机械设计制造工艺基础
《机械制造工艺》基础知识点

《机械制造工艺》基础知识点材料成型机理:人为地将零件的加工过程分为热加工和冷加工两个阶段,而且是以冷去初加工和热变形加工为主。
从加工成型机理分类,加工工艺分为去除加工、结合加工和变形加工。
机械加工工艺过程:是机械产品生产过程的一部分,是直接生产过程。
其原意是指采用金属切削刀具或磨具来加工工件,使之达到所要求的形状、尺寸、表面粗糙度和力学物理性能,成为合格零件的成产过程。
六点定位原理:采用6个按一定规则布置的约束点来限制工件的6个自由度,实现完全定位。
从设计和工艺两个方面来分析,基准可分为设计基准和工艺基准两大类。
设计基准:设计者在设计零件时,根据零件在装配结构中的装配关系和零件本身解构要素之间的互相位置关系,确定标注尺寸的起始位置,这些起始位置可以是点、线或面,称之为设计基准。
工序:一个(或一组)工人在一个工作地点对一个(或同时对几个)工件连续完成的那一部分工艺过程。
工艺基准:零件在加工工艺过程中所用的基准称为工艺基准。
工艺基准又可进一步分为:工序基准、定位基准、测量基准和装配基准。
工序基准:在工序图上用来确定本工序所加工表面加工后的尺寸、形状和位置的基准。
定位基准:在加工时用于工件定位的基准。
可以分为粗基准和精基准,又可分为固有基准和附加基准。
零件的加工质量包含零件的机械加工精度和加工表面质量两个方面。
机械加工精度:是指零件加工后的实际几何参数与理论几何参数的符合程度。
机械加工误差:是指零件加工后的实际几何参数与理论几何参数的偏离程度。
零件的加工精度包含3方面的内容:尺寸精度、形状精度和位置精度。
误差的敏感方向:加工精度影响最大的那个方向(即通过切削刃的加工表面的法向)。
加工原理误差:是指采用了近似的成形运动或近似的切削刃轮廓进行加工而产生的误差。
影响机床误差的因素:导轨导向误差、主轴回转误差和传动链的传动误差。
主轴回转误差:是指主轴实际回转轴线对其理想回转轴线的漂移。
主轴回转轴线的运动误差可以分为分解为径向圆跳动、轴向圆跳动和倾角摆动三种基本形式。
机械制造工艺基础复习题及答案

机械制造工艺基础复习题及答案《机械制造工艺基础》复习题第1章切削与磨削过程一、单项选择题1、金属切削过程中,切屑的形成主要是(1)的材料剪切滑移变形的结果。
①第Ⅰ变形区②第Ⅱ变形区③第Ⅲ变形区④第Ⅳ变形区2、在正交平面内度量的基面与前刀面的夹角为(1)。
①前角②后角③主偏角④刃倾角3、切屑类型不但与工件材料有关,而且受切削条件的影响。
如在形成挤裂切屑的条件下,若加大前角,提高切削速度,减小切削厚度,就可能得到(1)。
①带状切屑②单元切屑③崩碎切屑④挤裂切屑4、切屑与前刀面粘结区的摩擦是(2)变形的重要成因。
①第Ⅰ变形区②第Ⅱ变形区③第Ⅲ变形区④第Ⅳ变形区5、切削用量中对切削力影响最大的是(2)。
①切削速度②背吃刀量③进给量④切削余量6、精车外圆时采用大主偏角车刀的主要目的是降低(2)。
①主切削力Fc②背向力Fp③进给力Ff④切削合力F7、切削用量三要素对切削温度的影响程度由大到小的顺序是(2)。
①vcapf②vcfap③fapvc④apfvc8、在切削铸铁等脆性材料时,切削区温度最高点一般是在(3)。
①刀尖处②前刀面上靠近刀刃处③后刀面上靠近刀尖处④主刀刃处(加工钢料塑性材料时,前刀面的切削温度比后刀面的切削温度高,而加工铸铁等脆性材料时,后刀面的切削温度比前刀面的切削温度高。
因为加工塑性材料时,切屑在前刀面的挤压作用下,其底层金属和前刀面发生摩擦而产生大量切削热,使前刀面的温度升高。
加工脆性材料时,由于塑性变形很小,崩碎的切屑在前刀面滑移的距离短,所以前刀面的切削温度不高,而后刀面的摩擦产生的切削热使后刀面切削温度升高而超过前刀面的切削温度。
)(前刀面和后刀面上的最高温度都不在刀刃上,而是离开刀刃有一定距离的地方。
切削区最高温度点大约在前刀面与切屑接触长度的一半处,这是因为切屑在第一变形区加热的基础上,切屑底层很薄一层金属在前刀面接触区的内摩擦长度内又经受了第二次剪切变形,切屑在流过前刀面时又继续加热升温。
机械制造工艺基础知识点总结

机械制造工艺基础知识点第一章金属切削加工基础知识一、切削加工基本概念1、成形运动(切削运动)是为了形成工件表面所必需的、刀具与工件之间的相对运动。
成形运动(切削运动)包括主运动和进给运动。
2、主运动是指直接切除工件上的切削层,形成已加工表面所需的最基本运动。
一般来讲,主运动是成形运动中速度最高、消耗功率最大的运动,机床的主运动只有一个。
3、进给运动是指不断地把切削层投入切削的运动,以加工出完整表面所需的运动。
进给运动可能有一个或几个,通常运动速度较低,消耗功率较小。
4、切削过程中,工件上形成三个表面1)待加工表面——将被切除的表面;2)过渡表面——正在切削的表面;3)已加工表面——切除多余金属后形成的表面。
5、切削用量三要素1)切削速度v c切削刃上选定点在主运动方向上相对于工件的瞬时速度。
2)进给量f在进给运动方向上,刀具相对于工件的位移量,称为进给量。
3)背吃刀量a p背吃刀量是在通过切削刃基点并垂直于工作平面方向上测量的切削深度。
6、成形运动简图7、切削层尺寸要素(1)切削层:刀具切过工件的一个单程,或只产生一圈过渡表面的过程中所切除的工件材料层。
(2)切削层尺寸平面:通过切削刃基点并垂直于该点主运动方向的平面,称为切削层尺寸平面。
(3)切削层尺寸要素①切削厚度:指在切削层尺寸平面内,沿垂直于切削刃方向度量的切削层尺寸。
②切削宽度:指在切削层尺寸平面内,沿切削刃方向度量的切削层尺寸。
③切削面积:是指在给定瞬间,切削层在切削层尺寸平面里的实际横截面面积。
二、刀具角度1、车刀的组成三个刀面:前面、主后面、副后面两个切削刃:主切削刃、副切削刃一个刀尖2、辅助平面1)基面:过切削刃选定点,垂直于主运动方向的平面。
2)主切削平面:过切削刃选定点,与切削刃相切,并垂直于基面的平面。
3)正交平面:通过主切削刃上的某一点,并同时垂直于基面和切削平面的平面。
3、车刀的标注角度γ(1)前角在正交平面中测量,是刀具前面与基面之间的夹角。
机械制造工艺基础全套ppt课件

2.定位基准的分类
粗基准——在最初的切削工序中,只能使用毛 坯上未经加工的表面来定位,也称作毛基准 。
精基准——在后序的各工序中,采用已加工表 面作为定位基准表面。
15
3.粗基准的选择
(1)对于不需加工全部表面的零件,应采用始终不 加工的表面作为粗基准。
选择不加工表面作粗基准
16
用相互位置精度要求高的不加工表面作粗基准
25
2.划分加工阶段的作用
有利于消除或减小变形对加工精度的影响。 可尽早发现毛坯的缺陷。 有利于合理地选择和使用设备。 有种于合理组织生产和工艺布置。
26
三、工序的集中与分散
工序集中——在一道工序中尽可能多地包含加工内 容,而使工艺过程中总的工序数目减少。集中到极限时, 工艺过程只有一道工序,这道工序就能把工件加工到图 样规定的要求。
第一节 机械加工工艺过程的组成和特征
一、生产过程与工艺过程
1.生产过程
生产过程——将原材料转变为成品的全过程。
2.工艺过程
工艺过程——在生产过程中,直接改变原材料(或毛坯) 形状、尺寸和性能,使之变为成品或半成品的过程。
1
(1)工序 工序——一个或一组工人,在一个工作地点对一个 或一组工件所连续完成的那部分工艺过程。 工序是工艺过程的基本组成部分。
二、加工阶段的划分
粗加工阶段:切除工件各加工表面的大部分余量。在 粗加工阶段,主要的问题是如何提高生产率。
半精加工阶段:达到一定的准确度要求,完成次要表 面的最终加工,并为主要表面的精加工作好准备。
精加工阶段:完成各主要表面的最终加工,使工件的 加工精度和加工表面质量达到图样规定的要求。
4.精基准的选择
基准重合原则 基准统一原则 互为基准原则 自为基准原则 基准不重合误
机械制造的技术基础--装配工艺
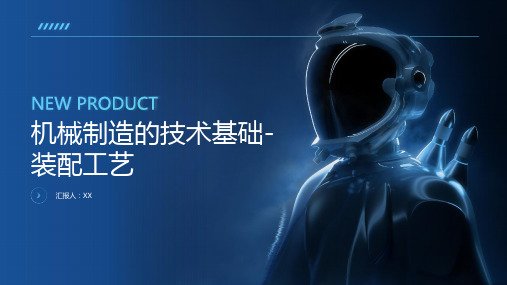
采用先进的装 配技术和工具, 如自动化装配、 机器人装配等
优化装配工艺 流程,减少不 必要的工序和
操作
提高装配人员 的技能和素质, 加强培训和考
核
采用精密测量 和检测设备, 确保装配精度
和质量
采用模块化、 标准化的设计 理念,提高装 配效率和精度
加强质量管理 和控制,确保 装配过程的稳 定性和可靠性
料浪费。
提高企业竞争力: 自动化装配技术 可以提高企业的 竞争力,使企业 在市场中占据更
有利的地位。
自动化装配系统的组成: 包括机械手、传送带、
控制系统等
自动化装配系统的分类: 根据自动化程度不同,可 以分为半自动装配系统和
全自动装配系统
半自动装配系统:需要 人工参与,但大部分工
作由机器完成
全自动装配系统:无需 人工参与,全部工作由
人性化设计:考虑操 作者的舒适度和安全 性,降低劳动强度, 提高工作效率
环保化设计:采用环保 材料和工艺,减少废弃 物和污染物的产生,降 低对环境的影响
优化装配工艺:通过 改进装配工艺,提高 产品质量和生产效率 ,降低生产成本
提高装配工艺的可靠性 和稳定性:通过优化装 配工艺,提高产品的可 靠性和稳定性,降低故 障率和维修成本
密封装置的类型:O型圈、V 型圈、垫片等
装配工艺流程:清洗、安装、 调整、检验
注意事项:避免损伤密封装置, 确保安装精度和密封性能
自动化装配技术
提高生产效率: 自动化装配技 术可以大大提 高生产效率, 减少人工操作
时间。
提高产品质量: 自动化装配技 术可以保证产 品的质量,减 少人为误差。
降低生产成本: 自动化装配技 术可以降低生 产成本,减少 人工费用和材
第1章机械制造工艺基础.ppt

1.3 生产纲领与生产类型
1.3.1 生产纲领
1. 生产纲领
生产纲领是指企业在计划期内应当生产的产品产
量和进度计划。因计划期常常定为1年,所以也称为年
产量。
年度生产计划也称作年生产纲领。
零件的生产纲领要记入备品和废品的数量 :
N=Qk(1+i1)(1+i2)
1.3 生产纲领与生产类型
2. 生产类型
机械加工工艺过程组成见图1-2。
1.2 工艺过程及其组成
1.2 工艺过程及其组成
1.2.1 工序 1. 工序及其划分
工序是一个(或一组)工人,在一个工作地对同 一个(或同时对几个)工件进行加工所连续完成的那 部分工艺过程 。工序是组成工艺过程的基本单元,也是生产计 划的基本单元。
特点:“三同”和“一个连续”。
1.2 工艺过程及其组成 复合工步举例
1.2 工艺过程及其组成
2.工作行程(走刀) 工作行程,也称走刀,它是切削工具以加工进
给速度,相对工件所完成一次进给运动的工步部分。 当工件表面的加工余量较大,不可能一次工作行程
就能完成,这时就要分几次工作行程(走刀)。工 作行程的次数也称行程次数。
刀具以非加工进给速度相对工件所完成一次进 给运动的工步部分,称作“空行程”。空行程能检 查刀具相对工件的运动轨迹。
是产品除外购件以外的全部零(部)件,在 由毛坯准备到成品包装入库的生产过程中,所经 过的各有关部门(科室、车间、工段、小组或工 种)或工序的先后顺序。
1.2 工艺过程及其组成
工艺过程: 工艺过程就是指改变生产对象的形状、尺寸、相对位置
和性质等,使其成为成品或半成品的过程。 机械加工工艺过程:
机械加工工艺过程是指利用机械加工的方法,直接改变 毛坯的形状、尺寸和表面质量,使其成为成品或半成品的过 程。
机械制造基础:制造工艺设计理论
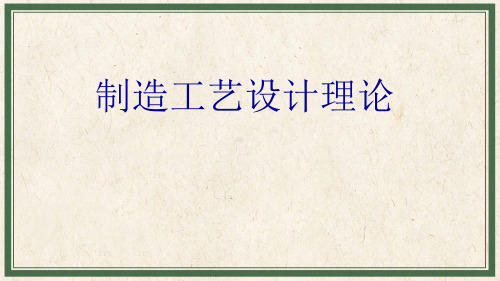
高速精铣 IT6~7
Ra 0.16¬1.25 精磨 IT6~8
Ra 0.16¬1.25
宽刀精刨 IT6
Ra 0.16¬1.25
刮研
Ra 0.04¬1.25
抛光
Ra0.008¬1.25
研磨 IT5~6 Ra0.008¬0.63
导轨磨 IT6
Ra0.16¬1.25
砂带磨 IT5~6
2、工序分散就是将工件的加工,分散在较多的工 序内进行。每道工序的加工内容很少,最少时每道 工序仅一个简单工步。
3、趋势:工序集中
工序集中与分散
概念:
工序1
工步1
集中:m较少 N较多 分散:m较多 N较少
工序2
工序3
工序m
工步1
工步1
工步1
工步2 工步3
工步2 工步3
工步2 工步3
工步2 工步3
工步n
研磨 IT5
Ra 0.008~0.32
超精加工 IT5
Ra 0.01~0.32
砂带磨 IT5
Ra 0.01~0.16
精密磨削 IT5
Ra 0.008~0.08
抛光
Ra 0.008~1.25
孔的典型加工路线
钻 IT10~13 Ra 5~80
粗镗 IT9~12 Ra 5~20
扩 IT9~13 Ra 1.25~40
被加工的某一表面,由于余量较大或其它原因,在切削 用量不变的条件下,用同一把刀具对它进行多次加工,每加 工一次,称一次走刀。
工艺设计步骤
任务1:零件加工前的原始资料
① 零件图(工作图) ② 产品生产纲领 ③ 毛坯资料 ④ 现场生产条件
⑤ 工艺资料
机械制造工艺基础习题册答案
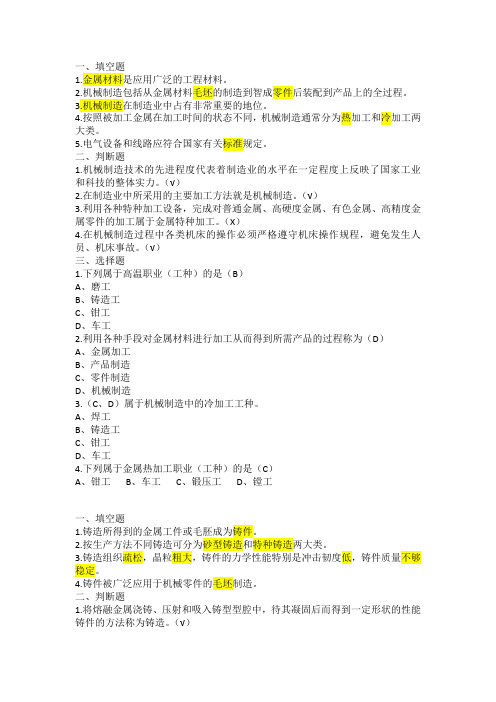
一、填空题1.金属材料是应用广泛的工程材料。
2.机械制造包括从金属材料毛坯的制造到智成零件后装配到产品上的全过程。
3.机械制造在制造业中占有非常重要的地位。
4.按照被加工金属在加工时间的状态不同,机械制造通常分为热加工和冷加工两大类。
5.电气设备和线路应符合国家有关标准规定。
二、判断题1.机械制造技术的先进程度代表着制造业的水平在一定程度上反映了国家工业和科技的整体实力。
(√)2.在制造业中所采用的主要加工方法就是机械制造。
(√)3.利用各种特种加工设备,完成对普通金属、高硬度金属、有色金属、高精度金属零件的加工属于金属特种加工。
(X)4.在机械制造过程中各类机床的操作必须严格遵守机床操作规程,避免发生人员、机床事故。
(√)三、选择题1.下列属于高温职业(工种)的是(B)A、磨工B、铸造工C、钳工D、车工2.利用各种手段对金属材料进行加工从而得到所需产品的过程称为(D)A、金属加工B、产品制造C、零件制造D、机械制造3.(C、D)属于机械制造中的冷加工工种。
A、焊工B、铸造工C、钳工D、车工4.下列属于金属热加工职业(工种)的是(C)A、钳工B、车工C、锻压工D、镗工一、填空题1.铸造所得到的金属工件或毛胚成为铸件。
2.按生产方法不同铸造可分为砂型铸造和特种铸造两大类。
3.铸造组织疏松,晶粒粗大,铸件的力学性能特别是冲击韧度低,铸件质量不够稳定。
4.铸件被广泛应用于机械零件的毛坯制造。
二、判断题1.将熔融金属浇铸、压射和吸入铸型型腔中,待其凝固后而得到一定形状的性能铸件的方法称为铸造。
(√)2.铸件内部易产生缩孔、缩松、气孔等缺陷,会导致铸件的力学性能特别是冲击韧度低,铸件质量不够稳定。
(√)3.铸件的力学性能特别是冲击韧度低,但铸件质量很稳定。
(X)4.由于铸造易产生缺陷,性能不高,因此多用于制造承受应力不大的工件。
(√)5.铁液包、钢液包和灼热件起重作业影响范围内不得设置休息室、更衣室和人行通道,不得存放危险物品,地面应保持干燥。
- 1、下载文档前请自行甄别文档内容的完整性,平台不提供额外的编辑、内容补充、找答案等附加服务。
- 2、"仅部分预览"的文档,不可在线预览部分如存在完整性等问题,可反馈申请退款(可完整预览的文档不适用该条件!)。
- 3、如文档侵犯您的权益,请联系客服反馈,我们会尽快为您处理(人工客服工作时间:9:00-18:30)。
机械设计制造工艺基础《机械设计制造工艺基础(第二版)》复习参考复习须矢口本书一共二十个知识点请各位同学参照本资料结合教材认真复习每一个知识点。
该份参考资料由学习小组成员中的张丽红、梁丹丹、舒扬、李帅、何斌五位同学负责归纳整理总结。
同学们在复习过程中如发现资料上有与教材不相符的地方请以教材为准并及时告知上述成员中任何一名同学我们好及时更正。
另外在打印过程中请勿随便改变字体大小否则容易将含有树状图分类的知识点对错位影响你的复习。
最后希望每一位同学都能认真复习考试取得让你满意的成绩。
切削加工的定义、分类、特点切削加工的定义:切削加工是利用切削工具从工件上切去多余材料的加工方法通过切削加工使工件变成符合图样规定的形状、尺寸和表面粗糙度等技术要求的零件。
切削加工的分类:机械加工和钳工加工两大类。
机械加工是通过工人操纵机床进行加工的其方法有车削、钻削、锤削、铳削、刨削、拉削、磨削、超精加工和抛光等。
钳工加工:一般在钳台上以手工工具为主其工作内容有划线、锯削、铿削、舌U削、研磨、钻孔、扩孔、皎孔、攻螺纹、套螺纹、机械装配和设备修理等。
切削加工的特点切削加工的精度和表面粗糙度的范围广泛且可获得很高的加工精度和很低的表面粗糙度。
切削加工零件的材料、形状、尺寸和重量的范围较大。
切削加工的生产率较高。
切削过程中存在切削力工具和工件均具有一定的强度和刚度且刀具材料的硬度必须大于工件材料的硬度。
切削用量三要素切削用量是衡量切削加工时切削运动大小及工件与刀具相对位置的量。
切削速度 Vc、进给量f、背吃刀量ap称为切削三要素。
切削速度:切削刃选定点相对于工件的主运动的瞬时速度。
进给量:刀具在进给方向上相对工件的位移量可用刀具和工件每转或每行程的位移量来表素和度量。
背吃刀量:在垂直于进给方向上测量的主切削刃切入工件的深度。
切削用量选择的一般原则:①背吃刀量的选择②进给量的选择③切削速度的选择切削三要素的选择与加工深度和生产率有关。
通常情况下粗加工要从生产率的角度考虑精加工要选择较小的切削用量。
切削运动的分析、特点切削运动分为主运动和进给运动。
主运动:由机床或人力提供的主要运动它促使刀具和工件之间产生相对运动从而使刀具前刀面接近工件。
进给运动:由机床或人力提供的运动它使刀具与工件之间产生附加的相对运动加上主运动即可不断地切除切屑得到具有所需几何特征的表面。
普通机床的主运动一般只有一个。
与进给运动相比它的速度高消耗机床功率多。
进给运动可以是一个或多个。
机床名称卧式机床钻床卧铳、立铳主运动进给运动工件车刀纵向、横向、斜向机床名称卧式机床钻床卧铳、立铳主运动进给运动工件车刀纵向、横向、斜向旋转运动直线运动钻头钻头轴向移动牛头刨床旋转运动铳刀工件纵向、横向直线移动旋转运动(有时也作垂直方向移动)刨刀工件横向间歇移动或刨往复运动刀垂向、斜向间歇移动机床名称龙门刨床外圆磨床内圆磨床平面磨床主运动进给运动工件刨刀横向、垂向、斜向间歇往复运动移动砂轮工件转动同时工件往复移高速旋转动砂轮横向移动砂轮工件转动同时工件往复移高速旋转动砂轮横向移动砂轮工件往复移动砂轮横向、高速旋转垂向移动切削瘤的影响与控制(1)切屑瘤的影响:切屑瘤的硬度比工件材料高能代替切些人进行切削保护刀刃以减小磨损.此外切屑瘤增大了刀具实际工作前角使切削轻快所以粗加工时可以利用切屑瘤来保护刀尖故常采用中等速度粗加工。
但是切屑瘤时生时灭使背吃刀量不断变化影响工件的尺寸精度;积屑瘤在工件已加工表面上刻画出不均匀的沟痕影响表面粗糙度 Ra值。
精加工应避免积屑瘤以保证加工质量故常采用高速或低速精加工。
(2)积屑瘤的控制:①提高前刀面的光滑程度②提高工件的硬度降低塑性③采用合适的切屑液④避开积屑瘤产生的速度范围第五至第八知识要点:1.2刀具与刀具切屑过程1.2.1刀具r刀具角度已加工表面1)车刀组成:刀柄和刀体在切削过程中工件上存在三个平■面J 过渡表面(P9看图理解)<待加工表面刀体(刀具切削部分):“三面两刃一尖”(前刀面、主后刀面、副后刀面、主切削刃、副切削刃、刀尖)2)确定刀具角度的静止参考系:P10 (基面Pr、切削平■面Ps、正交平■面Po、假定工作平■面Pf、背平■面Pp)。
注意:有助丁刀具角度的理解3)▲刀具角度主要掌握:前角、后角、主偏角、副偏角、刃倾角。
掌握程度:能判别和标注角度记忆个角度对刀具切削的影响P11- P12刀具材料:▲刀具材料应该具有的性质:具备高的硬度、高的耐磨性、高的耐热性、足够的强度和韧性、较好的工艺性。
「普通刀具材料:高速钢、硬质合金、涂层刀具材料刀具材料分类超硬刀具材料:陶瓷、人造聚晶金刚石、立方氮化硼1.2.2刀具切削过程刀具切削过程实质P15概念塑性金届切削过程是一个挤压变形切离过程分为:弹性变形塑性变形、挤裂和切离四个阶段。
切削变形区P161.2.3刀具切削过程中的物理现象〃切削力Fc1.总切削力分为J进给力Ff背向力Fp切削力是切削加工_不可避免的抗力它对切削产生不利影响因此应尽量减小它。
▲减小切削力措施:增大前角和减小背吃刀量带状切削「急剧磨损切削类型磨损类型y[ 挤裂切削I正常磨损 I单元切削2.切削热:切削过程中因变形和摩擦产生的热量传散途径:切屑、刀具、工件和周围介质▲减小切削热的途径:合理选择切削用量(尤其是切削速度)和刀具角度合理施加切削液。
▲人3.积屑瘤概念:以中等切削速度切削塑性金届常在刀尖附近长出一个“瘤”状硬质合金。
它是在第I变形区特定条件下产生特定条件:切削塑性金届;中等切削速度知屑瘤优点;积屑瘤附在刀尖上代替刀刃切削对刀刃有一定的保护作用;积屑瘤使实际工作前角增大。
切削变得轻快。
缺点:积屑瘤十生时灭使背吃刀量不断变化影响工件尺寸精度;积屑瘤在已加工表面上刻画不均匀的沟痕影响表面粗糙度Ra。
粗加工可以用积屑瘤保护刀尖故常采用中等切削速度加工;精加工应避免积屑瘤所以高速。
▲控制积屑瘤的措施:提高前刀面光滑度;提高工件硬度降低塑性;合理采用切削液;避开积屑瘤产生的速度范围。
4.表面变形强化和残余应力1.7加工精度和表面质量(零件机械加工质量)1.7.1加工精度概念P46分类:尺寸精度(标准公差等级为 20级)、形状精度、位置精度1.7.2表面质量厂表面几何形状精度:Ra、波度、纹理方向表面质量<一表面缺陷:表层加工硬化、表层残余内应力、表层金相组织影响表面粗糙度的主要因素:P48▲切削加工的阶段:粗加工、半精加工、精加工、精密加工、超精密加工。
注意各个阶段对切削的影响。
详细参看 P8表格九.零件加工原则机械加工工序的安排:基面先行(即先加工基准面在加工其他表面);②先面后孔;③先主后次④先粗后精零件加工中的阶段:粗---半精---精---超精+ .热处理的安排:在粗加工之前进行退火或正火半精加工之前粗加工之后进行调质或时效半精加工后进行淬火详细请见书本第八页.十一.为什么相同精度的孔比轴难加工成本高?答:因为孔的加工条件和外圆的加工条件不同加工孔的刀具刚度差排屑散热困难切削液不易进入切削区刀具易磨损成本高其次与轴加工相比孔的加工方法较多并且孔的形状尺寸相差很大,并且各项加工要求差别也很大因此孔的加工方案复杂的多.十二.车削的特点:1,切削过程比较平稳2,刀具简单3,易于保证工件各加工面的位置精度4,适应各种加工材料十三.铁、刨加工特点及应用(1)铢削(P290)可加工平面、沟槽、成型面和孔铢平面方式:端铢和周铁大平面用端铢。
其中端铢加工质量好于周铁;且生产效率高于周铁;但周铢适应性好于端铢。
铁削方式:顺铢(旋转方向和进给方向相同)和逆铢。
二者的选择:若铢床装有消除丝杆螺母间隙的机构或者精铢时可用顺铁;一般铢床没有上述机构特别是粗铁生产采用逆铢。
(2)刨铢(P31)可加工平面、沟槽、直线成型面等。
加工特点:通用性好;生产率低;加工质量低(3)铁、刨工艺特点和应用方面的比较(P32)加工质量一般同级均可达中等精度。
但加工大平面时刨削优于铢削。
生产率一股铢削高于刨削但加工窄长平面时刨削生产率高于铢削。
加工范围铢削比刨削广泛。
工时成本铢削高于刨削。
应用范围铢削比刨削广。
十四.常见表面的加工(1)外圆(P111)技术要求:尺寸精度、形状精度、位置精度、表面质量加工方法:车、磨、超精加工、研磨、抛光等(2)内孔(P113)技术要求:尺寸精度、形状精度、位置精度(与外圆要求不同)、表面质量加工方法:钻、扩、皎、车、鲤(用于大直径)、拉、磨、超精加工。
研磨和抛光等(3)平面(P115)技术要求:形状精度、位置尺寸及位置精度、表面质量加工方法:车、铁、刨、磨、刮、拉超精加工、研磨和抛光等(4)螺纹(P116)加工方法:车、铁、磨、攻、套、搓和滚等。
十五.齿轮的加工方法展成法:铢齿、拉齿和展成法磨齿成形法:滚齿、插齿、剃齿和成形法磨齿十六.基准(P192)厂①应选择不加工表面为粗准厂(1)设计基准②选择加工余量最小的表面< 为粗基准C粗基准③选表面尽可能平■整并且足够大的做粗基准基准< f定位基准]I④粗基准一般只在第一道工| 序中使用一次r①基准重合原则J '精基准J②基准统一原则V (2)制造基准|测量基准I③互为基准原则1④自为基准原则'装配基准十七.零件的安装和定位定位:在机床上加工工件时必须使工件在机床工作台或夹具上处丁某一正确的位置这一过程成为定位(定位中会出现完全定位、不完全定位、过定位、欠定位)。
、夹紧:将工件按定位位置夹牢、压紧的过程称为夹紧。
、安装:定位和夹紧统称为工件的安装。
、六点定位原理:要完全确定工件在机床上的位置要用分布适当的六个支撑点来限制工件的六个自由度这就是工件的六点定位原理(过定位与欠定位在工件安装过程中是不允许的但是不完全定位是提倡的)。
十八.零件的结构工艺性:零件所具有的结构是否便丁制造、装配和拆卸。
(P172-P184 的表格)。
十九.重要零件的机械加工过程:(盘套类零件、轴类零件P199、P202的表格中的工种、工序内容以及设备)二十.加工工艺方案:外圆内孔的加工方案并要把热处理穿插进去( P124以法兰盘为例)。