轴加工工艺过程
输出轴机械加工工艺过程表及工序表

输出轴机械加工工艺过程表及工序表本文档旨在提供输出轴的机械加工工艺过程表及工序表,以帮助制造商了解加工输出轴的步骤和要求。
工艺过程表下面是加工输出轴的工艺过程表,包括每个步骤的说明和要求:工序表下面是加工输出轴的工序表,描述了每个工序的步骤和要求:工序 1: 确定材料步骤:1. 根据设计要求和产品规格,选择合适的材料。
2. 材料选择要考虑强度、耐磨性和耐腐蚀性等因素。
工序 2: 预处理步骤:1. 清洁输出轴的表面,确保无灰尘、油脂和其他杂质。
2. 对输出轴的表面进行磨削,以去除划痕和不均匀的表面。
工序 3: 车削步骤:1. 使用车床对输出轴进行外径和内孔的车削。
2. 确保车削后的尺寸和精度符合设计要求。
工序 4: 切割步骤:1. 使用切割工具对输出轴进行长度切割。
2. 确保切割后的长度符合设计要求。
工序 5: 淬火步骤:1. 将输出轴放入淬火设备中进行淬火处理。
2. 控制淬火温度和时间,以确保输出轴达到所需的硬度和韧性。
工序 6: 抛光步骤:1. 使用抛光工具对输出轴进行抛光处理。
2. 确保抛光后的表面光滑并且没有明显的瑕疵。
工序 7: 配件安装步骤:1. 根据设计要求,安装必要的配件,如轴承和齿轮等。
2. 确保配件安装牢固可靠。
工序 8: 质检步骤:1. 对加工好的输出轴进行质量检查。
2. 检查尺寸、表面质量和其他关键指标是否符合设计要求。
工序 9: 表面处理步骤:1. 根据需求进行表面处理,如镀铬、喷涂或其他特殊处理。
2. 确保表面处理均匀并且符合产品要求。
工序 10: 包装步骤:1. 将加工好的输出轴逐个包装。
2. 使用适当的包装材料,确保输出轴在运输和储存过程中不受损。
以上是输出轴的机械加工工艺过程表及工序表,供参考使用。
具体加工过程和要求请根据实际情况进行调整和确认。
曲轴的加工工艺流程
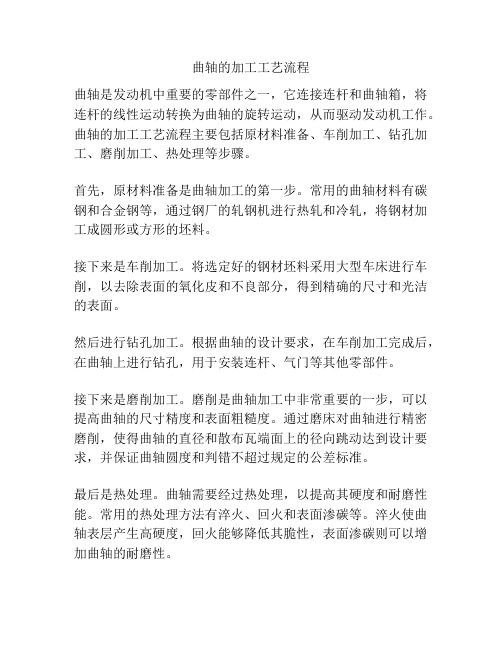
曲轴的加工工艺流程
曲轴是发动机中重要的零部件之一,它连接连杆和曲轴箱,将连杆的线性运动转换为曲轴的旋转运动,从而驱动发动机工作。
曲轴的加工工艺流程主要包括原材料准备、车削加工、钻孔加工、磨削加工、热处理等步骤。
首先,原材料准备是曲轴加工的第一步。
常用的曲轴材料有碳钢和合金钢等,通过钢厂的轧钢机进行热轧和冷轧,将钢材加工成圆形或方形的坯料。
接下来是车削加工。
将选定好的钢材坯料采用大型车床进行车削,以去除表面的氧化皮和不良部分,得到精确的尺寸和光洁的表面。
然后进行钻孔加工。
根据曲轴的设计要求,在车削加工完成后,在曲轴上进行钻孔,用于安装连杆、气门等其他零部件。
接下来是磨削加工。
磨削是曲轴加工中非常重要的一步,可以提高曲轴的尺寸精度和表面粗糙度。
通过磨床对曲轴进行精密磨削,使得曲轴的直径和散布瓦端面上的径向跳动达到设计要求,并保证曲轴圆度和判错不超过规定的公差标准。
最后是热处理。
曲轴需要经过热处理,以提高其硬度和耐磨性能。
常用的热处理方法有淬火、回火和表面渗碳等。
淬火使曲轴表层产生高硬度,回火能够降低其脆性,表面渗碳则可以增加曲轴的耐磨性。
以上就是曲轴的加工工艺流程。
在实际加工过程中,还需要仔细设计工艺路线,选择合适的加工设备和工具,保证每个加工步骤的精度和表面质量,以及严格控制每个加工步骤的尺寸公差,最终确保曲轴的质量和使用性能。
同时,加工过程中需要严格遵守安全操作规程,确保工人的人身安全和设备的正常运行。
双联齿轮轴机械加工工艺流程

双联齿轮轴机械加工工艺流程双联齿轮轴是一种机械零部件,其加工工艺流程包括数控编程、铣削、车削、热处理、齿轮加工和装配等关键步骤。
在制造过程中,需要严格按照工艺流程进行加工,以保证双联齿轮轴的质量和精度。
下面我们来详细介绍一下双联齿轮轴机械加工工艺流程。
一、数控编程数控编程是双联齿轮轴加工的第一步。
在这一阶段,需要根据零件的设计图纸和要求,利用CAD/CAM软件编写数控程序。
程序中包括了各种刀具的路径、切削速度、进给速度等参数,以及工件的加工坐标和工序顺序。
数控编程需要由经验丰富的技术人员完成,以确保程序的准确性和合理性。
二、铣削在数控编程完成后,就进入了实际的机械加工阶段。
首先是铣削工序,其目的是将工件的外形轮廓进行加工。
这一步需要使用数控铣床,根据编写好的程序,用不同的刀具进行切削。
在铣削过程中,需要根据工艺要求控制切削参数,如切削深度、进给速度等,确保加工出工件的精度和表面质量。
三、车削接下来是车削工序,车削主要用于加工双联齿轮轴的轴部。
同样需要使用数控车床,根据程序进行精确的切削。
车削工序中,需要根据工件的尺寸和形位公差,通过合理的切削参数和刀具选择,确保工件的几何形状和尺寸精度。
四、热处理热处理是双联齿轮轴加工的重要工序之一。
通过热处理,可以改善工件的组织结构和性能,增强其硬度和耐磨性。
对于双联齿轮轴来说,通常会采用渗碳淬火的热处理工艺,以保证工件的表面硬度和韧性。
热处理过程需要控制加热温度、保温时间和冷却速度,以确保工件获得良好的热处理效果。
五、齿轮加工双联齿轮轴的齿轮是其关键部件之一,齿轮加工是加工工艺流程中的重要环节。
通常采用滚齿和磨齿工艺,以确保齿轮的精度和平整度。
在齿轮加工过程中,需要控制加工工艺参数,如刀具的选择、切削速度、进给速度等,以获得良好的加工质量。
六、装配最后是双联齿轮轴的装配工序。
在装配过程中,需要将经过加工和热处理的各个部件进行组装,并进行必要的调试和检验。
装配过程需要严格按照装配图纸和工艺要求进行,以确保双联齿轮轴的功能和性能。
轴加工工艺流程

轴加工的工艺流程一般分为以下几个步骤:
1.材料准备:选择符合要求的轴材料,进行检查和准备,包括截
断、切割、去毛刺、清洗等工序。
2.粗加工:将轴材料进行粗加工,包括车削、钻孔、铣削、刨削
等工序,依据轴的形状和尺寸要求进行,以保证轴的几何形状和表面粗糙度满足要求。
3.热处理:对轴进行热处理,包括淬火、回火、正火等工序,提
高轴的硬度、强度和耐磨性,以及改善轴的组织结构和性能。
4.精加工:对轴进行精加工,包括磨削、抛光、拉削、滚压等工
序,使轴的表面精度和光洁度达到要求,同时保证轴的尺寸精度和形状公差符合要求。
5.表面处理:对轴进行表面处理,包括喷涂、电镀、镀铬、喷砂
等工序,以提高轴的表面质量和防腐性能。
6.检验:对轴进行质量检验,包括尺寸测量、表面检查、硬度测
试等,以保证轴的质量符合要求。
7.包装:对轴进行包装,包括防潮、防锈、防震等措施,以确保
轴在运输和存储过程中不受损坏。
以上是轴加工的一般工艺流程,具体的步骤和顺序可能会根据轴的材料、形状和尺寸要求而有所不同。
轴类零件加工工艺过程【详解】

轴类零件加工工艺过程内容来源网络,由“深圳机械展(11万㎡,1100多家展商,超10万观众)”收集整理!更多cnc加工中心、车铣磨钻床、线切割、数控刀具工具、工业机器人、非标自动化、数字化无人工厂、精密测量、3D打印、激光切割、钣金冲压折弯、精密零件加工等展示,就在深圳机械展.轴类零件是常见的零件之一。
按轴类零件结构形式不同,一般可分为光轴、阶梯轴和异形轴三类;或分为实心轴、空心轴等。
它们在机器中用来支承齿轮、带轮等传动零件,以传递转矩或运动。
台阶轴的加工工艺较为典型,反映了轴类零件加工的大部分内容与基本规律。
下面就以减速箱中的传动轴为例,介绍一般台阶轴的加工工艺。
1.零件图样分析图A-1 传动轴图A-1所示零件是减速器中的传动轴。
它属于台阶轴类零件,由圆柱面、轴肩、螺纹、螺尾退刀槽、砂轮越程槽和键槽等组成。
轴肩一般用来安装在轴上零件的轴向位置,各环槽的作用是使零件装配时有一个正确的位置,并使加工中磨削外圆或车螺纹时退刀方便;键槽用于安装键,以传递转矩;螺纹用于安装各种锁紧螺母和调整螺母。
根据工作性能与条件,该传动轴图样(图A-1)规定了主要轴颈M,N,外圆P、Q以及轴肩G、H、I有较高的尺寸、位置精度和较小的表面粗糙度值,并有热处理要求。
这些技术要求必须在加工中给予得到确保。
因此,该传动轴的关键工序是轴颈M、N和外圆P、Q的加工。
2.确定毛坯该传动轴材料为45钢,因其属于一般传动轴,故选45钢可满足其要求。
本例传动轴属于中、小传动轴,并且各外圆直径尺寸相差不大,故选择¢60mm的热轧圆钢作毛坯。
3.确定主要表面的加工方法传动轴大都是回转表面,主要采用车削与外圆磨削成形。
由于该传动轴的主要表面M、N、P、Q的公差等级(IT6)较高,表面粗糙度Ra值(Ra=0.8 um)较小,故车削后还需磨削。
外圆表面的加工方案(参考表A-3)可为:粗车→半精车→磨削。
4.定位基准合理地选择定位基准,对于零件的尺寸和位置精度有着决定性的作用。
轴的加工工艺过程及其简

轴的加工工艺过程及其简
轴的加工工艺过程包括以下几个步骤:
1. 材料准备:选择合适的轴材料,根据产品的要求进行切割、锯切等预处理工作。
2. 车削加工:采用车床等设备对轴进行车削加工,主要包括粗车、精车、修整等工序,使轴的外径和长度达到设计要求。
3. 镟削加工:通过镟床对轴的内孔进行加工,以确保轴的内外径的误差在允许范围内。
4. 磨削加工:使用磨床对轴的表面进行磨削加工,以提高轴的表面光洁度和精度。
5. 淬火处理:对已经加工完成的轴进行淬火处理,以增加轴的硬度和耐磨性。
6. 硬车处理:使用硬车床对轴进行硬车加工,以确保轴的垂直度和平行度等精度要求。
7. 钻孔加工:对轴进行钻孔加工,以便安装其他零件或采取其他应用需求。
8. 表面处理:对轴的表面进行除锈、抛光、喷涂等处理工艺,以增加轴的美观度和防腐性能。
轴的加工工艺过程可以根据实际情况进行调整和补充,具体操作时需根据产品的要求和加工的设备条件进行选择。
曲轴加工工艺流程
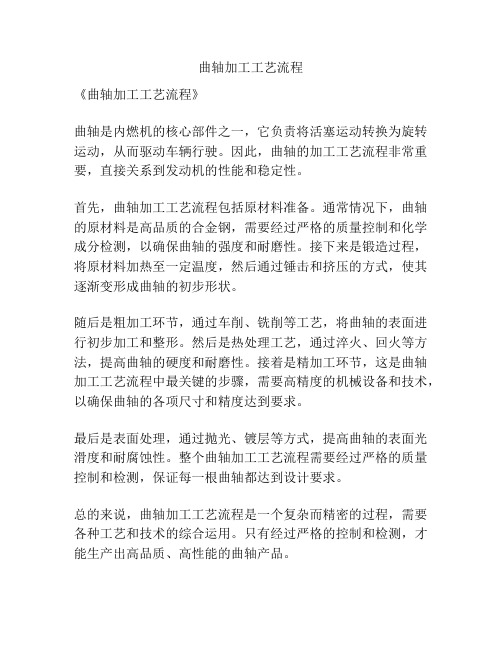
曲轴加工工艺流程
《曲轴加工工艺流程》
曲轴是内燃机的核心部件之一,它负责将活塞运动转换为旋转运动,从而驱动车辆行驶。
因此,曲轴的加工工艺流程非常重要,直接关系到发动机的性能和稳定性。
首先,曲轴加工工艺流程包括原材料准备。
通常情况下,曲轴的原材料是高品质的合金钢,需要经过严格的质量控制和化学成分检测,以确保曲轴的强度和耐磨性。
接下来是锻造过程,将原材料加热至一定温度,然后通过锤击和挤压的方式,使其逐渐变形成曲轴的初步形状。
随后是粗加工环节,通过车削、铣削等工艺,将曲轴的表面进行初步加工和整形。
然后是热处理工艺,通过淬火、回火等方法,提高曲轴的硬度和耐磨性。
接着是精加工环节,这是曲轴加工工艺流程中最关键的步骤,需要高精度的机械设备和技术,以确保曲轴的各项尺寸和精度达到要求。
最后是表面处理,通过抛光、镀层等方式,提高曲轴的表面光滑度和耐腐蚀性。
整个曲轴加工工艺流程需要经过严格的质量控制和检测,保证每一根曲轴都达到设计要求。
总的来说,曲轴加工工艺流程是一个复杂而精密的过程,需要各种工艺和技术的综合运用。
只有经过严格的控制和检测,才能生产出高品质、高性能的曲轴产品。
轴加工工艺过程

轴加工工艺过程
外圆表面粗加工(以顶尖孔定位)→外圆表面半精加工(以顶尖孔定位)→钻通孔(以半精加工过的外圆表面定位)→锥孔粗加工(以半精加工过的外圆表面定位,加工后配锥堵)→外圆表面精加工(以锥堵顶尖孔定位)→锥孔精加工(以精加工外圆面定位)。
当主要表面加工顺序确定后,就要合理地插入非主要表面加工工序。
对主轴来说非主要表面指的是螺孔、键槽、螺纹等。
这些表面加工一般不易出现废品,所以尽量安排在后面工序进行,主要表面加工一旦出了废品,非主要表面就不需加工了,这样可以避免浪费工时。
但这些表面也不能放在主要表面精加工后,以防在加工非主要表面过程中损伤已精加工过的主要表面。
对凡是需要在淬硬表面上加工的螺孔、键槽等,都应安排在淬火前加工。
非淬硬表面上螺孔、键槽等一般在外圆精车之后,精磨之前进行加工。
主轴螺纹,因它与主轴支承轴颈之间有一定的同轴度要求,所以螺纹安排在以非淬火-回火为最终热处理工序之后的精加工阶段进行,这样半精加工后残余应力所引起的变形和热处理后的变形,就不会影响螺纹的加工精度。
- 1、下载文档前请自行甄别文档内容的完整性,平台不提供额外的编辑、内容补充、找答案等附加服务。
- 2、"仅部分预览"的文档,不可在线预览部分如存在完整性等问题,可反馈申请退款(可完整预览的文档不适用该条件!)。
- 3、如文档侵犯您的权益,请联系客服反馈,我们会尽快为您处理(人工客服工作时间:9:00-18:30)。
CA6140
专用夹具
外圆车刀
轴线基准
7
精车
精车外圆∮55mm*50mm,精车15°的锥面,精车的外圆∮60.3m,精车∮75mm端面使两台阶总长保持148mm,锥面到∮75mm端面98mm,切槽4mm*1mm,倒角C1俩个;调头,精车外圆∮55mm*50mm,精车15°的锥面,精车的外圆∮60.3m,精车∮75mm端面使两台阶总长保持148mm,锥面倒∮75mm端面98mm,倒角C1俩个,切槽4mm*1mm
卧式车床
CA6140
专用夹具
外圆车刀
轴线基准
4
热处理
调质处理HB240~280
5
钳工
修研两端中心孔
6
半精车
半精车外圆∮55.5mm*50mm,半精车15°的锥面。半精车∮60.5mm使两台阶总长147mm,半精车∮75mm端面使台阶总长147.5mm,调头,半精车外圆∮55.5mm*50mm,半精车15°的锥面。半精车∮60.5mm使两台总长147mm,半精车∮75mm端面使台阶总长147.5mm
轴加工工艺过程
阶梯轴加工工艺过程
工序号
工序名称
工序内容
设备
夹具
刀具
基准
名称
型号
名称
名称
名称
1
下料
∮75mm*710mm 45钢棒料
2
粗车
车∮75mm端面见平,钻中心孔;调头车同你端面保证总长为700mm,钻中心孔
卧式车床
CA6140
专用夹具
端面车刀
中心钻
轴线基准
3
粗车
粗车外圆∮63mm*145mm,粗车外圆∮58mm*50mm,调头,粗车外圆∮63mm*145mm,粗车外圆∮58mm*50mm
卧式车床
CA6140
专用夹8
钳工
修研中心孔
9
磨削
磨削外圆∮60mm,调头,磨削外圆∮60mm
万能磨床
GD-6025
专用夹具
砂轮
轴线基准
10
铣削
用铣模铣削槽(14+0.2)mm*(12-0.2)mm;调头,铣另一个槽。铣32mm*10mm的深槽;调头,铣另一个。
卧式铣床
卧式车床
CA6140
专用夹具
麻花钻
丝锥
轴线基准
13
钳工
去毛刺
14
检验
X6020
专用夹具
三面刃铣刀
轴线基准
11
钻削
用钻模钻∮6mm的孔在圆柱面上,使其中心面与端面长100+0.5mm,深30mm。调头,钻另一个孔。钻∮6mm的孔在轴端面上,使其孔底与端面为100+0.5mm,调头,钻同样一个孔。
立式钻床
卧式钻床
Z526
专用夹具
麻花钻
轴线基准
12
车削
在端面上∮6mm的孔内车削的内螺纹,深度为15mm,调头,车削同样的螺纹。