2015年-2016年工伤事故分析报告
工伤事故分析报告
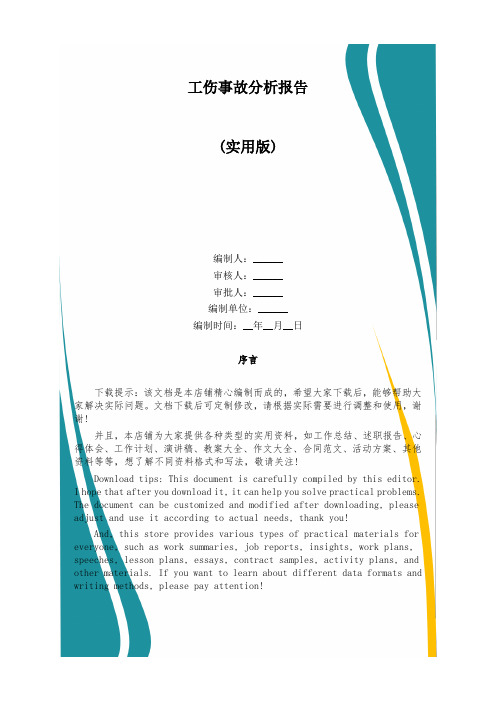
工伤事故分析报告(实用版)编制人:______审核人:______审批人:______编制单位:______编制时间:__年__月__日序言下载提示:该文档是本店铺精心编制而成的,希望大家下载后,能够帮助大家解决实际问题。
文档下载后可定制修改,请根据实际需要进行调整和使用,谢谢!并且,本店铺为大家提供各种类型的实用资料,如工作总结、述职报告、心得体会、工作计划、演讲稿、教案大全、作文大全、合同范文、活动方案、其他资料等等,想了解不同资料格式和写法,敬请关注!Download tips: This document is carefully compiled by this editor.I hope that after you download it, it can help you solve practical problems. The document can be customized and modified after downloading, please adjust and use it according to actual needs, thank you!And, this store provides various types of practical materials for everyone, such as work summaries, job reports, insights, work plans, speeches, lesson plans, essays, contract samples, activity plans, and other materials. If you want to learn about different data formats and writing methods, please pay attention!工伤事故分析报告工伤事故分析报告(通用3篇)工伤事故分析报告篇1关于煤机公司申某X意外事故的调查调查时间:X年X月X日星期X18:10调查人员:发展中心:王、郑、刘X公司安全部:刘X调查内容:XX车间工伤事故事故发生时间:事故发生地点:当事人:郭某、申某、牛某负责人:车间主任——申某安全部负责人——刘X事故处理:事故发生当天早上5:30左右,事故发生后相关负责人等第一时间将伤者送往东胜中心医院接受治疗。
工伤事故分析报告 (4)

工伤事故分析报告1. 引言工伤事故是指在工作过程中,由于人身意外事故导致工人受伤或丧失劳动能力的事件。
工伤事故对劳动者和企业都带来了极大的损失,因此分析工伤事故的原因和趋势对于预防事故的发生具有重要意义。
本报告将对工伤事故进行分析,并提出相应的预防措施。
2. 数据收集与分析为了深入了解工伤事故的情况,我们收集了过去一年内发生的工伤事故的相关数据。
以下是对这些数据的分析结果。
2.1 事故类型分析通过对事故类型的分类统计,我们得出了如下结果:•机械伤害:占总事故数的40%•坠落伤害:占总事故数的30%•电击伤害:占总事故数的20%•化学伤害:占总事故数的10%可以看出,机械伤害和坠落伤害是发生频率最高的两类工伤事故。
2.2 事故发生地点分析根据事故发生地点的统计结果,我们得出了以下结论:•车间事故:占总事故数的50%•建筑工地事故:占总事故数的30%•办公室事故:占总事故数的20%事故最容易发生的地点是车间,其次是建筑工地,办公室事故相对较少。
2.3 事故造成的伤害程度分析根据伤害程度的统计数据,我们得出了以下结论:•轻伤:占总事故数的50%•重伤:占总事故数的30%•死亡:占总事故数的20%大部分事故造成的是轻伤,但也有一定数量的重伤和死亡事故发生。
3. 原因分析为了找出工伤事故发生的原因,我们对每个事故案例进行了详细的调查和分析。
以下是我们总结出的主要原因:•机械维护不当•安全设施缺失•工人培训不足•操作不规范•管理不到位这些原因在多起事故中都有出现,说明了事故发生的根本原因是管理和操作方面的问题。
4. 预防措施为了避免工伤事故的发生,我们提出了以下预防措施:•加强机械设备的维护保养,确保设备运行正常;•安全设施的完善,包括安全护栏、防护板等;•加强对工人的培训,使其熟悉相关操作规程;•制定并执行严格的操作规范;•强化管理措施,建立健全的安全管理体系。
通过采取以上措施,我们可以有效降低工伤事故的发生概率,并保障劳动者的安全和生命健康。
工伤事故报告范文
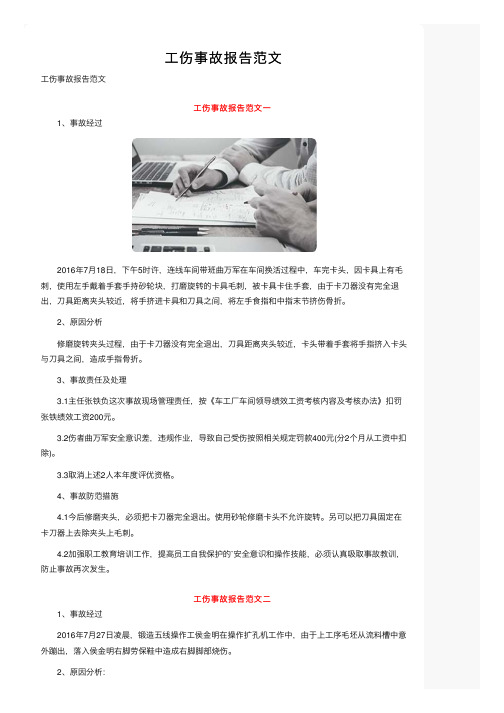
⼯伤事故报告范⽂⼯伤事故报告范⽂ ⼯伤事故报告范⽂⼀、事故经过 1 2、原因分析 修磨旋转夹头过程,由于卡⼑器没有完全退出,⼑具距离夹头较近,卡头带着⼿套将⼿指挤⼊卡头与⼑具之间,造成⼿指⾻折。
3、事故责任及处理 3.1主任张铁负这次事故现场管理责任,按《车⼯⼚车间领导绩效⼯资考核内容及考核办法》扣罚张铁绩效⼯资200元。
3.2伤者曲万军安全意识差,违规作业,导致⾃⼰受伤按照相关规定罚款400元(分2个⽉从⼯资中扣除)。
3.3取消上述2⼈本年度评优资格。
4、事故防范措施 4.1今后修磨夹头,必须把卡⼑器完全退出。
使⽤砂轮修磨卡头不允许旋转。
另可以把⼑具固定在卡⼑器上去除夹头上⽑刺。
4.2加强职⼯教育培训⼯作,提⾼员⼯⾃我保护的`安全意识和操作技能,必须认真吸取事故教训,防⽌事故再次发⽣。
⼯伤事故报告范⽂⼆ 1、事故经过 2016年7⽉27⽇凌晨,锻造五线操作⼯侯⾦明在操作扩孔机⼯作中,由于上⼯序⽑坯从流料槽中意外蹦出,落⼊侯⾦明右脚劳保鞋中造成右脚脚部烧伤。
2、原因分析: 设备存在安全隐患,没有被及时处理,流料槽挡铁过低,上⼯序⽑坯意外从流料槽中蹦出;同时事故⼈员劳保鞋⽆鞋带处于敞开状态,不正确穿戴劳保⽤品,造成热⽑坯掉⼊鞋内,造成脚部灼伤。
3、事故责任及处理 3.1⼚长助理韩⼩五、线长翟战芳负这次事故现场管理责任,按《锻造⼚安全⽂明⽣产考核办法》扣罚韩⼩五、翟占芳绩效⼯资200元。
3.2伤者侯⾦明安全意识差,导致⾃⼰受伤按照相关规定罚款300元。
3.3取消上述3⼈本年度评优资格。
4、事故防范措施 4.1检查各⽣产线流料槽挡铁⾼度,不合格进⾏更换。
4.2加强职⼯教育培训⼯作,提⾼员⼯⾃我保护的安全意识。
正确穿戴好劳保⽤品,每天各线线长班前会对员⼯劳保穿戴进⾏检查。
阅读延伸》》⼯伤事故申报流程 ⼀、当事⼈发⽣⼯伤后,需24⼩时内在⼈⼒资源部进⾏备案,并附⼯伤发⽣情况说明(时间,地点,经过,就医情况,是否有⼈垫付医疗费⽤等信息); ⼆、⼈⼒资源部接到备案后,48⼩时内(节假⽇顺延)向⼯伤部门提交“⼯伤事故登记表”,进⾏备案; 三、当事⼈在发⽣⼯伤后⼀个⽉内,向⼈⼒资源部提交如下相关材料: 1、当事⼈⾝份证复印件; 2、医院病历复印件; 3、夜班排班表(仅上夜班⼈员提交); 4、交通事故认定书、民事赔偿调解书(附各项赔偿明细)上下班路线图、上下班时间表/排班表(仅发⽣交通事故⼈员提交); 四、⼈⼒资源部将相关材料提交⼯伤认定部门,等待社保局⼯伤科审核; 五、⼯伤认定部门通知⼈⼒资源部审核结果,⼈⼒资源部通知当事⼈提交报销医疗费⽤所需如下材料: 1、⼯伤医疗费⽤清单; 2、药费原始凭证、病历; 3、住院、治疗费⽤(总费⽤清单); 4、出院⼩结; 5、内置钢板、钢钉需医院提供的内置材料条形码(仅有此项治疗的当事⼈提交); 六、⼈⼒资源部将材料提交⼯伤部门进⾏费⽤报销审核,等待审核结果; 七、查询费⽤报销审核结果,将报销费⽤通过财务部转⼊当事⼈银⾏账户。
工伤事故分析报告
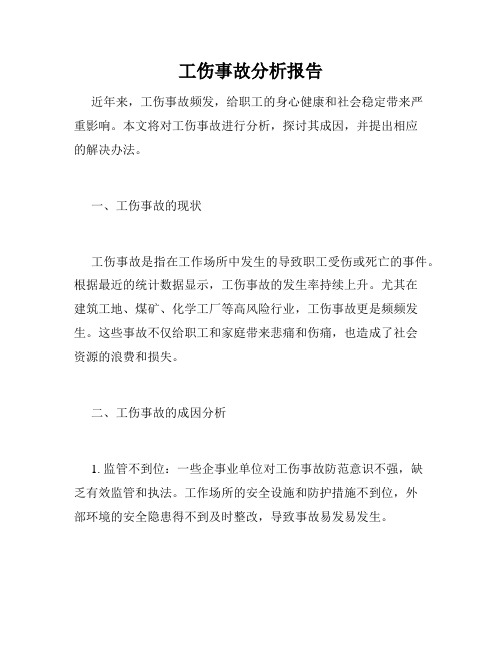
工伤事故分析报告近年来,工伤事故频发,给职工的身心健康和社会稳定带来严重影响。
本文将对工伤事故进行分析,探讨其成因,并提出相应的解决办法。
一、工伤事故的现状工伤事故是指在工作场所中发生的导致职工受伤或死亡的事件。
根据最近的统计数据显示,工伤事故的发生率持续上升。
尤其在建筑工地、煤矿、化学工厂等高风险行业,工伤事故更是频频发生。
这些事故不仅给职工和家庭带来悲痛和伤痛,也造成了社会资源的浪费和损失。
二、工伤事故的成因分析1. 监管不到位:一些企事业单位对工伤事故防范意识不强,缺乏有效监管和执法。
工作场所的安全设施和防护措施不到位,外部环境的安全隐患得不到及时整改,导致事故易发易发生。
2. 职工意识不强:一些职工自身安全意识不足,对于工作中的潜在危险缺乏足够的预防意识。
在工作中违章操作、使用不符合标准的工具设备等行为屡见不鲜,从而增加了工伤事故发生的可能性。
3. 经营利益压力:在以经济利益为导向的公司中,为了追求更高的利润,一些企业会忽视安全生产问题。
他们可能不安排充足的培训、不提供足够的安全设备,进而给职工带来安全隐患。
4. 技术条件滞后:在一些产业中,技术条件过于陈旧,设备维护保养不到位,存在着潜在的安全隐患。
特别是在高风险行业,技术条件滞后可能导致设备故障频发,从而引发工伤事故。
三、工伤事故的解决办法1. 加强监管体系:政府部门应加大对企事业单位的监管力度,确保相关安全法规的落实。
同时,也要建立联合执法机制,加大对违法企业的惩罚力度,形成强有力的监管体系。
2. 提高职工安全意识:企业应加强职工的安全培训和教育,提高职工的安全防范意识。
可以通过定期安全培训、安全知识宣传、事故案例分享等方式,让职工了解工作中的安全风险和如何避免事故的发生。
3. 增加经济补偿:政府应建立健全的工伤保险制度,提高工伤赔偿金标准,为工伤职工提供更有力的保护。
此外,企业也应建立自己的工伤补偿机制,提高职工的安全保障意识。
4. 加强技术创新:在高风险行业中,企业应加大科技研发投入,提升技术条件和设备质量。
年度工伤分析报告模板

年度工伤分析报告模板年度工伤分析报告一、工伤情况概述本年度,共发生XX起工伤事故,造成XX人死亡,XX人重伤,XX人轻伤。
工伤事故整体呈现下降趋势,但仍然存在一定的安全隐患。
二、工伤原因分析1. 人为原因:人为操作不合规范、操作不当、违反工作纪律等是工伤事故的主要原因。
对此,应对员工进行持续的安全教育和培训,强化工作纪律意识,提高员工的安全操作技能。
2. 设备原因:设备故障、维护不当、老化等因素也是工伤事故的重要原因。
对于老化的设备,应及时更换或修理,加强日常维护工作,确保设备的正常运行。
3. 环境原因:工作环境不良,包括通风不好、照明不足、地面湿滑等,也容易引发工伤事故。
对于这些环境问题,应及时进行整改,并制定相关的安全规范,确保员工的工作环境安全。
三、工伤部位分析1. 身体部位:头部、上肢和下肢是工伤事故中最容易受伤的部位。
这些部位的伤害往往会对员工的工作和生活造成较大的影响。
在具体工作中,应加强对这些部位的防护,提高员工的安全防护意识。
2. 内脏部位:内脏器官的损伤也是工伤事故中的重要伤害类型,如头部和胸部的撞击伤、内脏挤压伤等。
对于从事高风险职业的员工,应加强相关防护措施,减少内脏损伤的发生。
四、工伤年龄分析年轻员工是工伤事故的高发群体,其中18-29岁的员工占比最高。
主要原因是缺乏安全意识和工作经验。
针对这一情况,应加强对于年轻员工的安全教育,提高他们的安全防护意识和工作技能。
五、工伤性质分析1. 机械伤:机械设备的操作和维护是造成机械伤事故的主要原因。
要加强对机械设备的安全检查,提高员工的机器操作技能。
2. 高处坠落伤:工人在高空作业时没有正确使用安全带或护栏,或者作业平台没有进行足够的安全保护,容易发生高处坠落事故。
应建立高空作业的具体规范和操作程序,确保员工的安全作业。
六、工伤预防措施1. 加强安全教育培训,提高员工的安全意识和操作技能。
2. 定期检查设备并进行维护,确保设备的正常运行。
工伤事故分析报告5篇

工伤事故分析报告工伤事故分析报告5篇随着个人的文明素养不断提升,报告与我们愈发关系密切,我们在写报告的时候要注意语言要准确、简洁。
写起报告来就毫无头绪?下面是小编精心整理的工伤事故分析报告,欢迎阅读与收藏。
工伤事故分析报告有限公司是牛仔服饰生产知名、核心企业之一,公司成立于20xx年9月,位于中国举世闻名的经济发达地区——长三角地区、江苏省服装名镇——程桥,占地面积达50亩,建设面积8500㎡。
现拥有各类进口、国产设备1600多台,员工人数300多人,其中专业管理人员26人。
自20xx年生产外贸订单以来,目前公司拥有固定资产20xx万元,配有空调服装流水线车间5900㎡。
总公司具备完整的产品研发、生产、洗水和后整理等配套作业能力,并能独立完成酵洗、漂洗、石洗、碧纹洗、套染喷砂、手擦、立体猫须等多种复杂洗水、染色加工工艺,年产量达400万件以上。
公司技术打样中心配有加拿大PAD服装CAD打版排料软件,主要生产牛仔服装、茄克、风衣、晴棉防寒服、童装等十多个系列的服装,年生产能力150万件,产品远销美国、欧洲、日本、韩国和香港等十多个国家和地区,其中80%外销美国,公司与世界服装零售商BeBeJcpenneyPerry EllsKohl′s等建立了良好的合作关系。
公司通过ISO9001质量体系认证,严格执行各项质量标准,贯彻“高标准、零缺陷”的管理要求,并遵循“最快捷、最有效、最彻底”的处理原则,做到客户与工厂的“零距离” 、产品质量“零缺陷” 、企业内外“零抱怨”,也是企业近年来提出的新要求新标准。
随着六合区社会保险的不断推进完善,所显现出的问题更多。
工伤问题涉及面广,社会影响巨大,一旦发生工伤事故,不但用工单位正常的经营生产会受到影响,而且更为重要的是对工伤职工本人及其家庭带来严重后果,造成经济上、精神上的巨大损失。
鉴于工伤问题的严重性,我们特对20xx年的工伤事故情况进行分析,来预防工伤事故的发生,维护工伤者的权益,促进生产经营单位的良好发展。
工伤事故分析报告

工伤事故分析报告工伤事故分析报告根据本公司工伤事故的实际情况,结合相关数据和分析结果,我们为大家报告以下工伤事故的分析结果。
首先,本次工伤事故发生在本公司生产车间。
具体情况为一名员工在操作机器时不慎手指被夹伤,进一步造成严重的手指骨折。
经过调查分析,我们得出以下结论。
首先,事故发生的原因主要是操作员工没有正确按照操作规程进行操作。
在事故发生时,员工没有戴好劳保手套,并且操作过程中没有注意到机器的运行状态。
这种疏忽大大增加了发生事故的概率。
其次,事故的发生也与机器设备本身的安全性有一定的关系。
通过对机器设备的检查发现,这台机器在设计时没有考虑到操作的便捷性以及安全性。
在操作过程中,机器的活动部分没有足够的防护措施,容易造成操作人员的伤害。
另外,我们还发现公司对员工的安全培训存在一定的不足。
操作员在上岗前没有接受足够的培训和教育,缺乏对安全操作的意识和技能。
这种状况直接导致了此次工伤事故的发生。
以此为基础,我们提出以下对策和建议:首先,公司应加强对员工的安全教育和培训,特别是对操作员的培训。
培训内容应包括操作规程的正确实施、戴劳保用品和注意机器运行状态等相关知识和技能。
同时,公司应优化机器设备的安全性能,加强与设备生产厂商的沟通,要求对机器进行改进,增加相关防护措施,减少操作员的伤害风险。
此外,公司还应建立一套完善的安全监控机制,包括加强对设备的定期维护和检查,以及进行安全巡视等措施,确保设备的正常运行和操作员的安全。
最后,公司应制定严格的安全制度和操作规程,并加强对其执行的监督。
同时还应建立健全的事故报告和处理机制,遇到事故时及时采取有效的应对措施,确保事故不再发生或尽可能减少其损失。
通过对本次工伤事故的分析和解决方案的提出,我们相信可以有效地预防类似的事故的发生,保障员工的安全和健康,促进公司的持续发展。
工伤事故分析报告

工伤事故分析报告根据最新数据显示,工伤事故在全球范围内仍然十分普遍,给企业、员工及整个社会带来了巨大的负面影响。
因此,对工伤事故进行全面的分析是非常有必要的。
本文将从事故原因、影响及预防措施等方面对工伤事故进行分析报告。
首先,工伤事故的原因是多方面的。
一方面,人为原因是工伤事故的主要原因之一。
这包括员工的操作不当、安全意识淡漠、违规操作等等。
另一方面,设备设施的缺陷也是工伤事故的重要诱因。
例如,设备老化、维护不及时、设备故障等都可能导致事故的发生。
此外,管理不善也是工伤事故的一个重要原因,例如缺乏完善的安全管理制度、培训不足等。
其次,工伤事故给企业、员工及整个社会带来了巨大的影响。
对企业而言,工伤事故不仅会造成生产中断、设备损失等直接经济损失,更重要的是会损害企业形象和声誉,影响企业的可持续发展。
对员工而言,工伤事故可能导致伤残、失业甚至生命危险,给个人和家庭带来沉重的负担。
对社会而言,工伤事故会增加医疗资源的压力,引发社会不安定因素,降低生活质量和幸福指数。
最后,为了预防工伤事故的发生,需要采取一系列的措施。
首先,建立健全的安全管理制度是必不可少的。
企业应该制定详细的安全规程,明确责任分工,建立安全督导机制,确保每个环节都得到有效监督和控制。
同时,加强员工培训也非常重要。
通过培训能够提高员工的安全意识,掌握正确的操作方法,提高应对突发事件的能力。
此外,加强设备设施的维护和检修,确保其正常运行,避免因设备故障导致的事故发生。
此外,加强监督检查和隐患排查,及时发现问题并采取措施进行整改。
综上所述,工伤事故分析报告总结了工伤事故的原因、影响及预防措施。
通过汲取事故教训,加强企业内部安全管理和员工培训,采取有效的安全措施,可以降低工伤事故的发生率,保障员工的安全和生命健康,推动企业和社会的可持续发展。
- 1、下载文档前请自行甄别文档内容的完整性,平台不提供额外的编辑、内容补充、找答案等附加服务。
- 2、"仅部分预览"的文档,不可在线预览部分如存在完整性等问题,可反馈申请退款(可完整预览的文档不适用该条件!)。
- 3、如文档侵犯您的权益,请联系客服反馈,我们会尽快为您处理(人工客服工作时间:9:00-18:30)。
关于2015年至2016年工伤事故分析报告
一.工伤事故总体情况
2015年公司进行了组织架构调整、经营战略规划调整,同比生产能力比2014年没有很大的提高,为了扩大生产改善管理,2015年7月份导入精益生产管理,2016年进行人员精简整编,2016年11月起公司扩大生产规模,同年引进了少量成型半自动输送系统。
设备得到改善,但是工伤事故也频繁发生,小伤频繁发生,较大十级以上工伤事件也有发生,2016年在全体职工的共同努力改善下,工伤事故发生率得到了有效的控制。
数据报告分析具体如下:全厂现在职职工最高峰时700多人, 2015年工伤28起,总费用支出93232.47元,2016年截止11月工伤发生数6起,费用支出:36852.24元(其中包括2015年工伤未结案的二次理疗费用)。
二.工伤事故发生的部门、月份、受伤部位等情况
表1:2015年工伤事故部门分布发生比率
费用:
表2:2015年-2016年工伤事故发生月份统计表表3: 2015年-2016年工伤事故受伤部位统计表
三、工伤事故原因分析
根据我公司所发生的工伤事故,发生工伤事故的原因多种多样,受伤部位80%在手指部位,但综合起来不外乎是人的不安全因素,物的不安全状态,管理缺陷,员工安全意识不足等方面,具体体现如下:
1、人的因素
一、2015年/2016年发生的工伤,主要人为操作不当导致,作业现场操作方法没有形成标准化,员工未按规范操作等原因导致事故发生;
二、个别管理人员缺乏安全意识,对安全工作重视不足。
将工作重心放在了产品生产上,对日常安全生产工作重视度不够。
对员工安全知识的培训宣导、岗前操作教育培训没有做到位,存在应付检查现象。
三、员工技能素质不强,防范技能欠缺。
一是员工专业技能不强,对生产工艺、机械设备性能、劳动防护用品认识不够,员工为图省事,有的直接不用;加上技术不够娴熟,容易发生事故。
2、物的因素
一是小部分设备缺乏安全防护设施。
类似管件车间有小部分机械设备无防护,无警示牌是造成事故的一个重要方面。
部分受控气动设备没有做防呆装置,也是导致事故发生的部分原因。
3、管理因素
新员工上岗前缺少必要的技能和安全生产知识培训。
当前员工流动性很大,加上招工困难,公司一招到工人,不管熟练与否,只通过了行政部岗前安全基本知识培训,新手直接上岗,生产车间内并未及时做岗位安全培训,引发事故。
四、对策及措施
1.要加强安全生产培训,提高员工安全生产能力。
要求各部门及车间建立健全岗前培训制度,对新员工及换岗员工开展有关技能、安全防范以及紧急避险的岗前培训。
对在岗职工有针对性地分工种、分岗位进行全员培训,切实提高员工劳动技能和安全生产意识。
2.建立健全规章制度,强化作业现场管理。
公司要严格建立和完善科学合理的安全生产制度和操作规则,使员工有章可循。
同时要加大安全检查力度,将突击检查与全面检查相结合,要对公司的每一个生产环节进行定期巡查,发现问题立即进行整改,杜绝安全生产隐患。
同时加强对员工的日常管理,对违反、违规操作、操作失误的现象要予以批评教育,确保员工有章必循。
3.落实安全责任,建立绩效考核机制。
安全生产要层层落实责任,明确安全责任制度,对发生安全事故的,要追究是责任事故或非责任事故,直接落实本部门车间管理负责人的责任。
4.启动多能工技能看板,实现目视化管理,确实落实实施新员工上岗前的技能教育培训,减少不必要的意外伤害损失。
2017年“0”工伤事故目标。
奖励奖金《》?
行政部人力资源课
2016年11月17日
附件: 2015年-2016年工
伤事故分析报告.xlsx
工伤事故报告(进
行中)(2).xlsx。