转炉炼钢的基本任务及原理(谷风参考)
转炉炼钢的基本任务及原理

脱碳反应的作用
脱碳反应除了调整钢液碳含量的作用 外,其反应产物CO气体的上浮排除 使得脱碳反应给炼钢带来独特的作用。
➢ 促进熔池成分﹑温度均匀; ➢ 提高化学反应速度; ➢ 降低钢液中的气体含量和夹杂物数量: ➢ 造成喷溅和溢出:
. 22
2.2.1 脱碳反应
转炉中的脱碳反应以间接氧化为主:(FeO)+[C]={CO}+Fe。这是一 个吸热反应,因此,熔池温度升高至1500℃左右后脱碳反应方能激烈 进行。
如:
2[O]+[Si]=(SiO2)
或 2(FeO)+[Si]=2Fe+(SiO2)
在渣-金界面上往往产生元素的间接氧化反
应。
. 18
2.1.4炼钢熔池中元素的氧化次序
溶解在铁液中的元素的氧化次序可以通过 与1molO2的氧化反应的标准吉布斯自由能 变化来判断。
在标准状态下,反应的ΔGo负值越多,该 元素被氧化的趋势就越大,则该元素就优 先被大量氧化。
氧化性——炉渣向金属熔池传氧的能力,一般以 渣中氧化铁( %∑ FeO)含量来表示。
把Fe2O3折合成FeO有两种计算方法:全氧法和全 铁法。全铁法较合理。
炉渣的氧化能力是个综合的概念,其传氧能力还 受炉渣粘度、熔池搅拌强度、供氧速度等因素的 影响。
. 11
1.3.4炉渣成分的变化规律
冶炼过程中,转炉中熔渣成分的变化规律大致如下:
. 5
1.2.2转炉里的氧气射流
3、射流的温度渐高 射流进入炉膛后被1450℃的炉气逐渐加
热,加之混入射流的炉气(CO)及金属滴被 氧化放热,使射流的温度逐渐升高。模拟实 验表明,距喷头孔径15~20倍处射流的温度 在1300~1600℃之间;距喷头孔径35~40倍 处射流的温度高达2150~2300℃,有人称转 炉里的氧气射流就象一个高温火炬。
转炉炼钢的冶炼原理

转炉炼钢的冶炼原理
转炉炼钢法:这种炼钢法使用的氧化剂是氧气。
把空气鼓入熔融的生铁里,使杂质硅、锰等氧化。
在氧化的过程中放出大量的热量(含1%的硅可使生铁的温度升高200摄氏度),可使炉内达到足够高的温度。
因此转炉炼钢不需要另外使用燃料。
转炉炼钢是在转炉里进行。
转炉的外形就像个梨,内壁有耐火砖,炉侧有许多小孔(风口),压缩空气从这些小孔里吹炉内,又叫做侧吹转炉。
开始时,转炉处于水平,向内注入1300摄氏度的液态生铁,并加入一定量的生石灰,然后鼓入空气并转动转炉使它直立起来。
这时液态生铁表面剧烈的反应,使铁、硅、锰氧化(FeO,SiO2 , MnO,) 生成炉渣,利用熔化的钢铁和炉渣的对流作用,使反应遍及整个炉内。
几分钟后,当钢液中只剩下少量的硅与锰时,碳开始氧化,生成一氧化碳(放热)使钢液剧烈沸腾。
炉口由于溢出的一氧化炭的燃烧而出现巨大的火焰。
最后,磷也发生氧化并进一步生成磷酸亚铁。
磷酸亚铁再跟生石灰反应生成稳定的磷酸钙和硫化钙,一起成为炉渣。
转炉的基本知识
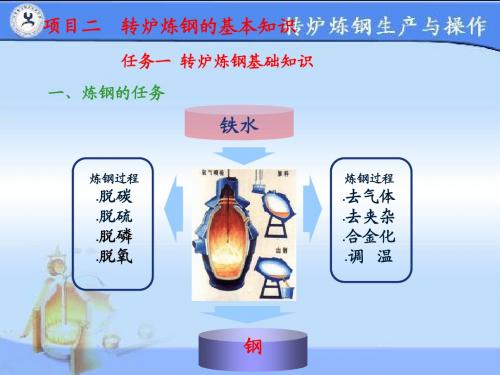
◆实际生产中为了脱磷怎样操作
实际生产中为了去磷, 实际生产中为了去磷,吹炼过程中应根据去磷反 应的热力学条件,首先搞好前期化渣( 应的热力学条件,首先搞好前期化渣(尽可能采用软 使用活性石灰;使用合成渣料), ),尽快形成高氧 吹;使用活性石灰;使用合成渣料),尽快形成高氧 化性炉渣,以利在吹炼前期低温去磷。若铁水磷含量 化性炉渣,以利在吹炼前期低温去磷。 还可在化好渣的情况下倒掉部分高磷炉渣, 高,还可在化好渣的情况下倒掉部分高磷炉渣,以提 高脱磷效率。而在吹炼中 后期, 吹炼中、 高脱磷效率。而在吹炼中、后期,则要控制好炉渣碱 ),保证磷稳定在炉渣中 度和渣中 (FeO),保证磷稳定在炉渣中,而不发生 ),保证磷稳定在炉渣中, 回磷现象。在吹炼前期快速降低, 回磷现象。在吹炼前期快速降低,进入吹炼中期略有 回升, 回升,而到吹炼后期再度降低
钢水
]+{O 氧气直接氧化) [Si]+{ 2}=( ]+{ }=(SiO2) (氧气直接氧化)
◆ Si氧化反应特点 氧化反应特点
低温有利于Si 低温有利于 的氧化 放热反应
Si氧化 氧化 特点 碱性渣中氧化很彻底
SiO2 主要与 主要与CaO结合成 结合成 稳定的2CaO.SiO2 稳定的
氧化图解 变化规律
总述
顶吹转炉炉内成分变化
复合吹炼转炉炉内成分变化
(一)金属液成分变化规律
氧化图解 变化规律
1、Si
氧化特点
◆
变化规律
在吹炼初期就大量氧化。在吹炼初期, 在吹炼初期就大量氧化 在吹炼初期,一 在吹炼初期
般在5分钟内就被氧化到很低,一直到吹炼终点, 般在 分钟内就被氧化到很低,一直到吹炼终点, 分钟内就被氧化到很低 也不发生硅的还原。 也不发生硅的还原。
转炉 原理

转炉原理
转炉是一种用来炼钢的设备,其原理是利用高温将原料中的杂质和不纯物质去除,从而得到高纯度的钢材。
转炉的操作过程可以大致分为两个阶段:吹炼和出钢。
在吹炼阶段,首先将底吹氧气和喷吹煤气混合物以高速吹入转炉中。
煤气在高温下燃烧,产生的热量使转炉内部的温度升高。
吹入的氧气则与煤气中的一部分碳反应生成一氧化碳和二氧化碳,同时释放出大量的热量。
这些燃烧和反应过程会形成一个高温高碳的还原区,也称为“焦墨区”。
焦墨区内的高温和高碳环境有助于将原料中的杂质和不纯物质还原为气体或脆性的固体物质,从而实现了炉内的净化作用。
炉内的搅拌装置会将炉内的材料搅拌均匀,促进反应的进行。
吹炼过程中,转炉的操作工人会根据炉内的温度和氧气供应量等参数进行调节,以控制反应的速度和程度。
一般来说,吹炼时间为20-30分钟左右。
吹炼结束后,开始进行出钢操作。
操作工人会逐渐停止底吹和喷吹,采取顶吹的方式将氩气或氮气吹入炉内,以稳定温度,并形成一个保护层,防止钢液的再次氧化。
在出钢过程中,操作工人会打开底部的钢水口,将炉内的钢液流出,并通过连铸设备进行凝固和成型。
同时,还会对钢液进
行取样分析,以确保钢材的质量达到要求。
总的来说,转炉通过高温和高碳环境以及氧气的吹入,实现了对原料中的杂质和不纯物质的去除,从而得到高纯度的钢材。
这种炼钢方式具有高效、灵活和环保等特点,广泛应用于钢铁行业。
转炉炼钢车间
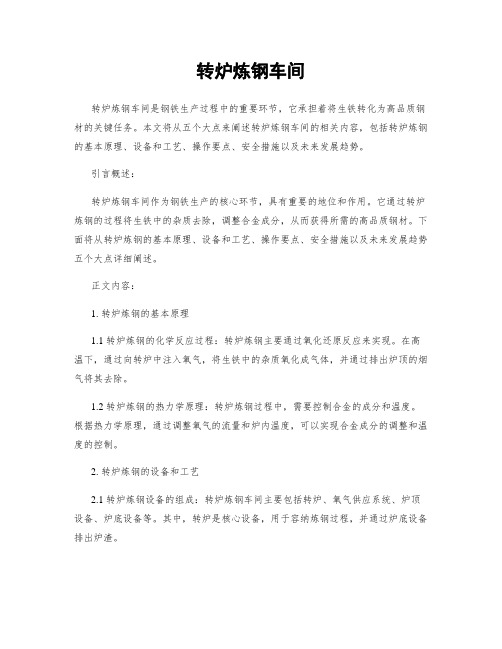
转炉炼钢车间转炉炼钢车间是钢铁生产过程中的重要环节,它承担着将生铁转化为高品质钢材的关键任务。
本文将从五个大点来阐述转炉炼钢车间的相关内容,包括转炉炼钢的基本原理、设备和工艺、操作要点、安全措施以及未来发展趋势。
引言概述:转炉炼钢车间作为钢铁生产的核心环节,具有重要的地位和作用。
它通过转炉炼钢的过程将生铁中的杂质去除,调整合金成分,从而获得所需的高品质钢材。
下面将从转炉炼钢的基本原理、设备和工艺、操作要点、安全措施以及未来发展趋势五个大点详细阐述。
正文内容:1. 转炉炼钢的基本原理1.1 转炉炼钢的化学反应过程:转炉炼钢主要通过氧化还原反应来实现。
在高温下,通过向转炉中注入氧气,将生铁中的杂质氧化成气体,并通过排出炉顶的烟气将其去除。
1.2 转炉炼钢的热力学原理:转炉炼钢过程中,需要控制合金的成分和温度。
根据热力学原理,通过调整氧气的流量和炉内温度,可以实现合金成分的调整和温度的控制。
2. 转炉炼钢的设备和工艺2.1 转炉炼钢设备的组成:转炉炼钢车间主要包括转炉、氧气供应系统、炉顶设备、炉底设备等。
其中,转炉是核心设备,用于容纳炼钢过程,并通过炉底设备排出炉渣。
2.2 转炉炼钢的工艺流程:转炉炼钢的工艺流程一般包括预热、装料、吹氧、炼钢和出钢等环节。
在各个环节中,需要严格控制时间、温度和氧气流量等参数,以确保炼钢过程的稳定性和高效性。
3. 转炉炼钢的操作要点3.1 转炉炼钢操作的准备工作:在进行转炉炼钢前,需要对设备进行检查和维护,确保其正常运行。
同时,还需要准备好炼钢所需的原料和辅助材料。
3.2 转炉炼钢操作的注意事项:在操作过程中,需要注意炉内温度和压力的变化,及时调整氧气流量和炉渣的排出速度。
同时,还要密切关注炼钢过程中的各项指标,确保炼钢质量的稳定和优良。
4. 转炉炼钢的安全措施4.1 转炉炼钢操作的安全要求:在转炉炼钢过程中,需要严格遵守安全操作规程,佩戴个人防护装备,确保人员的安全。
转炉炼钢炼钢工艺学
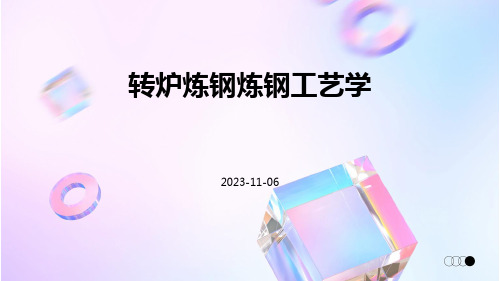
在钢的熔炼过程中,液态相变包括碳和其他合金元素的溶解 和扩散。这些相变过程受到温度、成分和其他因素的影响。
钢的纯净化原理
去除杂质
为了提高钢的纯度,需要去除铁水中的杂质,如硫、磷、氮等。这些杂质可 以通过造渣或添加脱氧剂等方式去除。
合金化
为了调整钢的成分和性能,需要向熔融的钢水中加入合金元素,如碳、硅、 锰等。这些元素可以通过合金铁块或废钢等方式添加。
02
转炉炼钢技术
转炉炼钢的工艺流程
装炉
将铁水、废钢等原材料装入炉内,形成铁水包和 废钢包。
熔化
通过高温加热铁水包和废钢包,将铁水和废钢熔 化为液态。
氧化
向熔化的铁水中吹入氧气,使其中的碳、硅、锰等 元素氧化生成气体,去除杂质。
脱碳
继续向熔化的铁水中吹入氧气,降低铁水中的碳含量, 使铁的含量增加。
炼技术等。
环保技术
采用炉气循环技术、烟气净化 技术等,减少废气排放,提高
环保水平。
炼钢工艺技术的智能化与自动化
智能化技术
采用人工智能、大数据分析等技术,实现对生产过程的智能监控、智能优化。例如,利用AI技术对炉况进行智 能诊断、智能推荐操作策略等。
自动化技术
通过自动化设备、仪表的运用,实现生产过程的自动化控制、操作。例如,采用自动加料系统、自动出钢系统 等。
调整成分
根据需要加入合金元素,调整铁水的成分以满足产品 要求。
出钢
将符合要求的铁水倒入钢包中,进行浇铸成钢坯。
转炉炼钢的原材料
铁水
由高炉或直接还原铁熔化而成,是转炉炼 钢的主要原料。
氧气
用于氧化反应,将铁水中的杂质氧化成气 体,提高铁水的纯度。
废钢
由报废的钢铁制品和加工过程中的余料组 成,作为添加元素加入到铁水中。
冶金安全生产技术(转炉炼钢)

转炉炼钢安全生产技术
操作流程:装料时,把炉体倾斜,先装入称量好 的废钢,接着装入铁水。然后使炉体直立,一边喷吹 氧气一边投入轧钢铁皮、石灰等辅助原料。用氧气喷 枪进行喷吹出现着火现象。后期,降下副枪测定铁水 中的碳浓度和温度,预测达到目标的时间,最后上升 氧枪,把炉体倒向装料侧,从炉口进行测温和取样, 再把炉体倒向出钢侧出钢。出钢后再把炉体倒向装料 侧排出渣。
转炉炼钢安全生产技术
(2)兑铁、加废钢时发生大喷的原因—— 均发生在 留渣作业
留渣操作中,若兑入铁水,炉内条件发生根本变 化,一方面铁水带来大量碳,另一方面铁水温度较低, 使炉内残留炉渣及钢水温度骤然下降,促进碳氧反应 的剧烈进行,就会发生“爆炸”性大喷。
转炉炼钢安全生产技术
(3)终点倾炉大喷原因 后吹时间长或由于操作不当,炉内尚在剧烈反应, 使大量钢渣外涌,形成喷溅。 补炉料粘结不牢,倾炉时突然塌落,造成钢渣猛烈 外涌性喷溅。 出钢或兑铁过程中炉衬大面积塌落。
转炉炼钢安全生产技术
三、重点危险因素的分析及对策 1、转炉氧枪坠落爆炸
转炉冶炼过程中C-O反应所需的氧气由氧枪提供, 反应过程中高温高达1700℃以上,为了防止氧枪烧坏, 氧枪均采取高压水冷却,但如果氧枪直接与高温液面接 触,即使有在冷却系统完好的情况下,氧枪也会被烧坏, 高压水击入高温液面下,形成爆炸。
转炉炼钢安全生产技术
预防转炉喷溅伤害的对策: ③吹炼中途加料,尽量采用小批次的办法,以避免熔 池温度明显降低,抑制碳氧反应而使渣中氧化铁升高。 ④炉渣不化,提枪化渣时,不能长时间高枪位吹氧, 否则,氧化铁大量增加,引起喷溅。一旦发生喷溅, 不能立即降枪,若此时降枪,脱碳反应更加激烈,反 会加剧喷溅。此时可适当提枪,一方面减缓脱碳反应, 另一方面借助氧气流股的机械冲击力冲击炉渣,使气 体排出,减轻炉渣发泡程度。如果是金属喷溅,可适 当提枪增加渣中氧化铁,另外加适量萤石,使炉渣快 速熔化覆盖钢液面。
转炉炼钢原理及工艺

转炉炼钢原理及工艺
转炉炼钢是通过加热合金材料,然后将其在氧气中抽出到转炉,形成一个旋转坩埚里,再使材料在转炉内不断熔化、混合、渣滓沉淀,达到钢的熔化和净化,最后冷却固化,即可获得均匀的高质量的钢的过程。
转炉炼钢的工艺路径主要包括:原料进炉、熔炼、净化、合金添加、出炉等步骤。
1、原料进炉:将碳钢和合金料装入转炉,加热至溶化温度,开始熔融。
2、熔炼:转炉内熔融的温度受多种因素的影响,如加料量、加料温度、炉气系统的平衡性、熔炼时间等。
3、净化:即清洁熔化渣滓,消除杂质,把金属液中的杂质置于渣滓中,让金属液纯度升高。
4、合金添加:将净化后的钢液入合金添加系统,加入合金钢料,使钢液按照要求的成分,营造钢种具有相应的技术性能。
5、出炉:金属液改变形态,冷却成指定的形状和尺寸,经过纯化后形成高质量钢。
- 1、下载文档前请自行甄别文档内容的完整性,平台不提供额外的编辑、内容补充、找答案等附加服务。
- 2、"仅部分预览"的文档,不可在线预览部分如存在完整性等问题,可反馈申请退款(可完整预览的文档不适用该条件!)。
- 3、如文档侵犯您的权益,请联系客服反馈,我们会尽快为您处理(人工客服工作时间:9:00-18:30)。
转炉所用氧枪采用拉瓦尔喷头,且尺寸按P出 /的P0展<开0.5和28衰3要减求慢设,计动,能通利常用M率高高达,1对.5熔~池2.2的,搅流拌股 力强。 2、射流的速度渐慢、截面积渐大
射流进入炉膛后,由于受反向气流(向上的 炉气)的作用而速度逐渐变慢;同时,由于吸收 部分炉气而断面逐渐变大,扩张角120左右。
经验学习 5
1.2.2转炉里的氧气射流
3、射流的温度渐高 射流进入炉膛后被1450℃的炉气逐渐加
热,加之混入射流的炉气(CO)及金属滴被 氧化放热,使射流的温度逐渐升高。模拟实 验表明,距喷头孔径15~20倍处射流的温度 在1300~1600℃之间;距喷头孔径35~40倍 处射流的温度高达2150~2300℃,有人称转 炉里的氧气射流就象一个高温火炬。
转炉炼钢的基本任务及原理
经验学习
董娟
1
转炉炼钢
转炉炼钢(converter steelmaking)是以铁水、废钢、 铁合金为主要原料,不借助外加能源,靠铁液本身的物理 热和铁液组分间化学反应产生热量而在转炉中完成炼钢过 程。
转炉按耐火材料分为酸性和碱性, 按气体吹入炉内的部位有顶吹、底吹和侧吹; 按气体种类为分空气转炉和氧气转炉。碱性氧气顶吹和顶
物; ➢ 废钢带入得泥沙和铁锈;氧化物或冷却
剂带入的脉石。 炉渣的组成以各种金属氧化物为主,并
含有少量硫化物和氟化物。 炼钢炉渣的基本体系是CaO-SiO2-FeO。
经验学习 10
1.3.3 炼钢炉渣的主要性质
碱度(basicity): R=1.3~1.5,低碱度渣; R=1.8~2.0,中碱度渣; R≥2.5,当向铁液中吹入氧气时,如果在铁液与气相 界面有被溶解的元素如[Si]﹑[Mn]﹑[C],虽有 大量的铁原子存在,但根据元素的氧化次序 [Si]﹑[Mn]﹑[C]将优先于铁而被氧化。
气泡对喷孔产生后座
喷入熔池的气体形成气泡时,残余气袋在距喷孔直 径二倍的地方受到液体的挤压而断裂,气相内回流压向喷 孔端面,这一现象称为气泡对喷孔的后座。
经验学习 7
1.3 转炉炼钢炉渣
1.3.1 炼钢炉渣的作用 1.3.2 炼钢炉渣的来源及其组成 1.3.3 炼钢炉渣的主要性质
经验学习 8
1.3.1 炼钢炉渣的作用
(2)(CaO):随着所加石灰的溶化,渣中的(CaO)含 量渐升至50% (中期因炉渣“返干”溶化很慢甚至停止)。
(3)(SiO2)和(MnO):吹炼初期,硅、锰的氧化使之浓 度很快分别达到20%和14%,而后随着所加石灰的熔化逐 渐降低至10%和6%。
经验学习 12
转炉冶炼的基本原理
物料平衡 热平衡
氧化性——炉渣向金属熔池传氧的能力,一般以 渣中氧化铁( %∑ FeO)含量来表示。
把Fe2O3折合成FeO有两种计算方法:全氧法和全 铁法。全铁法较合理。
炉渣的氧化能力是个综合的概念,其传氧能力还 受炉渣粘度、熔池搅拌强度、供氧速度等因素的 影响。
经验学习 11
1.3.4炉渣成分的变化规律
底复吹转炉由于其生产速度快、产量大,单炉产量高、成 本低、投资少,为目前使用最普遍的炼钢设备。 转炉主要用于生产碳钢、合金钢及铜和镍的冶炼。
经验学习 2
转炉炼钢图示
经验学习 3
1.1转炉炼钢的基本任务
炼钢的基本任务包括: 1.脱碳、脱磷、脱硫、脱氧; 2.去除有害气体和夹杂; 3.提高温度; 4.调整成分
经验学习 6
1.2.3底吹气体对熔池的作用
搅拌熔池
实际生产中,从底部喷入熔池的气流一般为亚音速, 除在喷嘴处可能存在一段连续流股外,喷入的气体将形成 大小不一的气泡并自动上浮。气泡群在上浮过程中,因压 力减小而膨胀,并驱动、抽引金属液向上运动,而后沿四 周炉壁向下,并补向中心,从而对熔池尤其是其底部产生 强烈的搅拌,
经验学习 13
2 转炉冶炼的基本反应
主要阐述转炉吹炼过程中的硅锰氧化、脱 碳、脱硫和脱磷等基本反应及熔体成分的 变化情况,为学习后面的工艺内容作好理 论准备。
硅锰的氧化、脱碳、脱硫和脱磷是炼钢的 基本反应,但在转炉炼钢中又有其特殊性。
经验学习 14
2.1转炉内的基本反应
一炉钢冶炼过程
从装料到出钢,倒 渣,转炉一炉钢的冶炼 过程包括装料、吹炼、 脱氧出钢、溅渣护炉和 倒渣几个阶段,如右图 所示。一炉钢的吹氧时 间通常为12-18min,冶 炼周期为40min左右。
炼钢过程通过供氧、造渣、加合金、搅拌、 升温等手段完成炼钢基本任务。 氧气顶吹转炉炼 钢过程,主要是降碳、升温、脱磷、脱硫以及脱 氧和合金化等高温物理化学反应的过程,其工艺 操作则是控制供氧、造渣、温度及加入合金材料 等,以获得所要求的钢液,并浇成合格钢钢锭或 铸坯。
经验学习 4
1.2.1转炉里的氧气射流
作用:
通过对炉渣成分、性能及数量的调整,可 以控制金属中各元素的氧化和还原过程;
向钢中输送氧以氧化各种杂质; 吸收钢液中的非金属夹杂物,并防止钢液
吸气(H、N)。 其它作用。如:保护渣。
副作用:侵蚀炉衬;降低金属收得率。
经验学习 9
1.3.2 炼钢炉渣的来源及其组成
炼钢炉渣的来源: ➢ 加入的各种造渣材料及被侵蚀炉衬; ➢ 炼钢中化学反应的产物:氧化物和硫化
经验学习 15
2.1.2炼钢熔池中氧的来源
氧的来源: ➢ 直接向熔池中吹入工业纯氧(>98%); ➢ 向熔池中加入富铁矿; ➢ 炉气中的氧传入熔池。
铁液中元素的氧化方式有两种:直接氧化 (direct oxidation)和间接氧化(indirect oxidation)。
经验学习 16
2.1.3直接氧化方式
冶炼过程中,转炉中熔渣成分的变化规律大致如下:
(1)(FeO):呈下凹弧形变化:吹炼初期,为了化渣枪 位较高,渣中的(FeO)含量高达28%(复吹为16%); 中期随脱碳进行(FeO)被大量消耗而逐渐降至12%以下 (太低,出现返干,复吹为6%);随着[C]的减少,脱碳 速度下降,(FeO)的浓度又渐升至15%(复吹为12%)。