筒形件的拉深模具设计
筒形件一次拉深模具课程设计

目录序言 (2)第一部分冲压成形工艺设计 (4)Ⅰ明确设计任务,收集相关资料 (4)Ⅱ制定冲压工艺方案 (5)Ⅲ定毛坯形状,尺寸和主要参数计算...................... 6-7 第二部分冲压模具设计 (8)Ⅰ确定模具类型机结构形式 (8)Ⅱ计算工序压力,选择压力机 (8)Ⅲ计算模具压力中心 (9)Ⅳ模具零件的选用. . . . . . . . . . . . . . . . . . . . . . . . . . . . . . . . . . . . . . 10-12 Ⅴ冲压设备的校核 . . . . . . . . . . . . . . . . . . . . . . . . . . . . . . . . . . . . . . . .12Ⅵ其他需要说明的问题. . . . . . . . . . . . . . . . . . . . . . . . . . . . . . . . . . . .13Ⅶ模具装配. . . . . . . . . . . . . . . . . . . . . . . . . . . . . . . . . . . . . . . . . . . . . 13 设计总结 (14)参考文献 (15)序言目前我国模具工业与发达国家相比还相当落后。
主要原因是我国在模具标准化,模具制造工艺及设备等方面与工业发达国家相比差距很大。
随着工业产品质量的不断提高,模具产品生成呈现的品种、少批量、复杂、大型精密更新换代速度快。
模具设计与技术由于手工设备,依靠人工经验和常规机加工,技术向以计算机辅助设计,数控编程切屑加工,数控电加工核心的计算机辅助设计(CAD/CAM)技术转变。
模具生产制件所表现出来的高精度,高复杂程度,高生产率,高一致性和抵消耗是其它制造加工方面所不能充分展示出来,从而有好的经济效益,因此在批量生产中得到广泛应用,在现代工业生产中有十分重要的地位,是我国国防工业及民用生产中必不可少的加工方法。
圆筒形件拉深模的设计

向: 伸长
凸缘部分 切 向: 压缩
厚度方向: 一定范围内变薄,一定范围外增厚
(2)凹模圆角部分
(3)筒壁部分
圆筒形件拉深模设计
第一节 拉深基本原理
(4)凸模圆角部分 (5)筒底部分
2.应力
拉深成形后制件壁厚和硬度分布
三、拉深时凸缘区的应力分布与起皱
1.拉深过程中某一瞬间,凸缘区的应力分布 (1)径向拉应力边缘最小为0,凹模口处最大。 (2)切向压应力边缘最大,凹模口处最小,但不为0。
圆筒形件拉深模设计
内容简介: 拉深是基本冲压工序之一
本学习情境在分析拉深变形过程及拉深件质量影响因素 的基础上,介绍了拉深工艺计算、工艺方案制定和拉深模设 计。涉及到拉深变形过程分析、拉深件质量分析、拉深系数 及最小拉深系数的影响因素、圆筒形件的工艺计算、其它形 状零件的拉深变形特点、拉深工艺性分析与工艺方案确定、 拉深模的典型结构、拉深模的工作零件设计、辅助工序等。
圆筒形件拉深模设计
第一节 拉深基本原理
(3)在R′=0.61 Rt处,径向拉应力等于切向压应力,往内,拉 应力占优、厚度变薄,往外,压应力占优、厚度增厚。 2.整个拉深过程中σ1max、σ3max的变化规律 (1)σ1max的变化规律
由小逐渐增大,当Rt=(0.8~0.9)R时,σ1max最大,即拉深 刚开始不久拉应力即达到最大;然后逐渐减小,结束时为零。 (2)σ3max的变化规律
编辑本段生产类型
生产类型通常分为三类。
1.单件生产 单个地生产某个零件,很少重复地生 产。
2.成批生产 成批地制造相同的零件的生产。
3.大量生产 当产品的制造数量很大,大多数工作 地点经 常是重 复进行 一种零 件的某 一工序 的生产 。
[机械电子]圆筒形件拉深模设计
![[机械电子]圆筒形件拉深模设计](https://img.taocdn.com/s3/m/9afb6e40856a561253d36f83.png)
按功能分类
(1)经济型数控车床 采用步进电动机和单片机对普通车床 的进给 系统进 行改造 后形成 的简易 型数控 车床, 成本较 低,但 自动化 程度和 功能都 比较差 ,车削 加工精 度也不 高,适 用于要 求不高 的回转 类零件 的车削 加工。
(2)普通数控车床 根据车削加工要求在结构上进行专门 设计并 配备通 用数控 系统而 形成的 数控车 床,数 控系统 功能强 ,自动 化程度 和加工 精度也 比较高 ,适用 于一般 回转类 零件的 车削加 工。这 种数控 车床可 同时控 制两个 坐标轴 ,即X轴 和Z轴 。
圆筒形件拉深模设计
学习目的与要求:
1.了解拉深变形规律及拉深件质量影响因素; 2.掌握拉深工艺计算方法。 3.掌握拉深工艺性分析与工艺设计方法; 4.认识拉深模典型结构及特点,掌握拉深模工作零件设计方 法; 5.掌握拉深工艺与拉深模设计的方法和步骤。
圆筒形件拉深模设计
本学习情境重点:
1.拉深变形规律及拉深件质量影响因素; 2.拉深工艺计算方法; 3.拉深工艺性分析与工艺方案制定; 4.拉深模典型结构与结构设计; 5.拉深工艺与拉深模设计的方法和步骤。
热处理的高速钢,又叫作白钢。
硬质合金 硬质合金由难熔材料的碳化钨、碳 化钛和 钴的粉 末,在 高压下 成形, 经1350-1560摄氏度 高温烧
结而成的。具有极高的硬度,常温下 可达HR A92, 仅次于 金刚石 ;红硬 性很好 ,在1000摄氏 度左右 仍能保 持良好 的切削 机能; 具有较 高使用 强度, 抗弯
圆筒形件拉深模设计
第一节 拉深基本原理
(2)网格变化
① 筒底 无变化
② 筒壁 无变化
③ 凸缘区 径向伸长,切向压缩。
(2)拉深变形特点
第一节 圆筒形零件拉深讲解
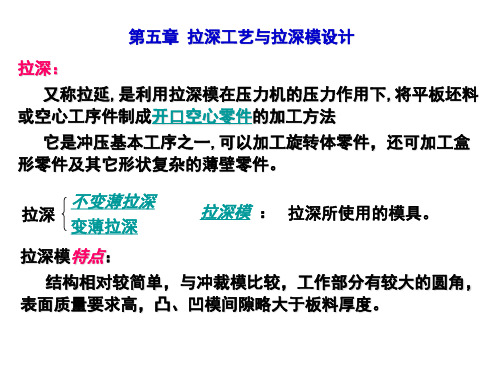
筒壁传力区拉裂: 由于拉应力超过抗拉强度引起板料断裂。
一、无凸缘圆筒形零件拉深 4、圆筒形零件拉深成形的缺陷及防止措施
1)凸缘变形区的起皱 主要决定于:
切向压应力σ3的大小,越大越容易失稳起皱; 凸缘区板料本身的抵抗失稳的能力。
凸缘宽度越大,厚度越薄,材料弹性模量和硬化模量越小, 抵抗失稳能力越差。
第n次拉深系数: mn=dn/dn-1
6、拉深系数的确定 1)拉深系数的概念
拉深系数m 表示拉深前后坯料(工序件)直径的变化率.
m 愈小,说明拉深变形程度愈大,相反变形程度愈小. 拉深件的总拉深系数等于各次拉深系数的乘积,即
若m 取得过小,会使拉深件起皱、断裂或严重变薄超差。 极限拉深系数: 工件在危险断面不至拉破时,所能达到的最小拉深系数mmin。
压料装置产生的压料力Fy大小应适当;
在保证变形区不起皱的前提下,尽量选用小的压料力。 理想的压料力是随起皱可能性变化而变。
9、圆筒形零件拉深的压料力和拉深力
2)拉深力与压力机的公称压力 ①拉深力F
按经验公式可计算出圆筒形件带压料装置和不带压料装置的 首次拉深和以后各次拉深的拉深力。 ②压力机的公称压力
②金属的流动过程 工艺网格实验 材料转移:高度、厚度发生变化。
③拉深变形过程
外力
凸缘产生内应力: 径向拉应力σ1;切向压应力σ3
凸缘塑性变形: 径向伸长,切向压缩,形成筒壁
直径为d高度为H的圆筒形件(H>(D-d)/2)
拉深单元变形动画
一、无凸缘圆筒形零件拉深
2、圆筒形零件拉深过程中坯料内的应力与应变状态 拉深过程中某一瞬间坯料所处的状态
当筒壁拉应力超过筒壁材料的抗拉强度时,拉深件就会在 底部圆角与筒壁相切处——“危险断面”产生破裂。
4.5拉深模具设计

深度拉深件或落料拉深复合模:
应使工艺力曲线位于压力机滑块 的许用压力曲线之下,还需对压力机 的电机功率进行校核
三. 压力机的选择
深度拉深件或落料拉深复合模:
1 F1 max h1
1000
① 计算拉深功A
首次拉深:
以后各次拉深:
凸、凹模工作部分形状
带压边圈的拉深
:
a:用于直径d≤100mm的拉深件
b:用于直径d>100mm的拉深件
五. 拉深工艺的辅助工序
润滑
热处理
目的:消除加工硬化及残余应力
对于普通硬化金属(如08钢、10钢、15钢等), 若工艺过程正确,模具设计合理,一般可不要进行中 间热处理。 对高度硬化金属(如不锈钢、耐热钢等),一般 一、二道工序后就要进行中间热处理。
凸模圆角的影响
:
凸模圆角rp↓↓→rp处弯曲变形程度 ↑→“危险断面”受拉力大→工件易产生局部变薄; 凸模圆角rp↑↑→凸模与毛坯的接触面↓→ 易产生底部变薄和内皱
四. 凸、凹模工作部分的尺寸设计
凹模圆角半径rd的计算
:
首次拉深: d r
1
0.8 ( D d )t
以后各次拉深: d n
r (0.6 ~ 0.8)rdn1
式中:rd1、rdn-1、rdn——首次、第(n-1)次和第n 次拉深模的凹模圆角半径 D——毛坯直径;d——中径;t——工件厚度。
有平面凸缘拉深件,最后一次拉深时:
凹模圆角半径应和拉深件的一致,即rdn=r。
四. 凸、凹模工作部分的尺寸设计
凸模圆角半径rd的计算
四. 凸、凹模工作部分的尺寸设计
课程设计带凸缘筒形件首次拉深的拉深模设计
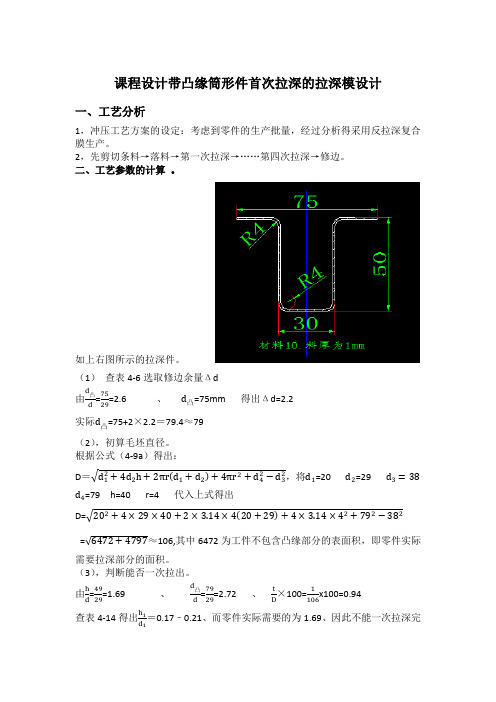
课程设计带凸缘筒形件首次拉深的拉深模设计一、工艺分析1,冲压工艺方案的设定:考虑到零件的生产批量,经过分析得采用反拉深复合膜生产。
2,先剪切条料→落料→第一次拉深→……第四次拉深→修边。
二、工艺参数的计算 。
如上右图所示的拉深件。
(1) 查表4-6选取修边余量Δd 由d 凸d=7529=2.6 、 d 凸=75mm 得出Δd=2.2实际d 凸=75+2×2.2=79.4≈79 (2),初算毛坯直径。
根据公式(4-9a )得出:D =√d 12+4d 2h +2πr (d 1+d 2)+4πr 2+d 42−d 32,将d 1=20 d 2=29 d 3=38d 4=79 h=40 r=4 代入上式得出D=√202+4×29×40+2×3.14×4(20+29)+4×3.14×42+792−382 =√6472+4797≈106,其中6472为工件不包含凸缘部分的表面积,即零件实际需要拉深部分的面积。
(3),判断能否一次拉出。
由h d =4929=1.69 、d 凸d=7929=2.72 、 t D ×100=1106x100=0.94查表4-14得出h1d 1=0.17﹣0.21、而零件实际需要的为1.69、因此不能一次拉深完成。
(4),计算拉深次数及各工序的拉深直径。
,因此需要用试凑法计算利用表4-14来进行计算,但由于有两个未知数m和d td1拉深直径。
下面用逼近法来确定第一的拉深直径。
的值为由于实际拉深系数应该比极限拉伸系数稍大,才符合要求,所以上表中d td11.5、1.6、1.7的不合适。
因为当d t的值取1.4的时候,实际拉深系数与极限拉深系数接近。
故初定第一次d1拉深直径d1=56.因以后各次拉深,按表4-8选取。
故查表4-8选取以后各次的拉深系数为当m2=0.77时d2=d1×m2=56×0.77=43mm当m2=0.79时d3=d2×m3=43×0.79=34mm当m3=0.81时d4=d3×m4=34×0.81=27mm<29mm因此以上各次拉程度分配不合理,需要进行如下调整。
圆筒形件拉深工艺计算

拉深工艺与拉深模设计
圆筒形件拉深工艺计算
三、圆筒形件拉深的压料力与拉深力
2.拉深力与压力机公称压力 (2)压力机公称压力
单动压力机,其公称压力应大于工艺总压力Fz。 工艺总压力为 Fz F FY
注意: 当拉深工作行程较大,尤其落料拉深复合时,应使工艺
力曲线位于压力机滑块的许用压力曲线之下。
在实际生产中,可以按下式来确定压力机的公称压力 Fg : 浅拉深 Fg (1.6 ~ 1.8)Fz 深拉深 Fg (1.8 ~ 2.0)Fz
(1)工序件直径的确定
确定拉深次数以后,由表查得各次拉深的极限拉深系
数,适当放大,并加以调整,其原则是:
1)保证m1m2…mn= 2)使m1<m2<…mn
d D
最后按调整后的拉深系数计算各次工序件直径:
d1=m1D d2=m2d1
…
dn=mndn-1
拉深工艺与拉深模设计
圆筒形件拉深工艺计算
二、拉深次数与工序件尺寸
极限拉深系数[m]
从工艺的角度来看,[m]越小越有利于减少工序数。
拉深工艺与拉深模设计
圆筒形件拉深工艺计算
一、拉深系数与极限拉深系数
2.影响极限拉深系数的因素
(1)材料的组织与力学性能 (2)板料的相对厚度t / D
t/D
[m]
(3)拉深工作条件
1)模具的几何参数 2)摩擦润滑 3)压料圈的压料力
拉深工艺与拉深模设计
圆筒形件拉深工艺计算
二、拉深次数与工序件尺寸
1.拉深次数的确定 (2)推算方法
1)由表4.4.1或表4.4.2中查得各次的极限拉深系数; 2)依次计算出各次拉深直径,即
d1=m1D;d2=m2d1;…;dn=mndn-1; 3)当dn≤d时,计算的次数即为拉深次数。
筒形件拉深
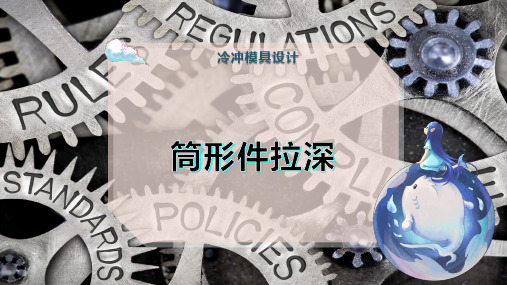
2.拉深系数
习惯上常用拉深系数m来表示变形量。 对于首次拉深,ml=d1/d0; 对于第二次拉深m2=d2/d1;
…
对于第n次拉深,mn=dn/dn-1。
在制定拉深工艺时,通常采用尽可能小的 拉深系数。
但所能采用的拉深系数不能低于某一极限值, 该极限值称为极限拉深系数。
数次拉深的极限拉深系数分别用[m1]、[m2]、 [m3]等来表示。
1 2
d0 d1
1
2
对于多次拉深,变形系数为
cn
hn h
d
2 0
d
2 n
4d1
t0 tn
d 0 dn
d0 dn 2dn
t0 tn
1 2
d0 dn
1
t0 tn
2
(4.3) (4.4)
式中,dn——经过n次拉深后工件侧壁的平均直径 t0——毛坯厚度;
tn——经过n次拉深后工件侧壁的平均厚度。
式中
d0——坯料直径;
d——工序件直径;
r——工序件圆角半径。
1.3 带法兰筒形件的拉深
1.拉深系数
实际上,带法兰筒形件
的拉深是无法兰筒形件
拉深的某一中间状态,
如图4.7所示。带法兰筒
形件的拉深系数以mf来
表示:
mf= d
d0
(4.8)
图4.7 筒形件拉深过程
表4.6 带法兰筒形件首次拉深的极限相对深度 h1/d1(10钢)
表4.7 带法兰筒形件首次拉深的极限拉深系数[mf] (10钢)
表4.8 带法兰筒形件首次拉深的极限拉深系数 (10钢)
2.多次拉深
需要多次拉深的带法兰工件,应在首次拉深中 就获得工件所要求的法兰直径。在以后各工序 中,法兰直径不再变化,只要逐次减小筒形部 分的直径而已,如图4.8所示。
- 1、下载文档前请自行甄别文档内容的完整性,平台不提供额外的编辑、内容补充、找答案等附加服务。
- 2、"仅部分预览"的文档,不可在线预览部分如存在完整性等问题,可反馈申请退款(可完整预览的文档不适用该条件!)。
- 3、如文档侵犯您的权益,请联系客服反馈,我们会尽快为您处理(人工客服工作时间:9:00-18:30)。
新余学院课程设计任务书学号学生姓名专业材料成型及控制工程课程设计题目筒形件的拉深模具设计研究主要内容及基本要求一、设计内容:1、设计一幅拉深模完成下图(圆筒形件,材料为08F 厚度t=1mm,小批量生产,其未注公差尺寸精度等级为IT14)的拉深。
2.模具整体方案设计:包括零件的工艺分析、模具类型的确定、压力中心计算、毛坯尺寸计算、压力机选择等。
3.模具整装配图和模具重要零件选用与设计。
4.撰写此模具设计的说明书二、技术要求:1、要求每位学生完成模具整体装配图1 张,2、主要零件(凸模、凹模、凸凹模等)图3-5张3、详细的设计计算过程4、有关零件的选用依据及过程5、主要零件(凸模、凹模、凸凹模等)的制造工艺规程1-2份6、课程设计说明书(不少于5千字)第一章概述一、模具概述模具是高新技术产业的一个组成部分,是工业生产的重要基础装备.用模具生产的产品,其价值往往是模具价值的几十倍。
模具技术是一门技术综合性强的精密基础工艺装备技术,涉及新技术、新工艺、新材料、新设备的开发与推广应用.是冶金、材料、计量、机电一体化、计算机等多门学科以及铸、锻、热处理、机加工、检测等诸多工种共同打造的系统工程。
用模具生产制品具有高效率、低消耗、高一致性、高精度和高复杂程度等特点,这是其他任何加工制造方法所不及的。
目前,模具制造业已成为与高新技术产业互为依托的产业,模具工业技术水平的高低已成为衡量国家制造业水平的重要标志之一。
二、冷冲模具工业的现状到了21世纪.随着计算机软件的发展和进步.CAD/CAE/CAM技术日臻成熟,其现代模具中的应用越来越广泛。
目前我国冲压模具无论在数量上,还是在质量、技术和能力等方面都已有了很大发展,但与国民经济需求和世界先进水平相比,仍具有较大的差异,一些大型、精密、复杂、长寿命的高档模具每年仍大量进口,特别是中高档轿车的覆盖件模具。
目前仍主要依靠进口。
而一些低档次的简单冲模,则已供.过于求,市场竞争非常激烈。
三、冷冲模具的发展方向发展模具工业的关键是制造模具的技术、相关人才以及模具材料。
模具技术的发展是模具工业发展最关键的—个因素,其发展方向应该为适应模具产品“交货期短”、“精度高”、质量好”和“价格低”的要求服务。
为此,急需发展如下:1.全面推广模具CAD/CAM/CAE技术::随着微机软件发展和进步,普及CAD /CAM/CAE技术的条件已基本成熟,各企业需要加大CAD/CAM技术培训和技术服务的力度,同时进一步扩大CAE技术的应用范围。
2.模具扫描及数字化系统:高速扫描机和模具扫描系统具备从模型或实物扫描到加工出期望的模型所需的诸多功能,这样可以大大缩短模具研制制造周期。
3.电火花加工:电火花加工(EDM)虽然已受到高速铣削的严峻挑战,但其固有特性和独特的加工方法是高速铣削所不能完全替代的。
4.优质材料及先进表面处理技术:选用优质钢材和应用相应的表面处理技术来提高模具的寿命就显得十分必要。
5.模具研磨抛光将自动化、智能化:模具表面的质量对模具使用寿命、制件外观质量等方面均有较大的影响,研究自动化、智能化的研磨与抛光方法替代现有手工操作,提高模具表面质量是重要的发展趋势。
第二章 工艺方案分析及确定第一节 零件工艺性分析如图2-1所示拉深零件,材料为08F ,厚度为1mm 。
其工艺性分析内容如下:图2-1 筒形件拉深零件图1.材料分析此拉深模选用材料为08F08F 是极软的低碳钢,强度、硬度很低,而塑性、韧性极高,具有良好的冷变形性和焊接性,正火后切削加工性尚可,退火后导磁率较高,剩磁较少,但淬透性、淬硬性极低。
因此,此材料具有良好的拉深成形性能。
2.结构分析零件为一无凸缘筒形件,结构简单,底部圆角半径为R3,满足筒形拉深件底部圆角半径大于一倍料厚的要求,因此,零件具有良好的结构工艺性。
3.精度分析零件图上所有未注公差的尺寸,属于自由尺寸,可按IT14级确定工件尺寸的公差。
因此,普通拉深即可达到零件的精度要求。
查公差表可得工件基本尺寸公差为:74.0078+φ 74.0098+ 25.003+R 25.001+4.变形特点的分析1)拉深时的变形区在毛坯的凸缘部分,其它部分为传力区,不参与主要变形;2)毛坯变形区在切向压应力和径向拉应力作用下,产生切向压缩和径向拉长变形;3)极限变形参数主要受到毛坯传力区承载能力的限制。
第二节工艺方法的确定由上面分析可知,为了保证工件的性能,该工件不能一次拉深到位,至少需经过两次拉深。
而完成该工件需经过落料、拉深工序。
综合实际情况,可有以下3种方案(如表格2-1所示)供选择:根据本零件的设计要求以及各方案的特点,决定采用第2种方案比较合理。
第三章 零件工艺计算第一节 拉深工艺计算零件的材料厚度为1mm ,所以所有的计算以中线为准。
1. 确定零件修边余量零件的相对高度23.11785.098≈+-=d h ,由文献[1]表5-2查得修边余量mm 8.3=δ,故修正后拉深件的总高应为mm 3.1018.35.97=+。
2. 确定坯料尺寸DD A A D ni i 计算出由公式∑===144ππ其中:、iA A A A A R d A R R d R A R H d A ∑=++=∑=-=+-=-=3212232214D )2(4]8)2(2[4)(πππππ而mm d 79=带入数值 mm H 3.101= mm R 5.3= mm D 8.194≈算得3. 判断是否采用压边圈零件的相对厚度%51.0%1008.1941%100=⨯=⨯D t ,由文献[2]表4-11知:该拉深工艺须采用压边圈。
4. 确定拉深次数先判断能否一次拉出406.08.19479≈==D d m 总零件的总拉深系数由文献[1]表5-3, 56.01=m 取,78.0=n m , 由此可知:56.0406.01=<=m m 总,故判断不能一次拉深成形。
故可根据公式nn m D m d n lg )lg(lg 11-+=求得289.2≈n 取较大整数:3=n5. 确定各次拉深半成品尺寸1)调整各次拉深系数,使各次拉深后系数均大于文献[1]表5-3查得的相应极限拉深系数。
调整后,实际选取6.01=m ,81.02=m ,83.03=m 。
所以各次拉深的直径确定为:m m 88.116m m 8.1946.011=⨯==D m d m m 67.94m m 88.11681.0122=⨯==d m d m m79m m 67.9483.0233=⨯==d m d2)各次半成品的高度计算:取各次的r 凹分别为: 由文献[1]表5-18取r 1=8t=8mm, r 2=(0.6-0.8)r 1=(4.8-6.4)mm 取r 2=5mm,r 3=3.5mm则由公式可计算出各次h :)32.0(43.0)(25.01111111r d d r d Dk h ++-=)32.0(43.0)(25.022222212r d d r d k Dk h ++-=)32.0(43.0)(25.0333333213r d d r d k k Dk h ++-=其中n n m k 1=,1-=n n n d m d 。
在将所有已知数据带入可求得:h 1=55.5mm, h 2=78.7mm, h 3=122.3mm6. 拉深件工序尺寸图根据前面分析计算,可知本零件须三次拉深,各工序尺寸如图3-1所示图3-1各工序尺寸图7.排样计算零件采用单直排排样方式,查得零件间的搭边值为0.8mm ,零件与条料侧边之间的搭边值为1.0mm ,若模具采用无侧压装置的导料板结构,则条料上零件的步距S=D+a=194.8+0.8=195.6mm ,条料的宽度应为mm 8.196m m )0.128.194()2(07.007.00max --∆-=⨯+=+=a D B故一个步距内的材料利用率1η为: 1η=A/BS ⨯100=π2)2/(D /BS ⨯10000=π(194.8/2)2/(196.8×195.6)×100%=77.4零件的排样图如图3-2所示:图3-2 排样图第二节 拉深压力计算与设备的选择1. 首次拉深模具为落料拉深复合模,动作顺序是先落料后拉深,现分别计算落料力落F拉深力拉F 和压边力压F 。
kN 6.234N 234576N29518.19414.33.1≈=⨯⨯⨯⨯==τKLt F 落 落卸卸P K P =式中卸K —卸料系数,查参考文献[2]表2-17知04.0=卸K ~0.05,取04.0=卸K 。
所以 38.923457604.0=⨯=卸P KNkN 92N 202690.85952188.16114.311≈=⨯⨯⨯⨯==K t d F b σπ拉由文献[3]表4-10查取K1=0.85由文献[3]表4-12查取P=2.75落压拉F kN F F <=+=+1081692 ,所以,应按照落料力的大小选用设备。
初选设备为J23-35.2.二次拉深:kN 70N 015470.8952167.4914.3222≈=⨯⨯⨯⨯==K t d F b σπ拉由文献[3]表4-10查取K2=0.8根据以上力的计算,初选设备为J23-10.3.末次拉深:kN 54N 415150.7495219714.3333≈=⨯⨯⨯⨯==K t d F b σπ拉由文献[3]表4-10查取K3=0.744.压力中心的计算图3-3 压力中心图由于是圆形工件,如图3-3所示,所以工件的压力中心应为圆心即O(97.4,97.4) 5.压力设备的选择1) 落料拉深复合模设备的选用kN16N 6.15927N75.2])8288.116(8.194[4])2[422212≈=⨯⨯+-=+-=ππ,(压P r d D F A根据以上计算,同时考虑拉深件的高度选取开式双柱可倾压力机JH23-40, 由文献[2]表9-9查取其主要技术参数为: 公称压力:400KN 滑块行程:80mm 最大装模高度:330mm 连杆调节长度:65mm工作台尺寸:700460⨯mm mm 模柄孔尺寸:7050⨯mm φmm 垫板厚度:65mm2) 第二三次拉深模设备的选用考虑零件的高度,选取开式双柱可倾压力机JH23-80,以保证拉深的顺利操作,其主要技术参数如下:公称压力:800KN 滑块行程:130mm 最大装模高度:380mm 连杆调节长度:90mm工作台尺寸:800540⨯mm mm 模柄孔尺寸:8060⨯mm φmm 垫板厚度:100mm第三节 拉深模工作零件设计与计算一、凸、凹模刃口尺寸计算1.首次拉深凸、凹模尺寸的刃口尺寸计由上边计算可知:第一次拉深件后零件直径为116.88mm ,由公式t Z 2.1=确定拉深凸、凹模间隙值Z ,所以间隙mm 2.1mm 12.1=⨯=Z ,则拉深凹模直径mm63.118mm )2.1287.04.088.115()4.0(08.0008.000min A +++=⨯+⨯+=+∆+=A Z D D δ拉深凹模刃口尺寸如图3-4所示图3-4 拉深凹模刃口尺寸图拉深凸模直径mm23.116)87.04.088.115()4.0(005.0005.00min T ---=⨯+=∆+=T d D δ拉深凸模刃口尺寸如图3-5所示图3-5 拉深凸模刃口尺寸图2.二次拉深凸、凹模尺寸刃口尺寸计算由文献[2]表2-8查取Z=1.1拉深凹模直径m m22.96m m )1.1287.04.067.93()4.0(08.0008.000min A +++=⨯+⨯+=+∆+=A Z D D δ拉深凹模刃口尺寸如图3-6所示图3-6拉深凹模刃口尺寸图拉深凸模直径mm02.94)87.04.067.93()4.0(005.0005.00min T ---=⨯+=∆+=T d D δ拉深凸模刃口尺寸如图3-7所示图3-7 拉深凸模刃口尺寸图 3.末次拉深凸、凹模尺寸计算由文献[2]表2-8查取Z=1.05拉深凹模直径mm4.80mm )05.1274.04.078()4.0(08.0008.000min A +++=⨯+⨯+=+∆+=A Z D D δ拉深凹模刃口尺寸如图3-8所示图3-8拉深凹模刃口尺寸图拉深凸模直径mm3.78)74.04.078()4.0(005.0005.00min T ---=⨯+=∆+=T d D δ拉深凸模刃口尺寸如图3-9所示图3-9 拉深凸模刃口尺寸图二、落料拉深复合模其它工艺计算根据零件形状特点,刃口尺寸计算采用分开制造法。