获得很高的加工精度和加工效率。
金刚石刀具的上述特性是由金刚石晶体状态决定的。
在金刚石晶体中,碳原子的四个价电子按四面体结构成键,每个碳原子与四个相邻原子形成共价键,进而组成金刚石结构,该结构的结合力和方向性很强,从而使金刚石具有极高硬度。
由于聚晶金刚石(PCD)的结构是取向不一的细晶粒金刚石烧结体,虽然加入了结合剂,其硬度及耐磨性仍低于单晶金刚石。
但由于PCD烧结体表现为各向同性,因此不易沿单一解理面裂开PCD刀具材料的主要性能指标:①PCD的硬度可达8000HV,为硬质合金的80~120倍;②PCD的导热系数为700W/mK,为硬质合金的1.5~9倍,甚至高于PCBN和铜,因此PCD刀具热量传递迅速;③PCD的摩擦系数一般仅为0.1~0.3(硬质合金的摩擦系数为0.4~1),因此PCD刀具可显著减小切削力;④PCD的热膨胀系数仅为0.9×10 -6~1.18×10 -6,仅相当于硬质合金的1/5,因此PCD刀具热变形小,加工精度高;⑤PCD 刀具与有色金属和非金属材料间的亲和力很小,在加工过程中切屑不易粘结在刀尖上形成积屑瘤。
PCD刀具的应用: 工业发达国家对PCD刀具的研究开展较早,其应用已比较成熟。
自1953年在瑞典首次合成人造金刚石以来,对PCD刀具切削性能的研究获得了大量成果,PCD刀具的应用范围及使用量迅速扩大。
目前,国际上著名的人造金刚石复合片生产商主要有英国De Beers公司、美国GE公司、日本住友电工株式会社等。
据报道,1995年一季度仅日本的PCD刀具产量即达10.7万把。
合金表面类金刚石膜的表面特征

合金表面类金刚石膜具有以下表面特征:
高硬度:金刚石是自然界中最硬的物质之一,合金表面覆盖金刚石膜后,可显著提高表面硬度。
金刚石膜具有极高的硬度(约为1500-10000 HV),使得合金表面具备优异的耐磨性和抗刮擦性。
低摩擦系数:金刚石膜的表面具有较低的摩擦系数,这意味着合金表面覆盖金刚石膜后,摩擦损耗减小,摩擦系数降低,从而提高了合金材料的耐磨性能。
耐腐蚀性:金刚石膜具有优异的化学稳定性和耐腐蚀性能,可以有效保护合金表面免受腐蚀、氧化和化学侵蚀的影响。
优异的热导性:金刚石膜具有良好的热导性,可以有效提高合金表面的散热性能,减少热应力和热疲劳的发生。
光滑度和平整度:金刚石膜具有良好的光滑度和平整度,使得合金表面变得光滑、平整,并减少表面粗糙度,有利于减少摩擦、磨损和腐蚀。
生物相容性:金刚石膜具有良好的生物相容性,对于医疗器械和生物材料应用具有潜在的优势。
总体而言,合金表面覆盖金刚石膜后,具备高硬度、低摩擦系数、耐腐蚀性、优异的热导性和光滑度等特征,可在许多领域中提供重要的性能改善和保护。
这使得金刚石膜成为一种重要的功能性涂层材料。
- 1、下载文档前请自行甄别文档内容的完整性,平台不提供额外的编辑、内容补充、找答案等附加服务。
- 2、"仅部分预览"的文档,不可在线预览部分如存在完整性等问题,可反馈申请退款(可完整预览的文档不适用该条件!)。
- 3、如文档侵犯您的权益,请联系客服反馈,我们会尽快为您处理(人工客服工作时间:9:00-18:30)。
60
0,1225 0,25
Inconel turning
Tinalox InoCon Ferrocon
Flank Wear (µm)
200 150 100 50 0 0 200 400 600 800 1000 1200 1400
1600
1800
2000
Cutting length L (m)
Zecha „Quality Line“ Outstanding price-/performance ratio for standard applications
024 // <Author>
www.cemecon.de
The Right Tool for CFRP
025 // <Author>
03 // <Author>
80.000 tools/day
www.cemecon.de
溅射技术较电弧技术的优势
电弧技术 溅射技术
优势 - 沉积速率快 - 结构简单 -金属离化率高 -绕镀性好
劣势 -液滴,表面粗糙 -残余应力大 -沉积厚涂层受限
优势 -表面光滑、无液滴 -灵活 -无残余应力 -可沉积厚涂层
PVD Sputtering
www.cemecon.de
业务范围
Job Coating Service
Technology Transfer
24/7 service production in Würselen (Aachen) 35 PVD and 12 diamond machines ≈ 150.000 round tools/months ≈ 1 – 1,5 Mio cutting inserts/months
HiPIMS-TiAlN: less defects, no delamination
08 // <Author> www.cemecon.de
HiPIMS 的优势(厚度均匀性)
Source: IOT Aachen 09 // <Author> www.cemecon.de
HiPIMS 的优势(小径刀)
019 // <Author>
www.cemecon.de
Diamond Coated Tools
020 // <Author>
www.cemecon.de
Diamond Coated Tools
CVD diamond coating typ. 6-20 µm
021 // <Author>
www.cemecon.de
劣势 - 沉积速率低 -金属离化率低 -绕镀性差
04 // <Author>
www.cemecon.de
VD涂层与电弧涂层 CemeCon PVD Sputter Process 高能离子溅射工艺
ARC - Prozess 电弧工艺
• smooth surfaces • 光滑的表面结构 • droplet free and high density • 无液滴和微孔
wear max. wear AlTiN Saturn InoCoN
Wear [µm]
80 60 40 20 0
Cutting data: n= 3813 1/min, Vc= 80 m/min, Vf= 446 mm/min, fz= 0,035, ap= 5mm, ae= 3mm t = 34min, wet
011 // <Author>
www.cemecon.de
Hitachi: Si-containing coatings for micro-tools
012 // <Author>
www.cemecon.de
HiPIMS的优势(更好的附着力)
InoCon® – Si doped – outstandingly high 120 N scratch FerroCon® – AlTiN – 130 N
FerroCon recommended for Inconel
015 // <Author> www.cemecon.de
InoCon: Hard Milling
Workpiece material: 1.2379 (X153CrMoV12) , 62 HRC Tool: Ø6mm ballnose endmill Cutting data: n= 6366 1/min, Vc= 120 m/min, Vf= 1655 mm/min, zf= 0,13, ap= 0,1mm, ae= 0,1mm t = 100min, dry TiAlSiN State-of-the-art 71 µm wear Flank side Flank side InoCon 19 µm wear
05 // <Author> www.cemecon.de
赛利PVD涂层与电弧涂层
电弧涂层工艺 溅射涂层工艺
PVD 溅射工艺 极光滑的刀具表面 完好的切削刃
06 // <Author>
www.cemecon.de
HiPIMS的优势 电弧 CemeCon 溅射 溅射 = 光滑
竞争者 HiPIMS
炙热并且稠密的等离子体
014 // <Author>
www.cemecon.de
FerroCon vs. InoCon, Inconel Turning
Finishing
Cutting conditions Value Units m/min mm/rev mm
Speed
Feed rate Depth of cut
CemeCon HiPIMS
低应力 厚涂层
07 // <Author>
www.cemecon.de
HiPIMS 的优势(小径刀)
B75 ø0,075mm B75 ø0,075mm
Competitor: Defects and delamination
B75 ø0,075mm
B75 ø0,075mm
www.cemecon.de
涂层材料表
026 // <Author>
www.cemecon.de
CemeCon patent EP 200002890
023 // <Author> www.cemecon.de
Graphite Machining
diamond coated tool with ball nose; product line 560 – High End Line
highest precision level, very fine surface quality due to the smooth diamond coating liftetime Zecha tool: > 1.000 min in Graphite type TTK50 liftetime was: 300 min
AlTiN
InoCon
InoCon: Wear is less and more uniform
017 // <Author> www.cemecon.de
InoCon: Stainless Steel Milling
70
Wear [µm]
60 52 µm 50 44 µm 40
Vc= 179 m/min ae= 1 mm ap= 5 mm
Endmill: Ø10 mm cutting length: 145 m CrNi (1.4571, V4A), dry
Hardlox
ICon
InoCon better than Hardlox
018 // <Author> www.cemecon.de
CVD Diamond Production at CemeCon
013 // <Author> www.cemecon.de
HIPIMS的优势
HIPIMS技术对用户的主要益处
N S
S N Source
N S
Me Me Me
• 对形状复杂的工件可获得更 加一致的涂层 • 加强的刻蚀 • 涂层附着力增强 • 涂层更加致密 • 涂层具有更高的硬度
Me+ Me+ Me+
Today‘s state of the art Ø 0,075 mm
HiPIMS for Ø 0,075 mm
010 // <Author> www.cemecon.de
Hitachi: Si-containing coatings for micro-tools Hitachi: Si-containing coatings for micro-tools
Morphology of Diamond Coatings standard (micro-cyrstalline) – smooth layer (nano-cyrstalline)
022 // <Author>
www.cemecon.de
Multilayer Diamond Coatings for Cutting Tools
Rake side
Rake side InoCoN: less wear + more uniform
016 // <Author>
www.cemecon.de
InoCon: Stainless Steel Milling
120 100
Workpiece material: 1.4301 Tool: Ø8mm endmill