混凝土强度偏低原因分析
工程混凝土强度不足的原因及处理方案

工程混凝土强度不足的原因及处理方案工程建设施工规范规定了结构混凝土的强度等级必须符合设计要求。
然而,仍有一些工程的混凝土因强度不足而造成不少质量问题。
混凝土强度低下会导致结构构件承载力下降,抗渗、抗冻性能及耐久性下降。
因此,必须认真分析处理混凝土强度不足问题。
混凝土强度不足的常见原因包括原材料质量问题和其他因素。
原材料质量问题包括水泥质量不良和骨料(砂、石)质量不良。
水泥质量不良可能是由于水泥出厂质量差,或者储存时间过长,造成水泥结块,活性降低而影响强度。
另外,水泥熟料中含有过多的游离氧化钙(CaO)或游离氧化镁(MgO),有时也可能由于掺入石膏过多而造成水泥安定性不合格。
这些都会破坏水泥结构,导致混凝土开裂,降低混凝土强度。
骨料质量不良也会导致混凝土强度不足。
石子强度低、石子体积稳定性差、石子形状与表面状态不良、以及骨料中有机杂质含量高等问题都会影响混凝土强度。
例如,针片状石子含量高会影响混凝土强度,而具有粗糙的和多孔的表面的石子对混凝土强度产生有利的影响,尤其是抗弯和抗拉强度。
因此,在工程建设过程中,必须严格控制原材料的质量,避免使用质量不良的水泥和骨料。
同时,对于已经出现混凝土强度不足的情况,需要认真分析原因,并采取相应的处理措施,以确保工程质量。
5)黏土和粉尘含量高会导致混凝土强度下降。
这是因为微小的颗粒会包裹在骨料表面,影响骨料和水泥的粘结。
此外,这些颗粒会增加骨料表面积,需要更多的水来混合。
黏土颗粒也会干缩湿胀,对混凝土造成一定的破坏。
6)高含量的三氧化硫会对混凝土产生不利影响。
骨料中含有硫铁矿或生石膏等硫化物或硫酸盐,当三氧化硫含量较高时,可能会与水泥的水化物作用,产生硫铝酸钙,导致混凝土体积膨胀,裂缝和强度下降。
7)高含量的云母会对混凝土的物理力学性能产生不利影响。
云母表面光滑,与水泥石的粘结性能极差,容易沿节理裂开。
3)拌合水质量不合格也会导致混凝土物理力学性能下降。
使用有机杂质含量较高的沼泽水、含有腐殖酸或其它酸、盐(特别是硫酸盐)的污水和工业废水会对混凝土产生不利影响。
商品混凝土强度不足的原因分析及预防措施
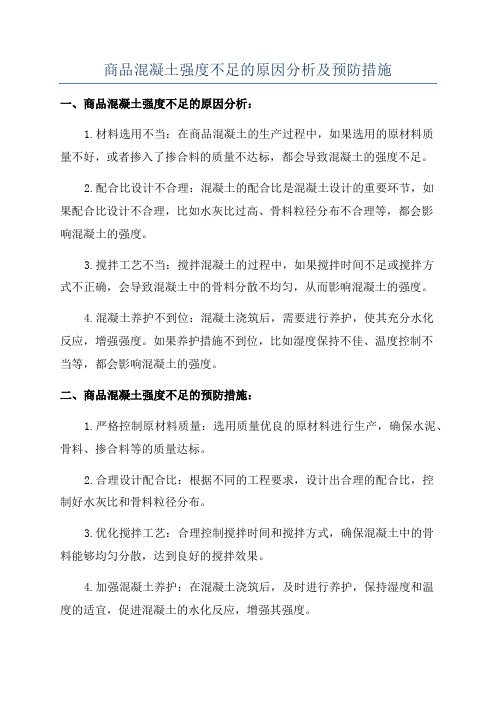
商品混凝土强度不足的原因分析及预防措施一、商品混凝土强度不足的原因分析:1.材料选用不当:在商品混凝土的生产过程中,如果选用的原材料质量不好,或者掺入了掺合料的质量不达标,都会导致混凝土的强度不足。
2.配合比设计不合理:混凝土的配合比是混凝土设计的重要环节,如果配合比设计不合理,比如水灰比过高、骨料粒径分布不合理等,都会影响混凝土的强度。
3.搅拌工艺不当:搅拌混凝土的过程中,如果搅拌时间不足或搅拌方式不正确,会导致混凝土中的骨料分散不均匀,从而影响混凝土的强度。
4.混凝土养护不到位:混凝土浇筑后,需要进行养护,使其充分水化反应,增强强度。
如果养护措施不到位,比如湿度保持不佳、温度控制不当等,都会影响混凝土的强度。
二、商品混凝土强度不足的预防措施:1.严格控制原材料质量:选用质量优良的原材料进行生产,确保水泥、骨料、掺合料等的质量达标。
2.合理设计配合比:根据不同的工程要求,设计出合理的配合比,控制好水灰比和骨料粒径分布。
3.优化搅拌工艺:合理控制搅拌时间和搅拌方式,确保混凝土中的骨料能够均匀分散,达到良好的搅拌效果。
4.加强混凝土养护:在混凝土浇筑后,及时进行养护,保持湿度和温度的适宜,促进混凝土的水化反应,增强其强度。
5.加强施工管理:加强对混凝土施工过程的管理,确保施工操作规范,避免人为因素对混凝土强度的影响。
6.强度监测与质量控制:定期对生产的混凝土进行强度监测,及时发现问题并采取措施进行调整和改进。
7.建立完善的质量管理体系:建立混凝土质量管理的相关制度和流程,从原材料采购到生产施工全过程进行质量监控,确保混凝土的质量稳定可靠。
总之,商品混凝土强度不足的原因很多,但通过合理的技术措施和施工管理,可以有效地预防这些问题的发生,保证混凝土的强度达到设计要求。
混凝土强度不足常见原因及处理措施
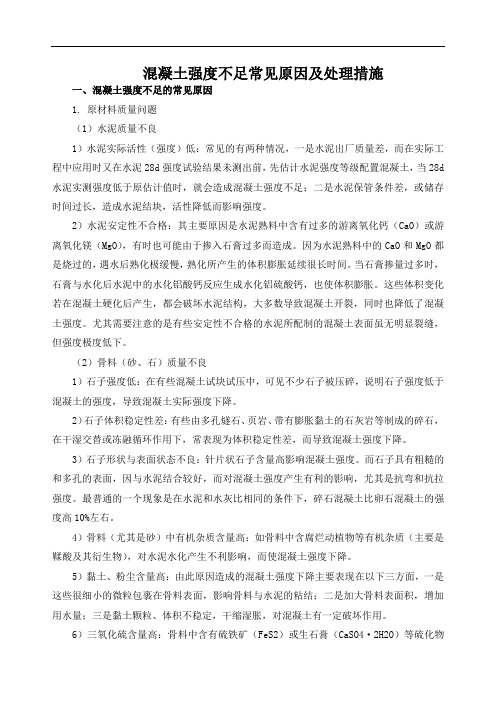
混凝土强度不足常见原因及处理措施一、混凝土强度不足的常见原因1. 原材料质量问题(1)水泥质量不良1)水泥实际活性(强度)低:常见的有两种情况,一是水泥出厂质量差,而在实际工程中应用时又在水泥28d强度试验结果未测出前,先估计水泥强度等级配置混凝土,当28d 水泥实测强度低于原估计值时,就会造成混凝土强度不足;二是水泥保管条件差,或储存时间过长,造成水泥结块,活性降低而影响强度。
2)水泥安定性不合格:其主要原因是水泥熟料中含有过多的游离氧化钙(CaO)或游离氧化镁(MgO),有时也可能由于掺入石膏过多而造成。
因为水泥熟料中的CaO和MgO都是烧过的,遇水后熟化极缓慢,熟化所产生的体积膨胀延续很长时间。
当石膏掺量过多时,石膏与水化后水泥中的水化铝酸钙反应生成水化铝硫酸钙,也使体积膨胀。
这些体积变化若在混凝土硬化后产生,都会破坏水泥结构,大多数导致混凝土开裂,同时也降低了混凝土强度。
尤其需要注意的是有些安定性不合格的水泥所配制的混凝土表面虽无明显裂缝,但强度极度低下。
(2)骨料(砂、石)质量不良1)石子强度低:在有些混凝土试块试压中,可见不少石子被压碎,说明石子强度低于混凝土的强度,导致混凝土实际强度下降。
2)石子体积稳定性差:有些由多孔燧石、页岩、带有膨胀黏土的石灰岩等制成的碎石,在干湿交替或冻融循环作用下,常表现为体积稳定性差,而导致混凝土强度下降。
3)石子形状与表面状态不良:针片状石子含量高影响混凝土强度。
而石子具有粗糙的和多孔的表面,因与水泥结合较好,而对混凝土强度产生有利的影响,尤其是抗弯和抗拉强度。
最普通的一个现象是在水泥和水灰比相同的条件下,碎石混凝土比卵石混凝土的强度高10%左右。
4)骨料(尤其是砂)中有机杂质含量高:如骨料中含腐烂动植物等有机杂质(主要是鞣酸及其衍生物),对水泥水化产生不利影响,而使混凝土强度下降。
5)黏土、粉尘含量高:由此原因造成的混凝土强度下降主要表现在以下三方面,一是这些很细小的微粒包裹在骨料表面,影响骨料与水泥的粘结;二是加大骨料表面积,增加用水量;三是黏土颗粒、体积不稳定,干缩湿胀,对混凝土有一定破坏作用。
混凝土试块抗压强度不合格的原因分析

混凝土试块抗压强度不合格的原因分析一、前言混凝土试块的抗压强度是评价混凝土强度的重要指标,但在实际生产和施工过程中,经常出现混凝土试块抗压强度不合格的情况。
本文就混凝土试块抗压强度不合格的原因进行分析,以期能够更好地提高混凝土品质。
二、试块抗压强度不合格的表现混凝土试块抗压强度不合格的表现主要有以下几个方面:1. 试块抗压强度低于设计要求或标准规定的强度等级;2. 试块抗压强度的标准偏差大于规定值;3. 试块抗压强度的变异系数大于规定值。
三、试块抗压强度不合格的原因分析1. 混凝土配合比设计不合理混凝土的配合比是影响混凝土强度的关键因素之一。
如果混凝土的配合比设计不合理,就会导致混凝土试块抗压强度不合格。
例如,水灰比过大、砂率过大、石子过大或过小等都会影响混凝土强度,从而导致试块抗压强度不合格。
2. 混凝土材料不合格混凝土的材料质量也是影响混凝土强度的重要因素。
如果混凝土材料不合格或掺杂有杂质,就会影响混凝土的强度。
例如,水泥掺杂有太多的灰尘或其他杂质,砂子掺杂有太多的黏土或其他杂质,石子掺杂有太多的碎石或其他杂质等都会影响混凝土试块抗压强度。
3. 混凝土拌和不均匀混凝土拌和不均匀也是试块抗压强度不合格的原因之一。
混凝土在拌和的过程中,如果水分、水泥、骨料等成分没有充分混合,就会导致混凝土强度不均匀,从而导致试块抗压强度不合格。
4. 混凝土浇筑不规范混凝土浇筑不规范也会导致试块抗压强度不合格。
例如,混凝土浇筑时没有按照设计要求进行密实和振捣,就会导致混凝土中存在空洞或夹杂物,从而导致试块抗压强度不合格。
5. 混凝土养护不当混凝土试块在养护过程中,如果没有按照设计要求进行养护,就会导致试块抗压强度不合格。
例如,混凝土试块在养护过程中没有保持充足的湿度,或者养护时间不足等都会影响混凝土试块抗压强度。
6. 试块制备不当试块制备不当也是试块抗压强度不合格的原因之一。
例如,试块在制备过程中没有按照规定的方法进行制备,或者试块的质量不符合规定等都会导致试块抗压强度不合格。
混凝土整改报告
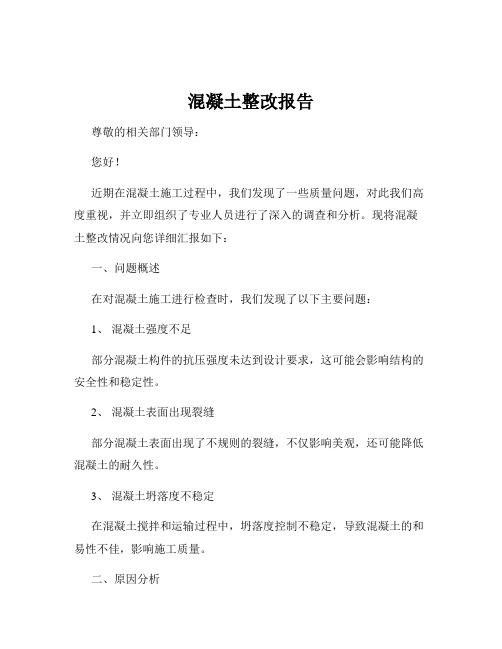
混凝土整改报告尊敬的相关部门领导:您好!近期在混凝土施工过程中,我们发现了一些质量问题,对此我们高度重视,并立即组织了专业人员进行了深入的调查和分析。
现将混凝土整改情况向您详细汇报如下:一、问题概述在对混凝土施工进行检查时,我们发现了以下主要问题:1、混凝土强度不足部分混凝土构件的抗压强度未达到设计要求,这可能会影响结构的安全性和稳定性。
2、混凝土表面出现裂缝部分混凝土表面出现了不规则的裂缝,不仅影响美观,还可能降低混凝土的耐久性。
3、混凝土坍落度不稳定在混凝土搅拌和运输过程中,坍落度控制不稳定,导致混凝土的和易性不佳,影响施工质量。
二、原因分析针对上述问题,我们进行了认真的分析,主要原因如下:1、原材料质量问题(1)水泥:水泥的强度和安定性可能存在波动,影响了混凝土的强度。
(2)骨料:骨料的级配不合理,含泥量超标,导致混凝土的强度和耐久性下降。
2、配合比设计不合理混凝土配合比未根据实际施工条件和原材料情况进行优化,导致混凝土的性能无法满足要求。
3、施工工艺不当(1)搅拌时间不足:混凝土搅拌不均匀,影响了其强度和和易性。
(2)浇筑过程中的振捣不规范:振捣不足或过度振捣,导致混凝土内部出现空洞或离析现象。
(3)养护不到位:混凝土浇筑后,养护时间不足或养护方法不正确,影响了混凝土的强度增长和裂缝控制。
4、质量控制体系不完善在混凝土生产和施工过程中,质量检验和控制措施不够严格,未能及时发现和解决问题。
三、整改措施为了彻底解决混凝土质量问题,我们采取了以下整改措施:1、原材料控制(1)加强对水泥的检验,确保其质量符合国家标准和设计要求。
(2)严格控制骨料的质量,选择级配良好、含泥量合格的骨料。
2、优化配合比根据实际情况,重新进行混凝土配合比设计,并在施工过程中根据原材料的变化及时调整。
3、改进施工工艺(1)严格控制混凝土搅拌时间,确保搅拌均匀。
(2)加强对浇筑过程中振捣的管理,制定振捣操作规程,确保振捣质量。
结构实体检测混凝土强度不足原因分析
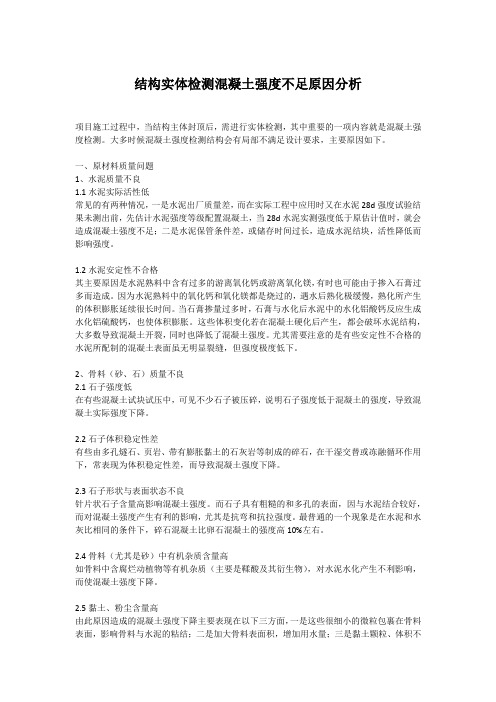
结构实体检测混凝土强度不足原因分析项目施工过程中,当结构主体封顶后,需进行实体检测,其中重要的一项内容就是混凝土强度检测。
大多时候混凝土强度检测结构会有局部不满足设计要求,主要原因如下。
一、原材料质量问题1、水泥质量不良1.1水泥实际活性低常见的有两种情况,一是水泥出厂质量差,而在实际工程中应用时又在水泥28d强度试验结果未测出前,先估计水泥强度等级配置混凝土,当28d水泥实测强度低于原估计值时,就会造成混凝土强度不足;二是水泥保管条件差,或储存时间过长,造成水泥结块,活性降低而影响强度。
1.2水泥安定性不合格其主要原因是水泥熟料中含有过多的游离氧化钙或游离氧化镁,有时也可能由于掺入石膏过多而造成。
因为水泥熟料中的氧化钙和氧化镁都是烧过的,遇水后熟化极缓慢,熟化所产生的体积膨胀延续很长时间。
当石膏掺量过多时,石膏与水化后水泥中的水化铝酸钙反应生成水化铝硫酸钙,也使体积膨胀。
这些体积变化若在混凝土硬化后产生,都会破坏水泥结构,大多数导致混凝土开裂,同时也降低了混凝土强度。
尤其需要注意的是有些安定性不合格的水泥所配制的混凝土表面虽无明显裂缝,但强度极度低下。
2、骨料(砂、石)质量不良2.1石子强度低在有些混凝土试块试压中,可见不少石子被压碎,说明石子强度低于混凝土的强度,导致混凝土实际强度下降。
2.2石子体积稳定性差有些由多孔燧石、页岩、带有膨胀黏土的石灰岩等制成的碎石,在干湿交替或冻融循环作用下,常表现为体积稳定性差,而导致混凝土强度下降。
2.3石子形状与表面状态不良针片状石子含量高影响混凝土强度。
而石子具有粗糙的和多孔的表面,因与水泥结合较好,而对混凝土强度产生有利的影响,尤其是抗弯和抗拉强度。
最普通的一个现象是在水泥和水灰比相同的条件下,碎石混凝土比卵石混凝土的强度高10%左右。
2.4骨料(尤其是砂)中有机杂质含量高如骨料中含腐烂动植物等有机杂质(主要是鞣酸及其衍生物),对水泥水化产生不利影响,而使混凝土强度下降。
混凝土试件强度不合格原因分析

混凝土试件强度不合格原因建筑工程中需求最大的材料是混凝土,其质量的好坏能够直接影响工程结构的安全性。
混凝土试件抗压强度在很大程度上反映建筑工程质量。
混凝土试件强度不合格或无效的情况下,不能反映混凝土的真实质量,但对工程质量的验收有着最直接的影响。
要判定混凝土真实质量状况,需要采取破损或者非破损的混凝土强度检测方法。
这不仅增加了成本,也会影响施工进度。
混凝土是一个过程产品,有多种因素影响到试件的试压值。
本文以混凝土质量、试件取样、制作、养护及检测等几方面分析试件强度不合格原因。
2混凝土质量存在问题2.1混凝土原材料原因2.1.1水泥(1)水泥强度不稳定,导致试件强度波动大。
(2)水泥品种较多,质量参差不齐,不同品种水泥强度忽高忽低,导致混凝土强度忽高忽低。
2.1.2细骨料机制砂细度模数偏低或偏高,混凝土稳定性差,导致混凝土试件强度波动大。
机制砂细度模数偏低,其表面积增大,在混凝土中水泥浆用量一定的情况下,颗粒表面相对减薄,混凝土就变得干稠,流动性就变小,导致坍落度降低。
相反,当机制砂细度模数偏高时其表面积减小,在混凝土中水泥浆用量一定的情况下,包裹砂子表面后就会有多余的水泥浆流出,混凝土就会变稀,流动性变大,从而导致坍落度增大。
混凝土强度受到严重影响。
2.1.3碎石(1)碎石含泥量高:碎石含泥高影响混凝土胶结材料与骨料的粘结性,导致强度不合格。
(2)碎石压碎指标高:碎石强度低于混凝土的强度,当混凝土受压时,石子首先被压碎,导致混凝土的实际强度降低。
特别是使用风化或软质岩石破碎加工成的碎石拌制的混凝土易发生此类问题。
(3)骨料体积稳定性差:尤其是由页岩、带有膨胀松土的石灰岩等制成的骨料,在干湿交替或冻融循环作用下,常表现为体积稳定性差,发生变形,破坏混凝土已经形成的内部结构,导致混凝土强度降低,严重时会使混凝土试件受到破坏。
(4)碎石级配不合理、粒径大、针片状含量高。
混凝土拌合物包裹性差,在将混凝土拌合物装入试模时可能出现有的试件浆体偏多,从而导致出现强度偏低的现象。
混凝土强度分析
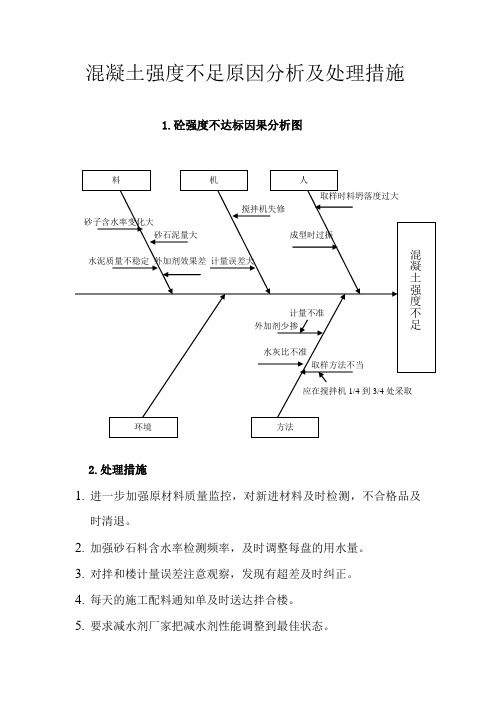
混凝土强度不足原因分析及处理措施
1.砼强度不达标因果分析图
2.处理措施
1.进一步加强原材料质量监控,对新进材料及时检测,不合格品及
时清退。
2.加强砂石料含水率检测频率,及时调整每盘的用水量。
3.对拌和楼计量误差注意观察,发现有超差及时纠正。
4.每天的施工配料通知单及时送达拌合楼。
5.要求减水剂厂家把减水剂性能调整到最佳状态。
6.要求试验室取样员加强混凝土取样及成型知识学习,在正确位置
取样,确保取样均匀,且成型时无过振,保证砼强度均匀。
7.严格按按设计120-160mm范围将坍落茺控制到140-160mm之间,
2013.04.16。
- 1、下载文档前请自行甄别文档内容的完整性,平台不提供额外的编辑、内容补充、找答案等附加服务。
- 2、"仅部分预览"的文档,不可在线预览部分如存在完整性等问题,可反馈申请退款(可完整预览的文档不适用该条件!)。
- 3、如文档侵犯您的权益,请联系客服反馈,我们会尽快为您处理(人工客服工作时间:9:00-18:30)。
喷射混凝土强度偏低原因分析
足技术经济合理的要求,如以低标号水泥配制高强度混凝土,即使水泥用量很多,也难以达到设计强度等级的要求。
在经济上也极不合理。
反之,如以高标号水泥配制低强度混凝土,由于水灰比大,水泥用量少,混凝土拌合物的和易性不好,施工质量得不到保证。
同时,高标号水泥价格昂贵,将造成浪费。
因此,应根据工程的不同需要,合理选用不同的水泥标号,不应有什么用什么,造成浪费或影响质量。
⑶安定性不良
水泥熟料如果烧结得不充分,就会产生较多的游离氧化钙,它在凝结硬化过程中水化较慢,当水泥已经凝结硬化后,还在继续起水化作用,产生体积膨胀,在水泥水化中体积膨胀97.9%,破坏已经硬化的水泥石结构,便出现龟裂、弯曲、松脆或崩溃等不安定的现象。
水泥安定性不良除了烧结不充分的原因外,还和水泥贮存时间有关,因为新出厂水泥温度一般都比较高,贮存一定时间,使水泥温度降低,其残存的游离氧化钙被消解,水泥性能得到稳定。
体积安定性不合格的水泥属于废品,不能使用。
⑷水泥贮存期
水泥的贮存期不能过长,因为水泥在存放时接触空气,会吸收水分而产生轻微的水化作用,生成氢氧化钙(Ca(OH)2),然后又再吸收二氧化碳而生成碳酸钙(C a C O3), 从而降低水泥颗粒的胶接能力,延迟凝结时间,强度下降。
鉴于上述原因,规范规定,水泥的出厂贮存时间一般不超过3 个月,超过3 个月应进行复试,并按试验结果使用。
但有些施工单位常常早存水泥,有些工程还拖延工期,水泥积压,则造成混凝土强度达不到设计要求的事故。
⑸水泥受潮
水泥受潮,使松散的水泥颗粒外部和水发生作用,凝结成块。
再使用时,就不能很好地和水发生水化作用,降低水泥原有的胶结能力,强度显著降低。
结块大而又坚硬的表示严重受潮,不能使用;如果是轻微的受潮,结块小而比较松,能用手捏成粉的可以用,但要加强搅拌;受潮中等的可筛去硬块,并压碎松快后降级使用于次要工程或次要部位。
为了防止水泥受潮,建筑工地上的水泥仓库应尽量搭设在地势高、干燥、运输方便、周围排水好的地方。
仓库地坪平整后干铺一层砖,在砖上面铺一层油毡纸。
运到工地的水泥应迅速入仓,仓库尽量封闭,下面垫高,离地离墙约30cm,堆放高度不要超过10 包,便于使用。
入库的水泥应按不同的品种、牌号、标号、出厂日期等分别堆放,标上标签,避免搞错,上述水泥不能混用。
2 、砂
⑴砂的级配
良好的级配要求是小颗粒恰好填满中等颗粒的空隙,而中等颗粒又恰好填满大颗粒的空隙,这样一级一级的互相填满,则最后达到砂的总空隙率最小,需要填充这些空隙的水泥浆也越小,从而达到提高混凝土强度和节约水泥的目的。
所以,级配如何是评定砂质量的重要指标。
⑵含混量
砂的含混量过高,妨碍水泥与砂(石子)的粘接,降低混凝土强度。
混凝土强度等级高于或等于C30 时,含泥量(按重量计)不超过3%;泥块含量不大于1%;混
凝土强度等级低于C30 时,含泥量不大于5%;泥块含量不大于2%。
⑶坚固性
砂的坚固性,用硫酸钠溶液检验,试拌经5 次循环后,其重量损失不应大于1%。
当同一产源的砂,在类似的气候条件下使用有可靠经验时,可不作坚固性检验。
⑷有害物质含量
砂中含有云母、轻物质(如煤和褐煤等)、有机质、硫化物及硫酸盐等有害物质,会影响混凝土的抗渗性,甚至腐蚀水泥,降低混凝土强度。
3 、石子
⑴颗粒级配
石子级配好坏对节约水泥,保证混凝土具有良好的和易性和密实性均有很大关系。
特
混凝土的强度增长与养护时期的气温有密切关系。
气温越低,养护时间越长,强度增长越慢,尤其在负温度时,水化作用基本停止,甚至有被冻裂的危险。
因此,冬季施工浇筑的混凝土,必须做好养护工作,在受冻前,混凝土的抗压强度必须大于等于混凝土的临界强度,否则混凝土就会被冻坏。
混凝土受冻临界强度如下:硅酸盐水泥或普通硅酸盐水泥配制的混凝土,为设计强度等级的30%;矿渣硅酸盐水泥配制的混凝土为设计强度等级的40%,但C10 以下的混凝土不得低于5mp a。
八、混凝土被腐蚀
混凝土的腐蚀大多由于酸、碱、盐类或地下水等侵蚀下的化学腐蚀。
当混凝土和硫酸接触时,水泥石与硫酸作用生成碳酸钙,体积膨胀,混凝土遭受破坏,强度降低。
当混凝土和盐酸、硝酸接触后,盐酸、硝酸与混凝土中游离的氧化钙反应,形成极易溶于水的氧化钙和硝酸钙,使混凝土强度降低和遭受破坏。
当混凝土遭到强碱时,就严重腐蚀混凝土,破坏水泥石,从而降低了混凝土的强度。
盐类对混凝土也具有较强的影响,会使混凝土体积膨胀,促进混凝土破坏,强度降低。
九、混凝土运输或在现场等待时间过长
混凝土生产时使用的外加剂中有一定的缓凝组分,能起到缓凝的效果,但是缓凝时间有限,超过两个小时后水泥开始水化,之后坍落度也开始下降,混凝土强度会有一部分损失,也就是说在混凝土施工中混凝土运输到施工结束时间最好控制在两个小时以内,超过两个小时,混凝土开始初凝,等待时间越长,水泥水化越多,所形成的水泥石利用率越低,导致强度损失就越大。
十、其他原因
有些生产车间经常受到高温,温热气体的侵害,雨水、烟尘、化学介质当交替作用,初凝混凝土受振,以及遭受地震、火灾等灾害,均会降低混凝土的强度。