低温精馏原理及精馏塔
精馏塔的工作原理
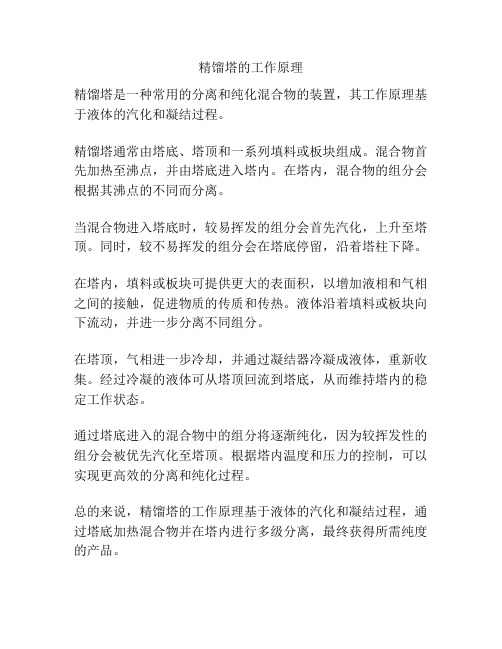
精馏塔的工作原理
精馏塔是一种常用的分离和纯化混合物的装置,其工作原理基于液体的汽化和凝结过程。
精馏塔通常由塔底、塔顶和一系列填料或板块组成。
混合物首先加热至沸点,并由塔底进入塔内。
在塔内,混合物的组分会根据其沸点的不同而分离。
当混合物进入塔底时,较易挥发的组分会首先汽化,上升至塔顶。
同时,较不易挥发的组分会在塔底停留,沿着塔柱下降。
在塔内,填料或板块可提供更大的表面积,以增加液相和气相之间的接触,促进物质的传质和传热。
液体沿着填料或板块向下流动,并进一步分离不同组分。
在塔顶,气相进一步冷却,并通过凝结器冷凝成液体,重新收集。
经过冷凝的液体可从塔顶回流到塔底,从而维持塔内的稳定工作状态。
通过塔底进入的混合物中的组分将逐渐纯化,因为较挥发性的组分会被优先汽化至塔顶。
根据塔内温度和压力的控制,可以实现更高效的分离和纯化过程。
总的来说,精馏塔的工作原理基于液体的汽化和凝结过程,通过塔底加热混合物并在塔内进行多级分离,最终获得所需纯度的产品。
(完整版)精馏塔工作原理

精馏塔单元一、工作原理简述二、典型精馏塔动画演示三、工艺流程简介四、组态画面及设施说明一、工作原理简述精馏是化工生产中分别互溶液体混淆物的典型单元操作,其本质是多级蒸馏,即在必定压力下,利用互溶液体混淆物各组分的沸点或饱和蒸汽压不一样,使轻组分(沸点较低或饱和蒸汽压较高的组分)汽化,经多次部分液相汽化和部分气相冷凝,负气相中的轻组分和液相中的重组分浓度渐渐高升,进而实现分别。
精馏过程的主要设施有:精馏塔、再沸器、冷凝器、回流罐和输送设施等。
精馏塔以进料板为界,上部为精馏段,下部为提留段。
必定温度和压力的料液进入精馏塔后,轻组分在精馏段渐渐浓缩,走开塔顶后所有冷凝进入回流罐,一部分作为塔顶产品(也叫馏出液),另一部分被送入塔内作为回流液。
回流液的目的是增补塔板上的轻组分,使塔板上的液体构成保持稳固,保证精馏操作连续稳固地进行。
而重组分在提留段中浓缩后,一部分作为塔釜产品(也叫残液),一部分则经再沸器加热后送回塔中,为精馏操作供给必定量连续上涨的蒸气气流。
二、精馏塔动画演示1.板式塔构造2.板式塔工作原理三、工艺流程简介本单元是一种加压精馏操作,原料液为脱丙烷塔塔釜的混淆液,分别后馏出液为高纯度的 C4 产品,残液假如C5 以上组分。
67.80C 的原料液经流量调理器FIC101 控制流量( 14056Kg/h)后,从精馏塔 DA405 的第 16 块塔板(全塔共32 块塔版)进料。
塔顶蒸气经全凝器EA419 冷凝为液体后进入回流罐FA408;回流罐 FA408 的液体由泵 GA412A/B 抽出,一部分作为回流液由调理器FC104 控制流量( 9664KG/H)送回 DA405 第 32 层塔板;另一部分则作为产品,其流量由调理器 FC103 控制( 6707Kg/h)。
回流罐的液位由调理器 LC103 与 FC103 构成的串级控制回路控制。
DA405 操作压力由调理器 PC102 分程控制为。
低温精馏原理及精馏塔
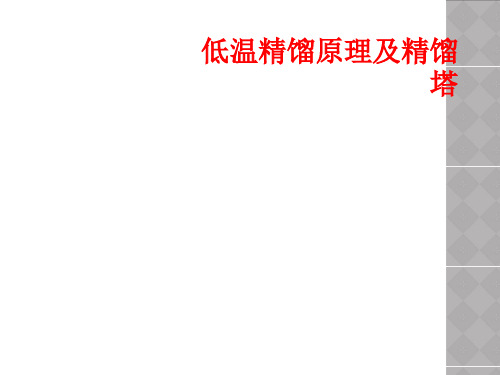
上塔压力低些有什么好处
上塔的低温产品气体出塔后要通过换热器回收冷量,经复热后再离开装置。上塔的压力 需要能够克服气体在通过换热器时的阻力。但是,要求在满足需要的情况下,尽可能地 低。这是因为:
1)在压冷力凝相蒸应发地器会中自冷动凝降的低液。氮通量常不,变上、塔主压冷力温降差低不0.变01得MP情a,况下下塔,压如力果可上降塔低压0力.0降3M低P,a。则对下于塔 全低压制氧机,随着下塔压力降低,空压机的排气压力也可降低,进塔空气量会增加, 从而可以增加氧产量和降低制氧机的能耗。
得下塔顶部压力。
5)下塔底部压力的确定 下塔底部压力等于下塔顶部加上塔塔板总阻力。 P下塔底=△P下塔板+P下塔顶
温度为进下塔饱和空气温度
双级精馏塔的物料平衡和能量平衡
物量平衡:即入塔的空气量等于出塔的分离氧、氮之和。 组分平衡:空气分离后所得的各气体中某一组分量的总和等于加工空气两种该组分的
氮产品。由此可见,如果下塔提供的中间产品不合格,上塔是很难生产出纯度和数量都合乎要求的氧、 氮产品的。这是因为在设计上塔时,是根据氧、氮产品的数量和一定的液空和液氮量计算出上塔的回流 比,再根据液空和液氮的纯度和回流比以及一定的操作压力,确定为分离出合格产品所需要的塔板数。 对全低压流程的上塔,还需要考虑膨胀空气的影响。也就是说,只有当液空、液氮的数量和纯度以及膨 胀空气进入上塔的状态和数量都符合要求,并在规定的操作压力下,经过这么多块塔板的精馏,才能获 得纯度和数量都合格的产品。如果液空和液氮的纯度和数量改变了,上塔回流比一定会发生变化,如果 还是用这么多块塔板来进行精馏,就不能得到纯度和数量都符合要求的产品了。因此,下塔工况的调整 就成为从上塔获得合格产品的基础。
2)上塔底部压力和温度的确定。
精馏塔的工作原理

精馏塔的工作原理
精馏塔是一种用于分离液体混合物的设备,其工作原理基于不同组分的沸点差异。
在精馏塔内,液体混合物被加热至沸点,然后通过塔内的填料或塔板进行分离。
本文将介绍精馏塔的工作原理及其应用。
首先,精馏塔内的液体混合物被加热至沸点。
在加热的过程中,液体混合物中
沸点较低的组分首先蒸发,形成蒸汽。
蒸汽与塔内填料或塔板接触,发生传质和传热过程。
其次,填料或塔板的设计能够提供大量的表面积,使得蒸汽和液体之间能够充
分接触。
这种充分接触使得液体混合物中沸点较低的组分易于从液相转移到蒸汽相,从而实现分离。
最后,蒸汽在塔内上升时,逐渐冷却凝结成液体,这些液体被收集并成为产品。
而未被蒸发的液体则向下流动,经过多次回流和再沸馏,最终得到所需的产品。
精馏塔的工作原理可以应用于许多领域,例如石油化工、化学工程、食品加工等。
在石油化工中,精馏塔被广泛用于原油的分馏,将原油中的不同碳链长度的烃类分离出来,得到汽油、柴油、煤油等产品。
在化学工程中,精馏塔可用于分离和提纯化学品,如酒精、醋酸等。
在食品加工中,精馏塔可用于提取天然香料和酒精等。
总之,精馏塔的工作原理基于不同组分的沸点差异,通过加热、蒸发、冷凝等
过程,实现了液体混合物的分离。
它在化工领域有着广泛的应用,为生产提供了重要的分离技术支持。
精馏塔的原理及控制要求
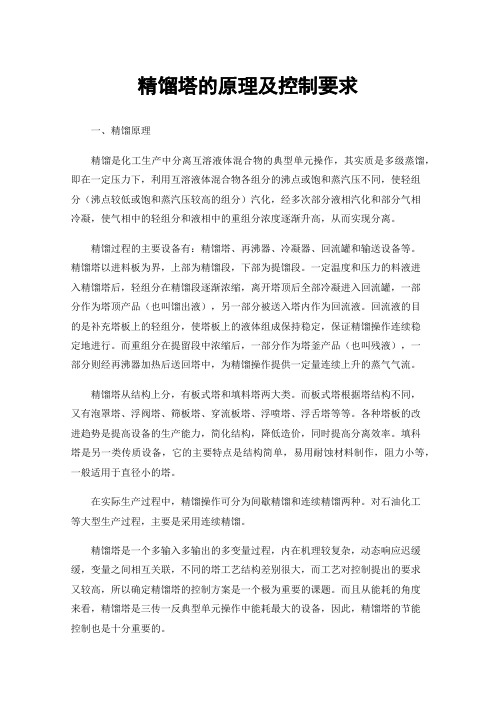
精馏塔的原理及控制要求一、精馏原理精馏是化工生产中分离互溶液体混合物的典型单元操作,其实质是多级蒸馏,即在一定压力下,利用互溶液体混合物各组分的沸点或饱和蒸汽压不同,使轻组分(沸点较低或饱和蒸汽压较高的组分)汽化,经多次部分液相汽化和部分气相冷凝,使气相中的轻组分和液相中的重组分浓度逐渐升高,从而实现分离。
精馏过程的主要设备有:精馏塔、再沸器、冷凝器、回流罐和输送设备等。
精馏塔以进料板为界,上部为精馏段,下部为提馏段。
一定温度和压力的料液进入精馏塔后,轻组分在精馏段逐渐浓缩,离开塔顶后全部冷凝进入回流罐,一部分作为塔顶产品(也叫馏出液),另一部分被送入塔内作为回流液。
回流液的目的是补充塔板上的轻组分,使塔板上的液体组成保持稳定,保证精馏操作连续稳定地进行。
而重组分在提留段中浓缩后,一部分作为塔釜产品(也叫残液),一部分则经再沸器加热后送回塔中,为精馏操作提供一定量连续上升的蒸气气流。
精馏塔从结构上分,有板式塔和填料塔两大类。
而板式塔根据塔结构不同,又有泡罩塔、浮阀塔、筛板塔、穿流板塔、浮喷塔、浮舌塔等等。
各种塔板的改进趋势是提高设备的生产能力,简化结构,降低造价,同时提高分离效率。
填科塔是另一类传质设备,它的主要特点是结构简单,易用耐蚀材料制作,阻力小等,一般适用于直径小的塔。
在实际生产过程中,精馏操作可分为间歇精馏和连续精馏两种。
对石油化工等大型生产过程,主要是采用连续精馏。
精馏塔是一个多输入多输出的多变量过程,内在机理较复杂,动态响应迟缓缓,变量之间相互关联,不同的塔工艺结构差别很大,而工艺对控制提出的要求又较高,所以确定精馏塔的控制方案是一个极为重要的课题。
而且从能耗的角度来看,精馏塔是三传一反典型单元操作中能耗最大的设备,因此,精馏塔的节能控制也是十分重要的。
二、精馏塔的主要干扰因素精馏塔的主要干扰因素为进料状态,即进料流量F、进料组分zf ,进料温度Tf或热焓FE.此外,冷剂与加热剂的压力和温度及环境温度等因素也会影响精馏塔的平衡操作。
精馏塔原理
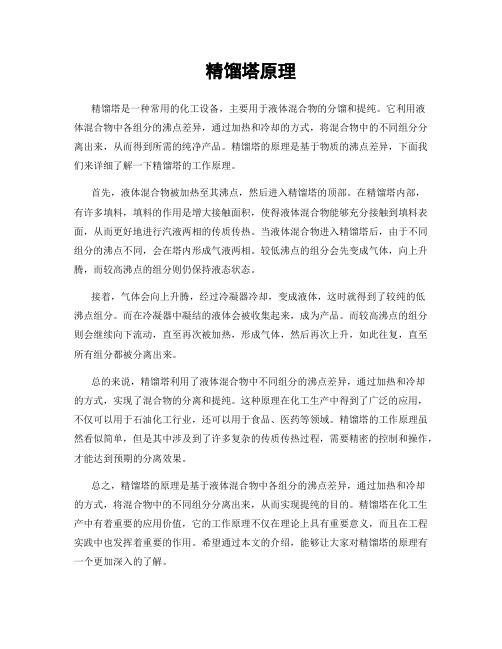
精馏塔原理精馏塔是一种常用的化工设备,主要用于液体混合物的分馏和提纯。
它利用液体混合物中各组分的沸点差异,通过加热和冷却的方式,将混合物中的不同组分分离出来,从而得到所需的纯净产品。
精馏塔的原理是基于物质的沸点差异,下面我们来详细了解一下精馏塔的工作原理。
首先,液体混合物被加热至其沸点,然后进入精馏塔的顶部。
在精馏塔内部,有许多填料,填料的作用是增大接触面积,使得液体混合物能够充分接触到填料表面,从而更好地进行汽液两相的传质传热。
当液体混合物进入精馏塔后,由于不同组分的沸点不同,会在塔内形成气液两相。
较低沸点的组分会先变成气体,向上升腾,而较高沸点的组分则仍保持液态状态。
接着,气体会向上升腾,经过冷凝器冷却,变成液体,这时就得到了较纯的低沸点组分。
而在冷凝器中凝结的液体会被收集起来,成为产品。
而较高沸点的组分则会继续向下流动,直至再次被加热,形成气体,然后再次上升,如此往复,直至所有组分都被分离出来。
总的来说,精馏塔利用了液体混合物中不同组分的沸点差异,通过加热和冷却的方式,实现了混合物的分离和提纯。
这种原理在化工生产中得到了广泛的应用,不仅可以用于石油化工行业,还可以用于食品、医药等领域。
精馏塔的工作原理虽然看似简单,但是其中涉及到了许多复杂的传质传热过程,需要精密的控制和操作,才能达到预期的分离效果。
总之,精馏塔的原理是基于液体混合物中各组分的沸点差异,通过加热和冷却的方式,将混合物中的不同组分分离出来,从而实现提纯的目的。
精馏塔在化工生产中有着重要的应用价值,它的工作原理不仅在理论上具有重要意义,而且在工程实践中也发挥着重要的作用。
希望通过本文的介绍,能够让大家对精馏塔的原理有一个更加深入的了解。
低温精馏原理及精馏塔
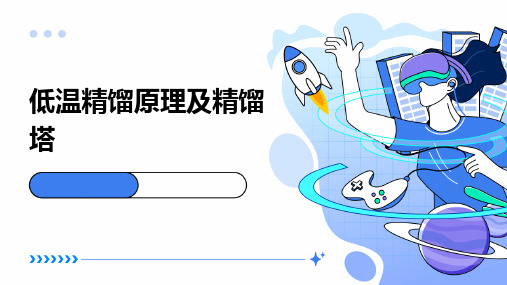
将预处理后的原料液加入精馏 塔中,控制进料流量和温度。
回流
将部分塔顶蒸汽冷凝后回流至 塔内,以提供更多的蒸汽和热 量,促进组分分离。
原料液预处理
对原料液进行预处理,如加热、 过滤、离心等,以去除杂质和 悬浮物。
加热
通过加热装置将原料液加热至 沸腾状态,使不同组分的蒸汽 得以分离。
采出
根据需要从塔底或塔顶采出产 品,如馏分油或水。
质。
填料塔
填料塔内填充有一定高度的填料, 液体自上而下通过填料,气体自下 而上通过填料,通过传质元件实现 液气传质。
流化床塔
流化床塔内装有大量固体颗粒作为 传质元件,液体和气体分别从底部 和顶部进入,在流化床内实现传质。
精馏塔的设计原则
分离效率高
能耗低
稳定性好
易于维护和操作
精馏塔应具有较高的分 离效率,确保产品纯度
低温精馏是指在低温条件下,利用物质间不同的沸点、蒸汽压等特性,通过精馏 塔进行分离的过程。
低温精馏通常用于分离和提纯气体、液体或低熔点固体混合物,特别适用于高纯 度气体、液体或特殊材料的分离。
低温精馏的原理和特点
原理
基于物质间沸点的不同,通过加热和 冷凝的方法,使混合物在精馏塔内逐 级分离。
特点
低温精馏具有高纯度、高回收率、低 能耗等优点,但也存在设备成本高、 操作难度大等挑战。
01
02
03
日常检查
每天对精馏塔进行外观检 查,查看塔体是否有裂缝、 变形、腐蚀等问题。
运行监控
通过仪表监控精馏塔的运 行参数,如压力、温度、 液位等,确保其在正常范 围内。
阀门和管道检查
定期对精馏塔的阀门、管 道进行检查,确保其密封 良好,无泄漏。
化工精馏原理

化工精馏原理
精馏是一种分离技术,用于将混合物中的组分通过升华和冷凝的方式进行分离。
该过程基于分子之间的不同挥发性和沸点的差异。
精馏的基本原理是利用组分在不同温度下的汽化和冷凝特性。
在精馏塔内,混合物被加热,使得易挥发的组分蒸发成气体,然后通过冷凝器冷却,转变回液体。
随后,这些液体进入分馏塔的不同部位,从而实现对组分的分离。
在精馏塔内,由于塔的高度,温度逐渐降低。
这导致组分的挥发性逐渐降低,使其向下凝结,并最终收集在不同的容器中。
高挥发性的组分在较低温度下首先凝结,低挥发性的组分在较高温度下凝结。
精馏塔内的分馏效果取决于各种因素,包括初始混合物的成分、入口温度、压力、塔的结构和精馏塔体系的设计等。
通过调整这些参数,可以实现较高效率的分离效果。
化工精馏广泛应用于石油、化工、制药等行业。
它可以用于分离原油、制取石油产品,提取溶剂、纯化有机化合物,以及获得高纯度的化学品等。
精馏技术的不断改进和创新也不断提高着分离效率和产品质量。
- 1、下载文档前请自行甄别文档内容的完整性,平台不提供额外的编辑、内容补充、找答案等附加服务。
- 2、"仅部分预览"的文档,不可在线预览部分如存在完整性等问题,可反馈申请退款(可完整预览的文档不适用该条件!)。
- 3、如文档侵犯您的权益,请联系客服反馈,我们会尽快为您处理(人工客服工作时间:9:00-18:30)。
哪些因素会影响塔板阻力的变化,观察 塔板阻力对操作有何实际意义?
影响塔板阻力的因素很多,包括筛孔孔径大小、塔板开孔率、 液体的密度、液体的表面张力、液层厚度、蒸气的密度和蒸 气穿过筛孔的速度等等。其中,蒸气和液体的密度以及液体 的表面张力在生产过程中变化很小。孔径大小与开孔率虽然 固定不变,但当筛孔被固体二氧化碳或硅胶粉末堵塞时,也 会发生变化,造成阻力增大。此外,液层厚度和蒸气的筛孔 速度取决于下流液体量和上升蒸气量的多少,在操作中也有 可能发生变化,从而影响塔板阻力的变化。特别是筛孔速度 对阻力的影响是成平方关系,影响较大。 所以,在实际操作中,可以通过塔内各部分阻力的变化来判 断塔内工况是否正常。如果阻力正常,说明塔内上升蒸气的 速度和下流液体的数量正常。如果阻力增高,则可能是某一 段上升蒸气量过大或塔板筛孔堵塞;如果进塔空气量、膨胀 空气量以及氧、氮、污氮取出量都正常,也即上升气量没有 变化,那就可能是某一段下流液体量大了,使塔板上液层加 厚,造成塔板阻力增加;如果阻力超过正常数值,并且产生 波动,则很可能是塔内产生了液悬;当阻力过小时,有可能 是上升蒸气量太少,蒸气无法托住塔板上的液体而产生漏液 现象。因此阻力大小往往可作为判断工况是否正常的一个重 要手段。
2)上塔底部压力和温度的确定。 上塔底部压力是指上塔最后一块塔板下面, 液氧面上压力。等于上塔顶部加上塔塔 板总阻力。 P上塔底=△P上塔板+P上塔顶 =0.015+0.12=0.135MPa 上塔底部的温度是液氧面上氧气的饱和温 度,它由氧纯度和压力决定。根据底部压 力和氧气浓度查气、液平衡图得上塔低 部温度。 T上塔顶=92.8K
上塔压力低些有什么好处
上塔的低温产品气体出塔后要通过换热器回收冷量,经 复热后再离开装置。上塔的压力需要能够克服气体在通 过换热器时的阻力。但是,要求在满足需要的情况下, 尽可能地低。这是因为: 1)在冷凝蒸发器中冷凝的液氮量不变、主冷温差不变得 情况下,如果上塔压力降低,则下塔压力相应地会自动 降低。通常,上塔压力降低0.01MPa,下塔压力可降低 0.03MPa。对于全低压制氧机,随着下塔压力降低,空 压机的排气压力也可降低,进塔空气量会增加,从而可 以增加氧产量和降低制氧机的能耗。 2)上、下塔压力降低,可改善上、下塔的精馏工况。因为 压力低时,液体中某一组分的含量与其上方处于相平衡 的蒸气中同一组分的含量的差数要大些,而压力高时此 差数会减小。气、液相浓度差越大,则氧、氮的分离效 果越好。即在塔板数不变的情况下,压力低一些,有利 于提高氧、氮的纯度。因此在操作时,要尽可能降低上 塔压力。 应指出,上塔压力降低是有限的。因为氧、氮产品的排 出压力有一定要求,在排出过程中,还要克服换热器和 管道的阻力。
下塔的物料平衡和能量平衡
V空=V液空+V液氮 V空y空=V液空x液空+V液氮x液氮 • V空h空+Q下跑冷 • =V液空h液空+V液氮h液氮+Q下主冷
上塔的物料平衡和能量平衡
V氧+V氮=V液空+V液氮= V空 V空y空=V氧y 氧+V氮y 氮 • V 氧h 氧+ V 氮 h 氮 • =V液空h液空+V液氮h液氮+Q上主冷+Q上跑冷
精馏塔内的空气是怎样被分离成氧和来自的压缩空气经清除水分、二氧化碳,并在热交换器中被冷却及膨 胀(对中压流程)后送入下塔的下塔,作为下塔的上升气。 因为它含氧21%,在0.6MPa下,对应的饱和温度为100.05K。 在冷凝蒸发器中冷凝的液氮从下塔的顶部下流,作为回流液 体。因其含氧为0.01%~1%,在0.6Mpa下的饱和温度约为 96.3K。由此可见,精馏塔下部的上升蒸气温度高,从塔顶下 流的液体温度较低。下塔的上升气每经过一块塔板就遇到比 它温度低的液体,气体本身的温度就要降低,并不断有部分 蒸气冷凝成液体。由于氧是难挥发组分,氮是易挥发组分, 在冷凝过程中,氧要比氮较多地冷凝下来,于是剩下的蒸气 中含氮浓度就有所提高。就这样一次、一次地进行下去,到 塔顶后,蒸气中的氧绝大部分已被冷凝到液体中去了,其含 氮浓度高达99%以上。这部分氮气被引到冷凝蒸发器中,放 出热量后全部冷凝成液氮,其中一部分作为下塔回流液从上 往下流动。液体在下流的过程中,每经过一块塔板遇到下面 上升的温度较高的蒸气,吸热后有一部分液体就要气化。在 气化过程中,由于氮是易挥发组分,氧是难挥发组分,因此 氮比氧较多地蒸发出来,剩下的液体中氧纯度就有所提高。 这样一次、一次地进行下去,到达塔底就可以得到氧含量为 38%~40%的液空。因此,经过下塔的精馏,可将空气初步 分离成含氧38%~40%的液空和含氮99%以上的液氮。
调整下塔纯度是调整上塔纯度的基础
双级精馏塔分离空气是先将空气在下塔分离成富氧液空 和液氮,然后再送到上塔进一步分离成纯氧和纯氮产品。 由此可见,如果下塔提供的中间产品不合格,上塔是很 难生产出纯度和数量都合乎要求的氧、氮产品的。这是 因为在设计上塔时,是根据氧、氮产品的数量和一定的 液空和液氮量计算出上塔的回流比,再根据液空和液氮 的纯度和回流比以及一定的操作压力,确定为分离出合 格产品所需要的塔板数。对全低压流程的上塔,还需要 考虑膨胀空气的影响。也就是说,只有当液空、液氮的 数量和纯度以及膨胀空气进入上塔的状态和数量都符合 要求,并在规定的操作压力下,经过这么多块塔板的精 馏,才能获得纯度和数量都合格的产品。如果液空和液 氮的纯度和数量改变了,上塔回流比一定会发生变化, 如果还是用这么多块塔板来进行精馏,就不能得到纯度 和数量都符合要求的产品了。因此,下塔工况的调整就 成为从上塔获得合格产品的基础。
双级精馏塔内温度、压力确定
1)上塔顶部压力和温度确定 上塔顶部压力等于氮气克服流过各换热 器,阀门和管道阻力及排出时所必须的 压力之和。 P上塔顶=△P设备+P排氮 =0.015+0.105=0.12MPa 上塔顶部的温度与顶部压力和氮气浓度 有关,根据顶部压力和氮气浓度查气、 液平衡图得上塔顶部温度。 T上塔顶=78.16K
5)下塔底部压力的确定 下塔底部压力等于下塔顶部加上塔塔板总 阻力。 P下塔底=△P下塔板+P下塔顶 温度为进下塔饱和空气温度
双级精馏塔的物料平衡和能量平衡
物量平衡:即入塔的空气量等于出塔的 分离氧、氮之和。 组分平衡:空气分离后所得的各气体中 某一组分量的总和等于加工空气两种该 组分的量。 能量平衡:即进入塔内的热量(包括冷 损)总和应等于出塔产品的热量之和。
低温精馏原理及精馏塔
1.概述 1.概述
低温法空气分离步骤:首先使加 工空气液化,然后利用氧、氮等组分 的沸点差,采用精馏的方法使空气分 离获得氧气和氮气。
对两种沸点不同的物质(例如氧与氮)组成 的混合液体,在吸收热量而部分蒸发时,易挥发 组分氮将较多地蒸发;而混合蒸气在放出热量而 部分冷凝时,难挥发组分氧将较多地冷凝。如果 将温度较高的饱和蒸气与温度较低的饱和液体接 触,则蒸气将放出热量给饱和液体。蒸气放出热 量将部分冷凝,液体将吸收热量而部分蒸发。蒸 气在部分冷凝时,由于氧冷凝得较多,所以蒸气 中的低沸点组分(氮)的浓度有所提高。如果进 行了一次部分蒸发和部分冷凝后,氮浓度较高的 蒸气及氧浓度较高的液体,再分别与温度不同的 液体及蒸气进行接触,再次发生部分冷凝及部分 蒸发,使得蒸气中的氮浓度及液体中的氧浓度将 进一步提高,这样的过程进行多次,蒸气中的氮 浓度越来越高,液体中的氧浓度越来越高,最终 达到氧、氮的分离。这个过程就叫精馏。
3)冷凝蒸发器中液氧的平均压力和平均 温度的确定。 冷凝蒸发器液氧面上的压力即为上塔底 部压力。液氧底部压力等于液氧面上的 压力加上液氧柱产生静压。 P液氧底=P上塔底+ h液氧*液氧密度 T液氧平均= ( T液氧面+ T液氧底)/2
4)下塔顶部压力和温度确定 △ T主冷= T氮冷凝- T液氧平均 下塔顶部压力和氮气浓度及氮冷凝温度有 关,根据冷凝温度和氮气浓度查气、液 平衡图得下塔顶部压力。
然后将液空经节流降压后送到上塔中部,作为进一步 精馏的原料。与下塔精馏的原理相同,液体下流时, 经多次部分蒸发,氮较多地蒸发出来,于是下流液体 中的含氧浓度不断提升,达到上塔底部可得到含氧 99.2%~99.6%的液氧。从液空进料口至上塔底部塔 板上的精馏是提高难挥发组分的浓度,叫提馏段。这 部分液氧在冷凝蒸发器中吸热而蒸发成气氧,在 0.14Mpa下它的温度为93.7K左右。一部分气氧作为 产品引出,大部分作为上塔的上升气。在上升过程中, 部分蒸气冷凝,蒸气中的氮含量不断增加。由于上塔 中部液空入口处的上升气中还有较多的氧组分,如果 将它放掉,氧的损失太大,所以应再进行精馏。从冷 凝蒸发器中引出部分含氮99%以上的液氮节流后送至 上塔顶部,作为回流液,蒸气再进行多次部分冷凝, 同时回流液多次部分蒸发。其中氧较多地留在液相里, 氮较多地蒸发到气相中,到了上塔顶,便可得到含氮 99%以上的氮气。从液氮进料口到液空进料口是为了 进一步提高蒸气中低沸点组分(氮)的浓度,叫精馏 段。如果需要纯氮产品还需要再次精馏,才能得到含 氮99.99%的纯氮产品。这就是精馏塔内将空气分离 成氧、氮的过程。
为什么全低压空分设备能将膨胀空 气直接送入上塔
全低压空分设备的冷量大部分靠膨胀机产生,而全低压空分 设备的工作压力即为下塔的工作压力,为0.55~0.65MPa。 该压力的气体在膨胀机膨胀制冷后,压力为0.13MPa左右, 已不可能像中压流程那样送入下塔参与精馏。如果膨胀后的 空气只在热交换器内回收冷量,不参加精馏,则这部分加工 空气中的氧、氮就不能提取,必将影响到氧、氮的产量和提 取率。 由于在全低压空分设备的上塔其精馏段的回流比大于最小回 流比较多,就有可能利用多余回流液的精馏潜力。因此可将 膨胀后的空气直接送入上塔参与精馏,来回收膨胀空气中的 氧、氮,以提高氧的提取率。 由于全低压空分设备将膨胀空气直接送入上塔,因此制冷量 的变化将引起膨胀量的变化,必然要影响上塔的精馏。制冷 与精馏的紧密联系是全低压空分设备的最大特点。
进上塔的膨胀空气量受什么条件限制