涂装外观检验标准
涂装件外观检验通用规范
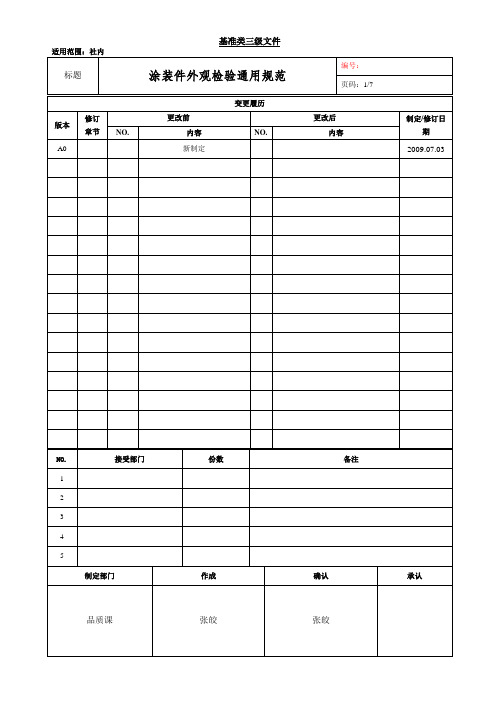
编号: 页码:2/7
1. 目的: 明确和规范公司涂装产品的表面检验标准,以确保生产和检验有章可循,确保产
品受入检验及出荷品质符合行业及客户要求。 2. 适用范围:
本标准适用于公司所有涂装品的受入检验,完成品检验,以及外协供应商。
3.职责 3.1 品质部:依本标准进行检验与测试; 3.2 物流部(仓库)依本标准进行仓存。
以上 ,允许 3 以上 ,允许 5
处以内
处以内
宽 0.20mm 以 宽 0.30mm 以
内,长度
内,长度
10mm 以内,间 20mm 以内,间距
距100mm 以上, 150 mm以上,可
可以接收3处
以接收5 处
深度≥0.20mm 深度≥0.50mm
不接受
不接受
C 级面 可接受,但不能对 产品造 成功能性影响。 具体可参照样板。
变化,或仅有少量涂层迁移到软布(或脱脂棉)上为合格(用 95%无水酒精,则来 回擦拭涂膜50 次) 7.3.5 盐雾试验: 具体操作依据盐雾试验作业指导书,具体标准按客户产品图纸要求或国家相关标准或
行业相关标准执行,一般来说按5%盐水35℃500H 不发霉氧化管控(未特别指示情 况下)。
7.3.6 耐湿性 没有特别指示的情况下:50℃湿度98%以上的恒温恒湿,240 小时无异常。 7.3.7 耐沸腾水性 没有特别指示的情况下:浸入自来水 98~100℃ 3 小时无异常。 7.3.8 耐湿水性 没有特别指示的情况下:浸入自来水 40~50℃240 小时无异常。 7.3.9 耐盐水性 没有特别指示的情况下:100%NaC1 液体中浸泡(20℃)240 小时无异常 7.3.10 耐碱性 没有特别指示的情况下:5%NaOH 液体中浸泡(20℃)48 小时无异常 7.3.11 耐酸性没有特别指示的情况下:5%醋酸液体中浸泡(20℃)24 小时无异常 7.3.12 耐油性 没有特别指示的情况下:60℃ Spindle油中浸泡60分钟无异常 附加说明:以上性能测试项目只列入描述,具体项目要求依据喷涂行业标准进行。
油漆外观质量检查标准【合集】(1)

涂装外观质量检查标准 (1)油漆相关质量检验标准 (3)涂装外观质量检查标准1主题和适用范围:本标准规定了公司的涂装外观质量检查内容和方法,适用于油漆的外观质量检查。
2术语:2.1色差:涂层颜色与规定的标准颜色有差异的现象。
2.2颗粒与异物:涂层表面粘附尘粒、涂料沉淀物、线头等物质影响涂层外观质量的现象。
2.3缺漆(露底):涂层表面漏喷或虚枪,局部显露底层的现象。
2.4流痕:涂层局部过厚产生的漆液流坠条痕的现象。
2.5缩孔(麻点):涂层中混入油污等异物,在局部湿漆膜上产生表面张力的变化,引起涂层局部收缩而产生的凹坑。
2.6针孔(气孔):溶剂不当或烘干条件不当引起突破涂层的针状小孔穴。
2.7起皱:涂层表面呈现凸凹不平,无规则的线状折皱现象。
2.8桔皮:涂层表面呈现桔子皮状的不平滑现象。
2.9渗色、发花:底漆颜色渗到面漆层或面漆搅拌不均匀产生的杂色现象。
2.10擦伤划痕:成膜后的涂层在外力作用下产生的线状或片状擦痕。
2.11生锈:底材受腐蚀,使涂层表面出现锈痕的现象。
2.12杂漆:涂层表面被异色涂料沾污的现象。
2.13打磨痕:修补涂层缺陷时,打磨产生的现象。
2.14光斑和雾圈:涂层局部修补后,光泽高的补漆区形成光斑,周围漆膜不完整的漆雾散落区形成雾圈。
2.15坑包:因磕碰产生的凸凹现象。
2.16涂层不干:由于涂料组成或烘干制度不当引起漆膜干燥不良的现象。
2.17胶上漆膜开裂:胶与漆的应力不同引起的密封胶条上漆膜开裂现象。
2.18水迹点:由于涂装时零件上的水点引起的漆膜表面上产生凹点或露底现象。
3检查区域划分:按汽车使用条件和对涂层质量的要求,从高到低分为A、B、C、D四个区域A区:影响外观最明显的部位。
包括:左右外侧表面腰线以上(不包括腰线部分)车窗以下区域,前外表面前围板,左右侧围外盖板外表面。
B区:影响外观较明显部分。
包括:车身前围及侧围的其他部分(A区以外部分),左右前支柱,左右侧围外盖板外表面,保险杠上表面及前表面,车身内部内饰后可见部分。
汽车喷涂产品检验标准
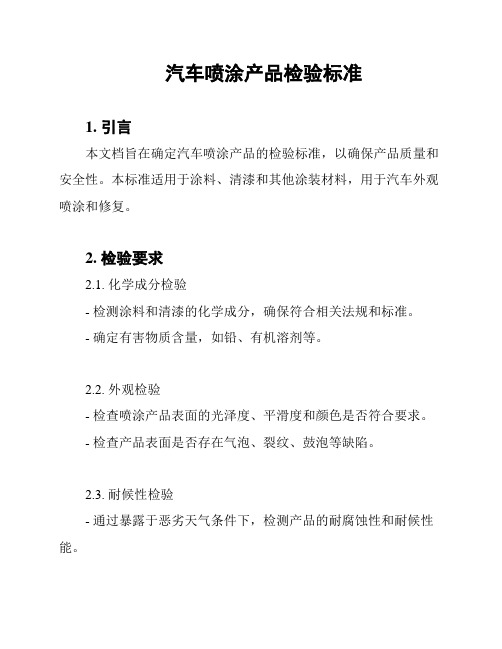
汽车喷涂产品检验标准
1. 引言
本文档旨在确定汽车喷涂产品的检验标准,以确保产品质量和安全性。
本标准适用于涂料、清漆和其他涂装材料,用于汽车外观喷涂和修复。
2. 检验要求
2.1. 化学成分检验
- 检测涂料和清漆的化学成分,确保符合相关法规和标准。
- 确定有害物质含量,如铅、有机溶剂等。
2.2. 外观检验
- 检查喷涂产品表面的光泽度、平滑度和颜色是否符合要求。
- 检查产品表面是否存在气泡、裂纹、鼓泡等缺陷。
2.3. 耐候性检验
- 通过暴露于恶劣天气条件下,检测产品的耐腐蚀性和耐候性能。
2.4. 附着力检验
- 确定涂层与底材之间的粘附力,以评估涂层的质量和稳定性。
2.5. 耐化学品检验
- 检测涂层的耐化学品性能,包括耐溶剂、酸碱、汽油等。
2.6. 薄膜厚度检验
- 测量涂层的薄膜厚度,以确保涂层均匀和符合要求。
3. 检验方法
- 使用合适的仪器和设备进行检验,包括光泽度计、显微镜、
冷热循环试验箱等。
- 根据相关标准和法规执行检验过程,并记录检测结果。
4. 结论
- 根据检验结果确定产品是否符合标准要求,以及是否能够满
足汽车喷涂的使用要求和性能。
5. 参考文献
- [相关法规和标准]
以上为汽车喷涂产品检验标准的基本内容,详细的检验流程和要求应根据具体情况和相关标准进行进一步制定。
以下内容是你可以参考的相关法规和标准:
[相关法规和标准1]
[相关法规和标准2]
[相关法规和标准3]。
涂装检验标准

涂装检验标准
1、电泳漆要求漆层均匀,附着良好,无桔皮、起皱、露底等现象,漆膜达实干状态。
2、面漆喷涂需作前期处理,表面磕碰划伤、坑凹变形拉延缺陷及锤痕必须用腻子找补,腻子要求打磨平整光滑,附着力良好,并达到实干状态。
3、面漆要求喷涂均匀,色泽饱满,无明显色差,颜色亮丽,符合标准色板。
主视面不允许有流挂、针孔、失光、离油、麻点、鼓泡、裂纹、桔皮、起皱、划痕、杂质、雾圈及打磨痕迹等缺陷,非主视面允许有轻微桔皮颗粒(100mm ×100mm范围内,直径≤的颗粒不多于8个,直径≤的颗粒不多于5个)
4、漆膜硬度要求大于HB,亮度要求大于90,漆膜附着力要求使用2mm划格器划格后,用普通胶带纸粘,漆层不脱落。
5、车身内部影响密封性能的部位打金属密封胶,要求均匀切实,密封良好,达实干状态。
6、烤漆后的质量缺陷以及流转过程中的磕碰划伤,修补后必须使用指定的抛光机及抛光剂进行抛光处理。
编制:审核:批准:
表面油漆质量符合要求,
1其表面:应光洁,无磕碰变形和划伤;无起皱、缺漆、桔皮、漆膜不干、流挂(≯3mm)、缩孔(≯5处)和色差现象。
允许:颗粒:眼睛距补漆部位0.5米,目测100mm×100mm 范围内颗粒点少于10个;打磨痕:眼睛距补漆部位米,目测无打磨痕;米,目测无补漆雾
圈。
2整车
A区(车门、车身左右、翼子板、发动机罩、散热器面罩)侧不允许有打磨痕迹,补漆雾圈直径小于Ф100mm补漆数量不超过一处;。
喷漆外观质量检验标准(二)

喷漆外观质量检验标准(二)引言概述:喷漆外观质量检验标准是用来评估喷漆产品外观质量的标准,从而确保产品在外观方面达到一定的质量要求。
本文将介绍喷漆外观质量检验的五个主要方面,包括颜色一致性、涂层厚度、光泽度、漆面平整度和表面缺陷。
这些方面涵盖了评估喷漆外观质量的关键指标,有助于生产厂商和检验人员确保产品在外观方面达到客户的期望。
正文:一、颜色一致性1. 根据客户要求,确定喷漆产品的颜色标准。
2. 使用色差仪或人工目测方法,对喷漆产品颜色进行检测。
3. 比较检测结果与颜色标准的差异,判断颜色一致性是否合格。
4. 针对不合格的喷漆产品,进行调整或重新喷涂,直至达到颜色标准。
二、涂层厚度1. 使用涂层厚度仪测量喷漆产品的涂层厚度。
2. 根据客户要求,确定涂层厚度的上下限值。
3. 比较测量结果与上下限值,判断涂层厚度是否符合要求。
4. 针对不合格的喷漆产品,进行调整或重新喷涂,直至达到涂层厚度要求。
三、光泽度1. 使用光泽度计测量喷漆产品的光泽度。
2. 根据客户要求,确定光泽度的要求值。
3. 比较测量结果与要求值,判断光泽度是否符合要求。
4. 针对不合格的喷漆产品,进行调整或重新喷涂,直至达到光泽度要求。
四、漆面平整度1. 视觉检测喷漆产品的漆面平整度,检查有无凹凸不平、起皮等现象。
2. 使用手工方式或检测仪器,测量喷漆产品的平整度。
3. 根据客户要求,确定漆面平整度的标准。
4. 比较测量结果或视觉检测结果与标准,评估漆面平整度是否合格。
5. 针对不合格的喷漆产品,进行修复或重新喷涂,直至漆面平整度符合要求。
五、表面缺陷1. 视觉检测喷漆产品表面是否存在气泡、瑕疵等缺陷。
2. 使用放大镜或显微镜,对喷漆产品表面进行详细检查。
3. 根据客户要求,确定表面缺陷的允许数量和尺寸。
4. 比较检测结果与标准,判断表面缺陷是否在可接受范围内。
5. 针对有过多或大尺寸的表面缺陷的喷漆产品,进行修复或重新喷涂,以确保产品质量。
粉末涂装的检验要求

1、粉末喷涂件验收内容1.1外观1.1.1主要表面是指涂装后对工件外观和其它性能起主要作用的表面1.1.2粉末喷涂件外观应平整、光滑、主要表面不允许有直径大于1.5mm或深度超过0.2mm的凹坑。
不允许有直径超过0.5mm的颗粒突起。
每80×80mm范围内直径小于1.5mm的凹坑不允许超过1处,每40×40mm范围内直径小于0.5mm的颗粒突起不允许超过2处。
1.1.3主要表面无划痕、无明显磨擦失光现象,允许轻微桔皮现象;其它表面允许有轻微擦伤和划痕,划痕的长度小于20mm,擦伤的范围小于20×20mm,所有划伤、磨擦痕迹只允许表层轻微擦伤,划痕和擦伤的深度小于0.005mm。
1.1.4粉末涂层应厚薄均匀,无流挂、起瘤现象。
1.1.5粉末涂层应无漏喷、起泡、针孔、起皮、剥落等现象。
1.1.6涂层颜色应符合标准样板,不允许有杂色,自制标准样板的有效期为1年,每年更换一次。
1.1.6外观检查主要采用目视法检查,检查员的双眼视力正常,必须达到1.2以上。
外观检查时零件与眼睛的距离为350mm,放在散射的日光下、从45°和90°两个不同角度去进行观察;在进行颜色检查时工件与标准试样应放在同一平面上,并且最好在接近垂直于试样的方位上观察,两个试样的观察方向应相同,一般情况下颜色的观察也需在散射的日光下进行。
1.2涂层厚度一般情况下涂层厚度为60-80μm,采用涂层测厚仪进行检测,每件产品检测至少5个点以上。
对于结构复杂的产品,局部涂层厚度允许超差10%。
1.3附着力按照GB9286划格法进行检测,2mm间距,要求达到1级以上。
1.4光泽按照GB9754规定采用光泽度仪进行检测,要求有光≥85%,半光50±10%,无光≤20%。
1.5铅笔硬度按照GB6739规定进行检测,要求达到2H以上。
1.6耐盐雾性按照GB10125标准进行检测,要求达到500小时以上涂层无变化。
喷漆件外观检验标准

外观检验标准<适用位置>A 杆上面B 杆侧面(实车组装时上侧)C 杆侧面(实车组装时下侧)D 杆里面2.0 检查方法:目视在500lx的亮度下一臂距离处。
可旋转30度角,同一面的注视时间不超过15秒钟。
3.0 检查内容:见下表图例11. 光泽的差异,光泽不均12. 泛白,模糊晕色8. 水迹9. 桔皮10. 颜色的差异5. 纤维状垃圾6.涂层剥落,涂层破裂7. 气泡目视下无不协调的感觉A面.长度不允许超过1mm, 宽度不允许超过0.1mm,不卡住指甲的伤痕。
B,C面.长度不允许超过3mm, 宽度不允许超过0.2mm.A面.长度不允许超过1mm, 宽度不允许超过0.2mmB,C面.长度不允许超过3mm, 宽度不允许超过0.2mm.不能有明显的不均A面.直径不允许超过0.5mm,2个以内;单个直径不允许超过1mm, 高度在0.1以内。
B,C面.直径不允许超过1mm,3个以内;单个直径不允许超过1.5mm,高度在0.2以内。
B,C面.直径不允许超过1mm,3个以内;单个直径不允许超过1.5mm。
1.涂装颗粒,凸点2. 凹陷3. 伤痕、压痕4. 划伤,擦伤A面. 直径不允许超过0.5mm, 在100 mm的距离内不能超过两点. 同一面上不能超过三个大于0.3mm 的凸起点B,C面. 单个直径不允许超过1mm, 同一面上不能超过三个大于0.5mm 的凸起点A面. 直径不允许超过0.5mm, 在100 mm的距离内不能超过两点, 同一面上不能超过三个凹陷点不能有参照样品A面.不允许有1.0 范围此标准适应于雅阁雨刮臂的喷漆产品,客户有特殊要求时,依客户要求检验。
现象限度B,C面. 单个直径不允许超过1mm, 同一面上不能超过三个大于0.8mm 的凸起点.头杆处凹陷位置不允许超过中心与边缘的1/2,如图。
A面.长度不允许超过0.8mm, 宽度不允许超过0.2mm ;B,C面.长度不允许超过2mm, 宽度不允许超过0.3mm.头杆孔的两侧边不允许超过5mm.不能剥落,破裂A 杆上面C 杆侧面(实车组装时下侧)B 杆侧面(实车组装时上侧)D 杆里面13.底材露出不能露底材【备注】同一面100mm内不允许出现2个以上缺陷同时共存(允许2个所有缺陷)。
涂装质量检验标准

涂装质量检验标准TZ-JYBZ检验项目:1 外观检查腻子有无明显缺陷:砂纸印、砂眼、腻子印、腻子边、凹坑等喷漆均匀一致,无流漆、漏底、桔皮、油点、漏喷、针孔、气泡、划伤、发花、油漆脱落、明显色差,200mm2之内允许1个脏点<1mm,外观检验方法检查部位A、B、C三类(A外观可见、B、外观不易见、C外观不可见)2厚度厚度≥60um,检验方法:用漆膜厚度测试仪在不同的三个部位测试,3.漆面附着力油漆附着力检验过程:用百格刀在测试样本表面划10×10个(100个)1mm×1mm小网格,每一条划线应深及油漆的底层;用毛刷将测试区域的碎片刷干净;用3M600号或610号胶纸或等同效力的胶纸牢牢粘住被测试小网格,并用橡皮擦用力擦拭胶带,以加大胶带与被测区域的接触面积及力度;用手抓住胶带一端,在垂直方向(90°)迅速扯下胶纸,同一位置进行2次相同试验。
三、油漆附着力检验结果判定:要求附着力≥4B时为合格。
四、油漆附着力检验说明5B-划线边缘光滑,在划线的边缘及交叉点处均无油漆脱落;4B-在划线的交叉点处有小片的油漆脱落,且脱落总面积小于5%;3B-在划线的边缘及交叉点处有小片的油漆脱落,且脱落总面积在5%~15%之间;2B-在划线的边缘及交叉点处有成片的油漆脱落,且脱落总面积在15%~35%之间;1B-在划线的边缘及交叉点处有成片的油漆脱落,且脱落总面积在35%~65%之间;0B-在划线的边缘及交叉点处有成片的油漆脱落,且脱落总面积大于65%附着力大于4B级。
检验工具:目视、漆膜厚度测试仪、色差计、百格刀、桔皮仪、手感、重点检查的部位:左前门翼子板、左前门外板、左前门内板、左门中立柱、左侧后门外板、左侧后门内板、左下边梁、左侧后立柱(轮眉上部)、大顶、后门外板、后门内板、后门流水槽、后保险杠、右前翼子板、左前门外板、右前门内板、右门中立柱、右侧后门外板、右侧后门内板、右下边梁、右侧后立柱(轮眉上部)、前机盖外板、前机盖内侧、前机盖流水槽编制:审批: 日期:。
- 1、下载文档前请自行甄别文档内容的完整性,平台不提供额外的编辑、内容补充、找答案等附加服务。
- 2、"仅部分预览"的文档,不可在线预览部分如存在完整性等问题,可反馈申请退款(可完整预览的文档不适用该条件!)。
- 3、如文档侵犯您的权益,请联系客服反馈,我们会尽快为您处理(人工客服工作时间:9:00-18:30)。
内容页次1.目的 2 2.范围 2 3.优先原则 2 4.外观 2 5.表面划分 4 6.塑料件 4 7.金属板金件 5 8.铸造件8 9.油漆和喷涂件9 10.产品标识10
1.0.目的
该程序是为了建立和描述用来判定零件、装配件、产品外观质量合格与否的准则
2.0.范围
2.1凡本公司所生产的和供应商提供的所有产品,包括零件、装配件和成品。
如客户有特定要求和规范,应以要求的规范为准。
2.2本规范适用于所有的塑料件、金属板金件、丝印和喷涂件及产品的标识。
3.0.优先原则
在发生矛盾时,采用以下优先原则:
3.1.文件应与特别规定的适用性上保持一致,如零件的公差。
3.2.采购合同或专门条款。
3.3.现用的图纸或要求。
3.4.本外观标准。
4.0.外观
4.1.总体要求
在本标准的各个部分中,外观检查使用时间和距离来描述。
该标准可用于员工培训,任何加工过程的外观表面质量控制以及判定产品合格与否。
4.2.观察条件
所有检查都应在正常灯光下,独立的标准的观察条件下进行。
检查中,仅肉眼检查之为准。
零件表面检查不需任何放大帮助,45°观察角下进行。
A级表面在检查时,可旋转表面,利用最强的反射。
B级、C级则不需要。
5.0.表面划分
A级(装饰表面):用户经常看到的表面。
例如底座,面板表面等等。
B级(适当装饰表面):不翻动时偶然才会看到的表面。
例如架式底盘的两侧和顶部,后面等等。
C级(非装饰表面):翻动才会看到的表面。
例如底盘的外部和内部零件等6.0.塑料件
6.1.接受标准
6.1.1. 可接受的A、B、C级缺陷都应不影响产品的装配或功能,如有影响就应自动拒收。
6.1.2. 检查要求和观察条件参考第4部分(外观标准/检验要求)
6.1.3. 公差表中是指50平方英寸(约320cm2)范围内允许存在缺陷的数量,超过50平方英寸其缺陷数按比例增加,如同时存在2种以上的缺陷应拒收。
6.3. 缺陷定义
6.3.1. 突起:表面上局部高出(如水泡,肿块,山脊状)
6.3.2. 变色:与原色不同,或在同一零件中颜色不一致
6.3.3. 流痕:表面呈波纹、条纹状
6.3.4. 雾状:透明件中呈现云雾状
6.3.5. 凹坑:零件表面的小弹坑
6.3.6. 斑点:粘在表面上的细小颗粒
6.3.
7. 划伤:表面上的线状浅槽
6.3.8. 缩水:表面局部下陷
6.3.9. 溶接线:流料溶接处形成的可见线
6.3.10.色泽差:表面光泽不一致
6.3.11.分型线/飞边:零件在模具接合点处形成的可见线或突出线
6.3.12.质地变化:对于同一取样零件切片上有明显的质地结构变化
6.3.13.脱模:喷射润滑油,易于零件脱模
6.3.14.色差:零件颜色与色板不同
6.4. 公差表(塑胶件)
每个表面的缺陷数量不得超过可接受的限度,此表可用于检验人员的培训和判定产品的拒收。
7.0.金属板金件
7.1.接受标准
7.1.1.可接受的A、B、C级缺陷应不影响装配或功能,如有影响就应自动拒收。
7.1.2.检查要求和观察条件参考第4部分(外观标准/检验要求)
7.1.3.特别适用于已电镀和需电镀的零件
7.1.4.公差表中是指50平方英寸(约320cm2)范围内允许存在缺陷的数量,超过50平方英寸其缺陷数按比例增加,如同时存在2种以上的缺陷应拒收。
7.3.缺陷定义
7.3.1.彩虹纹:镀锌层出现局部变色或彩纹
7.3.2.生锈/ 氧化:暴露在空气中的母材发生了化学反应
7.3.3.变色:与原色不同或不一致
7.3.4.划伤:用指甲不可感知的,但可见的沟槽
7.3.5.浅度划伤:通过旋转可以看到,但不是从所有角度和边都能看到的沟槽
7.3.6.浅槽:用指甲可感知的,可见的沟槽
7.3.7.镀痕:由于电镀过程造成工件表面明显的不一致,如水纹、钩痕
7.3.8.麻痕:基材表面的沙坑状痕迹,涂装后仍可见
7.3.9.色泽差:局部表面上出现光泽不足或光泽过强
7.3.10.油脂:加工过程中遗留在表面上未清洗掉的油污
7.3.11.污点:在涂层或表面上留有杂物
7.3.12.疤痕:表面上有小弹坑
7.3.13.模痕:由成型模留下的过程痕迹,这种痕迹在所有的零件上都存在,
并位于成型弯曲的区域,但其它痕迹不能定义为模痕
7.3.14.光亮表面:由于研磨介质的作用而形成的,如带式、轮式抛光机形成
的光亮表面
7.3.15.手指印:正常的制造过程中,在工件表面留下的手指印
注:任何痕迹、划伤都不得渗透镀层。
7.4.公差表(板材零件)
每个表面的缺陷数量不得超过可接受的限度,此表可用于检验人员的培训和判定产品的拒收。
8.0.铸造件
8.1.接受标准
8.1.1.可接受的A、B、C级缺陷应不影响装配或功能,如有影响就应自动拒收。
8.1.2.检查要求和观察条件参考第4部分(外观标准/检验要求)
8.1.3. 公差表中是指50平方英寸(约320cm2)范围内允许存在缺陷的数量,超过50平方英寸其缺陷数按比例增加,如同时存在2种以上的缺陷应拒收。
8.3.缺陷定义
8.3.1.胀大:由于老化,模具尺寸的变大
8.3.2.热裂纹:一定长度的裂纹,条纹,鳍片
8.3.3.缩水:表面塌陷
8.3.4.气孔:由于气孔,坑,未填充等原因产生的空洞
8.3.5.突出:表面上高出的区域(水泡,肿块,山脊状)
8.3.6.斑点:粘在表面上的细小颗粒
8.3.7.划伤:表面由浅槽形成的线
8.3.8.溶接线:表面上形成的可见线或痕迹
8.4.公差表(铸造件)
每个表面的缺陷数量不得超过可接受的限度,此表可用于检验人员的培训和判
9.0.油漆和喷涂件
9.1.接受标准
9.1.1.所有等级都必须显示出良好的工艺,如果需要,须达到颜色、光泽、密度、厚度、着附力和耐压的要求。
9.1.2.喷漆件只要符合B级和C级的缺陷标准即可。
9.1.3.检查要求和观察条件参考第4部分(外观标准/检验要求)
9.1.4. 公差表中是指50平方英寸(约320cm2)范围内允许存在缺陷的数量,超过50平方英寸其缺陷数按比例增加,如同时存在2种以上的缺陷应拒收。
9.3.缺陷定义
9.3.1.垃圾:外来的物质
9.3.2.凹痕:材质上的局部压痕
9.3.3.划痕:母材上的部分材料被移动,转移
9.3.4.划伤:浅槽
9.3.5.桔皮皱:局部未粘附的油漆汇聚而形成的皱面
9.3.6.涂料堆积:由于局部堆积过多的涂料,干后形成不一致的表面
9.3.7.色差:颜色不一致
9.3.8.光亮面:母材上覆盖的涂料不足
9.3.9.纹理变化:零件表面出现明显的纹理变化
9.3.10.气泡:局部上由于涂料中混入空气或未粘附而形成的缺陷
9.3.11.污点:由于材料缺陷或未清洗干净,表面上形成的污点或不均匀的颜
色
9.4.公差表(喷涂件)
每个表面的缺陷数量不得超过可接受的限度,此表可用于检验人员的培训和判定产品的拒收。
10.0.产品标识
10.1.接受标准
10.1.1. 可接受的A、B、C级缺陷应不影响装配或功能,如有影响就应自动拒收。
10.1.2. 检查要求和观察条件参考第5部分(外观标准/检验要求)。
10.1.3. 此部分特别适用于所有产品的标识,如标签,丝印,盖章,蚀刻。
10.3.公差表
每个表面的缺陷数量不得超过可接受的限度,此表可用于检验人员的培训和判。