瓦楞纸箱塌箱原因及解决对策
瓦楞问题产生的原因及解决办法(ppt共54张)

瓦 楞 问 题 产 生的原 因及解 决办法 (PPT54 页)
瓦 楞 问 题 产 生的原 因及解zation Expert Team
瓦 楞 问 题 产 生的原 因及解 决办法 (PPT54 页)
瓦楞辊表面有异物
四
瓦楞辊之间间 隙太大或不平衡
楞
导纸板位置不
不
当、带脏或磨损
均
瓦楞原纸含水量不均衡
瓦楞原纸张力太小
瓦 楞 问 题 产 生的原 因及解 决办法 (PPT54 页)
解决办法
清理瓦楞辊表面 修正上、下瓦楞 辊之间的间隙 检查、修正、清 理或更换导纸板
加大预热包角 适当调整张力控制
Network Optimization Expert Team
产生原因
瓦楞辊表面温度不 均衡或温度不够
二
双面机加热板温度不够
部
车速太快
分
脱
原纸含水量太高
胶
胶黏剂质量不好
胶黏剂附着量小
瓦 楞 问 题 产 生的原 因及解 决办法 (PPT54 页)
解决办法
检查冷凝水排放装置和 供水气压是否符合要求 检查供气部分是否有故障
适当降低车速 加大预热或换纸 修正胶黏剂质量 加大胶黏剂附着量
瓦 楞 问 题 产 生的原 因及解 决办法 (PPT54 页)
产生原因
传送带运行压力不够
四
纵
输送桥架输出瓦 楞纸板张力不够
向
向
下
面纸含水量不均衡
翘
面纸张力太大
瓦 楞 问 题 产 生的原 因及解 决办法 (PPT54 页)
解决办法
适当加大张力系 统的控制力度 适当预热
瓦楞纸板常见质量问题和产生原因及解决办法

•
改善粘合剂质量 调整合理间隙,增大粘合 剂着量
检查冷凝水排放装置和 供气气压是否符合要求 检查供气部分是否有故 障 加大予热或换纸 适当降低车速
增加粘合剂浓度 清理双面机并检查供气 系统 加在予热或更换原纸 调整分切园刀的咬合和 贴合间隙 调整合理间隙,增大粘合 剂附着量 适当降低车速
质量问题
面纸折皱
解决办法
瓦楞辊表面不清洁 瓦楞辊热量不均衡 粘合剂粘度不够
粘合剂附着量太大
• 清除瓦楞辊表面脏物 • 检查冷凝水排放情况
• 调整粘合剂的制作,检 查各种原料质量
• 修正和调整涂胶间隙、 减小着胶量
帆布带污损、透气性不好 • 双面机热板表面有异物 •
• 瓦楞原纸含水不均衡张力小 • 适当予热并加大张力控制
• 过纸天桥张力不均衡
质量问题
楞倾斜 楞不均
产生原因
解决办法
涂胶辊和浮动辊不平行 •
双面机重量辊位置不当或压 • 力大
过纸天桥张力太大
•
瓦楞原纸含水过高
•
瓦楞辊不平行
•
瓦楞辊贴合间隙太小
•
瓦楞辊表面有脏物
•
检查和修正二者的调整 装置
适当控制重量辊的投放 并检查平衡度 减低控制器的张力
•
3. 预热包角调控不平衡 •
4. 过纸天桥过多堆积
•
5. 过纸天桥输出瓦楞纸板 •
张力过大
适当加大张力系统的控 制力度 适当预热或喷水后予热
检查并修整传动装置, 保证运转平行 减少堆积 适当减小输出张力控制
1. 帆布带运行压力不够 •
2. 过纸天桥图形出瓦楞纸 •
板疑义力不够
3布不均衡
喷淋或予热控制
纸箱厂纸板各种常见不良的解决方案
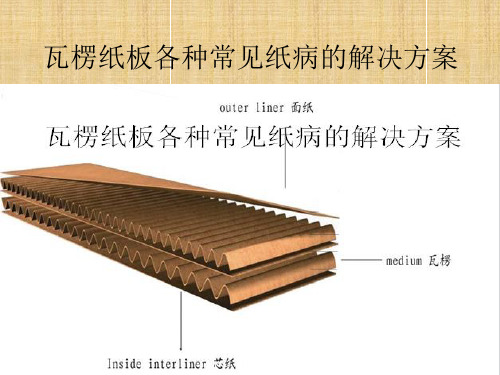
二十、面纸划痕
原因分析:①原纸制造时的划痕;②预热器有毛刺所致;③烘干机热 板上面有胶渣纸屑等异物,便磨擦划伤面纸;④烘干机后的各纸板托 架宥毛刺或硬物划伤;⑤堆码机转送带接扣部分开裂。 解决方法:①更换瓦纸;②打磨预热器;③清除热板异物;④清除异 物打磨毛刺;⑤更换皮带扣或将翘起带扣敲平。
二十一、白卡纸板泛黄
2.经双面机后瓦楞破碎 原因分析:①天桥各导纸辊或多重预热器缸面有毛刺造成机械划伤; ②天桥至单面机的传输带接扣扎破。 解决方法:①检查到有导致瓦楞破碎的毛刺,用砂纸或板挫打磨光滑; ②更换带扣,重新接好。
七、压线破损
1.里纸破裂 原因分析:①里纸质次,太薄;②里纸脱水严重无韧性;③压线凸轮 楞角不圆滑;④压痕过深。 解决方法:①更换里纸或适当调浅压痕深度;②里纸可不经过预热器; ③更换弧形压线轮或打磨光滑凸轮楞角;④适度调整压线深度。
2.面纸起皱 原因分析:①导纸辊不平行;②烘干机进纸口偏斜;③瓦纸水分不平 衡;④瓦纸两端张力不平衡。 解决方法:①校正导纸辊;②纠正烘干机进纸口;③增大瓦纸预热面 积;④更换瓦纸。
3.瓦纸打皱 原因分折:瓦纸两端强力、水分、厚薄不均,制动不足。 解决方法:调整预热面积,涨紧制动闸阀或将瓦纸翻转使用,如仍出 现打皱现象,可更换瓦纸。
十七、纸板面纸出现大量黑色斑点
原因分析:面纸中含有塑料成份,瓦纸在加热过程中,细小的塑料熔化 即出现大小不等的黑色斑点。 解决方法:由于上述现象,原纸未经使用极难察觉,除选择具有良好信 誉品牌面纸。
十八、面纸露楞
原因分析:①涂胶量过大;②面纸太薄。 解决方法:①现面纸厚薄、车速、温度适量涂胶;②减少用胶量仍不能 解决,更换瓦纸。
2. 面纸破裂 原因分析:①面纸质次;②压痕线过深;③压痕凹轮太深不圆滑;④ 压线调节装置失灵;⑤纸板过于。 解决方法:①对面纸喷蒸汽,增大涂胶量并适当提高烘干机车速;② 调浅压线;③更换压痕凹轮或打磨;④修正压线调节装置后再生产; ⑤适当提高烘干机车速,关闭部分烘干机热源。
纸箱厂如何解决纸箱塌箱问题

纸箱厂如何解决纸箱塌箱问题
1、要控制好原纸的使用,检查瓦楞纸的施胶情况,原纸表面吸水性指标药效。
如果原纸表面施胶差,吸水性就会偏高,很容易手冷库低温、潮湿的环境影响,导致纸箱回潮,变软,整理抗压强度降低。
2、生产纸板时要控制纸板的水分含量纸板的水分含量不可过多,因为水分大则纸板的硬度低,影响纸板的边压指数。
在纸板加工过程中,单面机和双面机工序上胶量不能过大。
一旦上胶量大,纸板的楞形会变形,而瓦楞的形状是直接影响纸板的边压的,边压降低,纸箱的抗压强度也随之降低。
3、纸板的粘合强度要大粘合强度是瓦楞纸与里纸、面纸的粘合力。
如果万一出现纸板假粘,纸箱受压后,面纸或里纸便会与瓦楞纸分离,那么纸箱的抗压强度会直线下降。
4、生产环节中的间隙压力控制要适中尤其要注意糊箱机上糊的间隙压力不能太小,双面机,模切机上的太阳轮间隙压力要控制在合理的范围内,以避免将瓦楞形压溃,影响纸板纸箱的抗压强度。
5、使用泼水剂、防水光油等解决纸箱表面防水防潮问题。
本文章由泰昌仪器有限公司提供。
瓦楞纸板质量影响因素分析
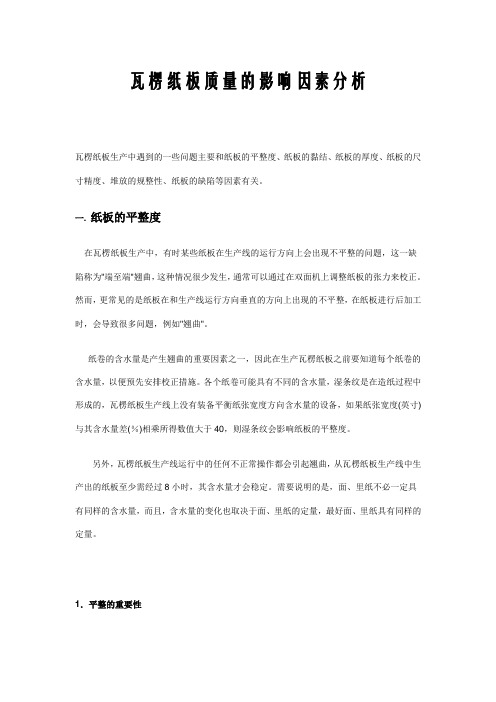
瓦楞纸板质量的影响因素分析瓦楞纸板生产中遇到的一些问题主要和纸板的平整度、纸板的黏结、纸板的厚度、纸板的尺寸精度、堆放的规整性、纸板的缺陷等因素有关。
一. 纸板的平整度在瓦楞纸板生产中,有时某些纸板在生产线的运行方向上会出现不平整的问题,这一缺陷称为"端至端"翘曲,这种情况很少发生,通常可以通过在双面机上调整纸板的张力来校正。
然而,更常见的是纸板在和生产线运行方向垂直的方向上出现的不平整,在纸板进行后加工时,会导致很多问题,例如"翘曲"。
纸卷的含水量是产生翘曲的重要因素之一,因此在生产瓦楞纸板之前要知道每个纸卷的含水量,以便预先安排校正措施。
各个纸卷可能具有不同的含水量,湿条纹是在造纸过程中形成的,瓦楞纸板生产线上没有装备平衡纸张宽度方向含水量的设备,如果纸张宽度(英寸)与其含水量差(%)相乘所得数值大于40,则湿条纹会影响纸板的平整度。
另外,瓦楞纸板生产线运行中的任何不正常操作都会引起翘曲,从瓦楞纸板生产线中生产出的纸板至少需经过8小时,其含水量才会稳定。
需要说明的是,面、里纸不必一定具有同样的含水量,而且,含水量的变化也取决于面、里纸的定量,最好面、里纸具有同样的定量。
1.平整的重要性当纸板直接作为成品出售时,翘曲往往被用户认为是质量问题而成为扯皮的根源。
更进一步说,瓦楞纸板的平整度对以后的加工操作有很大的影响。
在自动堆积机中,纸板平整才能堆积稳定,才能很方便地由滚轮传送器运出去,堆积的稳定性对于从瓦楞纸板生产线终端传送到库房,再从库房传送到后加工设备是很重要的。
后加工设备的自动进料器不能接受过于翘曲的纸板,翘曲的纸板会引起阻塞和机器停车,大大降低生产效率。
同时,如果后加工设备不能够连贯地传送纸板,就会导致不准确的印刷记数和模切操作.纸板翘曲也会导致粘盒、粘箱困难。
另外,纸板翘曲会降低纸箱的抗压强度,因为箱壁偏移使纸箱易垮塌。
2。
翘曲度的测量为了在瓦楞纸板生产线上进行各种调整以平整翘曲也为了纸板在厂内、外的质量控制,都需要测量翘曲度。
纸箱在使用过程中出现的问题及解决方法

操作有关。
6.纸箱的印刷设计不合理
瓦楞纸板的瓦楞形状和结构,决定了瓦楞纸 板的承压力。印刷对瓦楞纸板会造成一定损伤, 压力的大小和承受面积的大小是影响纸箱抗压 强度的一个主要因素。如果印刷压力过大,容易 将瓦楞压溃,楞高降低。特别是在压线处印刷时, 为了在压线部位进行强制的、清晰的印刷会将整 个纸板压溃,使纸箱抗压强度大幅度下降,因此 要尽量避免在此印刷。纸箱满版或四周印刷图文 时,除压印辊对瓦楞纸板有压迫作用外,油墨对 纸面还有浸润作用,这又使纸箱的抗压强度有所
2.瓦楞纸板达到规定的厚度
瓦楞纸板的厚度对纸箱的抗压强度影响很 大。在生产过程中,瓦楞辊磨损严重,造成瓦楞纸 板的厚度下降,纸箱的抗压强度也随之下降,导
致纸箱的破损率增加。
3.减少瓦楞的变形
首先,要控制好原纸的质量,特别是瓦楞芯 纸的环压强度、水分等物理指标。其次,对瓦楞 纸板工艺进行研究,改变因瓦楞辊的磨损、瓦楞 辊间的压力不足等因素导致的瓦楞变形。第三, 改进纸箱制造工艺,调整制箱机的送纸辊的间隙, 以及将纸箱印刷改成柔性版印刷为主,以减少瓦 楞的变形。同时也要注意纸箱的运输,尽量采用 厢体车运输纸箱,减少因油布、绳子的捆扎和装 卸工的踩踏而引起瓦楞变形。
(二)纸箱的大量破损主要由于以下因素:
Hale Waihona Puke 1.纸箱的箱体尺寸设计不合理
纸箱的长、宽、高的尺寸与纸箱的破损关系 较大。纸箱的尺寸一般是根据所要装的瓶数及瓶 高来确定的。箱长是长方向上的瓶数×瓶 的直径,箱宽是宽方向上的瓶数×瓶的直 径,箱高基本上是瓶高。箱体的四边周长相当于 支撑纸箱压力载荷的整个侧壁,一般周长越长, 抗压强度越高,但这种增高并不成比例。如果四 边周长太大,即内装物的瓶数比较多,整箱产品 的毛重就大,对纸箱的要求也高,需要有较高的 抗压强度和耐破度,来保证纸箱的使用性能,否 则,纸箱比较容易在流通过程中发生破损等现 象。市场上,596mL×24 瓶纯水箱在所有的
瓦楞纸板常见质量问题和产生原因及解决办法

修正瓦楞辊的贴合间隙 清理瓦楞表面异物
瓦楞辊贴合间隙大
• 修正瓦楞辊的贴合间隙
瓦画辊贴合间隙不平衡 •
导纸板位置不正、磨损或带
脏
瓦楞原纸含水水均衡
•
瓦楞原纸的张力太小
•
检查并修正或更换导纸 板
加大予热包角 适当调整张力控制
瓦楞纸板常见质量问题和产生原因及 解决办法
质量问题
平行度
• 瓦楞辊表面带脏
• 清理瓦楞辊,保持干净
• 导纸板位置不正,、带脏或磨损 • 检查、修正、清理或更换导
纸板
• 涂胶辊、浮动辊间隙不当
• 调整二者的贴合间隙
• 粘合剂质量不好
• 检查并重新制作粘合剂
• 瓦楞原纸含水不均衡张力小 • 适当予热并加大张力控制
• 过纸天桥张力不均衡
瓦楞纸板常见质量问题和产生原因及 解决办法
1. 面纸予热包角太大 2. 里纸予热包角太小 3. 过纸天桥堆积过多 4. 单面机涂胶量过大
5.涂胶仙涂胶量偏少
6.车速太低
7.双面机热板温度高
8.重量辊施加压力过大
解决办法
• 减少包角、降低予热 • 增大包角、加强予热 • 减少过纸天桥的堆积 • 适当控制单面机的着胶
量 • 适当增大涂胶机的着胶
7.双面机热板温度高 8.重量辊施加压力过大
解决办法
• 减少包角、降低予热
• 增大包角、加强予热 • 减少过纸天桥的堆积 • 适当控制单面机的着胶
量 • 适当增大涂胶机的着胶
量 • 根据实际运行质量,适
当提高车速
• 提高车速或人为降低热 板
• 适当投放重量辊
PPT文档演模板
瓦楞纸板常见质量问题和产生原因及 解决办法
瓦楞纸箱常见问题原因及解决方法
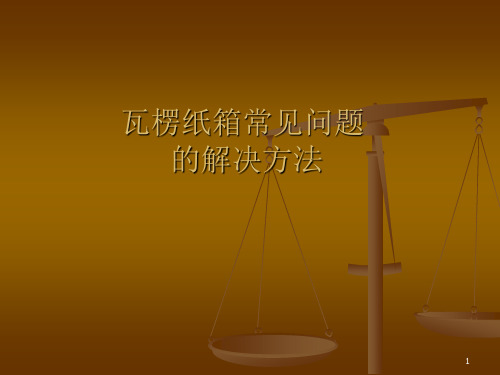
解决 1.提高水墨的干燥速度 : a)减少第一色水墨的黏度 b) 减少第一色水墨膜层厚度 c) 适量加入快干剂 d) 降低机器速度 e) 降低表面张力 f) 提高烘干温度 2.调整第二色墨粘度,使之高于第一色墨粘度 3. 降低干燥速度: a) 加慢干溶剂 b)关闭干燥器 c)提高机器速度
3
因素 4.第二色墨PH值过高或过低
23
2.
水墨、纸板、印刷机结构方面的改 变 , 印版、使用速度及环境、供应 商、操作员习惯或机器设定的改变
原因 只是整个的图像周围有重影 1. 印版的压力过大 2. 网纹辊与印版压力过大 只最前边缘/ 最后边缘有重影 1. 网纹辊印版压力过大 2. 印版包衬变形 3. 印版或版筒衬垫松弛
解决 只是整个的图像周围有重影 1. 减小印版与纸板压力 2. 调整减少网纹辊压力,检查印版 水平和衬垫 只最前边缘/ 最后边缘有重影 1. 调整减少网纹辊压力,检查印版 水平和衬垫 2. 使用薄的衬版材料 3. 重装印版使其贴紧版筒
解决 7.清洁机器,替换水墨 8.检查并调整水墨 pH 9.联系水墨供应商
9.水墨配方
12
原因 1. 二辊水墨量调节不当
2.
网纹辊磨损或肮脏,网纹楞线太粗, 或 网目粗糙
3. 印版太硬 4. 水墨粘度太低 5. 印版太光滑 6. 水墨配方不对
解决 1. 减少网纹辊表面上的水墨量: a) 适当增加压力 b)更换刮墨刀 c)变更水墨配方 2. a) 更换或清理网纹辊 b) 使用别的或比较高网目的网纹辊 c) 调整水墨粘度或配方 3. 使用较软印版 4. 用新鲜的水墨调高水墨粘度 5. 清理或替换印版 6. 建议请教水墨供应商
解决 1.减小印版衬垫 2.检查并调整水墨 pH 到合适值 3.调平,修补, 清理或替换印版或整个衬 垫 4.减少水墨膜层厚度 : a)降低水墨粘度 b) 逐渐增加水墨利用率 c) 降低网纹辊墨量 5.调整参数 ,调整压力辊,版和网纹 辊压力 ,使轴平行 6. a)加慢干剂减慢干燥 b) 停止吹气或加热干燥 c)提高机器速度
- 1、下载文档前请自行甄别文档内容的完整性,平台不提供额外的编辑、内容补充、找答案等附加服务。
- 2、"仅部分预览"的文档,不可在线预览部分如存在完整性等问题,可反馈申请退款(可完整预览的文档不适用该条件!)。
- 3、如文档侵犯您的权益,请联系客服反馈,我们会尽快为您处理(人工客服工作时间:9:00-18:30)。
瓦楞纸箱塌箱原因及解决对策
众所周知,瓦楞纸箱最主要的力学指标就是空箱抗压强
度。
在实际使用过程中,瓦楞纸箱可能会受到来自外界局部应力的破坏性冲击,但在正常运输条件下,这种局部应力发生的概率很小,尤其对托盘集合包装而言,这种应力发生的情况几乎可以忽略。
然而,瓦楞纸箱包装件一般都会有堆码的情况,并且最底部的瓦楞纸箱不仅承受来自其顶部载荷的静态压力,还要承受运输过程中因振动、冲击等造成的动态压力。
在这种情况下,瓦楞纸箱具有足够的抗压强度是保护内装物的必要前提。
但瓦楞纸箱在实际使用过程中经常会发生塌箱现象,这
对于少部分非销售包装,内装产品可以承压且不容易损坏的产品而言,瓦楞纸箱塌箱问题的出现并非不可接受,而对于大部分运输包装和销售产品来说,瓦楞纸箱塌箱问题的出现完全是不可接受的,外包装箱的严重变形极有可能导致内装产品出现问题,没有消费者会为一个内装物可能损坏的产品买单。
因此,对于瓦楞纸箱塌箱问题必须引起足够的重视,否则将会对最终的产品销售产生严重的负面影响。
塌箱原因分析造成瓦楞纸箱塌箱的原因有很多,从最初的原纸质量到
最后的仓储销售,各个环节都有可能导致瓦楞纸箱塌箱,主要原因归纳如下。
1)原纸质量。
由于原纸本身不具备防潮性,而且没
有进行相应的防潮处理,因此使得其制成的普通瓦楞纸箱在放入冷库储存到搬至库外的过程中,由于温差极易导致瓦楞纸箱吸潮,含水率迅速从10%升至19%,从而使得瓦楞纸箱
抗压强度急剧下降,产生卧箱和破损现象,进而影响内装物质量。
2)原纸含水率偏高。
原纸含水率太高,容易造成瓦
楞变形、瓦楞纸箱抗压强度降低,干燥后又容易产生瓦楞纸板翘曲变形等物理损伤。
3)在瓦楞纸制造过程中,由于施胶量控制不当,影
响了成品后瓦楞纸板的黏合强度,从而造成塌箱。
4)印刷工艺和过程控制中压力控制不当。
压力过大
时,导致瓦楞变形。
5)运输过程中车辆的振动和冲击,造成瓦楞纸箱的
变形破损,甚至内装物的损坏。
这种损坏是无法避免的。
6)人工搬运、周转次数多。
人工搬运次数多,瓦楞
纸箱不可避免地受到较大的外部冲击,从而造成瓦楞纸箱本身的强度降低。
7)仓储湿度。
商品库存周期有长有短,南北方空气
湿度差异较大,对于库存周期较长而湿度又大的仓储条件,
瓦楞纸箱抗压性能下降较多。
8)仓储时间。
即使在恒定温湿度条件下,仓储时间
过长也会导致瓦楞纸箱慢慢“老化” ,瓦楞纸箱本身的强度也会随之降低。
9)仓储堆码方式。
如悬臂式堆码、错落式堆码、狼
牙交叉式堆码以及无货架堆码等大高度堆码方式,将大大降低瓦楞纸箱的抗压强度。
10)其他因素。
模切加工工艺、手提孔的位置、添加
内衬、纸箱结构以及远洋运输环境等因素都会影响瓦楞纸箱的抗压强度。
塌箱解决对策上述塌箱问题的原因可以简单归纳为生产工艺、运
输过
程、储存过程以及其他因素几类。
下面,笔者将对这几个方面原因的解决对策进行阐述。
1.生产工艺
相对来说,改变瓦楞纸箱生产工艺是改善瓦楞纸箱塌箱
问题最简单、最直接的方式,因为这只是技术参数方面的变动,不涉及设备能力问题。
1)在原纸表面通过印刷、涂胶、淋膜等工艺增加原
纸的防潮性能。
2)控制瓦楞纸板的含水率,使瓦楞纸板在不增加任
何费用的情况下保持最佳的抗压性能性能。
含水率为
楞纸板强度为100%;含水率为12%时,瓦楞纸板强度下降
为66%;含水率为16%时,瓦楞纸板强度下降至43%。
3)在瓦楞纸板生产过程中,施胶量并非越多越好
如果施胶量过多,则会导致瓦楞顶部变形,成品瓦楞纸板厚度变小,瓦楞纸板定量变大,抗压强度降低,这样不仅浪费了胶黏剂,还增加了运输成本。
如果施胶量过少,虽然可以节省生产成本,但容易造成面纸芯纸黏合不牢,瓦楞纸板的抗压强度也会降低。
因此,提高淀粉糊的固含量,同时减少施胶量,最大程度地降低施胶过程中对瓦楞结构的破坏,可以保证在最节省胶黏剂的情况下,使瓦楞纸板的黏合强度和抗压强度达到最佳状态。
4)如果采用在瓦楞纸板上直接印刷的方式,单色小
面积印刷时瓦楞纸箱强度约降低7%,单色大面积印刷时瓦
楞纸箱强度约降低12%,单色满版印刷时瓦楞纸箱强度约降
低20%,多色大面积印刷时瓦楞纸箱强度约降低30%,多色
满版印刷时瓦楞纸箱强度约降低50%。
因此,如果采用先印
刷原纸再制作瓦楞纸板的方式,可将印刷对瓦楞纸板的影响降到最小。
2.运输过程
运输过程中的振动和人工机械搬运的冲击对瓦楞纸箱
强度会造成一定的影响。
任何交通工具在运输过程中都会产生振动,并且这种危害无法通过技术手段完全消除,所以瓦
楞纸箱必须面对振动造成的影响。
在交通路面较好的情况下,运输1000〜2000km后瓦楞纸箱强度约降低10%左右。
而由人工和机械两种原因造成的冲击,往往人工冲击所
造成的损伤要比机械冲击严重得多,一次人工装卸且很少受
到撞击的情况下,瓦楞纸箱强度约降低10%;多次装卸且很
少受到撞击的情况下,瓦楞纸箱强度约降低20%;而多次装
卸且经常受到撞击的情况下,瓦楞纸箱强度可降低50%,甚
至更多。
快递运输过程中甚至出现过标准六面体的瓦楞纸箱运送到目的地之后几乎变成了球型的情况,瓦楞纸箱抗压强度几乎完全丧失。
对此,应将物流向集合包装方向发展,尽量降低人工装卸次数,从而减少对瓦楞纸箱的损伤。
3.储存过程
在瓦楞纸箱储存过程中,其强度主要受湿度的影响。
如
果瓦楞纸箱没有经过防潮处理,假定湿度为RH50%时,瓦楞
纸箱强度为100%;当湿度升至RH60%时,瓦楞纸箱强度约
为90%;湿度升至RH70%时,瓦楞纸箱强度约为80%;湿度
升至RH80%时,瓦楞纸箱强度约为68%;湿度继续升至RH90%
时,瓦楞纸箱强度约为48%;当湿度达到RH100%时,瓦楞
纸箱强度约为15%。
所以,针对潮湿的仓库或环境,应当加
强通风或安装除湿机来降低空气中的湿度。
另外,低湿度还
可以有效避免瓦楞纸箱发霉变质。
即使没有其他任何因
素影响,瓦楞纸箱在存储过程中其强度也会随着时间的推移
逐渐降低,这属于自然“老化”现象,无法避免。
在一般温湿度条件下,堆码10天后瓦楞纸箱强度约降低37%,堆码30 天后瓦楞纸箱强度约降低40%,堆码90 天后瓦楞纸箱强度约降低45%,堆码180天后瓦楞纸箱强度约降低50%,而
在南方梅雨季节堆码180 天后瓦楞纸箱强度约降低80%以上。
瓦楞纸箱的四个角部承受了全部强度的3/4 ,是最主要
的受力部位,所以瓦楞纸箱的堆码方式对瓦楞纸箱强度的影响非常大。
堆码时瓦楞纸箱上下四角对齐是保持瓦楞纸箱强度的最佳状态,若此时的强度为100%,则悬臂堆码(纸箱
超出托盘)时,瓦楞纸箱强度降低20%〜40%;层层错位堆
码时,瓦楞纸箱强度降低9%〜15%;互锁式层层错位堆码时,
瓦楞纸箱强度降低40%〜60%,甚至托盘顶铺板的间隙也会
导致瓦楞纸箱强度降低9%〜25%。
可见,错误的堆码方式将导致瓦楞纸箱强度出现大幅下降,因此应选择正确的堆码方式,如齐平式堆码法、底部二层活用堆码法,必要时瓦楞纸箱四周还可以使用纸护角来提高整体强度。
4.其他因素
1 )瓦楞纸箱两侧面各开一个手提孔时,瓦楞纸箱强
度约降低20%,两侧面和两正面各开一个手提孔时,瓦楞纸
箱强度约降低30%。
手提孔虽然会降低瓦楞纸箱强度,但便
于人工搬运,可降低野蛮装卸的风险。
因此,为避免因开孔而导致瓦楞纸箱强度降低,可在开孔部位粘贴加强纸板或安
装塑料护手。
2)为提高瓦楞纸箱强度,可在瓦楞纸箱内部增加支
撑结构,辅助增强瓦楞纸箱强度,或者通过合理的缓冲包装结构设计来辅
助加强瓦楞纸箱强度。
3)远洋运输时,集装箱内不仅湿度大,昼夜温差还
容易导致集装箱四壁产生积水,所以远洋运输时瓦楞纸箱定要注意防水处理。
结论总之,导致瓦楞纸箱塌箱的原因有很多。
生产工艺可以
视作单一控制方面,将生产工艺控制好之后再控制运输过程和储存过程。
因为生产工艺的改进往往比较简单,只需做个小小的改动,就能有效提高瓦楞纸箱抗压强度,从而解决实际的大问题,而运输过程和储存过程的改变有时很难实现。
因此,不能一出现瓦楞纸箱塌箱问题就提高瓦楞纸箱抗压强度,那样势必会造成包装材料成本的增加,不利于包装减量化,更不利于环保事业。
而且,运输过程和储存过程必须结合起来考虑,二者同步存在,但时间长短不一,应综合考虑多方面因素,才能合理确定瓦楞纸箱的抗压强度。