木板来料检验标准
板材来料检验规范

4.平面度要求≤4mm
3.0+0/-0.16
冷
扎
板
1.0+0/-0.08
1.2+0/-0.09
1.其厚度尺寸要求用千分尺测量.
1.5+0/-0.10
2.对于板厚有特殊要求的,见技术要求.
2.0+0/-0.11
3.平面度要求≤4mm
2.5+0/-0.12
3.0+0/-0.13
≤28
≤35
单位:mm
8.板材宽度/长度公差要求(摘选GB/T708-2006)
公称厚度
宽度允许偏差
公称宽度
≤125
>125-250
>250-400
>400-600
>600
≤0.40
+0.3/-0
+0.6/-0
+0.3/-0
+1.5/-0
+2.0/-0
>0.40-1.0
+0.5/-0
+0.8/-0
+0.3/-0
板材来料检验指导书
文件名称:
板材检验指导书
文件编号:
页码:
1/5
版本/修改状态:
A/0
发布日期:
2019-1-12
1.目的
为检验员提供来料检验规则和检验方法,保证来料质量状况,从而稳定产品质量。
2.适用范围
本标准适用于本公司所有采购板材物料的检验。
3.检验工具
游标卡尺;千分尺;卷尺
4.用语定义
4.1表面缺陷:指表面裂纹、腐蚀斑点、折痕、压痕、摩擦痕、气泡、生锈、金属压入物、非金属压入物、脏污、色差等缺陷。
2.5 -0.05/-0.11
3.0 -0.05/-0.12
铝
板
木箱来料检验规范
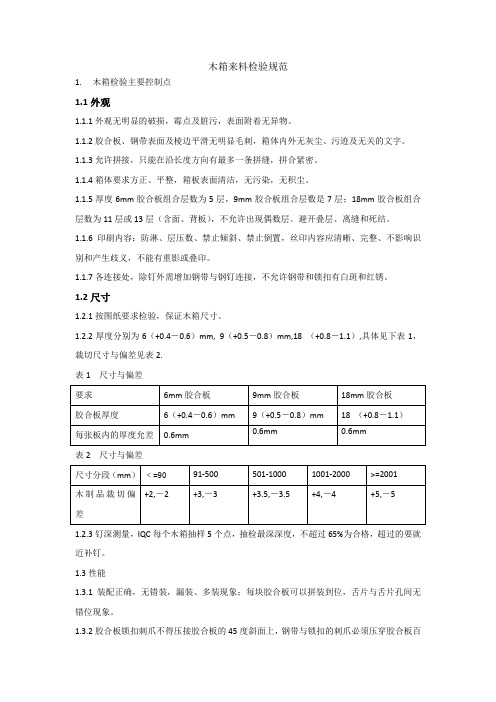
木箱来料检验规范
1.木箱检验主要控制点
1.1外观
1.1.1外观无明显的破损,霉点及脏污,表面附着无异物。
1.1.2胶合板、钢带表面及棱边平滑无明显毛刺,箱体内外无灰尘、污迹及无关的文字。
1.1.3允许拼接,只能在沿长度方向有最多一条拼缝,拼合紧密。
1.1.4箱体要求方正、平整,箱板表面清洁,无污染,无积尘。
1.1.5厚度6mm胶合板组合层数为5层,9mm胶合板组合层数是7层;18mm胶合板组合层数为11层或13层(含面、背板),不允许出现偶数层。
避开叠层、离缝和死结。
1.1.6印刷内容:防淋、层压数、禁止倾斜、禁止倒置,丝印内容应清晰、完整、不影响识别和产生歧义,不能有重影或叠印。
1.1.7各连接处,除钉外需增加钢带与钢钉连接,不允许钢带和锁扣有白斑和红锈。
1.2尺寸
1.2.1按图纸要求检验,保证木箱尺寸。
1.2.2厚度分别为6(+0.4-0.6)mm, 9(+0.5-0.8)mm,18 (+0.8-1.1),具体见下表1,裁切尺寸与偏差见表2.
表1 尺寸与偏差
尺寸与偏差
表2
近补钉。
1.3性能
1.3.1装配正确,无错装,漏装、多装现象;每块胶合板可以拼装到位,舌片与舌片孔间无错位现象。
1.3.2胶合板锁扣刺爪不得压接胶合板的45度斜面上,钢带与锁扣的刺爪必须压穿胶合板百
度,并有不小于0.5mm的折返长度。
1.3.3箱子内装500kg的货物,可满载堆叠4层,底层箱子至少能承受1500kg的栽荷。
附录A胶合板外观判定。
最新木材质量验收标准

最新木材质量验收标准
精品文档木材质量验收标准
1 适用范围
本标准适用玻璃成品包装用木材的进料检验。
2 引用标准
GB153.1 —84 、GB153.2 —84、GB1822.3 —84 GB155.1 —84 、
GB155.2—84、GB155.3 —84
3 木材种类
3.1 适用的木材种类有:马尾松、白松、红松、油松、马尾松、云南松、云衫、椴木。
3.2 所选用的包装板材应具有以下特性:强度高、握钉力强、不易劈裂和开裂、易干燥、不变形的树种,加工成型的板材,湿度应保持在20%以下。
在验收使用前须试用。
4 尺寸要求
4.1 尺寸公差
长度:+30mm -20mm 宽度:+2mm -2mm
厚度:> 20mm : + 2mm —2mm < 20mm : + 2mm —1mm
5 材质要求
5.1 腐朽:不允许(整批木材只允许有 1 0 %的发黑,但不能腐朽)。
5.2 裂纹:
任何板长方向的表面裂纹不得大于100mm,横向裂纹小于1mm,且每根木板上的裂纹不得超过 2 条;
5.3 夹皮:不允许
5.4带裂纹木材占整批木材的比例应小于10%;
5.5 边皮:不允许
5.6 树节:精品文档。
木材来料检验规范
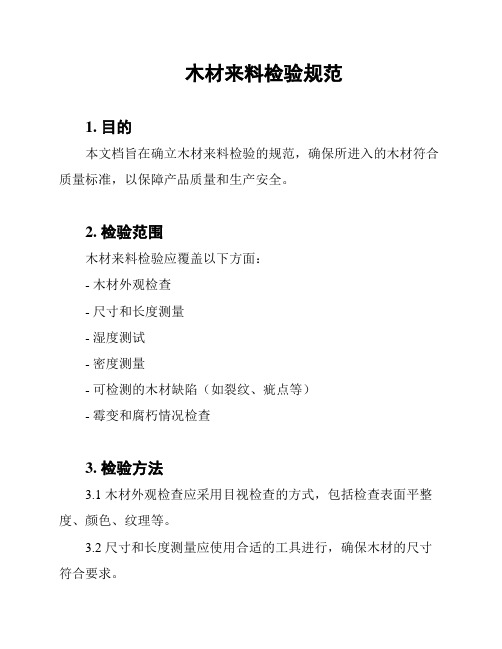
木材来料检验规范
1. 目的
本文档旨在确立木材来料检验的规范,确保所进入的木材符合质量标准,以保障产品质量和生产安全。
2. 检验范围
木材来料检验应覆盖以下方面:
- 木材外观检查
- 尺寸和长度测量
- 湿度测试
- 密度测量
- 可检测的木材缺陷(如裂纹、疵点等)
- 霉变和腐朽情况检查
3. 检验方法
3.1 木材外观检查应采用目视检查的方式,包括检查表面平整度、颜色、纹理等。
3.2 尺寸和长度测量应使用合适的工具进行,确保木材的尺寸符合要求。
3.3 湿度测试应使用适当的湿度计进行,确保木材的湿度在合
理范围内。
3.4 密度测量可采用非破坏性或破坏性的测量方法,以确定木
材的密度。
3.5 可检测的木材缺陷应通过仪器或人工检查,以确保木材没
有明显的缺陷。
3.6 霉变和腐朽情况检查应通过肉眼观察或者相关检测工具进行,以排除有害的霉变和腐朽木材。
4. 检验记录
每次木材来料检验都应做详细的检验记录,并保存至少一年,
以备查证和追溯需要。
5. 检验结果处理
5.1 若木材来料检验结果符合质量标准,可以接受并进入下一
步工序。
5.2 若木材来料检验结果不符合质量标准,应及时通知供应商,并协商解决方案。
6. 审核与更新
本文档应定期进行审查和更新,以适应木材来料检验技术的发展和公司需求的变化。
木材来料一般检验规范

陷、木材构造缺陷、伤疤(损伤)、木材加工缺陷、变形缺陷等。按实际情况
+0.5L+0.005L2+0.000125L(14-L)(D-10)〕2*10000确定; 式中:V—材积( M3 );L—检尺长( M );D—检尺径( CM )。 也可直接参照附表 GB4814—84《原木材积表》。 4品质标准及检验方法: 纵裂长度、外夹皮长度、弯曲水平长度、弯曲拱高、扭转倾斜高度、环裂半径、弧开裂
锯材中的节子个数是在检尺长内任意选择节子最多的1M 中查定 B 腐朽
在一个材面中存在数块腐朽时,不论其间距大小,均按各块的实际面积相加计算。 C 裂纹、夹皮(欠边)
彼此接近的裂纹,相隔不足5MM 的按整条裂纹计算; 相邻或相对的贯通裂纹,宽度在2MM 内不计,2MM 以上的检量裂纹全长。 夹皮(欠边)按裂纹计算。 D 虫洞 按虫洞最多的板面计算。 E 其它Байду номын сангаас
1
2
3
4
二
3
第
2
20
0
3
1
3
一
0
151
~280
第
2
40
3
4
4
5
二
0
第
3
32
1
3
2
5
一
2
281
~500
第
3
64
4
5
6
7
二
木材类检验标准
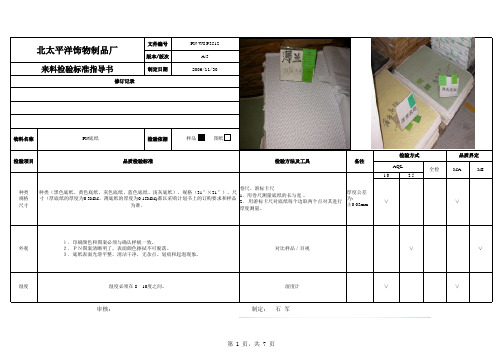
文件编号PN-WI-P3512版本/版次A/5制定日期2006/11/301.02.5外观∨∨∨审核: 制定: 石 军湿度湿度必须在 8---10度之间。
湿度计∨∨ 1.印刷颜色和图案必须与确认样板一致。
2.PN图案清晰明了,表面颜色擦拭不可脱落。
3.底纸表面光滑平整,清洁干净,无杂点、划痕和起泡现象。
对比样品/目视品质界定AQL全检MA MI种类规格尺寸种类(黑色底纸、黄色底纸、灰色底纸、蓝色底纸、浅灰底纸)、规格(31″×21″)、尺寸(厚底纸的厚度为0.3MM 、薄底纸的厚度为0.15MM)都以采购计划书上的订购要求和样品为准.卷尺、游标卡尺1.用卷尺测量底纸的长与宽 。
2. 用游标卡尺对底纸每个边取两个点对其进行厚度测量。
厚度公差为:±0.05mm ∨样品 图纸检验项目品质检验标准检验方法及工具备注检验方式北太平洋饰物制品厂来料检验标准指导书修订记录物料名称PN 底纸检验依据文件编号PN-WI-P3512版本/版次A/5制定日期2006/11/301.02.5外观TNU、MCE、MAP三个订单使用的莎比利纹路有区别。
∨∨审核:制定:石军材质颜色、纹路、材质必须与标准样品一致比对样品 / 目视、分色箱∨1.尼斯木皮、MCE、MAP订单中的莎比利要求有尼斯,其余的木皮不可有尼斯。
2.木皮表面不可有虫眼,死结疤,蓝斑,破裂。
3.木皮表面光滑平整。
4.白栓木皮的纹路宽度为3MM-6MM之间。
5.枫木雀眼的大小、稀密度同确认样板。
比对样品 / 目视品质界定AQL全检MA MI种类规格尺寸种类(直纹黑胡桃COA订单、山纹黑胡桃COR订单、直纹白栓MVD订单、黑檀MCH订单、直纹枫木SAF订单、细纹枫木FDG订单、桦木MAP订单、直纹橡木、橡胶木ULT订单、尼斯、黑铁木DIM订单、莎比利TNU、MCE、MAP订单、安格利ULT订单、枫木雀眼KAB订单、人造斑马纹MCE订单、人造红橡ESQ订单,规格)、尺寸都以采购计划书上的订购要求和样品为准。
木材来料检验(收货)指引

1.木材含水率
1.1预干板含水率要求:
1.1.1每批来料≤25m3,检测数量(随机抽样)不少于40块(根)。
1.1.2每批来料26 m3~50 m3,检测数量(随机抽样)不少于60块(根)。
1.1.3每批来料51 m3~80 m3,检测数量(随机抽样)不少于80块(根)。
1.1.4每批来料81 m3以上,检测数量(随机抽样)不少于100块(根)。
1.2湿木材不作含水率规定范围
1.3含水率要求
1.3.1楸木、椿(京)木含水率14%以下。
1.3.2橼木含水率25%以下。
1.4含水率超标处理
1.4.1每批木材检测数量中20%以内超过含水率要求(其中最高含水率值不能超过百分之五个点),可按预干板收货入库。
1.4.2每批木材检测数量中21%~50%超过含水率要求,每超一个百分点每立方米扣款5元。
1.4.3每批木材检测数量中51%以上超过含水率要求,整批按湿材入库。
2.验(量)尺工具、单位
2.1普通卷尺
2.2验(量)尺单位:mm(毫米)
3.材径要求
3.1楸木板自然宽要求>150mm,120mm≤可接受≤150mm(但不能列入A、B级),<120mm 拒收。
3.2椿(京)木板宽要求>130mm,100mm≤可接受≤130mm(但不能列入A、B级),<100mm拒收。
3.3橼木板自然宽要求>100mm,80mm≤可接受≤100mm(但不能列入A、B级),<80mm 拒收。
4.木材规格
4.1长度规格(预干板、湿材)。
木制家具质量检验标准

❖ 木材的检验标准
木材的颜色与 油漆颜色的关系 可接受的为√ 不可接受为×
❖ 实木备料检验标准
1. 对木材端裂的要进行打端头后再 断料,断料时选料对木材的利用和 品质的稳定起着很重要的作
2. 在断料操作过程中不可有起毛, 发黑,端头不成直角,角度不精准 等现象
3. 对于弯翘的料,如弯曲度不大要 过手压刨,注意手压刨之后的厚度 和宽度规格不能小于标准规格。
。 ❖ 产品表面包装前必须清除产品上的灰尘,舒美布必须确实能保护到产品 ❖ 严格按照包装设计标准进行包装,所有包装必须符合长途运输标准,包装完
成后内部配件不可有晃动,碰撞等现象 ❖ 五金,说明书,脚柱等配件必须齐全后才可以进行包装 ❖ 8. 所有油漆完成后需要包装的产品正面不可有以下缺点:粗糙,流油,桔皮
木制家具质量检验标准
2020年7月17日星期五
第一篇 进料检验
实木原材料 检验标准
❖ 1.所有木材含水率需控制在8到12之间。
❖ 2.木材厚度必须达到采购标准,误差不可超过 +2MM,否则列入下一规格计算。
❖ 3.木材弯曲以2M长不超过5MM为标准。
❖ 4.木材端裂以不超过20MM为准。
❖ 5.所有木材不可有面裂,内裂,虫孔,腐朽,黑 斑,严重色差,等现象,不可有边材现象。
8. 拼板料不可有错位,混拼,拼缝,色差,含水率偏差等 不良现象。
9. 四面刨在加工物料时规格必须符合要求,刀型与图纸相 符,需要一面砂光的加0.5MM余量,需要两面砂光的加 1MM余量
10. 四面刨在成型时不得有刀痕,发黑,撕裂等现象发生.
❖薄片加工检验标准
1.泊片裁切的纹路要符合设计要求, 其取料尺寸要与料单相符. 2.所有板料在开料时表面不允许有 划伤,碰伤,压伤等不良现象. 3.泊片的山纹和直纹的取舍取决于 客人的要求,产品的部件位置,产品设 计的需要. 4.泊片拼接时必须要严密,不可有乱 拼,重叠,拼缝,穿孔色差等现象. 5.泊片拼接时严格按照设计图和客 人要求,不可随意乱拼. 6.热压泊片时涂胶要均匀,胶压后产 品不可有鼓泡,脱胶,溢胶,压伤,重叠, 歪斜等不良现象.
- 1、下载文档前请自行甄别文档内容的完整性,平台不提供额外的编辑、内容补充、找答案等附加服务。
- 2、"仅部分预览"的文档,不可在线预览部分如存在完整性等问题,可反馈申请退款(可完整预览的文档不适用该条件!)。
- 3、如文档侵犯您的权益,请联系客服反馈,我们会尽快为您处理(人工客服工作时间:9:00-18:30)。
严重 1.无尺寸偏差要求项检验, 主要 均采用目测方法. 严重 2.有尺寸偏差要求项的检 主要 验,采用游标卡尺或钢卷尺 进行实测. 严重 主要 3.检验标记:对于不合格的 次要 木板,经返修后可以再使用 次要 的,在退回返修时必须用黑 色记号笔做出明显标记. 主要 主要 4.木板仿形检验:将划线皮 主要 样放置对应的木板面(划线 皮样上所注明的划线方向) 检验周边是否与皮样平齐. 主要 部分复杂板形对照确认样 品实测或重要部位对比. 主要 4.木板强度检验:单板听 声:用硬木棍敲击板面应 主要 为清脆的“咚咚”声为合 格,如声为“扑扑”的声 严重 响则内部脱胶分层为不合 格;连体板则将板反扣于 严重 地,人立板上用脚轻蹬板 主要 腰处,无破裂声为合格,或 板腰处着地,两手施力于板 两端无破裂声为合格,弹 性间距<6cm 严重 5.有客户特殊要求的冲击 和疲劳测试,应随机抽样送 专检机构测试,并提供测试 报告.
测 试
木板要可以 通过各项测 2.木板组立后要可以通过客户要求的冲击和疲劳测试 。 试 3.客户无特殊要求时,木板可以通过常规检测. 4.木板的湿度要达到要求(8-12度)。 文字标识要 1.木板的产品名称要正确。 正确 2.木板要与送货单上的产品一致。 1.木板边缘1.5CM以内不能有后加工孔。 木板的其它 2.木板不能偏厚,以免造成螺丝无法锁定。 要求要过到 3.木板不能使用松木(松木会渗油)。 要求 4.我司要求木板用蒸汽模压木板。 是否有防霉 1.确认没有防霉包。 包 2.确认无尚在侵蚀的昆虫,无贯通裂缝,腐朽材、树皮 。 备注:所有上述项目,目视很明显时全部视为严重问题
标 识
严重
其 它 要 求主要源自严重浙江安吉五星家具有限公司
木 板 来 料 检 验 标 准
检验项目 允收标准 等级 检验方法与标准
1.纵横交错(一层横一层竖)。 叠合方式是 2.各层板片厚薄均匀,没有明显断层现象。 否合格 3.板片厚薄均匀,不能出现偏差太大。 1.板片与板片之间不能有明显开胶、裂痕现象。 外 观 2.木板不能有发霉、打湿现象。 3.木板不能有未修边严重割物毛刺等不良。 表面是否有 4.板片必须双面层层上胶,绝不允许单面上胶。 明显不良 5.板片层数必须足够,如1.2CM厚则为9-11层。 6.退货木板再送贷时上面的黑漆必须处理干净。 7.木板使用的材质是否合格。 1.参照技术部标准尺寸,长、宽尺寸偏差正负0.3CM以 木板的尺寸 内(以上公差为实际产品允收为准)。 是否合格 2.参照技术部标准尺寸,厚度正0.1CM,负0.1CM。 规 格 1.木板的仿形要正确,与样板可以吻合,尺寸错位 0.3CM以内。 木板的仿形 2.放置在水平面上木板反翘(座0.3CM,背0.5CM)。 是否合格 3.木板的定位孔偏差在2MM以内。对角线尺寸偏差在 正0.3至负0.3cm以内 组 立 木板可以组 1.内外板组立反翘在3MM以内。 立 2.内外板组立弧度上下错位3MM以内。 1.木板要可以通过拉背、水平、垂直等客户要求的各 项测试。