汽车轻量化材料及成形技术
汽车轻量化中辊压成形的关键技术

汽车的白车身减重是轻量化的重要内容。
辊压件是白车身的重要构件。
本文介绍了汽车中辊压成形的应用及关键技术,特别是高强钢的辊压成形中的回弹、变形能以及扭曲、侧弯、边波等缺陷的预防和解决办法。
开发了多代保险杠、防撞杆、门槛等辊压件产品。
对于辊压成形国内外先进技术的发展作了介绍。
汽车轻量化中的辊压件为减少能源消耗和环境污染,汽车轻量化成为世界各国汽车制造的新趋势。
白车身作为汽车的重要部件,占到总车重量的40%左右,因此白车身的减重优化成为轻量化设计的重要内容。
目前国际上新车型白车身开发设计,广泛采用先进高强度钢板,其中有相当部分的构件,诸如前后保险杠、门梁、框轨、车顶弓型架、车身的B柱及底盘等构件,都是由辊压成形制造方式完成的。
辊压成形工艺广泛应用于汽车部件的制造,汽车上很多部件是由辊压工艺生产的(图1)。
辊压成形工艺与传统冲压相比,具有高效、节材、环保、成本低等突出优点,成为汽车部件制造工艺方法之一。
据统计采用辊压工艺制造的汽车部件,大约为车重的10%左右。
图1 辊压工艺生产的汽车零件辊压成形是通过顺序配置的多道次成形轧辊,把卷材、带材等金属板带不断地进行弯曲,以制成特定断面的型材。
辊压成形与其他板金属成形的工艺相比,具有以下优点:⑴生产效率高,适合于大批量生产,和冲压、折弯工艺相比提高效率10倍以上,制造成本大幅降低。
⑵加工产品的长度基本不受限制,可以连续生产。
⑶产品的表面质量好,尺寸精度高。
⑷在辊压成形生产线上可以集成其他的加工工艺,如冲孔、焊接、压花等。
⑸与热轧和冲压工艺相比能够节约材料15%~30%。
⑹生产噪声低,无环境污染。
辊压成形工艺加工出来的型材其断面结构合理、品种规格繁多、几何尺寸精确,体现了现代社会对材料轻型化、合理化、功能化的使用要求。
辊压成形是一种高效节能的工艺技术,符合“发展循环经济,创建节约社会”的政策要求。
辊压成形采用先进的高效生产工艺,使成形截面达到最好的力学性能。
高强钢辊压成形的关键技术先进高强度钢AHSS(Advanced High Strength Steel)具有优良的材料性能。
汽车轻量化用铝合金材料及应用技术的研究

汽车轻量化用铝合金材料及应用技术的研究摘要:在广大人们的日常出行以及交通运输过程当中,汽车作为较为主流的交通工具往往发挥着极为重要的作用和价值,受到了社会各界以及广大人民群众的重点关注,对于汽车制造生产行业的相关内容保持着紧密的关注态度,针对汽车制造品质水平要求不断提高。
结合当前汽车制造生产行业的整体发展现状来看,各个汽车制造生产公司为了提高自身的行业竞争能力,逐步在汽车制造过程当中积极推广轻量化材料,汽车更高的性能以及更加良好的安全性。
在实际汽车生产材料选用的过程中采取轻量化材料,不但能够大大提高汽车制造生产的资金投入,还能满足当前社会绿色稳定发展的各方面要求,不断提高企业的核心竞争能力。
得益于各类新型汽车生产材料的研发和创新,我国汽车生产公司的制造生产工艺水平不断提升,有效推广了汽车制造行业的持续稳定发展。
为此,相关技术人员要就汽车轻量化设计工作当中铝合金材料的应用进行分析和探究,再结合当前轻量化建设工作现状的基础之上,明确铝合金材料的实际应用状况和应用要求,以此来为广大技术人员提供参考和帮助。
关键词:金属材料;汽车轻量化;发展现状;具体方案引言:在当今经济社会的发展模式下,全国各地经济联系极为密切,广大人民综合素质也在不断进步,这让人民群众对于汽车制造生产的要求不断提高,在各类经济活动开展、货物运输以及人员出行的过程中,汽车将作为重要的交通工具发挥相应的作用,这让我国汽车制造行业呈现出极为迅猛的发展趋势。
但结合我国近些年来汽车交通工具的整体应用状况来看,虽然汽车为广大人民群众的出行和经济活动带来了良好的帮助,但也制造了巨大的环境污染以及能源消耗问题,这与现代社会低碳环保持续稳定发展的理念相悖。
为此,在汽车生产数量以及需求量不断增多的过程中,相关汽车生产公司要积极主动的开展轻量化设计工作,选用铝合金等新型轻量化生产材料,以此来实现汽车生产制造的低碳环保目标。
详细来说,积极主动的推广和应用轻量化铝合金汽车设计材料,能够有效缓解当前汽车制造行业不错能源消耗以及环境破坏问题,让企业的核心竞争能力大幅度提高,为企业创造更为丰厚的经济效益。
汽车铝合金轻量化材料的应用及技术工艺
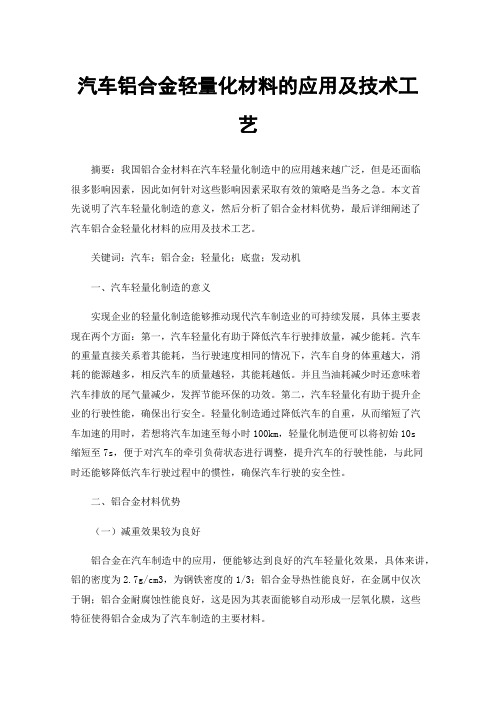
汽车铝合金轻量化材料的应用及技术工艺摘要:我国铝合金材料在汽车轻量化制造中的应用越来越广泛,但是还面临很多影响因素,因此如何针对这些影响因素采取有效的策略是当务之急。
本文首先说明了汽车轻量化制造的意义,然后分析了铝合金材料优势,最后详细阐述了汽车铝合金轻量化材料的应用及技术工艺。
关键词:汽车;铝合金;轻量化;底盘;发动机一、汽车轻量化制造的意义实现企业的轻量化制造能够推动现代汽车制造业的可持续发展,具体主要表现在两个方面:第一,汽车轻量化有助于降低汽车行驶排放量,减少能耗。
汽车的重量直接关系着其能耗,当行驶速度相同的情况下,汽车自身的体重越大,消耗的能源越多,相反汽车的质量越轻,其能耗越低。
并且当油耗减少时还意味着汽车排放的尾气量减少,发挥节能环保的功效。
第二,汽车轻量化有助于提升企业的行驶性能,确保出行安全。
轻量化制造通过降低汽车的自重,从而缩短了汽车加速的用时,若想将汽车加速至每小时100km,轻量化制造便可以将初始10s缩短至7s,便于对汽车的牵引负荷状态进行调整,提升汽车的行驶性能,与此同时还能够降低汽车行驶过程中的惯性,确保汽车行驶的安全性。
二、铝合金材料优势(一)减重效果较为良好铝合金在汽车制造中的应用,便能够达到良好的汽车轻量化效果,具体来讲,铝的密度为2.7g/cm3,为钢铁密度的1/3;铝合金导热性能良好,在金属中仅次于铜;铝合金耐腐蚀性能良好,这是因为其表面能够自动形成一层氧化膜,这些特征使得铝合金成为了汽车制造的主要材料。
(二)生产材料能够回收利用铝合金是回收率较高的金属材料,这是因为铝合金在应用过程中出现腐蚀问题的概率较低。
铝合金材料在制作成产品、使用、回收加工成铝锭、再次制作成产品的循环过程中,损耗率也仅仅为5%,其回收利用价值是所有金属材料中最高的,目前大部分国家应用汽车制造铝合金为再生铝材料。
此外,铝的熔点较低,流动性能良好,因此能够制作成各种结构复杂、形状不规则的构件,这位汽车制造提供了便利条件,同时也便于铝合金回收利用。
6. 汽车轻量化的九大关键工艺
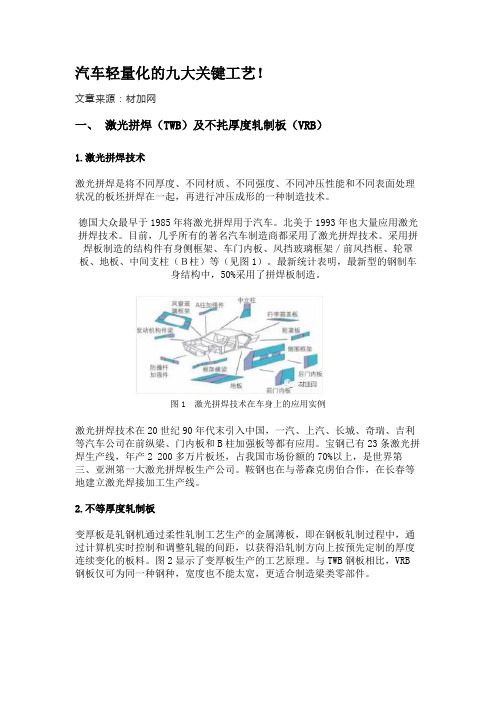
汽车轻量化的九大关键工艺!文章来源:材加网一、激光拼焊(TWB)及不扥厚度轧制板(VRB)1.激光拼焊技术激光拼焊是将不同厚度、不同材质、不同强度、不同冲压性能和不同表面处理状况的板坯拼焊在一起,再进行冲压成形的一种制造技术。
德国大众最早于1985年将激光拼焊用于汽车。
北美于1993年也大量应用激光拼焊技术。
目前,几乎所有的著名汽车制造商都采用了激光拼焊技术。
采用拼焊板制造的结构件有身侧框架、车门内板、风挡玻璃框架/前风挡框、轮罩板、地板、中间支柱(B柱)等(见图1)。
最新统计表明,最新型的钢制车身结构中,50%采用了拼焊板制造。
图1 激光拼焊技术在车身上的应用实例激光拼焊技术在20世纪90年代末引入中国,一汽、上汽、长城、奇瑞、吉利等汽车公司在前纵梁、门内板和B柱加强板等都有应用。
宝钢已有23条激光拼焊生产线,年产2 200多万片板坯,占我国市场份额的70%以上,是世界第三、亚洲第一大激光拼焊板生产公司。
鞍钢也在与蒂森克虏伯合作,在长春等地建立激光焊接加工生产线。
2.不等厚度轧制板变厚板是轧钢机通过柔性轧制工艺生产的金属薄板,即在钢板轧制过程中,通过计算机实时控制和调整轧辊的间距,以获得沿轧制方向上按预先定制的厚度连续变化的板料。
图2显示了变厚板生产的工艺原理。
与TWB钢板相比,VRB 钢板仅可为同一种钢种,宽度也不能太宽,更适合制造梁类零部件。
图2 不等厚度轧制板生产原理德国Mubea公司有两条变厚板生产线,年产7万t。
板厚为0.7~3.5m m,原始板料的最高强度为800MP a级别。
目前,欧洲70余个车型使用变厚板或者变厚管产品。
奔驰C级车中通道加强板、前地板纵梁、后保险杠、后地板横梁等11个零件使用了VRB钢板。
我国宝钢和东北大学均开展了VRB钢板的研发和生产工作,目前具备了小批量供货的能力。
借助于强大的材料开发能力,宝钢形成了VRB零件的设计、材料开发、成形过程模拟、模具设计和产品质量评估的能力,并已试制成功前纵梁、仪表板支架、顶盖横梁等零件,同时也轧制成功了1 500MPa级别的非镀层和铝硅镀层的热冲压成形钢板,成功试制了热冲压成形VRB中通道零件。
汽车轻量化的技术与方法
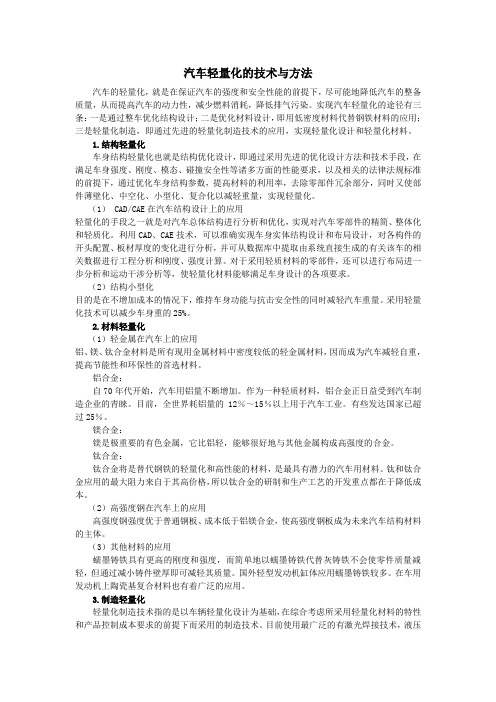
汽车轻量化的技术与方法汽车的轻量化,就是在保证汽车的强度和安全性能的前提下,尽可能地降低汽车的整备质量,从而提高汽车的动力性,减少燃料消耗,降低排气污染。
实现汽车轻量化的途径有三条:一是通过整车优化结构设计;二是优化材料设计,即用低密度材料代替钢铁材料的应用;三是轻量化制造,即通过先进的轻量化制造技术的应用,实现轻量化设计和轻量化材料。
1.结构轻量化车身结构轻量化也就是结构优化设计,即通过采用先进的优化设计方法和技术手段,在满足车身强度、刚度、模态、碰撞安全性等诸多方面的性能要求,以及相关的法律法规标准的前提下,通过优化车身结构参数,提高材料的利用率,去除零部件冗余部分,同时又使部件薄壁化、中空化、小型化、复合化以减轻重量,实现轻量化。
(1) CAD/CAE在汽车结构设计上的应用轻量化的手段之一就是对汽车总体结构进行分析和优化,实现对汽车零部件的精简、整体化和轻质化。
利用CAD、CAE技术,可以准确实现车身实体结构设计和布局设计,对各构件的开头配置、板材厚度的变化进行分析,并可从数据库中提取由系统直接生成的有关该车的相关数据进行工程分析和刚度、强度计算。
对于采用轻质材料的零部件,还可以进行布局进一步分析和运动干涉分析等,使轻量化材料能够满足车身设计的各项要求。
(2)结构小型化目的是在不增加成本的情况下,维持车身功能与抗击安全性的同时减轻汽车重量。
采用轻量化技术可以减少车身重的25%。
2.材料轻量化(1)轻金属在汽车上的应用铝、镁、钛合金材料是所有现用金属材料中密度较低的轻金属材料,因而成为汽车减轻自重,提高节能性和环保性的首选材料。
铝合金:自70年代开始,汽车用铝量不断增加。
作为一种轻质材料,铝合金正日益受到汽车制造企业的青睐。
目前,全世界耗铝量的12%~15%以上用于汽车工业。
有些发达国家已超过25%。
镁合金:镁是极重要的有色金属,它比铝轻,能够很好地与其他金属构成高强度的合金。
钛合金:钛合金将是替代钢铁的轻量化和高性能的材料,是最具有潜力的汽车用材料。
简述汽车轻量化材料及制造工艺

简述汽车轻量化材料及制造工艺摘要:现如今,汽车在生活中得到不断普及,带来的环保性问题、节能型问题、安全性问题等越来越明显。
在这种情况下,汽车的轻量化研究越来越受到人们的重视,不仅有助于控制污染物的排放,还有助于提升汽车使用性能和安全性能,对于汽车的发展和进步有着重要的意义。
文章就此对汽车轻量化材料及制造工艺展开讨论。
仅供参考。
关键词:汽车;轻量化材料;制造工艺一、汽车轻量化材料及制造工艺研究原则综合分析汽车整体构造,其中车身构造重量在总重量中占据的比重较大,约占1/3。
所以通过优化车身材料选取能有效降低汽车自重。
当前在汽车车身材料选取过程中需要依照以下基本原则。
首先汽车在稳定行驶过程中要对汽车安全性、舒适性、稳定性进行探析。
其次各类的焊接部件能冲压成型,生产制造中技术工艺性能完善,最后材料应用具有可回收性与良好的经济性。
汽车工业全面发展的重要动力是基于材料基础进步基础上,提升汽车安全性,突出节能减排重要作用。
二、汽车轻量化材料的应用1.铝合金铝合金的比重仅仅是钢材质的30%,假设弯曲刚度为相同状态时,铝合金相对厚度是1.43,计算出49%为其减重潜能;假设弯曲强度相等的话,那么其减重潜力是38%。
有报道表明,如将汽车车身材料全部换为铝合金,在同等条件下会比铸铁、低碳钢等材质的车身每千克少排放13千克至20千克的温室气体,这也是当前阶段铝合金越发广泛的应用于汽车车身材质的直接原因,此种情况在豪华汽车中更加明显。
大量B级和C级汽车随着我国汽车制造业的发展相继问世,近些年更是有一批档次较高的新型汽车出现。
相关法律法规也随之不断完善,进一步推动了铝合金材质在国内汽车市场的应用。
此外,铝合金材料的冶炼技术对于汽车行业的发展也有十分积极的推动作用,现阶段主要有以下几种应用形式:铝合金锻件应用在车轮、汽车悬架支架的构件方面;铸造件应用在车身壳体和发动机缸盖等、车身结构等铝合金基拉拉伸件。
现阶段成本较高和焊接工艺性较差是阻碍铝合金材质推广和应用的首要原因,因此必须致力于铝合金冶炼技术的改进、成型工艺性的改进以及材料成本的降低,进而推进铝合金材料在我国汽车行业的应用,进一步推进我国汽车轻量化的发展进程。
汽车轻量化的主要技术

汽车轻量化的主要技术
汽车轻量化是汽车行业开发、提高汽车性能和减少燃油消耗的重要技术。
通过汽车轻量化,不仅有效的减轻汽车重量,提高汽车的加速性能,减少能耗,而且有助于减少材料和能源的消耗。
汽车轻量化的主要技术有:
1.车身材料改进:通过使用合理的车身材料,达到车身更轻、更坚固,
更好、更有效的结构,从而减少车身重量。
通常使用的材料包括:钢材、铝
合金、高强度塑料等。
2.底盘优化设计:车身下部部分是重车身重量最大的部分,通过优化设计,减少底盘的重量和面积,减少结构梁的数量,加强车身的刚性,改善汽
车行驶的舒适性,实现底盘结构的轻量化。
3.焊接工艺优化:焊接技术是车身部件轻量化的重要技术,有助于将大
型车身部件拆分,缩小模型尺寸,从而实现更轻量化的结构。
4.金属发泡:金属发泡是一种可以大大减少汽车重量的复合材料技术。
金属发泡材料特殊的复合结构,能极大的降低车身重量,同时又能满足强度
和刚性的要求。
汽车轻量化已经成为当前汽车行业的主流发展,通过应用上述多种技术,可以大大减小汽车重量,提高能源利用效率,减少燃料消耗,是提高汽车效
率和节省能源的有效措施。
汽车轻量化材料技术发展现状

汽车轻量化材料技术发展现状引言随着汽车工业的高速发展,汽车轻量化材料技术日益受到关注。
汽车轻量化是指通过使用轻质材料替代传统材料,减轻汽车的整体重量,从而降低燃料消耗和排放,提高汽车的性能和安全性。
本文将全面、详细、完整地探讨当前汽车轻量化材料技术的发展现状。
二级标题1. 金属材料技术传统的汽车结构材料主要是高强度钢材,随着技术的进步和需求的变化,汽车制造商开始探索更轻、更强韧的金属材料。
以下是当前主要的几种金属材料技术:•铝合金:铝合金具有优异的轻量化特性和较高的强度,适用于车身和底盘部分。
如奥迪A8采用的铝合金车身结构,相比传统钢结构减重了40%。
•镁合金:镁合金比铝合金更轻,但也更昂贵和容易受到腐蚀。
它通常用于发动机和传动系统中的零部件,如发动机缸盖和传动壳体。
•钛合金:钛合金是一种高强度和高抗腐蚀性的金属材料。
轻量化的钛合金材料在高端汽车和赛车中广泛应用,但由于成本较高,应用范围有限。
2. 聚合物材料技术聚合物材料是一种轻量化的非金属材料,具有良好的机械性能和成本效益。
以下是当前主要的几种聚合物材料技术:•碳纤维复合材料:碳纤维具有高强度和轻质特性,广泛应用于汽车零部件制造。
例如,保时捷911 GT3采用碳纤维复合材料制作的车体,减重约100kg。
•玻璃纤维增强塑料:玻璃纤维增强塑料结合了玻璃纤维的高强度和塑料的轻质性能。
它常用于车身和内饰件的制造,如保险杠和门板。
•高性能塑料:高性能塑料具有优异的机械性能和耐高温性能,在汽车行业得到广泛应用。
例如,聚酰胺材料常用于发动机零部件制造。
3. 其他轻量化材料技术除了金属和聚合物材料,还有其他一些轻量化材料技术在汽车行业得到应用:•轻质玻璃:轻质玻璃具有较低的密度和较高的强度,可用于汽车的车窗和天窗,减轻车身重量。
•复合材料:复合材料由两种或多种材料的组合构成,在汽车行业具有广泛的应用。
如铝基复合材料、聚酯基复合材料等。
•生物基材料:生物基材料是一种以农产品或农林废弃物为原料制造的材料,具有环保和可再生的特点。
- 1、下载文档前请自行甄别文档内容的完整性,平台不提供额外的编辑、内容补充、找答案等附加服务。
- 2、"仅部分预览"的文档,不可在线预览部分如存在完整性等问题,可反馈申请退款(可完整预览的文档不适用该条件!)。
- 3、如文档侵犯您的权益,请联系客服反馈,我们会尽快为您处理(人工客服工作时间:9:00-18:30)。
图6 可用超高强度钢制造的车身件 硼合金超高强钢的强度可以达
到1 500 MPa,是铝合金的5倍,而 密度只有铝合金的3倍,因此减重比 铝合金更有效。比如全铝合金车身
可减重30%,而硼合金钢可使白车 身减重33%,但成本却比铝制车身 减少30%。车身强度也大幅提高, 碰撞安全等级达到最高级,能够同 时满足汽车对轻量化和安全性能的 要求。当钢板厚度分别减少0.05、 0.10、0.15 mm时,车身减重分别为 6%、12%、18%。采用先进的高强 度钢,增加了安全性,降低了噪声 和振动,提高了燃油效率,减轻了 汽车总质量。成本不增加,而加速 性、驾驶性能则有所改善。 1.3 塑料及复合材料
目前,钛及其合金可用于制造 发动机配气系、曲轴连杆机构和底 盘零件,如气门、气门弹簧、凸轮 轴、连杆等。此外,钛合金板材和 管材还可用于消声器及车轮。钛合 金材料的应用范围已从赛车逐渐扩 大到批量生产的轿车。美国在其新 一代汽车研究计划中指出,钛在汽
车上的可能应用主要分布在发动机 零件和底盘部件上,每辆汽车仅底 盘部件的潜在用钛量就达9.9 kg。由 于汽车用钛合金零部件的出色性能, 发达国家的汽车用钛量持续增长。 1995年,全球汽车领域用钛量只有 100 t,2002年就超过了1 000 t。随 着材料技术的进步,钛合金材料的 生产和加工成本将不断降低,有望 在汽车领域得到更大的应用。
镁合金和塑料、铝合金零件相 比,除易于回收利用、是典型的绿 色结构材料外,还具有突出的资源 优势。我国是一个镁资源大国,镁 矿产品种类多、储量丰富,占世界 可利用镁资源储量的70%左右。 因此,在许多传统金属矿产日益枯 竭和全球对技术革新、能源消耗、 废气污染及噪声限制不断升级的今 天,加速镁合金的研究、开发和产 业化具有重要的现实意义。
(2)镁合金
汽车零部件有60多种,单车上的镁 合金质量为9.3~20.3 kg。如仪表板 骨架、转向盘(图3)、气缸体、气 缸盖、进气歧管、轮毂、车身部的镁合金板材等。为进一步 扩大镁合金的应用,国外又在开发 耐蚀性好的镁合金及其表面处理技 术。
北美正在使用和研制的镁合金 汽车零部件有100多种,是世界上汽 车用镁合金量最大的地区,单车上的 镁合金质量为5.8~26.3 kg。
15~25
10~12.5
100~250
50~167
镁合金 1.74~1.9
45
24~26
180~300
118~172
轻量化材料与汽车产品设计、 制造工艺的结合将更为密切,汽车 车身结构材料将趋向多材料设计方 向。通过新的成形技术,不断优化 设计,提高性能,降低成本,促进 汽车轻量化不断发展。 1.1 轻合金
表1 各种材料的相关力学性能对比
材料
比重ρ /g·cm-3
弹性模量 E/GPa
比弹性模量 E/ρ
拉伸强度 σ /MPa
比拉伸强度 σ /ρ
铸铁
7.15
180
24.3
200~400
27~54
钢
7.8
210
27
200~500
27~64
铝合金
2.7
70
25.9
200~350
73~128
塑料
1.13~2.0
欧美的汽车用镁合金压铸件正 在以年均25%的速度增加,汽车用 镁量正在以年均20%的速度上升。 世界各大汽车公司都已经把采用镁 合金零部件的多少作为衡量其汽车 产品技术是否领先的标志。福特汽 车公司计划在今后20年内将每辆汽 车的镁合金用量提高到113 kg。
Magna国际公司认为镁合金 压铸件可以达到净成形一次加工成 品,不需要二次加工,因而在成本 上可以和铝合金压铸件竞争。在保 证强度要求的前题下,若采用最佳 化设计,镁合金比铝合金可减轻质 量33%。随着新型镁合金材料的不 断开发和加工技术的改进,汽车用 镁合金市场将不断拓宽并持续稳定 增长。
与通用塑料相比,工程塑料具 有优良的机械性能、耐化学性、耐 热性、耐磨性、尺寸稳定性等特 点,比被取代的金属材料轻且成型 时能耗少。从20世纪70年代起,以 软质聚氯乙烯、聚氨酯为主的泡沫 类、衬垫类、缓冲材料等塑料在汽 车工业中被广泛采用。福特公司开 发的LTD试验车,塑料化后的车身取 得了轻量化方面的明显成果,整车 减重可达300 kg以上。
机械科学研究总院先进制造技术研究中心 姜 超 华南精密设计开发研究院汽配技术中心 张 悦
1 轻量化材料
世界汽车材料技术主要发展方 向仍然是轻量化和环保。虽然钢铁 材料仍保持主导地位,但高强度钢 和超高强度钢、铝合金、镁合金、 塑料和复合材料用量在不断增长, 铸铁和中、低强度钢的应用将逐步 减少,各种材料的性能差异(见表 1)导致其在汽车上的应用比例不断 变化。
(1)铝合金
尝试着生产出了流线型铝车身的K 型车。2006年,奥迪铝材及轻量设 计中心整合了轻量化产品开发、生 产规划和质量保障功能,其在该领 域研发的重心已超越了单纯的铝材 概念,将研究方向扩展至对高强度 钢材、型材、加固塑胶及镁合金材 料的应用,系统地将轻量化设计运
导热系数 W/mk 80 46 247 20~50 157
此前,曾一度出现合成塑料的 车身,成本和强度都没有问题,但 不能推广的最大原因在于当车身发 生损坏时很难进行局部修补,甚至 要整件更换。
(2)复合材料 20世纪80年代以来,许多世界 著名的车辆制造商投入大量人力、 物力开发了复合材料,并对先进复 合材料在汽车工业中的应用进行研 究。20世纪80年代后期,复合材料 车身外覆盖件得到大量的应用和推 广,如发动机罩盖、翼子板、车门、 车顶板、导流罩、车箱后挡板等,甚 至出现了全复合材料的轿车车身, 如大众的1-Litre Car原型车,外壳使 用强化碳纤维材质(图7),车身长
太平洋地区 1
1
2
2
2
3
3
45
6
7 8 9 11 13 16
其他
5
5
7
8
7
8
9
9 10 11 11 12 14 15 17 18
发达国家轿车平均每车用铝量 已达到130 kg以上。铝合金材料是 当前汽车材料研究的热点,在合金 改良、成型性、铸件的疲劳强度、 结构件的可焊接性、原材料循环利 用等方面;在发展低成本、稳定制 造的生产工艺方面,均有待于深入 研究。我国汽车材料用铝仅达到日 本20世纪80年代的水平,与汽车 工业的高速发展极不适应。增加品 种、提高质量、降低成本,已成为 我国铝加工行业和汽车行业跟踪世 界先进水平应发展的研究方向。
表3 汽车上镁合金用量的发展趋势
kt
1991 1992 1993 1994 1995 1996 1997 1998 1999 2000 2001 2002 2003 2004 2005 2006
北美
10 12 14 18 23 31 39 44 49 51 55 60 65 72 78 86
欧洲
8 7 6 9 10 9 16 23 30 35 40 45 50 55 60 66
用于车身、发动机、悬架等各个领 域,在保证整车高性能、舒适性和 安全性的前提下,达到显著降低油 耗的目的。见图1、图2。
宝马新5系是世界上首款采用创 新的钢铝组合结构的汽车。车身前 部采用铝材,车身其他部位由钢材 制成。这样使整车质量比上代5系最 多减轻了75 kg。另外,BMW是世界 上唯一将铝制传动轴作为动力传输 的汽车生产商,主要目的也是为了
图4 镁合金纵梁支架 目前,应用的镁合金材料主要 为铸造镁合金,AM、AZ、AS系列 为传统的铸造镁合金,其中AZ91D 用量最大。近年来,为适应发动 机零件工作温度较高的需要,欧 美等国家先后开发出AE、Mg-AlCa、Mg-Al-Sr等抗蠕变镁合金,以 及最近的ZAC8506(Mg-8Zn-5Al0.6Ca)。变形镁合金新材料有美国 开发的ZK60变形镁合金,日本的 IM Mg-Y系变形镁合金以及可以进行
铝合金是轻量化材料中应用比 较成熟的材料之一。根据美国铝学 会的报告,汽车上每使用0.45 kg铝就 可减轻车重1 kg。理论上铝制汽车 可以比钢制汽车减重40%左右。对 于1辆1 300 kg重的轿车,若质量减轻 10%,其燃油消耗可降低8%。
早在1913年,NSU汽车联盟公 司生产的8/24型汽车便实现了全铝 合金车身。1923年,奥迪生产了六 缸全铝合金发动机。同年,奥迪还
塑料在汽车中的应用范围正在 由内饰件向外装件、车身及结构件 扩展,今后的重点发展方向是开发 结构件、外装件用的增强塑料复合 材料、高性能树脂材料及塑料,并 会更加重视材料的可回收性。从品
2008年第12期
汽 车 工 艺 与 材 料 AT&M 11
A T&M论坛
AT & M
FORUM
种上看,聚烯烃材料因密度小、性 能好、成本低,其用量会有较大的 增长。预计聚丙烯和聚氯乙烯今后 分别可保持8%、4%的年增长率,聚 乙烯的增长势头也比较强劲。
2007年,中国海绵钛和钛加工 材料均呈翻番式增长,海绵钛的产 量已居世界第一位,是我国车用钛 合金材料的有利条件。 1.2 超高强钢
超高强度钢可制造大部分车身 件,见图5,图6。不论从成本角度 ,还是从性能角度来看,高强度钢 板是满足车体轻量化、提高撞击安 全性的最佳材料。为适应今后更为 严格的法规,高强度钢的使用量将 会越来越大。随着用户对撞击安全 性能要求的提高,其作用也将愈发 明显。
镁合金变速杆几乎被日本所有 生产自动变速汽车的企业采用。日 本大多数生产手动变速汽车的企业 也在开始应用镁合金变速杆。日本 采用镁合金座椅架的车种在不断增 加,另外镁合金变速器壳体、仪表
10 汽 车 工 艺 与 材 料 AT&M
2008年第12期
A T&M论坛
AT & M
FORUM